Теплофизика высоких температур, 2019, T. 57, № 6, стр. 819-834
Новый механизм взаимодействия сварочного дугового разряда постоянного тока обратной полярности с поверхностью алюминия
А. Е. Балановский *
Иркутский национальный исследовательский технический университет
Иркутск, Россия
* E-mail: fuco.64@mail.ru
Поступила в редакцию 13.03.2019
После доработки 16.05.2019
Принята к публикации 24.06.2019
Аннотация
Представлены результаты исследования сварки алюминия постоянным током обратной полярности в среде защитных газов (аргон) на стадии привязки и образования ванны расплавленного металла. Показано, что катодные пятна в диапазоне токов 5–50 А и длительностью воздействия до 1 с не очищают поверхность алюминия от катодной пленки, а переплавляют поверхностный слой. Проведен анализ типов формирующихся катодных пятен на поверхности алюминия. Показано, что основным механизмом удаления оксидной пленки является испарение. Предложен новый механизм взаимодействия сварочного дугового разряда с поверхностью алюминия, где основную роль в формировании сварочной ванны играет неподвижное катодное пятно, которое испаряет оксидную пленку, с одной стороны, а с другой стороны, за счет высокой плотности тепла интенсивно нагревает поверхностный слой алюминия до фазового перехода. После образования сварочной ванны неподвижное катодное пятно исчезает, наступает диффузный режим горения сварочной дуги, который характеризуется однородным распределением электрического поля по длине разрядного промежутка с низким падением потенциала и занимает практически весь межэлектродный зазор.
ВВЕДЕНИЕ
В работе продолжено исследование различных стадий горения сварочного дугового разряда на поверхности алюминия, покрытого оксидной пленкой [1, 2]. Ранее изучились процессы, протекающие на стадии привязки и формирования сварочной ванны на постоянном токе прямой полярности. Показано, что на стадии привязки искровой разряд оказывает существенное термическое воздействие, заключающееся в оплавлении поверхности в зоне привязки искры и развитии процессов рекристаллизации аморфной матрицы пленки в зоне термического влияния [1]. На стадии формирования сварочной ванны сварочная дуга горит в парах алюминия, и вследствие этого продукты конденсации снижают температуру сварочного столба в анодной области. Продукты конденсации алюминия формируются по кластерному механизму с образованием фрактальных нитевидных структур. Кластерный механизм характеризуется выходом в парообразное состояние недиссоциированных молекулярных блоков алюминия, которые в процессе конденсации образуют сложный по морфологии состав пленки оксида алюминия на поверхности сварочной ванны [2]. В большинстве фундаментальных работ, посвященных сварке алюминия, предполагается, что оксид алюминия Al2O3 имеет высокую температуру плавления (2046°С) по сравнению с алюминием [3, 4]. Из-за этого окисная пленка не расплавляется в процессе сварки и покрывает поверхность алюминия прочной оболочкой, затрудняющей образование общей ванны [3]. Известно, что качественные сварные соединения получаются при сварке постоянным током обратной полярности или переменным током [5, 6]. В качестве основных гипотез, объясняющих механизм “удаления” оксидной пленки с поверхности алюминия, привлекаются процессы и эффекты по аналогии с рассматриваемыми в теории газового разряда, такие как бомбардировка поверхности оксидной пленки положительными ионами и катодное распыление материала при сварке постоянным током на обратной полярности и переменным током [6–10]. Однако убедительных доказательств в пользу основных гипотез удаления оксидной пленки авторы [6–10] не приводят, а просто исходят из факта, что если ванна расплавленного металла образовалась, следовательно, по их мнению, произошла “очистка” (катодное распыление) поверхности катодными пятнами. Известно, что аналогия не является доказательством, и привлечение экспериментальных результатов, полученных по вакуумным дугам [11–20], к объяснению механизма удаления оксидной пленки с поверхности алюминия при сварке на обратной полярности не корректно по следующим причинам.
Во-первых, очистка – не совсем корректный термин, так как искажает физическую картину процесса воздействия катодных пятен в вакуумных дугах на поверхность металла по конечному результату. Наблюдение за эродированными дорожками [11–15], оставленными катодным пятном на поверхности металла после короткой импульсной операции, выявило, что плотность тепловой энергии в катодном пятне имеет высокое значение 1010 Вт/м2 [21], 1012 Вт/м2 [22] или больше [23]. Вследствие высокой плотности тепловой энергии в катодном пятне, по мнению [12], слой оксида под пятном нагревается до температуры испарения и испаряется с поверхности за очень короткое время. Во время удаления оксида испарением под оксидом образуется расплавленный металл. Из-за сильной реактивной силы испарения почти весь расплавленный металл выталкивается наружу. В результате, шероховатость поверхности может быть оценена как равная глубине расплавленной дорожки. Конечным результатом такой “очистки” является хаотически оплавленная поверхность с участками сильного и слабого расплавления поверхностного слоя материала катода и участками, не тронутыми катодными пятнами. Количество испарившейся оксидной пленки и переплавленной с поверхностным слоем металла неизвестно, так как авторы [11–20] рассматривают такую обработку поверхности не в качестве финишной операции, а как промежуточную – под покраску и напыление, где действительно необходима поверхность с грубой шероховатостью. В работе [24] результаты вакуумной очистки поверхности оксидного слоя нанометровой толщины на нержавеющей стали SUS430 оценены с использованием оже-электронной спектроскопии (AES). Показано, что оксидный слой существует после обработки. Отметим, что применительно к сварке алюминия интерес представляет большой объем расплавленной ванны без следов оксидной пленки, а соответствующих работ в открытой печати нет.
Во-вторых, известно [25–27], что катодные пятна разделяются на типы 1, 2, 3, которые определены в зависимости от времени существования и скорости движения пятна. Распространенность различных типов пятен зависит от тока дуги, материала катода и характеристик поверхности катода (например, оксидной или другой пленки, шероховатости). В работе [28] отмечается, что катодные пятна медленно движутся на оксидном слое и их средняя скорость составляет 26.1 м/с. С другой стороны, зафиксированы катодные пятна вблизи центра сварочной ванны, где в основном был удален оксидный слой, они двигались с высокой скоростью, и их средняя скорость достигла 121.9 м/с. Максимальная скорость катодного пятна вблизи центра сварочной ванны – 1 км/с [28], но не ясно, как авторы идентифицировали каждое катодное пятно, по каким признакам, свойствам.
В-третьих, в работах [6, 29, 30] указано на неустойчивость сварочной дуги при сварке на обратной полярности при токах менее 50 А. Более того, на таких токах при сварке тонколистового алюминия не всегда удается получить ванну расплавленного алюминия после катодной очистки на обратной полярности.
В-четвертых, вопросы качественной очистки от оксидной пленки на токе обратной полярности остаются актуальными в связи с повышением требований к качеству сварных изделий из алюминия в авиа- и аэрокосмической отрасли. В работе [31] проведены исследования, которые показали наличие поверхностных загрязнений, возникающих во время сварки алюминиевого сплава AA2219 на постоянном токе обратной полярности и переменном токе, вызванных процессами сварки с металлическим электродом в инертном газе (MIG), в частности с вольфрамовым электродом (TIG), что в значительной степени влияет на качество сварных швов. Образование таких загрязнителей изучалось редко. Было установлено, что эти загрязнители в основном состоят из комплексов Al2O3, MgO, карбида и хрома. Таким образом, по имеющейся на сегодняшний день информации, работ, посвященных изучению разрушения оксидной пленки при сварке алюминия, ничтожно мало.
Основная цель данной работы – исследовать механизм разрушения оксидной пленки в процессе сварки алюминия постоянным током обратной полярности. Представлены предварительные результаты экспериментальных исследований особенностей сварочной дуги, горящей на постоянном токе обратной полярности в среде защитного газа (аргона).
МАТЕРИАЛЫ, ПРИБОРЫ И МЕТОДИКА ИССЛЕДОВАНИЯ
В методическом плане экспериментальные работы подробно описаны в [1, 2, 32, 33]. Для проведения исследований использовалась сварочная дуга постоянного тока обратной полярности (силой тока в пределах 2–100 А), которая горела вертикально между вольфрамовым неплавящимся электродом (диаметром 2.4 мм) и поверхностью алюминиевого сплава АМг-6 (изделие). Длина дуги изменялась от 1 до 8 мм. Дуга горела как стационарно, так и в динамическом режиме в интервале скоростей перемещения образцов 3.3–8 мм/с. Общее время горения дуги в стационарном режиме составляло 0.03–4 с, в динамическом – 1–20 с. Условия проведения эксперимента соответствуют реальному технологическому процессу сварки неплавящимся электродом (вольфрам) в среде защитного газа (аргон) на постоянном токе обратной полярности (минус на изделии), который используется в промышленности для сварки изделий из стали, алюминия, меди, титана. В международной классификации TIG – Tungsten Inert Gas – ручная дуговая сварка неплавящимся электродом в среде инертного защитного газа. Поскольку чаще всего в качестве материала для неплавящихся электродов применяется вольфрам, в немецкоязычной литературе используется сокращение WIG (Wolfram Inert Gas), иногда встречается обозначение GTA (Gas Tungsten Arc). В качестве источника питания сварочной дуги применялся стандартный промышленный сварочный источник тока с напряжением холостого хода 70 В и максимальным током 250 А, для возбуждения сварочной дуги – высоковольтный искровой разряд, входящий в стандартный комплект оборудования для сварки. Измерения тока и напряжения выполнялись цифровым осциллографом Tektronix TDC-1012B, фотографирование – цифровыми зеркальными камерами (ά SONY 350, Canon 550d-18-50). Процедура работы с камерой подробно изложена в [32, 33]. Для исследования быстропротекающих процессов использовалась скоростная кинокамера Рco.dimax, оснащенная 12-битной высокочувствительной матрицей КМОП. Время экспозиции составляло от 2 мкс до 40 мс. Электронно-микроскопические исследования поверхности алюминия после зажигания и привязки дуги проведены на базе ИРНИТУ с помощью растрового электронного микроскопа JIB-4501 JEOL многолучевой системы, оснащенной электронной и ионной пушкой JIB-4501, в комплекте с безазотной системой энергодисперсионного микроанализа, просвечивающего электронного микроскопа Tecnai G2 20F S-TWIN FEI. Полученные фотографии обрабатывались при помощи программы ACDSee-7.С. Оптический профилометр Bruker Contour GT-K1 использовался для измерения профиля поверхности катодных автографов.
РЕЗУЛЬТАТЫ ИССЛЕДОВАНИЙ
На рис. 1 представлены снимки поверхности алюминиевых образцов после воздействия стационарной сварочной дуги постоянного тока обратной полярности при различных режимах воздействия. Под номером 1 показана поверхность алюминия после воздействия при следующих параметрах: сварочный ток – 5 А, напряжение – 15 В, длина дуги – 5 мм, расход газа (аргон) – 12 л/мин, время воздействия – 1.5 с. Номер 2 соответствует току 10 А, напряжению 14 В; номер 3 – 18 А и 12 В, остальные параметры как в первом случае. При этом образование сварочной ванны не зафиксировано, есть отдельные точки, где видны расплавленные зоны алюминия (показаны стрелками). С увеличением длительности воздействия сварочной дуги до 2.5 с (номер 4, 10 А, 14 В) зафиксировано образование сварочной ванны. В следующей серии экспериментов под номерами 5–8 длина дуги была уменьшена до 1.5 мм при времени воздействия 1.5 с, сила сварочного тока соответственно составила 5, 10, 18, 30 А. Зафиксировано образование сварочной ванны, площадь которой увеличивается с повышением силы тока.
Рис. 1.
Поверхности алюминия после воздействия сварочного дугового разряда постоянного тока обратной полярности.
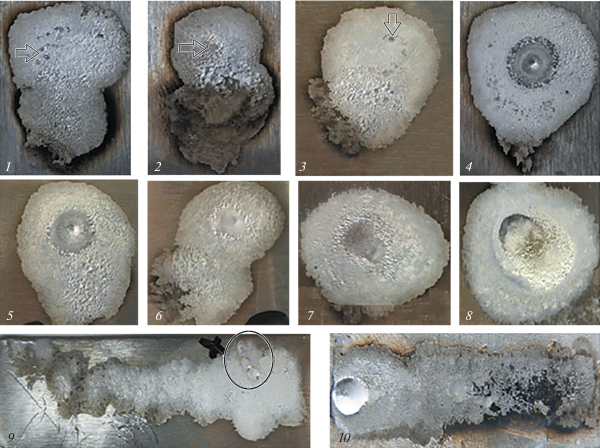
На образцах под номерами 9, 10 показана поверхность алюминия в динамическом режиме воздействия сварочной дуги постоянного тока обратной полярности, когда дуга горела стационарно, а образец перемещался под ней со скоростью 5 мм/с. При этом длина дуги составляла 5 мм, расход газа (аргон) – 12 л/мин, сварочный ток – 30 А (образец 9, начало горения дуги слева) и 90 А (образец 10, начало горения дуги справа). Видно, что динамический режим воздействия сварочной дуги влияет на формирование сварочной ванны. При токе 30 А поверхность только оплавляется в площади воздействия быстро перемещающихся катодных пятен. При токе 90 А сварочная ванна отчетливо зафиксирована только в конце воздействия. Вся поверхность в площади воздействия катодных пятен переплавлена и содержит загрязнения. По длине сварочной дорожки видно, что в центре есть отпечаток круглой формы. По всей видимости, с момента поджига дуги и ее движения по поверхности алюминия в этом месте образовалась сварочная ванна, но в дальнейшем внутренние условия взаимодействия дуги с поверхностью изменились, и видны только участки расплавленной поверхности от воздействия быстро перемещающихся катодных пятен.
Представляет интерес след от медленно движущегося катодного пятна на образце 9 (начало его образования зафиксировано крестиком на фото). Данное пятно возникло в конце горения сварочной дуги на периферии площади воздействия и начало медленно (относительно быстро перемещающихся катодных пятен) двигаться к центру сварочной дорожки под углом ~45°. В процессе движения оно остановилось и, не дойдя до центра, погасло, при этом оставило ярко выраженный след.
На рис. 2, 3 показаны снимки поверхности алюминия в следе рассмотренного выше катодного пятна, полученные на электронном микроскопе при различном увеличении. По всему пути продвижения катодного пятна остались четкие отпечатки воздействия с характерной топографией поверхности, обозначенной 1–7 на рис. 2 и 1–5 на рис. 3. В некоторых случаях для более четкой детализации поверхностной топографии представлены дополнительные снимки при большем увеличении (обозначено стрелками). В месте возникновения катодного пятна (6, 7 и далее по стрелке) видны одиночные кратеры и бугорки. Высота бугорков составляет 0.4–1.1 мкм. Их распределение по площади неравномерное, но очень плотное. Под номером 6 показано конусообразное углубление с разорванной поверхностью в вершине конуса. Топография поверхности конуса представлена на снимке 1. Поверхность покрыта микрократерами диаметром 1.2–1.8 мкм, которые равномерно распределены по площади. В некоторых местах фиксируются разрывы поверхностного слоя. За конусным углублением (по ходу движения катодного пятна) топография поверхности в виде микрократеров сохраняется (снимок 2). На снимке 3 поверхность опять становится бугристой. Здесь зафиксирован кратер квадратной формы с длиной стороны 5.99 мкм. На снимке 4 катодное пятно остановилось и образовалось конусное углубление. Поверхность представлена микрократерами диаметром 1.2–1.8 мкм. В вершине конусного углубления поверхность алюминия также деформирована и разорвана. После временной остановки катодное пятно продолжило движение, по ходу движения топография поверхности представлена на снимке 5, где видны некоторые дополнительные детали в виде каплеобразных вытянутых бугорков, редких микрократеров, микропустот и разрывов поверхностного слоя.
Рис. 2.
Электронные снимки поверхности алюминия в 2/3 области дорожки воздействия катодного пятна (отмечено крестиком) на образце 9 (рис. 1).
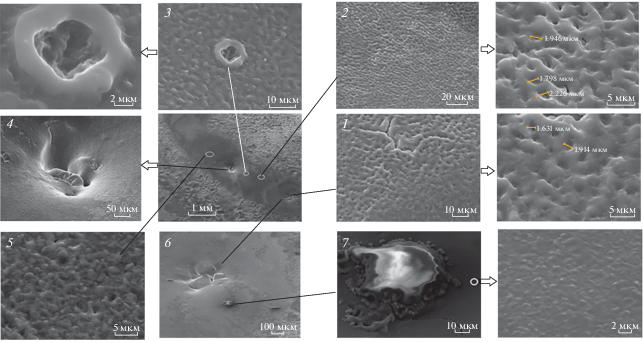
Рис. 3.
Электронные снимки поверхности алюминия в области окончания дорожки воздействия катодного пятна (отмечено крестиком) на образце 9 (рис. 1).
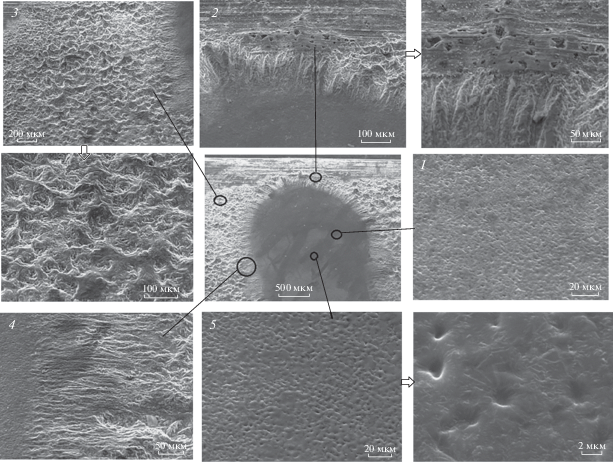
На рис. 3 приведены снимки катодного следа (1, 5) и его периферии (2–4). Для детализации дополнительно представлены снимки при большем увеличении. На снимке 5 показан центр дорожки катодного следа с относительно плотным распределением микрократеров. На дополнительном снимке при большем увеличении видна неравномерность их распределения и новые детали топографии поверхности – микропластинки, сформированные вокруг микрократеров в процессе кристаллизации расплавленной поверхности. На снимке 1 этих деталей нет, а сами микрократеры выглядят как микроуглубления на поверхности. На периферии катодного следа (снимки 2–4) топография поверхности существенно другая. На снимке 2 четко видна деформация поверхностного слоя алюминия в виде полос, смятия и отрыва, с множеством микропор. На снимке 3 представлена поверхность после воздействия быстро перемещающихся катодных пятен. Дополнительный снимок при большем увеличении показывает, что поверхностный слой алюминия буквально “искорежен”, небольшие объемы металла перекручены и вырваны. По мнению авторов [11–21], это результат очистки поверхности от оксидной пленки алюминия, с чем трудно согласиться. На снимке 4 в месте отвода тепла от катодного следа видны перекрученные объемы металла поверхностного слоя цилиндрической протяженной формы, которые напоминают “микрожгуты, канаты”.
На рис. 4 представлены результаты измерения шероховатости поверхности катодного следа (рис. 1, снимок 9), полученные с использованием оптического профилометра Bruker Contour GT-K1. Прибор измеряет параметры шероховатости в соответствии с международным стандартом ISO 4287–97 по восьми параметрам шероховатости: Ra – средняя шероховатость, Rq – среднеквадратичная шероховатость, Rsk – ассиметрия, Rku – эксцесс, Rp –максимальная высота пика профиля, Rv – максимальная глубина впадин профиля, Rz – высота по десяти точкам, Rt – максимальная высота профиля. Максимальные и минимальные значения отмечены цветом (размерность цветовой шкалы приведена на рис. 4), и автоматически вычислены перепады высот в мкм. Всего было сделано измерений в 294 200.900 точках поверхности катодного следа. В площади следа поверхность имеет низкие значения параметров шероховатости (Ra – 2.175 мкм) по оси х и у. Плотно распределенные микрократеры, зафиксированные на электронных фото по ходу движения пятна, дополнительно подтверждены профилограммами поверхности. Среднеквадратичная шероховатость Rq – 3.08 мкм. Максимальная глубина микрократеров, обозначенная на рис. 4 параметром Rv, составляет 17.072 мкм. Максимальная высота микровыступов Rp – 11.088 мкм. Отличие в визуализации микрократеров заключается в том, что оптический профилометр строит изображение по измерениям геометрических параметров кратеров, а так как кратеры имеют ультрамикронные размеры, то он представляет их в виде частиц.
Рис. 4.
Измерение шероховатости поверхности алюминия в области воздействия катодного пятна на образце 9 (рис. 1).
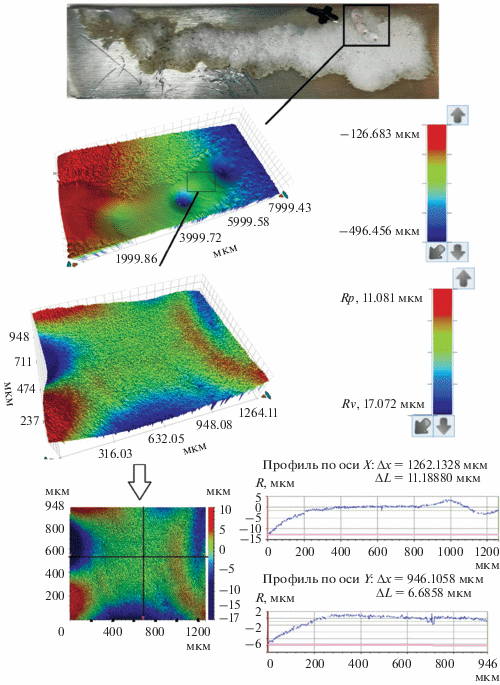
На рис. 5 приведены результаты изучения топографии поверхности ванны расплавленного металла (рис. 1, снимок 6) с использованием электронного микроскопа. В центре расплавленной ванны формируется дентридная структура (снимок 3). На периферии сварочной ванны (снимки 2, 4) структуры расплава различные. На снимке 4 – бугорковая поверхность, а на снимке 2 – микрократеры. На снимке 1 представлена топография поверхности, прилегающая к сварочной ванне, которая сформирована в результате воздействия быстро перемещающихся катодных пятен. Фиксируем “искореженную” поверхность, которую трудно описать. Дополнительно показана структура углублений, которая тоже трудно поддается краткому описанию из-за множества структурных особенностей.
На рис. 6 представлены результаты визуализации процесса образования сварочной ванны при воздействии стационарного сварочного дугового разряда постоянного тока обратной полярности. Сварочная ванна образуется не сразу, как было принято считать ранее, а имеет временной интервал формирования. Катодные пятна, взаимодействуя с поверхностью алюминия (рис. 6а–6в) не испаряют катодную пленку. Площадь обработки алюминия при переходе от рис. 6а к рис. 6в увеличивается, а пленка остается на поверхности. Далее возникает сварочная ванна (рис. 6д), которая увеличивается в размерах (рис. 6д, 6е). По мере продолжения разряда в стационарном режиме видно, что над поверхностью сварочной ванны начинает формироваться область осаждения оксида алюминия (зеленый цвет). Это совпадает с режимом формирования сварочной ванны при сварке постоянным током положительной полярности, описанной ранее [2].
Рис. 6.
Визуализация процесса образования сварочной ванны при воздействии стационарного сварочного дугового разряда постоянного тока 70 А обратной полярности (фокусное расстояние – 50 мм, диафрагма – 18, выдержка – 1/13).
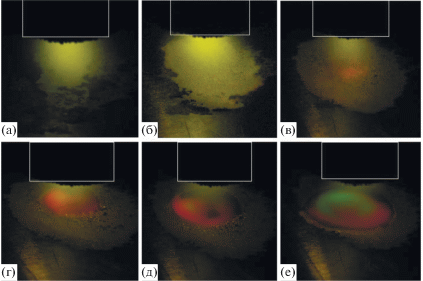
Детальная визуализация формирования сварочной ванны с использованием высокоскоростной съемки позволила установить, как она образуется и какую роль играют катодные пятна. При больших токах этот процесс происходит быстро. Следовательно, надо подобрать режимы тока, которые позволят зафиксировать процесс. В ходе многочисленных экспериментов такой режим был определен, в диапазоне тока 10–35 А возможно зафиксировать все стадии формирования сварочной ванны. На рис. 7 представлена динамика формирования ванны на поверхности алюминия в течение 5 с при длине дуги 5 мм. В момент зажигания разряда на поверхности алюминия образуются быстро перемещающиеся катодные пятна, в местах их образования фиксируется катодный факел. На начальном отрезке времени есть и анодный факел. По прошествии 0.12–2.3 с формируется разветвленная поверхность, на которую воздействуют быстро перемещающиеся катодные пятна (рис. 7а–7в). Анодный факел исчезает. В этот отрезок времени зафиксировано два типа быстро перемещающихся катодных пятен по яркости, на рис. 7б они отмечены (1 и 2). Видео скоростной съемки размещено в дополнительных материалах к статье (скорость воспроизведения – 3 и 32 кадр/с)11. Анализ большого количества отснятого материала показывает, что катодные пятна типа 1 преимущественно имеют интенсивную яркость и факел. После них всегда образуются темные точки на поверхности алюминия (3 на рис. 7г), соответствующие микроплавлению, которые видны также на рис. 1 (снимки 1 и 2).
Рис. 7.
Динамика формирования расплавленной ванны на поверхности алюминия: ток – 16 А, расход газа – 10 л/мин (масштаб – 10 мм).
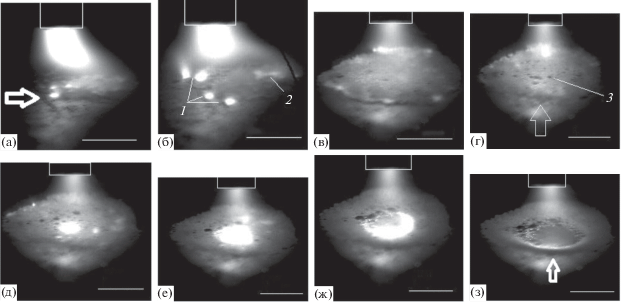
Катодные пятна типа 2 (рис. 7б) имеют минимальную яркость и предположительно формируются в местах точек микроплавления после ярких пятен 1 на границе контакта жидкого алюминия и оксидной пленки (твердая фаза). Они менее яркие, так как располагаются ниже поверхности и видна только часть света от них. По мере развития разряда количество микропятен плавления на поверхности алюминия от катодных пятен типа 1 увеличивается, и вся поверхность в пятне обработки выглядит как ажурная, со множеством темных точечных пятен. Эти пятна – миниотверстия в пленочном поверхностном слое алюминия. На рис. 7г–7е видно большое количество миниотверстий (пустот). Катодные пятна типа 2, возникая в местах миниотверстий поверхности плавления на границе жидкого алюминия и твердой фазы оксидной пленки, расклинивают и отрывают поверхностную пленку, создавая купол. Пленка начинает деформироваться (рис. 7г, показано стрелкой). По прошествии 3 с на поверхности пленки формируется большое неподвижное катодное пятно, быстро перемещающиеся пятна исчезают (рис. 7д, 7е). Это пятно стоит на месте в течение 20–50 мкс, а затем начинает быстро, в течение 5–10 мкс, увеличиваться в размере (рис. 7ж) с образованием ванны расплава. Все это сопровождается деформацией пленки оксида алюминия (рис. 7з, стрелка показывает деформацию). После образования ванны расплава начинают появляться быстро перемещающиеся катодные пятна по границе ванны и оксидной пленки.
На рис. 8 показаны основные стадии формирования сварочной ванны. Первая стадия – формирование на ажурной куполообразной поверхности алюминия неподвижного катодного пятна. Вторая стадия – образование жидкой ванны под неподвижным катодным пятном, третья стадия – увеличение объема жидкой фазы с возникновением сварочной ванны. Формирование купола зафиксировано не только скоростной съемкой, но и измерением профиля сварочной ванны с использованием оптического профилометра (рис. 8). Для формирования купола важную роль играет расход газа. При минимальном расходе газа 1–2 л/мин неподвижное катодное пятно проваливается вниз и горит под куполом пленки оксида алюминия. Границу купола и поверхность алюминия хорошо видно (3 на рис. 8). Далее пятно начинает разрастаться, а возникающие на границе расплава (1) и оксидной пленки быстро перемещающиеся катодные пятна вызывают интенсивное испарение (2 на рис. 8). На основе анализа покадровых фото скоростной съемки видно, как пленка буквально “тает”, когда с ней соприкасаются быстро перемещающиеся катодные пятна, и ванна жидкой фазы увеличивается. Однако это увеличение имеет предел (рис. 7з), когда площадь первичного воздействия превышает площадь сварочной ванны. Дальнейшего расширения жидкой фазы не наблюдается, что, по всей видимости, связано с лимитом тепловой мощности сварочной дуги.
Рис. 8.
Динамика формирования купола на поверхности алюминия в процессе воздействия сварочного дугового разряда постоянного тока обратной полярности и измерение топографии сварочного кратера (масштаб – 10 мм).
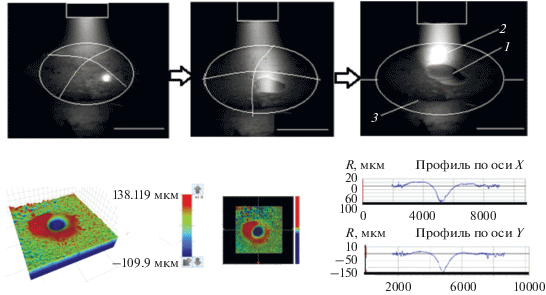
На рис. 9 представлены результаты анализа осциллограмм, полученных в динамическом режиме горения сварочной дуги постоянного тока обратной полярности на поверхности алюминия. Согласно работам А. Андерса, в частности [34], напряжение дуги является параметром, который показывает мгновенные изменения энергетического состояния дугового разряда, тогда как ток изменяется относительно плавно, так как он определяется полным сопротивлением цепи. Анализ напряжения сопоставлялся с результатами изменения топографии поверхности по данным скоростной камеры. Это позволило определить ряд особенностей взаимодействия сварочной дуги с поверхностью. При токах от 10 до 100 А, скорости перемещения образца 3.3 мм/м и постоянстве других параметров зафиксировано несколько стадий горения дуги. В области малых токов (от 10 до 30 А) сварочная ванна не образуется. При этом в отдельные моменты времени фиксируются всплески напряжения (рис. 9а, 9б), которые соотносятся с образованием ярко выраженного микропятна оплавления на поверхности алюминия. Начальная стадия привязки малоамперной дуги на поверхности алюминия характеризуется повышенным напряжением, что связано с быстрым перемещением катодных пятен по большей площади и, как следствие, удлинением дуги. Далее процесс стабилизируется в пределах пятна нагрева с диаметром, соответствующим соплу сварочной горелки.
Рис. 9.
Осциллограммы напряжения в процессе воздействия сварочного дугового разряда постоянного тока обратной полярности при v = 3.3 мм/с и различных значениях тока и длины дуги: (а) – I = 10 А, L = 5 мм; (б) – 20, 5; (в) – 40, 5; (г) – 80, 5; (д) – 100, 5; (е) – 40, 2; (ж) – 60, 2; (з) – 90, 6.
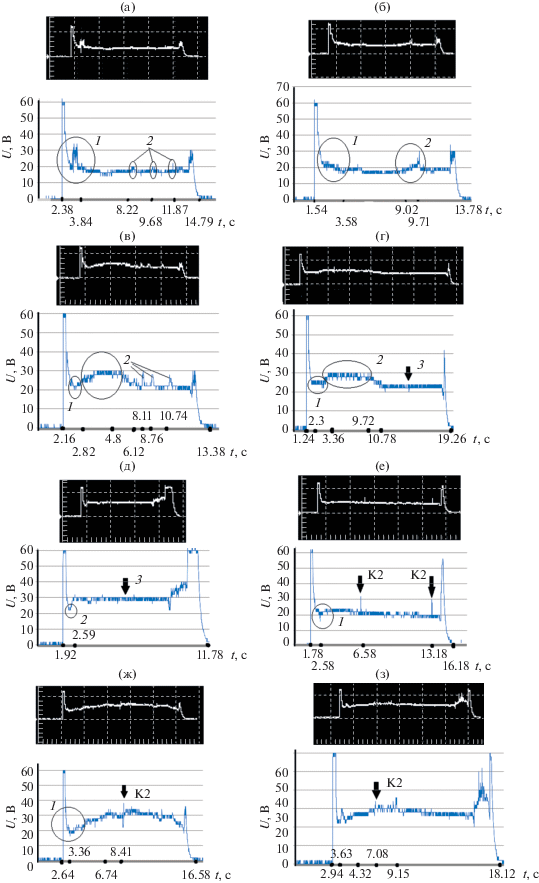
В диапазоне токов 40–80 А также присутствует стадия привязки (рис. 3а), которая по длительности времени уменьшается, и далее следует нарастание напряжения до образования небольшого объема сварочной ванны. В дальнейшем режим горения дуги изменяется, сварочная ванна исчезает, и на поверхности остаются быстро перемещающиеся катодные пятна, которые в хаотичном порядке оплавляют большую площадь поверхности. В отдельных случаях фиксируется всплеск напряжения с образованием медленного катодного пятна на осциллограммах (рис. 9в, 9г). При токе 100 А (рис. 9д) видно, что сразу образуется неподвижное катодное пятно диаметром 1–2 мм. Далее наблюдается повышение напряжения до образования ванны расплава, и в дальнейшем фиксируется устойчивая сварочная ванна. При уменьшении длины дуги до 2 мм можно четко фиксировать образование неподвижных катодных пятен по характерному всплеску напряжения (К2 на рис. 9е–9з).
На осциллограмме рис. 9е при силе тока 40 А сварочная ванна не образуется, хотя длина дугового промежутка составляет 2 мм. Поверхность алюминия переплавлена в хаотичном порядке быстрым перемещением катодных пятен по большей площади поверхности. В отдельные моменты зафиксировано образование неподвижного пятна (К2). Осциллограмма на рис. 9ж показывает стационарный режим горения дуги со стадией привязки и нарастанием напряжения до сварочной ванны с образованием неподвижного катодного пятна. Динамический режим показан на рис. 9ж при токе 90 А. На стадии привязки сразу образовалось неподвижное катодное пятно и стало расти (контрагированная привязка), потом распалось (напряжение снизилось, и наступила стадия действия быстрых катодных пятен). Далее напряжение стало возрастать, момент образования сварочной ванны зафиксирован всплеском напряжения К2 с образованием неподвижного катодного пятна. Затем оно распалось, а ванна исчезла, и на поверхности возникли быстро перемещающиеся катодные пятна.
ОБСУЖДЕНИЕ РЕЗУЛЬТАТОВ
Представленные результаты показывают, что принятый в теории сварочных процессов по аналогии с вакуумным разрядом механизм разрушения оксидной пленки путем катодного распыления (очистки) не отражает реально протекающих физических процессов.
Во-первых, необходимо отказаться от использования неточного термина “очистка” поверхности, как не соответствующего действительности. Происходит переплавление поверхности алюминия (вместе с оксидной пленкой) катодными пятнами в хаотическом порядке. На рис. 1 и снимке 3 рис. 3 это четко видно. Поверхность алюминия содержит участки с высокой (запредельной) шероховатостью и состоит из отдельных участков расплавленного металла с продуктами конденсации. Проведен также дополнительный эксперимент. В режиме малых токов 10–20 А на постоянном токе обратной полярности была обработана поверхность алюминия с характерной топографией, как на рис. 1 (снимки 1, 9). Таким образом, по мнению сторонников традиционного механизма, была очищена поверхность от оксидной пленки. Далее возбуждалась сварочная дуга постоянного тока прямой полярности с силой тока 100 А (длина дуги – 2 мм, расход защитного газа – 12 л/мин) для получения чистой сварочной ванны. Дуга поджигалась, но ванна не формировалась, так как покрывалась оксидной пленкой. В процесс горения дуги сварочный разряд постоянно прерывался и переходил в искровую форму (так как включался блок поджига дуги). Были опробованы импульсные режимы сварки на постоянном токе прямой полярности с силой тока в импульсе 150 А – эффекта образования чистой сварочной ванны нет, поскольку продолжает формироваться оксидная пленка, которая покрывает оплавленную поверхность. В этом отношении можно привести другой аргумент – это лазерная очистка (laser cleaning), которая более точно соотносится с физикой процесса [35]. Существует три механизма лазерного удаления оксидных слоев с металлических подложек: термическая абляция, механическое воздействие и их комбинация. Удаление органических загрязнений основано на испарении загрязняющих веществ, поэтому не ожидается значительного теплового воздействия на подложку. Однако для удаления оксидного слоя взаимодействие между лазерным лучом и оксидным слоем может генерировать достаточные тепловые эффекты, чтобы вызвать дополнительное термическое окисление или даже плавление тонкого слоя поверхности. Такой тепловой эффект зависит от ряда факторов: длины волны лазерного луча, ширины импульса, длительности импульса, толщины оксидных слоев, природы оксидных слоев, а также материалов подложки.
В работе [36] представлены электронные фотографии поверхности сплава AA7024-T4, полученные в ходе лазерной очистки при плотностях мощности лазерного излучения 3.5, 5.7, 7.1, 8.5, 11.3 Дж/см2 (лазерная очистка проводилась с помощью волоконного лазера ALT-LC-NP-500 с диодной накачкой, длиной волны 1064 нм, длительностью импульса 10 нс и частотой повторения 10 кГц в окружающей атмосфере). Начиная с плотности мощности 7.1 Дж/см2, очищенная поверхность была частично расплавлена. В то же время авторы отмечают, что с увеличением плотности мощности более 7.1 Дж/см2 толщина слоя с высоким содержанием кислорода была менее 100 нм и все еще содержала магний, хотя его содержание было значительно снижено. Соединение MgAl2O4 было идентифицировано, поскольку присутствовали все пики спектральных характеристик Mg2s, Al2s и O1s. Концентрации Mg, Al и O в ат. % составляли 57.85%, 36.66% и 5.49% соответственно. Поскольку MgAl2O4 представляет атомное соотношение Mg : Al : O как 1 : 2 : 4, наиболее вероятно, что весь алюминий связан с образованием MgAl2O4, и избыточное количество магния и кислорода может быть связано с образованием других соединений. Дальнейшее увеличение плотности мощности до 11.3 Дж/см2 привело к полностью расплавленным поверхностям образцов алюминия с типичной волнистой структурой затвердевания, характерной для сварочных процессов. Представленную в [36], как и в других работах по лазерной очистке, топографию лазерной поверхности с небольшой волнистостью в диапазоне плотности мощности лазерного излучения 7–15 Дж/см2 даже в первом приближении нельзя сравнить с искореженной поверхностью алюминия, получаемой после обработки катодными пятнами на рис. 1–3. Это совершенно разные механизмы воздействия на поверхность алюминия по конечному результату.
Во-вторых, необходимо отметить, что никакого “глобального распыления” поверхностной оксидной пленки до образования чистой поверхности алюминия катодными пятнами, как утверждают сторонники механизма катодного распыления, не происходит. Это хорошо видно на рис. 1 и особенно на снимках 1–3 рис. 6. Быстро перемещающимися катодными пятнами можно долго воздействовать на поверхность алюминия, но сварочная ванна при этом образовываться не будет. Отсюда следует, что в условиях сварочной дуги при сварке алюминия постоянным током обратной полярности катодные пятна играют важную роль, но не главную. При этом необходимо внести изменения в терминологию катодных пятен применительно к поверхности алюминия, так как существующая градации пятен [27] имеет неопределенность. Быстро перемещающиеся катодные пятна оставляют грубую переплавленную поверхность алюминия (рис. 3, снимки 3, 4) без образования сварочной ванны. Это противоречит градации пятен [27]. Медленно перемещающиеся катодные пятна (относительно указанных выше) вызывают появление на поверхности характерного (с геометрическими размерами) расплавленного следа. Поверхность металла в площади следа имеет специфическую топографию (рис. 2–4). Ширина следа соотносится с диаметром катодного пятна при условии, что пятно имеет форму круга.
Впервые зафиксировано образование квадратного одиночного кратера (рис. 2, снимок 3), который, по всей видимости, можно отнести к автографу катодного пятна. Механизм его образования в виде квадрата не известен.
Еще один зафиксированный тип пятна – неподвижное большое пятно с диаметром в начале формирования 1–2 мм и в конце существования 3–6 мм (рис. 7д). Возможно, это группа пятен, дальнейшие более точные исследования позволят это установить. Только с появлением этого типа пятна на поверхности алюминия начинает формироваться сварочная ванна. При этом в момент ее формирования частота появления быстро перемещающихся катодных пятен снижается, и к концу процесса образования сварочной ванны они исчезают совсем. Анализ осциллограмм напряжения (рис. 9) показывает две стадии горения дуги на поверхности алюминия, отличающиеся величиной напряжения, которая зависит от давления газа, длины дуги и тока разряда. В режиме быстро перемещающихся катодных пятен напряжение на дуге минимальное, при неподвижном пятне оно максимальное. В последнем случае происходит интенсивное испарение, что хорошо видно на рис. 6–8. Отличие в терминах “испарение” и “распыление” заключается в том, что в первом случае переход материала (в данном случае алюминия) в газовую фазу происходит под воздействием тепловой энергии, получаемой от катодного пятна. При распылении атомы выбиваются с поверхности алюминия за счет кинетической энергии ионами металла из области катодного пятна. Таким образом, основным механизмом формирования сварочной ванны при сварке постоянным током обратной полярности является испарение.
Отметим некоторые особенности скорости перемещения быстрых пятен, полученные при изучении катодного следа (снимок 9 на рис. 1 и рис. 2–4). Время жизни катодного пятна составляет порядка 20–40 мкс, после чего пятно гаснет, и рядом может появиться новое пятно, возможно, до погасания предыдущего. Пятно за время своей жизни может иметь катодный факел, а может быть просто точечным объектом на поверхности алюминия. В результате гашения и возникновения рядом новых пятен создается впечатление, что пятно движется. Однако явно выраженные следы оплавления поверхности отсутствуют. Более того, на покадровой съемке скоростной камеры в большинстве случаев видно пятно в одном цвете (белом), которое не имеет каких-либо классифицирующих признаков (размер, внутреннюю структуру, оттенок цвета и т.д.). Поэтому, когда оно перемещается и не оставляет на поверхности алюминия характерного следа, нельзя сказать, что это одно и то же пятно, а следовательно, не корректно по нему определять скорость. В данном исследовании они идентифицированы как быстро перемещающиеся катодные пятна, но с учетом приведенного детального анализа более корректно (пока не доказано другое) называть такие катодные пятна точечными или короткоживущими. Медленно движущиеся катодные пятна оставляют на поверхности характерный след (рис. 2–4). Время их существования по сравнению с короткоживущими велико. Их движение состоит из двух этапов – ускоренного и инерционного. Ускоренное движение началось от места возникновения (рис. 2, снимок 6) до остановки (рис. 2, снимок 5). Далее оно качнулось и погасло, что-то помешало двигаться дальше. При этом если на участке ускоренного движения от места привязки до остановки видны четкие микрократеры и углубления, то на участке инерционного движения количество кратеров становится меньше и плотность их распределения уменьшается (рис. 3, снимок 5). Относительная равномерность микрократеров и углублений на всем протяжении и в площади следа позволяет выдвинуть две гипотезы их происхождения.
Первая – это подпленочное кипение [2], протекающее за счет тепла, выделяемого из катодного пятна, при низкой температуре плавления алюминия. Пока неясным остается распределение тепла в катодном пятне, так как топография следа показывает множество локальных микроисточников тепла в пятне с формированием микрократеров. Другим моментом является само движение пятна с такими локальными микроисточниками, поскольку при движении должен оставаться смазанный след. В качестве аналога можно привести пример с лейкой. Если из лейки в течение 1–2 с поливать песок, возникнут равномерно распределенные точечные углубления. При движении лейки точки перейдут в линии (бороздки). Однако на представленных фото (рис. 2–4) по ходу движения катодного пятна не зафиксированы бороздки, смазанность или размытость следа. В настоящее время такую поверхность с относительно равномерным распределением микрократеров и углублений можно получить на металле роликом для накатки. Это позволяет выдвинуть нетривиальную гипотезу о вращении внутренней структуры наподобие накатного ролика в катодном пятне, или что само пятно вращается. Тогда можно объяснить топографию полученного следа.
Представленная гипотеза о происхождении следа не претендует на точное физическое обоснование, а является лишь попыткой из логики полученного экспериментального факта объяснить топографию поверхности в площади следа. Однако в случае квадратного кратера (рис. 2, снимок 3), образовавшегося в следе, у автора нет никакого объяснения, как он возникает.
Рассмотрим механизм формирования купола в пятне воздействия сварочной дуги с поверхностью алюминия. Пленка оксида алюминия при равномерном нагреве в печи в интервале температур до 780 К сохраняет свою сплошность, несмотря на различие коэффициентов термического расширения пленки и металла. Нагрев до 870 К показывает образование складок и отсутствие трещин и надрывов. Поверхностная пленка обладает пластичностью и способна растягиваться и сжиматься. Эффект куполообразования на поверхности металлов, имеющих оксидные пленки, не является чем-то уникальным, он описан в работах по лазерной абляции металлов фемто- и наносекудными импульсами. Складчатые поверхности так же рассмотрены в этих работах, как и интенсивное порообразование в поверхностном слое металлов. Причины возникновения связаны с высокой плотностью теплового воздействия, резкого градиента температур и напряжений на границе раздела оксидная пленка–металл. Большой градиент температуры вблизи нагреваемой поверхности до начала плавления возникает вследствие отвода тепла вглубь слоя за счет теплопроводности. Есть еще один механизм образования купола, который не связан с локальным нагревом и градиентом температур и напряжений. Водород может облегчить отделение защитного оксидного слоя от металлов и сплавов [37]. Известно, что пленка трехводного гидрата окиси алюминия (гидрогенит) содержит около 34.6% влаги [3]. Вероятные источники водорода при сварке алюминия проанализированы в работе [3]. Из всех источников водорода автор выделил как самый опасный – водород, находящийся в оксидной пленке. При сварке в процессе мгновенного нагрева большая часть влаги, входящей в состав гидрогенита, успевает реагировать с металлом алюминия с выделением водорода. Водород является единственным газом со значительной растворимостью в расплавленном алюминии. Для чистого алюминия при температуре плавления 660°С и 1 атм растворимость водорода находится в диапазоне 0.67–0.77 мл на 100 г в жидкости и около 0.035 в твердом состоянии [3]. Кроме того, компоненты сплава АМг будут влиять на растворимость водорода в алюминии: например, добавление магния до 6% почти удваивает растворимость водорода в алюминии [3].
Авторы [37, 38] провели исследование, нагревая гидрогенизированный алюминий внутри просвечивающего электронного микроскопа (все это снято на видео в режиме реального времени), и показали, что воздействие водорода всего за несколько минут может значительно ухудшить целостность высокотемпературной поверхности раздела металл–оксид. Кроме того, существует критическая температура ∼150°C, выше которой рост полостей на границе раздела металл–оксид переходит в усадку с последующим образованием нескольких гигантских полостей. Пересыщение вакансий, активация дальнего диффузионного пути вдоль оторванной границы раздела и диссоциация водородно-вакансионных комплексов являются критическими факторами, влияющими на это поведение. Повреждение водородом пассивированных металлических поверхностей при высоких температурах можно представить как четырехступенчатый процесс [37, 38].
Результаты [37, 38] показали, что образование пузырей Н связано с вакансиями и пустотами. Такой физический механизм типичен для образования пузырей H в большинстве металлов. Авторы отмечают, что, хотя эти изменения активно протекают под поверхностным оксидным слоем, они не вызывают каких-либо явных изменений в морфологии внешней поверхности пленки. Следовательно, эти полости могут не проходить обычную оптическую или SEM-проверку и могут представлять значительную угрозу надежности материала, например отслоение оксида от лопаток турбины или ускоренная коррозия. Эти исследования важны тем, что показывают отслоенные области, которые могут существовать на поверхности алюминия, а воздействие сварочной дуги только интенсифицирует этот процесс. Воздействие водорода может сильно подорвать целостность границы раздела металл–оксид при повышенной температуре. Потеря целостности сопровождается образованием гигантских полостей на границе раздела оксидная пленка–алюминий. Быстро возникающие точечные катодные пятна пробивают отслоившуюся пленку или создают условия для ее отслоения под действием градиента температур, напряжений и водорода. В дальнейшем, по мере охвата большей поверхности, эти пятна нагревают поверхность алюминия до температуры плавления. Тогда, как только возникла жидкая фаза алюминия, образуется неподвижное катодное пятно, которое возникает не на поверхности оксида алюминия, а на границе раздела твердая пленка–жидкая фаза.
Эффект стабилизации катодного пятна на границе раздела жидкой и твердой фаз хорошо известен [23–27]. Необходимо напомнить [3], что сплавы алюминия – это бинарные сплавы и в зависимости от основного легирующего элемента (медь, марганец, магний и т.д.) имеют различную температуру плавления, а некоторые имеют области жидкой и твердой фаз. Дополнительным фактом возникновения и стабилизации катодного пятна на границе раздела может служить низкая работа выхода магния, имеющегося в составе сплава АМг-6, по сравнению с алюминием – 3.67 и 4.2 эВ соответственно. Высокая плотность теплового потока в неподвижном катодном пятне не успевает отводиться в объем металла теплопроводностью, и образуется жидкая ванна, которая из-за усадки и высокой жидкотекучести алюминия как бы проваливается под пленку, что создает эффект купола. Пленка нависает над сварочной ванной. Как только образовалась сварочная ванна, неподвижное катодное пятно исчезает, и сварочный разряд переходит в диффузный режим горения сварочной дуги, который характеризуется однородным распределением электрического поля по площади сварочной ванны и по длине разрядного промежутка с низким падением потенциала и занимает практически весь межэлектродный зазор.
В заключение необходимо отметить факт, на который не обращают внимания технологи, но который активно используется при продаже сварочного оборудования для сварки алюминия, – так называемую большую зону очистки от оксидной пленки, которая фактически выглядит как на рис. 5, снимок 1. На самом деле такую поверхность необходимо рассматривать как технологический дефект типа подреза, который считается недопустимым дефектом при сварке черных металлов. В работе [39] зафиксированы образование микротрещин в зонах дополнительной “очистки” алюминия при сварке алюминиевого сплава А1050 и снижение усталостной прочности в этих зонах по сравнению с основным металлом.
Таким образом, проведенные исследования позволяют утверждать, что при сварке алюминиевых сплавов постоянным током обратной полярности взаимодействие сварочной дуги с поверхностью алюминия происходит по новому механизму, предложенному выше. Существующая в настоящий момент концепция катодного распыления оксидной пленки с дальнейшим формированием сварочной ванны оказалась неверной и не соответствует экспериментальным фактам, приведенным в данной работе. Конечно, многие поднятые вопросы требуют дополнительных экспериментальных исследований по уточнению и детализации нового механизма взаимодействия сварочной дуги с поверхностью алюминия.
ЗАКЛЮЧЕНИЕ
Установлено, что при сварке алюминия постоянным током обратной полярности сварочная дуга горит в парах интенсивно испаряющегося алюминия. Концепция распыления алюминия катодными пятнами с последующим формированием сварочной ванны не соответствует реальным физическим процессам, протекающим на поверхности алюминия.
Показано, что в диапазоне малых токов взаимодействие сварочной дуги с поверхностью алюминия протекает в два этапа. На первом этапе быстро возникающие точечные катодные пятна испаряют оксидную пленку в хаотическом порядке, нагревая тем самым тонкий слой алюминия до температуры плавления. На втором этапе в месте появления жидкой фазы алюминия возникает неподвижное катодное пятно, которое начинает увеличиваться в диаметре, интенсивно испарять оксидную пленку и формировать ванну жидкого расплава. В диапазоне больших токов неподвижное катодное пятно образуется сразу в момент поджига, и из-за высокой плотности теплового потока, поступающего в алюминий из области катодного пятна, возникает сварочная ванна.
Список литературы
Балановский А.Е. Исследование искровой стадии привязки сварочного дугового разряда на поверхности алюминия // ТВТ. 2018. Т. 56. № 3. С. 329.
Балановский А.Е. Исследование стадии привязки сварочного дугового разряда постоянного тока прямой полярности на поверхности алюминия // ТВТ. 2018. Т. 56. № 4. С. 503.
Никифоров Г.Д. Металлургия сварки плавлением алюминиевых сплавов. М.: Машиностроение, 1972. 264 с.
Mathers G. The Welding of Aluminium and Its Alloys. Cambridge: Woodhead Publ. Ltd., 2002. 242 p.
Sarrafi R., Kovacevic R. Cathodic Cleaning of Oxides from Aluminum Surface by Variable-polarity Arc // Welding J. 2010. V. 89. P. 1.
Абралов М.А. Аргонодуговая сварка алюминиевых сплавов. Ташкент: Фан, 1989. 232 с.
Юсуфова З.А., Лесков Г.И. К вопросу о механизме разрушения окисных плен при сварке алюминиевых сплавов в среде инертных газов // Сварочное производство. 1970. № 7. С. 57.
Будник В.П., Рабкин Д.М., Смиян О.Д., Товмаченко В.Н. Термическое разрушение окисной пленки при сварке алюминия // Автоматическая сварка. 1975. № 10. С. 74.
Будник В.П. Влияние вида инертного газа на температуру ванны и разрушение оксидной пленки при сварке алюминия // Автоматическая сварка. 1994. № 12. С. 23.
Sarrafi R., Kovacevic R. Real-time Observation of Cathodic Cleaning During Variable-polarity Gas Tungsten Arc Welding of Aluminium Alloy // Proc. Institution of Mechanical Engineers. Part B: J. Eng. Manufacture. 2009. V. 223. P. 1143.
Shi Z., Yuan Q., Zhao R. et al. The Influence of Protection Gas Pressure on the Descaling Process of Vacuum Arc in Removing Oxide Layer on Metal Surface // IEEE Trans. Plasma Sci. 2011. V. 39. № 7. P. 1585.
Takeda K., Takeuchi S. Removal of Oxide Layer on Metal Surface by Vacuum Arc // Mater. Trans. JIM. 1997. V. 38. № 7. P. 636.
Saito M., Tobe S., Iwao T., Inaba T. Effect of Pressure on Surface Roughness Treated by Cathode Spots of Low Pressure Arc // 22nd Int. Symp. on Discharges and Electrical Insulation in Vacuum (ISDEIV). Matsue, 2006. P. 550.
Shi Z., Li W., Yan N., Zhang Y. et al. Experimental Investigation on the Effect of Vacuum Arc on Removing Oxide Layer on Metal-tube Surface in a Transverse Magnetic Field // 25th Int. Symp. on Discharges and Electrical Insulation in Vacuum (ISDEIV). Tomsk, 2012. P. 293.
Tang Z., Wu R., Yang S. et al. Interaction between Arc Spot Plasma and Steel Surface in Descaling // IEEE Trans. Plasma Sci. 2015. V. 43. № 5. P. 1793.
Tang Z.L., Yang K., Liu H.X. et al. Dynamics of Cathode Spots in Low-pressure Arc Plasma Removing Oxide Layer on Steel Surfaces // Phys. Plasmas. 2016. V. 23. № 3. P. 033501-1.
Takeda K., Sugimoto M. Surface Modification by Cathode Spots of a Vacuum Arc // IEEE Trans. Plasma Sci. 2001. V. 29. № 5. P. 718.
Li W., Shi Z., Wang C. et al. The Motion Characteristics of a Single Cathode Spot in Removing Oxide Layer on Metal Surface by Vacuum Arc // IEEE Trans. Plasma Sci. 2017. V. 45. № 1. P. 106.
Kamishima S., Iwao T., Yumoto M. Split Process of Low-pressure Arc Cathode Spots on SS400 (Fe + C) Surface with Oxide Layer // IEEJ Trans. Electr. Electron. Eng. 2010. V. 5. № 6. P. 670.
Sato A., Iwao T., Yumoto M. Cathode Spot Movement of a Low-pressure Arc for Removing Oxide Layer // IEEE Trans. Plasma Sci. 2007. V. 35. № 4. P. 1004.
Takeda K. Dry Cleaning of Metal Surfaces by a Vacuum Arc // Surf. Coat. Technol. 2000. V. 131. № 1–3. P. 234.
Shi Z., Wang S.J.L., Yuan Q., Song X. Experimental Investigation on the Motion of Cathode Spots in Removing Oxide Film on Metal Surface by Vacuum Arc // J. Phys. D: Appl. Phys. 2008. V. 41. № 17. P. 175 209.
Месяц Г.А. Эктоны в вакуумном разряде: пробой, искра, дуга. М.: Наука, 2000. 424 с.
Toru Iwao, Yoshihiro Inagaki, Motoshige Yumoto. Smooth Surface Treated by Low-pressure Arc Discharge // Vacuum. 2006. V. 80. № 11–12. P. 1284.
Раховский В.И. Физические основы коммутации электрического тока в вакууме. М.: Наука, 1970. 536 с.
Вакуумные дуги. Теория и приложения / Под ред. Лафферти Дж. М.: Мир, 1982. 432 с.
Любимов Г.А., Раховский В.И. Катодное пятно вакуумной дуги // УФН. 1978. Т. 125. № 4. С. 665.
Tashiro S., Sawato H., Tanaka M. Experimental Observation of Cleaning Action of Cathode Spots in AC TIG Welding of Aluminum Plates // Trans. JWRI. 2010. V. 39. № 2. P. 180.
Ленивкин В.А., Дюргеров Н.Г., Сагиров Х.Н. Технологические свойства сварочной дуги в защитных газах. М.: Машиностроение, 1989. 264 с.
Лапин И.Е., Косович В.А., Савинов А.В. Об устойчивости дуги при сварке неплавящимся электродом тонколистового алюминия и его сплавов // Сварочное производство. 1996. № 10. С. 17.
Lei Zhao, Qiang Wang, Guan Yingchun, Bao Qiang Cong. Analysis and Comparison of Aluminum Alloy Welded Joints between Metal Inert Gas Welding and Tungsten Inert Gas Welding // Surface Rev. Lett. 2015. V. 22. № 6. P. 1550079-1.
Балановский А.Е. Возможности цифровой визуализации процесса нагрева и плавления металла при дуговом разряде с неплавящимся электродом // Сварочное производство. 2016. № 6. С. 31.
Балановский А.Е. Визуализация процесса нагрева и плавления металла в анодной области при дуговом разряде с неплавящимся электродом // ТВТ. 2016. Т. 54. № 5. С. 663.
Ros J., Anders A. Time and Material Dependence of the Voltage Noise Generated by Cathodic Vacuum Arcs // J. Phys. D: Appl. Phys. 2008. V. 38. P. 4184.
Wang Qiang, Guan Yingchun, Cong Baoqiang, Qi Bojin. Laser Cleaning of Commercial Al Alloy Surface for Tungsten Inert Gas Welding // J. Laser Appl. 2016. V. 28. P. 022507.
Dimogerontakis T., Oltra R., Heintz O. Thermal Oxidation Induced During Laser Cleaning of an Aluminium-Magnesium Alloy // Appl. Phys. A. 2005. V. 81. № 6. P. 1173.
Li Meng, Xie De-Gang, Ma Evan, Li Ju, Zhang Xi-Xiang, Shan Zhi-Wei. Effect of Hydrogen on the Integrity of Aluminium–Oxide Interface at Elevated Temperatures // Nat. Commun. 2017. V. 8. P. 14564.
De-Gang Xie, Zhang-Jie Wang, Jun Sun, Ju Li, Evan Ma, Zhi-Wei Shan. In Situ Study of the Initiation of Hydrogen Bubbles at the Aluminium Metal/Oxide Interface // Nature Materials. 2015. V. 14. P. 10.1038.
Katoh M., Nishio K., Yamaguchi T., Mukae S. Micro-cracks in Aluminium Alloys Developed in the Cleaning Action Region // Welding International. 1995. V. 9. № 5. P. 360.
Дополнительные материалы отсутствуют.
Инструменты
Теплофизика высоких температур