Высокомолекулярные соединения (серия А), 2020, T. 62, № 5, стр. 370-379
ПОЛУЧЕНИЕ, МЕХАНИЧЕСКИЕ И ТЕРМИЧЕСКИЕ СВОЙСТВА КОМПОЗИЦИОННЫХ МАТЕРИАЛОВ НА ОСНОВЕ ВТОРИЧНОГО ПОЛИПРОПИЛЕНА И МОДИФИЦИРОВАННЫХ БАЗАЛЬТОВЫХ ВОЛОКОН
К. Б. Галицейский a, Я. А. Тиманцев b, Р. В. Докучаев c, Т. А. Мацеевич c, М. И. Бузин b, К. С. Пиминова b, А. А. Аскадский b, c, *
a Московский авиационный институт (Национальный исследовательский университет)
125993 Москва, Волоколамское ш., 4, Россия
b Институт элементоорганических соединений им. А.Н. Несмеянова Российской академии наук
119991 Москва, ул. Вавилова, 28, Россия
c Московский государственный строительный университет
129337 Москва, Ярославское ш., 26, Россия
* E-mail: andrey@ineos.ac.ru
Поступила в редакцию 07.10.2019
После доработки 25.03.2020
Принята к публикации 03.04.2020
Аннотация
Представлены композиционные материалы на основе вторичного полипропилена и коротко-рубленых базальтовых волокон. Композиты имеют в своем составе от 5 до 20% базальтовых волокон; каждый композит был прогрет при температуре 500, 650 и 750°С. Для всех образцов получены кривые растяжения и сжатия. Модуль упругости при растяжении достигает 2120 МПа при содержании базальтовых волокон 20%, причем для исходного вторичного полипропилена этот модуль равен 705 МПа. Прочность 44.5 МПа (для исходного вторичного полипропилена прочность 32.0 МПа), удельная ударная вязкость 18.3 кДж/м2 (для исходного вторичного полипропилена эта величина составляет 14.4 кДж/м2).
В настоящей работе получены композиционные материалы на основе вторичного полипропилена и базальтовых волокон, детально исследованы их предельные механические и релаксационные свойства. В данном случае решалась задача изменения свойств поверхности базальтовых волокон с целью улучшения его адгезии к полиолефиновой матрице. Структура и некоторые свойства базальтовых волокон уже были рассмотрены в ряде работ [1–3], где отмечалось, что механические свойства базальтовых волокон зависят от химического строения и условий обработки, например, таких как температура вытяжки. Так, прочность базальтовых волокон на растяжение имеет тенденцию к увеличению с ростом температуры вытяжки. Модуль упругости базальтовых волокон колеблется между 78 и 90 ГПА для волокна из разных источников, а самый высокий модуль был получен в работе [1]. В большинстве публикаций утверждается, что по сравнению со стекловолокном базальтовое волокно имеет более высокий или сопоставимый модуль и прочность [1, 2], хотя в работе [3] сообщается о гораздо более низкой его прочности.
Помимо хороших механических свойств, базальт обладает высокой хемо- и термостойкостью [2], неплохими тепловыми, электрическими и звукоизоляционными свойствами [4]. Теплоизолирующая способность базальта в 3 раза больше, чем асбеста [5, 6], благодаря чему базальт широко используют в противопожарной защите [4–6]. Также у базальта в 10 раз лучше электроизоляционные свойства, чем у того же стекла [5, 6]. Базальт гораздо более химически стоек, чем стекловолокно, особенно в сильных щелочах. По базальтовым композитным трубам можно транспортировать агрессивные жидкости и газы [4–6]. Полимербетоны на основе полибутадиеновой матрицы с кварцевым песком и пеплом в качестве заполнителей обладают очень высоким сопротивлением к кислотам и щелочам, превосходной твердостью и адгезией к металлическим элементам, введенным в композит. Удельная работа разрыва составляет 80–90 МПа. Кроме того, сам базальт можно использовать в широком диапазоне температуры от –260–200 до +650–800°C по сравнению со стекловолокном (от –60 до +450–460°C) [4–6, 9, 8 ]. Замена стекловолокна базальтовым волокном может уменьшить риск загрязнения окружающей среды высокотоксичными металлами и их оксидами, которые продуцируются в производстве стекловолокна. Кроме того, оно имеет более высокую жесткость и прочность, чем то же стекловолокно [9, 10]. Поэтому базальтовое волокно все более широко используют, изучают его действие в композитах на основе ряда полимеров [8, 11]. В некоторых случаях базальтовое волокно смешивают с другим волокном в матрице с образованием гибридного композита [12, 13].
Что касается вторичного ПП, то в работах [14–17] был осуществлен комплекс исследований релаксационных свойств материалов на основе этого полимера. Выполнены эксперименты по релаксации напряжения в условиях растяжения и сжатия при разной температуре и деформациях, получены обобщенные релаксационные кривые, определены области линейного и нелинейного механического поведения, а также проведено сравнение механических релаксационных свойств первичного и вторичного ПП. Оказалось, что модуль упругости вторичного ПП существенно выше, чем первичного, но предельная деформация при растяжении резко снижается. При сжатии обобщенные кривые релаксации вторичного ПП лежат существенно выше по напряжению, чем аналогичные кривые для первичного ПП, что связано с увеличением степени кристалличности при рециклинге ПП. Полученные в работах [14–17] данные легли в основу монографии [18].
В целом, использованию вторичных материалов, получаемых в результате рециклинга, в современном мире уделяется повышенное внимание, поскольку это снижает антропогенную нагрузку на окружающую среду. Армированные композиты на основе вторичного ПП в данной работе получены с использованием в качестве наполнителя коротко-рубленых базальтовых волокон, поверхность которых обработана нестандартным способом, приводящим к образованию химических групп ≡CH, =CH2, –CH3. Принцип обработки можно пояснить на примере монодисперсных частиц углерода [19, 20]. Такие частицы были получены в процессе хлорирования метана, проводимого в проточном реакторе в неравновесном режиме при дефиците хлора. Они обладают ультрадисперсностью (наноразмерностью) и монодисперсностью. Ультрадисперсность создает достаточно большую площадь поверхности границы раздела фаз, и таким образом увеличивает влияние межфазных явлений за счет поверхностного слоя. Реализация на практике такого рода процесса из-за возможной его неустойчивости представляет достаточно сложную инженерную и технологическую задачу. Такой же процесс применим к обработке поверхности базальтовых волокон, в результате которой увеличивается термодинамическая и технологическая совместимость ПП с поверхностью волокон и повышается модуль упругости композитов и их прочность.
Исследование композитов ПП, наполненных базальтовыми волокнами, проведено в работе [21]. Так, для получения композитов рубленые базальтовые волокна на первой стадии совмещались с ПП в двухшнековом экструдере с дальнейшим литьем под давлением на второй стадии. Улучшение совместимости ПП с базальтовыми волокнами достигалось комбинацией замасливателя и аппрета. В качестве замасливателя в работе [21] был использован малеинизированный полипропиленовый воск, аппретом служил аминосилан. Полученные композиты обнаружили увеличение прочности при изгибе и растяжении, но одновременно наблюдалось снижение удельной ударной вязкости и удлинения при разрыве. В работе [22] исследованы механические свойства и структура наполненных короткими базальтовыми волокнами композитов на основе ПП и металлоценового этиленпропиленового эластомера. Показано, что введение коротко-рубленых базальтовых волокон в смеси полипропилен–металлоценовый этиленпропиленовый эластомер обеспечивает хорошую адгезию волокна с матрицей путем добавления малеинизированного полипропилена, что влечет повышение модуля упругости и предела текучести при растяжении. При испытаниях на образцах с надрезом удельная ударная вязкость композитов полипропилен–металлоценовый этиленпропиленовый эластомер–базальтовое волокно–малеинизированный полипропилен улучшается с увеличением содержания волокон.
Реакции, проходящие на поверхности твердого тела, имеют ряд существенных отличий от объемных реакций. Для осуществления таких реакций и получения требуемого результата, необходимо выполнять следующие условия. Во-первых, подготовить поверхность, при которой проводится термовакуумирование и обработка в различных средах, окислительной и(или) восстановительной [23]. Во-вторых, следует поддерживать заданный режим неравновесного процесса путем отвода непрореагировавших компонентов и побочных продуктов реакции [23].
Поверхностные свойства базальтового волокна зависят от его химического состава – это, главным образом, SiO2 и MxOy (М – это в основном Al, Fe и, в значительно меньшей доле, Ti, Ca, Na). Такие примеси, как фосфор и сера, не рассматриваются в силу их незначительного содержания. Все структурные элементы состава базальта, согласно работе [23], обладают каталитической активностью. Поскольку основным компонентом в составе базальтового волокна является SiO2 (~49%), то в настоящей работе рассмотрены реакции, приводящие к появлению химических групп ≡CH, =CH2, –СH3 на поверхности базальтовых волокон, химически связанных с SiO2.
Пиролиз метана является автокаталитическим процессом; данный процесс ускоряет такой элемент, как хлор [24]. Важно, что характерное для поверхностных реакций, большее по сравнению с объемными, выделение тепла при образовании химической связи, а также автокаталитический характер процесса могут привести к тому, что пиролиз будет протекать не только на поверхности, но и в некотором приповерхностном объеме. Интенсивность данного процесса возрастает, что может привести к полной диссоциации молекул CH4 и отложению на поверхности пиролитического углерода. Поэтому важно задать такие термодинамические параметры, которые бы поддерживали процесс в неравновесном состоянии при минимальных отклонениях температуры, давления и концентрации от заданных. Этого можно достичь выбором скорости потока газовой фазы, который не только выводит непрореагировавшие компоненты и побочные продукты реакции, но и отводит тепло из реакционной зоны. Принципиальная схема установки показана на рис. 1.
ЭКСПЕРИМЕНТАЛЬНАЯ ЧАСТЬ
Получение композиций и образцов
В данной работе использовали рубленое базальтовое волокно марки “КВ-41” фирмы “Каменный век” Общества с ограниченной ответственностью “Базальтовые материалы” (Россия). Основные технические характеристики исходных базальтовых волокон марки “КВ-41”:
Тип и содержание замасливателя, мас. % | силановый, ≥0.4 |
Диаметр монофиламента, мкм | 13–21 |
Длина волокна, мм | 5.8 |
Влажность, мас. % | <0.1 |
Для модификации поверхности базальтового волокна в первую очередь осуществляли термовакуумирование волокон при температуре 500, 650 и 750°С в течение 2 ч. После чего проводили обработку поверхности сначала парами тетрахлорметана в проточном реакторе с целью замещения атомов кислорода на атомы хлора, а затем, уже хлорированную поверхность в токе CH4 для замещения хлора на целевые алкильные группы.
Также подвергали обработке удаление замасливателя при помощи нагревания в окислительной среде. Исходный лубрикант – прямой замасливатель марки “КВ-12”. Лубрикант полностью удаляли еще до начала обработки.
На стадии смешения исходных компонентов для приготовления композиций на основе вторичного ПП поэтапно выполняли следующие операции:
– дробление технологических отходов литьевого производства до частиц, размером не более 5 мм в диаметре;
– смешение сухих компонентов в емкости для получения исходной смеси;
– экструдирование смеси в двухшнековом лабораторном экструдере (диаметр шнека 30 мм, L/D = 15) при температуре по зонам 210–220–210°С и скорости вращения шнека 60–65 об/мин;
– вытягивание экструдата в виде стренги с последующим охлаждением в водной ванне;
– грануляцию стренги.
Для измерения механических свойств композитов образцы для испытаний на растяжение и сжатие получали методом литья под давлением на ручном лабораторном литьевом прессе при температуре материального цилиндра 215°С. Методом горячего прессования изготавливали пластины размером 70 × 140 мм толщиной 4.0 мм, из которых затем выпиливали образцы необходимого размера для испытаний на изгиб, удар и релаксацию напряжения. Прессование образцов проводили на лабораторном гидравлическом прессе рамной конструкции при описанном далее режиме прессования. Пресс-форму открытого типа с навеской композиции помещали между нагретыми до 220°С плитами пресса и выдерживали в течение 10 мин при удельном давлении 3 МПа. По истечении заданного промежутка времени давление увеличивали до 8 МПа, и форму выдерживали в течение 5 мин под этим давлением. Далее без размыкания плит пресса и при постоянно поддерживаемом давлении форму охлаждали до 60°С, после чего ее извлекали из пресса.
Методы исследования
Поверхность модифицированных базальтовых волокон исследовали методом инфракрасной ИК-фурье-спектроскопии в режиме пропускания. ИК-спектры снимали с помощью спектрофотометра “Nicolet 360 FTIR” в диапазоне волновых чисел 400–4000 см–1.
Для определения наличия углеводородных групп на поверхности модифицированных базальтовых волокон применяли метод рентгенофлуоресцентного анализа (РФА). Спектры РФА снимали с помощью энергодисперсионного спектрометра “SSD X-Max” (“Oxford Instruments”, Великобритания).
Кривые растяжения получали на разрывной машине “ИР-5046” при различной скорости деформации. Для определения модуля упругости при растяжении скорость опускания нижней траверсы машины составляла 2 мм/мин, для остальных показателей – 50 мм/мин. Датчики испытательной машины подключали к компьютеру для автоматической регистрации и обработки данных измерений. Использовали лопатки с длиной рабочей части 60.0 ± 1.0 мм, шириной 10.0 ± 0.4 мм, толщина рабочей части 2.0 ± 0.2 мм.
При испытании на сжатие использовали образцы цилиндрической формы высотой 15 мм и диаметром 10 мм. Кривые сжатия получали на разрывной машине “ИР-5046” при разной скорости деформации. Для нахождения модуля упругости при растяжении скорость опускания нижней траверсы машины составляла 2 мм/мин, для остальных показателей – 10 мм/мин.
Максимальное напряжение при изгибе и ударную вязкость образцов определяли на приборе типа “Динстат” в соответствии с DIN-53435. Испытания проводили для образцов размером 15 × × 10 × 4 мм без надреза.
Испытания на релаксацию напряжения осуществляли на приборе для микромеханических испытаний конструкции Дубова–Регеля в режиме одноосного сжатия на образцах размером 4 × × 4 × 6 мм с плоскопараллельными гранями. Напряжение, действующие на образец, измеряли с помощью фотоэлектрооптического динамометра, показания которого преобразовали в электрический сигнал и регистрировали с помощью гальванометра.
Теплофизические свойства композиционных материалов исследовали методом ДСК на приборе DSC-822 (“Mettler–Toledo”, Швейцария) при скорости нагревания 10 град/мин в атмосфере воздуха.
Термическую стабильность полученных композиционных материалов оценивали методом ТГА на приборе “Derivatograth-C” (“МОМ”, Венгрия) на воздухе при скорости нагревания 10 град/мин и массе образцов 25 мг.
РЕЗУЛЬТАТЫ И ИХ ОБСУЖДЕНИЕ
Прежде всего, следует охарактеризовать свойства вторичного ПП, использованного в данной работе. Показатель текучести расплава вторичного ПП составляет 3.2 г/10 мин. Плотность образца, отпрессованного вторичного ПП, составляет 0.9740 г/см3. Расчет степени кристалличности αcr был проведен по формуле
(1)
${{{\alpha }}_{{cr}}} = \frac{{{{{\rho }}_{{cr}}}({\rho } - {{{\rho }}_{a}})}}{{{\rho (}{{{\rho }}_{{cr}}} - {{{\rho }}_{a}}{\text{)}}}},$Величины ρcr и ρa рассчитаны с помощью компьютерной программы “Каскад”, и было найдено αcr = 67%. Для первичного ПП степень кристалличности αcr = 65%.
Термомеханическая кривая вторичного ПП, использованного в данной работе, показана на рис. 2. Видно, что температура плавления составляет ~170°С, что соответствует ПП.
Чтобы оценить влияние температуры термообработки, были проведены опыты с варьированием температуры аппретирования от комнатной до 750°С. Полученные материалы испытаны на растяжение, сжатие, изгиб, удельную ударную вязкость. Каждое испытание проводилось от 4 до 6 раз. Результаты испытаний на растяжение образцов обобщены в табл. 1 и на рис. 3 и 4.
Таблица 1.
Значения модуля упругости, максимального напряжения и предельной деформации при растяжении
Температура обработки, °С | Доля базальтового волокна, % | Модуль упругости, МПа | Напряжение при разрыве, МПа | Предельная деформация при растяжении, % |
---|---|---|---|---|
20 | 0 | 705 ± 16 | 26.5 ± 0.3 | – |
5 | 1060 ± 86 | 33.1 ± 0.6 | 11 ± 1 | |
10 | 1390 ± 41 | 33.5 ± 0.5 | 10 ± 1 | |
15 | 1860 ± 133 | 34.2 ± 0.4 | 10 ± 1 | |
20 | 1670 ± 118 | 37.7 ± 0.9 | 9 ± 1 | |
500 | 5 | 870 ± 87 | 31.9 ± 0.3 | 13 ± 3 |
10 | 1330 ± 54 | 33.6 ± 0.7 | 11 ± 4 | |
15 | 1730 ± 117 | 35.7 ± 1.3 | 9 ± 2 | |
20 | 2120 ± 228 | 37.9 ± 0.7 | 8 ± 2 | |
650 | 5 | 1010 ± 52 | 34.8 ± 0.9 | 20 ± 3 |
10 | 1440 ± 149 | 35.9 ± 1.9 | 10 ± 1 | |
15 | 1660 ± 127 | 36.3 ± 1.3 | 9 ± 2 | |
20 | 1810 ± 136 | 38.1 ± 1.7 | 8 ± 1 | |
750 | 5 | 1270 ± 92 | 36.1 ± 1.5 | 24 ± 4 |
10 | 1360 ± 109 | 37.2 ± 1.3 | 14 ± 2 | |
15 | 1410 ± 129 | 38.3 ± 1.4 | 11 ± 1 | |
20 | 1730 ± 186 | 38.6 ± 0.4 | 9 ± 1 |
Рис. 3.
Зависимость модуля упругости от степени наполнения базальтовых волокон при растяжении. Здесь и на рис. 4–7 температура обработки волокон 20 (1), 500 (2), 650 (3) и 750°С (4).
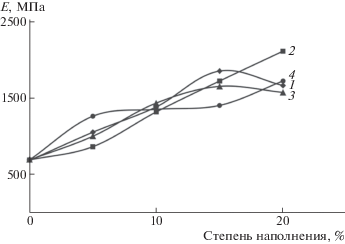
Значения модуля упругости и предела вынужденной эластичности при сжатии приведены в табл. 2 и на рис. 5.
Таблица 2.
Модуль упругости и предел вынужденной эластичности при сжатии
Температура обработки, °С | Доля базальтового волокна, % | Модуль упругости, МПа | Предел вынужденной эластичности при сжатии, МПа |
---|---|---|---|
20 | 0 | 320 ± 15 | 41.0 |
5 | 340 ± 27 | 39.1 | |
10 | 330 ± 23 | 40.3 | |
15 | 320 ± 23 | 39.7 | |
20 | 370 ± 10 | 39.7 | |
500 | 0 | – | – |
5 | 440 ± 27 | 39.3 | |
10 | 420 ± 15 | 41.2 | |
15 | 390 ± 35 | 40.9 | |
20 | 410 ± 10 | 39.6 | |
650 | 0 | – | – |
5 | 360 ± 29 | 38.9 | |
10 | 350 ± 11 | 39.9 | |
15 | 320 ± 13 | 43.2 | |
20 | 330 ± 30 | 39.2 | |
750 | 0 | – | – |
5 | 360 ± 21 | 38.2 | |
10 | 315 ± 25 | 40.4 | |
15 | 280 ± 12 | 41.4 | |
20 | 370 ± 27 | 44.5 |
Из приведенных данных видно, что добавление коротко-рубленых базальтовых волокон (5–20 мас. %) в состав ПП матрицы вызывает значительное повышение модуля упругости образцов, при этом чем больше степень наполнения, тем выше модуль упругости материала (рис. 3). Такая зависимость прослеживается и для композитов с обработанными базальтовыми волокнами, и с необработанными. По сравнению с исходным вторичным ПП модуль упругости композитных материалов увеличился в 2–3 раза: с 705 МПа до 1580–2120 МПа. Наибольшие и наименьшие значения модуля упругости при равных степенях наполнения ω = 20 мас. % были получены для образцов, обработанных при 500 и 650°С соответственно. Для остальных исследуемых образцов значения модуля упругости составили в среднем на 20% ниже максимального, что, вероятнее всего, связано с меньшим адгезионным взаимодействием между ПП матрицей и базальтовым волокном.
Как известно, при наполнении волокном большое значение приобретают прочностные и деформационные характеристики самих волокон при условии реализации достаточно хорошего адгезионного взаимодействия между волокном и матрицей. В этом случае прочность материала определяется не только прочностью прослоек полимерной матрицы, но и прочностью волокон, проходящих через элемент поперечного сечения образца [25–30]. Так как прочность при растяжении базальтового волокна (2700–3200 МПа) значительно превышает аналогичный показатель для ПП (26.5 МПа), то во время приложения нагрузки к образцу адгезионное взаимодействие на поверхности волокна может оказаться больше, чем прочность волокна, в результате чего механическое воздействие воспринимается не только матрицей, но и самими волокнами. Помимо адгезии на границе раздела фаз при разрушении наполненных пластмасс значительное влияние также оказывает наличие микроскопических дефектов. Основной причиной появления трещин в образце при разрушении является концентрация напряжения в местах возникновения. Наполнитель в составе полимерной матрицы может препятствовать развитию трещин в материале, что непосредственно ведет к замедлению процессов разрушения.
По сравнению с ненаполненным вторичным ПП предел прочности полученных композитов (табл. 3) увеличился с 26.5 до 38.0 МПа (среднее значение при ω = 20 мас. %). Однако, сравнивая результаты разрушающей нагрузки композита с немодифицированными волокнами и композитов с модифицированными волокнами, при высоких степенях наполнения особых различий не было выявлено: значения отличались друг от друга менее чем на 5%, что может быть объяснено погрешностью в проведении испытаний и математической обработке данных.
Таблица 3.
Прочность при изгибе и удельная ударная вязкость
Температура обработки, °С | Доля базальтового волокна, % | Прочность при изгибе, МПа | Удельная ударная вязкость, кг см/см2 |
---|---|---|---|
20 | 0 | 77.0 | 14.4 |
5 | 63.0 | 17.0 | |
10 | 67.0 | 18.3 | |
15 | 74.0 | 15.4 | |
20 | 66.0 | 13.6 | |
500 | 5 | 69.0 | 16.5 |
10 | 71.0 | 18.0 | |
15 | 73.0 | 14.7 | |
20 | 72.0 | 14.3 | |
650 | 5 | 72.0 | 11.1 |
10 | 73.0 | 14.6 | |
15 | 70.0 | 10.0 | |
20 | 65.0 | 5.3 | |
750 | 5 | 76.0 | 13.4 |
10 | 73.0 | 11.4 | |
15 | 66.0 | 7.1 | |
20 | 66.0 | 8.0 |
Одним из существенных факторов влияния на свойства композита можно назвать формирование переходного слоя, в котором макромолекулы полимера частично утрачивают сегментальную подвижность в результате сорбции на поверхности наполнителя, что влечет уменьшение относительного удлинения при разрыве [30]. Именно такая тенденция и прослеживается при анализе данных испытания.
Механические свойства изготовленных композитов были также исследованы при испытании на сжатие (см. табл. 2 и рис. 5).
Из полученных зависимостей модуля упругости при сжатии от степени наполнения видно, что модуль упругости исследуемых композитов вырос на ~25% по сравнению с ненаполненным ПП (320 МПа для ненаполненного ПП и 390 МПа для наполненного ПП). Сравнивая результаты для композитов, наполненных немодифицированными и модифицированными базальтовыми волокнами, можно выделить композит, в котором обработка базальтового волокна проведена при 500°С. Значение модуля упругости при сжатии этого композита при максимальной степени наполнения составила 390 МПа, в то время как для композита с немодифицированными базальтовыми волокнами модуль упругости при сжатии равен 360 МПа. Важно, что при наполнении волокнами ПП матрицы возрастает максимальное напряжение при сжатии (см. табл. 2).
Прочность при изгибе и удельная ударная вязкость представлены в табл. 3 и на рис. 6 и 7. Эти характеристики примерно такие же, как и для исходного вторичного ПП. Зависимости удельной ударной вязкости от степени наполнения показаны на рис. 7. При умеренных значениях температуры обработки волокон удельная ударная вязкость возрастает.
Исследование ПП и композиций методом ТГА (рис. 8) показало, что температура уменьшения массы на 10% на воздухе ($Т_{{\text{д}}}^{{10\% }}$) для ПП и наполненного образца 2 совпадает и равна 310°С. Однако при больших степенях разложения термоокислительная деструкция образца 2 замедляется, и окончание изменения массы этого образца наблюдается при существенно более высоких значениях температуры, чем для исходного ПП. Введение в состав композиции модифицированных базальтовых волокон, прогретых при разной температуре, приводит к существенному возрастанию величины $Т_{{\text{д}}}^{{10\% }}$, которая одинаковая для всех этих составов (табл. 4).
Рис. 8.
Кривые ТГА для исходного вторичного ПП (1) и его композиций (2–5) при скорости нагревания 10 град/мин на воздухе; степень наполнения базальтовых волокон 20%. Композиты с базальтовыми волокнами прогреты при 20 (2), 500 (3), 650 (4) и 750°С (5).
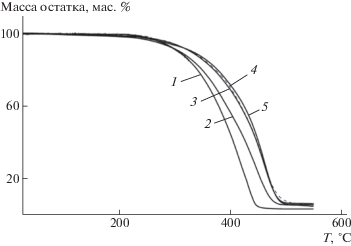
Таблица 4.
Термические характеристики исследованных образцов
Образец, № | Т, °С | ||
---|---|---|---|
уменьшения массы на 10% | плавления | окисления | |
1 | 310 | 166.3 | 219 |
2 | 310 | 166.6 | 215 |
3 | 327 | 167.0 | 218 |
4 | 327 | 167.2 | 224 |
5 | 327 | 167.8 | 224 |
На кривых ДСК, приведенных на рис. 9, присутствует эндотермический пик плавления и начальный участок экзотермического пика окисления, когда за счет присоединения кислорода воздуха происходит образование перекисных соединений, распадающихся при повышении температуры с образованием летучих продуктов. Низкотемпературное окисление полиолефинов известный факт. В данном случае увеличение массы за счет присоединения кислорода не наблюдается, так как окисление начинается в температурной области начала потери массы. Следовательно, конкурируют два процесса – деструкция и окисление.
Рис. 9.
Кривые ДСК для исходного вторичного ПП (1) и его композиций (2–5) при скорости нагревания 10 град/мин на воздухе. Композиты с базальтовыми волокнами прогреты при 20 (2), 500 (3), 650 (4) и 750°С (5).
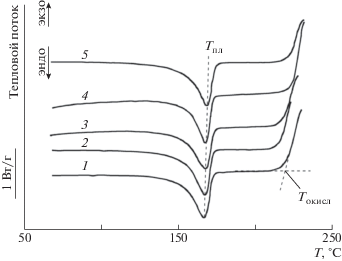
Из данных ДСК (табл. 4) следует, что температура плавления композиций несколько возрастает при внесении в ПП модифицированных базальтовых волокон, что указывает на изменение размеров кристаллитов и участие добавок в формировании кристаллической фазы.
Данная работа выполнена при финансовой поддержке Министерства науки и высшего образования Российской Федерации (проект “Теоретико-экспериментальное конструирование новых композитных материалов для обеспечения безопасности при эксплуатации зданий и сооружений в условиях техногенных и биогенных угроз” № FSWG-2020-0007 и тема госзадания ИНЭОС РАН № 0085-2019-0004).
Список литературы
Subramanian R.V., Tang T.J.Y., Austin H.F. // SAMPE Quarterly. 1977. P. 1.
Artemenko S.E. // Fiber Chem. 2003. V. 35. № 3. P. 226.
Sim J., Park C. // Composites. B. 2005. V. 36. № 6. P. 504.
Van de Velde K., Kiekens P., Van Langenhove L. // Proc. 10th International Conference on Composites/Nano Engineering. New Orleans: University of New Orleans, 2003. P. 20.
Chantladze T. Industrial assimilation of the effective type of fiber with multicomponent charge. http://www.tctv.ne.jp
http://www.basaltex.com
Figovsky O., Beilin D., Blank N., Potapov J., Chernyshev V. // Cement Concr. Comp. 1998. V. 18. № 6. P. 437.
Sergeev V.P., Chuvashov Yu.N., Galushchak O.V., Pervak I.G. // Power Metallurgy and Metal Ceramics. 1994. V. 33. № 9–10. P. 555.
BGF Ltd. Product literature: http://www.bgf.com
Albarrie Ltd. Product literature: http://www.albarrie.com/Filtration/fil-basalt.html
http://www.laseroptronix.com
Fire Resistant Board Material. 2001: Eur. Pat.
Zihlif A.M., Ragosta G. // J. Thermoplast. Comp. Mater. 2003. V. 16. № 3. P. 273.
Аскадский А.А., Пахнева О.В., Попова М.Н. // Пласт. массы. 2007. № 7. С. 47.
Аскадский А.А., Пахнева О.В., Попова М.Н. // Пласт. массы. 2007. № 8. С. 45.
Askadskii A.A., Golovanov A.V., Pahneva O.V., Po-pova M.N. // Polymer Scince A. 2009. V. 51. № 5. P. 576.
Попова М.Н., Аскадский А.А., Голованов А.В. // Пласт. массы. 2009. № 6. С. 40.
Аскадский А.А., Мацеевич Т.А., Попова М.Н. Вторичные полимерные материалы. Механические и барьерные свойства, пластификация, смеси и нанокомпозиты. М.: АСВ, 2017.
Галицейский К.Б., Петунова М.Д., Афанасьев Е.С., Аскадский А.А. // Пласт. массы. 2017. № 7–8. С. 18.
Алесковский В.Б., Галицейский К.Б. Пат. 2287543 Россия. 2006.
Шитов Д.Ю. Дисс. … канд. техн. наук. М.: Российский химико-технологический университет имени Д.И. Менделеева, 2015.
Нгуен Минь Туан, Чалая Н.М., Осипчик В.С. // Пласт. массы. 2018. № 3–4. С. 40.
Алесковский В.Б. Химия надмолекулярных соединений. СПб.: Санкт-Петербургский ун-т, 1996.
Фиалков А.С. Углерод, межслоевые соединения и композиты на его основе. М.: АспектПресс, 1997.
Askadskii A.A. Computational Materials Science of Polymers. Cambridge: Cambridge Int. Sci. Publ., 2003.
Аскадский А.А., Хохлов А.Р. Введение в физикохимию полимеров // М.: Научный мир, 2009.
Аскадский А.А., Кондращенко В.И. Компьютерное материаловедение полимеров. М.: Научный мир, 1999. Т. 1.
Аскадский А.А., Попова М.Н., Кондращенко В.И. Физикохимия полимерных материалов и методы их исследования. М.: АСВ, 2015.
Guro M. Wyller, Thomas J. Preston, Trygve T. // Energy Procedia. 2017. V. 124. P. 3.
Кербер М.Л. Полимерные композиционные материалы. СПб.: Профессия, 2008.
Дополнительные материалы отсутствуют.
Инструменты
Высокомолекулярные соединения (серия А)