Вестник Военного инновационного технополиса «ЭРА», 2022, T. 3, № 3, стр. 227-261
АДДИТИВНЫЕ ЭНЕРГОГЕНЕРИРУЮЩИЕ ТЕХНОЛОГИИ ПЛАЗМЕННОЙ ПЕРЕРАБОТКИ ОТХОДОВ: ТЕХНИКО-ЭКОНОМИЧЕСКИЙ АНАЛИЗ
А. В. Артемов 1, *, А. В. Переславцев 1, С. А. Вощинин 1, С. С. Тресвятский 1, С. В. Коробцев 1, П. И. Петренко 1, Н. С. Чемоданов 1
1 Национальный исследовательский центр “Курчатовский институт”
Москва, Россия
* E-mail: arsenyart@icloud.com
Поступила в редакцию 15.03.2022
После доработки 20.03.2022
Принята к публикации 20.03.2022
Аннотация
Обобщены результаты расчета базовой плазменной переработки отходов различного морфологического состава. Обсуждаются аддитивные технологии (АТ) – варианты базовой технологии, объединенные с энергетическим блоком (ВТПК), блоком получения водорода (ВТПК + Н2) и блоком алга-технологий (ВТПК + БАТ). Улучшение АТ ВТПК достигается выделением водорода из пирогаза методом короткоцикловой адсорбции (КЦА) и получением водорода с использованием процесса углекислотного риформинга и паровой конверсии монооксида углерода (ВТПК + Н2). Наиболее перспективной АТ является ВТПК + БАТ, при реализации которой происходит выращивание и переработка микроводорослей Chlorella vulgaris в биодизельное топливо, биомассу и глицерин. Проведен технико-экономический анализ работы ВТПК + БАТ. Высокая степень декарбонизации достигается за счет полного извлечения СО2 из технологических потоков, высокой степени внутреннего использования СО2 (до 88%) и заменой (до 98%) природного газа вырабатываемым биодизелем и горючими компонентами пирогаза. Показана перспективность переработки побочного продукта (глицерина) в триацетин переэтерификацией триглицеридов жирных кислот метанолом. Предложен вариант агро-промышленно-коммунального кластера (АПКК), перерабатывающего отходы коммунального сектора и региональных промышленных и сельскохозяйственных предприятий и обеспечивающего их сырьем и энергией.
ОГЛАВЛЕНИЕ
Введение
1. Методы исследования
2. Результаты расчета. Базовая технология
3. Результаты расчета АТ1: “Комплекс ВТПК”
4. Результаты расчета АТ2: “Комплекс ВТПК + + Н2”
5. Результаты расчета АТ3: “Комплекс ВТПК + + БАТ”
Заключение
ВВЕДЕНИЕ
Аддитивные технологии (АТ) – термин, который появился недавно и относится к базовой технологии, объединенной с технологией, позволяющей улучшить показатели базовой технологии. Впервые термин АТ был предложен Американским международным обществом тестирования материалов в стандарте ASTMF2792.1549323 и описывает АТ как процесс присоединения технологий [1]. Большинство публикаций по АТ касается в основном 3D-печати [2, 3]. Применение АТ эффективно в химической технологии для оптимизации с целью создания энергоэффективных производств с минимизацией отходов [4, 5]. Как будет показано ниже, применение АТ перспективно для плазменной переработки отходов [6–20] как к одному из современных методов термической переработки отходов [21–23]. В настоящем обзоре обобщены данные по АТ плазменной переработки отходов и предпринята попытка оценить их эффективность. Из числа возможных АТ рассматривались те, которые являются энергогенерирующими и позволяют реализовать избыток энергетических ресурсов на внешнем рынке (тепловая и электрическая энергия, водород, дизельное топливо).
1. МЕТОДЫ ИССЛЕДОВАНИЯ
В обзоре проанализированы результаты расчетов базовой и различных АТ плазменной переработки отходов, выполненных с помощью алгоритмов и программ расчета, разработанных в НИЦ “Курчатовский институт” и подробно описанных в [6]. В основе расчета лежат энергетический и материальный балансы унитарного плазменного блока (УПБ), рис. 1. УПБ представляет собой плазменный конвертер. Загрузка сырья – отходов производства и потребления (ОПП) – происходит с помощью загрузочного устройства (системы шиберов), расположенного в верхней части конвертера. В нижней части конвертера находится плавильная камера, в которую введены четыре плазматрона и в которую вводится определенное расчетное (в зависимости от морфологического состава ОПП) количество кислорода, необходимого для перевода неорганической части ОПП в базальтоподобный шлак (БПШ). Производительность УПБ по сырью – 12 500 тонн в год. Среднемассовая температура в УПБ 1300–1500°С. БПШ в расплавленном состоянии выгружается из плавильной зоны реактора, расположенной в нижней его части. БПШ является обязательным продуктом плазменной переработки отходов [7], его количество определяется в основном морфологическим составом отходов [6]. Требуемая производительность по отходам достигается включением в технологическую схему нескольких УПБ. В этом случае производительность будет кратной 12 500 т/г.: 12 500, 25 000, 37 500, 50 000, 62 500 и т.д. Расчет равновесного состава пирогаза проводили по методике [6] с использованием данных о среднем составе ОПП (табл. 1). Обычно производительность комплексов плазменной переработки отходов составляет 20 000–50 000 т/г. [24]. В данном обзоре ориентировались в основном на производительность 25 000 т/г.
Рис. 1.
Эскиз унитарного плазменного блока (УПБ). Стрелками показано расположение датчиков контроля температуры в блоке.
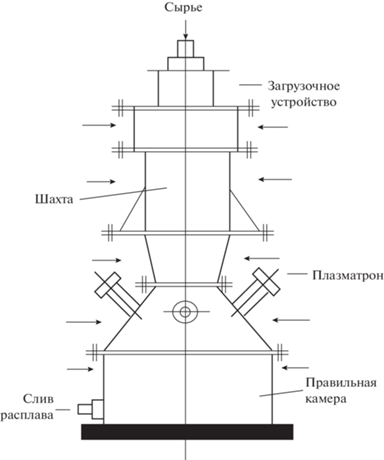
Таблица 1.
Средний элементный состав ОПП
ОПП | Элементный состав, мас. % | |||||||
---|---|---|---|---|---|---|---|---|
С | Н | О | N | S | Н2О | SiO2 | Зола | |
ТКО | 34.84 | 3.38 | 28.45 | 0.15 | 0.14 | 14.87 | 15.45 | 2.71 |
ТНО | 59.10 | 7.89 | 0.70 | 0.21 | 2.49 | 19.74 | 9.86 | |
АБ | 35.50 | 8.00 | 2.00 | 4.44 | 50.00 | 0.05 | ||
ОПМ | 52.10 | 7.89 | 28.70 | 0.21 | 0.49 | 8.74 | 3.86 | |
АП | 74.60 | 12.40 | 1.00 | 12.00 | ||||
ОД | 18.00 | 3.00 | 24.00 | 0.10 | 49.90 | 5.00 | ||
БО | 46.08 | 7.78 | 17.03 | 4.00 | 0.09 | 20.20 | 4.80 | |
МО | 29.43 | 4.20 | 29.43 | 0.13 | 0.20 | 16.18 | 20.22 | 0.21 |
2. РЕЗУЛЬТАТЫ РАСЧЕТА. БАЗОВАЯ ТЕХНОЛОГИЯ
Расчет базовой технологии проводили в соответствии с принципиальной технологической схемой (рис. 2), согласно которой ОПП подавали в верхнюю часть УПБ, в нижней части которого расположены четыре плазматрона (ПЛ) ЭДП-600 (на рис. 2 – один ПЛ). Рабочим газом в ПЛ является СО2, подаваемый в ПЛ из хранилища СО2 (ХРСО2). Как будет показано соответствующими расчетами, этого количества СО2 недостаточно для функционирования ПЛ. Поэтому в ПЛ подается дополнительный СО2 из внешних источников. Электроэнергию Е ПЛ также получают из внешних источников. В плавильную камеру УПБ подают строго расчетное количество кислорода для обеспечения полного превращения неорганических компонентов ОПП в базальтоподобный шлак, который выводится из нижней части УПБ. Расчет этого количества О2 проводят таким образом, чтобы реальная электрическая мощность одного ПЛ составляла 540 кВт (90% номинальной мощности плазматрона ЭДП-600). Пирогаз из УПБ поступает в котел-утилизатор (КУ), где отдает свое тепло с выработкой теплоносителя (Т) – пара. Охлажденный пирогаз из КУ направляют на стадию очистки пирогаза (ОПИР), после чего очищенный пирогаз направляют на стадию абсорбционного выделения СО2 (ВСО2). Выделенный углекислый газ направляется в Х-РСО2. Оставшиеся газы после соответствующей очистки (на рис. 2 не показано) поступают в атмосферу. При использовании базовой технологии УПБ производительностью 12 500 т/г.:
− часовая производственная мощность – 1679 кг/ч;
− номинальное время эксплуатации – 8760 ч/г.;
− годовая загрузка по времени реальной эксплуатации – 85%;
− реальное время эксплуатации в году – 7446 ч;
− время сервисного и технического обслуживания – 1314 ч.
Увеличение производительности базовой технологии достигается использованием нескольких УПБ.
Выделение СО2 проводят абсорбционным методом под давлением при температуре ~30°С. В качестве абсорбента используют метилдиэтаноламин (МДЭА), который зарекомендовал себя эффективным поглотителем СО2 [25] – при взаимодействии СО2 с МДЭА происходит быстрая реакция образования карбоната диэтаноламмония. При снижении давления до 0.1 МПа и повышении температуры насыщенного абсорбента до 120°С происходит разложение образовавшегося карбоната и выделение из раствора СО2. Основными этапами этой стадии процесса являются:
– абсорбция СО2 из пирогаза под давлением 2.25 МПа водным раствором МДЭА;
– отдувка СО2 и регенерация насыщенного СО2 раствора МДЭА при температуре около 120°С;
– циркуляция раствора МДЭА с использованием теплообменного, холодильного и насосного оборудования.
Степень извлечения СО2 составляет не менее 90% (обычно 91–95%). Абсорбцию СО2 с использованием в качестве абсорбента МДЭА проводят в насадочной колонне, заполненной насадочными контактными элементами – стальными кольцами Рашига размером 25 × 25 × 0.8 мм. Слой насадки опирается на опорно-распределительную решетку. В верхней части насадочная колонна оснащена распределителем регенерированного абсорбента (МДЭА). Используемая насадка имеет следующие основные характеристики:
− удельная поверхность – 220 м2/м3;
− свободный объем – 0.92 м3/м3;
− эквивалентный диаметр – 0.017 м;
− число элементов в 1 м3 – 55 000;
− насыпная плотность – 640 кг/м3.
Принципиальная технологическая схема выделения СО2 с использованием МДЭА (насосное и компрессорное оборудование на схеме не показано) приведена на рис. 3 [25].
Рис. 3.
Принципиальная технологическая схема выделения СО2 с использованием МДЭА. АБС – абсорбер, КНД – колонна низкого давления (дросселирующая), ДЕС – десорбер-регенератор, СЕП – сепаратор, ХОЛ – холодильник, КИП – кипятильник, ТО – теплообменник. Q – теплоноситель.
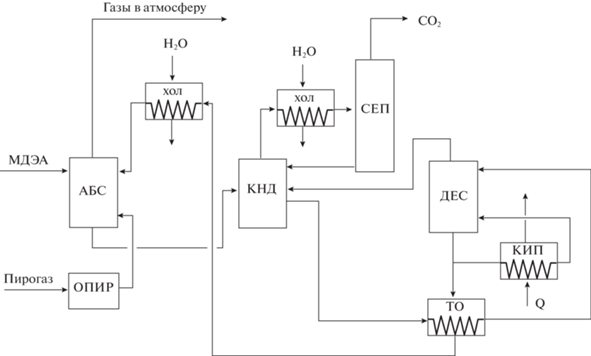
Результаты расчета базовой технологии плазменной переработки ОПП различного морфологического состава для производительности 12 500 т/г. при единичной мощности одного плазматрона 540 кВт приведены в табл. 2.
Таблица 2.
Результаты расчета базовой технологии плазменной переработки ОПП различного морфологического состава. Производительность по отходам 12 500 т/г.
Показатель | Морфологические виды отходов | ||||||
---|---|---|---|---|---|---|---|
ТКО | ТНО | ОПМ | АП | ОД | БО | МО | |
Дополнительное дутье О2 в плавильную камеру, кг/ч | 294 | 645 | 420 | 843 | 238 | 482 | 252 |
Выработка базальтоподобного шлака, т/год | 1213 | 1192 | 467 | 1450 | 604 | 580 | 2470 |
Количество СО2-плазмообразующего газа, кг/ч | 803 | 1174 | 950 | 1373 | 768 | 1012 | 782 |
Количество СО2, выделенное из пирогаза, кг/ч | 810 | 461 | 552 | 298 | 846 | 555 | 644 |
Содержание СО в пирогазе, кг/ч | 615 | 1652 | 1449 | 2043 | 515 | 1286 | 913 |
Содержание Н2 в пирогазе, кг/ч | 47 | 71 | 61 | 90 | 51 | 68 | 40 |
Мольное отношение Н2 : СО | 1.1 | 0.6 | 0.6 | 0.6 | 1.4 | 0.7 | 0.6 |
Прибыль/убыток базовой технологии, млн. руб./г. | –216 | –171 | –186 | –163 | –227 | –221 | 136 |
Наибольшее количество БПШ образуется при переработке медицинских отходов (МО) (2470 т/г.), наименьшее (467 т/г.) – при переработке отходов полимерных материалов. Наибольшее дополнительное дутье кислорода, обеспечивающее единичную мощность плазматрона 540 кВт, в случае переработки автомобильных покрышек (843 кг/ч), наименьшее (238 кг/ч) – при переработке отходов деревообработки. Не наблюдается корреляции между этими двумя параметрами – дополнительным дутьем кислорода в плавильную камеру и выработкой БПШ.
Степень извлечения СО2 из пирогаза во всех случаях составила ~95%. Для большинства отходов выполняется соотношение: количество СО2 – плазмообразующего газа, необходимого для функционирования ПЛ, больше, чем количество СО2, выделяемого из пирогаза. Для устойчивой работы базовой технологии необходимо, чтобы было обратное соотношение. Это возможно только при дополнительном вводе СО2 из внешних источников (рис. 2).
В пирогазе после абсорбционной очистки от СО2, в ходе которой удаляется основное количество Н2О, присутствуют СО, Н2 и СН4. Количество образующихся СО и Н2 в пирогазе при переработке отходов различного морфологического состава приведено в табл. 2. Мольное отношение Н2 : СО для этих отходов изменяется в пределах 0.6–1.4. Количество СН4 в пирогазе варьируется в пределах 75–571 кг/ч.
Базовая технология не обеспечивает положительных экономических результатов плазменной переработки отходов различного морфологического состава:
– при суммарных годовых капитальных затратах функционирования одного УПБ 2774 млн. руб. срок окупаемости базовой технологии при переработке всех видов отходов более 20 лет (горизонт планирования), за исключением переработки МО;
– при переработке только МО в количестве 12500 т/г. базовая технология окупится через 14.6 г. В течение данного срока годовая прибыль от переработки этих отходов составит 136 млн. руб./г.;
– при переработке других видов отходов по базовой технологии получения прибыли не происходит (табл. 2), технология в таком варианте является дотационной;
– положительные экономические результаты, полученные для МО, связаны в основном с высокой стоимостью переработки (25 000 руб./тонна) по сравнению с переработкой других отходов (руб./т): ТКО – 1500, ТНО – 4500, ОПМ – 3500, АП – 5000, ОД – 800, БО – 1200;
– локальная переработка такого количества МО вряд ли возможна, так как количество МО, накопленных за год в одном из крупнейших госпиталей России – госпитале им. Н.И. Бурденко, на порядок меньше ~1600 т/г. [8].
Таким образом, основными недостатками базовой технологии плазменной переработки отходов являются:
– отсутствие экономической эффективности;
– необходимость использования из внешних источников большого количества электроэнергии – 3660 кВт (2160 кВт – потребляемая мощность четырех плазматронов + 1500 кВт для функционирования инфраструктуры);
– необходимость использования из внешних источников дополнительного количества СО2 для обеспечения функционирования четырех плазматронов;
– не использование газовых энергетических компонентов пирогаза – СН4, СО и Н2.
Для устранения этих недостатков были разработаны АТ плазменной переработки отходов.
3. РЕЗУЛЬТАТЫ РАСЧЕТА АТ1: “КОМПЛЕКС ВТПК”
Эта АТ, предусматривающая объединение УПБ (одного или нескольких) с одной или несколькими газотурбинными установками (ГТУ), получила название “Комплекс ВТПК”. Принципиальная схема этой АТ приведена на рис. 4. В отличие от базовой технологии в случае АТ1 электроэнергию Е ПЛ получают от ГТУ. После выделения СО2 пирогаз, содержащий в основном СО, Н2 и СН4, направляется в ГТУ для смешивания с природным газом. СО2 выделяется также из газообразных продуктов ГТУ. Из ХРСО2 часть СО2 поступает в качестве плазмообразующего газа в ПЛ, а большая часть СО2 остается в ХРСО2 и реализуется внешним потребителям или выводится на захоронение. Необходимость выделения СО2 раздельно из пирогаза и из газообразных продуктов ГТУ обусловлена двумя основными факторами:
– количество СО2, выделяемое только из пирогаза, недостаточно для обеспечения всех ПЛ плазмообразующим газом;
– современными экологическими требованиями, предусматривающими снижение выбросов СО2 в атмосферу [26], высокими эмиссионными квотами для СО2 (на момент написания данной работы – 63 евро за тонну СО2) и стратегией низкоуглеродного развития России.
В Комплексе ВТПК в качестве ГТУ (рис. 4) предусмотрено использование ГТЭС Урал-6000 производства ОАО “Авиадвигатель” со следующими основными характеристиками:
− номинальный расход природного газа –2448 нм3/ч;
− номинальная мощность 6140 кВт;
− температура газа за силовой турбиной двигателя 474°С.
С использованием АТ1 Комплекса ВТПК ранее был выполнен технико-экономический анализ плазменной переработки:
− тяжелых нефтяных остатков в смеси с твердыми бытовыми отходами [10];
− смеси твердых бытовых отходов, МО и отработанных автомобильных покрышек [10];
− углеводородного сырья и углеводородных отходов [11];
− нефтесодержащих отходов [12];
− стеклосодержащих отходов [13];
− иловых отходов [14];
− отходов Байкальского целлюлозно-бумажного комбината [15];
− медицинских отходов [8, 27];
− смеси коммунальных, полимерных и медицинских отходов [28].
В данном обзоре для удобства сопоставления результатов с данными предыдущих исследований [9] были проведены дополнительные расчеты с использованием отходов следующего морфологического состава (мас. %): ТКО – 70, ТНО – 5, ОПМ – 5, АП – 7, ОД – 6, БО – 2, МО – 5. Выбор такой сложной смеси отходов демонстрировал возможности разработанной программы для расчета технико-экономических показателей при проектировании Комплекса с учетом преимущественного состава образующихся отходов в регионе. Результаты расчетов приведены в табл. 3.
Таблица 3.
Результаты расчета АТ1 Комплекса ВТПК по вариантам 1, 2 и 3
Параметр | Вариант 1 | Вариант 2 | Вариант 3 | ||||||||||||
---|---|---|---|---|---|---|---|---|---|---|---|---|---|---|---|
Производительность по отходам (т/г.)/число УПБ/число ПЛ | 12 500/1/4 | 25 000/2/8 | 50 000/4/16 | ||||||||||||
Число ГТУ в Комплексе | 0* | 1 | 2 | 3 | 4 | 0* | 2 | 4 | 6 | 8 | 0* | 4 | 8 | 12 | 16 |
Количество СО2 из газообразных продуктов ГТУ, кг/ч | 5572 | 9721 | 13 869 | 18 017 | 11 145 | 19 441 | 27 737 | 36 033 | 22 290 | 38 882 | 55 474 | 72 067 | |||
Степень внутреннего использования СО2 (w), массовые доли | 0.14 | 0.08 | 0.06 | 0.05 | 0.14 | 0.08 | 0.06 | 0.05 | 0.14 | 0.08 | 0.06 | 0.05 | |||
Суммарная установленная мощность ГТУ, кВт | 6140 | 12 280 | 18 420 | 24 560 | 12 280 | 24 560 | 36 840 | 49 120 | 24 560 | 49 120 | 73 680 | 98 240 | |||
Степень замещения природного газа синтез-газом, % | 24.2 | 12.1 | 8.1 | 6.1 | 24.2 | 12.1 | 8.1 | 6.1 | 24.2 | 12.1 | 8.1 | 6.1 | |||
Численность населения в зоне Комплекса по обеспечению Е и Т/по переработке отходов, чел. | 0/ 27778 | 20453/ 27778 | 75531/ 27778 | 130609/27778 | 185678/27778 | 0/55556 | 40906/ 55556 | 151062/ 55556 | 261218/ 55556 | 371374/ 55556 | 0/111111 | 81812/ 111111 | 302124/ 111111 | 522435/111111 | 742747/ 111111 |
Срок окупаемости, лет | Более 20 лет | Более 20 лет | Более 20 лет | 18.36 | 15.16 | Более 20 лет | Более 20 лет | 17.18 | 13.17 | 11.30 | Более 20 лет | Более 20 лет | 13.03 | 10.44 | 9.25 |
Прибыль/Убыток, млн. руб./г. | –191.5 | –158.7 | –39.5 | 79.6 | 161.5 | –232.4 | –119.3 | 119.2 | 286.2 | 477.0 | –268.7 | –42.7 | 347.5 | 729.2 | 1110.9 |
Сумма капитальных затрат, млн. руб. | 2774 | 4230 | 4641 | 5052 | 5462 | 3399 | 4834 | 5649 | 6465 | 7281 | 3852 | 6099 | 7730 | 9361 | 10 992 |
Проводили расчет трех вариантов для производительности Комплекса ВТПК 12 500, 25 000 и 50 000 т/г. Для этих производительностей число УПБ соответственно равно 1, 2 и 4, а суммарное количество плазматронов равно 4, 8 и 16 соответственно. Число установок ГТУ (NГТУ) варьировали в пределах от 1 до 16 (табл. 3). Расчеты всех вариантов проводили для электрической мощности одного плазматрона 540 кВт. В табл. 3 для сравнения всех указанных производительностей Комплекса ВТПК приведены результаты расчета базовой технологии (NГТУ = 0). Степень внутреннего использования СО2 (w) рассчитывали по формуле
где А – количество плазмообразующего СО2, кг/ч; С – количество СО2, выделенного из пирогаза, кг/ч; Д – количество СО2, выделенного из газообразных продуктов ГТУ, кг/ч.С увеличением NГТУ в Комплексе ВТПК для всех вариантов расчета происходит снижение w (с 0.14 до 0.05) и степени замещения природного газа горючими компонентами синтез-газа (с 24.1 до 6.1%) – табл. 3. В ходе расчета вариантов 1–3 АТ1 Комплекса ВТПК равные значения, не зависимые от NГТУ, имели исходные (расчетные) данные (табл. 4).
Таблица 4.
Исходные данные и результаты расчета АТ1 Комплекса ВТПК по вариантам 1, 2 и 3
Параметр | Вариант | ||
---|---|---|---|
1 | 2 | 3 | |
Производительность по отходам, т/г. | 12 500 | 25 000 | 50 000 |
Количество СО2, выделенного из пирогаза, кг/ч | 733 | 1466 | 2932 |
Количество СО2-плазмообразующего газа, кг/ч | 871 | 1741 | 3483 |
Дополнительное дутье кислорода в плавильную камеру УПБ, кг О2/ч | 341 | 682 | 1363 |
Суммарное количество плазматронов | 4 | 8 | 16 |
Количество синтез-газа (СН4+СО+Н2) после выделения СО2 из пирогаза, кг/ч | 1002 | 2004 | 4008 |
Выработка базальтоподобного шлака, т/г. | 1205 | 2410 | 4821 |
Поток пирогаза, кг/ч: СО | 830 | 1661 | 3322 |
Н2 | 52 | 104 | 208 |
СН4 | 73 | 146 | 292 |
Н2О | 645 | 1290 | 2580 |
СО2 | 772 | 1543 | 3086 |
О2 | 0 | 0 | 0 |
N2 | 5 | 11 | 21 |
Сумма | 2377 | 4754 | 9509 |
По результатам расчетов АТ1 Комплекса ВТПК (табл. 3, 4) можно сделать следующие основные выводы:
– для всех вариантов расчета с увеличением NГТУ в Комплексе ВТПК ожидаемо возрастает количество СО2, выделяемого из газообразных продуктов ГТУ (табл. 3);
– при увеличении как NГТУ, так и производительности Комплекса ВТПК значительно возрастает численность населения региона, обеспеченная тепловой и электрической энергией и возможностью переработки отходов (при норме переработки отходов 450 кг/год/чел) – табл. 3;
– увеличение производительности Комплекса ВТПК кратно увеличивает капитальные затраты (табл. 3). Введение каждой дополнительной ГТУ увеличивает сумму капитальных затрат на 411 млн. руб.;
– положительные экономические показатели Комплекса ВТПК достигаются только при высокой производительности по отходам и больших значениях NГТУ (табл. 3). Наилучшие достигаемые показатели (табл. 3) при производительности по отходам 50 000 т/г. и сроке окупаемости 9.25 лет: прибыль 1.1 млрд. руб. в год при капитальных затратах 11 млрд. руб.
Анализ вариантов расчета Комплекса ВТПК показывает, что АТ1, обеспечивая решение основной задачи – переработку отходов, не обладает достаточными экономическими преимуществами (высокие капитальные затраты, большой срок окупаемости, относительно низкая прибыль). Более того, в области положительных экономических результатов снижаются экологические показатели процесса – минимальные значения имеет степень внутреннего использования СО2 (w) и степень замещения природного газа горючими компонентами синтез-газа. Нерешенной остается проблема использования большого количества СО2, выделенного из пирогаза и газообразных продуктов ГТУ. Поэтому поиск АТ, позволяющих улучшить и экономические, и экологические показатели плазменной переработки отходов, был продолжен.
4. РЕЗУЛЬТАТЫ РАСЧЕТА АТ2: “КОМПЛЕКС ВТПК + Н2”
Вариант 1. Одним из наиболее простых способов улучшить экономические показатели плазменной переработки отходов является выделение водорода из пирогаза с помощью короткоцикловой адсорбции (КЦА) [29] и реализации его на внешнем рынке или использовании внутри агро-промышленно-коммунального кластера (АПКК) в блоке химической переработки (БХП). При производительности Комплекса 25 000 т/г. содержание водорода в пирогазе при плазменной переработке отходов различного морфологического состава находится в узком интервале 90–100 кг/ч [30]. Принципиальная схема варианта 1 АТ2 приведена на рис. 5.
Очищенный пирогаз после стадии выделения СО2 (ВСО2), содержащий Н2, СО, СН4, Н2О, проходит сероочистку (на рис. 5 не показано). Сероочистку проводят при температуре 30–40°С, давлении 2.2 МПа в трех адсорберах, загруженных цеолитом NaX (первый адсорбер – на стадии очистки, второй – на стадии охлаждения, третий – на стадии регенерации). После сероочистки газовый поток направляют на стадию КЦА, где происходит очистка водородсодержащего газа от примесей (СО, СО2, СН4, Н2О) при температуре 30–40°С и давлении 2.1 МПа. Очистка происходит в четырех адсорберах, замкнутых в периодические циклы адсорбции–десорбции. Каждый из адсорберов имеет три последовательных слоя адсорбента: первый слой (нижний) – корунд для удаления основной массы воды; второй слой (средний) содержит активированный уголь для удаления СО2 и СН4; третий слой (верхний) содержит цеолиты для удаления СО и N2. КЦА обеспечивает получение водорода с чистотой 99.9999%. Обычно степень извлечения Н2 составляет 75–85% [29]. После КЦА кроме водорода получают сбросный газ, содержащий в основном СО и СН4 и следы Н2О, СО2 и Н2, который направляют на установку ГТУ и используют для частичной замены природного газа.
Этот вариант при производительности Комплекса по отходам 25 000 т/г. позволяет с использованием доступных и отработанных методов выделять из пирогаза водород в количестве ~80 кг/ч. При реальном времени эксплуатации Комплекса в течение года 7446 ч и стоимости водорода 165 390 руб./т дополнительная годовая прибыль от реализации водорода может достигать 90–100 млн. руб. Акцент на выделение водорода из пирогаза сделан не случайно – водород является одним из наиболее востребованных энергоносителей во всем мире, для получения которого обычно используют сложные энергозатратные технологии [31, 32]. Производство водорода в мире растет на 3–4% в год и в настоящее время составляет ~120 млн. т/г. Диапазон оценок мирового рынка водорода к середине века широкий, верхняя планка находится на уровне 700 млн. т/г. В ближайшие три года Россия планирует направить на развитие водородной энергетики 9 млрд. руб. Преимущества плазменной технологии получения водорода из отходов заключаются в получении дешевого водорода (затраты на его получение связаны в основном с установкой разделения пирогаза методом КЦА и окупаются уже в первый год эксплуатации установки) и использовании возобновляемого сырья (отходов).
Однако вариант 1 Комплекса ВТПК + Н2 не решает задачу утилизации и/или использования СО2.
Вариант 2. Этот вариант Комплекса ВТПК + + Н2, так же как и вариант 1, предусматривает выделение водорода из пирогаза с помощью КЦА, а отличием является то, что выделяемый из пирогаза и газообразных продуктов ГТУ СО2 последовательно подвергают углекислотному риформингу (УКР) с получением смеси СО + Н2, разделением этой смеси методом КЦА, паровой конверсией СО (ПКСО) с получением смеси СО2 и Н2 и выделением СО2 абсорбционным методом. Принципиальная технологическая схема плазменной переработки отходов по варианту 2 АТ2 приведена на рис. 6. Ниже приведены основные технологические особенности и элементы аппаратурного оформления стадий УКР и ПКСО.
Углекислотный риформинг. Использование стадии УКР в процессе плазменной переработки ОПП описано в [11, 33]. Эта стадия включена в состав Комплекса ВТПК с целью получения синтез-газа (СО + Н2) и дальнейшего его использования только в процессе Фишера–Тропша для получения углеводородов. Не предусматривалось выделение водорода (как товарного продукта) из синтез-газа. В варианте 2 АТ2 выбор УКР для превращения СО2, полученного в Комплексе ВТПК + Н2, был основан на следующем:
– в УКР в качестве исходных реагентов используются СО2 и СН4, которые уже имеются в Комплексе;
– продуктами УКР являются СО и Н2, разделить которые можно на стадии КЦА, входящей в состав Комплекса;
– СО может быть превращен в водород и СО2 в процессе ПКСО с разделением Н2 и СО2 и возвратом СО2 на стадию УКР;
– использование УКР позволяет проводить процесс совместного получения водорода и плазменной переработки ОПП с реализацией замкнутого цикла по СО2, что кратно увеличивает экологическую привлекательность предлагаемой технологии.
УКР подробно описан в [34]. Основной реакцией этого процесса является
(2)
$\begin{gathered} {\text{С}}{{{\text{Н}}}_{4}} + {\text{С}}{{{\text{О}}}_{{\text{2}}}} \rightleftarrows 2{\text{СО}} + 2{{{\text{Н}}}_{2}}, \\ \Delta Н = + 247{\text{ кДж/моль}}. \\ \end{gathered} $Так как реакция сильно эндотермическая (ΔН > 0) и сопровождается увеличением объема, она протекает в области высоких температур 600–900°С и невысоких давлений – обычно 0.1 МПа (1 атм.). При атмосферном давлении и температуре 900°С выход Н2 и СО приближается к 100%.
Реакция (2) каталитическая. Предложено много различных катализаторов этого процесса, которые подробно описаны в [34]. Обычно используют никелевые или платиновые катализаторы. Основным препятствием к использованию Ni-катализаторов является их легкая дезактивация коксовыми отложениями, образующимися в условиях основной реакции (2) за счет протекания диссоциации метана
(3)
${\text{С}}{{{\text{Н}}}_{4}} \rightleftarrows {\text{С}} + 2{{{\text{Н}}}_{2}},\quad \Delta Н = + 75{\text{ кДж/моль\;}}~~~~$(4)
$2{\text{СО}} \rightleftarrows {\text{С}} + {\text{С}}{{{\text{О}}}_{{\text{2}}}},\quad \Delta Н = --173{\text{ кДж/моль}}{\text{.\;}}~$Другой проблемой УКР являются высокие температуры. Однако в условиях работы Комплекса эти проблемы могут быть решены за счет получения высокотемпературных потоков на различных стадиях и возможности организации теплообмена для реализации основной реакции (2).
Среди никелевых катализаторов наибольшее распространение получил Ni/Al2O3, который проявляет высокую активность на начальной стадии, но достаточно быстро закоксовывается. Никелевые катализаторы Ni/MgO, Ni/CaO, Ni/MnO и Ni/ZrO2 проявляли большую устойчивость в отношении коксообразования. Никелевый катализатор Ni0.03Mg0.97О, представляющий собой твердый раствор NiOиMgO и полученный методом соосаждения солей Ni и Mg, имел значительно более высокую коксоустойчивость [35] по сравнению с катализаторами Ni/Al2O3 и Ni/SiO2. Конверсия смеси СН4 + СО2 на катализаторе Ni0.03Mg0.97О при 850°С и давлении 0.1–0.2 МПа стабильно составляла 100%. Промотирование этого катализатора благородными металлам (Pt, Pd, Rh) значительно снижает углеотложение и увеличивает стабильность его работы при высоких температурах. Большое влияние на активность, селективность, стабильность и склонность к коксообразованию оказывает метод приготовления катализатора и выбранные для этого исходные реагенты и модифицирующие добавки. Так, катализатор Ni/MgO, промотированный Cr2O3, имеющий состав: 6% Ni, 1% Cr2O3, 93% MgO, обеспечивал высокую конверсию уже при температуре 700°С. Схожую с никелевыми активность и стабильность проявляют кобальтовые катализаторы. Металлы платиновой группы (Pt, Pd, Ru, Rh) в УКР метана более активны, чем Ni- и Co-катализаторы. Реакция протекает со значительной скоростью уже при 500°С. Из нанесенных на Al2O3, MgO и ZrO2 металлов наиболее активны Ru и Rh.
В [36, 37] предложено проводить УКР в присутствии алюминидов никеля Ni3Al, который готовили самораспространяющимся высокотемпературным синтезом (СВС) из спрессованных порошков Ni и Al с последующим просеиванием катализатора и отбором нужной фракции [37]. При температуре 1223 К этот катализатор обеспечивал конверсию СО2 82.2%, а СН4 79.6%. Выход синтез-газа (СО + Н2) составил 80.9%. Дополнительное введение в состав Ni3Al никеля (5–10%) и молибдена (2–10%) [36] улучшает каталитические свойства образцов: конверсия СО2 возрастает до 99%, конверсия СН4 – до 89%, а выход синтез-газа возрастает до 90%. Дополнительное введение никеля и молибдена улучшало стабильность работы катализатора.
Перспективными катализаторами УКР являются биметаллические катализаторы Ni–Ru и Ni–Rh и карбид молибдена [38, 39].
В настоящее время одним из главных направлений в решении проблемы поиска катализаторов УКР является разработка улучшенных никелевых систем, которые способствовали бы кинетическому ингибированию образования углерода на их поверхности в условиях, термодинамически благоприятных для углеотложения, в результате сочетания с подходящими носителями, такими как La2O3, MgO, TiO2, CeO2, с помощью эффективных промоторов, включая La2O3, Li2O и др., а также новых методов приготовления, таких как метод кристаллизации в твердой фазе, золь-гель-метод, цитратный метод [40–43].
В [44] в качестве катализаторов УКР использованы керамические Ni–Co-мембраны. Для приготовления катализатора использовали порошки Ni (содержащего 10% Al) и Со3О4 в соотношении 1 : 1. Катализатор получали методом СВС. УКР метана проводили в проточном реакторе с установленной каталитической мембраной или загруженными гранулами катализатора в следующих условиях: СН4:СО2 = 1:1, Т = 400–800°С, w = 20–750 л/ч, Рвход = 1.1 атм., Рвыход = 1 атм. Использование этого катализатора позволяет значительно снизить содержание углерода в катализаторе.
Среди методов получения нанесенных металлических (никелевых, кобальтовых, платиновых и др.) катализаторов для их использования, в том числе, в процессе УКР эффективным может оказаться электроконденсационный метод получения высокодисперсных металлов (золей металлов) в жидкой фазе в сочетании с гетерокоагуляцией золя металла на поверхности неорганического носителя [45–51].
Добавки La2O3, CeO2 к Ni/Al2O3 улучшают показатели УКР – увеличивают активность и стабильность работы катализатора [52]. Катализатор Ni/Al2O3, модифицированный La2O3, обеспечивает практически 100%-ную селективность по водороду. В процессе УКР использование Ni/Al2O3, модифицированного редкоземельными металлами, позволяет регулировать соотношение Н2:СО. Платиновые катализаторы Pt/CeO2 активны в процессе УКР метана при температурах менее 650°С [52].
Активными катализаторами в УКР являются NdCaCoO4 со слоистой перовскитоподобной структурой и мезопористый 20%Co/SiO2, которые позволяют получать стабильные значения конверсии метана, углекислого газа и выхода синтез-газа [53]. Катализатор NdCaNiOn при 850°С обеспечивал высокие степени конверсии СО2 (86%) при выходе СО 88%, водорода 78%. При 940°С выход СО приближается к количественному (97%) [54].
Механизм и кинетика УКР подробно описаны в [34, 55] и в настоящем обзоре не обсуждаются.
Технологические аспекты УКР. Промышленной реализации УКР препятствуют два основных фактора: высокая эндотермичность процесса (необходимость высоких энергозатрат) и низкая стабильность катализатора по отношению к закоксовыванию [34]. Именно поэтому в литературе имеется ограниченное число публикаций, касающихся технологии УКР, и основное внимание уделяется паровому риформингу метана и автотермическому риформингу как наиболее экономичным методам получения водорода.
Зарубежными фирмами “Caloric” и “HaldorTorsoe” разработаны две технологии УКР: Calcor и Sparg [56, 57].
Практически отсутствует информация по использованию УКР в процессе плазменной переработки ОПП с целью получения водорода.
Большинство работ, посвященных УКР, описывают процесс в традиционных проточных реакторах с насыпным катализатором (трубчатые реакторы), в которых высокие конверсии по реагентам достигаются за счет высоких температур (800–1100°С). Традиционным УКР в синтез-газ является процесс, осуществляемый в проточном трубчатом реакторе (так называемый трубчатый реактор с внешним обогревом, рис. 7) при 1073 К, давлении 1 атм и использовании в качестве катализатора Ni/Al2O3 [58]. В этих условиях удается достичь конверсии СН4 и СО2 ~96% при отношении Н2:СО ~ 0.96. Основным недостатком этого процесса является быстрая дезактивация катализатора из-за высокой доли процессов коксообразования. Проведение УКР в присутствии катализаторов на основе благородных металлов (Pt, Pd/Al2O3, Pt,Pd/SiO2, Pt,Pd/CeO2, Pt,Pd/ZrO2) на том же традиционном оборудовании позволяет снизить температуру процесса в среднем на 200°С и уменьшить коксообразование, но высокая стоимость этих катализаторов сдерживает их внедрение. Использование трубчатых каталитических реакторов для проведения эндотермических химических процессов достаточно хорошо известно [59, 60].
Рис. 7.
Принципиальная технологическая схема трубчатого каталитического реактора с внешним обогревом для проведения эндотермических реакций. Жирной линией показано движение теплоносителя в межтрубном пространстве.
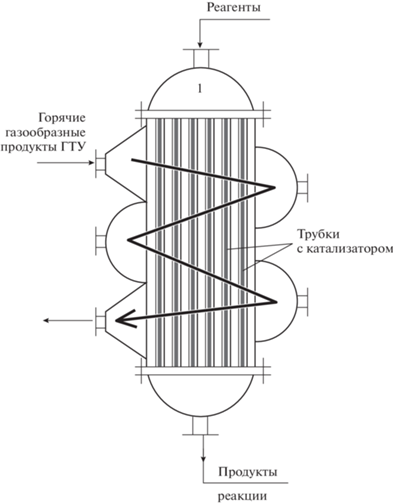
Реактор с внешним обогревом использован в [61]. Он представляет собой цилиндр из термостойкого материала (кварц) с расположенным внутри неподвижным слоем катализатора. Для обогрева реактора используют внешний источник – трубчатую печь. УКР метана проводят при температуре 850°С. В качестве катализатора используют Ni/Al2O3. В этих условиях удается достичь конверсии метана и СО2 ~95% при соотношении Н2:СО ~ 0.95.
В [58] в качестве реакторного блока для проведения УКР предложено использовать пористый керамический каталитический модуль, который представляет собой продукт термического синтеза уплотненной методом вибропрессования высокодисперсной экзотермической смеси никеля и алюминия. Смесь содержит (мас. %): никель 56–96 и алюминий 4–44. Пористый керамический каталитический модуль может дополнительно содержать карбид титана в количестве 20 мас. % по отношению к массе модуля, а также каталитическое покрытие в количестве 0.002–6 мас. % по отношению к массе модуля, включающее: La и MgO или Ce и MgO, или La, Ce и MgO, или ZrO2, Y2O3 и MgO, или Pt и MgO, или W2O5 и MgO. Синтез-газ получают путем конверсии смеси метана и углекислого газа при температуре 450–700°С и давлении 1–10 атм. в фильтрационном режиме на пористом керамическом каталитическом модуле при скорости подачи смеси метана и углекислого газа через модуль, равной 500–5000 ч–1. Предложенная технология и оборудование позволяют проводить процесс при более низких температурах и получать селективность по синтез-газу, близкую к 90%.
Применение реакторов из керамических материалов для УКР описано и в других работах. Так, в [62] предложена конструкция каталитического реактора с керамическими обогревательными трубами, допускающая длительную эксплуатацию при высоких температурах.
Использование для УКР мембранного реактора и мембранного катализатора на основе карбида молибдена (Мо2С) [63] вряд ли в ближайшее время будет реализовано в промышленности в основном из-за относительно невысокого содержания каталитического компонента в мембранных катализаторах (каталитических мембранах) и, как следствие, невозможности обеспечить необходимую производительность мембранного каталитического реактора. Устранение этого недостатка путем размещения катализатора в виде неподвижного слоя частиц в мембранном реакторе с селективной мембраной [63] значительно усложняет конструкцию реактора. Для синтеза катализатора Мо2С, так же как и нитрида алюминия, помимо СВС [37] может быть использован электроэрозионный метод [64].
В [11, 52, 65] предложен кольцевой плазменный реактор (рис. 8) для проведения эндотермических процессов, в том числе УКР. Основными отличительными особенностями этого реактора являются:
Рис. 8.
Принципиальная схема кольцевого плазменного реактора для проведения эндотермических каталитических реакций: 1 – плазматрон, 2 – плазмохимическая зона, 3 – термоизоляционная (керамическая) перегородка, 4 – буферная зона, 5 – кольцевой слой катализатора, 6 – отражающая перегородка, 7 – направляющая перегородка.
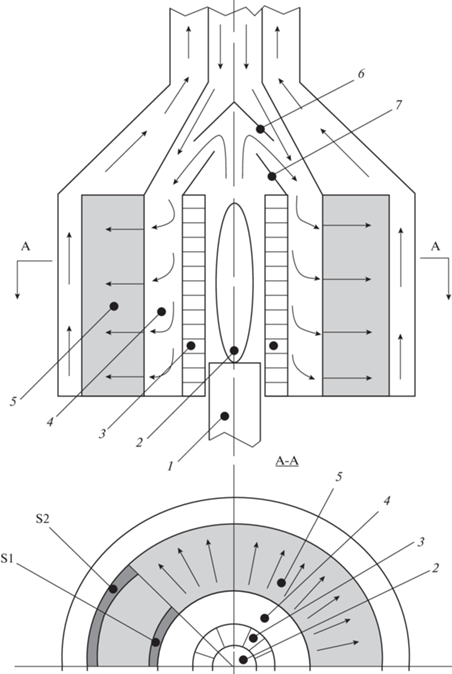
– слой катализатора имеет форму кольца, в котором движение реагентов осуществляется в радиальном направлении. Ширина кольца определяется несколькими параметрами, основными из которых являются: невысокий градиент температур в слое катализатора, обеспечивающий протекание реакции в заданном температурном интервале; объем элементарного слоя катализатора должен быть таким, чтобы выполнялось соотношение S2/S1 = 2 (рис. 8). Это соотношение вытекает из факта увеличения давления в реакторе приблизительно в 2 раза, для стабилизации давления необходимо соответствующее увеличение объема;
– устройством, обеспечивающим нагрев реагентов и катализатора, является ПЛ, потребляющий в качестве рабочего газа диоксид углерода. Нагретые продукты плазмохимического превращения диоксида углерода смешиваются в буферной зоне с исходным диоксидом углерода и направляются непосредственно в зону каталитической реакции;
– температура процесса регулируется параметрами работы ПЛ, размером плазмохимической зоны (за счет перемещения плазмотрона вдоль своей оси) и соотношением продуктов плазмохимического превращения и сырьевого диоксида углерода.
Увеличение производительности процесса с использованием этого реактора достигается оптимальной организацией теплообмена, радиальным движением реакционной смеси и вовлечением в реакцию продуктов плазмохимического превращения рабочего газа ПЛ, которые инициируют протекание процесса в сторону образования основных продуктов реакции.
Полученный в результате УКР синтез-газ (СО + Н2) направляют на установку КЦА для выделения Н2 и объединения его с основным потоком Н2, выделенным из пирогаза, а СО направляют на установку ПКСО для дополнительного получения водорода.
Паровая конверсия монооксида углерода. Реакция ПКСО
(5)
${\text{СО}} + {{{\text{Н}}}_{2}}{\text{О}} \leftrightarrows {\text{С}}{{{\text{О}}}_{2}} + {{{\text{Н}}}_{2}}$Катализаторы высокотемпературной ПКСО. Традиционный высокотемпературный катализатор ПКСО, используемый в промышленности, – двойной оксид железа и хрома, интервал рабочих температур 310–480°С. Этот катализатор показывает удовлетворительную активность и хорошую термостойкость, поскольку активатор (хром) действует как структурный стабилизатор. Преимуществами промышленного катализатора являются также низкая стоимость, возможность длительного использования и устойчивость к сере. Активность катализатора Fe3O4/Cr2O3 может быть увеличена путем легирования оксидов железа и хрома небольшими добавками CuO, CoO, ZnO [68]. Реакция ПКСО значительно ускоряется, если добавить к Fe3O4/Cr2O3 небольшое количество родия [69]. В [70] был использован катализатор на основе железа, промотированный оксидами Ce и Al. Его активность и термостойкость оказались такими же, как у коммерческого катализатора Fe3O4/Cr2O3. Была показана возможность отказа от Cr как высокотоксичного компонента катализатора.
Катализаторы низкотемпературной ПКСО. Стандартный катализатор для реакции низкотемпературной ПКСО (CuO/ZnO/Al2O3) работоспособен в интервале температур 160–250°С при контакте с воздухом. При температуре 300°С катализатор дезактивируется. В [71] на этой стадии реакции были испытаны катализаторы Pt/ZrO2 и Pt/TiO2 с добавками рения, которые проявили высокую активность в основном за счет увеличения реакционной способности адсорбированного монооксида углерода по отношению к водяному пару.
В [72] установили высокую каталитическую активность карбида молибдена (Мо2С) в реакции паровой конверсии – он более активен, чем коммерческий катализатор CuO/ZnO/Al2O3 в реакции, осуществляемой при атмосферном давлении и температуре 220–295°С. Карбид молибдена не катализирует реакцию метанирования. Основным методом синтеза карбида молибдена является окисление молибдена до МоО3 с последующим его восстановлением до Мо2С при 700°С водородом. Мо2С может быть также получен электроконденсационным или электроэрозионным методом [48, 49]. Карбиды молибдена и вольфрама проявляли высокую каталитическую активность не только в процессе ПКСО, но и в УКР метана.
На современных производствах водорода паровой конверсией СО имеется стадия только высокотемпературной (ВТ) конверсии, а оставшееся количество СО удаляют в процессе очистки на стадии КЦА [73]. Новые катализаторы стадии ВТ‑конверсии проводят при температуре на входе 320–350°С и отношении пар : СО, равном 0.4‒0.6. Получение медьсодержащего катализатора паровой конверсией СО описано в патенте [74].
В последнее время разработана среднетемпературная (СТ) конверсия СО, в которой ВТ- и низкотемпературная (НТ) конверсии объединены в одну стадию. Используются катализаторы на основе меди, что позволяет снизить отношение пар/углерод, уменьшить спекание и нежелательные реакции Фишера–Тропша. Однако в одностадийной СТ-конверсии возможны перегревы выше 350°С. Кроме того, особенности кинетики на стадии СТ-конверсии могут приводить к нежелательному процессу образования метанола. Превращение СО в СТ-конверсии ниже, чем в ВТ, но значительно выше, чем в НТ, и приближается к равновесию [73].
Процесс ПКСО может быть осуществлен в трубчатом реакторе, схема которого была приведена выше. Теплоносителем могут быть газовые продукты ГТУ, пирогаз или другой приемлемый теплоноситель.
Приведенные выше данные об УКР метана и ПКСО позволили объединить эти каталитические стадии с процессом плазменной переработки отходов для синтеза схемы одновременной переработки отходов и получения водорода, полностью исключающей (или значительно снижающей) выбросы СО2 в атмосферу (рис. 6).
Предлагаемая схема получения водорода в процессе плазменной переработки ОПП с включением стадий УКР и ПКСО использует наиболее теплосодержащие газовые потоки (пирогаз и газообразные продукты ГТУ) непосредственно в самой схеме – для обеспечения высоких температур на стадиях УКР и ПКСО, тем самым значительно улучшая технико-экономические показатели процесса.
Другие подобные решения (например, [75]), предусматривающие разработку “высокоэффективного энерготехнологического комплекса по использованию природного газа для производства электроэнергии, тепла и синтетического жидкого топлива с частичным секвестированием выбросов диоксида углерода в атмосферу”, имеют существенные отличия от предлагаемой технологии, основные из которых следующие:
− не предусматривают переработку ОПП;
− не предусматривают получение товарного водорода;
− плазменную технологию используют для проведения комбинированного паро-углекислотного риформинга метана при 1100–1500°С
(6)
${\text{С}}{{{\text{Н}}}_{4}} + 0.33{\text{ С}}{{{\text{О}}}_{2}} + 0.66{{{\text{Н}}}_{2}}{\text{О}} = 2.66{{{\text{Н}}}_{2}} + 1.33{\text{СО\;}}$− снижение выбросов СО2 в атмосферу составляет лишь ~30%.
Использование АТ2 Комплекса ВТПК + Н2 по варианту 2 для переработки ОПП с добавлением стадий КЦА, УКР метана и ПКСО и объединение этих стадий в единое целое (рис. 6) позволит значительно снизить затраты на производство водорода по сравнению с процессами электролиза воды, плазменного пиролиза метана и парового риформинга метана (последний считается наиболее дешевым промышленным методом получения водорода) и позволит осуществить практически полную переработку пирогаза.
Получение водорода в процессе переработки ОПП с использованием предлагаемой технологии по схеме: ВТПК → выделение СО2 → УКР метана → паровая конверсия СО в Н2 позволяет использовать весь полученный Н2 в газовых турбинах на метано-водородном топливе для получения энергии (электрической, тепловой) для работы самого Комплекса. Такая организация процесса позволит создать замкнутый цикл не только по СО2, но и по энергоносителям, значительно снижая потребление СН4 из внешних источников.
В результате выделения СО2 и его переработки по варианту 2 АТ2 Комплекса ВТПК + Н2 по предлагаемой схеме (рис. 6) с конверсией 90% на обеих стадиях (УКР и ПКСО) может быть получено ~2500 кг/ч водорода (при производительности Комплекса по отходам 25 000 т/г.). При стоимости водорода 165 390 руб./т и реальном времени эксплуатации Комплекса в течение года 7446 ч дополнительная прибыль от реализации водорода составит ~3 млрд. руб. Одновременно со значительным увеличением прибыли и улучшения экологических показателей процесса за счет более чем 80%-ного внутреннего использования СО2 значительно возрастают капитальные затраты (до нескольких десятков млрд. рублей) за счет использования энерго- и материалоемких каталитических технологий, что сдерживает внедрение этой технологии.
НИЦ “Курчатовский институт” имеет опыт в создании плазменных технологий получения водорода с использованием СО2. Еще в 70–80-х гг. прошлого века по инициативе и под руководством акад. В.А. Легасова был разработан процесс “Повод” (“Получение водорода”) для обеспечения постоянной выходной мощности АЭС, что позволяло значительно улучшить работу АЭС в течение всего периода ее работы: при избытке вырабатываемой электроэнергии часть ее использовалась в плазматроне для выработки водорода, который мог сжигаться в газовой турбине той же АЭС при пиковых нагрузках. Получение водорода на установке “Повод” проводили следующим образом. СО2 предварительно вводили в установку в требуемом количестве. На первой стадии СО2 превращался в плазмохимическом реакторе:
Конверсия СО2 составляла 35–40%. При большей конверсии СО2 получаемая смесь газов взрывоопасна. Разделение газовой смеси проводили в системе мембранных разделителей. Выделенный СО2 возвращали в процесс, а монооксид углерода направляли на стадию ПКСО:
(8)
${\text{СО}} + {{{\text{Н}}}_{2}}{\text{О}} = {\text{С}}{{{\text{О}}}_{2}} + {{{\text{Н}}}_{2}},$Реакция (7) может быть использована как универсальный метод снижения выбросов СО2 [45], обогащения атмосферы кислородом, а после выделения СО и для получения водорода с использованием ПКСО по реакции (8).
5. РЕЗУЛЬТАТЫ РАСЧЕТА АТ3: “КОМПЛЕКС ВТПК + БАТ”
АТ3 была разработана как наиболее эффективный и менее затратный способ связывания образующегося СО2 с помощью микроводорослей (МВ) [26, 76–78]. Механизм фиксации углекислого газа МВ подробно описан в [77, 79]. Преимущество использования МВ для улавливания СО2 заключается в том, что захваченный биомассой МВ углерод доступен для преобразования в продукты с высокой добавленной стоимостью [80].
Среди всех видов зеленых водорослей наиболее коммерчески успешными и широко используемыми в промышленности являются представители рода хлорелла, которые при включении в рацион животных способны оказывать благоприятное воздействие на многие показатели их роста и здоровья. В частности, при добавлении в рацион животных Chlorella vulgaris происходит улучшение показателей эффективности использования корма, а также выживаемости за счет повышения иммунитета и устойчивости к болезням. Данные эффекты связаны с наличием у Chlorella vulgaris так называемого фактора роста хлореллы (CGF), состоящего из определенного набора сахаров, нуклеиновых кислот, пептидов, белков и витаминов, не встречающегося у других МВ [81]. С точки зрения питательной ценности МВ Chlorella vulgaris содержат 61.6% белков, 12.5% жиров, 13.7% углеводов, а также более 20 витаминов и минералов, таких как железо, калий, кальций, фосфор, магний, провитамин А, инозитол, биотин, фолиевую кислоту и все незаменимые аминокислоты, что делает их хорошей пищевой или кормовой добавкой, обеспечивающей естественный цельный рацион. Кроме того, Chlorella vulgaris содержит пигменты хлорофиллы и каротиноиды в количестве ~4000 мг в 1 кг биомассы и является одним из немногих среди известных на данный момент видов, способных производить сразу несколько каротиноидов, выполняющих в организме животных функцию антиоксидантов [81].
Помимо использования биомассы МВ в качестве пищи и источника ценных для фармацевтической промышленности веществ МВ могут служить источником сырья для производства различных видов возобновляемого биотоплива, например биодизеля, биоводорода, биометана и биоэтанола. Биодизельное топливо (БТ) широко известно [82, 83] как один из источников энергии, получаемой из возобновляемого биологического материала путем переэтерификации низшими спиртами.
Для решения проблемы утилизации вырабатываемого в унитарном плазменном блоке и ГТУ СО2 было предложено дополнить Комплекс ВТПК блоком алга-технологий (БАТ) [17, 19, 20], в котором СО2 использовался для производства микроводорослей Chlorella vulgaris с последующей их переработкой в БТ, биомассу и глицерин (ГЛ). Принципиальная технологическая схема Комплекса ВТПК + БАТ приведена на рис. 9.
Процесс непрерывного производства биомассы и последующего получения БТ из микроводорослей Chlorella vulgaris состоит из трех основных этапов (разведения и выращивания МВ, сбора урожая, получения биомассы и БТ) и заключается в следующем:
− в специальных емкостях (инкубаторах-смесителях, ИС) готовится семенной материал МВ Chlorella vulgaris;
− полученный семенной материал направляется в фотобиореакторы (ФБР), наполненные водой, химический состав которой обеспечивает максимальный темп роста МВ;
− в процессе роста рабочих клеток МВ полученная биомасса (водно-водорослевая суспензия) насыщается углекислым газом, что при наличии постоянного освещения и поддержания постоянной положительной температуры способствует ускоренному фотосинтезу и размножению МВ, при котором они активно поглощают углекислый газ и одновременно выделяют в атмосферу кислород как продукт жизнедеятельности.
После достижения МВ максимального прироста по массе (от 30 до 50 раз) вся эта зеленая биомасса автоматически отгружается в сепаратор (СЕП), где происходит отделение от нее воды, которая вместе с питательными веществами, оставшимися в ней, через систему восстановления воды (оборотная вода, ОВ) возвращается в ФБР.
Полученная в результате сепарации пастообразная алга-биомасса поступает на пресс (ПР), где под давлением разрушаются стенки клеток МВ и из них выделяется жидкость (масло с остатками воды), а балластная алга-биомасса (отжим, жмых) отделяется. Отжим (жмых) алга-биомассы (АБМ) удаляется, а жидкая масляно-водяная смесь подается на центрифугу (ЦФ), где происходит окончательное отделение алга-масла (МС) от воды. Оборотная вода, содержащая питательные вещества, также возвращается через систему восстановления воды в ФБР. Отжим (жмых) АБМ влажностью до 50% отправляется в расходно-накопительный резервуар, откуда он отгружается внешним потребителям как питательная смесь для сельскохозяйственных животных, птиц и рыб, как удобрение в различных сферах применения или для другого применения. Подробно процесс получения алга-биомассы и БТ описан в [84–88].
Поскольку жизненный цикл МВ определяется в основном условиями фотосинтеза, расчеты проводили при различной площади БАТ (4–20 га), обеспечивающей различный выход продуктов фотосинтеза, прежде всего триглицеридов жирных кислот (ТЖК) – исходных веществ для синтеза метиловых эфиров жирных кислот (МЭЖК), применяемых как эффективная добавка к дизельному топливу:
(9)
$\begin{gathered} {{R}_{1}}({\text{O}}){\text{COC}}{{{\text{H}}}_{2}}{\text{CH}}\left( {{\text{OC}}({\text{O}}){{R}_{2}}} \right){\text{C}}{{{\text{H}}}_{2}}{\text{OC}}({\text{O}}){{R}_{3}} + 3Me{\text{OH }} = {\text{HOC}}{{{\text{H}}}_{2}}{\text{CH}}\left( {{\text{OH}}} \right){\text{C}}{{{\text{H}}}_{2}}{\text{OH}} + \\ {\text{ (ТЖК)}}\quad \quad \quad \quad {\text{(Метанол) (ГЛ)}} \\ + \;Me{\text{OC}}({\text{O}}){{R}_{1}} + Me{\text{OC}}({\text{O}}){{R}_{2}} + Me{\text{OC}}({\text{O}}){{R}_{3}}, \\ \left( {{\text{МЭЖК}}} \right) \\ \end{gathered} $Для увеличения выхода МЭЖК перед переэтерификацией метанолом ТЖК могут быть облагорожены гидрированием водородом в присутствии Ni–Cu/CeO2–ZrO2-катализатора под давлением водорода 1.0 МПа в интервале температур 300–380°С [89]. Аналогичное решение было предложено в [90] с использованием промышленных катализаторов гидроочистки МоО3(12%) + + СоО(4%)/Al2O3 и Со(14.38%) + Мо(3.93%)/Al2O3. Гидрирование проводили при температуре 330°С и парциальном давлении водорода 2–5 МПа.
ТЖК помимо переэтерификации метанолом могут непосредственно быть переработаны в компоненты моторных топлив. В [91] гидрировали ТЖК при температуре 420–560°С и давлении водорода 5 МПа в присутствии модифицированного промышленного алюмоплатинового катализатора марки АП-64 (~0.64 мас. % Pt на Al2O3). Выход компонентов дизельного топлива (алканов С17–С21) достигает 48–64%. После переэтерификации метанолом глицеринсодержащие отходы производства МЭЖК могут быть переработаны с использованием различных технологий [92], в том числе в реакторе колонного типа со стационарным слоем катализатора с целью извлечения ГЛ [93].
По сравнению с другими растительными источниками производства БТ (табл. 6) использование МВ позволяет получать значительно большее количество МС с высоким содержанием энергетических компонентов. Кроме того, сырье растительного происхождения составляет конкуренцию пищевым продуктам. Для производства исходных масел требуются значительная площадь сельскохозяйственных земель и значительные затраты энергии на выращивание, сбор и переработку этих культур. Альтернативой животному и растительному сырью являются МВ, которые позволяют снизить стоимость производства БТ из-за более высокого выхода масла (табл. 6). Кроме того, БТ на основе МВ не будет вступать в конкуренцию с производством пищевых продуктов и получением другой сельскохозяйственной продукции.
Таблица 5.
Выработка биотоплива из различных источников
Источники получения биотоплива из масла | Удельное содержание масла, л/га/г. | Удельное содержание энергии, МВт ⋅ ч/г. |
---|---|---|
Соя | 446 | 4 |
Подсолнечник | 952 | 9 |
Рапс | 1190 | 11 |
Касторовые семена | 1413 | 13 |
Пальмовое масло | 5950 | 55 |
Китайское сальное дерево | 6527 | 61 |
Микроводоросли при содержании триацилглицеридов 15% | 11 204 | 104 |
Микроводоросли при содержании триацилглицеридов 50% | 100 000 | 931 |
Таблица 6.
Результаты расчета АТ3: Комплекс ВТПК + БАТ
Параметр | Площадь БАТ, м2/га | Степень реализации биодизеля на внешнем рынке, % | ||||
---|---|---|---|---|---|---|
0 | 25 | 50 | 75 | 100 | ||
Суммарная степень замещения природного газа, % | 40 000/4 | 34.96 | 29.27 | 23.55 | 17.84 | 12.12 |
80 000/8 | 57.84 | 46.41 | 34.98 | 23.55 | 12.12 | |
120 000/12 | 80.71 | 63.56 | 46.41 | 29.27 | 12.12 | |
160 000/16 | 100 | 80.71 | 57.84 | 34.98 | 12.12 | |
200 000/20 | 100 | 97.85 | 69.28 | 40.70 | 12.12 | |
Степень внутреннего использования СО2 (w), % | 40 000/4 | 32.35 | 33.64 | 35.04 | 36.56 | 38.22 |
80 000/8 | 49.98 | 53.54 | 57.66 | 62.45 | 68.12 | |
120 000/12 | 63.47 | 69.60 | 77.04 | 86.27 | 98.01 | |
160 000/16 | 74.11 | 82.82 | 93.85 | 100 | 100 | |
200 000/20 | 78.37 | 88.95 | 100 | 100 | 100 | |
Срок окупаемости Комплекса ВТПК + БАТ, лет | 40 000/4 | 7.04 | 5.18 | 4.82 | 3.83 | 3.49 |
80 000/8 | 5.84 | 4.32 | 3.86 | 3.28 | 3.04 | |
120 000/12 | 5.38 | 4.02 | 3.45 | 3.10 | 2.87 | |
160 000/16 | 5.14 | 3.87 | 3.32 | 3.02 | 2.78 | |
200 000/20 | 4.99 | 3.78 | 3.25 | 2.95 | 2.72 | |
Чистая годовая прибыль Комплекса ВТПК + БАТ, млрд. руб. | 40 000/4 | 1.28 | 2.30 | 3.31 | 4.33 | 5.35 |
80 000/8 | 2.48 | 4.51 | 6.54 | 8.58 | 10.61 | |
120 000/12 | 3.67 | 6.72 | 9.77 | 12.82 | 15.87 | |
160 000/16 | 4.87 | 8.93 | 13.00 | 17.07 | 21.14 | |
200 000/20 | 6.06 | 11.15 | 16.23 | 21.32 | 26.40 |
Для производства МВ использовали трубчатые ФБР, обеспечивающие наибольшую производительность [94, 95]. В качестве примера приведены характеристики БАТ (SБАТ = 4 га) и ФБР для выращивания МВ Chlorella vulgaris и получения БТ, АБМ и ГЛ:
− площадь БАТ – 40 000 м2;
− световая площадь ФБР – 37 564 м2;
− сухой объем реактора – 9267 м3;
− сечение реактора – 0.76 м2;
− длина реактора, 12121м
− объем воды – 6720 м3;
− биопродуктивность – 3945 кг/ч;
− производительность – 3834 кг/ч.
Математическая модель ФБР кольцевого сечения, учитывающая ослабление интенсивности светового поля, обусловленное удалением от источника излучения, приведена в [96]. Результатом является модель гетерогенного фотохимического реактора на основе двухпоточной аппроксимации уравнения переноса оптического излучения и кинетики фотолиза. В [97] приведена математическая модель процесса культивирования микроводорослей в ФБР и разработана схема взаимосвязи процессов массопереноса с метаболизмом отдельной клетки.
Подробный обзор работ о математическом моделировании в биотехнологии проведен в [98]. В [99] предложена математическая модель массообменных процессов, сопровождающих рост МВ Chlorella vulgaris в аэрируемом ФБР. Получены профили концентраций углекислого газа в среде и пузырях воздуха и определены параметры модели. Сделан вывод об относительном постоянстве стехиометрии фотосинтеза, что значительно упрощает расчет ФБР. Выбор маршрутов массопереноса углекислого газа и кислорода в процессе культивирования МВ Chlorella vulgaris в автотрофном режиме в ФБР с аэрацией описан в [100]. Разработаны математические модели, описывающие пути массопереноса между клетками МВ и соприкасающимися с ними жидкой и воздушной фазами. На основе экспериментальных данных проведен сравнительный анализ моделей. Для углекислого газа и кислорода выбраны маршруты, наиболее корректно описывающие массообмен.
В [101, 102] исследован механизм влияния света на содержание хлорофилла (а) в биомассе МВ методом математического моделирования, основанного на представлениях о синтезе и фотодеструктивном окислении хлорофилла (а). Предложен новый подход к моделированию светозависимого содержания хлорофилла (а) в биомассе МВ, в основе которого лежит представление о двустадийности фотоавтотрофного роста МВ. На первой стадии в процессе фотосинтеза образуется резервная часть биомассы, из которой на второй стадии происходит биосинтез клеточных структур. Для различных условий рассмотрены три частных решения, описывающих зависимость содержания хлорофилла (а) от внешней интенсивности света, и оценены величины кинетических коэффициентов, адекватно описывающих экспериментальные и расчетные данные, в том числе для Chlorella vulgaris (R2 = 0.8). Показано, что доля хлорофилла (а) в структурной биомассе МВ составляет 2.5–3.5% и является видоспецифичным параметром.
Расчет проводили при следующих основных параметрах работы Комплекса ВТПК + БАТ:
– использовали отходы морфологического состава (мас. %): ТКО – 70, ТНО – 5, ОПМ – 5, АП – 7, ОД – 6, БО – 2, МО – 5;
– производственная мощность Комплекса по отходам 25 тыс. т/г. Основное технологическое оборудование, входящее в состав Комплекса: газотурбинные модули ГТЭС “Урал-6000” (Г-ТЭС-6000) суммарной установленной мощности 24 560 кВт – 4 шт.; унитарные плазменные модули (УПМ) производительностью 12.5 тыс. т/г. по отходам – 2 шт.; плазматроны номинальной электрической мощности 600 кВт (“ЭДП-600”) – 8 шт. (опытные образцы плазматронов ЭДП-600 спроектированы и созданы в НИЦ “Курчатовский институт”);
– для работы плазматронов в оптимальном режиме (электрическая мощность ~ 540 кВт) дополнительное дутье кислорода в плавильную камеру ВТПК составляет 682 кг О2 в час (или 203 кг О2 на 1 т отходов). Расчет количества дополнительного дутья кислорода в плавильную камеру ВТПК проводили по методике, описанной в [15];
– площадь БАТ варьировали в пределах 4–20 га. Минимальная площадь БАТ, равная 4 га, была выбрана из практических соображений как вполне достаточная для получения прибыли от эксплуатации Комплекса ВТПК + БАТ и имеющая большой запас для ее увеличения;
– расчетная влажность биомассы – 50%;
– для указанного выше морфологического состава отходов и других параметров работы Комплекса количество СО2 из блока ВТПК было постоянным – 1466 кг/ч;
– в качестве плазмообразующего газа использовали СО2 – постоянное его количество во всех расчетах составляло 1741 кг/ч;
– постоянным также являлось количество получаемого БПШ – 2410 т/г.
В расчетах Комплекса ВТПК + БАТ полагали, что вся полученная АБМ реализуется внешним потребителям, а полученное БТ либо полностью используется в качестве энергоносителя в ГТУ, либо реализуется (весь или часть) внешним потребителям. Расчетами было установлено, что использование всей или части получаемой АБМ в виде добавки к отходам и переработки в Комплексе ВТПК + БАТ не приводит к положительным результатам: значительно возрастает срок окупаемости и уменьшается годовая прибыль.
Сравнение варианта работы Комплекса ВТПК с вариантом работы Комплекса ВТПК + + БАТ при полном использовании произведенного биодизельного топлива в ГТУ и при минимальной площади БАТ – SБАТ = 40 000 м2 (4 га) показало значительную эффективность Комплекса ВТПК + БАТ как в экологическом, так и в экономическом плане:
– значительно (почти в 4 раза) возрастает степень использования СО2 (w) в самом Комплексе – с 8.33 до 32.35%. Величину w рассчитывали (исходя из эквимолярного поглощения СО2 и выделения О2 в процессе получения МВ) по формуле
(10)
$w = \left( {{\text{А}} + 1.375{\text{В}}} \right){\text{/}}\left( {{\text{С}} + {\text{Д}}} \right),$– значительно (почти в 3 раза) возрастает степень замещения природного газа пирогазом (после его очистки и выделения из него СО2) и биодизелем (с 12.12 до 12.12 + 22.84 = 34.96%). Оба этих показателя в полной мере соответствуют тенденции декарбонизации промышленного производства;
– значительно (более чем в 2 раза) сокращается срок окупаемости затрат – с 17.18 до 7.04 лет (горизонт планирования – 20 лет);
– значительно (более чем в 5 раз) возрастает годовая чистая прибыль – с 119 до 1280 млн. руб. При этом капитальные затраты на Комплекс ВТПК + БАТ по сравнению с Комплексом ВТПК возрастают лишь на 56% – с 5649 до 8809 млн. руб.
Улучшенные экономические показатели работы Комплекса ВТПК + БАТ достигаются в основном за счет замещения природного газа собственными энергетическими ресурсами (БТ и горючими компонентами пирогаза) и продажей на внешнем рынке всего производимого глицерина и АБМ.
Вариант 1 (SБАТ = 40 000 м2). Экономические показатели работы Комплекса ВТПК + БАТ при SБАТ = 40 000 м2 могут быть улучшены, если все производимое БТ или его часть реализовывать на внешнем рынке. В этом случае с увеличением степени реализации степень внутреннего использования СО2 (w) увеличивается с 32.35 до 38.22% (табл. 6), а степень замещения природного газа БТ снижается (табл. 6) с 34.96 до 12.12% (при полной реализации БТ на внешнем рынке). Экономические показатели заметно улучшаются. Чистая годовая прибыль возрастает с 1.28 до 5.35 млрд. руб. (табл. 6) при 100%-ной реализации произведенного БТ на внешнем рынке (по сравнению с Комплексом ВТПК возрастание чистой прибыли более чем на порядок – с 0.12 до 5.35 млрд. руб.). Увеличение степени внутреннего использования СО2 (w) с увеличением степени реализации БТ на внешнем рынке связано с меньшим количеством используемого биодизельного топлива в ГТУ и, как следствие, меньшим количеством образующегося СО2 в газообразных продуктах ГТУ.
При 100%-ной реализации произведенного БТ на внешнем рынке срок окупаемости Комплекса ВТПК + БАТ снижается до 3.5 лет (табл. 6), что делает эту технологию привлекательной для инвестиций даже при минимальной площади БАТ (SБАТ = 40 000 м2). Улучшаются и другие экономические показатели: EBITDA, рентабельность и др.
При указанных выше параметрах работы Комплекса ВТПК + БАТ суммарный поток пирогаза (4754 кг/ч) и его компонентный состав во всем исследованном диапазоне изменения SБАТ = 4–20 га остаются постоянными (кг/ч): СО – 1661, Н2 – 104, СН4 – 146, Н2О – 1290, СО2 – 1543, О2 – отсутствует, N2 – 11. При использовании всего произведенного БТ (14652 т/г.) внутри Комплекса ВТПК + БАТ в качестве энергоносителя в ГТУ количество производимого в ГТУ СО2 составляет 23 234 кг/ч и линейно уменьшается с уменьшением доли БТ, используемого в ГТУ, до величины 19 441 кг/ч при использовании всего произведенного БТ для продажи.
При выборе количества реализуемого БТ внешним организациям необходимо учитывать экономические потери Комплексом – снижение степени декарбонизации и увеличение затрат на квоты по выработке СО2, которые на момент написания обзора составляли 63 евро за 1 т СО2. Как было показано ранее, с увеличением доли БТ, реализуемой внешним организациям, прибыль Комплекса ВТПК + БАТ возрастает. И наоборот, с увеличением доли БТ, реализуемой на внешнем рынке, снижается доля БТ, используемая внутри Комплекса и, как следствие, снижается прибыль предприятия за счет снижения степени декарбонизации и увеличения выплат СО2-квот. Определение экстремума результирующей кривой и выбор оптимальной доли БТ, используемой для продажи, являются задачей оптимального управления Комплексом ВТПК + БАТ.
Рис. 10.
Принципиальная технологическая схема непрерывного получения ТАЦ этерификацией глицерина уксусной кислотой при катализе серной кислотой в реакционно-ректификационной колонне с боковыми ректификационными колоннами (БРК): Р – распределительная тарелка, Г – глухая тарелка. Число БРК – 2. Т – теплоноситель из Комплекса ВТПК.
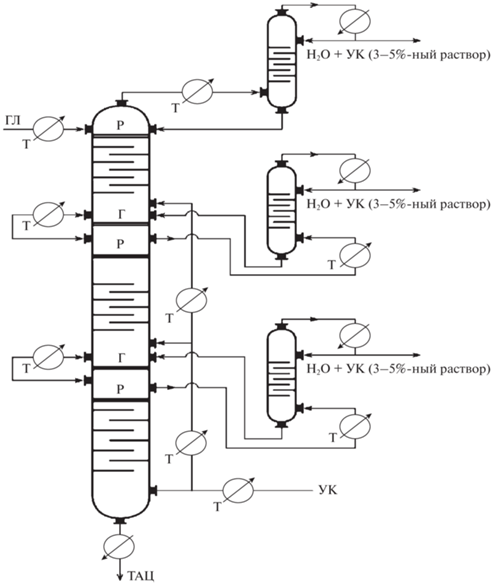
Вариант 2 (SБАТ = 80 000 м2). Результаты расчета Комплекса ВТПК + БАТ для площади БАТ 80 000 м2 приведены в табл. 6. Увеличение площади БАТ до 8 га приводит к увеличению выработки БТ до 29 304 т/г. Реализация всего этого количества БТ на внешнем рынке позволяет получать годовую прибыль 10.61 млрд. руб. (табл. 6). С другой стороны, использование всего произведенного БТ вместе с энергетическими компонентами пирогаза (СО, Н2, СН4) внутри Комплекса позволяет на 57.84% заменить использование природного газа (табл. 6). Количество произведенной электроэнергии, необходимой для годового обслуживания БАТ площадью 8 га, возрастает до 19 061 МВт · ч (при количестве электроэнергии, поставляемой на внешний рынок 106 330 МВт · · ч/г.). Возрастает количество произведенной АБМ до 25 559 т/г. Возрастает и количество произведенного ГЛ – до 2233 т/г. Увеличение площади БАТ до 8 га приводит к еще большему снижению срока окупаемости Комплекса ВТПУ + БАТ – до 3.04 лет (при 100%-ной реализации БТ на внешнем рынке) – табл. 6. При 100%-ной реализации БТ на внешнем рынке при SБАТ = 80 000 м2 степень внутреннего использования СО2 возрастает до 68.12%. При увеличении площади БАТ до 8 га стоимость капитальных затрат на строительство Комплекса ВТПК + БАТ возрастает до 12.4 млрд. руб.
Вариант 3 (SБАТ = 120 000 м2). Результаты расчета Комплекса ВТПК + БАТ для площади БАТ 120 000 м2 (12 га) приведены в табл. 6. Увеличение площади БАТ до 12 га приводит к увеличению выработки БТ до 43 956 т/г. Реализация всего этого количества БТ на внешнем рынке позволяет получать годовую прибыль 15.87 млрд. руб. (табл. 6). С другой стороны, использование всего произведенного БТ вместе с энергетическими компонентами пирогаза (СО, Н2, СН4) внутри Комплекса ВТПК + БАТ позволяет на 80.71% заменить использование природного газа (табл. 6). Количество произведенной электроэнергии, необходимой для годового обслуживания БАТ площадью 12 га, составляет 28 593 МВт · ч (при количестве электроэнергии, поставляемой на внешний рынок, равном 96 799 МВт · ч/г.). Количество произведенной АБМ возрастает до 3833 т/год. Возрастает и количество произведенного ГЛ – до 3349 т/г. Увеличение площади БАТ до 12 га приводит к снижению срока окупаемости Комплекса ВТПК + БАТ до 2.87 лет (при 100%-ной реализации БТ на внешнем рынке) – табл. 6. При SБАТ = = 12 га и 100%-ной реализации БТ на внешнем рынке степень внутреннего использования СО2 (w) практически достигает 100% (98.01% – табл. 6). Стоимость капитальных затрат на строительство Комплекса ВТПК + БАТ возрастает до 16 млрд. руб.
Вариант 4 (SБАТ = 160 000 м2). Результаты расчета Комплекса ВТПК + БАТ для площади БАТ 160 000 м2 (16 га) приведены в табл. 6. Увеличение площади БАТ до 16 га приводит к увеличению выработки БТ до 58 609 т/г. Реализация всего этого количества БТ на внешнем рынке позволяет получать годовую прибыль 21.14 млрд. руб. (табл. 6). Использование всего произведенного БТ вместе с энергетическими компонентами пирогаза (СО, Н2, СН4) внутри Комплекса позволяет полностью (табл. 6) заменить использование природного газа. Количество произведенной электроэнергии, необходимой для годового обслуживания БАТ площадью 16 га, составляет 38 123 МВт · ч (при количестве электроэнергии, поставляемой на внешний рынок, равном 87 268 МВт · ч/г.). Количество произведенной АБМ возрастает до 51 117 т/г. Возрастает и количество произведенного ГЛ до 4466 т/г. Как видно из данных табл. 6, уже при реализации ~60% произведенного БТ на внешнем рынке степень внутреннего использования СО2 составляет ~100% при приемлемом сроке окупаемости Комплекса (~3.15 лет). Окончательный выбор площади БАТ и степени реализации БТ на внешнем рынке определяется на предпроектной стадии. Стоимость строительства Комплекса ВТПК + БАТ с SБАТ = 16 га составляет 19.6 млрд. руб.
Вариант 5 (SБАТ = 200 000 м2). Результаты расчета Комплекса ВТПК + БАТ для площади БАТ 200 000 м2 (20 га) приведены в табл. 6. Увеличение площади БАТ до 20 га приводит к увеличению выработки БТ до 73261 т/г. Реализация всего этого количества БТ на внешнем рынке позволяет получать годовую прибыль 26.40 млрд. руб. (табл. 6). Использование всего произведенного БТ вместе с энергетическими компонентами пирогаза (СО, Н2, СН4) внутри Комплекса ВТПК + БАТ позволяет полностью заменить использование природного газа. Более того, остается еще ~25% произведенного БТ для его реализации на внешнем рынке (табл. 6). Количество произведенной электроэнергии, необходимой для годового обслуживания БАТ площадью 20 га, составляет 47 654 МВт · ч (при количестве электроэнергии, поставляемой на внешний рынок, равном 77 737 МВт · ч/г.). Количество произведенной АБМ возрастает до 63 897 т/г. Возрастает и количество произведенного ГЛ до 5582 т/г. Как видно из данных табл. 6, уже при 50%-ной реализации произведенного БТ на внешнем рынке степень внутреннего использования СО2 составляет 100% при вполне приемлемом сроке окупаемости Комплекса (3.25 лет). Окончательный выбор площади БАТ и степени реализации БАТ на внешнем рынке определяется на предпроектной стадии с учетом полученных закономерностей. Стоимость строительства Комплекса ВТПК + БАТ с SБАТ = = 20 га составляет 23.19 млрд. руб.
Переработка глицерина. Одним из основных продуктов при реализации АТ3: Комплекса ВТПК + БАТ является ГЛ. В последние годы из-за повышенного интереса к “зеленым” технологиям объем производства БТ в Европе вырос в 25 раз и достиг уровня 25 млн. т/г., и на мировом рынке сложилась ситуация с перепроизводством ГЛ. Поэтому появился интерес к технологиям, перерабатывающим ГЛ-содержащее сырье в продукты с высокой добавленной стоимостью [103, 104].
Перспективным методом переработки ГЛ является получение триацетина (ТАЦ) по реакции этерификации ГЛ с уксусной кислотой (УК):
(11)
$\begin{gathered} {\text{HOC}}{{{\text{H}}}_{2}}{\text{CH}}\left( {{\text{OH}}} \right){\text{C}}{{{\text{H}}}_{2}}{\text{OH}} + 3{\text{С}}{{{\text{Н}}}_{3}}{\text{С}}\left( {\text{О}} \right){\text{ОН = }} \\ = {\text{С}}{{{\text{Н}}}_{3}}\left( {\text{O}} \right){\text{COC}}{{{\text{H}}}_{2}}{\text{CH}}\left( {{\text{OC}}\left( {\text{O}} \right){\text{С}}{{{\text{Н}}}_{3}}} \right){\text{C}}{{{\text{H}}}_{2}}{\text{OC}}\left( {\text{O}} \right){\text{С}}{{{\text{Н}}}_{3}} + {\text{ }}3{{{\text{Н}}}_{2}}{\text{О}}. \\ \end{gathered} $Этот процесс каталитический и использует различные гомогенные или гетерогенные кислотные катализаторы [105–112]. ТАЦ известно как вещество с широким спектром применения:
− в качестве безопасной пищевой добавки (Е1518), в том числе как возможный источник питания для систем искусственного питания при длительных космических перелетах;
− в косметической и фармацевтической промышленности в качестве увлажняющего агента, пластификатора и растворителя;
− в качестве добавки к топливу как антидетонационная присадка, снижающая стук двигателя при использовании бензина, улучшающая устойчивость к низким температурам и вязкостные характеристики биодизеля. Является связующим веществом твердого ракетного топлива;
− в химической промышленности используется в качестве пластификатора и отвердителя при литье пластиков и в производстве различных смол.
При разработке технологии получения ТАЦ в условиях гомогенного катализа необходимо учитывать, что реакция взаимодействия глицерина с УК протекает последовательно через равновесные стадии образования моноацетина (МАЦ) и диацетина (ДАЦ):
(12)
${\text{ГЛ}} + {\text{УК}} \leftrightarrow \left( {{{k}_{1}}} \right){\text{ МАЦ}} + {{{\text{Н}}}_{2}}{\text{О}},~$(13)
${\text{МАЦ}} + {\text{УК}} \leftrightarrow \left( {{{k}_{3}}} \right){\text{ ДАЦ}} + {{{\text{Н}}}_{2}}{\text{О}},$(14)
${\text{ДАЦ}} + {\text{УК}} \leftrightarrow \left( {{{k}_{5}}} \right){\text{ ТАЦ}} + {{{\text{Н}}}_{2}}{\text{О}}.~$Кинетические закономерности этих стадий в присутствии в качестве катализатора серной кислоты подробно описаны в [105]. В случае использования гомогенного катализатора процесс обычно проводят либо в реакторе смешения (РС), либо в колонном реакционно-ректификационном реакторе (РРР). Синтез ТАЦ как в РС, так и в РРР не приводил к удовлетворительным показателям процесса даже при больших мольных соотношениях ГЛ : УК (1 : 6), и выход ТАЦ в обоих реакторах составлял 10–15% при конверсии ГЛ 95–96% [106]. Низкий выход ТАЦ обусловлен отсутствием технологических приемов по сдвигу химического равновесия в сторону ТАЦ – отводом воды из зоны реакции. Другой причиной низкого выхода целевого продукта являются значительные потери тепла и не оптимальный температурный режим в реакторах – процесс проводят при температуре до 120°С, а УК начинает испаряться уже при 118°С, в то время как в реакционной зоне должен быть ее избыток.
Для смещения равновесия в сторону образования целевого продукта (ТАЦ) в соответствии с уравнениями реакций (12)–(14) необходимо выводить воду из реакционной зоны. Для этого вместо УК предложено использовать уксусный ангидрид (УА): при его взаимодействии с реакционной водой образуется УК, которая реагирует с МАЦ и ДАЦ с образованием ТАЦ. Таким образом вода выводится из зоны реакции. Этот прием был использован в патентах [113, 114]. Процесс проводили в РРР следующим образом. Жидкий ГЛ, нагретый до температуры реакции (~150°С), подают на верхнюю тарелку РРР. В середину РРР подают УА. Перегретые пары УК (при температуре реакции ~150°С) подают в низ РРР. С низа РРР отводят охлажденный ТАЦ в смеси с УК и УА. В качестве катализатора используют п-толуолсульфоновую кислоту в количестве 0.1–0.5 мас. % от количества ГЛ при давлении до 3 атм. и температуре 100–180°С. Катализатор вводят вместе с ГЛ. Процесс проводят при мольном соотношении УК : ГЛ от 2.5 : 1 до 5 : 1 и мольном соотношении УА : ГЛ от 0.1 : 1 до 1.5 : 1. Общее время контакта реагентов – не менее 1 ч.
С верха РРР отбирают реакционную воду, содержащую 3–5% УК. Смесь ТАЦ, УК и УА, отбираемую с низа РРР, подвергают ректификации с получением чистого ТАЦ. Выделенные УА и УК рециркулируют. В присутствии катализатора из 100 кг/ч ГЛ, 139 кг/ч УК и 50 кг/ч УА получают 237 кг/ч ТАЦ (выход 82%). Недостатком этой технологии является использование в качестве дополнительного реагента УА, что значительно увеличивает себестоимость продукции и усложняет процесс ректификации целевого продукта с необходимостью дополнительного выделения и рециркуляции УА.
Для реализации АТ3: Комплекс ВТПК + БАТ была предложена технология непрерывного получения ТАЦ этерификацией глицерина уксусной кислотой в реакционно-ректификационной колонне с боковыми ректификационными колоннами в присутствии в качестве гомогенного катализатора H2SO4 (рис. 10). Эта технология не предусматривает использования в качестве реагента УА [19].
Процесс проводят при давлении до 2 атм., температуре до 180°С, мольном соотношении УК : ГЛ до 10 : 1, количестве катализатора до 0.5 мас. % по отношению к ГЛ и температуре паров УК на входе в колонны до 130°С. Проведение процесса при указанных выше условиях по предложенной технологии позволяет сместить равновесие целевой реакции в сторону образования ТАЦ за счет постоянного многократного отбора воды из реакционной зоны. Регулирование температуры в боковых ректификационных колоннах и в системах внешнего теплообмена между Р- и Г-тарелками (рис. 10) позволяет оптимизировать температурный режим и получать высокие показатели по выходу ТАЦ. Наилучшие показатели по выходу ТАЦ (94%) были достигнуты в реакционно-ректификационной колонне с тремя боковыми ректификационными колоннами.
Преимуществом предложенной технологии синтеза ТАЦ из глицерина, полученного при производстве БТ с использованием МВ Chlorella vulgaris, является возможность использования теплоносителя (пара) – Т, полученного в ГТУ Комплекса ВТПК + БАТ в количестве ~370 тыс Гкал/г. для обеспечения тепловой энергией реакционно-ректификационной колонны (рис. 10). Использование этого теплоносителя не скажется на работе БАТ, так как проектом предусматривается обеспечение этого блока только электроэнергией, без использования тепловой энергии, получаемой в КУ и ГТУ. Количества вырабатываемой в ГТУ электрической энергии вполне достаточно для обеспечения БАТ (рис. 11).
Рис. 11.
Зависимость количества электроэнергии (А) и доли электроэнергии от суммарного избыточного количества электроэнергии, вырабатываемой комплексом ВТПК, необходимой для функционирования БАТ (Б) от площади БАТ. Цифрами указаны результаты расчета.
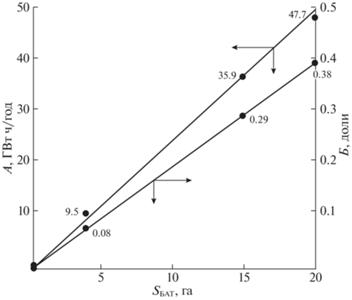
При выборе гомогенного катализатора процесса необходимо иметь в виду, что применение серной кислоты ведет к значительной интенсификации процесса и хорошему выходу целевого продукта. Но при этом велика вероятность протекания побочных процессов: дегидратации спирта, образования сложных эфиров сульфокислот, осмоления и др. Селективными гомогенными катализаторами являются бензол- и толуолсульфокислоты. Эти катализаторы более дорогие и имеют температуру плавления выше комнатной, что усложняет технологический процесс введения их в реакционную массу. Применение соляной кислоты требует особой осторожности из-за вероятности выделения хлороводорода при нагревании. Наиболее безопасным и селективным катализатором является ортофосфорная кислота.
Известны различные гетерогенные катализаторы для интенсификации процесса взаимодействия глицерина с УК с целью получения ТАЦ. В [109] в качестве катализатора предложено использовать мезопористый силикагель SBA с нанесенным на его поверхность иттрием (3%).
Известно [110] использование в качестве катализатора активированного угля с предварительной активацией его поверхности серной кислотой (85°С, 4 ч). Использование этого катализатора при 120°С, мольном отношении ГЛ : УК = 1 : 8 и продолжительности процесса 3 ч позволило получить 91%-ную конверсию ГЛ.
В [111] в качестве гетерогенного катализатора исследован MoO3/SiO2. Наилучшие результаты были получены при 118°С и мольном отношении ГЛ:УК = 1:10. Через 20 ч конверсия ГЛ составила 100%, селективность по ТАЦ – 76%.
Перспективными гетерогенными катализаторами являются ионообменные смолы. Так, при использовании в качестве катализатора А-15 (ионообменная смола Амберлист А-15) при температуре 120°С в течение 120 мин при молярном отношении ГЛ : УК = 1 : 6 (использовали 5% А-15 на 1 моль ГЛ) была достигнута 100%-ная степень превращения ГЛ. Продукты реакции: МАЦ – 3.5%, ДАЦ – 8.7%, ТАЦ – 87.8%. Увеличить выход ТАЦ при этерификации глицерина УК в присутствии ионообменных смол можно, изменив условия реакции и используя прием дополнительного введения образующего азеотроп вещества (толуола) для удаления из реакционного объема воды. В [112] процесс проводили при 105°С, начальном мольном соотношении ГЛ : УК = 1 : 6 в присутствии катализатора в количестве 5% от количества ГЛ. В присутствии катализаторов А‑15 и А-70 при использовании в качестве образующего азеотроп с водой толуола были получены высокие результаты по выходу ТАЦ (табл. 7).
Таблица 7.
Этерификация глицерина УК в присутствии А-15 и А-70 с использованием образующего азеотроп с водой толуола
Катализатор | Продолжитель-ность реакции, ч | Конверсия ГЛ, % | Селективность, % | |||
---|---|---|---|---|---|---|
МАЦ | ДАЦ | ТАЦ | Высококипящие примеси1 | |||
А-15 | 10 | 100 | 0 | 12.3 | 83.9 | 3.8 |
А-15 | 24 | 100 | 0 | 0 | 95.3 | 4.7 |
А-70 | 10 | 100 | 0 | 7.5 | 87.6 | 4.9 |
А-70 | 24 | 100 | 0 | 0 | 94.1 | 5.9 |
Еще одним преимуществом ионообменных смол является возможность формования из них различных типов насадок (например, колец Рашига) и использование их не только в качестве катализатора, но и массообменного элемента. Промышленная реализация процесса получения ТАЦ этерификацией глицерина УК в присутствии гетерогенного катализатора (в том числе ионообменной смолы) может быть осуществлена в двух типах трехфазных (жидкая фаза – ГЛ, газовая фаза – перегретые пары УК, твердая фаза – катализатор) реакторов: реактор с неподвижным слоем катализатора типа насадочной колонны и РС (“сларри-реактор”). Возможна также реализация процесса в каскаде трехфазных РС. Процесс проводят при температуре 120°С, при которой реакционные пары воды и частично пары УК вместе с другими высококипящими компонентами удаляются из зоны реакции. Высококипящие компоненты конденсируются в холодильнике и возвращаются в зону реакции. Вода (содержащая 3–5 мас. % УК) выводится из системы. Процесс проводят в течение 2–3 ч. После окончания реакции из выделенного продукта под вакуумом отгоняют УК, МАЦ и ДАЦ.
Получение достаточно большого количества ГЛ (до 6500 т/г.) при производительности по отходам 25 000 т/г. закладывает основу для развития Комплекса ВТПК + БАТ в направлении получения химическими и физико-химическими методами кроме ТАЦ другой химической продукции [115], например:
1) Получения водорода путем конверсии ГЛ с водяным паром в присутствии катализатора на основе никеля, оксида магния и титана [116]:
(15)
${{{\text{С}}}_{3}}{{{\text{Н}}}_{8}}{{{\text{О}}}_{3}} + 3{{{\text{Н}}}_{2}}{\text{О}} = 3{\text{С}}{{{\text{О}}}_{2}} + 7{{{\text{Н}}}_{2}}.$При 650°С максимальный выход водорода составлял 56.5%. Этот процесс хорошо сочетается с АТ3 (Комплекс ВТПК + БАТ): полученный СО2 после абсорбционного выделения может быть рециркулирован на стадию БАТ, а необходимый пар может быть получен в блоке ВТПК в КУ. Из 6500 т/г. глицерина при 50%-ном выходе водорода может быть получено ~500 т/г. водорода. А с учетом водорода, выделяемого из пирогаза (80 кг/ч или 596 т/г. при реальном времени эксплуатации Комплекса в течение года 7446 ч при годовой загрузке по времени 85%), годовая производительность по водороду может достигать 1096 т/г. Этот процесс может быть реализован в стандартном трубчатом реакторе [59] с непосредственным обогревом газообразными продуктами ГТУ (рис. 12).
Рис. 12.
Принципиальная технологическая схема паровой конверсии глицерина: 1 – трубчатый реактор, 2 – пароперегреватель, 3–5 – теплообменники, 6 – сепаратор.
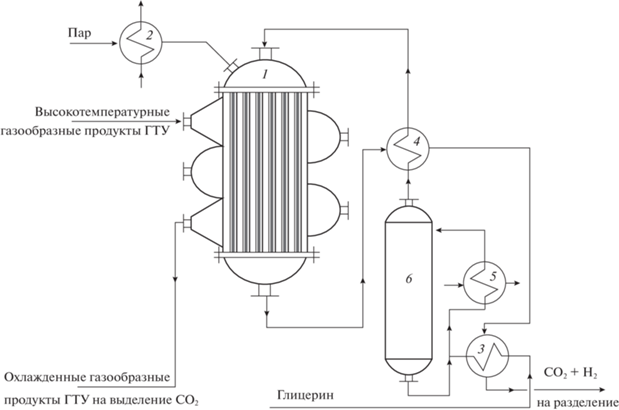
2) Парофазной дегидратацией ГЛ на катализаторе 0.5В2О3/Аl2O3 может быть получен акролеин – ценное химическое сырье, используемое в производстве сложных эфиров акриловой кислоты [117]. Для проведения дегидратации водного раствора ГЛ в проточном реакторе при 280°С использовали алюмофосфатные катализаторы на основе оксидов металлов (Ce, Cu, Fe, Mn, Mo, V, W), нанесенных на Al2O3. Наилучшей селективностью к образованию акролеина обладают W- и Mo-катализаторы [118].
3) При взаимодействии ГЛ с ацетоном или формальдегидом в присутствии кислотных катализаторов могут быть получены ацетали и кетали, являющиеся эффективными присадками к топливам: происходит увеличение октанового числа и стабильности топлив при одновременном уменьшении образования нагара и смолообразования в двигателе [119, 120].
4) В [121] исследовано каталитическое дегидроксилирование ГЛ в 1,2-пропандиол в проточном реакторе – один из способов утилизации избытка ГЛ, накапливающегося при производстве БТ. В качестве катализатора использовали никель Ренея. Этот катализатор проявляет большую активность: при 220°С и давлении водорода 2 МПа конверсия ГЛ и выход 1,2-пропандиола составляют соответственно 88 и 35%. При использовании катализатора кобальта Ренея при 200°С и давлении водорода 3 МПа выход 1,2-пропандиола составил 44% при конверсии ГЛ ~97% [122]. 1,2‑Пропандиол может быть получен также гидрогенолизом ГЛ [123, 124]. ГЛ с чистотой не менее 95% гидрируют водородом при давлении 20–100 атм. и температуре 180–240°С в присутствии катализатора, содержащего (мас. %): CuO 20–60, ZnO 30–70, MnO 1–10. Процесс проводят в автоклаве. Целевой продукт 1,2-пропандиол используется в качестве компонента тормозных и гидравлических жидкостей, смазочных материалов и антифризов, в косметических препаратах, в пищевой промышленности и в качестве растворителей для жиров, смол, масел и красок. Этот же процесс может быть реализован в трехфазном реакторе [125] при давлении 20–30 атм. в присутствии медьсодержащего катализатора. ГЛ и водород подают в верхнюю часть реактора, при этом ГЛ течет по поверхности частиц катализатора при удельном расходе 0.2–0.7 ч–1.
5) В [126] исследована реакция паровой конверсии ГЛ (в том числе его 80%-ного водного раствора) на катализаторе Ni/C для получения синтез-газа и водорода. В области умеренных температур (520°С) были получены высокие значения конверсии ГЛ. Состав образующегося синтез-газа удовлетворяет требованиям синтеза метанола. При практически полной конверсии ГЛ (температура более 700°С) наблюдается высокая селективность по водороду (до 60%).
6) Перспективным методом переработки является синтез эпихлоргидрина (ЭПХГ) гидрохлорированием ГЛ [127, 128]. ЭПХГ является крупнотоннажным химическим продуктом, мировое производство которого превышает 1.6 млн. т/г. Он применяется в качестве сырья в производстве эпоксидных и ионообменных смол, ПАВ, каучуков и др. ЭПХГ востребован атомной промышленностью. Синтез проводят в присутствии в качестве катализатора УК (~5% от ГЛ) при температуре 120–140°С при мольном соотношении HCl : ГЛ = 2.14–2.16 : 1 в каскаде реакторов смешения с подачей хлористого водорода и ГЛ противотоком. При конверсии ГЛ 75–76% селективность образования целевого продукта составляет 89–94%. После ректификации получают целевой ЭПХГ чистотой не менее 99.5%.
7) Еще один способ переработки глицерина – его гетерогенно каталитическая конденсация с н‑бутиловым и другими спиртами с получением простых эфиров [129]. Простые эфиры ГЛ обладают рядом уникальных физико-химических свойств и представляют огромный интерес для лакокрасочных материалов и процессов тонкого органического синтеза.
С использованием вырабатываемой в Комплексе ВТПК + БАТ избыточной тепловой и электрической энергии возможно создание производства не только по переработке глицерина в ТАЦ, но и других химических производств, перерабатывающих компоненты пирогаза (Н2, СО) в продукцию, выделив эти производства в отдельный БХП.
Обобщение результатов АТ3: Комплекс ВТПК + + БАТ. На рис. 13 приведены данные о количестве СО2, выделяемого из газообразных продуктов пиролиза. В зависимости от площади БАТ и степени реализации БТ внешним организациям это количество СО2 изменяется в интервале 19.441–38.408 т/ч. С увеличением площади БАТ и уменьшением степени реализации БТ внешним организациям количество СО2 увеличивается. Наименьшее количество СО2 (19.441 т/ч) образуется при 100%-ной степени реализации БТ внешним организациям. Такой характер зависимости объясняется тем, что чем меньшее количество произведенного в Комплексе БТ реализуется на внешнем рынке, тем большее его количество замещает природный газ в ГТУ, увеличивая количество СО2 в составе газообразных продуктов ГТУ (другого пути использования БТ в предложенной модели Комплекса ВТПК + БАТ не существует). Количество СО2, выделяемое из ГТУ, во всем интервале (19.441–38.408 т/ч) удовлетворяет количеству СО2, необходимому для производства МВ Chlorella vulgaris на площади БАТ 4–20 га. Конкретное количество СО2 определяется на предпроектной стадии после выбора площади БАТ.
Рис. 13.
Зависимость количества СО2, выделяемого из газообразных продуктов ГТУ, от площади БАТ Комплекса ВТПК + БАТ. Степень реализации БТ внешним организациям (%): 1 – 0, 2 – 25, 3 – 50, 4 – 75, 5 – 100.
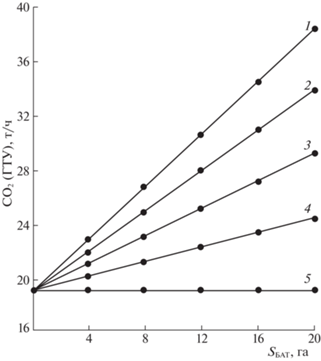
На рис. 14 приведены зависимости количества О2, выделяемого в БАТ, и количества БТ, вырабатываемого в Комплексе ВТПК + БАТ, от площади БАТ. Оба этих параметра (и количество О2, и количество БТ) возрастают с увеличением SБАТ. Реализация АТ3 помимо отмеченных экологических преимуществ:
Рис. 14.
Зависимость количества О2, выделяемого в БАТ, и количества производимого биодизеля от площади БАТ Комплекса ВТПК + БАТ.
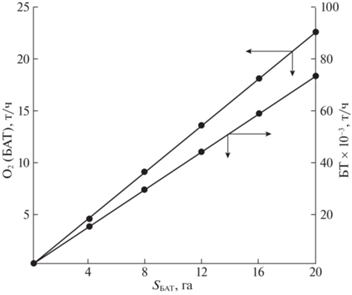
– высокой степени использования СО2 внутри Комплекса;
– высокой степени замены природного газа энергетическими компонентами, вырабатываемыми в самом Комплексе;
– полной декарбонизацией (извлечением СО2) из газообразных продуктов;
– в атмосферу поступает О2 в количестве ~4–22 т/ч в зависимости от SБАТ.
Кислород, вырабатываемый в БАТ, может быть уловлен и использован в самом Комплексе для дополнительного дутья О2 в плавильную камеру ВТПК (0.682 т/ч) и/или в БХП АПКК (рис. 21) для производства химической продукции, например для прямого синтеза пероксида водорода из элементов [130].
Зависимость степени внутреннего использования СО2 (w) от площади БАТ при различной степени реализации БТ внешним организациям приведена на рис. 15. С увеличением SБАТ при прочих равных условиях величина w возрастает, что связано прежде всего с большим количеством СО2, необходимым для производства МВ на большей площади.
Рис. 15.
Зависимость степени внутреннего использования СО2 (w) от площади БАТ Комплекса ВТПК + + БАТ. Степень реализации БТ внешним организациям (%): 1 – 0, 2 – 25, 3 – 50, 4 – 75, 5 – 100.
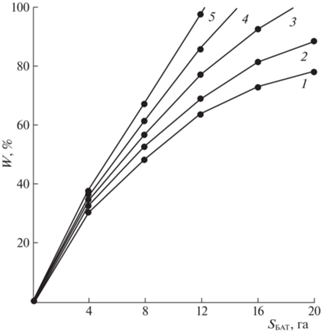
При постоянной SБАТ с увеличением степени реализации БТ внешним организациям величина w также возрастает, что связано с уменьшением доли БТ, используемого как энергоноситель в ГТУ и, как следствие, образованием меньшего количества СО2 в газообразных ГТУ и большей степени использования СО2 в БАТ. При SБАТ = = 12 га и 100%-ной реализации БТ внешним организациям достигается почти 100%-ная степень внутреннего использования СО2. Для SБАТ = 8 и SБАТ = 4 га максимальная степень внутреннего использования СО2 также достигается при 100%‑ной реализации БТ внешним организациям и составляет 68.12 и 38.22% соответственно. По-видимому, оптимальной является SБАТ = 12 га, которая позволяет варьировать величину w в диапазоне 60–100% и реализовывать БТ внешним организациям во всем допустимом интервале (до 100%).
Данные о количестве произведенной электроэнергии и АБМ для продажи внешним организациям в зависимости от площади БАТ Комплекса ВТПК + БАТ приведены на рис. 16. С увеличением SБАТ величина Е линейно уменьшается, что связано в основном с энергозатратами в БАТ при увеличении его площади. Наоборот, с увеличением SБАТ возрастает количество произведенной АБМ. Знание количества произведенной АБМ важно при определении SБАТ в предпроектный период – количество производимой АБМ должно соответствовать потребностям животноводства в регионе функционирования Комплекса (табл. 8). В противном случае при перепроизводстве АБМ необходимо будет либо уменьшать SБАТ, что приведет к снижению выработки БТ и ухудшению экономических показателей процесса, либо искать другие пути реализации АБМ.
Рис. 16.
Зависимость количества произведенной электроэнергии и алга-биомассы для продажи внешним организациям от площади БАТ Комплекса ВТПК + БАТ.
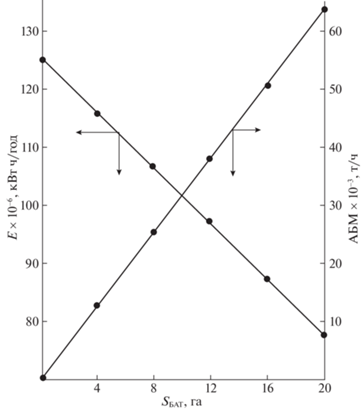
Таблица 8.
Количество голов свиней, дойных коров и яичных кур при ежесуточном кормлении их АБМ в течение года в зависимости от площади БАТ
Объект | Площадь БАТ, га | ||||
---|---|---|---|---|---|
4 | 8 | 12 | 16 | 20 | |
Свиньи | 17 716 | 35 433 | 53 149 | 70 865 | 88 582 |
Дойные коровы | 4811 | 9621 | 14 432 | 19 242 | 24 053 |
Яичные куры | 2 746 036 | 5 492 073 | 8 238 109 | 10 984 145 | 13 730 182 |
На рис. 17 приведена зависимость суммарной степени замещения природного газа (α + β) газообразными горючими продуктами пирогаза (α) и биодизелем (β) от площади БАТ при различной степени реализации БТ внешним организациям. Как видно из рисунка, 100%-ной степени замещения природного газа удается достичь при полном использовании БТ внутри Комплекса и SБАТ ~ 16 га. При этом ~25% БТ остается для реализации на внешнем рынке. При других условиях при меньшей площади БАТ не удается достичь 100%-ной степени замещения природного газа:
Рис. 17.
Зависимость суммарной степени замещения природного газа от площади БАТ Комплекса ВТПК + БАТ. Степень реализации БТ внешним организациям (%): 1 – 0, 2 – 25, 3 – 50, 4 – 75, 5 – 100.
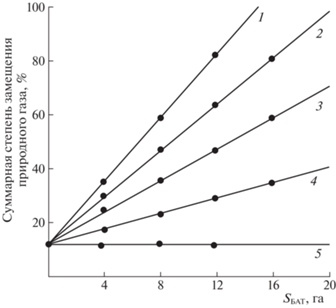
− для SБАТ = 4 га (α + β)max = 34.96%;
− для SБАТ = 8 га (α + β)max = 57.84%;
− для SБАТ = 12 га (α + β)max = 80.71%.
Выбор SБАТ на предпроектной стадии должен проводиться с учетом всех факторов, в том числе суммарной степени замещения природного газа газообразными горючими продуктами пирогаза и биодизелем.
Основные экономические показатели работы Комплекса ВТПК + БАТ:
− сумма капитальных затрат на строительство Комплекса (рис. 18),
− чистая годовая прибыль Комплекса (рис. 19),
Рис. 19.
Зависимость чистой годовой прибыли (П) от площади БАТ Комплекса ВТПК + БАТ. Степень реализации БТ внешним организациям (%): 1 – 0, 2 – 25, 3 – 50, 4 – 75, 5 – 100. Пунктиром показана зависимость суммы капитальных затрат на строительство Комплекса ВТПК + БАТ.
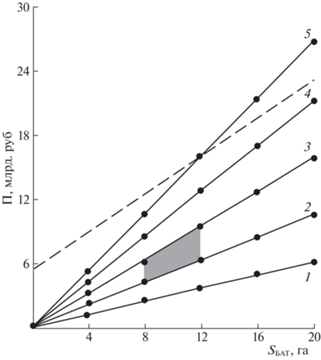
− простой срок окупаемости (рис. 20),
Рис. 20.
Зависимость простого срока окупаемости (PVP) от площади БАТ Комплекса ВТПК + БАТ. Степень реализации БТ внешним организациям (%): 1 – 0, 2 – 25, 3 – 50, 4 – 75, 5 – 100.
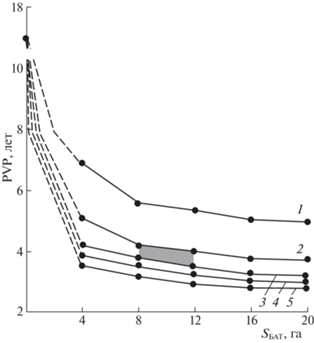
определяются для данной структуры и производительности Комплекса в основном двумя факторами – величиной площади БАТ и степенью реализации БТ внешним организациям. Приемлемый срок окупаемости 3.5–4.5 года (выделенная область на рис. 20) достигается при SБАТ = 8–12 га и степени реализации БТ на внешнем рынке 25–50%. При этих условиях чистая годовая прибыль Комплекса составляет 4.5–10 млрд. руб., а суммарные капитальные затраты составляют 12–16 млрд. руб. (рис. 18). Полученные результаты по экономическим показателям Комплекса ВТПК + + БАТ необходимо использовать на предпроектной стадии. Из приведенных зависимостей видно, что уже при SБАТ = 16 га годовая прибыль перекрывает суммарные капитальные затраты (рис. 19). При этой же величине SБАТ = 16 га весь требуемый природный газ может быть замещен собственными внутренними энергетическими источниками Комплекса.
Предложенная АТ3: Комплекс ВТПК + БАТ получения БТ с использованием МВ Chlorella vulgaris позволяет не только проводить процесс с высокой степенью внутреннего использования СО2 (до 88%), практически полной заменой природного газа производимым БТ и горючими компонентами пирогаза и высокими экономическими показателями, но и гарантированно обеспечивает (помимо решения основной задачи – переработки ОПП) сбыт всей производимой продукции:
− электроэнергии: для функционирования Комплекса ВТПК + БАТ и поставок внешним потребителям;
− тепловой энергии: для функционирования установки получения ТАЦ и поставок внешним потребителям;
− БПШ: для производства базальтовых волокон;
− углекислого газа: для выращивания МВ;
− АБМ: для корма КРС в животноводстве;
− БТ: для использования внутри Комплекса ВТПК + БАТ и/или для поставок внешним потребителям;
− ГЛ: для переработки в химические продукты.
На основе АТ3: Комплекс ВТПК + БАТ предложена структура АПКК, вариант которого приведен на рис. 21. АПКК перерабатывает отходы региональных предприятий и обеспечивает их сырьем и энергоносителями. Производственная мощность Комплекса на предпроектной стадии определяется на основе численности населения и усредненного морфологического состава отходов с учетом некоторого коэффициента запаса. Так, при норме ТКО на одного человека 450 кг/г. и производственной мощности Комплекса 25 тыс. т/г. численность населения (Н) в зоне функционирования Комплекса составляет
где 0.7 – доля ТКО в составе отходов, 1.2 – коэффициент запаса.ВЫВОДЫ
Использование аддитивных технологий позволяет значительно улучшить экономическую и экологическую составляющую базовой технологии плазменной переработки отходов.
Реализация рассмотренных аддитивных технологий плазменной переработки ОПП позволит не только организовать экономически эффективную (с малым сроком окупаемости) переработку отходов с выработкой тепловой и электрической энергии, но и позволит при достаточно больших площадях БАТ полностью исключить использование углеводородного топлива (природного газа) и значительно декарбонизировать данную технологию.
Аддитивные технологии плазменной переработки отходов полностью закрывают вопрос о востребованности производимой продукции.
Использование получаемого в Комплексе ВТПК + БАТ СО2 в самом Комплексе и замена природного газа БТ и газообразными продуктами переработки возобновляемого сырья (отходов) позволяет отнести получаемые продукты (в том числе водород) и саму технологию к числу “зеленых”, что делает ее более привлекательной как в экономическом, так и в экологическом плане по сравнению с традиционной технологией колосникового сжигания.
Работа выполнена в рамках внутренней субсидии НИЦ “Курчатовский институт” № 1569 “Развитие гетерогенных плазменно-пучковых технологий для объемной модификации и создания новых материалов, экологически чистой энергетики и переработки отходов”.
Список литературы
Апостолов А.Г. // Успехи в химии и химической технологии. 2020. Т. 34. № 6. С. 29.
Kitson P.J., Marie G., Francoia J.P. et al. // Science. 2018. № 359 (6373). P. 314.
Parra-Cabrera C., Achille C., Kuhn S. et al. // Chem. Soc. Rev. 2013. V. 47. № 1. P. 209.
Тарасова Н.П., Зайцев В.А., Кузнецов В.А. // Успехи в химии и химической технологии. 2014. Т. 28. № 4. С. 19.
Мешалкин В.П., Ходченко С.М. // Все материалы. Энциклопедический справочник. 2017. № 6. С. 2.
Переславцев А., Вощинин С., Артемов А. Плазменная переработка отходов производства и потребления. London: Lambert Academic Publishing, 2020. 351 p.
Артемов А.В., Переславцев А.В., Вощинин С.А. и др. // Химическая технология. 2021. Т. 22. № 7. С. 294.
Артемов А.В., Переславцев А.В., Вощинин С.А. и др. // Военно-медицинский журнал. 2021. Т. 342. № 4. С. 59.
Артемов А.В., Переславцев А.В., Вощинин С.А. и др. // Экология промышленного производства. 2021. № 3. С. 2.
Артемов А.В., Бульба В.А., Вощинин С.А. и др. // Рос. хим. журн. 2010. Т. 54. № 6. С. 26.
Артемов А.В., Бульба В.А., Вощинин С.А. и др. // Рос. хим. журн. 2010. Т. 54. № 6. С. 9.
Артемов А.В., Переславцев А.В., Вощинин С.А. и др. // Химическая безопасность. 2017. Т. 1. № 2. С. 1874.
Артемов А.В., Вощинин С.А., Переславцев А.В. и др. // Твердые бытовые отходы. 2018. № 3. С. 39.
Артемов А.В., Переславцев А.В., Вощинин С.А. и др. // Твердые бытовые отходы. 2019. № 11. С. 28.
Артемов А.В., Переславцев А.В., Вощинин С.А. и др. // Вода: химия и экология. 2019. № 1012. С. 114.
Артемов А.В., Переславцев А.В., Вощинин С.А. и др. // Военно-медицинский журнал. 20207. № 4. С. 59.
Артемов А.В., Переславцев А.В., Вощинин С.А. и др. // Экология промышленного производства. 2021. № 3. С. 2.
Артемов А.В., Переславцев А.В., Вощинин С.А. и др. // Вода: химия и экология. 2019. № 10–12. С. 114.
Артемов А.В., Переславцев А.В., Вощинин С.А. и др. // Экология промышленного производства. 2022. № 1. С. 2.
Артемов А.В., Переславцев А.В., Вощинин С.А. и др. // Биотехнология. 2022. № 7. С. 55.
Ducharme Caroline. Technical and economic analysis of Plasma-assisted Waste-to-Energy processes (Dissertation). Earth Engineering Center. Columbia University. USA. 2010. 79 p.
Qinglin Zhang. Mathematical modeling of municipal solid waste plasma gasification in a fixed-bed melting reactor (Dissertation). Royal Institute of Technology. Stockyjlm. Sweden. 2011. 196 p.
Umberto Arena // Waste Management. 2012. V. 32. P. 625.
Потравный И.М., Баах Д. // Управленческие науки / Management Science in Russia. 2021. Т. 11. № 3. С. 6.
Привалова Е.И., Мяки-Арвела П., Мурзин Д.Ю. и др. // Успехи химии. 2012. Т. 81. № 5. С. 435.
Смоллбоун Э. // 10 прорывных идей в энергетике на следующие 10 лет. Глобальная энергия. 2021. С. 4.
Артемов А., Переславцев А., Вощинин С. и др. // Русский инженер. 2020. № 4 (69). С. 30.
Артемов А.В., Переславцев А.В., Вощинин С.А. и др. // Экология промышленного производства. 2021. № 2. С. 7.
Мельгунов М.С. // Промышленный катализ в лекциях. 2009. № 8. С. 62.
Артемов А.В., Переславцев А.В., Вощинин С.А. и др. // Энергия: экономика, техника, экология. 2021. № 6. С. 30.
Журавлев И.Б., Залужный А.А., Птицын П.Б. Технико-экономические исследования (ТЭИ) по теме приоритетного направления научно-технического развития “Водородная энергетика”. М.: ЦАИР, частное учреждение “Наука и инновации”. 2021. 150 с.
Дубинин А.М., Кагарманов Г.Р., Финк А.В. // Изв. вузов. Химия и химическая технология. 2009. Т. 52. № 2. С. 54.
Артемов А.В., Переславцев А.В., Крутяков Ю.А. и др. // Экология и промышленность России. 2011. № 9. С. 20.
Крылов О.В. // Российский химический журнал. 2000. Т. 44. № 1. С. 19.
Tomishige K., Chen Y.-G., Fujimoto K. // J. Catal. 1999. V. 181. № 1. P. 91.
Найбороденко Ю.С., Касацкий Н.Г., Китлер В.Д. и др. Патент РФ 2349380 МПК B01J 37/00, B01J 21/02, B01J 23/705, B01J 23/88, C07C 1/04. Катализатор и способ получения синтез-газа углекислотной конверсией метана., опубл. 20.03.2009. БИ № 8.
Аркатова Л.А., Харламова Т.С., Галактионова Л.В. и др. // Журн. физ. химии. 2006. Т. 80. №8. С. 1403.
Crisafulli C., Scire S., Minico S. // Appl. Catal. 2002. № 225. P. 1.
Shested J., Jacobsen C.J., Rokni S., Rostrup-Nielsen J.R. // J. Catal. 2001. № 201. P. 206.
Крылов О.В. Гетерогенный катализ. М.: Академкнига, 2004. 679 с.
Hu Y.H., Ruckenstein E. // Adv. Catal. 2004. V. 48. P. 297.
Tomishige K. // Catal. Today. 2004. № 89. P. 405.
Hao Z., Zhu H.Y., Lu G.Q. // Appl. Catal. 2003. № 242. P. 275.
Федотов А.С., Антонов Д.О., Уваров В.И. и др. // Док. РАН. 2014. Т. 459. № 3. С. 309.
Артемов А.В. // Катализ в промышленности. 2001. № 2. С. 18.
Артемов А.В., Жильцов В.А., Крутяков Ю.А. и др. // Вопросы атомной науки и техники. 2008. № 4. С. 150.
Артемов А.В., Кулыгин В.М., Переславцев А.В. и др. // Катализ в промышленности. 2011. № 5. С. 34.
Артемов А.В., Жильцов В.А., Крутяков Ю.А. и др. Патент РФ 2437741 МПК B22F 9/14, B82B 3/00. Способ получения нанодисперсных металлов в жидкой фазе. опубл. 27.12.2011. БИ № 36.
Артемов А.В., Жильцов В.А., Крутяков Ю.А. и др. Патент РФ 2430999 МПК C25C 7/00, B82B 3/00. Устройство для получения нанодисперсных металлов в жидкой фазе. опубл. 10. № 28.
Артемов А.В., Брыкин А.В., Арсеньева Д.Ю. // Катализ в промышленности. 2015. Т. 15. № 5. С. 11.
Артемов А.В., Брыкин А.В., Кочнев А.М. и др. Патент РФ на полезную модель 153579 МПК B01J 37/02, B82B 1/00. Установка для получения нагруженных веществами из нанодисперсий тел носителей. опубл. 27.07.2015. БИ № 21.
Брыкин А.В., Артемов А.В., Колегов К.А. // Катализ в промышленности. 2013. № 4. С. 7.
Дедов А.Г., Локтев А.С., Мазо Г.Н. и др. // Докл. РАН. 2015. Т. 462. № 1. С. 58.
Дедов А.Г., Шляхтин О.А., Локтев А.С. и др. // Докл. РАН. 2017. Т. 477. № 4. С. 425.
Бухаркина Т.В., Гаврилова Н.Н., Скудин В.В. // Катализ в промышленности. 2015. Т. 15. № 3. С. 54.
Крылов О.В. // Катализ в промышленности. 2007. № 2. С. 13.
Ferreira-Aparicio H., Benito M.J. // Catal. Rev. 2006. V. 47. P. 491.
Цодиков М.В., Тепляков В.В., Магсумов М.И. и др. Патент РФ 2325219 МПК B01D 71/02, C01B 3/38. Пористый керамический каталитический модуль и способ получения синтез-газа в его присутствии. опубл. 27.05.2008. БИ № 15.
Производство капролактама / Под ред. Овчинникова В.И., Ручинского В.Р. М.: Химия, 1977. С. 118.
Чернышев А.К., Герасименко В.И., Сокол Б.А. и др. Капролактам: свойства, производство, применение. М.: ЗАО “МНИК “ИНФОХИМ”, 2016. Т. 1. С. 396.
Исмагилов З.Р., Кузнецов В.В., Шикина Н.В. и др. Патент РФ 2350386 МПК B01J 23/83, B01J 21/04, B01J 37/02, B01J 37/04, C01B 3/26, C01B 3/38. Катализатор, способ его приготовления и способ получения синтез-газа из метана. опубл. 27.03.2009. БИ № 9.
Тимошин Е.С., Морозов Л.Н., Батанов А.А. // Химическая технология. 2020. Т. 21. № 4. С. 181.
Бухаркина Т.В., Гаврилова Н.Н., Скудин В.В. // Катализ в промышленности. 2015. № 4. С. 14.
Брыкин А., Артемов А., Арсеньева Д. // Современная электроника. 2015. № 2. С. 2.
Артемов А.В., Крутяков Ю.А., Переславцев А.В. и др. Международная заявка WO 2012/112065 МПК C01B 3/34, B01J 19/08, C01B 3/38. Способ и устройство для получения синтез-газа. дата межд. публ. 23.08.2012.
Юрьева Т.М., Демешкина Н.П., Хасин А.А. и др. Патент РФ 2314870 МПК С01В 3/16, B01J 23/86, B01J 37/04. Катализатор паровой конверсии монооксида углерода, способ его приготовления и способ его использования. опубл. 20.01.2008. БИ № 2.
Дубровский А.Р., Кузнецов С.А., Рябов Е.В. и др. // Рос. хим. журн.2011. Т. 55. № 2. С. 43.
Burke L.D., Nugent P.F. // Gold Bull. 1998. № 31. P. 39.
Lei Y., Cant N.W., Trimm D.L. // Chem. Eng. J. 2005. V. 114. P. 81.
Liu Q., Ma W., He R., Mu Z. // Catal. Today. 2005. V. 106. P. 52.
Tida H., Igarashi A. // Ibid. 2006 V. 303. P. 48.
Patt J., Moon D.J., Philips C. et al. // Catal. Lett. 2000 V. 65. P. 193.
Крылов О.В. // Катализ в промышленности. 2004. № 8. С. 48.
Комова З.В., Фирсов О.П., Вейнбендер А.Я. и др. Патент РФ 2282496 МПК B01J 21/02, B01J 23/80, B01J 37/04. Способ приготовления медьцинкалюминиевого катализатора (варианты). опубл. 27.08.2006. БИ № 24.
Батенин В.М., Масленников В.М., Штеренберг В.Я. и др. // Докл. РАН. 2018. Т. 483. № 5. С. 506.
Singh J., Dhar D.W. // Front. Mar. Sci. 2019. № 6. article № 29.
Zhou W., Wang J., Chen P. et al. // Renew. Sust. Energ. Rev. 2017. V. 76. P. 1163.
Варфоломеев С.Д., Вассерман Л.А. // Биотехнология. 2011. № 2. С. 9.
Vuppaladadiyam A.K., Yao J.G., Florin N. et al. // Chemsuschem. 2018. V. 11. № 2. P. 334.
Khan M.I., Shin J.H., Kim J.D. // Microbial Cell Factories. 2018. V. 17. article № 36.
Ahmad M.T., Shariff M., Yusoff F. et al. // Rev. Aquac. 2020.V. 12. № 1. P. 328.
Saeedi Dehaghani A.H., Pirouzfar V. // Heфтexимия. 2018. V. 58. № 4. P. 496.
Kwon E.E., Jeon Y.J., Yi H. // Bioresour. Technol. 2013. V. 129. P. 672.
Fukuda H., Kondo F., Noda H. // J. Biosci. Bioeng. 2001. V. 92. № 5. P. 405.
Yuzhong L., Cruz-Morales P., Zargar A. et al. // Cell. 2021. V. 184. № 6. P. 1636.
Rene H.N., Barbosa M.J. // Science (N.Y.). 2010. V. 329. P. 796.
Voloshin R.A., Rodionova M.V. et al. // Int. J. Hydrogen Energy. 2016. V. 41. P. 17257.
Rahman M.A., Aziz M.A. et al. // J. Radiat. Res. Appl. Sci. 2017. V. 10. P. 140.
Селищева С.А., Лебедев М.Ю., Решетников С.И. и др. // Катализ в промышленности. 2012. № 2. С. 63.
Воропаев П.А., Золотарева М.С., Штепа О.И. и др. // Успехи в химии и химической технологии. 2021. Т. 35. № 7. С. 66.
Цодиков М.В., Яндиева Ф.А., Чистяков А.В. и др. // Докл. РАН. 2012. Т. 447. № 5. С. 534.
Джабаров Г.В., Биккулова А.И., Воронов М.С. и др. // Успехи в химии и химической технологии. 2017. Т. 31. № 12. С. 42.
Козеева И.С., Густякова С.И., Макаров А.А. и др. // Успехи в химии и химической технологии. 2016. Т. 30. № 11. С. 19.
Campbell M.N. // Guelph Eng. J. 2008. № 1. P. 2.
Chisti Y. // Biotechnol. Adv. 2007. V. 25. P. 294.
Петренко А.В., Макаров В.В. // Успехи в химии и химической технологии. 2008. Т. 22. № 1. С. 21.
Скичко А.С., Лукьянова А.В., Крыцовкина Н.Г. и др. // Успехи в химии и химической технологии. 2010. Т. 24. № 1. С. 33.
Кулов Н.Н., Гордеев Л.С. // Теоретические основы химической технологии. 2014. Т. 48. № 3. С. 243.
Болдырева В.Г., Скичко А.С. // Успехи в химии и химической технологии. 2019. Т. 33. № 11. С. 20.
Аркадьева И.Н., Скичко А.С. // Успехи в химии и химической технологии. 2013. Т. 27. № 1. С. 12.
Лелеков А.С., Тренкеншу Р.П. // Математическая биология и биоинформатика. 2020. Т. 15. № 2. С. 158.
Лелеков А.С., Тренкеншу Р.П. // Математическая биология и биоинформатика. 2021. Т. 16. № 1. С. 101.
Зорин В.В., Петухова Н.И., Шахматов Р.Н. // Рос. хим. журн. 2011. Т. 55. № 1. С. 77.
Плетнев М.Ю. // Биотехнология. 2009. № 1. С. 3.
Mufrodi Z., Rochmadi S., Budiman A. // Int. J. Chem. 2012. V. 4. № 2. P. 101.
Mufrodi Z., Sutijan R., Budiman A. // Eng. J. 2013. V. 18. № 2. P. 29.
Печенев Ю.Г., Савинова М.А., Анкудимов В.А. и др. Патент РФ 2047596 МПК С07С 69/18, С07С 67/08. Способ получения триацетина. опубл. 10.11.1995.
Bremus N., Dieckelmann G., Jeromin L. Et al. Патент США 4381407 МПКС07С 69/18, С07С 67/08. Process for the continuous production of triacetin. опубл. 26.04.1983.
Khayoon M.S., Triwahyono S., Hameed B.H., Jalil A.A. // Chem. Eng. J. 2014. V. 243. P. 473.
Khayoon M.S., Hameed B.H. // Bioresour. Technol. 2011. V. 102. P. 9229.
Kotbagi T.V., Pandhare S.L., Dongare M.K., Umbar-kar S.B. // J. Environ. Anal. Chem. 2015. № 2. P. 2380.
Rfle S., Armbruster U., Umbarkar S. et al.10-th Green Chemistry Conference. Barselona. Spain. 2013.
Печенев Ю.Г., Савинова М.А., Анкудимов В.А. и др. Патент РФ 2047596 МПК С07С 69/18, С07С 67/08. Способ получения триацетина. опубл. 10.11.1995.
Bremus N., Dieckelmann G., Jeromin L. et al. Патент США 4381407 МПКС07С 69/18, С07С 67/08. Process for the continuous production of triacetin. опубл. 26.04.1983.
Hersecski Z., Marton G. // Proc. 10-th Intern. Conf. Environ. Sci. Tech. Greece. 2007. P. B-284.
Adhikarri S., Fernando S.D., Haryanto A. // Renew. Energy. 2009. V. 33. P. 109.
Данов С.М., Есипович А.Л., Белоусов А.С. и др. // Катализ в промышленности. 2017. № 2. С. 102.
Супрун В., Папп Ч. // Катализ в промышленности. 2011. № 1. С. 7.
Mota C.J.A., da Silva C.X.A., Rosenbach N. et al. // Energy Fuels. 2010. № 10. P. 2733.
Варфоломеев С.Д., Вольева В.Б., Усачев С.В. и др. // Катализ в промышленности. 2010. № 5. С. 39.
Королев Ю.А., Грейш А.А., Козлова Л.М., Кус-тов Л.М. // Катализ в промышленности. 2010. № 4. С. 34.
Королев Ю.А., Грейш А.А., Козлова Л.М. и др. // Катализ в промышленности. 2010. № 3. С. 63.
Штанковиак Ф., Франке О. Патент РФ 2436761 МПК С07С 31/20, С07С 29/60. Способ получения 1,2-пропандиола гидрогенолизом глицерина. опубл. 20.12.2011. БИ 35.
Штанковиак А., Франке О. Патент РФ 2439047 МПК С07С 31/20, С07С 29/60. Способ получения 1,2-пропандиола гидрогенолизом глицерина. опубл. 10.01.2012. БИ 1.
Меньщиков В.А., Ачильдиев Е.Р., Семенов И.П. Патент РФ 2663419 МПК С07С 29/60, С07С 31/20, С07С 29/60. Способ получения 1,2-пропандиола из глицерина. опубл. 06.08.2018. БИ 22.
Михайлов Ю.М., Кустов Л.М., Алешин В.В. и др. // Катализ в промышленности. 2011. № 1. С. 73.
Dmitriev G., Zanaveskin L. // Chem. Eng. Trans. 2011. V. 24. Pt. 1. P. 43.
Дмитриев Г.С., Занавескин Л.Н. // Химическая промышленность сегодня. 2012. № 3. С. 8.
Самойлов В.О., Рамазанов Д.Н., Нехаев А.И., Максимов А.А. // Нефтехимия. 2016. Т. 56. № 2. С. 144.
Ипполитов Е.Г., Артемов А.В., Трипольская Т.А. и др. // Катализ в промышленности. 2001. № 3. С. 7.
Дополнительные материалы отсутствуют.
Инструменты
Вестник Военного инновационного технополиса «ЭРА»