Физикохимия поверхности и защита материалов, 2019, T. 55, № 3, стр. 304-313
Пути повышения адгезионной прочности твердых износостойких наноструктурных покрытий в системе Ti–B–(Cr, Si, C)–N
Ф. В. Кирюханцев-Корнеев 1, *, А. Н. Шевейко 1, М. И. Петржик 1
1 Национальный исследовательский технологический университет “МИСиС”,
119049 Москва, Ленинский пр-т, 4, Россия
* E-mail: kiruhancev-korneev@yandex.ru
Поступила в редакцию 20.09.2018
После доработки 24.10.2018
Принята к публикации 15.11.2018
Аннотация
Изучены структура и свойства покрытий Ti–B–N, Ti–Cr–B–N, Ti–Si–B–C–N, полученных методом магнетронного распыления СВС-мишеней. Рассмотрены способы повышения адгезионной прочности покрытий: нанесение подслоев, подача на подложку высокого напряжения смещения в начале осаждения покрытия, предварительное ионное травление подложки, а также имплантация высокоэнергетическими ионами на различных этапах осаждения. Для исследования адгезии покрытий использован метод скратч-тестирования.
ВВЕДЕНИЕ
При повышении эксплуатационных свойств изделий трибологического назначения за счет нанесения твердых износостойких покрытий ключевым фактором является адгезия. Особенно актуальна проблема повышения адгезии при осаждении покрытий методом магнетронного распыления. Существует ряд методов, способствующих увеличению адгезионных свойств тонких покрытий, полученных методом магнетронного распыления. Например, нанесение подслоев между покрытием и подложкой увеличивает адгезионную прочность покрытий [1, 2]. В работе [3] было установлено, что очистка подложки органическим растворителем и термообработка практически не влияют на адгезию покрытий, а плазменная очистка, может увеличить прочность сцепления более чем в 6 раз. Кроме того, увеличение напряжения смещения способно улучшить не только адгезию, но и плотность покрытия, что объясняется непрерывной ионной бомбардировкой как поверхности подложки, так и растущего покрытия [4]. Также известно, что адгезионную прочность покрытия можно улучшить путем регулирования температуры осаждения [5].
В настоящей работе на примере твердых наноструктурных покрытий Ti–B–(Cr, Si, C)–N рассмотрены различные способы повышения адгезионной прочности покрытий: нанесение подслоев Ti/TiN, подача высокого напряжения смещения в начале осаждения, травление подложки ионами Ar+ и имплантация высокоэнергетическими ионами титана.
1. МАТЕРИАЛЫ И МЕТОДЫ
Покрытия были получены методом магнетронного распыления композиционных мишеней TiB2 + TiN, TiB + Ti9Cr4B + Cr2Ti, TiB2 + SiC. Мишени были изготовлены методом самораспространяющегося высокотемпературного синтеза (СВС) с использованием порошков титана (марки ПТС), хрома (марки ПХ-1С), нитрида бора (марки СВС-М), карбида кремния, бора аморфного коричневого. Мишени имели диаметр 125 мм и толщину 8 мм. Для осаждения использовалась модернизированная установка УВН-2М, в вакуумной камере которой находились два планарных магнетрона и источник ионов Ar+ щелевого типа. На одном магнетроне закреплялась титановая мишень, на другом – композиционная СВС-мишень. Через натекатели в камеру подавался аргон или газовая смесь Ar + 14% N2. В качестве подложек использовался монокристаллический кремний КЭФ-4.5 (100), хромистая сталь типа 65Х13 и твердый сплав ТТ8К6. Перед установкой в вакуумную камеру, подложки подвергались ультразвуковой очистке в изопропиловом спирте. На подложки в процессе осаждения подавалось напряжение смещения Uсм = –250 В, температура подложек составляла 200–250°С. Для нанесения покрытий также использовалась комбинированная установка на базе имплантора “Сокол-50/20” позволившая совместить процесс магнетронного распыления с бомбардировкой подложки высокоэнергетическими ионами титана. Принципиальная схема процесса магнетронного распыления и магнетронного распыления с ионной имплантацией показана на рис. 1. Подробная конструкция установки для реализации второго метода представлена также в работе [6]. При осаждении покрытий с помощью магнетронного распыления поддерживалось постоянное давление на уровне 0.2 Па. Во время ионной имплантации и магнетронного распыления при ассистировании имплантором давление составляло 0.07 Па. Структура покрытий была исследована при помощи рентгенофазового анализа (РФА) на приборе Geigerflex Rigaku, просвечивающей электронной микроскопии (ПЭМ) на приборе JEM-200CX Jeol и рентгеновской фотоэлектронной спектроскопии (РФЭС) на приборе PHI 5500 ESCA. Физико-механические свойства покрытий оценивались при наноиндентировании на приборе Nano Hardness Tester (CSM Instruments). Нагрузка на индентор составляла 4 мН. Адгезионные свойства были исследованы с помощью скратч-тестирования на приборе Revetest (CSM Instruments) путем царапания поверхности покрытий алмазным конусом с радиусом закругления 200 мкм при увеличивающейся нагрузке. При адгезионных испытаниях определялась минимальная критическая нагрузка, приводящая к растрескиванию или отслаиванию покрытия. Критическая нагрузка фиксировалась по следующим параметрам: остаточной глубине проникновения индентора (RD), глубине проникновения индентора (PD), акустической эмиссии (AE), коэффициенту трения (FC), силе трения (FF), а также с помощью наблюдения царапины в оптический микроскоп (OM). Трибологические испытания по схеме “стержень-диск” проводились на установке Tribometer (CSM Instruments) при следующих условиях: линейная скорость 10 см/c, нормальная нагрузка 5 Н, контр-тело – 3-мм шарик WC + 6% Co, радиус дорожки 7 мм, 10 000 циклов. Шероховатость и толщина покрытий оценивалась на профилометре Alpha-step 200 (Tencor Instruments).
2. СТРУКТУРА И СВОЙСТВА ПОКРЫТИЙ
Основной структурной составляющей покрытий Ti–B–N и Ti–Cr–B–N по данным РФА и ПЭМ является ГЦК-фаза на базе TiN. Кроме того, с помощью РФЭС в покрытиях Ti–B–N и Ti–Cr–B–N обнаружены аморфные фазы составов TiB2 и CrB2, соответственно. Основу покрытий Ti–B–Si–C–N составляла гексагональная фаза на основе TiB2. Темнопольные изображения и электроннограммы покрытий представлены на рис. 2. Средний размер кристаллитов, оцененный по темнопольным изображениям структуры, составлял соответственно 3, 1 и 5 нм для покрытий Ti–B–N, Ti–Cr–B–N и Ti–Si–B–C–N.
Рис. 2.
Структура покрытий (а) Ti–B–N (распыление в Ar), (б) Ti–Cr–B–N (Ar + 14% N2) и (в) Ti–Si–B–C–N (Ar + 14% N2).
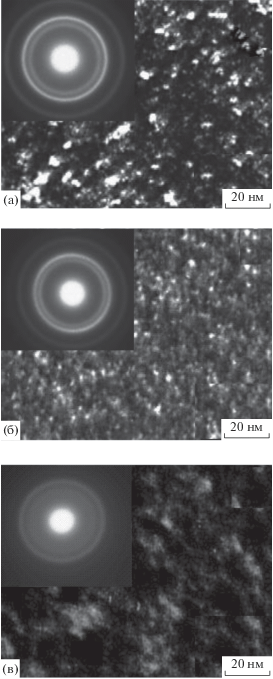
Твердость (Н), модуль упругости (Е) и упругое восстановление рассчитывали по данным наноиндентирования покрытий, нанесенных на твердосплавные подложки. Для покрытий Ti–B–N, Ti–Cr–B–N и Ti–Si–B–C–N были получены значения: Н = 34 ГПа, Е = 380 ГПа, Н = 33 ГПа, Е = 370 ГПа и Н = 29 ГПа, Е = 310 ГПа, соответственно. Покрытия имели достаточно высокую величину упругого восстановления – на уровне 58–60%.
Покрытия Ti–B–N и Ti–Cr–B–N имели коэффициент трения 0.60 и 0.45. Скорость износа для покрытий Ti–B–N составляла 3 × 10–7 мм3 Н–1 м–1, для Ti–Cr–B–N 7 × 10–7 мм3 Н–1 м–1, что в 4–8 раз ниже, чем у покрытий TiNx. Более полные сведения о покрытиях Ti–B–N и Ti–Cr–B–N приведены в работе [7].
3. ПУТИ ПОВЫШЕНИЯ АДГЕЗИОННОЙ ПРОЧНОСТИ ПОКРЫТИЙ
3.1. Использование ионного травления
Перед нанесением покрытий Ti–Cr–B–N для увеличения адгезионной прочности было использовано предварительное травление твердосплавной подложки ионами аргона. Энергия ионов составляла 1.5–2.0 кэВ, плотность тока, регистрируемого на подложке 10 мА/см2. Время осаждения покрытий составляло 60 мин.
Двухмерные изображения поверхностей покрытий после осаждения, а также поверхности подложки после ионного травления, приведены на рис. 3. Видно, что после ионного травления твердосплавная подложка имеет сильно развитый рельеф поверхности. Стрелками показаны вытравленные ионами аргона карбидные зерна WC (~1 мкм) и (Ti, Ta, W)C (2–3 мкм). Покрытия в целом наследуют рельеф подложки, а с увеличением времени ионного травления (τi) пропорционально возрастает шероховатость покрытий. Параметры, характеризующие шероховатость, измеренные на дистанции 5 мкм, приведены в табл. 1.
Рис. 3.
Рельеф поверхности: подложки ТТ8К6 после ионного травления в течение 15 мин (а), покрытий Ti–Cr–B–N без ионного травления (б), после ионного травления 5 мин (в), 15 мин (г).
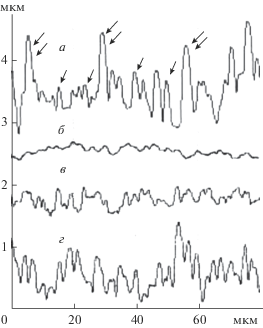
Таблица 1.
Параметры шероховатости и критическая нагрузка для покрытий Ti–Cr–B–N
τi, мин | Ra, нм | Rz, нм | Rmax, нм | LOM, Н | LAE, Н |
---|---|---|---|---|---|
0 | 2.7 | 5.2 | 11.1 | 27 | 21–27 |
5 | 6.6 | 11.3 | 27.6 | <89 | ~70 |
15 | 17.7 | 17.6 | 68.2 | 93–99 | 93 |
При царапании покрытия Ti–Cr–B–N, осажденного без ионного травления, при достижении нагрузки L = 27 Н происходило отслоение покрытия в области царапины (рис. 4). Причем на кривых зависимости контрольных параметров от нагрузки фиксировался перегиб. При использовании предварительного ионного травления значения критической нагрузки увеличивались. Для покрытия, нанесенного после 5 мин ионного травления, растрескивание наблюдалось при L > > 70 Н, а отслоения покрытия не наблюдалось при достижении L = 107 Н. Для покрытия, нанесенного после 15 мин ионного травления, лишь при нагрузке 98 Н фиксировалось появление первой шевронной трещины на дне царапины (рис. 5а). Однако, отслаивания покрытия не происходило и при достижении L = 110 Н (рис. 5б). По изменению акустической эмиссии видно, что растрескивание начинается при L ~ 93 Н (рис. 5в). Плавный ход кривых для остальных параметров свидетельствует об отсутствии отслоений при царапании. Небольшой скачок при ~60 Н можно связать с дефектами твердосплавной подложки.
Рис. 4.
Изображение царапины (а) и диаграмма скратч-тестирования (б) покрытия Ti–Cr–B–N, осажденного без предварительного ионного травления подложки.
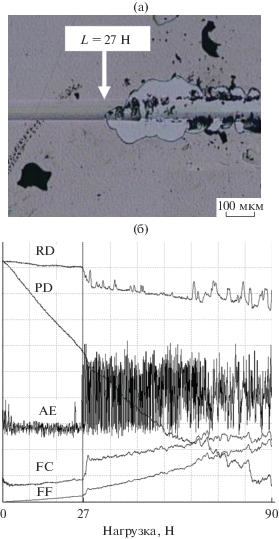
Рис. 5.
Изображения царапины (а, б) и диаграмма скратч-тестирования (в) покрытия Ti–Cr–B–N, осажденного после предварительного ионного травления подложки в течение 15 мин.
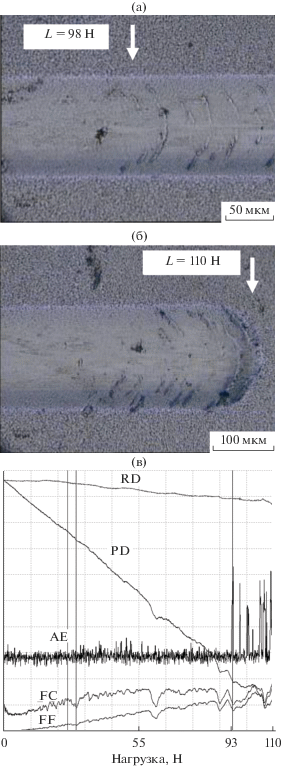
Анализ результатов свидетельствует о четкой корреляции между временем ионного травления, величиной шероховатости и величиной критической нагрузки начала разрушения. Таким образом, для достижения максимальной адгезионной прочности следует перед нанесением покрытия обеспечить хорошо развитый рельеф поверхности подложки путем вытравливания ионным пучком отдельных ее структурных составляющих. Однако надо заметить, что сильно развитый рельеф покрытия не благоприятен с позиции трибологии. Отдельные выступы на поверхности могут служить очагами разрушения или скалывания покрытия на этапе приработки трущихся поверхностей из-за концентрации напряжений на локальных участках.
3.2. Нанесение подслоев Ti/TiN и подача высокого напряжения смещения
Метод нанесения подслоев получил, достаточно широкое распространение в практике осаждения вакуумных покрытий [8–11]. Применение подслоев подразумевает минимизацию напряжений на границе раздела подложка-покрытие. Как правило, при осаждении покрытий на основе тугоплавких соединений титана используются подслои Ti [3], TiN [9] или их комбинация [10]. Толщины подслоев Ti/TiN как правило составляют ~100–500 нм [9, 10], однако эффект повышения адгезионной прочности обнаружен и для сравнительно тонких подслоев ~50 нм [11]. Для увеличения адгезии иногда используется подача на подложку высокого напряжения смещения в первые минуты осаждения [11, 12]. За счет обратного распыления материала подложки и последующего соосаждения такое технологическое решение позволяет получать градиентные переходные слои, содержащие элементы подложки и покрытия.
В данной работе на примере покрытия Ti–B–Si–C–N рассмотрена возможность повышения адгезии за счет нанесения подслоев Ti/TiN и подачи высокого напряжения смещения в начальный момент осаждения покрытия. Перед циклом напыления проводилась очистка твердосплавных подложек с помощью ионного источника в течение 15 мин. Нанесение подслоев осуществлялось путем распыления титановой мишени либо в Ar, либо последовательно в Ar и смеси Ar + 14% N2. В начальный момент осаждения на подложку подавалось напряжение смещения –500 В. Различные варианты переходных слоев описаны в табл. 2. Время осаждения покрытий Ti–B–Si–C–N составляло 60 мин.
Таблица 2.
Характеристики подслоев и критическая нагрузка для покрытий Ti–B–Si–C–N
Характеристики переходных слоев | LОМ, Н | |||
---|---|---|---|---|
расчетная толщина подслоя, нм | время подачи Uсм при осаждении, с | |||
Ti | TiN | –250 В | –500 В | |
– | – | – | – | 7.5 |
20 | 5 | – | – | 13.1 |
40 | 5 | – | – | 7.4 |
40 | 5 | – | 0–80 | 11.3 |
200 | – | 0–120 | 120–180 | 6.0 |
100 | 100 | 0–300 | 300–360 | 9.2 |
Значения критической нагрузки, приводящей к появлению первого дефекта при царапании, по данным оптической микроскопии (LОМ) приведены в табл. 2. При царапании покрытия, осажденного без подслоев, при L ~ 7.5 Н наблюдался перегиб кривой AE, связанный, по-видимому, с началом истирания покрытия внутри дорожки (показано пунктирной стрелкой на рис. 6а). Об отсутствии отслоений свидетельствует пологий ход кривой остаточной глубины (RD). При достижении L = 29 Н возникает первое отслоение, сопровождающееся одиночным всплеском на кривой акустической эмиссии (AE). При L = 34 Н происходит полное истирание покрытия – на всех кривых скратч-тестирования наблюдается перегиб (см. также рис. 6б). На кривой остаточной глубины RD при нагрузке 35 Н наблюдается ступенька, по высоте совпадающая с толщиной покрытия. Осаждение подслоев Ti (20 нм) и TiN (5 нм) без подачи высокого напряжения смещения (см. табл. 2) позволило повысить значение критической нагрузки почти в два раза. Согласно данным оптической микроскопии и диаграммам скратч-тестирования отслоение покрытия начиналось при L = 13–15 Н (рис. 7). Причем истирания покрытия, как в случае без подслоев, не наблюдалось. Увеличение критической нагрузки наблюдалось также при осаждении подслоев Ti (40 нм) и TiN (5 нм) с кратковременной (80 с) подачей на подложку высокого напряжения смещения (табл. 2). Стоит отметить, однако, что, для всех покрытий, нанесенных с промежуточными слоями, отслоение начиналось при L ≤ 15 Н, в то время, как для покрытия без подслоев – при L ~ ~ 30 Н. Таким образом, собственно адгезионная прочность покрытий Ti–Si–B–C–N при нанесении подслоев понижалась.
Рис. 6.
Изображения царапины (а, б) и диаграмма скратч-тестирования (в) покрытия T–Si–B–C–N, осажденного без подслоев.
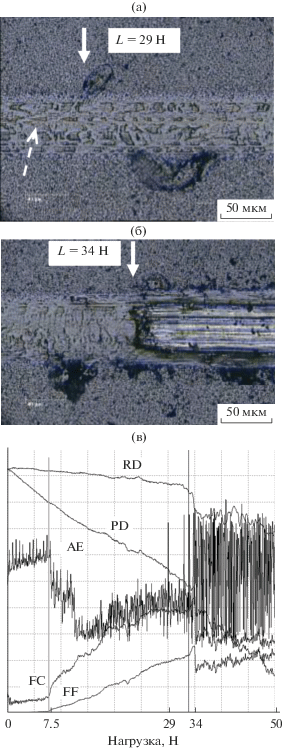
Рис. 7.
Изображение царапины (а) и диаграмма скратч-тестирования (в) покрытия T–Si–B–C–N, осажденного с использованием тонких подслоев Ti/TiN без подачи высокого напряжения смещения.
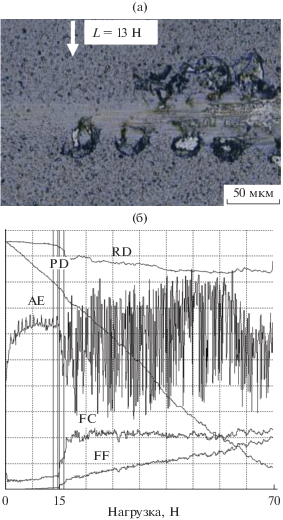
Отсутствие положительного эффекта при нанесении подслоев может быть связано с различием в типах кристаллических решеток: основной структурной составляющей покрытий Ti–B–Si–C–N является гексагональная фаза TiB2, в то время, как нитрид титана, нанесенный в качестве подслоя, имеет кубическую решетку. Также возможно, что из-за подачи высокого напряжения смещения в слоях покрытия, прилежащих к подложке, существенно возрастает уровень внутренних напряжений, что отрицательно отражается на адгезии покрытий. Понижение адгезионной прочности покрытий при увеличении Uсм по абсолютной величине отмечалось в работах [13, 14].
Таким образом в данной работе положение о целесообразности нанесения дополнительных слоев Ti/TiN для повышения адгезии титансодержащих многокомпонентных покрытий не нашло подтверждения.
3.3. Ионная имплантация
Влияние ионной имплантации на адгезионные свойства покрытий было исследовано на примере системы Ti–B–N. Перед нанесением покрытий было использовано предварительное травление подложки (ТТ8К6) ионами аргона в течение 3 мин. Имплантация высокоэнергетическими ионами титана осуществлялась на различных технологических этапах (рис. 8). Ускоряющее напряжение составляло 30 кВ. Плотность потока 1 × 1014 ионов/(cм2 с). Средний заряд ионов равнялся двум, однако, в ионном пучке присутствовали также ионы Ti+ и Ti3+. В табл. 3 приведены значения нагрузок, при которых наблюдается появление первого дефекта.
При проведении адгезионных испытаний было установлено, что покрытие 1, осажденное без использования ионной имплантации, начинает разрушаться при L = 35 Н. Из рис. 9а видно, что при этой нагрузке на поверхности покрытия фиксируются первые отслоения. При увеличении нагрузки помимо отслоений отмечается появление узких шевронных трещин. Далее идет чередование областей отслоений и областей с растрескиванием. Возникновение каждого отслоения сопровождается провалом на кривой RD. Такая картина наблюдается до полного разрушения покрытия. Судя по кривым на диаграмме скратч-тестирования (рис. 9б), а также по изображениям, полученным на оптическом микроскопе, этот момент наступает при достижении L = 73–76 Н. В группе покрытий, осажденных с применением ионной имплантации, наилучшие результаты показал образец 2. При скратч-тестировании первая шевронная трещина появляется при L = 48 Н, первое отслоение – при L = 51 Н (рис. 10). Затем, как и в случае образца 1, идет чередование областей отслоений и областей растрескивания. Однако разрушения до подложки не происходит даже после достижения нагрузки 110 Н (рис. 10б). Остальные покрытия, осажденные с использованием ионной имплантации, разрушались приблизительно при той же нагрузке, что и контрольный образец 1. Достижение подложки фиксировалось во всех случаях, за исключением покрытия 2, при L ≤ 75 Н. Надо отметить, что покрытия 1–4 имели толщину 2.5–2.8 мкм, в то время, как толщина покрытия 5 составляла 1.4–1.5 мкм. Этим различием можно объяснить некоторое повышение критической нагрузки разрушения для образца 5. Ниже будет детально рассмотрено влияние толщины на поведение покрытий при царапании.
4. ВЛИЯНИЕ ТОЛЩИНЫ ПОКРЫТИЙ НА РЕЗУЛЬТАТЫ СКРАТЧ-ТЕСТИРОВАНИЯ
Разброс в значениях критической нагрузки: для покрытий Ti–Cr–B–N L ~ 70–100 Н, для покрытий Ti–Si–B–C–N L ~ 5–15 Н, для Ti–B–N L ~ ~ 30–50 Н (при использовании предварительного ионного травления) может быть обусловлен различным уровнем внутренних напряжений в покрытиях, который в свою очередь определяется составом и структурой покрытий. Разброс можно также связать и с различной толщиной покрытий, поскольку скорости распыления использованных СВС-мишеней различны. Для проверки влияния толщины покрытий (h) на результаты скратч-тестирования были исследованы покрытия Ti–B–N и Ti–Cr–B–N, нанесенные в течение разного времени (τ) при прочих одинаковых условиях. Для покрытий Ti–Cr–B–N использовалось травление ионами аргона в течение 5 мин, для покрытий Ti–B–N использовалось ионное травление в течение 3 мин и имплантация ионами титана в первые 10 мин осаждения.
Результаты представлены в табл. 4. Видно, что для каждого из покрытий величина критической нагрузки разрушения понижается с увеличением толщины. Кроме того, было отмечено, что и характер разрушения также зависит от толщины покрытия. Разрушение покрытия 1 начинается с появления небольших осыпаний или скрашиваний покрытия, расположенных по краям царапины (рис. 11а). Затем при увеличении L на дне царапины появляются шевронные трещины и следы истирания покрытия. В случае покрытия 2 при достижении критической нагрузки 50 Н появляется сетка мелких трещин (рис. 11б), локализованных по краям царапины и не распространяющихся на всю ширину царапины при увеличении нагрузки. При повышении нагрузки отдельные мелкие трещины сливаются и покрытие между ними, отделяется от подложки, образуя отслоение. При L = 62–64 Н наблюдаются отслоения, перерезающие царапину, одновременно фиксируется касание индентором подложки. Для покрытия 3 вслед за небольшими дефектами внутри царапины следует отслоение покрытия с оголением подложки (рис. 11в).
Таблица 4.
Критическая нагрузка для покрытий Ti–B–N и Ti–Cr–B–N различной толщины
Покрытие | № | τ, мин | h, мкм | LOM, Н |
---|---|---|---|---|
Ti–B–N | 1 | 20 | ~0.7 | ~65 |
2 | 40 | ~1.8 | ~50 | |
3 | 60 | ~2.5 | ~38 | |
Ti–Cr–B–N | 4 | 30 | – | >90 |
5 | 60 | ~1.0 | ~70 | |
6 | 120 | – | ~40 |
В случае покрытий Ti–Cr–B–N также обнаружено изменение характера разрушения при увеличении толщины. При царапании наиболее тонкого покрытия (4), четких моментов, характеризующих начало разрушения, не зафиксировано. Однако обнаружено появление сетки мелких дефектов, расположенных поперек царапины, которые с трудом различимы в микроскоп и практически не отслеживаются по акустической эмиссии и остальным контрольным параметрам (рис. 12). Для покрытия Ti–Cr–B–N (6) разрушение начинается с появления мелких трещин, локализованных по краям царапины, которые при увеличении нагрузки сливаются и образуют отслоение, как и в случае покрытия 2. Таким образом, повышение толщины покрытий приводит к снижению критических нагрузок, определяемых методом скратч-тестирования.
ВЫВОДЫ
Методом магнетронного распыления композиционных СВС-мишеней получены покрытия Ti–B–N, Ti–Cr–B–N и Ti–Si–B–C–N. Исследована структура, физико-механические и трибологические свойства покрытий. Рассмотрены различные технологические пути повышения адгезионной прочности покрытий. Показано, что наиболее универсальными способами повышения адгезионной прочности покрытий являются предварительное травление подложки ионами аргона и имплантация подложки высокоэнергетическими ионами титана. Изучено влияние толщины покрытий на поведение покрытий при скратч-тестировании.
Работа выполнена при финансовой поддержке Министерства образования и науки России (Госзадание № 11.7172.2017/8.9).
Список литературы
Lei Li, Langping Wang, Likai Zhao, Xiaofeng Wang. Microstructure and adhesion strength of NiAl coating prepared on Q235 substrate by combustion synthesis assisted with Cu–Zn interlayer // Surface and Coatings Technology. 2018. V. 344. P. 564–571.
Hoe-Kun Kim, Joung-Hyun La, Kyu-Sung Kim, Sang-Yul Lee. The effects of the H/E ratio of various Cr–N interlayers on the adhesion strength of CrZrN coatings on tungsten carbide substrates // Surface and Coatings Technology. 2015. V. 284. P. 230–234.
Ju Dy Lim, Pui Mun Lee, Daniel Min Woo Rhee, Kam Chew Leong, Zhong Chen. Effect of surface treatment on adhesion strength between magnetron sputtered copper thin films and alumina substrate // Applied Surface Science. 2015. V. 355. P. 509–515.
Kulwant Singh, Krishnamurthy N., Suri A.K. Adhesion and wear studies of magnetron sputtered NbN films // Tribology International. 2012. V. 50. P. 16–25.
Joung Hyun La, Myeon Gyu Song, Hoe Kun Kim, Sang Yul Lee, Woo Sung Jung. Effect of deposition temperature on microstructure, corrosion behavior and adhesion strength of Zn–Mg coatings on mild steel // J. Alloys and Compounds. 2018. V. 739. P. 1097–1103.
Shtansky D.V., Sheveyko A.N., Sorokin D.I., Lev L.C., Mavrin B.N., Kiryukhantsev-Korneev Ph.V. Structure and properties of multi-component and multilayer TiCrBN/WSex coatings deposited by sputtering of TiCrB and WSe2 targets, Surface and Coatings Technology. 2008. V. 202. P. 5953–5961.
Штанский Д.В., Кирюханцев-Корнеев Ф.В., Шевейко А.Н., Башкова И.А., Малочкин О.В., Левашов Е.А., Дъяконова Н.Б., Лясоцкий И.В. Структура и свойства покрытий Ti–B–N, Ti–Cr–B–(N) и Cr–B–(N), полученных магнетронным распылением CВC-мишеней // Физика твердого тела. 2005. Т. 47. № 2. С. 242–251.
Hu X., Han Z., Li G., Gu M. Microstructure and properties of Ti–Si–N nanocomposite films // J. Vac. Sci. Technol. A. 2002. V. 20(6). P. 1921–1926.
Chen Y.-H., Gurus M., Chung Y.-W., Keer L.M. Thermal stability of hard TiN/SiNx multilayer coatings with an equiaxed microstructure // Surface and Coating Technology. 2002. V. 154. P. 162–166.
Baker M.A., Klose S., Rebholz C., Leyland A., Matthews A. Evaluated the microstructure and performance of nanocomposite PVD TiAlBN coatings // Surface and Coating Technology. 2002. V. 151–152. P. 338–343.
Zhong D., Sutter E., Moore J.J., Mustoe G.G.W., Levashov E.A., Disam J. Mechanical properties of Ti–B–C–N coatings deposited by magnetron sputtering // Thin Solid Films. 2001. V. 398–399. P. 320–325.
Штанский Д.В., Левашов Е.А., Шевейко А.Н., Мур Дж.Дж. Оптимизация параметров вакуумного реакционного осаждения сверхтвердых Ti–Si–B–N-покрытий // Известия вузов. Цветная металлургия. 1991. № 1. С. 67–72.
Rickerby D.S., Bull S.J. Engineering with surface coatings: the role of coating microstructure // Surface and Coating Technology. 1989. V. 39–40. P. 315–328.
Carrasco C.A., Vergara V.S., Benavente R.G., Mingolo N., Rios J.C. The relationship between residual stress and process parameters in TiN coatings on cooper alloy substrates // Materials Characterization. 2002. V. 48. P. 81–88.
Дополнительные материалы отсутствуют.
Инструменты
Физикохимия поверхности и защита материалов