Теплофизика высоких температур, 2020, T. 58, № 4, стр. 634-640
Термодинамика расплавов в основе технологии переработки богатейших редкометальных руд томторского месторождения
Л. М. Делицын 1, *, В. М. Батенин 1, **
1 ФГБУН Объединенный институт высоких температур РАН
Москва, Россия
* E-mail: delitzin@ihed.ras.ru
** E-mail: vbat6@mail.ru
Поступила в редакцию 03.03.2020
После доработки 16.03.2020
Принята к публикации 30.03.2020
Аннотация
Предложено объяснение причин распада сложного поликомпонентного фосфатно-силикатного расплава, содержащего оксиды редкоземельных элементов (TR2O3) и тяжелые металлы (Nb, Ta, Zr), на два равновесных конденсированных расплава с контрастным распределением компонентов между ними. Каждый из расплавов представляет собой новый тип искусственного сырья для получения редкоземельных и тяжелых металлов. Реализация данного процесса позволяет вовлечь в промышленное использование богатейшее Томторское месторождение редкометальных руд, переработка которых практически невозможна освоенными в настоящее время способами.
ВВЕДЕНИЕ
Ликвационная11 модель широко используется при изучении процессов формирования рудных образований, возникающих при дифференциации магматических расплавов [1].
Явление ликвации расплавов в простых двухкомпонентных системах MeO–SiO2 зафиксировано И.В. Грейгом в 20-е годы ХХ в. Экспериментально показано, что системы MeO–SiO2 характеризуются широкими областями ликвации расплавов при температуре 1693°С. Причем сам акт фазового распада на две жидкие фазы протекает с очень большой скоростью. Попытки объяснить механизм фазового ликвационного распада расплавов с позиций их структуры, начатые еще в 1940–50 гг. с публикации работ У. Уоррена и А. Пинкуса, Е. Левина и С. Блока, В. Вейля, Ф. Глассера, И. Варшау и Р. Роя и др., были обобщены в [2–4]. Основной причиной ликвации расплавов считалось стремление стеклообразователя и модификатора образовать катион-кислородные координационные полиэдры. При их сходстве по форме и размерам несмешиваемость не наступает. Если же такого сходства нет, то в зависимости от относительной силы связи конкурирующих катионов либо возникает несмешиваемость, либо расплав переходит в нестабильное состояние и линия ликвидуса приобретает S-образный характер. В этом случае ниже линии ликвидуса в закаленных стеклах формируется метастабильная ликвация, но это уже совсем другая задача, относящаяся к стеклообразному состоянию, где все процессы протекают при высокой вязкости матрицы, а размеры сосуществующих фаз имеют порядок микрон.
Позднее в [2] было показано, что первичной причиной возникновения несмешиваемости расплавов следует считать электростатическое силовое взаимодействие между ионами расплава, которое вызывает стремление двух различных катионов организовать вокруг себя самостоятельные кислородные полиэдры. Для наступления фазового разделения необходимы, во-первых, определенная степень силы взаимодействия катион–кислород, а во-вторых, структурная несовместимость возникающих катион-кислородных группировок, структурная характеристика которых зависит от степени поляризации анионов, т.е. кислорода. В [2] проведено сравнение ширины области ликвации при температуре t0.5, соответствующей 0.5tкр (в градусах Цельсия), с силой поля катионов Z/r 2. Для расчета ширины поля ликвации при t0.5 для 15 систем, в которых установлен купол ликвации и определена верхняя критическая точка, получены уравнения бинодальной кривой ликвации и экстраполированы до t0.5. В обобщенном виде уравнение имеет вид (рис. 1)
Рис. 1.
Зависимость ширины области ликвации расплавов Δ0.5 при t0.5 от силы поля катионов Z/r 2 для систем SiO2–RnOm.
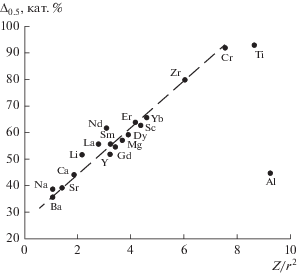
Для сравнения различных оксидов (R2O, RO, R2O3, RO2) ширина области ликвации представлена в катионных процентах. Исключением является система SiO2–Al2O2, что объясняется особенностями координации алюминия. Очевидно, что сила поля катиона является основным фактором, определяющим величину области ликвации в простых силикатных системах.
На прямой рис. 1 редкоземельные оксиды находятся в ее средней части, что допускает возможность ликвационного разделения редких земель и кремнезема в расплавах и для более сложных систем.
Необходимо подчеркнуть, что полученная зависимость имеет эмпирический характер и не дает возможности определить термодинамические параметры ликвации расплавов в случае сложных природных редкоземельно-редкометальных систем. Соответственно, для использования ликвационного механизма в технологических целях приходится обращаться к вопросам взаимной растворимости несмешивающихся расплавов, тем более что уравнение (рис. 1) получено на основании высокотемпературных исследований ликвации расплавов при температурах около 1700°С и для технических целей трудно реализуемо. Для ликвации природного сырья приведенное уравнение лишь указывает на принципиальную возможность осуществления процесса ликвации расплавов.
Целью настоящей статьи является экспериментальное доказательство возможности ликвационной плавки руд Томторского месторождения с контрастным распределением в образующихся несмешивающихся расплавах редкоземельных и тяжелых металлов.
ОБОБЩЕННАЯ ДИАГРАММА ЛИКВАЦИИ РУДНО-СОЛЕВЫХ РАСПЛАВОВ
Введем некоторые ограничения:
1) явление ликвации протекает в области жидкофазного состояния системы;
2) процесс ликвации, т.е. распад гомогенного расплава на несмешивающиеся жидкие фазы, – необратимый;
3) расслоенные расплавы находятся в состоянии равновесия;
4) при охлаждении каждый из сосуществующих расплавов кристаллизуется в соответствии со своим химическим составом;
5) фазы в системе находятся в конденсированном состоянии.
Непременным условием успешного осуществления процесса ликвационной плавки является введение в системы “третьего компонента”, роль которого исключительно велика. Третий компонент вводится в виде специально подбираемых солевых добавок, что приводит при заданных термодинамических параметрах к протеканию промежуточных химических реакций, вызывающих значительное (на сотни градусов) понижение температуры плавления тугоплавких фаз, снижение вязкости силикатных расплавов, образование новых кристаллических фаз. Третий компонент, являясь растворителем для ряда рудных компонентов, экстрагирует их из шихты в процессе ликвационной плавки, в результате чего они концентрируются в солевом расплаве. Комбинируя соотношение солевых и силикатных компонентов в шихте, можно добиться изменения взаимной растворимости жидких фаз для получения продуктивного расплава заданного состава. Стабильность состава сосуществующих расплавов (жидких макрослоев) регулируется составом шихты, температурой и продолжительностью плавки. Для ряда систем (содержащих мышьяк, сурьму и висмут) возникает необходимость контролировать состав газовой фазы в теплоэнергетическом аппарате, где осуществляется процесс ликвационной плавки. В обобщенном виде для конденсированных систем принцип ликвационной плавки схематически описывается диаграммой: силикат (С)–рудный компонент (Р)–третий компонент (ТК) (рис. 2).
Рис. 2.
Диаграмма плавления редкоземельно-редкометального рудного сырья (Р) в присутствии третьего компонента (ТК): a–b, a1–b1, a2–b2 – составы равновесных расплавов; с, d, f – состав исходной шихты; kh – линия постоянного соотношения содержания кремнезема и рудного компонента; Ж1 + Ж2 – область несмесимости (ликвации) расплавов; Ж1 – силикатный расплав, Ж2 – продуктивный (рудно-солевой) расплав; t1 > t2 > t3.
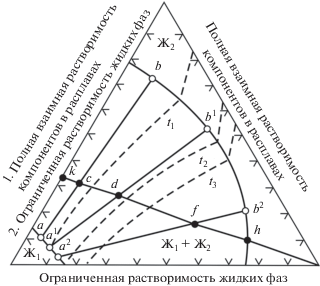
На диаграмме показаны возможные соотношения между компонентами в двойных системах. Причем рудные компоненты и третий компонент (растворитель) полностью взаиморастворимы в области жидкого состояния. Растворители и силикатные расплавы должны обладать ограниченной взаимной растворимостью. С увеличением количества вводимого в шихту растворителя (точки с, d, f) изменяется положение коннод, связывающих составы равновесных жидких фаз (а–b, a1–b1, a2–b2). При этом доля продуктивного солевого расплава увеличивается, а соотношение между силикатными и рудными компонентами остается постоянным (луч kh). Таким образом, диаграмма иллюстрирует процесс экстракции в расплавах, до некоторой степени аналогичный жидкостной экстракции в водно-солевых растворах и органических жидкостях [5]. Растворитель (ТК) после выполненной им работы выводится из системы и возвращается в голову процесса. Из продуктов ликвации осуществляется регенерация вводимого в шихту третьего компонента, который постоянно находится в обороте. Технологические потери растворителя не должны превышать 5%.
В этой связи рассмотрим фторидно-силикaтную систему SiO2–NaF (рис. 3, нижняя часть). Система SiO2–NaF наиболее простая среди двойных фтор-силикатных систем. Если в системах с оксидами происходит борьба за кислород между модификатором и стеклообразователем, то в SiO2–NaF происходит борьба между катионами за кислород и фтор в связи с чем процесс ликвации становится намного более сложным, чем в простых оксидных системах. Система SiO2–NaF осложнена рядом химических реакций, сопровождающихся образованием кремнефторида натрия и дисиликата натрия, что установлено методом микродифракции. На ее сложность указывает также S-образный характер верхней части линии ликвидуса (рис. 3). Соответственно, она относится к взаимным системам. На рис. 3: 1L – один расплав, Lsi – силикатный расплав, Lф – фосфатно-солевой, LF – фторидно-солевой расплав.
Рис. 3.
Диаграмма плавкости пирохлор-монацитовой руды: верхняя часть диаграммы – изотермы ликвации расплавов при 850–1200°С, нижняя часть – система SiO2–NaF.

Реакция между SiO2 и NaF может быть представлена в виде уравнения со стехиометрическими коэффициентами:
(1)
$6{\text{Si}}{{{\text{O}}}_{2}} + 2{\text{NaF}} \to {\text{S}}{{{\text{i}}}_{4}}{{{\text{O}}}_{7}}{{{\text{F}}}_{2}} + {\text{N}}{{{\text{a}}}_{2}}{\text{S}}{{{\text{i}}}_{2}}{{{\text{O}}}_{5}}.$В результате один атом мостикового кислорода в кремнекислородном тетраэдре замещается фтором, и простейшей трехмерной взаимосвязанной структурой, где все атомы кислорода мостиковые, является комплекс Si4O7F2. Одновременно происходит стабилизация такой структурной единицы, как ${\text{S}}{{{\text{i}}}_{2}}{\text{O}}_{5}^{{2 - }},$ которая по стехиометрическим соображениям балансируется как дисиликат натрия. Эта же реакция вызывает повышение щелочности силикатной жидкости. Фтор в данном случае действует в качестве деполимеризатора силикатного расплава, что приводит к значительному снижению температуры плавления кремнезема и появлению низкотемпературных силикатных жидкостей. Образование же в системе SiO2–NaF широкого поля двух несмешивающихся расплавов – силикатного и фторидного – свидетельствует о распределении фтора между двумя жидкими фазами и о двойственном механизме его растворимости, который заключается, согласно реакции (1), в замещении в силикатной сетке ~17% кислорода фтором, что вызывает частичную деполимеризацию силикатного расплава. Избыток фтора сверх 17% приводит к образованию прочного фторидного комплекса, связанного с такими металлическими катионами, как натрий. В итоге получаются два несмешивающихся расплава (силикатный и фторидный), каждый из которых является растворителем для соответствующих компонентов.
ЛИКВАЦИЯ РЕДКОЗЕМЕЛЬНО-РЕДКОМЕТАЛЬНЫХ РУД
В процессе ликвации редкоземельно-редкометальной руды с введением в шихту фторида натрия щелочно-фторидный комплекс является растворителем фосфатов редких земель, тогда как силикатный расплав является растворителем оксидов Nb, Ta, Zr, Fe, Al. Экспериментально установлено, что ортофосфаты редких земель с фторидом натрия полностью растворяются друг в друге в расплавленном состоянии [6, 7]. На рис. 3 представлены диаграмма плавкости пирохлор-монацитовой руды Томторского месторождения с фторидом натрия и положение областей ликвации для пяти изотермических сечений.
С возрастанием температуры до 1200°С ширина области ликвации увеличивается. Положения верхней критической точки, когда наступает гомогенное состояние расплава, достичь в условиях проведения экспериментов невозможно, поскольку упругость пара фторида натрия после 1200°С начинает увеличиваться и равновесия смещаются в область иных составов.
На рис. 4 показаны образцы ликвации богатой и рядовой фосфатно-редкоземельно-редкометальной руды в присутствии фторида натрия при температуре 1200°С в течение 1 ч. Расплавы очень четко разделяются друг от друга по плоской границе раздела фаз.
Рис. 4.
Ликвация расплава богатой монацит-пирохлоровой (а) и рядовой монацит-пирохлор-крандаллитовой (б) руд Томторского месторождения: верхний слой – силикатный расплав, нижний – фосфатно-солевой расплав; 1200°С, 1 ч.
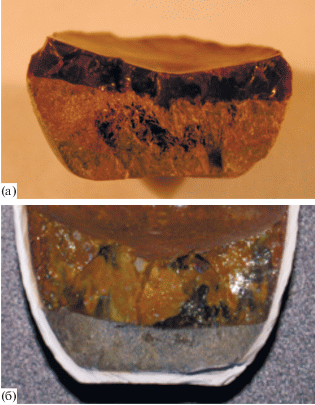
Особенностью ликвации расплавов является присутствие в силикатном расплаве мелких капель-шариков фосфатного расплава (рис. 5), а в фосфатном расплаве – мелких шариков силикатного расплава (рис. 6). По химическому и фазовому составу фосфатные капли-шарики отвечают фосфатно-солевому расплаву, силикатные шарики – силикатному.
Рис. 6.
Силикатные капли-шарики (черные) в фосфатно-солевой кристаллической матрице, диаметр шариков ≤20–50 мкм.
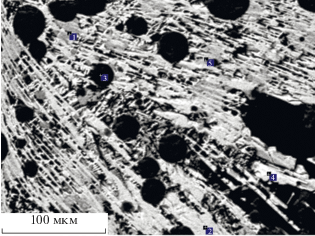
В табл. 1 показано содержание основных компонентов в несмешивающихся расплавах для пирохлор-монацитовых руд, коэффициенты распределения компонентов в каждом из слоев и извлечение компонентов. Данные в табл. 1 показывают контрастность распределения компонентов между расплавами, а также низкую взаимную растворимость расплавов. Об этом же свидетельствует и извлечение компонентов в расплавы.
Таблица 1.
Состав фосфатно-солевого и силикатного расплавов и извлечение компонентов (ε, %) в расплавы
Компоненты | Руда | Шихта | Расплавы | Кр | ε, % | ||
---|---|---|---|---|---|---|---|
фосфатно-солевой | силикатный | фосфатно-солевой | силикатный | ||||
P2O5 | 21.3 | 12.01 | 17.00 | 4.34 | 3.90 | 85.7 | 14.3 |
Nb2O5 | 8.83 | 4.98 | 5.40 | 5.015 | 1.07 | 55.0 | 45.0 |
SiO2 | 1.04 | 19.38 | 5.82 | 42.90 | 0.13 | 19.0 | 81.0 |
TiO2 | 2.40 | 1.35 | 1.47 | 1.53 | 0.96 | 60.0 | 40.0 |
Al2O3 | 2.86 | 1.61 | 1.21 | 4.51 | 0.26 | 29.0 | 71.0 |
Fe2O3 | 5.29 | 8.92 | 5.99 | 15.30 | 0.39 | 37.0 | 63.0 |
TR2O3 | 29.95 | 16.89 | 28.94 | 6.50 | 4.45 | 84.7 | 15.3 |
RO | 9.93 | 5.59 | 8.17 | 3.42 | 2.39 | 79.0 | 21.0 |
Na2O | 0.13 | 13.70 | 14.10 | 12.30 | 1.14 | 88.0 | 12.0 |
F | 0.20 | 8.50 | 11.80 | 5.02 | 2.35 | 71.0 | 29.0 |
Установлено, что P, TR2O3, F, оксиды Са, Sr, Вa и Na на ~85% извлекаются в фосфатно-солевой расплав, тогда как оксиды Si, Al, Fe и Nb на 70–80% извлекаются в силикатный расплав. Распределение компонентов между расплавами детально рассмотрено в публикациях [8–10]. С учетом того, что силикатный расплав можно путем простых технологических операций очистить от фосфатно-солевых капель-шариков, распределение компонентов будет еще более контрастным. После разложения фосфатного расплава азотной кислотой присутствующие в нем силикатные шарики можно выделить в виде отдельного самостоятельного промпродукта, обогащенного ниобием.
Контрастные фосфатно-солевой и силикатный расплавы являются промежуточными продуктами, переработка которых с целью получения концентрата солей редкоземельных металлов в отличие от переработки исходной руды является достаточно рядовым химико-технологическим процессом. Один из возможных вариантов обработки расплава выполнен авторами в лабораторном масштабе.
ПЕРЕРАБОТКА ФОСФАТНО-СОЛЕВЫХ РАСПЛАВОВ
Поскольку солевые и силикатные расплавы различны по составу и свойствам, то они перерабатываются различными методами. Фосфатно-солевой расплав легко растворяется в слабых растворах азотной кислоты. При этом температура и продолжительность не оказывают существенного влияния на его растворимость. Получаемые при этом продукционные азотно-фосфорнокислые фильтраты содержат основную часть редких земель, которые выделяют из растворов в две стадии: на первой – насыщенным раствором щавелевой кислоты с рН 1–2, на второй – 5% раствором аммиака с рН 8.5–9.0. На первой стадии в кислой среде выделяется основная часть редких земель (>90%) в составе концентрата оксалатов. На второй стадии для выделения недоизвлеченных остатков редких земель фильтраты, полученные после выделения оксалатов, обрабатываются слабыми растворами аммиака в щелочной среде с получением концентратов гидрооксидов.
Состав получаемых таким способом первичных концентратов приведен в табл. 2. Концентраты оксалатов намного чище по содержанию примесных компонентов, чем гидрооксидные концентраты. После дополнительной очистки обоих концентратов получают редкоземельные полупродукты, из которых экстракционными методами можно получать индивидуальные оксиды редких земель. При этом имеющиеся в руде незначительные примеси тория концентрируются в оксалатах, а урана – в гидрооксидном концентрате.
Таблица 2.
Химический состав оксалатного и гидрооксидного концентратов редких земель, мас. %
Компоненты | Фосфатно-солевой расплав | Силикатный расплав | Концентрат оксалатов РЗЭ | Концентрат гидрооксидов РЗЭ | ||
---|---|---|---|---|---|---|
высушенных при 105°С | прокаленных при 650°С | высушенных при 105°С | прокаленных при 650°С | |||
ΣTR2O3 | 21.50 | 11.36 | 49.27 | 65.95 | 7.11 | 9.04 |
Y2O3 | 0.78 | 0.40 | 2.11 | 2.82 | 0.25 | 0.32 |
Sc2O3 | 0.032 | 0.020 | 0.050 | 0.60 | 0.029 | 0.037 |
Nb2O5 | 3.33 | 3.00 | 0.20 | 0.27 | 0.30 | 0.38 |
P2O5 | 15.40 | 8.56 | 3.43 | 4.59 | 18.7 | 23.8 |
ThO2 | 0.120 | 0.067 | 0.092 | 0.123 | 0.0033 | 0.0042 |
UO2 | 0.043 | 0.0034 | 0.00032 | 0.00041 | 0.0024 | 0.0031 |
Если в табл. 2 приведено содержание редких земель в виде суммы (ΣTR2O3), то в табл. 3 представлена расшифровка содержания оксидов редких земель в составе концентратов оксалатов и гидрооксидов.
Таблица 3.
Расшифровка состава редкоземельных концентратов, высушенных при 105°С
Концентраты | Редкоземельные элементы, мас. % | ||||||||
---|---|---|---|---|---|---|---|---|---|
ΣTR2O3 | La2O3 | Ce2O3 | Pr2O3 | Nd2O3 | Sm2O3 | Eu2O3 | Gd2O3 | Tb2O3 | |
Оксалаты | 49.27 | 12.90 | 21.08 | 2.65 | 9.12 | 1.23 | 0.33 | 0.84 | 0.11 |
Гидроксиды | 7.11 | 2.46 | 3.04 | 0.33 | 1.00 | 0.12 | 0.031 | 0.084 | 0.011 |
Концентраты | Dy2O3 | Ho2O3 | Er2O3 | Tm2O3 | Yb2O3 | Lu2O3 | Y2O3 | Sc2O3 | Влага |
Оксалаты | 0.50 | 0.079 | 0.183 | 0.021 | 0.113 | 0.0136 | 2.17 | 0.050 | 25.3 |
Гидрoксиды | 0.056 | 0.0096 | 0.024 | 0.0027 | 0.015 | 0.0019 | 0.25 | 0.029 | 21.4 |
ПЕРЕРАБОТКА СИЛИКАТНЫХ РАСПЛАВОВ С ПОЛУЧЕНИЕМ КАРБИДА НИОБИЯ
В составе железо-силикатного расплава присутствуют редкие земли, фосфаты, щелочи и фтор, количество которых в сумме составляет 20–22%. В связи с этим расплав после охлаждения измельчается до фракции <145 мкм и подвергается предварительной обработке для очистки от фосфатов вначале в растворе 35–37% серной кислоты при температуре 95°С в течение 1 ч. От исходной навески (20–30 г) в раствор переходит 18–20% компонентов, в основном фосфаты редких земель. Затем нерастворимый остаток подвергается выщелачиванию 25–30%-ным раствором NaOH при температуре 95°С в течение 1–1.5 ч. При этом в раствор переходит еще 35% компонентов, в основном кремнезем. Нерастворимый остаток, обогащенный ниобием и железом, составивший 45–48% от исходного количества расплава был подвергнут карботермической плавке. Восстановительная плавка осуществлялась в печи Таммана в графитовом тигле в атмосфере аргона. Шихта, состоящая из силикатного расплава и восстановителя – углерода, нагревалась до температуры 1600°С и выдерживалась при этой температуре в течение 20 мин. Количество восстановителя составляло 14 г на 100 г силикатного расплава. В результате плавки получались корольки металла, которые легко отделялись после дробления, и стекловидная шлаковая масса. Отсутствие слитка металла, по-видимому, связано с малым количеством оксидов ниобия и железа в силикатном расплаве и высокой вязкостью силикатного шлака. Подобные каплеобразные металлические включения в стекловидной матрице характерны и для рудных месторождений, используемых в металлургии, в том числе редких металлов. Металлическая фаза состоит в основном из ниобия (74–78%) и углерода (6–9%), атомноe отношениe между которыми составляет [Nb] : [C] = 1 (рис. 7). Вторая фаза, присутствующая в корольках металла, содержит главным образом Fe (66–80%), Si (2–7%), P (7–18%), Nb (0.34–5.55%).
Содержание Nb в исходном силикатном расплаве – 3.5%, в монокарбиде ниобия – 76–78%. Размер кубических кристаллов NbC – 1–10 мкм. Твердость составляла 9–10 (по шкале Мооса). Карбид ниобия – материал для производства самых термостойких сверхтвердых сплавов: температура плавления – 3480°С, кипения – 4300°С. Областями применения порошков NbC являются металлообработка и изготовление режущих инструментов. В сплавах с карбидами Zr и U-235 это важнейший конструкционный материал для ТВЭЛов твердофазных ядерных реактивных двигателей. При ~12 К NbC переходит в сверхпроводящее состояние.
Дальнейшая переработка полученного сплава с извлечением ниобия в виде, пригодном для использования в промышленности, возможна несколькими способами. Эти способы предполагают прежде всего тщательное удаление фосфора из силикатного расплава, например, по схеме, предложенной для получения ферромарганца с дополнениями. Для выбора рациональной схемы переработки полученного сплава необходимы дополнительные исследования. Получение феррониобия не закончено и находится в стадии разработки.
ЗАКЛЮЧЕНИЕ
Показано, что ликвационная плавка может быть использована для переработки уникальных редкометальных руд Томторского месторождения. Добавление к исходной руде фторидов приводит к снижению температуры плавления с 1700 до 1200°С. Обнаружено, что при этом однородный расплав распадается на два контрастных несмешивающихся расплава: фосфатный расплав, который концентрирует редкие земли, и силикатный расплав, концентрирующий оксиды ниобия. В расплавах собирается до 80–85% целевых продуктов из исходного сырья. Продемонстрировано, что полученные расплавы могут быть переработаны с извлечением редкоземельных металлов и ниобия известными химическими методами.
Список литературы
Делицын Л.М. Механизм ликвации в природных и технологических силикатно-солевых расплавах – концентраторах редких земель и ниобия. М.: ГЕОС, 2018. 408 с.
Ликвационные явления в стеклах. Труды Первого всесоюзного симпозиума. Л.: Наука, 1969. 194 с.
Явления ликвации в стеклах. Л.: Наука, 1974. 219 с.
Роусон Р. Неорганические стеклообразующие системы. М.: Мир, 1970. 312 с.
Френсис А. Равновесие жидкость – жидкость. М.: Химия, 1969. 238 с.
Делицын Л.М., Синельщиков В.А., Батенин В.М., Бородина Т.И., Вальяно Г.Е. Экспериментальное исследование образования двойных фосфатов в системе LaPO4–NaF // Докл. РАН. 2015. Т. 465. № 4. С. 451.
Делицын Л.М., Синельщиков В.А., Батенин В.М., Сычев Г.А., Бородина Т.И., Вальяно Г.Е. Кристаллизация фаз в системе СеPO4–NaF // Докл. РАН. 2018. Т. 483. № 6. С. 645.
Делицын Л.М. Распределение ниобия и лантана между двумя несмешивающимися расплавами в системе LaPO4–SiO2–NaF–Nb2O5–Fe2O3 // Докл. РАН. 2017. Т. 477. № 3. С. 307.
Делицын Л.М. Распределение Nb и Ce между двумя несмешивающимися расплавами в системе CePO4–SiO2–NaF–Fe2O3–Nb2O5 // Докл. РАН. 2019. Т. 484. № 5. С. 572.
Делицын Л.М. Распределение TR2O3, P2O5 и Nb2O5 между двумя несмешивающимися расплавами в системе “Монацит–SiO2–NaF–Nb2O5–Fe2O3” // Докл. РАН. 2019. Т. 489. № 6. С. 65.
Дополнительные материалы отсутствуют.
Инструменты
Теплофизика высоких температур