Теплофизика высоких температур, 2020, T. 58, № 4, стр. 723-731
Энергетическая утилизация биомассы. Новые технологии
В. М. Зайченко 1, *, В. А. Лавренов 1, О. М. Ларина 1, **, И. И. Лищинер 1, О. В. Малова 1
1 Объединенный институт высоких температур РАН
Москва, Россия
* E-mail: zaitch@oivtran.ru
** E-mail: olga.m.larina@gmail.com
Поступила в редакцию 28.02.2020
После доработки 17.03.2020
Принята к публикации 30.03.2020
Аннотация
Рассмотрены возможности использования различных видов биомассы (растительного происхождения и вторичной биомассы) для производства синтез-газа методом термохимической конверсии на крупномасштабной установке для дальнейшего синтеза компонентов жидких моторных топлив. Из представленных результатов следует, что синтез-газ из осадков сточных вод имеет оптимальный состав для синтеза метанола с дальнейшим превращением в бензин. Синтез-газ из древесных отходов может быть применен для синтеза диметилового эфира и метанола для нужд химической промышленности.
ВВЕДЕНИЕ
Как известно, поступления от продажи топливно-энергетических ресурсов вносят значительный вклад в бюджет Российской Федерации. Необходимо тщательно отслеживать изменения, которые происходят в мире в использовании ископаемых топлив.
Еще сравнительно недавно оценивался временнóй период, на который человечество будет обеспечено запасами угля, нефти и газа. Считалось, что располагаемых ресурсов каменного угля хватит на 300 лет, природного газа – на 60, нефти – на 50. Всемирная конференция ООН по климату (декабрь 2015 г., Париж) рекомендовала с целью сокращения темпов роста температуры на планете в пределах 2°С к 2050 г. ограничить использование ископаемых топлив таким образом, чтобы к этому сроку использовать не более 10% от располагаемых запасов. В рамках обозначенных ограничений примерно 80% мировых запасов угля, 50% природного газа и 30% нефти должны остаться неизрасходованными.
Приоритеты в области использования ископаемых топлив меняются в значительной степени. Из области прогнозов это перешло к практическим мероприятиям, направленным на изменение топливно-энергетической стратегии, осуществляемой в настоящее время. Компания “Siemens”, например, сокращает выпуск турбин. В 2010 г. компания получила заказы на 300 газовых турбин мощностью более 100 МВт, а в 2017 г. заказано только 122 турбины [1].
Если данные подходы справедливы, то затраты на разведку и освоение новых месторождений ископаемых топлив не имеют смысла. Необходимо финансировать не разведку и освоение новых месторождений, а исследования, направленные на создание новых методов получения энергии без использования природных топлив.
Низкоуглеродистое развитие – это сохранение экологического равновесия и в конечном итоге забота об условиях жизни на нашей планете. Практика показывает, что подобные мероприятия, как правило, во многом имеют отрицательные последствия для нашей страны. В 2002 г. из-за ограничений по шумности отечественные самолеты перестали допускаться в европейские страны. Россия была вынуждена закупать импортные самолеты с разрешенным уровнем шумности.
По сути, мы находимся на пороге новой промышленной революции. Происходит замещение ископаемых топлив новыми наукоемкими технологиями, обеспечивающими минимизацию вредного влияния топливно-энергетического комплекса на природное равновесие. Приоритетным становится использование возобновляемых технологий и местных топливно-энергетических ресурсов, к которым относятся торф, древесные и сельскохозяйственные отходы, отходы жизнедеятельности различных видов. Основным направлением развития энергетики в настоящее время является переход на распределенное производство. Тепловую энергию нельзя передавать на большие расстояния, необходимо приблизить источники тепловой энергии к потребителю, в этом случае становится возможным одновременное производство тепловой и электрической энергии, т.е. когенерационное производство, что обеспечивает более высокую степень использования топлива по отношению к схемам с раздельным получением электрической и тепловой энергии. Распределенное производство энергии должно базироваться на использовании местных топливно-энергетических ресурсов. Значительная роль в этом процессе должна отводиться энергетической утилизации отходов. В наше время термин “отходы” должен быть заменен на термин “местные топливно-энергетические ресурсы”, использование которых с экономической точки является более выгодным по отношению к ископаемым топливам и обеспечивает возможность энергетической утилизации различного вида биомассы, в частности отходов различных видов.
Россия – лидер по запасам природных топлив: угля, нефти и природного газа. В то же время на территории нашей страны сосредоточено более 45% мировых запасов торфа и около 25% древесины. Сотни миллионов тонн отходов жизнедеятельности образуются ежегодно. Этот возобновляемый ресурс должен быть утилизирован, в противном случае экологическая ситуация может значительно измениться в худшую сторону. Должны быть разработаны новые технологии, обеспечивающие возможность промышленной переработки отходов с получением энергии и полезных продуктов.
Традиционным направлением переработки биомассы с целью энергетического либо промышленного применения является получение газов, которые могут быть использованы в качестве топлива, в результате процессов пиролиза и газификации [2, 3]. Основными недостатками существующих технологий является то, что получаемый газ содержит определенное количество жидкой фракции [4, 5]. Для использования данного газа в электропроводящем оборудовании необходима его очистка, что значительно усложняет и удорожает процесс. Практика показывает, что экономическая эффективность применения энергетического газа, полученного с использованием существующих технологий газификации и пиролиза, уступает традиционным технологиям получения энергии с использованием ископаемых топлив. При газификации получаемый газ примерно на 50% забалластирован негорючими компонентами [6], при пиролизе – не более 29% от массы перерабатываемого сырья переходит в газообразную фазу [7]. Необходима разработка технологии конверсии углеродсодержащих материалов в газообразное энергетическое топливо, не содержащее жидкой фазы и обладающее более высокими теплотехническими характеристиками по отношению к топливу, получаемому с помощью существующих технологий.
Цель данной работы – показать альтернативную существующим термохимическим способам переработки биомассы технологию, разработанную в ОИВТ РАН, представить результаты испытаний данной технологии в крупном экспериментальном масштабе и предложить один из вариантов применения данной технологии, в частности для производства компонентов жидких моторных топлив.
КРУПНОМАСШТАБНАЯ УСТАНОВКА ДЛЯ ПРОИЗВОДСТВА СИНТЕЗ-ГАЗА ИЗ БИОМАССЫ И РЕЗУЛЬТАТЫ ЭКСПЕРИМЕНТАЛЬНЫХ ИССЛЕДОВАНИЙ
Научные основы разработанной в ОИВТ РАН технологии изложены в работах [8–10]. Процесс осуществляется в две стадии. На первой проводится пиролиз перерабатываемого сырья, на второй осуществляется взаимодействие газообразных продуктов реакции, состоящих из конденсируемых и неконденсируемых продуктов, с образующейся при пиролизе твердой фазой. Температура первой стадии доходит до 800°С, второй – 1000°С. При этом происходит разложение высокомолекулярных конденсирующихся продуктов реакции СnHmОk, воды, а также СО2 и СН4 на водород и окись углерода с образованием синтез-газа.
На рис. 1 представлена крупномасштабная установка по термической конверсии биомассы с получением синтез-газа.
Характеристики данной установки при использовании древесины в качестве перерабатываемого сырья представлены в табл. 1.
Таблица 1.
Характеристики крупномасштабной установки для термической конверсии биомассы с получением синтез-газа (при использовании сосновой стружки в качестве перерабатываемого сырья)
Характеристика | Значение |
---|---|
Производительность по исходной биомассе, кг/ч | 50 |
Влажность исходной биомассы, % | 8.8 |
Зольность исходной биомассы, % | 0.5 |
Производительность по синтез-газу, м3/ч | 65 |
Удельный объемный выход синтез-газа, м3/кг | 1.30 |
Химический состав синтез-газа (в %): | |
водород (H2) | 49.2 |
монооксид углерода (CO) | 40.8 |
метан (CH4) | 3.2 |
диоксид углерода (CO2) | 5.0 |
азот (N2) | 1.8 |
Теплота сгорания синтез-газа, МДж/м3 | 10.5 |
Эффективность конверсии перерабатываемой биомассы в синтез-газ, % | 79.8 |
Рассматриваемый процесс обеспечивает высокую степень конверсии перерабатываемой биомассы в энергетический газ. Выход газового топлива составляет 1.2–1.5 м3 из 1 кг биомассы, а теплота сгорания – 10–12 МДж/м3. Содержание жидкой фазы в перерабатываемом газе составляет не более 50 мг/м3 [11]. Получаемый по разрабатываемой технологии синтез-газ также может быть непосредственно использован в виде топлива для газопоршневого агрегата с целью когенерационного производства тепловой и электрической энергии [12].
Предлагаемая технология применена к различным видам органических отходов. В табл. 2 представлены характеристики полученного синтез-газа.
Таблица 2.
Характеристики синтез-газа при использовании различных видов органических отходов
Сырье | Свойства синтез-газа | |
---|---|---|
[Н2] + [СО], % | [Н2]/[СО] | |
Древесные пеллеты | 92 | 1 |
Торфяные пеллеты | 90 | 1.2 |
Соломенные пеллеты | 78 | 1 |
Пеллеты из лузги подсолнечника | 80 | 1.2 |
Пометно-подстилочная масса | 83 | 1.2 |
Осадки сточных вод | 95 | 1.8 |
Опил (отходы целлюлозно-бумажного производства) | 96 | 1.0 |
Кора древесная | 92 | 1.6 |
Суммарное содержание окиси углерода и водорода составляет не менее 78%, а для отдельных видов сырья – более 90%. Данная технология может рассматриваться в качестве метода получения “зеленого водорода”, т.е. водорода (в том числе и для целей водородной энергетики), получаемого из сырья, которое нейтрально по отношению к выбросам двуокиси углерода.
Применение термического крекинга для переработки смол, образующихся в процессе пиролиза, является довольно распространенным способом. При температуре в зоне крекинга 900°С и использовании активированного угля в качестве наполнителя зоны термического крекинга и древесины в качестве сырья удается достичь степени конверсии смолы в неконденсируемые газы, равной 98.7% [13]. При использовании металлических катализаторов, нанесенных на поверхность древесного угля, в зоне термического крекинга при температуре 800°С и рисовой шелухи в качестве сырья удается достигнуть степени конверсии смолы порядка 90% [14, 15]. При этом суммарное содержание окиси углерода и водорода в получаемом синтез-газе не превышает 65% [14, 15]. Термический крекинг используется и для переработки газификационных смол, но содержание СО и Н2 в составе синтез-газа ограничивается 27–30%, поскольку изначально летучие продукты газификации сильно разбавлены инертным газом – азотом (более 60%) [16]. Кроме того, термический крекинг в случае его применения к процессу газификации незначительно улучшает качество получаемого синтез-газа [16].
Отдельно стоит отметить соотношение объемных долей водорода и окиси углерода, которое является важнейшим показателем при использовании синтез-газа для дальнейшего синтеза компонентов жидких моторных топлив (табл. 2). Технологии получения моторных топлив из биомассы развиваются быстрыми темпами. Сегодня речь идет не только о научных исследованиях, но и о практическом использовании жидких моторных топлив из биомассы в различных типах двигателей. В практику вводится обязательное использование биоавиакеросина. На Западе получение биоавиатоплива базируется в основном на использовании первичного растительного сырья (т.е. специально выращенных растений). Этот путь представляется неоптимальным. Отчуждение сельскохозяйственных угодий под получение жидких топлив вряд ли можно считать целесообразным. Для синтезирования топлива вполне приемлемо использовать торф и вторичную биомассу (т.е. разнообразные отходы), имеющиеся в больших количествах.
ЭКСПЕРИМЕНТАЛЬНАЯ УСТАНОВКА ДЛЯ ПОЛУЧЕНИЯ КОМПОНЕНТОВ ЖИДКИХ МОТОРНЫХ ТОПЛИВ И РЕЗУЛЬТАТЫ ИССЛЕДОВАНИЙ
Процесс получения компонентов жидких моторных топлив условно разделяется на две стадии: синтез метанола из синтез-газа и синтез жидких углеводородов из метанола.
Синтез метанола относится к числу наиболее отработанных гетерогенно-каталитических процессов, характеризующихся достаточно высокой селективностью, технологичностью и производительностью [17–19]. Основными факторами, влияющими на выход конечного продукта, являются давление, температура, соотношение между водородом и окисью углерода в исходной газовой смеси, время ее контакта с катализатором. При выборе оптимальных значений перечисленных параметров необходимо сочетать условия, вытекающие из термодинамических и кинетических закономерностей процесса, с комплексом технологических и экономических требований. Особое внимание следует уделить соотношению между водородом и окисью углерода в исходной газовой смеси. Известно, что оптимальной для реакции является величина [Н2]/[(СО + СО2)] ≥ 2. Кроме того, синтез-газ должен содержать 2.5–4 об. % СО2. Минимальное отношение [Н2] : [СО] должно быть равно 1.5 : 1 [20].
Превращение метанола в жидкие углеводороды происходит на цеолитных катализаторах. Процесс состоит из трех последовательных стадий: дегидратация метанола в диметиловый эфир (ДМЭ), дегидратация диметилового эфира в низшие олефины и превращение низших олефинов в смесь ароматических углеводородов, алканов, циклоалканов и алкенов [21]. Упрощенная схема реакций трансформации метанола записывается как
В зависимости от реакционных условий процесс превращения можно остановить на стадии получения низших олефинов, но производство бензиновой фракции, включающей ароматические углеводороды и алканы, является наиболее предпочтительным.
Из данных табл. 2 видно, что осадки сточных вод (ОСВ) и древесная кора являются оптимальным видом сырья для производства синтез-газа для дальнейшего синтеза метанола. Предлагаемые в настоящее время альтернативные способы получения синтез-газа приводят к получению соотношения [Н2]/[(СО + СО2)] < 2, и он может содержать 50–60% балластного газа – азота [16]. Например, в патенте РФ [22] описан способ получения метанола, согласно которому метанол получают из синтез-газа, содержащего 1.0–33.7% оксида углерода, 0.3–22.5% диоксида углерода при отношении объемного содержания водорода к сумме объемных содержаний оксидов углерода, равном 1.91–5.6, а также 0.5–50% азота.
На экспериментальной установке, расположенной в ОИВТ РАН (рис. 2), проводились исследования по получению бензиновой фракции из синтез-газа. В качестве сырья взяты древесные опилки и ОСВ. Синтез-газ из древесных опилок имеет отношение [Н2] : [СО] = 1 : 1 (табл. 2), но данный вид органических отходов является самым распространенным и вероятным для дальнейшего использования на территории России.
Базовыми элементами установки являются два изотермических каталитических реактора: реактор синтеза метилового спирта (Р-1) и реактор синтеза компонентов жидких моторных топлив (Р-2). Синтез-газ подается в реактор Р-1. Проходя через слой катализатора, синтез-газ преобразуется в метиловый спирт, который далее подается в реактор Р-2 для получения бензиновой фракции. Полное описание установки представлено в [23, 24]. Характеристики установки приведены в табл. 3.
Таблица 3.
Технические характеристики реакторов Р-1 и Р-2
Характеристики (при работе) | Р-1 | Р-2 |
---|---|---|
Температура внутри реактора, °С | 180–300 | 300–600 |
Давление внутри реактора, МПа | до 6 | до 6 |
Объемный расход сырья в процессе реакции, л/ч | до 500 | до 500 |
Используемый катализатор | Металл-оксидный CuO–ZnO/Al2O3 | Цеолитсодержащий типа ZSM-5 |
Высота слоя катализатора, мм | 221 | 221 |
Результаты исследования синтеза метанола в реакторе Р-1 из синтез-газа, полученного из ОСВ и древесных опилок, представлены в табл. 4. Расход синтез-газа составлял 400 л/ч.
Таблица 4.
Материальный баланс компонентов реакции в Р-1
ОСВ | Древесные опилки [25] | |||
---|---|---|---|---|
компоненты | состав, об. % | расход, г/ч | состав, об. % | расход, г/ч |
На входе в Р-1 | ||||
CO | 34.30 | 234.39 | 47.2 | 240 |
H2 | 61.95 | 30.24 | 48.0 | 16.86 |
CO2 | 0.40 | 4.28 | 3.7 | 29.1 |
N2 | 2.70 | 18.49 | 0.7 | 2 |
CH4 | 0.65 | 2.55 | 0.4 | 2 |
Н2О | 0 | 0 | 0 | 0 |
Итого | 100 | 289.96 | 100 | 289.96 |
На выходе из Р-1 (вход в Р-2) | ||||
CO | 27.5 | 130.62 | 49.0 | 147.37 |
H2 | 45.5 | 15.48 | 16.2 | 3.48 |
CO2 | 1.0 | 7.56 | 2.1 | 9.94 |
N2 | 3.8 | 18.27 | 0.7 | 2.0 |
CH4 | 0.9 | 2.52 | 1.3 | 2.21 |
CH3OH | 20.2 | 109.56 | 12.3 | 42.4 |
ДМЭ | 0.6 | 4.77 | 16.9 | 79.64 |
Н2О | 0.4 | 1.17 | 1.5 | 2.92 |
Итого | 100 | 289.96 | 100 | 289.96 |
Выходящий из реактора Р-1 синтез-газ содержит меньшее количество оксида углерода и водорода, что связано с проведением основной реакции синтеза метанола. Отношения [Н2]/[СО] для синтез-газа, полученного из ОСВ и древесных опилок, снижается до 1.65 и 0.33 соответственно, что говорит о возможности повторного использования вышедшего из реактора Р-1 синтез-газа из ОСВ для увеличения массового выхода метанола. Из-за низкого отношения [Н2]/[СО] синтез-газ из древесных опилок считается “бедным”. Общая конверсия СО для него составила 38.2%, при этом конверсия СО в CH3OH – 15.3%, в ДМЭ – 20.9%. Общая конверсия СО для синтез-газа из ОСВ равна 43.6%, конверсия СО в CH3OH – 41.4%, в ДМЭ – 1.3%. Диметиловый эфир в данном случае является побочным продуктом, образующимся в результате реакции дегидратации метанола, которая снижает выход метанола [26]. Таким образом, для дальнейшего синтеза бензиновой фракции оптимальным является синтез-газ из ОСВ, что подтверждается значением [Н2]/[СО] в его составе (табл. 2). “Бедный” синтез-газ может быть применен для получения отдельно ДМЭ и метанола для нужд химической промышленности.
Материальный баланс процесса синтеза бензина представлен на рис. 3.
Рис. 3.
Материальный баланс процесса синтеза бензина (а) и состав углеводородного газа (б) на выходе из реактора Р-2, мас. %.
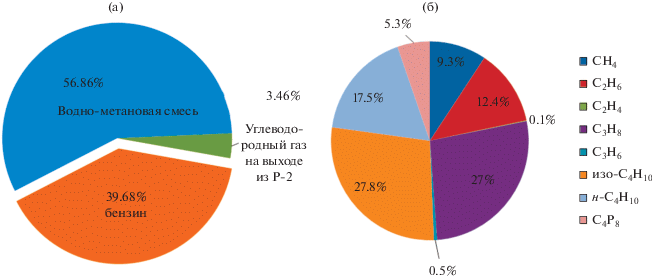
Выход бензина составил порядка 40% от массы подаваемого в реактор Р-2 метанола. Большую часть в продуктах реакции составляет водная фракция (более 56%). Она является побочным продуктом реакции превращения метанола в бензин. Хроматографический анализ не выявил в ее составе метанола. Углеводородные газы, выходящие из реактора Р-2, также не содержат метанола (рис. 4 б). Таким образом, конверсия метанола в бензиновую фракцию составила 100%.
Сравнительные данные по соответствию характеристик полученного синтетического бензина требованиям к бензину марки АИ-92 представлены в табл. 5.
Таблица 5.
Сравнительные характеристики синтетического бензина и бензина марки АИ-92
Наименование показателя | Требования к АИ-92 [28] | Характеристики полученного бензина |
---|---|---|
Октановое число: | ||
ОЧМ, единицы ОЧ | ≥83 | 83.50 |
ОЧИ, единицы ОЧ | ≥92 | 91.70 |
Объемная доля бензола, об. % | ≤1 | 0.28 |
Объемная доля углеводородов (об. %): | ||
олефиновых | ≤18 | 7.85 |
ароматических | ≤35 | 35.72 |
Объемная доля метанола, об. % | Отсутствует | Отсутствует |
Плотность при 15°С, кг/м3 | 725.0–780.0 | 744 |
Давление насыщенных паров бензина при 37.8°С, кПа | 35–80 | 61.10 |
Фракционный состав: | ||
объем испарившегося бензина при температуре (в %): | ||
70°С | 15–50 | 19 |
100°С | 40–70 | 46 |
150°С | ≥75 | 75 |
Температура конца кипения (выкипание 98 об. %), °С | 215 | 220 |
По основным показателям – фракционный состав (за исключением температуры конца кипения), объемная доля олефиновых углеводородов, октановые числа по моторному (ОЧМ) и исследовательскому (ОЧИ) методам – бензин синтетический, полученный конверсией метанола на цеолитсодержащем катализаторе, удовлетворяет требованиям к бензинам экологического класса ЕВРО-5 [27]. Содержания бензола (0.28%) и олефиновых углеводородов (7.05%) существенно ниже требований для бензина АИ-92. Низкое содержание наиболее токсичного ароматического углеводорода – бензола – также позволяет отнести полученный синтетический бензин к классу ЕВРО-5. Определенные расчетным методом ОЧМ и ОЧИ практически удовлетворяют требованиям для бензина АИ-92. Таких значений по детонационной устойчивости удалось достичь благодаря высокому содержанию высокооктановых изопарафиновых углеводородов в составе бензина. Температура выкипания 98% бензина составляет 220°С, что на 5°С выше, чем указано в требованиях к бензинам АИ-92. Следует отметить, что исследовалась исходная смесь углеводородов, полученная в процессе превращения метанола, предварительная стабилизация и фракционирование не проводились.
Таким образом, исходя из результатов экспериментальных исследований, можно составить цепочку превращения местных топливных энергетических ресурсов в компоненты жидких моторных топлив (табл. 6).
Таблица 6.
Цепочка превращения местных топливных энергетических ресурсов в компоненты жидких моторных топлив
Параметр | ОСВ | Древесные опилки |
---|---|---|
Масса сырья, г | 1 | 1 |
Объемный выход синтез-газа, м3 | 1.07* | 1.3 |
Массовый выход метанола, г | 170 | 138 |
Массовый выход ДМЭ, г | 7.4 | 259 |
Массовый выход бензина, г | 67 | – |
* Взято из [29].
Данные в табл. 6 показывают, что ОСВ являются оптимальным сырьем для производства как метанола, так и компонентов жидких моторных топлив. Данная схема учитывает один проход синтез-газа через слой катализатора. Отношение [Н2]/[СО] в составе синтез-газа после реактора Р-1 позволяет создать каскад из реакторов синтеза метанола для увеличения его выхода. Синтез-газ из древесных опилок имеет больший объемный выход, но в связи с низким отношением [Н2]/[СО] вследствие протекания побочной реакции основным компонентом является диметиловый эфир.
ЗАКЛЮЧЕНИЕ
Изменение приоритетов в развитии топливно-энергетического комплекса делает необходимым разработку и создание новых технологий получения энергии. Приоритетным на настоящий момент является энергетическое использование биомассы. В нашей стране имеются разработки по новым технологиям энергетического использования биомассы, к которой относятся отходы различных видов. Получаемое по разрабатываемой технологии газовое топливо может быть непосредственно использовано для целей распределенной энергетики. Синтез-газ, полученный при переработке древесной биомассы, можно использовать для производства электрической энергии или оксигенатов (диметилового эфира, метанола). При переработке отходов жизнедеятельности, утилизация которых является насущной проблемой сегодняшнего времени, использование разрабатываемых технологий позволяет получить газ с оптимальным составом для производства компонентов жидких моторных топлив.
Список литературы
https://www.gazeta.ru/business/2017/11/17/10991306. shtml
Hwai Ch.O., Wei-Hsin C., Yashvir S., Yong Ya. G., Chia-Yang Ch., Pau L. Show. A State-of-the-art Review on Thermochemical Conversion of Biomass for Biofuel Production: A TG-FTIR Approach // Energy Convers. Manage. 2020. V. 209. 112 634.
Shusheng P. Advances in Thermochemical Conversion of Woody Biomass to Energy, Fuels, and Chemicals // Biotechnol. Adv. 2019. V. 37. Is.4. P. 589.
Xun H., Mortaza G. Biomass Pyrolysis: A Review of the Process Development and Challenges from Initial Researches up to the Commercialisation Stage // J. Energy Chem. 2019. V. 39. P. 109.
Safarian S., Unnþórsson R., Richter Ch. A Review of Biomass Gasification Modelling // Renewable Sustainable Energy Rev. 2019. V. 110. P. 378.
Furness D.T., Judd S.J. Thermochemical Treatment of Sewage Sludge // J. CIWEM. 2000. V. 14. P. 57.
Pokorna E., Postelmans N., Jenicek P., Schreurs S., Carleer R., Yperman J. Study of Bio-oils and Solids from Flash Pyrolysis of Sewage Sludges // Fuel. 2009. V. 88. P. 1344.
Батенин В.М., Зайченко В.М., Косов В.Ф и др. Пиролитическая конверсия биомассы в газообразное топливо // Докл. РАН. 2012. Т. 446. № 2. С. 179.
Kosov V., Sinelschikov V., Zaichenko V. High-Calorific Gas Mixtures Produced from Biomass // Springer Proc. Phys. 2014. V. 1. P. 377.
Лавренов В.А., Ларина О.М., Синельщиков В.А., Сычев Г.А. Двухстадийная пиролитическая конверсия различных видов биомассы в синтез-газ // ТВТ. 2016. Т. 54. № 6. С. 950.
Зайченко В.М., Лавренов В.А., Синельщиков В.А. Исследование характеристик газообразного топлива, получаемого методом двухстадийной пиролитической конверсии древесных отходов // Альтернативная энергетика и экология. 2016. № 23–24. С. 42.
Цыплаков А.И. Газопоршневые энергоустановки на генераторном газе: особенности конструкции, опыт эксплуатации, результаты экспериментальных исследований. Препринт № 3-512. М.: ОИВТ РАН, 2013. 51 с.
Peng L., Qunxing H., Yong C., Fei W., Jianhua Y. Catalytic Cracking of Tar Derived from the Pyrolysis of Municipal Solid Waste Fractions over Biochar // Proc. Combustion Institute. 2019. V. 37. P. 2673.
Feiqiang G., Xiaolei L., Yuan L., Kuangye P., Chenglong G., Zhonghao R. Catalytic Cracking of Biomass Pyrolysis Tar over Char-supported Catalysts // Energy Convers. Manage. 2018. V. 167. P. 81.
Qing D., Shuping Z., Huaju L., Xiangqian L., Zhaoyu W. Catalytic Cracking of Biomass Tar Together with Syngas Production over Red Brick Powder-supported Nickel Catalysts // Fuel Proc. Technol. 2019. V. 194. 106 123.
Глазов С.В., Кислов В.М., Размыслов А.В., Салганская М.В. Конверсия продуктов газификации органических топлив в проточном фильтрационном конверторе с насадкой // Журн. прикл. химии. 2019. Т. 92. № 7. С. 927.
Тимофеев B.C., Серафимов JI.A. Принципы технологии основного органического и нефтехимического синтеза. М.: Высшая школа, 2003. 536 с.
Караваев М.М., Леонов В.Е., Попов И.Г., Шепелев Е.Т. Технология синтетического метанола. М.: Химия, 1984. 239 с.
Розовский А.Я., Лин Г.И. Теоретические основы синтеза метанола. М.: Химия, 1990. 268 с.
Елисеев О.Л. Технологии “газ в жидкость” // Рос. хим. журн. 2008. Т. 52. № 6. С. 53.
Шелдон Р.А. Химические продукты на основе синтез-газа. М.: Химия, 1987. 248 с.
Какичев А.П., Краснянская А.Г., Лендер А.А. и др. Способ получения метанола. Патент РФ № 2 181 117: МПК С07С29/154, С07С31/04. 2002.
Лищинер И.И., Малова О.В., Тарасов А.Л., Коробцев С.В., Кротов М.Ф., Потапкин Б.В. Особенности получения ДМЭ из синтез-газа на смесевых катализаторах // Катализ в промышленности. 2016. Т. 16. № 2. С. 23.
Лищинер И.И., Малова О.В., Тарасов А.Л. Конверсия ПНГ в ароматические углеводороды // Катализ в промышленности. 2018. № 5. С. 45.
Ершов М.А., Зайченко В.М., Качалов В.В., Климов Н.А., Лавренов В.А., Лищинер И.И., Малова О.В., Тарасов А.Л. Cинтез базового компонента авиабензина из синтез-газа, полученного из биомассы // Экология и промышленность России. 2016. Т. 20. № 12. С. 25.
Розовский А.Я. Диметиловый эфир и бензин из природного газа // Рос. хим. журн. 2003. Т. 47. № 6. С. 53.
ГОСТ 32 513–2013. Топлива моторные. Бензин неэтилированный. Технические условия. М.: Стандартинформ, 2014. 16 с.
Технический регламент таможенного союза о требованиях к автомобильному и авиационному бензину, дизельному и судовому топливу, топливу для реактивных двигателей и мазуту ТР ТС 013/2011, 2011. 22 с.
Larina O.M., Zaichenko V.M. Thermal Cracking in Charcoal and Ceramics of Pyrolysis Liquid from Sewage Sludge // J. Phys.: Conf. Series. 2018. V. 94. 012034.
Дополнительные материалы отсутствуют.
Инструменты
Теплофизика высоких температур