Физикохимия поверхности и защита материалов, 2022, T. 58, № 3, стр. 329-336
Влияние природы анионов на адгезионную долговечность битумно-анионитных защитных систем
Н. Н. Петров 1, 2, *, А. С. Черный 2, Д. В. Грицун 2, Т. В. Кукора 2, А. Б. Фурсина 2, Ю. Г. Петрова 3, Н. Н. Буков 2
1 Компания “Интеллектуальные композиционные решения”
350063 Краснодар, ул. Коммунаров, д. 31/1, Россия
2 ФГБОУ ВО “Кубанский государственный университет”, Факультет химии и высоких технологий
350040 Краснодар, ул. Ставропольская, 149, Россия
3 Лаборатория электрохимической защиты “Газпром ВНИИГАЗ”
142717 Московская область, пос. Развилка, Проектируемый проезд, 5537, Россия
* E-mail: nikpetro@yandex.ru
Поступила в редакцию 17.05.2021
После доработки 31.05.2021
Принята к публикации 07.06.2021
- EDN: LSMYQU
- DOI: 10.31857/S0044185622030160
Аннотация
Изучено влияние вводимого в качестве активного наполнителя сильноосновного анионита АВ-17-8 в различных ионных формах на адгезионную стойкость битумно-анионитных защитных систем при их катодной поляризации. Для изучения выбраны следующие ионные формы анионита: исходная хлоридная форма, а также нитрат-, гидроксо-, сульфат-, хромат-, карбонат-, силикат-, фосфат- и гидроксоалюминат-формы. Показано существенное влияние ионной формы вводимого анионита на катодное отслаивание, и как следствие адгезионную долговечность битумно-анионитных защитных противокоррозионных покрытий. Обнаружен эффект ингибирования отслаивания, объясняемый природой взаимодействия подвижного аниона микрорезервуара (частиц АВ-17-8) с образуемыми в анодной зоне на поверхности стали в “ячейке отслаивания” катионами железа (2+). Данный эффект может быть использован при создании защитных противокоррозионных покрытий с повышенной долговечностью и защитным ресурсом.
ВВЕДЕНИЕ
Глобальная хозяйственная деятельность человека привела к созданию планетарной технической инфраструктуры, взаимодействующей с природой.
Очевидно, что в настоящее время достигнут критический уровень современного техногенного воздействия на сбалансированные ранее природные среды. Протекающие под воздействием различных физико-химических факторов процессы как естественного, так и активированного старения ограничивают срок жизни и физический предел уязвимости создаваемых систем, и во многом определяют их ресурс и бесконфликтность по отношению к окружающей среде [1]. При этом вещественной основой любой технической системы, являются природные или синтетические материалы, обеспечивающие ее функционал и конструкционную целостность.
Сталь является одним из основных конструкционных элементов при строительстве производственных и гражданских сооружений. Долговечность и надежность при их эксплуатации во многом зависит от предотвращения термодинамически неизбежного процесса коррозии металла.
Одним из сложных объектов для противокоррозионной защиты являются различные подводные и подземные трубопроводы, от целостности которых зависит стабильность экономики и ее энергобезопасность.
На сегодняшний день имеется большое количество средств пассивной защиты поверхности металла (противокоррозионных покрытий), повышающих ресурс стальных конструкций.
До недавнего времени основными требуемыми свойствами защитных покрытий здесь являлись как можно более высокие диэлектрические характеристики и высокая адгезия к защищаемой поверхности. Однако, вследствие неизбежного старения структуры защитных материалов, и как следствие деградации их защитных свойств, такой подход оказался недостаточно эффективным [2–4]. Под действием внешних условий в изоляционных покрытиях происходят разнохарактерные физико-химические процессы, вызывающие их старение: окислительно-деструктивные процессы, изменяющие молекулярную и надмолекулярную полимерную структуру и вызывающие ухудшение защитных характеристик покрытий [5]. В результате старения происходит постепенное снижение защитной эффективности или накопление скрытых дефектов, приводящее к скачкообразному уменьшению одной или нескольких эксплуатационных характеристик покрытия определяющих его защитный потенциал [6].
Современный подход в борьбе с коррозией конструкций и сооружений в различных водных средах и почвах предполагает наличие активных методов защиты, которые должны осуществлять защиту совместно с пассивными методами, то есть с покрытиями. Классическими активными методами здесь являются протекторная и катодная защита, основанные на подавлении анодных процессов растворения металла электрическим током [7].
Многолетняя практика эксплуатации известных изоляционных термопластичных (например, битумных и битумно-полимерных) и термореактивных (например, эпоксидных) покрытий для трубопроводов свидетельствует о том, что физическая природа адгезионных связей покрытия с металлом не может обеспечить их сохранение в течение длительного срока. При применении данных покрытий в условиях катодной поляризации существенным фактом ослабления эффективности, приводящим к выше перечисленным проблемам, является их высокое катодное отслаивание [8, 9]. При этом начинается проникновение электролита под отслаивающееся покрытие и анодное растворение металла с проникновением в отслоившийся дефект катодно восстанавливающегося кислорода. Щелочная среда, формирующаяся в этом коррозионном элементе, способствует отслоению покрытия за счет растворения слоя амфотерных оксидов, распада полимера, и гидролиза межфазных адгезионных связей, что в итоге существенно уменьшает эффективность защиты и приводит к образованию коррозионных очагов [10].
В настоящее время развивается направление получения защитных материалов с самовосстанавливающейся адгезионной связью. При этом, независимо от пути “самовосстановления” конечным продуктом будет новая когезионно совместимая фаза на межслойной границе субстрат/покрытие [1].
Например, в работах [11, 12] показан эффект различных катионов металлов, вводимых в ионообменных микрорезервуарах. Показано, что введение в полимерную смесь катионов образующих нерастворимые гидроокиси существенно повышает долговечность адгезии и препятствует отслаиванию покрытий от стали. При этом ингибирование отслоения приближается к 100%.
Недостатками этих систем являются токсичность входящих в состав покрытия тяжелых металлов и относительно высокая стоимость реагентов для получения требуемой ионной формы катионита.
Цель данной работы – изучение возможности использования анионообменных микрорезервуаров и природы их подвижных противоионов – различных анионов для эффекта “самовосстановления” адгезии противокоррозионных систем, применяемых в условиях катодной поляризации.
ЭКСПЕРИМЕНТАЛЬНАЯ ЧАСТЬ
Используемые материалы. Объектами исследований являлись: сильноосновный анионит АВ-17-8 (ГОСТ 20301-74) в исходной хлоридной форме и его модифицированные образцы; битумное связующее и полиэтиленовая пленка (толщиной 1 мм) образующие двуслойное битумно-полимерное покрытие (производство АО “Делан”, Россия) [12]; двуслойные покрытия на основе приготовляемых по ниже описанной методике битумно-полиэлектролитных связующих.
Перевод анионита в выбранные ионные формы. Исходный анионит АВ-17-8 в Cl–-форме помещали (двукратно) в 5 мас. % водные растворы соответствующих солей натрия (нитрат, сульфат, хромат, карбонат, силикат, ортофосфат и алюминат), а также в 5 мас. % раствор гидроксида натрия при объемном соотношении анионит – раствор 1 : 4 и выдерживали при температуре окружающего воздуха 7 суток. После чего полученные аниониты отфильтровывали, промывали пятикратным избытком дистиллированной воды и высушивали до постоянной массы при температуре 110°C в сушильном шкафу.
Для контроля количественности процесса ионного замещения, после процедуры описанной выше, полученные аниониты анализировали на содержание подвижного аниона. Для этого навеску ионита помещали в 0.1 М раствор хлорида натрия и выстаивали при легком перемешивании 5 ч, затем отбирали аликвоту. После этого производили определение концентрации соответствующего аниона по методикам, указанным в табл. 1 и пересчитывали на содержание в фазе анионита.
Таблица 1.
Методы определения полноты процесса ионного обмена в анионнообменнике
№ п/п | Анион | Метод определения | Нормативный документ на метод определения |
---|---|---|---|
1 | OH– | Определение титриметрическим методом | ПНД Ф 14.1:2.245-07 |
2 | ${\text{OH}}_{3}^{ - }$ | Определение фотометрическим методом | ПНД Ф 14.1:2:4.4-95 |
3 | ${\text{SO}}_{4}^{{2 - }}$ | Определение титриметрическим методом | ГОСТ 31940-2012 |
4 | ${\text{SiO}}_{3}^{{2 - }}$ (по Si) |
Фотометрическое определение кремния | РД 52.24.432-95 |
5 | ${\text{CO}}_{3}^{{2 - }}$ | Определение титриметрическим методом | ГОСТ 31957-2012 |
6 | ${\text{PO}}_{4}^{{3 - }}$ | Определение фотометрическим методом | ПНД Ф 14.1:2.112-97 |
7 | ${\text{CrO}}_{4}^{{2 - }}$ (по Cr7+) |
Определение фотометрическим методом | ПНД Ф 14.1:2:4.52-96 |
8 | ${\text{Al}}({\text{OH}})_{4}^{ - }$ (по Al3+) |
Определение фотометрическим методом | ГОСТ 18165-2014 |
Меру количественности процесса замещения (замещенность) определяли по формуле:
где СОЕ – статическая обменная емкость анионита, мг экв г–1, Z – заряд подвижного иона, СAn – найденное cодержание аниона, ммоль/г.Полученные значения замещенности для всех образцов анионита находились в интервале 98 ± 4%.
Приготовление битумно-анионитного компаунда. Осуществляли смешивание предварительно подготовленных порошков анионита АВ-17-8 в выбранных ионных формах с битумным компаундом при температуре текучести битума в заранее подобранных условиях, обеспечивающих гомогенность распределения наполнителя в полимерной матрице. При этом наполнитель вводился в максимально возможной концентрации (10 мас. %) обеспечивающей неизменность начальных физико-механических характеристик битума [12].
Перед введением полученный анионит в различных ионных формах высушивали при температуре 110°C до воздушно-сухого состояния и просеивали порошок, полученный перемолом на планетарной мельнице. В дальнейшем использовали фракцию частиц, прошедших сито 50 мкм.
Нанесение покрытия на сталь. На предварительно подготовленные до степени Sa 3 стальные пластины (низкоуглеродистая сталь Ст. 3, Россия) подогретые до температуры 60 ± 10°C наносили изучаемые битумные расплавы толщиной 1–2 мм (температура расплава 180–190°C) при одновременном нанесении (без потери текучести битума) полимерной обертки при прокатке ее валиком до сцепления со связующим. Полученные образцы 100 × 100 мм оставляли охлаждаться при температуре 25 ± 5°С в условиях открытой атмосферы в течении трех суток, а затем проводили процедуру по определению их стойкости к катодному отслаиванию.
Определение катодного отслаивания образцов. Испытания проводили по методике, изложенной в ГОСТ 51164-98 (Россия). Для этого собирали ячейку, изображенную на рис. 1. В центре образца в изучаемом защитном покрытии сверлили цилиндрическое отверстие диаметром 0.6 см до образования в металле конического углубления. На пластину с помощью пластилина устанавливали трубу из полиэтилена таким образом, чтобы ось трубы совпала с центром высверленного в покрытии отверстия. Далее в трубу заливали электролит (раствор хлористого натрия) до уровня 50 мм от поверхности покрытия. Образец с помощью проводов соединяли с магниевым анодом, как показано на рис. 1. При этом на образце устанавливали потенциал минус 1.35 – минус 1.45 В по хлорсеребряному электроду сравнения. Образцы выдерживали в растворе электролита под действием наложенного катодного тока в течение 10 дней при температуре 25 ± 5°C. По окончании испытаний образец с покрытием демонтировали, промывали водой и вытирали ветошью. Площадь отслоившегося участка покрытия оголяли, осторожно поддевая и срезая покрытие скальпелем. Площадь отслаивания переводили на кальку, а затем вычисляли методом взвешивания. Относительная погрешность определения при этом не превышала 5%.
РЕЗУЛЬТАТЫ И ИХ ОБСУЖДЕНИЕ
Введение порошка анионита в битум изменяет морфологию компаунда (рис. 2). Как видно из микрофотографий поверхности поперечного разлома изучаемых образцов микроструктура компаунда при введении микрочастиц ламеризуется, появляются структурно-оформленные микронити.
Рис. 2.
Микрофотографии полученных битумных компаундов (поперечный разлом): (а) исходное битумное связующее, (б) битумный компаунд с добавкой порошка анионита (увеличение ×400).
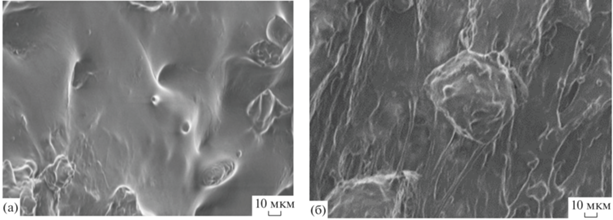
Изучение адгезионной долговечности материалов в условиях катодной поляризации проводилось с помощью теста на катодное отслаивание. Данный метод хорошо имитирует реальные условия жизненного цикла покрытия [13, 14], являясь ускоренным тестом, вследствие сходной природы отслаивания покрытия при проникновении под него электролита и формирующейся “ячейки отслаивания” в условиях катодной поляризации. При этом скорость отслоения зависит от природы испытываемой системы и субстрата, ее адгезионной стойкости и долговечности [15].
Полученные экспериментальные данные по отслаиванию представлены на рис. 3. Площадь отслаивания, как видно, изменяется при смене подвижного аниона в водимом анионите. Исходя из статистического распределения полученной выборки мы можем выделить три независимые группы значений (неперекрываемых с вероятностью выше 99% (3σ) интервала значений подмножеств выборки): I – группа с минимальным уменьшением отслаивания со средней площадью отслаивания 7.8 см2 (относительно исходного битума без введения анионита), II – центральная группа со средней площадью 3.2 см2 и III – группа с высоким подавлением отслаивания (средняя площадь отслаивания 0.95 см2), при этом система с введенным АВ-17-8 в гидроксо-форме не входит в названные группы, в связи с увеличением площади отслаивания по результатам теста.
Рис. 3.
Зависимость величины катодного отслаивания изучаемых систем от сорта вводимых анионов (n = 6).
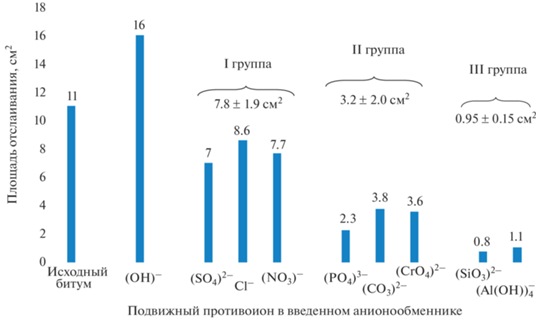
Как показано в работе [16] увеличение адгезионной стойкости происходит за счет взаимодействия активного фазового элемента материала покрытия с исходными или индуцированными соединениями внешней агрессивной среды. При этом конечным продуктом должна быть новая когезионно совместимая фаза (субфаза) на межслойной границе субстрат/покрытие.
Для объяснения полученных результатов необходимо определиться с источником активных фазовых элементов. Ионы натрия, находящиеся во внешнем растворе, образуют со всеми рассматриваемыми анионами легко диссоциирующие в водных растворах соединения, и по всей видимости, не могут вносить значительный вклад в кинетику отслаивания. Тогда как, ионы железа(II) образующиеся в формируемой на поверхности границы субстат/покрытие “ячейке отслаивания”, способны к взаимодействию с подвижными анионами микрорезервуара, роль которого выполняет введенный анионит. Свойства солей, образуемых железом(II) и изучаемыми анионами (табл. 2), в совокупности с механизмом неподавляемого отслаивания цитируемого нами ранее, на наш взгляд, объясняют получаемые результаты.
Таблица 2.
Значения растворимостей1, 2 в воде субфаз соответствующих анионов в изучаемых системах образующихся на границе сталь-покрытие
Субфаза | I группа | ОН– | II группа | III группа | |||||
---|---|---|---|---|---|---|---|---|---|
FeCl2 | Fe(NO3)2 | FeSO4 | Fe(OH)2 | FeCO3 | Fe3(PO4)2 | Fe(CrO2)2 | FeSiO3 | Fe(AlO2)2 | |
S, г/100 г Н2О | 62.6 | 82.3 | 26.3 | 5.6 × 10–6 | 5.8 × 10–5 | 3.9 × 10–7 | <0.01 | <0.01 | <0.01 |
Для сопоставления влияния природы вводимого в анионообменник активного иона и адгезионной стойкости изучаемых систем нами вычислены коэффициенты ингибирования отслаивания изучаемых систем по формуле (1):
где S0– площадь отслаивания исходного полимерного связующего, см2, Si – площадь отслаивания полимерного связующего с введенным анионообменником в соответствующей ионной форме, см2, Zi – коэффициент ингибирования отслаивания, %.Полученные величины коэффициентов представлены на рис. 4.
Рис. 4.
Механизм ингибирования катодного отслаивания покрытия при введении анионообменного микрорезервуара с активным анионом (PO4)3– (А) самодиффузия внешних гидроксид-ионов в толщу покрытия, (Б) ионный обмен в микрорезервуаре внешних гидроксид-ионов на подвижные защитные анионы и их высвобождение, (В) образование нерастворимой твердой субфазы).
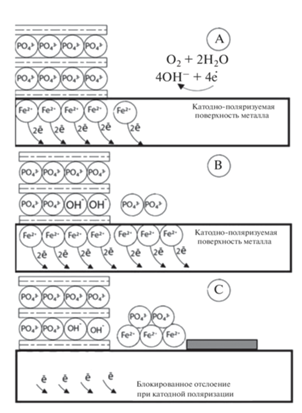
Базовый, практически значимый эффект ингибирования (средний коэффициент ингибирования отслаивания ‒ 71%) наблюдается для вводимых анионов II группы. Данные анионы образуют с катионами железа(II) нерастворимые в водном растворе соли.
Механизм ингибирования отслаивания здесь может быть представлен схемой, изображенной на рис. 5 на примере системы с фосфат-ионом, показывающей серьезное уменьшение величины отслаивания. Анионообменный резервуар в структуре покрытия начинает в результате обмена высвобождать фосфат ионы, связывающие ионы железа(II) на поверхности пластины в твердофазные соединения, тем самым обеспечивая образование на границе сталь/покрытие субфазы (нерастворимой твердой соли Fe3(PO4)2 (уравнения (2), (3)), блокирующей негативный массообмен и дополнительно защищающую металлическую поверхность.
(2)
$\begin{gathered} \left( {{\text{AB - }}17{\kern 1pt} - {\kern 1pt} {\text{PO}}_{4}^{{3 - }}} \right){\text{solid\;phase}} + 3{\text{O}}{{{\text{H}}}^{--}}{\text{\;liquid}} \to \\ \to ({\text{AB - }}17{\kern 1pt} - {\kern 1pt} {\text{O}}{{{\text{H}}}^{--}}){\text{\;solid\;phase}} + {\text{PO}}_{4}^{{3 - }}{\text{\;liquid,}} \\ \end{gathered} $(3)
${\text{\;}}2{\text{PO}}_{4}^{{3 - }} + 3{\text{F}}{{{\text{e}}}^{{2 + }}} \to {\text{\;F}}{{{\text{e}}}_{3}}{{\left( {{\text{P}}{{{\text{O}}}_{4}}} \right)}_{2}}{\text{solid\;phase}}{\text{.}}$Для систем группы III, показывающих наибольшее ингибирование отслаивания, содержащих силикат и тетрагидроксоалюминат анионы, возможно образование дополнительной устойчивой субфазы, вследствие гидролиза соединений, образующихся в результате взаимодействия высвобождающегося из покрытия аниона и катиона железа стальной пластины. Например, силикат ион в результате частичного взаимодействия во внешней агрессивной среде гидролизуется с образованием в виде дополнительной нерастворимой фазы диоксида кремния, что как видно дополнительно стабилизирует адгезию системы.
Анионы систем группы I не образуют малорастворимые или нерастворимые соединения в условиях катодной поляризации, однако при этом наблюдается эффект ингибирования отслаивания (ZI = 29%). По всей видимости, здесь происходит буферизация агрессивной щелочи в объеме вводимого анионита, при ионном обмене гидроксид-ионов на высвобождающиеся подвижные соответствующие противоионы из фазы АВ-17-8. Таким образом, сокращается подвод щелочи к поверхности “ячейки отслаивания” и скорость разрушения адгезионных связей уменьшается.
Для системы, содержащей анионит в гидроксо-форме наблюдается промотирование отслоения, несмотря на возможное образование нерастворимого гидроксида железа. Этот факт можно объяснить кинетическими явлениями. Вследствие роста ионной проницаемости системы здесь происходит увеличение концентрации щелочи в приповерхностном пространстве. При этом реакция образования гидроксида железа лимитируется скоростью образования ионов железа(II) в анодной зоне, а реакции деструкции адгезионных связей скоростью подвода щелочи в зону реакции. Здесь скорость подвода щелочи намного превышает таковую для скорости образования субфазы, что и является причиной ускорения разрушения адгезии покрытия.
Наблюдаемые эффекты ингибирования отслаивания, при введении в полимерное связующее анионита в соответствующих ионных формах, имеют хороший практический потенциал в противокоррозионной защите, в том числе, и для катодно-поляризуемых сооружений, включая магистральные нефте- и газопроводы.
На рис. 6 приведены фотоснимки битумно-полимерных покрытий, на которых показано ингибирование отслоения системы с введенным силикат-ионом. Ингибирование отслоения для данной системы относительно исходной, не содержащей активного наполнителя, составляет порядка 93%. При этом практически значимой величиной ингибирования отслоения можно считать коэффициент в 70–75%. Так, например, в работе [12] при испытаниях полимерной системы, содержащей катионит в магний(II) форме в камере солевого тумана показано, что при коэффициенте ингибирования отслоения в 70–75% наблюдается повышение адгезионной стойкости минимум в 2 раза, что существенно продлевает ресурс защитного покрытия.
ВЫВОДЫ
При введении в битумное связующее сильноосновного анионита с противоионами, образующими нерастворимые или малорастворимые соединения с ионами железа, наблюдается повышение адгезионной устойчивости получаемых композитов, при этом на степень ингибирования отслоения получаемых систем влияет природа аниона, введенного с анионообменником. Образование в разной степени нерастворимых соединений на границе “субстрат–покрытие”, блокирующих негативный массообмен и подавляющих образование “ячейки отслаивания”, дополнительно защищает металлическую поверхность в условиях катодной поляризации и может существенно продлить защитный ресурс противокоррозионного покрытия.
Таким образом, внедрение в практику противокоррозионной защиты покрытий, содержащих ионообменник (например, сильноосновный анионит АВ-17-8 в силикатной форме) может позволить существенно увеличить долговечность адгезионной связи с металлической поверхностью, повысить совместимость средств пассивной защиты (полимерных покрытий) со средствами электрохимзащиты и увеличить эффективность противокоррозионной защиты металлических конструкций, находящихся под активной катодной защитой.
Список литературы
Panyushkin V., Petrov N., Sokolov M., Bukov N. Highly Efficient Hybrid Protective Materials for Technically Complicated Systems in Natural Aggressive Conditions. In: Martínez L., Kharissova O., Kharisov B. (eds) Handbook of Ecomaterials. Springer, Cham, 2019, p. 3287–3346. https://doi.org/10.1007/978-3-319-68255-6_58
Scantlebury D. The dynamic nature of underfilm corrosion // Corrosion Science. 1993. V. 35. Iss. 5–8. P. 1363–1366.
Schneider O., Kelly R. Localised coating failure of epoxy coated aluminium alloy 2024-T3 in 0.5 M NaCL solutions: Comparison of conventional electrochemical techniques and microelectrochemical methods // Corrosion Science. 2007. V. 49. Iss. 2. P. 594–619. https://doi.org/10.1179/147842203767789195
Jenkins A.T.A., Armstrong R.D. The breakdown in the barrier properties of organic coatings due to filiform corrosion // Corrosion Science. 1996. V. 38. Iss. 7. P. 1147–1157.
Черезова Е.А., Мукменева Н.А., Архиреев В.П. Старение и стабилизация полимеров. Казань: Казанский национальный исследовательский технический университет, 2012. 140 с.
Momber A.W., Plagemann P., Stenzel V. The adhesion of corrosion protection coating systems for offshore wind power constructions after three years under offshore exposure // Int. J. Adhes. Adhes. 2016. V. 65. P. 96–101.
Ткаченко В.Н. Электрохимическая защита трубопроводных сетей. М.: Стройиздат, 2004. 320 с.
Cherkasov N.M., Gladkykh I.F., Filimonov V.A., Sergeyev V.I. The experience of asmol insulating coverings for main pipeline repairing // Oil and Gas Business. 2010. № 1. P. 1–9.
Min Xu, C.N. Catherine Lam, Dennis Wong, Edouard Asselin. Evaluation of the cathodic disbondment resistance of pipeline coatings // Progress in Organic Coatings. 2020. V. 146. Article 105728. https://doi.org/10.1016/j.porgcoat.2020.105728
Williams G., McMurray H.N., Loveridge M.J. Inhibition of corrosion-driven organic coating disbondment on galvanised steel by smart release group II and Zn(II)-exchanged bentonite pigments // Electrochimica Acta. 2010. V. 55. P. 1740–1748. https://doi.org/10.1016/j.electacta.2009.10.059
Petrov N.N., Koval’ T.V., Shel’deshov N.V., Bukov N.N. The effect of a counterion in a protective moisture-sensitive epoxy–polyelectrolyte/epoxy–carbon sandwich system // Protection of Metals and Physical Chemistry of Surfaces. 2017. V. 53. № 1. P. 133–138. https://doi.org/10.1134/S2070205117010154
Петров Н.Н. и др. Патент РФ № 2666917, 2018.
Nguyen, T., Hubbard, J.B., McFadden, G.B. Mathematical Model for the Cathodic Blistering of Organic Coatings on Steel Immersed in Electrolytes // The J. Coatings Technology. 1991. V. 63. P. 43–52.
Mahdavi Fariba, Forsyth Maria, Tan Mike Y.J. Techniques for testing and monitoring the cathodic disbondment of organic coatings: An overview of major obstacles and innovations: Review // Prog. Org. Coat. 2017. V. 105. P. 163–175.
Petrov N.N., Alovyagina A.S., Mikheev M.N., Bukov N.N., Panyushkin V.T. The Influence of the Ionic Form of Input Diatomite on the Cathodic Disbondment of Bitumen–Polymer Coatings // Protection of Metals and Physical Chemistry of Surfaces. 2020. V. 56. № 3. P. 603–608. https://doi.org/10.1134/s2070205120030272
Self-healing properties of new surface treatments / Edited by L. Fedrizzi, W. Fürbeth, F. Montemor.
Frankfurt: European Federation of Corrosion and The Institute of Materials by Maney Publishing, 2011. P. 20–26.
Дополнительные материалы отсутствуют.
Инструменты
Физикохимия поверхности и защита материалов