Теплофизика высоких температур, 2022, T. 60, № 4, стр. 575-583
Экспериментальное исследование прочности резиноподобной коксующейся теплозащиты
В. В. Миронов 1, *, М. А. Толкач 1, В. В. Тлевцежев 1
1 ГНЦ ФГУП “Центр Келдыша”
Москва, Россия
* E-mail: kerc@elnet.msk.ru
Поступила в редакцию 22.12.2020
После доработки 20.05.2021
Принята к публикации 28.09.2021
- EDN: GPMEGF
- DOI: 10.31857/S0040364422030140
Аннотация
Предложен метод и проведено экспериментальное исследование прочности прококсованного слоя типичного резиноподобного теплозащитного материала. Из анализа экспериментальных результатов и их сопоставления с известными данными, полученными при имитации натурных силовых нагрузок, установлен возможный диапазон изменения прочностных свойств прококсованного слоя для резиноподобной теплозащиты.
ВВЕДЕНИЕ
Одним из способов тепловой защиты камер сгорания энергодвигательных установок, работающих на твердом топливе, в том числе ракетных двигателей твердого топлива, является использование резиноподобных покрытий, которые, подвергаясь нагреву под действием конвективных и радиационных тепловых потоков, разлагаются с поглощением значительной доли поступающего тепла [1, 2]. При этом на поверхности теплозащитного покрытия формируется слой пористого коксового остатка, выполняющего функцию теплового сопротивления. Наиболее эффективная тепловая защита реализуется в том случае, когда коксовый остаток сохраняет целостность (не разрушается) в течение всего времени работы энергоустановки. Однако если по мере нарастания слоя коксового остатка происходит его разрушение, то процесс термодеструкции резиноподобного материала (РПМ) существенно интенсифицируется и для защиты стенок камеры сгорания энергоустановки потребуется существенно большая толщина защитного покрытия [3].
Прочностные свойства прококсованного слоя теплозащитных материалов являются важной характеристикой тепловой защиты для высокотемпературных установок. В условиях квазистационарного процесса термического разложения резиноподобного теплозащитного материала глубина термодеструкции (расположения фронта разложения) описывается простой зависимостью вида [1, 4]
где ${{\tau }_{{}}}$ − время воздействия высокотемпературной среды; ξ – постоянная, зависящая от теплофизических свойств разлагающегося материала.В этом случае глубина термодеструкции δд за полное время работы энергоустановки τp составит
Потребная толщина покрытия δтзп будет определяться как [3]
где kz – коэффициент запаса.Предположим, что за время τp по мере нарастания коксового слоя его разрушение реализуется $N$ раз. Тогда глубина термодеструкции может быть оценена величиной
откуда следует, что для одинаковых kz потребная толщина слоя тепловой защиты увеличится в $\sqrt N $ раз.
Для определения возможности разрушения коксового слоя теплозащитного покрытия (ТЗП) необходимо знать его прочностные характеристики и определить механизмы, приводящие к его разрушению.
Общая схема силового взаимодействия коксующихся теплозащитных материалов (ТЗМ) с нагревающим газовым потоком приведена на рис. 1.
Рис. 1.
Общая схема взаимодействия газового потока с элементом коксующейся тепловой защиты: СОК – силовая оболочка корпуса, ГПД – газообразные продукты деструкции.
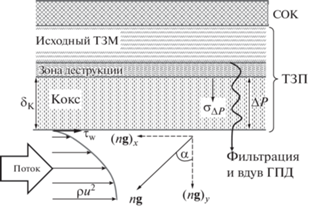
На рисунке показаны действующие на элемент поверхности ТЗП силы: τw ‒ касательная сила трения, обусловленная набегающим потоком; Fm ~ ng – вектор массовых сил, который может быть ориентирован к поверхности под различными углами α и приводить к появлению как нормальных Fy ~ (ng)y, так и тангенциальных (касательных) Fx ~ (ng)x отрывающих сил; ΔP ‒ перепад давления фильтрующихся газообразных продуктов деструкции по глубине разлагающегося материала (вызывает в нем отрывающие напряжения σΔP в направлении, перпендикулярном поверхности).
Следует отметить, что осевые (боковые) напряжения сдвига (отрыва) массовых сил Fx в общем случае действуют вместе с касательными напряжениями трения τw.
Напряжение отрыва σm от действия массовой силы Fm оценивается величиной
Касательные напряжение трения τw оцениваются величиной (в Н/м2 или Па)
В общем случае усилие на отрыв кокса FΔP создают и пиролизные газы в порах прококсованного слоя (см. рис. 1). Перепад давления по толщине прококсованного слоя ΔP и отрывное напряжение в данном случае σΔP, согласно закону Дарси, определяется толщиной прококсованного слоя δк, расходом пиролизных газов ρgV и газопроницаемостью кокса KV:
Здесь ρg – плотность пиролизного газа в порах прококсованного слоя; ν = μ/ρg ‒ кинематическая вязкость, м2/с; μ ‒ динамическая вязкость, Па с; KV ‒ вязкостный коэффициент газопроницаемости, м2.Аппроксимируя зависимость глубины коксования от времени воздействия τ высокотемпературного потока соотношением δк = ξ$\sqrt {{\tau }} $ [1, 3], получим следующее соотношение для оценки σΔP:
(1)
${{{{\sigma }}}_{{{{\Delta P}}}}} = {{\xi }}\sqrt {{\tau }} \nu {{{{\rho }}}_{g}}\frac{{{\xi }}}{{2\sqrt {{\tau }} }}\frac{1}{{{{K}_{V}}}} = \frac{{\frac{{{{{{\xi }}}^{2}}}}{2}\nu {{{{\rho }}}_{g}}}}{{{{K}_{V}}}} = \frac{{{{{{\xi }}}^{2}}{{\mu }}}}{{2{{K}_{V}}}}.$Величина μ определяется в процессе равновесного термодинамического расчета. Согласно расчетов по [6], для РПМ на основе этиленпропиленового каучука в области температур от 600 до 1300 К μ изменяется от 0.2 × 10–5 до 0.35 × 10–5 Па с.
Для определения вязкостного коэффициента газопроницаемости KV в (1) используются данные работы [7] для зависимости газопроницаемости от пористости углеграфитового материала (табл. 1).
Таблица 1.
Зависимость KV от пористости материала
Пористость, % | KV × 1012, м2 |
---|---|
22.4 | 0.32 |
17.7 | 0.22 |
14.3 | 0.10 |
Учитывая, что пористость кокса РПМ составляет до 80%, для оценок можно принять KV = 10–12 м2.
При KV = 10–11‒10–12 м2 и ξ ≈ (0.7–1.0) × 10–3 м/с1/2 [3] из (1) получается ${{{{\sigma }}}_{{{{\Delta P}}}}} = $ 0.5‒5.0 Па.
Из сделанных оценок при принятых значениях cf, ξ, μ, KV следует, что отрывные напряжения от массовых сил (при десятикратной перегрузке) могут быть более чем на порядок больше напряжений трения и напряжений, обусловленных давлением пиролизных газов внутри прококсованного слоя.
Для построения расчетных методик, позволяющих учитывать разрушение прококсованного слоя от напряжений трения, перепада давления по толщине кокса, а также от действия массовых сил, необходимо знать прочностные характеристики кокса ‒значение разрушающих напряжений σ.
Целью настоящей работы является экспериментальное изучение механизма высокотемпературного разрушения с определением прочности прококсованного слоя σ теплозащитных материалов на основе этиленпропилендиенового каучука с прямым измерением усилия и температур, при которых происходит разрушение (отслоение) прококсованного слоя РПМ. Кроме этого, выполнено сравнение прочности кокса с данными для РПМ на основе другого (бутадиен-нитрильного) каучука [8, 9].
Исследовался РПМ на основе этиленпропилендиенового каучука, близкий по составу и свойствам (теплофизическим характеристикам) к ТЗМ Р-864 [4, 10, 11].
ИЗВЕСТНЫЕ МЕТОДЫ И РЕЗУЛЬТАТЫ ЭКСПЕРИМЕНТАЛЬНОГО ИССЛЕДОВАНИЯ ПРОЧНОСТИ ПРОКОКСОВАННОГО СЛОЯ РЕЗИНОПОДОБНЫХ ТЕПЛОЗАЩИТНЫХ МАТЕРИАЛОВ
Известны работы [8, 9], где приведены результаты экспериментального определения прочности прококсованного слоя. В этих работах рассматривался резиноподобный неармированный теплозащитный материал на основе бутадиен-нитрильного каучука (содержанием 57.6%).
В экспериментах Центрального научно-исследовательского института специального машиностроения (ЦНИИСМ) [8] исследовалось влияние массовых сил на прогрев теплозащитного материала и разрушение его прококсованного слоя. Использовался модельный двигатель с газогенератором твердого топлива, который устанавливался на центрифуге.
В первой серии экспериментов работы [8] плоский образец с рабочей поверхностью 65 × 30 × 10 мм располагался так, что центробежная сила действовала параллельно рабочей поверхности образца, обтекаемого потоком газа с температурой 2500‒2700 К и скоростью до 70 м/с при атмосферном давлении. При проведении исследований использовалась центрифуга, позволяющая достигать скорости вращения до 1000 об/мин. Результаты экспериментов в виде зависимости глубины деструкции δд для центрального сечения образца от показателя перегрузки n при фиксированном времени испытания (t = 14 с) представлены на рис. 2 (каждая точка на графике соответствует среднему значению из 4‒5 опытов). Погрешность определения глубины деструкции оценена в ±12%.
Рис. 2.
Зависимость глубины деструкции δд от показателя перегрузки n при времени испытания t = 14 с: кривая ‒ осредняющая линия, проведенная по экспериментальным точкам.
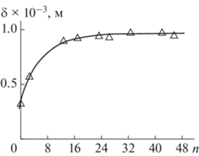
В работе [8] перегрузка создавалась вращением центрифуги от 400 до 1000 об/мин и при радиусе ~0.06 м. Легко получить, что в этом случае n изменялось в диапазоне 12.7‒67.3. Глубина деструкции испытанного резиноподобного ТЗМ с ростом показателя перегрузки значительно возрастает (рис. 2).
В экспериментах в поле массовых инерционных сил с помощью телевизионной системы были зафиксированы достаточно частые отрывы частиц кокса с поверхности образца. В экспериментах без перегрузки отрыва частиц кокса с поверхности образца не наблюдалось. Авторы [8] пришли к выводу о том, что наличие массовых сил приводит к интенсивному разрушению и уносу кокса с поверхности теплозащитного материала.
Значения напряжений σ* внутри прококсованного слоя, обусловленных инерционными силами, при которых происходит его разрушение (отрыв частиц кокса), оценивались с помощью следующего соотношения:
(2)
${{\sigma }}{\kern 1pt} * = l{{\delta }_{{\text{к}}}}\mathop \smallint \limits_{{{r}_{1}}}^{{{r}_{2}}} {{{{\rho }}}_{{\text{к}}}}a\left( r \right)dr{\text{/}}S.$После преобразований для определения σ* было получено и использовалось выражение
По результатам экспериментальных исследований в данной серии экспериментов авторы [8] определили предел прочности кокса в момент отрыва σ* ≈ 90 Па. Погрешность этого результата оценена в работе величиной ±12%. Полагается, что предел прочности кокса σ* равен действующему напряжению в момент отрыва.
Во второй серии экспериментов в [8] плоские образцы устанавливались так, что действие центробежных сил было направлено по нормали к их рабочим поверхностям от поверхности образца. Эксперименты выполнены при давлении P = 4.0 МПа, скорости газового потока ~5 м/с и температуре 3300 К. Тепловой поток к поверхности “холодного” образца ТЗМ составлял ~8.2 × 105 Вт/м2, что в три раза больше, чем в первой серии экспериментов. По семи опытам значение σ* составило 82 Па при погрешности ±14%.
Учитывая, что границы областей значений искомой величины σ* с учетом доверительных интервалов, определенные по двум разным методикам в рассмотренных сериях экспериментов (с отличающимися почти в три раза значениями тепловых потоков к нагреваемой поверхности), пересекаются, авторы [8] сделали вывод, что для РПМ σ* не зависит от величины теплового потока, подводимого к разрушающейся поверхности, и, соответственно, от темпа нагрева образца материала, а также что отрыв кокса происходит по сечению с наименьшей прочностью, которое расположено внутри зоны разложения материала.
В более поздней работе [9] приведены результаты определения прочности кокса при его разрушении, обусловленном касательными силами от обтекающего нагревающего потока. Исследования выполнены в два этапа.
На первом этапе эксперименты проведены в потоке продуктов сгорания ацетилена в кислороде с температурой Te ≈ 2300 К при скорости $v$ ≈ 77 м/с и давлении p ≈ 0.1 МПа.
Установлено, что кокс сохраняется без разрушения в течение всех экспериментов длительностью до 40 с. Максимальная толщина кокса достигала 8 мм.
При этом оцененная величина касательных напряжений составила τ = 16 ± 4 Па. Это значение τ в [9] принято за нижнюю оценку уровня механического нагружения, при котором кокс на поверхности образца типичного обугливающегося резиноподобного ТЗМ еще сохраняется (не отрывается).
На втором этапе для обеспечения проведения экспериментов с разрушением кокса использовалась установка с прогревом в потоке высокотемпературных газов (2100 К) при давлениях до 5 МПа, позволяющих достигать τ до 103 Па. Скоростной напор при постоянном давлении в газогенераторе (5 МПа) регулировался изменением размеров проточного канала (насадка), где размещался образец. Тепловой поток к поверхности в [9] оценен величиной Q ≥ 106 Вт/м2. Продолжительность эксперимента выбиралась так, чтобы обеспечить образование слоя отрываемого кокса толщиной до 1 мм.
По результатам экспериментов определялась зависимость массовой скорости уноса ТЗМ от скорости газового потока. Начиная с определенного значения скорости газового потока U, кокс на поверхности образца после испытания отсутствовал.
Условие полного разрушения кокса формулировалось как равенство касательных напряжений трения τ газового потока пределу прочности кокса на растяжение σ* в зоне сцепления последнего с исходным (неразложившимся) материалом:
По минимальному значению τ, при котором происходит унос кокса, определялось значение σ*. При этом напряжение трения газового потока рассчитывалось по формуле
где λ ‒ коэффициент сопротивления трубы, ρ – плотность газа.Эксперименты показали, что значение скоростного напора газа в трубе, при котором происходит разрушение кокса, не превышает ρU 2/2 = = 0.0117 МПа. При таком скоростном напоре падение давления в рабочем канале с образцами ТЗМ не превышало 0.4%, и значение ρ вычислялось по показаниям датчика давления на входе в канал.
Значение λ определялось при помощи выражения для течения в трубах с развитой шероховатостью [12]:
Минимальное значение скорости U, при которой имеет место отрыв кокса с образца ТЗМ при фиксированном давлении, определялось из серии экспериментов с заданной точностью как среднее из общего числа экспериментов. Толщина обугленного слоя Δ на образцах после экспериментов измерялась при минимальной скорости U. Высота элемента шероховатости Н принималась равной Δ. Значение τ рассчитывалось по выражению (4), а значение прочности кокса σ* исследовавшегося ТЗМ определялось из условия (3).
По результатам серии из 32 опытов получено σ* = 72 ± 17 Па.
В работе [9] сделан вывод: наименьшая прочность кокса резиноподобных ТЗМ наблюдается в зоне сцепления кокса с исходным материалом (область с Т ~ 650 К). Данная температура близка к температуре, соответствующей максимальной скорости термической деструкции исследуемого материала, – 690 К.
В табл. 2 приведены итоговые результаты по определению прочности кокса в работах [8] и [9].
В рассмотренных экспериментах температура материала (кокса) со стороны нагрева переменна по времени: в момент непосредственно после удаления слоя кокса ~700 К, в период образования слоя кокса на 100‒300 К ниже температуры потока (в зависимости от условий обтекания: температуры потока, конвективного и лучистого теплообмена).
В [8, 9] прочность прококсованного слоя оценивалась по косвенным признакам без прямого измерения усилий (“нагрузка” определялась расчетным путем – см. (2) и (4)), что приводит к значительным (до 24%) погрешностям. Кроме этого, в рассмотренных работах отсутствует экспериментальное определение температур, при которых происходит разрушение прококсованного слоя. Знания этих температур важны для построения расчетных методик.
ЭКСПЕРИМЕНТАЛЬНАЯ УСТАНОВКА И МЕТОДИКА ИССЛЕДОВАНИЙ
Эксперименты по определению прочности коксового слоя, образующегося во время прогрева (коксования) образца ТЗМ, с определением температур в области разрушения и прямым измерением прилагаемой нагрузки проводились на установке, схематически показанной на рис. 3.
Рис. 3.
Схема экспериментальной установки: 1 ‒ камера, 2 ‒ нагреватель, 3 – образец ТЗМ (РПМ), 4 ‒ электроконтакты.
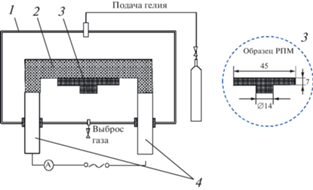
Способ определения предела прочности образца материала состоит в закреплении образца, его нагревании, нагружении растягивающим усилием до разрушения c прямым измерением разрушающего усилия и площади поперечного сечения в момент разрыва.
Установка состоит из камеры 1 и электрических контактов 4, к которым крепится нагревательный элемент (НЭ) 2 из графита марки ПРОГ-230. Для исключения горения образца во время испытаний камера 1 заполняется инертным газом (гелием) под давлением 0.1‒0.3 МПа. Температура НЭ может повышаться до ~3300 К. Образец материала изготавливается из единой заготовки материала и состоит из двух частей: пластины и цилиндрической части. Границей между пластиной-основанием образца и цилиндрической частью служит кольцевая проточка глубиной 2 мм. Образец крепится под нагревательным элементом, как показано на рис. 3. Первоначальные эксперименты без кольцевой проточки показали, что отрыв не прококсованной цилиндрической части образца происходит по сечению с неконтролируемой площадью и периметром, превышающим периметр цилиндрической части образца. В экспериментах с проточками различной глубины (1.5‒3 мм) получено, что наличие проточки не приводит к заметному изменению результатов.
Наряду с контактным нагревом (рис. 3) основные исследования выполнены с использованием нагрева излучением. В этом случае между образцом РПМ 2 и нагревательным элементом 1 имел место зазор (рис. 4). Образец 2 устанавливался на расстоянии 2‒3 мм от поверхности НЭ. Зазор регулировался с помощью специальной графитовой подложки 5.
Рис. 4.
Схема крепления образца ТЗМ к нагревательному элементу с зазором и устройством для фиксирования момента отрыва цилиндра: 1 – нагреватель, 2 ‒ образец РПМ, 3 – подставка, 4 – вольфрамовая нить, 5 – графитовая подложка; R ‒ сопротивление (15 кОм); mA – миллиамперметр; V – источник тока; Т1, Т2 – места заделки термопар.
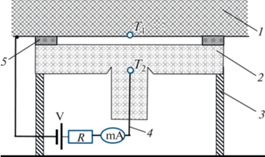
Лучистый нагрев использован с целью обеспечения газового зазора между НЭ и образцом и, следовательно, свободного оттока пиролизных газов от поверхностного (коксующегося) слоя ТЗМ. В этом случае устраняется накопление газообразных продуктов разложения ТЗМ в порах прококсованного слоя [4] и, следовательно, исключается влияние дополнительных сил давления на отрыв цилиндрической части образца от кокса (см. (1)), что повышает достоверность получаемых результатов.
Образец со стороны перекладины нагревается до температуры, близкой к температуре нагревателя, которая значительно выше температуры коксования материала образца. В процессе нагрева тепловая волна (и зона коксования) в образце ТЗМ движется со стороны НЭ вглубь материала. При подходе зоны коксования к кольцевой проточке в случае, если вес оставшегося (непрококсованного) цилиндрического участка образца с грузом достаточен, цилиндрическая часть образца отрывается. После остывания образца морфология среза (области разрыва) анализировалась визуально с использованием микроскопа. Отмечена незначительная шероховатость (зернистость) обеих поверхностей разрыва (как со стороны прококсованной части образца, так и на поверхности со стороны, не подвергнутой коксованию) с отклонением к поверхностям в направлении оси цилиндра не более 0.5 мм. При наличии кольцевой проточки сечение отрыва расположено в плоскости, перпендикулярной оси отрываемого цилиндра и проходящей через кольцевую проточку. Срез практически имеет форму круга.
Разрушающее усилие измеряется взвешиванием оторвавшейся части образца (в отдельных случаях с дополнительным грузом). Изменяя (уменьшая) вес груза и/или длину цилиндрического участка образца, эксперимент повторяется до тех пор, пока цилиндр не останется на месте (по окончании эксперимента). Средний вес цилиндрических частей образцов в двух соседних испытаниях (с оторвавшимся и не оторвавшимся цилиндрическим участком) принимается (в первом приближении) за предельную силу F отрыва коксового слоя.
При изучении механизма разрушения измерялись:
– температура нагревательного элемента Тнэ (Т1 на рис. 4);
– температура Тц образца в области кольцевой проточки в зоне отрыва (по оси цилиндра) (Т2 на рис. 4).
Для измерения температур использовалась вольфрам-рениевая термопара диаметром 0.2 мм, с диапазоном измерения от 300 до 2500 К и погрешностью ~0.1%. С учетом пологости профиля температуры в области разложения РПМ с минимальной толщиной зоны деструкции ~2 мм и перепадом температуры в 200 К (600‒800 К) [1] при погрешности установки термопары по глубине в 0.2 мм погрешность в измеряемой температуре составляет ~20 К, или ~3%.
Для фиксирования момента времени отрыва цилиндрического участка использовано электрическое устройство, схема которого приведена на рис. 4.
Устройство основано на диэлектрических свойствах исходного ТЗМ и достаточно высокой электропроводности прококсованного слоя материала.
При достижении фронтом коксования плоскости кольцевой проточки цепь замыкается, стрелка миллиамперметра отклоняется. В момент отрыва цепь размыкается, стрелка возвращается в исходное положение.
По результатам испытаний прочность кокса определяется по формуле
где F = mg – сила, под действием которой происходит отрыв цилиндрической части образца, – вес оторвавшейся части образца с дополнительным грузом (при его наличии); S – площадь разрыва кокса (м2), S = 1.54 см2.В качестве примера на рис. 5 приведена зависимость температуры Тнэ от времени испытания и температура в центре цилиндрической части Тц в плоскости проточки.
По наклону кривой Тц можно оценить темп нагрева b (К/с) в области кольцевой проточки в момент отрыва; τот, Tот – время и температура, при которых имело место отслоение (отрыв) цилиндрической части образца; τкц, Ткц – время и температура, при которых слой ТЗМ между нагревателем и плоскостью проточки образца становится электропроводным (начало коксования).
РЕЗУЛЬТАТЫ ЭКСПЕРИМЕНТАЛЬНЫХ ИССЛЕДОВАНИЙ
Исследовались образцы, изготовленные из двух пластин РПМ одной партии изготовления.
Основная часть экспериментов выполнена при близких значениях времени выхода нагревательного элемента на режим τвр (60‒90 с) при давлении гелия в камере 0.3‒0.35 МПа. Время выхода на режим и максимальная температура нагревателя определяются величиной пропускаемого через него тока. Исследования проведены в следующих диапазонах максимальных температур нагревательного элемента:
1) Тнэ =1890‒1970 К для образцов из первой пластины РПМ;
2) Тнэ =1840‒1940 К – для образцов из второй пластины РПМ.
Пример получаемых при измерениях результатов приведен на рис. 6 и 7 (для образцов из пластины №1).
Характерные времена и температуры прогрева в экспериментах для образцов из разных пластин представлены в табл. 3.
Таблица 3.
Условия проведения экспериментальных исследований образцов
№ пластины | τвр, с | τкц, с | τот, с | τ573, с | Тнэ, К | Ткц, К | Тот, К | b, К/с |
---|---|---|---|---|---|---|---|---|
1 | 68.7 | 136.6 | 181.0 | 135.0 | 1946 | 563 | 773 | 4.7 |
2 | 67.7 | 124.2 | 172.8 | 125.7 | 1916 | 421 | 850 | 11.9 |
Результаты обработки данных, включая рассчитанные по (5) предельные напряжения, при которых имел место отрыв прококсованного слоя, приведены в табл. 4.
Таблица 4.
Результаты экспериментальных исследований
Пластина № | 1 | 2 | Выборка по | ||
---|---|---|---|---|---|
Тнэ, К | 1898‒1973 | 1843‒1923 | 1843‒2073 | Тнэ | |
Средняя Тнэ, К | 1946 | 1883 | 1916 | ||
σa, Па | 52 | 43 | 44 | ||
σb, Па | 58 | 50 | 50 | ||
τвр, с | 60‒70 | 60‒90 | 60‒70 | 70‒90 | τвр |
Среднее τвр, с | 65 | 68.5 | 67.7 | 80 | |
σa, Па | 52 | 52 | 44 | 50 | |
σb, Па | 58 | 58 | 49 | 51 |
При вычислении σa по (5) величина F, под действием которой происходит разрыв кокса, определяется как среднее между максимальным весом не оторвавшейся цилиндрической части образца (определяется размерами цилиндрической части) и минимальным весом оторвавшегося цилиндра. Значение σb определялось по (5) с использованием величины F, полученной как полусумма средних значений веса оторвавшихся и не оторвавшихся цилиндрических частей образца.
Предельные напряжения σa и σb характеризуют прочность кокса и представляют собой предельное нормальное (растягивающее) усилие на единицу площади, при котором происходит разрыв прококсованного слоя.
Незначительное расхождение в σa и σb (в пределах погрешности), полученных для одинаковых выборок экспериментальных данных (по Тнэ и τвр), показывает возможность использования каждого из способов обработки данных для определения предельных напряжений.
Из полученных данных также следует, что изменение времени выхода нагревательного элемента на режим в пределах 60‒90 с не приводит к существенным изменениям в величине σ.
Отличие в σ для образцов из разных пластин составляет для σa 17%, для σb 15%. Однако связать полученные отличия с изменением свойств кокса для разных пластин невозможно, так как сравниваемые σ получены при отличающихся условиях прогрева: температуре нагревательного элемента и времени выхода на режим (см. табл. 4).
Полученные результаты по σ иллюстрированы на рис. 8. Приведено минимальное и максимальное значения σ для каждой из серий экспериментов. На рисунке также показано среднее значение σ = 39 Па (обозначено треугольником), полученное без использования графитовой подложки 4 (см. рис. 3), т.е. при прогреве без зазора между образцом и нагревателем для температуры нагревательного элемента 1773 К. Значение рассчитано аналогично σa.
Рис. 8.
Зависимость σ от температуры нагревательного элемента: № 1, № 2 ‒ номера пластин; темпы нагрева в области деструкции: 4.7 К/с для № 1 и 11.9 К/с для № 2.
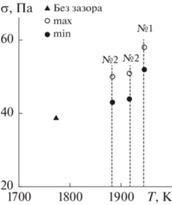
Более низкое значение прочности кокса, полученное в испытаниях без зазора между образцом и нагревателем, может быть связано и с более низкой температурой нагревателя, и занижено за счет уменьшения силы отрыва: при плотном прилегании образца к нагревательному элементу возможно существенное влияние на отрыв давления в порах прококсованного слоя. Оценки показали, что при частичном перекрытии пор на выходе из кокса (уменьшение газопроницаемости кокса, когда образец РПМ прижат к НЭ) ${{{{\sigma }}}_{{{{\Delta P}}}}}$ ≈ 5‒10 Па. Учитывая это, получим значение σ = 44‒49 Па, т.е. значение, близкое к величинам для случая экспериментов с газовым зазором.
Отличие в величине приведенных в табл. 4 σ (рис. 8) от данных работ [8, 9] (табл. 2) может быть связано с влиянием состава РПМ на прочность прококсованного слоя (в основе лежат различные каучуки: соответственно этиленпропилендиеновый и бутадиен-нитрильный). Кроме этого, более высокие значения σ* в [8, 9] могут быть обусловлены неучтенными особенностями разрушения кокса: в экспериментах [8, 9] отрыв кокса происходил не только по зоне контакта с неразложившимся материалом, но и по боковым поверхностям сцепления с другими частицами кокса.
Данное предположение подтверждается киносъемкой, выполненной авторами [8], – имеет место не отрыв коксового слоя в целом по зоне разложения, а отрыв отдельных его частиц, т.е. полученное авторами значение σ* учитывает и напряжения на фрагментацию прококсованного слоя на частицы. В результате σ* в [8, 9] для отрыва по зоне коксования завышено.
Утверждение в [8], что величина σ* всегда значительно меньше прочности сцепления частиц кокса между собой, представляется не вполне обоснованным.
При известной величине предельного напряжения σ, полученной экспериментально, возможная толщина слоя кокса δk, отрываемого от ТЗП инерционными силами в натурных изделиях, может быть определена с использованием соотношения
(6)
${{\delta }_{k}} = \sigma {\text{/}}({{\varphi }_{k}}{{\rho }_{m}}a) = \sigma {\text{/}}({{\varphi }_{k}}{{\rho }_{m}}9.8n).$На рис. 9 приведены результаты расчетов δk по соотношению (6). Расчеты проведены при φk = 0.3 и ρm = 1100 кг/м3. Представлены предельные кривые. Область выше кривой с заданной σ соответствует отрыву кокса при достижении перегрузкой заданной величины, ниже кривой расположена область без удаления прококсованного слоя – величины перегрузки недостаточно для отрыва прококсованного слоя заданной толщины.
Рис. 9.
Зависимость толщины отрываемого кокса δk от перегрузки n при различной прочности прококсованного слоя σ: 1 – θ = 90 Па, 2 – 80, 3 – 60, 4 – 50.
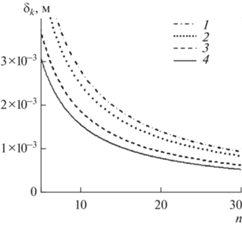
Согласно [8], при прочности σ = 82 Па толщина срывающегося кокса составляет порядка 1 мм. В этом случае, как следует из рис. 2 и 9, n ~ 25.
ЗАКЛЮЧЕНИЕ
Выполнены экспериментальные исследования и установлен диапазон изменения значений предельных напряжений при нормальном (растягивающем) нагружении прококсованного слоя РПМ на основе этиленпропилендиенового каучука (40‒60 Па).
Получены экспериментальные данные в части диапазона температур, при которых происходит разрушение и удаление кокса РПМ при нагрузках, приложенных по нормали к поверхности прогрева (773‒850 К) (табл. 3). Эти данные подтверждают предположение работ [8, 9], что разрушение (отрыв) прококсованного слоя происходит в зоне от температуры максимума скорости разложения до температуры конца разложения.
Сравнение полученных данных с результатами для РПМ на основе бутадиен-нитрильного каучука указывает на возможное существенное влияние на прочность (предельное разрушающие растягивающее напряжение) прококсованного слоя неармированных РПМ свойств каучука, лежащего в основе материала. Для установления причин отличий, обусловленных каучуком, требуются дальнейшие исследования.
Список литературы
Губертов А.М., Миронов В.В., Волкова Л.И. и др. Газодинамические и теплофизические процессы в ракетных двигателях твердого топлива / Под ред. Коротеева А.С. М.: Машиностроение, 2004. 512 с.
Миронов В.В., Толкач М.А. Термическая деструкция резиноподобных теплозащитных материалов под слоем конденсированной фазы // ТВТ. 2019. Т. 57. № 2. С. 269.
Кошлаков В.В., Миронов В.В., Чумакин К.А., Толкач М.А. Экспериментальные исследования разбросов теплозащитных характеристик резиноподобной теплозащиты // ТВТ. 2020. Т. 58. № 2. С. 266.
Полежаев Ю.В., Фролов Г.А. Тепловое разрушение материалов / Под ред. Скорохода В.В. Киев: Изд-во ИПМ НАНУ, 2005. 288с.
Мухамедов В.С. Твердотопливные двигатели специального назначения. СПб.: СОТ, 2018.
Трусов Б.Г. Компьютерное моделирование фазовых и химических равновесий // Инж. вестн.: электр. науч.-техн. журн. 2012. № 10. (http://engsi.ru/doc/483186.html)
Плевин Г.В., Сычева Л.И. Изменение пористой структуры и свойств углеграфитовых материалов в процессе пропитки пеками и последующей термообработки // Совершенствование технологии и улучшение качества электродной продукции. Сб. науч. тр. Челябинск: Южно-Уральск. кн. изд-во, 1974. № 6. С. 30.
Гаращенко А.Н., Кузнецов Г.В., Ткачев А.И. Механизм высокотемпературного разрушения резиноподобных теплозащитных материалов в поле массовых инерционных сил // ТВТ. 1995. Т. 33. № 3. С. 458.
Кузнецов Г.В. Экспериментальная оценка прочности кокса обугливающегося резиноподобного теплозащитного материала // ФГВ. 1996. Т. 32. № 5. С. 143.
Яскин А.В. Конструкции и отработка ракетных двигателей на твердом топливе. Учеб. пособ. Бийск: Изд-во Алт. гос. техн. ун-та, 2010. 200 с.
Конструкции ракетных двигателей на твердом топливе / Под ред. Лаврова Л.Н. М.: Машиностроение, 1993. 215 с.
Лойцянский Л.Г. Механика жидкости и газа. М.: Наука, 1978. 840 с.
Дополнительные материалы отсутствуют.
Инструменты
Теплофизика высоких температур