Физикохимия поверхности и защита материалов, 2020, T. 56, № 2, стр. 165-180
Импульсное магнетронное распыление (Pulsed Magnetron Sputtering) керамических СВС-мишеней как перспективная технология получения многофункциональных покрытий
Ф. В. Кирюханцев-Корнеев *
Национальный исследовательский технологический университет “МИСиС”
Москва, Ленинский пр-т, 4, Россия
* E-mail: kiruhancev-korneev@yandex.ru
Поступила в редакцию 11.07.2019
После доработки 18.07.2019
Принята к публикации 25.07.2019
Аннотация
Проведено исследование процессов импульсного магнетронного распыления (PMS-pulsed magnetron sputtering) многокомпонентных керамических мишеней при нанесении функциональных покрытий различного назначения. Установлены закономерности изменения структурных характеристик, механических и трибологических свойств при увеличении частоты электропитания магнетрона. Обобщая результаты, полученные с использованием технологии PMS при нанесении покрытий из многокомпонентных СВС-катодов, можно сделать следующие выводы: а) Структура покрытий. Импульсное распыление приводит к созданию более плотной и в то же время более дефектной структуры с высоким уровнем внутренних напряжений и шероховатости. Влияние импульсного режима на размер зерен зависит от типа распыления и конфигурации магнитных полей. Для реакционного распыления в ряде случаев выражено измельчение структуры. Обнаружен эффект увеличения толщины реакционных покрытий вследствие активации взаимодействия атомов, распыленных из мишени с атомами азота при осаждении и минимизации отравления поверхности мишени. б) Свойства покрытий. Влияние импульсного режима на адгеизионную прочность покрытий сводится к ее снижению. Зависимости твердости и других механических свойств от частоты импульсного питания носят экстремальный характер с максимумом при 50 кГц. Использование небольших частот (50–150 кГц) приводит к снижению коэффициента трения. При переходе к импульсному режиму наблюдается стабилизация коэффициента трения в процессе испытания, а также, в большинстве случаев – повышается износостойкость.
ВВЕДЕНИЕ
Технология катодного распыления материалов в вакууме на сегодняшний день является передовой в области инженерии поверхности [1]. Изобретение сбалансированного магнетрона (MS – magnetron sputtering) в начале 70-х годов [2, 3] стало серьезным шагом на пути преодоления ограничений по скорости осаждения покрытий. Разработка несбалансированного магнетрона в конце 80-х годов [4] и объединение их в системы с замкнутыми магнитными полями (CFUBMS – close field unbalanced magnetron sputtering) в начале 90-х годов [5] стали решающими событиями для массового использования магнетронного распыления. Новый этап в развитии технологии магнетронного напыления начался с применением импульсного магнетронного распыления (PMS-pulsed magnetron sputtering) в среднечастотном диапазоне (10–350 кГц). Технология позволила добиться стабилизации процесса реакционного распыления и подавления дуговых пробоев на катоде [6], возникающих вследствие образования на поверхности мишени диэлектрических слоев при взаимодействии материала с атомами реакционного газа [7]. Заряд на диэлектрике снимается во время периодической паузы распыления или периодической подачи на мишень кратковременных положительных импульсов [8, 9]. Различают три стадии развития разряда в импульсе: восстановление плазмы, стационарная плазма и рассеивание плазмы [10–12]. Экспериментально установлено, что при импульсном распылении с увеличением частоты импульсов скорость распыления снижается [13, 14], поэтому для получения максимальных скоростей распыления необходимо использовать минимальную частоту импульсов, достаточную для подавления пробоев. Обычно наблюдается прямая пропорциональность между скоростью нанесения и коэффициентом нагрузки [9, 15], однако при биполярных импульсах существует обратная тенденция [16].
Обработка литературных данных показала, что число публикаций, посвященных импульсному магнетронному распылению, непрерывно возрастает. На рис. 1 показан график зависимости количества англоязычных публикаций по годам журналов издательства Elsevier (www.sciencedirect.com) по тематике PMS.
Рис. 1.
Количество англоязычных публикаций издательства Elsevier по годам, затрагивающих импульсное магнетронное распыление (“pulsed magnetron sputtering”).
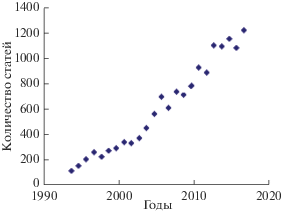
Исследования взаимосвязи между параметрами PMS, структурой и свойствами получаемых покрытий пока ограничено известными составами. В работах [17–19] для TiN было установлено изменение текстуры ГЦК фазы с (111) для DC на (200) при PMS. Переход к импульсному режиму вызывал повышение сжимающих напряжений и уменьшение размера зерна в TiN [18]. Твердость снижалась с 30 до 17 ГПа [17] или не изменялась [19]. Адгезионная прочность увеличилась с 24 до 65 Н, а коэффициент трения снижался с 0.39 до 0.09 [19]. Покрытия TiO2 [19, 20], полученные при импульсном распылении, обладают более плотной структурой с менее выраженным колонным ростом и более гладкой поверхностью, большей твердостью, адгезией, сопротивлением износу и коэффициентом преломления по сравнению с покрытиями, осажденными на постоянном токе [19]. Может быть обеспечен разный уровень кристалличности пленок TiO2 [21]. Вид распыляющих импульсов и коэффициента нагрузки влиял на структуру, которая менялась от анатаза до рутила [22]. Вид импульса (униполярный или биполярный) при PMS оказывает влияние на кристалличность при получении пленок Al2O3 [22]. В работе [23] на примере пленок TiN, CrN, TiAlN было установлено, что при импульсном распылении ток разряда и ионный ток на подложку выше, а напряжение разряда ниже, чем при распылении на постоянном токе. Переход к PMS вызывал снижение пористости и шероховатости. Подробные исследования пленок CrN, полученных при импульсном распылении, проводили в работах [24, 25]. В [25] покрытия CrNx,осажденные в импульсном режиме, имели ниже скорость роста (т.к. время эффективного распыления меньше), содержали меньшее количество азота, но больше аргона, чем покрытия, полученные на постоянном токе при тех же условиях. PMS покрытия CrN имели вдвое меньший размер зерна и более высокие механические и трибологические свойства. В покрытиях TiAlN метод PMS позволяет преодолеть проблемы, связанные с распылением поверхностной диэлектрической пленки AlN [26–28], а также с образованием гексагональной фазы в покрытиях [29]. В работе по Ti–Si–N [30] с увеличением частоты морфология покрытий изменялась от колончатой, до более плотной структуры, происходило измельчение зерна, росли напряжения, покрытия содержали меньше кремния, титана и кислорода.
В работах [31–33] покрытия Cr–B, меняли структуру с колонной на равноосную, плотную без каких-либо заметных дефектов. Шероховатость покрытий в режиме PMS была 10 нм, что существенно ниже, чем для DC покрытий (900 нм). Установлено, что покрытия, полученные в импульсном режиме, обладали меньшим коэффициентом трения на уровне 0.42 против 0.55 при DC из-за гладкой поверхности и более плотной структуры.
Обобщая вышеизложенное можно сделать вывод о перспективности использования технологии PMS в замен методам, использующим постоянный ток (DC). Важно отметить, что импульсные методы в настоящее время используются в основном для осаждения простых покрытий таких, как TiN, TiO2, CrN. По многокомпонентным системам, TiAlN [28], TiSiN [30], TiSiB [34] существуют ограниченные данные Недостаточно внимания уделено многокомпонентным составам.
Данная работа посвящена исследованию многокомпонентных покрытий, осажденных методом PMS при использовании керамических катодов, полученных методом самораспространяющегося высокотемпературного синтеза. В качестве объектов исследования были отобраны покрытия различного функционального назначения: жаростойкие (Cr–Al–Si–B–N [35, 36]), износостойкие (Ti–B–N [37, 38]), коррозионностойкие (Ti–Al–Si–C–N [39, 40]), биоактивные (Ti–Ca–C–O–P–N [41]), оптические (Zr–B–N [42–44]).
МЕТОДИКА ЭКСПЕРИМЕНТА
Мишени были получены из экзотермических смесей порошков с помощью самораспространяющегося высокотемпературного синтеза (СВС). Были использованы следующие смеси порошков, вес. %: 80.1Ti + 9.9C + 10.0Ca3(PO4)2 (мишень TiCaCOP), 63.9Ti + 17.3Al + 4.5C + + 14.3Si3N4 (мишень TiAlSiCN), 66.6Cr + 8.0Al + + 8.0Si + 17.4B (мишень CrAlSiB), 72.0Ti + 28.0B (мишень TiB2), 86.0Ti + 14.0B (мишень TiB), 80.8Zr + 19.2B (мишень ZrB2). Смешивание проводилось в шаровой мельнице ВМФ-4 c твердосплавными шарами диаметром 10 мм в течение 6 ч. Для силового СВС-компактирования был использован пресс ДА-1532Б с максимальным усилием прессования 160 тонн. Прикладываемое после охлаждения до 800°С давление составляло 20 МПа. Для изотермической выдержки мишеней после прессования использовались муфельные печи типа SNOL 7.2/1200 (Umega, Литва). Пористость полученных мишеней не превышала 5%. Заготовки после синтеза подвергались шлифовке на плоскошлифовальном станке 3Д711ВФ11-28. Шлифовка проводилась с двух сторон в присутствие специальных солевых водных растворов, препятствующих локальному перегреву и схватыванию. Для вырезки из СВС-мишеней катодов заданной геометрии использовался электроэрозионный станок APTA 200-2. Из заготовок были вырезаны дисковые катоды диаметром 120–125 мм и толщиной 5–10 мм.
Для осаждения нанокомпозиционных покрытий была использована установка для магнетронного распыления на базе вакуумной системы УВМ-2M с двумя магнетронами ВИ-2 и ионным источником щелевого типа для очистки подложек, оснащенная системой трансформаторов и выпрямительных мостов, а также импульсным двухканальным блоком питания Pinnacle+ (Advanced Energy, USA), позволяющим проводить напыления при токах до 15 А, частоте до 350 кГц, общей мощности до 5 кВт, коэффициенте нагрузки (duty cycle) до 45% при этом длительнрость обратного импулсьа можно варьировать от 0.4 до 5 мкс. В системе управления предусмотрена также функция дугогашения, позволяющая улучшить качество распыления, особенно в случае мишеней с недостаточной электропроводностью. Для ряда сравнительных экспериментов применялись установки несбалансированного магнетронного напыления: Teer UDP-850 (Великобритания) с замкнутыми магнитными полями типа CFUMBS и Unicoat-600 Элан Практик (РФ) с дуальной схемой. При нанесениях покрытий применялись Ar и газовая смесь Ar–15N2.
Подготовительные операции включали в себя обработку подложек и мишеней. В качестве подложек использовались следующие материалы: кремний марок КЭФ-4,5 (100) и КДБ (111), никель Н-2, твердые сплавы ТТ8К6 и ВК6М, никелевый жаропрочный сплав ХН65ВМТЮ, оксид алюминия марки ВОК-130. Очистка подложек проводилась в изопропиловом спирте с использованием ультразвуковой установки УЗДН-2Т. В вакууме для удаления адсорбированных примесей и оксидных слоев осуществлялся нагрев подложек до температуры 300–400°С с одновременной очисткой ионным источником (U = 3 кВ, I = 60 мА) при давлении 0.1 Па в течение 10 мин. Нанесение покрытий происходило при варьировании частота электропитания (f).
В процессе нанесения покрытий были проведены исследования механизмов и характера распыления многокомпонентных СВС-мишеней. Для изучения влияния способа подачи реакционного газа на конечный состав покрытий была выбрана сложная система покрытий Ti–Al–Si–C–N, имеющая в своем составе, связанный в нитридах, азот. Электрические характеристики магнетрона были исследованы с использованием осциллографа Ф4372. Производилась запись тока и напряжения при подключении импульсного блока через дополнительное сопротивление на магнетрон. Характеристики снимались через клеммы, подключенные к резистору цепи. Время деления составляло 1 мкс, напряжение деления 0.05 × 103 В. Ток поддерживался на уровне 1 А.
С целью установления влияния импульсного питания на процесс распыления производилась запись оптических эмиссионных спектров в процессе горения плазмы с использованием оптического эмиссионного спектрометра тлеющего разряда Plasmascope (Horiba JY, France), оснащенного световодом для ввода в вакуумную камеру. Измерения были выполнены при распылении мишени TiAlSiCN в аргоне при давлении 0.2 Па, без подачи на подложку отрицательного напряжения смещения. Были выполнены эксперименты при варьировании частоты электропитания, длительности обратного импульса и тока.
Изображения поперечных изломов покрытий были получены с помощью сканирующей электронной микроскопии на приборах S-4800 (HITACHI, Япония) и JSM-6700F (Jeol, Япония) при ускоряющем напряжении 10–20 кВ. Образцы покрытий исследовалась на просвечивающем электронном микроскопе JEM-200СХ при ускоряющем напряжении U = 200 кВ, а также на JEM-2100 (Jeol). Рентгенофазовый анализ покрытий выполнялся на дифрактометрах Geigerflex и Bruker с использованием CoKα-излучения, в ряде случаев использовалось более мягкое CuKα-излучение.
Для определения твердости (Н), модуля упругости (Е) и упругого восстановления (W) покрытий применялся метод наноиндентирования. Метод заключается во вдавливании индентора известной геометрии в образец при непрерывной фиксации зависимости нагрузки на индентор от глубины его проникновения. Расчет получаемых при наноиндентировании кривых проводился по методу Оливера–Фарра. В работе использовался нанотвердомер Nano-Hardness Tester (CSM Instruments, Швейцария), оснащенный индентором Берковича, нагрузка составляла 4 мН.
Для оценки влияния импульсного электропитания на шероховатость покрытий были проведены исследования на оптическом профилометре “WYKO NT 1100” (Veeco, США) Прибор использовался также для измерения профиля канавок после трибологических испытаний. Для испытаний покрытий с целью определения адгезионной прочности использовался скрач-тестер (Revetest, CSM Instruments. Швейцария). На приборе проводили царапание поверхности покрытия алмазным индентором типа Роквелла при непрерывно нарастающей нагрузке. Момент адгезионного разрушения покрытий фиксировался после испытаний визуально с помощью оптического микроскопа, оборудованного цифровой камерой, а также по изменению параметров: акустической эмиссии, силы трения, коэффициента трения, глубины проникновения индентора и остаточной глубины царапины. В результате испытаний определялась минимальная критическая нагрузка (Lc), которая приводила к отслаиванию покрытия.
Испытания на износостойкость покрытий проводилось на машине трения Tribometer (CSM Instruments, Швейцария). Использовалась схема “стержень – диск”, в качестве контртела использовался шарик из твердого сплава WC-6% Co с диаметром 3 мм, нагрузка составляла P = 5 Н, а линейная скорость 10 cм/с.
РЕЗУЛЬТАТЫ И ИХ ОБСУЖДЕНИЕ
Данные, полученные с использованием осциллографа, показаны на рис. 2–4. Из рисунков хорошо прослеживается отличие по частоте и длительности обратного импульса. Результаты исследования показали, что используемый блок электропитания позволяет генерировать стабильные по току, напряжению и времени импульсы в широких интервалах, характеристики на нагрузке хорошо коррелируют с паспортными данными устройства.
Рис. 2.
Осциллограммы тока при частоте 5 (для наглядности использовалось увеличенное время деления) (а) и 300 кГц (б) и длительности обратного импульса 1 мкс.
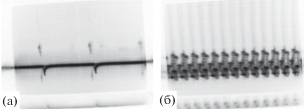
Рис. 3.
Осциллограммы тока при частоте 50 кГц и длительности обратного импульса 1 мкс (а), 3 мкс (б), 5 мкс (в).
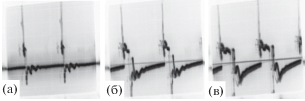
Рис. 4.
Осциллограммы напряжения при частоте 30 кГц, токе 1 А и длительности обратного импульса 5 мкс (а) и 0.5 мкс (б).
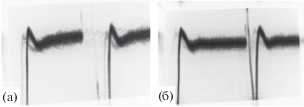
Результаты спектроскопических исследований магнетронной плазмы приведены на рис. 5–7. Спектры, снятые при токе 2 А и частоте 50 кГц по внешнему виду не отличались от спектров, полученных при постоянном токе. В то же время при повышении частоты до 300 кГц, наблюдалось заметное снижение интенсивности линий спектра (рис. 5). Данный эффект обнаружен и на токе 1 А (рис. 6). Причем понижение тока закономерным образом уменьшало интенсивность линий спектра. Установлено, что время обратного импульса (апробировано 1 и 5 мкс) влияет аналогично частоте, приводя к понижению свечения плазмы (рис. 7). Кроме того, серия повторных съемок показала высокую воспроизводимость результатов.
Рис. 5.
Спектры плазмы при токе 2 А, времени обратного импульса 1 мкс, частоте 0 и 50 кГц (а), 300 кГц (б).
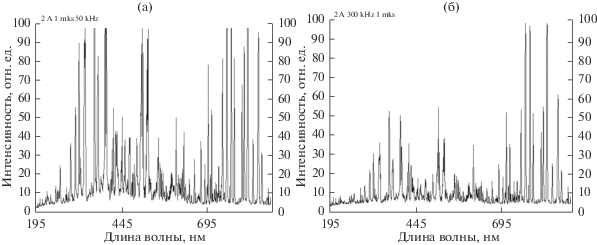
Рис. 6.
Спектры плазмы при токе 1 А, времени обратного импульса 1 мкс, частоте 0 кГц (а) и 300 кГц (б).
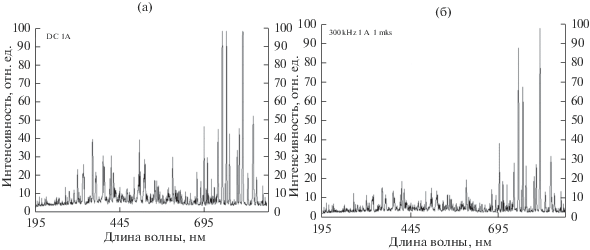
Рис. 7.
Спектры плазмы при токе 1 А, частоте 50 кГц и времени обратного импульса 1 мкс (а) и 5 мкс (б).
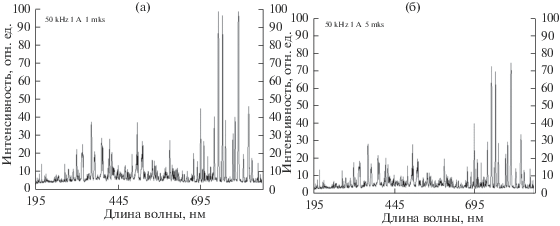
На основании полученных обзорных спектров были найдены интенсивности для каждого элемента при токе магнетрона 1 А и длительности обратного импульса 1 мкс. Были выбраны линии: Al 396 нм, Si 288 нм, Ti 365 нм, C 283 нм, N 420 нм, Ar 697 нм. Линии выбирались из расчета минимизации перекрывания и наложения близко расположенных линий. Результаты анализа показаны на рис. 8.
Рис. 8.
Интенсивности линий элементов в зависимости от частоты электропитания: исходная (а) и в пересчете на 100% (б) (распыление мишени TiAlSiCN).
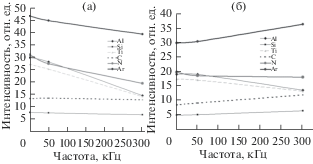
При увеличении частоты электропитания наблюдается уменьшение интенсивностей линий для всех выбранных элементов. Пересчет на 100% показал, что характер изменения интенсивностей неодинаков для различных элементов. Для алюминия, титана и азота наблюдается уменьшение интенсивности с увеличением частоты электропитания, для остальных элементов – увеличение. Различие вероятно связано с различием в электропроводности фазовых составляющих мишени. Кроме того, несомненное влияние на поведение элементов в области плазмы оказывает вес атомов элементов. Действительно, соотношение металлических элементов к неметаллическим уменьшается с 0.58 до 0.37 при возрастании частоты с 0 до 300 кГц.
Результаты микроскопических исследований изломов показали, что структура покрытий сильно зависит от типа конфигурации магнитных полей, а также удельной электрической мощности, подаваемой на керамическую мишень. Анализ морфологии покрытий, полученных с использованием сбалансированных магнетронов в системах Ti–B–N, Ti–Al–Si–C–N и Ti–Ca–C–O–P–N показал, что изменение частоты электропитания, не оказывает существенного влияния на тип формирующегося осадка. Большинство покрытий обладали плотной лишенной столбчатых или игольчатых зерен структурой. В одних случаях наблюдалась плотная аморфоподобная структура излома (рис. 9), в других случаях – глобулярная (рис. 10).
С целью сравнения покрытий, получаемых на установках с различной конфигурацией магнитных полей были проведены исследования в системе Ti–Ca–C–O–P–N при максимально близких энергетических режимах. Полученные с помощью сканирующей электронной микроскопии данные представлены на рис. 11. Обнаружено, что наиболее плотные покрытия формируются в системах сбалансированного типа даже в отсутствие импульсного питания, тогда как для несбалансированных систем плотность покрытий и столбчатый рост заметно подавляется лишь при переходе к импульсному режиму (рис. 11в и 11г). Для установки магнетронного напыления с замкнутыми магнитными полями увеличение частоты электропитания приводит к формированию более плотной столбчатой структуры с менее выраженными столбчатыми элементами (рис. 11в и 11г).
Рис. 11.
Морфология покрытий Ti–Ca–C–O–P–N, полученных на установке со сбалансированными магнетронами при частоте 0 кГц (а), на установке с дуальными несбалансированными магнетронами при частоте 40 кГц (б), на установке с несбалансированными магнетронами с замкнутыми магнитными полями при частоте 0 кГц (в) и 300 кГц (г).
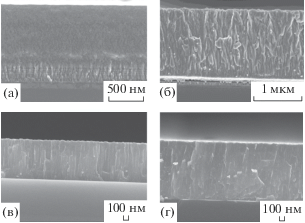
Отсутствие ярко выраженного воздействие импульсного электропитания на морфологию покрытий, по сравнению с простыми системами TiN, CrN, CrB2 и др. [23, 32] связано с тем, что покрытия, формируемые из сложнолегированных мишеней, сами по себе обладают плотной структурой за счет прерывания роста основных фаз при формировании покрытий из многокомпонентного потока [35–37]. Изменения, вызванные импульсным питанием, незаметны на общем фоне подавления столбчатой структуры за счет перекрывания роста кристаллитов аморфными прослойками или кристаллитами других фаз. Тем не менее, в распылительных системах с несбалансированными магнетронами наблюдается некоторое воздействие частоты на морфологию нанокомпозиционных покрытий, в целом схожее с тенденциями для двухкомпонентных покрытий – увеличение плотности при повышении частоты.
На рис. 12а приведены рентгенограммы покрытий Cr–Al–Si–B–N, осажденных при постоянном токе и при подаче импульсного электропитания. На рентгенограммах присутствуют пики от Al2O3, из-за попадания в зону анализа областей непокрытой подложки. Отражениям от покрытий соответствуют линии в положении ~46°. В случае импульсного питания характер рентгенограммы схожий со случаем для режима на постоянном токе, основная линия немного смещена в сторону меньших углов, имеет меньшую интенсивность и большее уширение. Детально покрытия этой системы изучены в работах [38, 39]. На рис. 12 представлены данные по покрытиям Zr–B–N, полученным при разных частотах в среде 100% азота. Помимо отражений от подложки (2Ө: 35° и 70°), обнаружены сильно уширенные пики небольшой интенсивности (2Ө = 30°–40°), которые близки к отражению от порошкового стандарта ZrB. Видно, что переход к импульсному режиму сопровождается снижением интенсивности линий, что можно объяснить меньшей толщиной покрытий. Также наблюдается увеличение ширины пиков, связанное с измельчением структуры. Расчет по формуле Шеррера дает значения 2.3 нм для покрытия на постоянном токе и 1.2 нм для образцов, полученных при 50 и 350 кГц.
Рис. 12.
Рентгенограммы покрытий в системах Cr‒Al–Si–B–N (а) и Zr–B–N (б), полученных при постоянном токе и при импульсном электропитании.
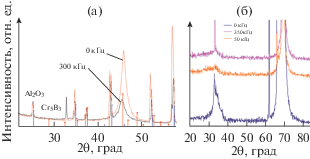
На рис. 13 приведены рентгенограммы для покрытий Ti–Ca–C–O–P–N, полученных при разных частотах на сбалансированном магнетроне. На всех дифрактограммах присутствуют пики (111), (200), (220) от ГЦК-фазы на основе карбонитрида титана. Средний размер кристаллитов, рассчитанный исходя из уширения линий (111) по формуле Шерера составлял 4.9, 4.4, и 5.5 нм для покрытий, полученных при частотах 0, 50, и 350 кГц соответственно.
Рис. 13.
Рентгенограммы покрытий Ti–Ca–C–O–P–N, полученных при частотах 0 кГц (вверху), 50 кГц (в середине) и 350 кГц (внизу) с использованием единичного сбалансированного магнетрона.
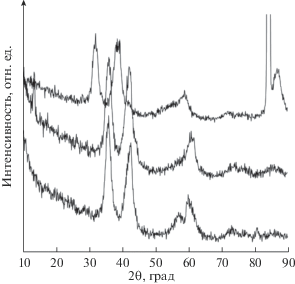
Расчеты по линиям (200) показали значения в диапазоне 3.9–4.1 нм для всех покрытий. Таким образом, прямого влияния частоты на размер кристаллитов для системы покрытий Ti–Ca–C–O–P–N установлено не было. Не было замечено сильного влияния частоты на текстурированность покрытий. При увеличении частоты с 0 до 350 кГц отношение интенсивностей линий I(111)/I(200) незначительно увеличивалось с 0.95 до 1.18. Наблюдаемое смещение пиков при повышении частоты может быть связано с различием в периоде решеток и со сжимающим напряжениями в покрытиях. Более значительное воздействие частоты на структуру покрытий было обнаружено при использовании для осаждения покрытий Ti–Ca–C–O–P–N системы из 4-х магнетронов с замкнутыми магнитными полями (рис. 14а).
Рис 14.
Рентгенограммы покрытий Ti–Ca–C–O–P–N, полученных при частотах 0 кГц и 300 кГц при использовании распылительной системы с замкнутыми магнитными полями (Cu-излучение) (а). Рентгенограммы покрытий Ti–Al–Si–C–N, полученных при частотах 0 кГц и 300 кГц (Co-излучение) (б).
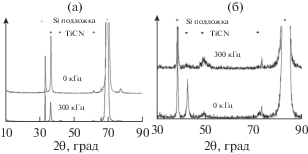
Как видно из рис. 14 основу покрытий, полученных при частотах 0 и 300 кГц составляет ГЦК-фаза с сильной текстурой в направлении (111). Отметим, что в случае покрытий, осажденных в системе с замкнутыми магнитными полями текстурированность намного выше, а уширение линий меньше, чем в случае покрытий, осажденных с использованием единичных сбалансированных магнетронов. При увеличении частоты с 0 до 300 кГц отношение интенсивностей линий I(111)/I(200) существенно понижается с 78.3 до 15.4 (рис. 14а), средний размер кристаллитов, рассчитанный из линий (111), уменьшается с 18.4 до 14.5 нм. Таким образом, при использовании несбалансированной магнетронной распылительной системы с замкнутыми магнитными полями, при увеличении частоты электропитания происходит измельчение структуры, а также снижается степень преимущественной ориентировки кристаллитов.
Близкие эффекты были обнаружены в системе покрытий Ti–Al–Si–C–N при сравнении режимов распыления постоянного тока и импульсного. При переходе к импульсному режиму наблюдалось смена преимущественной ориентировки с (111) на (200) (рис. 14б). Кроме того было замечено уменьшение размера кристаллитов. Уменьшение размера кристаллитов, а также смена преимущественной ориентировки были подтверждены также данными просвечивающей электронной микроскопии. Темнопольные изображения структуры и соответствующие им электронограммы для покрытий Ti–Al–Si–C–N представлены на рис. 15.
Рис. 15.
Темнопольные изображения структуры и электронограммы покрытий Ti–Al–Si–C–N, полученных при частоте 0 кГц (а) и 300 кГц (б). Результаты исследования покрытия Ti–Ca–C–O–P–N (осаждение при частоте 300 кГц) с помощью ПЭМ ВР (в).
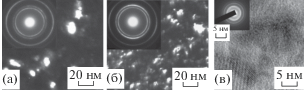
Согласно обсчетам темнопольных изображений структуры, средний размер кристаллитов ГЦК-фазы на основе TiCN уменьшался с ~7 до ~4 нм при переходе от распыления на постоянном токе (лабораторный трансформатор, ток 2 А, напряжение 500 В) к импульсному (блок Advanced Energy, ток 2 А, напряжение 500 В, частота 300 кГц).
Для покрытий Ti–Ca–C–O–P–N, полученных при частоте 350 кГц были проведены исследования с использованием просвечивающей электронной микроскопии высокого разрешения (рис. 15в). Согласно полученным результатам, основу покрытий Ti–Ca–C–O–P–N, осажденных при частоте 300 кГц, составляла фаза на основе карбонитрида титана. Кристаллиты имели неправильную форму, размер кристаллитов составлял от ~10 до ~20 нм. Вращение образцов в колонне микроскопа относительно электронного луча показало, что основной объем материала имеет кристаллическое строение. Разупорядоченные области локализованные в виде отдельных участков в объеме образца покрытия обнаружить не удалось. Данный факт может быть связан с низкой долей аморфной фазы в нанокомпозиционном покрытии Ti–Ca–C–O–P–N. Также возможно, что аморфная фаза формировалась в виде тонких (1–2 атомных слоя) прослоек между кристаллитами и не разрешалась из-за большой толщины участка под проходящим электронным пучком.
Для определения фазового состава, в том числе установления состава аморфных фаз, не обнаруживаемых дифракционными методами, были применены рентгеновская фотоэлектронная спектроскопия (прибор PHI 5500 ESCA Perkin-Elmer) и спектроскопия комбинационного рассеяния с использованием приборов LabRam и TRIAX (Horiba Jobin Yvon). В результате проведенных спектроскопических исследований было обнаружено, что большинство осажденных покрытий содержало помимо кристаллических фаз на основе TiN, TiCN, TiB2, CrB2 некоторое количество других фаз. Были выявлены следующие фазы: в покрытиях Ti–Al–Si–C–N – SiCxNy; в Ti–Ca–C–O–P–N – TiO2, SiO2, C; в Cr–Al–Si–B–N – BNx, SiNx, в Ti–B–N – BNx, TiB2, в Zr–B–N – BNx. Поскольку они не были обнаружены дифракционными методами, можно сделать заключение об их аморфной природе. Эксперименты по влиянию импульсных режимов на формирование покрытий, осаждаемых на постоянном токе с аморфной структурой, показали, что переход к импульсному питанию не приводит к кристаллизации.
Для установления взаимосвязи между данными спектроскопической диагностики плазмы, проведенной на предыдущем этапе, и составом уже осажденных покрытий были проведены измерения состава покрытий с помощью оптической эмиссионной спектроскопии тлеющего разряда (табл. 1). Фиксировались средние концентрации элементов по толщине покрытий за вычетом примеси кислорода (для большинства исследованных покрытий содержание кислорода составляло 2–3 ат. %).
Таблица 1.
Концентрации элементов в покрытиях Ti–Al–Si–C–N, полученных при 0 (1) и 300 кГц (2), ат. %
Покрытие | Ti | Al | Si | C | N | Ti/Al | (Ti + Al)/(Si + C + N) | Ti/N | Ti/(C + N) |
---|---|---|---|---|---|---|---|---|---|
1 | 31.80 | 15.10 | 7.00 | 19.50 | 26.60 | 2.11 | 0.88 | 1.20 | 0.69 |
2 | 29.80 | 13.20 | 9.30 | 17.40 | 30.30 | 2.26 | 0.75 | 0.98 | 0.62 |
Покрытия 1 и 2 были осаждены из одной мишени, при 0 и 300 кГц, соответственно. Из сравнения покрытий 1 и 2 следует, что предсказанное уменьшение интенсивности линий (концентрации) титана и алюминия действительно имеет место быть при переходе к импульсному распылению.
Закономерности распыления могут существенно отличаться для простых и многокомпонентных систем. Были проведены исследования химического состава покрытий, получаемых из мишени TiB в среде Ar + 15% N2. Использовались ранее подробно описанные блоки питания Advanced Energy (AE) а также блоки из лабораторных трансформаторов с диодными мостами. Основные параметры распыления поддерживались постоянными для изготовленных образцов. Результаты определения элементного состава покрытий, усредненного по толщине покрытий приведены в табл. 2.
Таблица 2.
Концентрации элементов и толщина покрытий Ti–B–N
Толщина, мкм | Ti, ат. % | B, ат. % | N, ат. % | |
---|---|---|---|---|
AE DC (0 кГц) | 2.38 | 42.4 | 32.1 | 25.5 |
AE 150 кГц | 2.47 | 42.4 | 32.3 | 25.3 |
AE 300 кГц | 2.51 | 42.5 | 33.2 | 24.3 |
Lab PS DC (0 кГц) | 2.15 | 40.8 | 31.3 | 27.9 |
Результаты исследований показывают, что в исследованной системе покрытий в рамках одного используемого блока состав покрытий при изменении частоты не изменяется. Некоторые отличия возникают при сравнении двух используемых блоков питания. Отметим, что отличия в закономерностях изменения химического состава от частоты у двух систем Ti–B–(N) и Ti–Al–Si–C–N вероятно связаны, во-первых, с отличием количества элементов, присутствующих в потоке от мишени (два и пять соответственно), а также с механизмом формирования покрытия (реакционный и нереакционный, соответственно). Важным моментом зафиксированным в ходе работы был эффект повышения скорости роста покрытий при увеличении частоты (табл. 2). Переход к импульсному режиму стимулирует формирование реакционных покрытий, за счет повышения общей поверхностной энергии при бомбардировке потоком частиц, в том числе заряженных. Кроме того повышение частоты ведет к более эффективному распылению мишени благодаря уменьшению отравления мишени азотом и стравливанию с ее поверхности тонких диэлектрических слоев или слоев с низкой проводимостью во время подачи обратного импульса. Отметим, что в случае покрытий Ti–Al–Si–C–N при повышении частоты электропитания заметно увеличивается степень ионизации рабочего газа (при исследованиях состава плазмы, было обнаружено, что интенсивность линий аргона возрастает с частотой).
На рис. 16 показаны трехмерные изображения поверхности покрытий Ti–Ca–C–O–P–N, осажденных на кремниевые подложки при частотах 0 и 350 кГц. На поверхности обоих типов покрытий присутствуют загрязнения, вероятно возникшие в процессе хранения и транспортировки. Им соответствуют резкие всплески на интерференционных картинах. Однако в случае покрытий, полученных при частоте 350 кГц, вся незагрязненная поверхность покрытий имеет выщерблены, локальные когезионные отслоения и другие дефекты. Шероховатость покрытий при увеличении частоты с 0 до 350 кГц возрастает с Ra = 1.8 нм до Ra = 3.7 нм. Аналогичный эффект, связанный с повышением шероховатости, был обнаружен при исследовании импульсных режимов напыления покрытий Ti–Al–Si–C–N.
Рис. 16.
Топография поверхности покрытий Ti–Ca–C–O–P–N, осажденных на кремний при частоте 0 кГц (а) и 350 кГц (б).
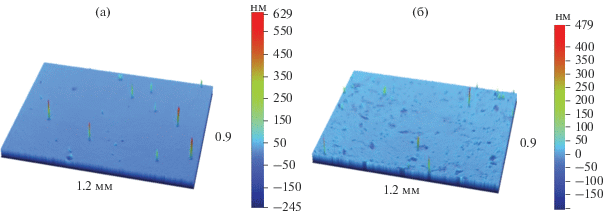
Основные данные измерений механических свойств для покрытий, осажденных при различных значениях температуры подложки (Т), напряжения смещения (Ucm), объeмной доли азота азота $({{P}_{{{{{\text{N}}}_{2}}}}})$, общего давления (P) и частоты (f) приведены в табл. 3. Результаты показали, что общее давление является одним из ключевых факторов, обеспечивающих высокий уровень твердости и упруго-пластических свойств. Так, покрытия в системе Ti–B–N, полученные при давлении 0.2 и 3 Па показали значения твердости соответственно 15 и 5.4 ГПа. Следующим важным технологическим параметром явилось парциальное давление азота. В покрытиях на основе боридов металлов, таких как Ti–B–N, Cr–Al–Si–B–N увеличение содержания азота в покрытиях приводило к заметному понижению как твердости, так и модуля упругости. Данный эффект может быть объяснен формированием в этих покрытиях дополнительной фазы на основе аморфного нитрида бора (a-BNx), при введении азота в состав покрытий. Фаза a-BNx обладает существенно более низкими значениями твердости и модуля упругости (H ~ 8 ГПа, E ~ ~ 90 ГПа), чем бориды переходных металлов (H ~ ~ 20–35 ГПа, E = 350–450 ГПа). В ходе работы было установлено, что в случае карбидных систем (Ti–Al–Si–C–N, Ti–Ca–C–O–P–N) характер влияния парциального давления азота более сложный, поскольку атомы азота встраиваются в решетку карбида титана без образования дополнительных аморфных фаз.
Таблица 3.
Механические свойства покрытий
Мишень | Т, °С | Ucm, В | ${{P}_{{{{N}_{2}}}}}$, % | P, Па | f, кГц | H, ГПа | Е, ГПа | W, % |
---|---|---|---|---|---|---|---|---|
TiB | 300 | –250 | 15 | 0.2 | 0 | 21 | 227 | 51 |
300 | –250 | 15 | 0.2 | 150 | 23 | 231 | 54 | |
300 | –250 | 15 | 0.2 | 300 | 20 | 223 | 50 | |
TiAlSiCN | 500 | –250 | 15 | 0.2 | 0 | 49 | 457 | 67 |
500 | –250 | 15 | 0.2 | 300 | 45 | 411 | 65 | |
TiCaCOP | 300 | –250 | 15 | 0.2 | 0 | 31 | 240 | 69 |
300 | –250 | 15 | 0.2 | 50 | 36 | 223 | 71 | |
300 | –250 | 15 | 0.2 | 300 | 33 | 229 | 71 | |
ZrB | 300 | 0 | 100 | 0.2 | 0 | 10 | 132 | 67 |
300 | 0 | 100 | 0.2 | 50 | 11 | 133 | 74 | |
300 | 0 | 100 | 0.2 | 300 | 14 | 145 | 80 |
Частота электропитания также влияла на механические свойства покрытий. В покрытиях Ti–B–N и Ti–Ca–C–O–P–N, осажденных с помощью блока питания Advanced Energy (США), зависимость механических свойств от частоты носила экстремальный характер (табл. 3). Максимальные значения твердости и модуля упругости достигались при f = 50–150 кГц. Покрытия, осажденные при большой частоте f = 300–350 кГц имели свойства ниже, чем покрытия, полученные на постоянном токе. Данная зависимость может быть объяснена двумя конкурирующими процессами при увеличении частоты электропитания – уплотнением структуры покрытий и увеличением концентрации дефектов в покрытии вследствие роста внутренних напряжений и их релаксации при локальных когезионных разрушениях. Сравнение покрытий Ti–Al–Si–C–N, полученных с помощью лабораторного трансформатора с диодными мостами на постоянном токе и с использованием блока Pinnacle + Advanced Energy при частоте 300 кГц, показало, что во втором случае покрытия имеют несколько более низкие механические свойства. Отличие может быть связано со сложностью оценки реальной мощности, подаваемой на магнетрон с лабораторного трансформатора без учета потерь.
Результаты, полученные для покрытий Ti–B–N, осажденных при разных частотах, в ходе проведения скратч-тестирования, приведены на рис. 17–19. Было установлено, что покрытия полученные на постоянном токе имеют наибольшие значения Lc2. Разрушение в виде отслоений начинаются при нагрузках свыше 34 Н. До этого момента наблюдаются лишь мелкие трещины при ~15 Н (Lc1). При частоте 150 кГц зафиксировано Lc2 = 16 Н, а при 300 кГц Lc2 = 26–31 Н. Относительно более низкие значения Lc2 в случае импульсных режимов вероятно связаны с высокими внутренними напряжениями в покрытиях.
Рис. 17.
Кривые скратч-тестирования и фотографии области разрушения для покрытия Ti–В–N, полученного при частоте 0 кГц.
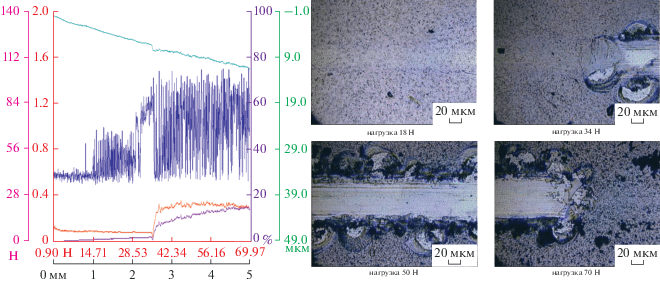
Рис. 18.
Кривые скратч-тестирования и фотографии области разрушения для покрытия Ti–В–N, полученного при частоте 150 кГц.
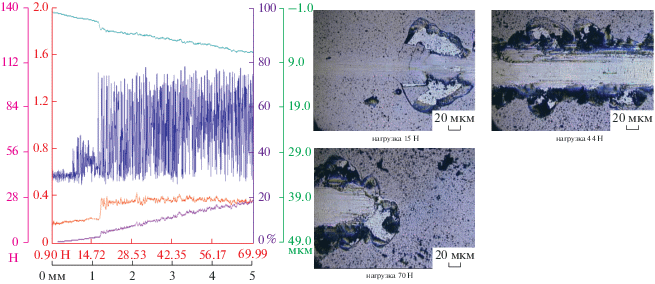
Рис. 19.
Кривые скратч-тестирования и фотографии области разрушения для покрытия Ti–В–N, полученного при частоте 300 кГц.
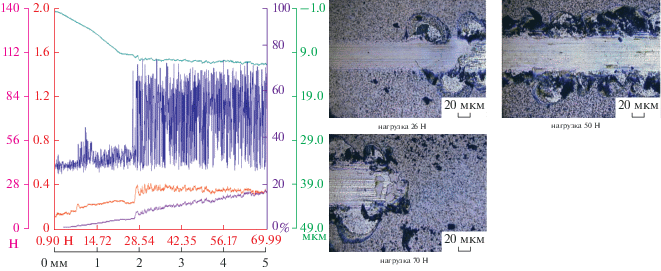
Типичные кривые скратч-испытаний покрытий Ti–Al–Si–C–N показаны на рис. 20 и 21. В случае покрытия, полученного при постоянном токе на графике акустической эмиссии видны выбросы, появляющиеся при нагрузке ~29–35 Н, которые связаны с деформацией покрытия по механизму смятия. Можно допустить наличие растрескивания покрытия, соответствующего нагрузке Lc1, однако визуальное наблюдение области разрушения опровергает это предположение. Остальные параметры скратч-тестирования монотонно изменялись при повышении нагрузки (дистанции), без каких либо скачкообразных изменений, соответствующих отслоению и касанию индентором подложки, что свидетельствует о высокой адгезионной прочности покрытий. При нагрузке около 60 Н в области царапины наблюдались участки, в которых нельзя исключить возможность когезионных отслоений.
Рис. 20.
Кривые скратч-тестирования и фотографии области разрушения для покрытия Ti–Al–Si–C–N, полученного при частоте 0 кГц.
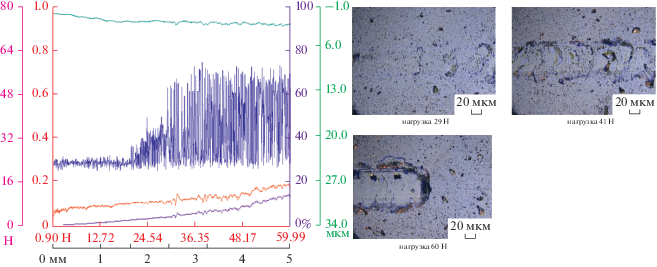
Рис. 21.
Кривые скратч-тестирования и фотографии области разрушения для покрытия Ti–Al–Si–C–N, полученного при частоте 350 кГц.
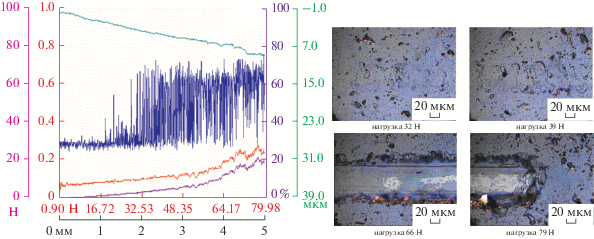
На рис. 21 показаны типичные изображения царапин, образовавшихся в процессе скратч-тестирования покрытий Ti–Al–Si–C–N, нанесенных на твердосплавные подложки при частоте 350 кГц. На микрофотографиях видно, что дефектность поверхности покрытий выше, чем при распылении на постоянном токе. Повышенная шероховатость поверхности и наличие дефектов затрудняет визуальную оценку параметра Lc1. Однако из кривой акустической эмиссии видно, что до 17–18 Н растрескивание покрытия отсутствует. При нагрузке ~33–36 Н начинается деформация покрытия по механизму смятия, но отслоений до подложки не наблюдается, т.е. основной механизм разрушения соответствует случаю с постоянным током. При достижении нагрузки порядка 55–60 Н наблюдается формирование отслоений по краям дорожки, а при нагрузке Lc > 65 Н визуально при наблюдении в микроскоп фиксируется истирание покрытия до подложки. Этот момент сопровождается изменением в наклоне кривых скратч-тестирования. На графиках акустической эмиссии, коэффициента трения и силы трения наблюдается перегиб.
В процессе трибологических испытаний было выяснено, что покрытия, полученные при средних частотах, обладают более низким коэффициентом трения, чем покрытия, полученные на постоянном токе и при максимальной частоте. Графики зависимости коэффициентов трения от дистанции пройденной шариком при испытаниях “стержень–диск” для покрытий Ti–Сa–C–O–P–N показаны на рис. 22. Из рисунка также видно, что пи прочих равных условиях осаждения и испытаний, образец, полученный при частоте 50 кГц сохраняется без разрушения дольше нежели покрытия, полученные при других частотах. Для оценки износостойкости в количественном выражении эксперименты были продублированы с меньшей дистанцией пробега. Вычисления скорости износа, величины обратно пропорциональной износостойкости материала, показали, что покрытия, осажденные при частоте 50 кГц, показали наименьшие значения – около 0.2 × 10–6 мм3 Н–1 м–1, тогда как покрытия на постоянном токе – 0.5 × 10–6 мм3 Н–1 м–1, а покрытия при максимальной частоте 1.5 × 10–6 мм3 Н–1 м–1. То есть средние частоты являются оптимальными, что объясняется максимальной твердостью этих покрытий в сочетании с удовлетворительной шероховатостью и низким уровнем дефектов.
Отметим, что в системе покрытий Ti–Al–Si–C–N явного эффекта от перехода к импульсному режиму обнаружено не было. В пределах ошибки механические свойства менялись незначительно. Однако основное влияние было зафиксировано в процессе трибологических испытаний покрытий. На рис. 22 показаны результаты трибологических испытаний покрытий в системе Ti–Al–Si–C–N. Видно, что при наложении импульсного питания происходит некоторое снижение коэффициента трения, но самое главное – происходит его стабилизация во времени.
Результаты измерения скорости износа показали, что при использовании импульсного режима износостойкость покрытий Ti–Al–Si–C–N возрастает вдвое. Скорость износа снижается с 5.9 × 10–6 до 2.93 × 10–6 мм3 Н–1 м–1. Типичные трехмерные профили областей износа показаны на рис. 23. Интересно отметить, существенное повышение шероховатости при использовании импульсного электропитания.
Рис. 23.
Трехмерные изображения областей износа для покрытий Ti–Al–Si–C–N, полученных при постоянном токе (а) и частоте 300 кГц (б).
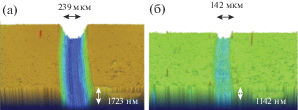
Результаты трибологических исследований покрытий Ti–B–N, полученных с использованием импульсного блока Advanced Energy (АЕ) при различных частотах и лабораторного трансформатора постоянного тока (ЛАТР) приведены на рис. 24.
Из рисунка 24 видно, что амплитуда колебаний значений коэффициента трения в процессе испытаний отличается для всех образцов покрытий, что связано с различием в шероховатости покрытий. Действительно, покрытия, полученные на постоянном токе с блоком АЕ имеют более низкую шероховатость и дефектность, чем покрытия, осажденные на импульсном режиме. Наиболее стабильный во времени коэффициент трения показали покрытия, осажденные на блоке АЕ при 0 кГц, с другой стороны покрытия, осажденные на импульсном режиме имели более низкий коэффициент трения.
Анализ дорожек с использованием оптического профилометра показал, что покрытия, осажденные с использованием ЛАТР на дистанции 100 м полностью изнашиваются, в то время, как при использовании блока АЕ и постоянного тока, скорость износа невелика и составляет 2.12 × × 10–6 мм3 Н–1 м–1. Близкие значения были определены для покрытия, осажденного при частоте 300 кГц – 3.51 × 10–6 мм3 Н–1 м–1. Покрытия, полученные при частоте 150 кГц, продемонстрировали полный износ. Низкая износостойкость может быть успешно объяснена их крайне низкой адгезионной прочностью. Важно отметить, что изменение частоты электропитания оказывало влияние на механизм износа покрытий (рис. 25).
Рис. 25.
Двухмерные изображения дорожек износа для покрытий Ti–B–N, осажденных при постоянном токе (слева) и при частоте 300 кГц (справа).
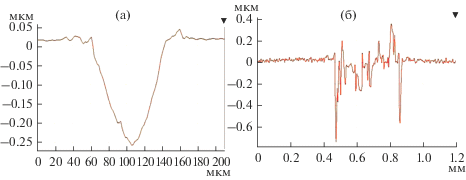
Ровная форма дорожки в случае покрытия, осажденного на постоянном токе, свидетельствует об абразивном механизме износа – постепенное истирание поверхности покрытия. В случае покрытия, полученного в частотном режиме, форма дорожки существенно изменяется. Глубина дорожки по центральной части сечения невелика и соизмерима с глубиной для случая покрытия на постоянном токе (0.2–0.3 мкм). Однако периферийные участки дорожки имеют большую глубину – около 0.6–0.8 мкм. Кроме того, профиль дна дорожки имеет зубчатую форму. Указанные особенности, свидетельствуют о том, что в случае покрытия, осажденного при частоте 300 кГц, механизм износа меняется на адгезионный. Вероятно, из-за высоких внутренних напряжений и дефектности в последнем случае идет взаимодействие сколотых фрагментов покрытия с еще не разрушенными областями по адгезионому механизму.
ВЫВОДЫ
Обобщая результаты, полученные с использованием технологии PMS при нанесении покрытий из многокомпонентных СВС-катодов, можно сделать следующие выводы:
а) Структура покрытий. Импульсное распыление приводит к созданию более плотной и в то же время более дефектной структуры с высоким уровнем внутренних напряжений и шероховатости. Влияние импульсного режима на размер зерен зависит от типа распыления и конфигурации магнитных полей. Для реакционного распыления в ряде случаев выражено измельчение структуры. Обнаружен эффект увеличения толщины реакционных покрытий вследствие активации взаимодействия атомов, распыленных из мишени с атомами азота при осаждении и минимизации отравления поверхности мишени.
б) Свойства покрытий. Влияние импульсного режима на адгеизионную прочность покрытий сводится к ее снижению. Зависимости твердости и других механических свойств от частоты импульсного питания носят экстремальный характер с максимумом при 50 кГц. Использование небольших частот (50–150 кГц) приводит к снижению коэффициента трения. При переходе к импульсному режиму наблюдается стабилизация коэффициента трения в процессе испытания, а также, в большинстве случаев – повышается износостойкость.
Список литературы
Kelly P.J., Arnell R.D. // Vacuum. 2000. V. 56. P. 159–172.
McLeod P.S., Hartsough L.D. // J. Vacuum Science and Technology. 1977. V. 14. P. 263–265.
Waits R.K. // J. Vacuum Science and Technology. 1978. V. 15. P. 179–187.
Window B., Savvides N. // J. Vacuum Science and Technology. A. 1986. V. 4. P. 196–202.
Sproul W.D., Rudnick P.J., Graham M.E., Rohde S.L. // Surface and Coatings technology. 1990. V. 43/44. P. 270–278.
Anders A. // Thin Solids Films. 2006. V. 502. P. 22–28.
Safi I. // Surface and Coatings Technology. 2000. V. 127. P. 203–219.
Carter D., Walde H., McDonough G., Roche G. Parameter Optimization in Pulsed DC Reactive Sputter Deposition of Aluminum Oxide, 45th Annual Technical Conference Proceedings. 2002. Society of Vacuum Coaters, p. 570–577.
Kelly P.J., Henderson P.S., Arnell R.D. // J. Vacuum Science and Technology A. 2000. V. 18. № 6. P. 2890–2896.
Arnell R.D., Kelly P.J., Bradley J.W. // Surface and Coatings Technology. 2004. V. 188–189. P. 158–163.
Misina M., Bradley J.W., Bäcker H., Aranda-Gonzalvo Y., Karkari S.K., Forder D. // Vacuum. 2003. V.68. P. 171–181.
Bradley J.W., Bäcker H., Aranda-Gonzalvo Y., Kelly P.J., Arnell R.D. // Plasma Sources Science and Technology. 2002. V. 11. P. 165–174.
Onifade A.A., Kelly P.J. // Thin Solid Films. 2006. V. 494. P. 8–12.
Musil J., Lestina J., Vlcek J., Tolg T. // J. Vacuum Science and Technology A. 2000. V. 19. № 2. P. 420–424.
Belkind A., Freilich A., Scholl R.J. // J. Vacuum Science and Technology A. 1999. V. 17. № 4. P. 1934–1940.
Lin J., Moore J.J., Mishra B., Sproul W.D., Rees J.A. // Surface and Coatings Technology. 2007. V. 201. P. 4640–4652.
Tung-Sheng Yeh, Jenn-Ming Wu, Long-Jang Hu. // Thin Solid Films. 2008. V. 516. P. 7294–7298.
Benegra M., Lamas D.G., Fernández de Rapp M.E., Mingolo N., Kunrath A.O., Souza R.M. // Thin Solid Films. 2006. V. 494. P. 146–150.
Kelly P.J., Beevers C.F., Henderson P.S., Arnell R.D., Bradley J.W., Bäcker H. // Surface and Coatings Technology. 2003. V. 174–175. P. 795–800.
Henderson P.S., Kelly P.J., Arnell R.D., Bäcker H., Bradley J.W. // Surface and Coatings Technology. 2003. V. 174–175. P. 779–783.
Treichel O., Kirchhoff. V. // Surface and Coatings Technology. 2000. V. 123, Issues 2–3. P. 268–272.
Bartzsch H., Frach P., Goedicke K., Gottfried Chr. Energetic Substrate Bombardment in Reactive Sputtering with Flange-Mounted Magnetrons in Different Pulse Modes, 45th Annual Technical Conference Proceedings. 2002. Society of Vacuum Coaters, p. 148–152.
Barshilia H.C., Rajam K.S. // Surface and Coatings Technology. 2006. V. 201. P. 1827–1835.
Jyh-Wei Lee, Shih-Kang Tien, Yu-Chu Kuo // Thin Solid Films. 2006. V. 494. P. 161–167.
Lin J., Wu Z.L., Zhang X.H., Mishra B., Moore J.J., Sproul W.D. // Thin Solid Films. 2009. V. 517. P. 1887–1894.
Åstrand M., Selinder T.I., Sjöstrand M.E. // Surface & Coatings Technology. 2005. V.2 00. P. 625–629.
Barshilia H.C., Yogesh K., Rajam K.S. // Vacuum. 2009. V. 83. P. 427–434.
Cremer R., Reichert K., Neuschütz D. // Surface and Coatings Technology. 2001. V.142–144. P. 642–648.
Moser M., Mayrhofer P.H., Székely L., Sáfrán G., Barna P.B. // Surface and Coatings Technology. 2008. V. 203. P. 148–155.
Sunal P., Messier R., Horn M.W. // Thin Solid Films. 2006. V. 515. P. 2185–2191.
Audronis M., Kelly P.J., Arnell R.D., Valiulis A.V. // Surface and Coatings Technology. 2006. V. 200. P. 4166–4173.
Audronis M., Kelly P.J., Leyland A., Matthews A. // Thin Solid Films. 2006. V. 515. P. 1511–1516.
Audronis M., Rosli Z.M., Leyland A., Kelly P.J., Matthews A. // Surface and Coatings Technology. 2008. V. 202. P. 1470–1478.
Audronis M., Leyland A., Matthews A., Kiryukhantsev-Korneev F.V., Shtansky D.V., Levashov E.A. // Plasma Process. Polym. 2007. V. 4. P. 687–692.
Kiryukhantsev-Korneev Ph.V., Pierson J.F., Bauer J.Ph., Levashov E.A., Shtansky D.V. // Glass Physics and Chemistry. 2011. V. 37. № 4. P. 411–417.
Kiryukhantsev-Korneev Ph.V., Pierson J.F., Kuptsov K.A., Shtansky D.V. // Applied Surface Science. 2014. V. 314. P. 104–111.
Kiryukhantsev-Korneev F.V., Shirmanov N.A., Sheveiko A.N., Levashov E.A., Petrzhik M.I., Shtanskii D.V. // Russian Engineering Research. 2010. V. 30. № 9. P. 909–919.
Kiryukhantsev-Korneev F.V., Novikov A.V., Sagalova T.B., Petrzhik M.I., Levashov E.A., Shtansky D.V. // Physics of Metals and Metallography. 2017. V. 118. № 11. P. 1136–1146.
Kiryukhantsev-Korneev F.V., Kuptsov K.A., Sheveiko A.N., Levashov E.A., Shtansky D.V. // Russian J. Non-Ferrous Metals. 2013. V. 54. № 4. P. 330–335.
Kuptsov K.A., Kiryukhantsev-Korneev Ph.V., Sheveyko A.N., Shtansky D.V. // Surface and Coatings Technology . 2013. V. 216. P. 273–281.
Shtansky D.V., Batenina I.V., Yadroitsev I.A., Ryashin N.S., Kiryukhantsev-Korneev Ph.V., Kudryashov A.E., Sheveyko A.N., Zhitnyak I.Y., Gloushankova N.A., Smurov I.Y., Levashov E.A. // Surface and Coatings Technology. 2012. V. 208. P. 14–23.
Kiryukhantsev-Korneev F.V., Lemesheva M.V., Shvyndina N.V., Levashov E.A., Potanin A.Yu. // Protection of Metals and Physical Chemistry of Surfaces. 2018. V. 54. № 6. P. 1147–1156.
Iatsyuk I.V., Lemesheva M.V., Kiryukhantsev-Korneev Ph.V., Levashov E.A. // IOP Conference Series: Materials Science and Engineering. 2018. V. 347. P. 012–028.
Кирюханцев-Корнеев Ф.В., Левашов Е.А. Эффект прозрачности в пленках Zr−B−N, полученных с помощью магнетронного распыления мишени ZrB2 Письма в ЖТФ, 2020, том 46, вып. 4 c. 30–32.
Дополнительные материалы отсутствуют.
Инструменты
Физикохимия поверхности и защита материалов