Физикохимия поверхности и защита материалов, 2023, T. 59, № 1, стр. 45-53
Структура и свойства износостойких покрытий Ti–C–Ni–Al, полученных методом HIPIMS
М. А. Засыпкин a, А. Д. Сытченко a, *, Ф. В. Кирюханцев-Корнеев a
a Национальный исследовательский технологический университет “МИСиС”
119049 Москва, Ленинский проспект, 4с1, Россия
* E-mail: alina-sytchenko@yandex.ru
Поступила в редакцию 01.06.2022
После доработки 08.06.2022
Принята к публикации 15.06.2022
- EDN: PUAKGS
- DOI: 10.31857/S0044185622700048
Аннотация
Проведены испытания покрытий, полученных методом высокомощного импульсного магнетронного распыления (HIPIMS) c использованием мишени 64% Ti–16% C–14% Ni–6% Al (42.5 ат. % Ti, 42.5 ат. % C, 7.5 ат. % Ni, 7.5 ат. % Al). Микроструктуру и состав покрытий изучали с помощью сканирующей электронной микроскопии, оптической эмиссионной спектроскопии тлеющего разряда и рентгенофазового анализа. Покрытия были исследованы с точки зрения их твердости, модуля упругости, упругого восстановления, стойкости к упругой деформации разрушения, сопротивления пластической деформации, коэффициента трения и износостойкости при трении-скольжения, стойкости к ударно-динамическому нагружению, а также жаростойкости. Были проведены натурные испытания покрытий на режущем инструменте. Проведено сравнение свойств покрытий, полученных на постоянном токе и при высокомощном импульсном режиме. Результаты показали, что покрытия Ti–C–Ni–Al обладали плотной однородной структурой, характеризовались твердостью 12–26 ГПа, модулем упругости 143–194 ГПа, упругим восстановлением 66–90%, низким коэффициентом трения 0.24–0.4, а также высокой жаростойкостью при 800°С. Покрытие, осажденное по оптимальному режиму, подтвердило высокую практическую эффективность в ходе натурных испытаний, снизив износ режущего инструмента на ~25%.
ВВЕДЕНИЕ
Избыточное трение и износ режущего инструмента ведут к снижению производительности металлорежущего оборудования и влекут за собой финансовые убытки, поэтому разработка новых видов эффективных износостойких покрытий является важной задачей в области инженерии поверхностей. Металлические покрытия отличаются высокой пластичностью, трещиностойкостью и прочностью, но их показатели твердости ниже, чем у керамических материалов. Керамические покрытия обладают высокой твердостью, износостойкостью стойкостью к окислению и коррозии, но также и высокой хрупкостью, что ограничивает их область применения для нагруженных механизмов. Преимущества обоих классов материалов могут быть скомбинированы в композитных металлокерамических покрытиях.
Широкое распространение в промышленности получили покрытия на основе систем Ti–C, Ti–N, Ti–C–N [1]. Карбид титана Ti–C сочетает в себе высокие твердость (до 27 ГПа), прочность при высоких температурах и износостойкость [2, 3]. Введение азота в покрытия Ti–C положительно влияет на жаро- и коррозионную стойкость [4]. Покрытия в системе Ti–C–Fe сочетают в себе высокую износостойкость карбида титана и низкую стоимость железа. Эти покрытия отличаются большей пластичностью и меньшей твердостью (9 ГПа) [5]. При добавлении алюминия в состав покрытия Ti–C, начиная с определенной его критической концентрации, резко возрастает коррозионная стойкость, что обусловлено образованием тонкой оксидной пленки на поверхности покрытия [6]. В то же время исследования покрытий на основе Ti–C–Al показали, что увеличение содержания алюминия отрицательно сказывается на твердости и модуле Юнга, что связано с падением уровня внутренних напряжений [7]. Также применяются покрытия на основе Ti–C–Ni [8, 9]. Нанокомпозитные покрытия на основе Ti–C–Ni, полученные методами магнетронного и катодного распыления, имеют значения твердости на уровне 27 ГПа, низкий коэффициента трения 0.20 и высокую термическую стабильность при температурах до 900°C [9]. Для совмещения положительных характеристик покрытий Ti–C–Al и Ti–C–Ni ранее нами была разработана и исследована система Ti–C–Ni–Al [10, 11]. Покрытия данной системы сочетают в себе высокие механические характеристики (твердость 29 ГПа) и стойкость к окислению при температуре до 800°С.
Металлокерамические покрытия на основе системы Ti–C–Ni обычно получают такими методами, как электродуговая наплавка [12], вакуумно-плазменное напыление [13], высокоскоростное газопламенное напыление [14], электроискровое легирование [10], а также лазерная наплавка [15] и магнетронное распыление постоянного тока (DCMS) [9, 16]. К основным преимуществам метода магнетронного распыления относится возможность нанесения покрытия необходимого состава на подложки из разных материалов, в число которых входят металлы и их сплавы, композитные материалы и керамики, полимеры и волокнистые материалы [17, 18]. Осаждение покрытий методом магнетронного распыления не вносит изменений в рельеф поверхности подложки и ее шероховатость [16]. Кроме того, покрытия, полученные этим методом, отличаются низкой концентрацией дефектов и плотной однородной структурой с равномерным химическим составом по всей толщине [19]. Также важным преимуществом магнетронного распыления является невысокая температура процесса, позволяющая наносить покрытия на материалы, не обладающие высокой термостойкостью [20]. В частности, это имеет значение для нанесения покрытий на инструменты из закаленных быстрорежущих сталей, избыточный нагрев которых приводит к их отпуску и последующему снижению твердости. Главным недостатком метода DCMS является низкая адгезионная прочность получаемых покрытий. Высокая степень адгезии может быть достигнута при помощи увеличения степени ионизации атомов в потоке распыляемого вещества с помощью высокомощного импульсного магнетронного распыления (HIPIMS) [21, 22]. Технология HIPIMS основана на применении коротких импульсов высокой мощности для распыления мишени, что значительно увеличивает плотность плазмы в камере магнетрона (до 1019 м−3) и степень ионизации распыляемого материала [23]. Увеличение этих параметров, в свою очередь, приводит к росту плотности и однородности покрытия [24].
Целью настоящей работы являлось исследование структуры и свойств покрытий Ti–C–Ni–Al, полученных методом HIPIMS при варьировании мощности, определение наиболее оптимального режима осаждения, а также проведение сравнительных натурных испытаний режущего инструмента с покрытием и без него.
МЕТОДИКА ЭКСПЕРИМЕНТА
Мишень для магнетронного напыления была получена методом СВС-компактирования. Мишень 64% Ti–16% C–14% Ni–6% Al (42.5 ат. % Ti, 42.5 ат. % C, 7.5 ат. % Ni, 7.5 ат. % Al) была вырезана из заготовки при помощи аппарата электроэрозионной резки. В качестве подложек для определения структуры покрытия использовались кремниевые пластины. Для исследования трибологических свойств покрытий использовались цилиндрические подложки из твердого сплава марки ВК6-М. Для исследования жаростойкости покрытий в качестве подложек использовались диски из никелевого сплава ХН65ВМТЮ. Все подложки перед осаждением покрытий были отполированы и очищены при помощи ультразвукового диспергатора УЗДН-2Т.
Покрытия были получены методом высокомощного импульсного магнетронного распыления HIPIMS в атмосфере чистого Ar с использованием вакуумной установки УВН-2М, принципиальная схема которой показана в работе [25]. Общее давление поддерживалось на уровне 0.2 Па. Длительность импульсов составляла 200 мкс, частота – 150 Гц, пиковая мощность зависела от режима осаждения и составляла от 60 до 120 кВт (табл. 1). Длительность цикла напыления составляла 40 мин. Перед нанесением покрытия подложки прошли дополнительную очистку в вакуумной камере ионами Ar+ со средней энергией ~2 кэВ в течение 20 мин с использованием источника ионов щелевого типа. Расстояния от мишени и источника ионов до подложки составляли 9 и 13 см соответственно.
Таблица 1.
Режимы осаждения покрытий
Параметр | Образец | ||
---|---|---|---|
1 | 2 | 3 | |
DC U, В | 1000 | 1000 | 1000 |
DC I, А | 1.5 | 2.5 | 3.5 |
ν, Гц | 150 | 150 | 150 |
τ, мкс | 200 | 200 | 200 |
Iпик, А | 100 | 200 | 157 |
Pпик, кВт | 60 | 90 | 120 |
Микроструктуру покрытий исследовали методом сканирующей электронной микроскопии (СЭМ) с использованием микроскопа Hitachi S-3400N, оснащенного спектрометром Thermo Scientific Noran 7. Фазовый состав определялся с помощью рентгеновского дифрактометра D8 Advance (Bruker) с монохроматическим излучением CuKα в диапазоне 2θ = 20°–80° в стандартной геометрии Брэгга–Брентано. Профили распределения элементов по глубине покрытий были получены методом оптической эмиссионной спектроскопии тлеющего разряда (ОЭСТР) с использованием прибора PROFILER 2 (Horiba Jobin Yvon). Покрытия были охарактеризованы с точки зрения их твердости, модуля Юнга и упругого восстановления с помощью нанотвердомера (CSM Instruments), оснащенного наконечником с алмазным индентором Берковича, при приложенной нагрузке 8 мН. Твердость и модуль Юнга были рассчитаны по методу Оливера–Фарра. Для оценки трибологических характеристик покрытий использовалась машина трения Tribometer (CSM Instruments). В качестве контртела использовался шарик диаметром 6 мм из стали 440С. Линейная скорость составляла 10 см/с, нормальная нагрузка – 1 Н. Стойкость к циклическому ударно-динамическому воздействию покрытий была изучена с помощью пневматического импакт-тестера (Cemecon). Образцы подвергались ударам с постоянной частотой 50 Гц в течение 105 циклов с использованием шарика из твердого сплава диаметром 5 мм. Нагрузка при этом составляла 500 Н. Для исследования морфологии дорожек износа, отпечатков после ударно-динамических и абразивных испытаний использовались оптический профилометр WYKO-NT1100 и оптический микроскоп Axiovert. Стойкость покрытий к окислению определялась при комнатной влажности (<30%). Образцы загружались в предварительно нагретую печь (SNOL 7.2/1200 (UMEGA)) и отжигались на воздухе при температурах 500, 600, 700 и 800°C с изотермической выдержкой в течение 1 часа при каждой температуре. После термической обработки образцы охлаждались на воздухе со средней скоростью 10°C/мин, после чего исследовались методами СЭМ и ОЭСТР.
Для проведения натурных испытаний покрытие было нанесено на сверло из стали Р6М5 диаметром 8.5 мм. Во время нанесения покрытия инструмент был закреплен во вращающемся патроне под углом 45° к плоскости магнетрона. В ходе испытаний проводилось сверление образца из отожженной стали У8А в сверлильном станке при 500 об./мин с измерением усилия подачи, необходимого для эффективного сверления. Изменение соответствующего усилия в зависимости от глубины сверления характеризовало износ режущей кромки.
РЕЗУЛЬТАТЫ И ИХ ОБСУЖДЕНИЕ
На рис. 1 представлено характерное изображение поперечного излома покрытий. Видно, что покрытия характеризуются плотной однородной структурой и отсутствием столбчатых зерен. Отметим, что наличие столбчатой структуры, как правило, неблагоприятно влияет на механические свойства покрытий, а также на их жаростойкость из-за интенсивной диффузии кислорода от поверхности вглубь материала по границам столбчатых зерен [26].
Согласно полученным элементным профилям (рис. 2), основные элементы были равномерно распределены по толщине покрытий. Толщины покрытий 1, 2 и 3, согласно данным ОЭСТР, составляли 1.3, 2.2, и 1.0 мкм соответственно. Скорость роста покрытия 1 составляла 32 нм/мин, покрытия 2 – 55 нм/мин, покрытия 3 – 25 нм/мин. Минимальная скорость роста покрытия 3 может быть связана с максимальной пиковой мощностью, которая приводит к увеличению скорости ионизации и плотности плазмы, при этом абсолютное количество ионов, не достигающих подложки, увеличивается [27]. Таким образом, максимальная скорость роста достигается при оптимальном значении пиковой мощности 90 кВт.
Усредненные по глубине значения концентраций элементов представлены в табл. 2. В составе покрытия 1 наблюдается максимальное содержание кислорода (30 ат. % против 17 ат. % для покрытия 2 и 20 ат. % для покрытия 3) и минимальное содержание углерода (25 ат. % против 43 ат. % для покрытия 2 и 39 ат. % для покрытия 3). Высокая концентрация кислорода, а также присутствие азота в составе покрытий могут быть связаны с проникновением этих газов из состава защитной среды вследствие низкой скорости осаждения в режиме HIPIMS [11]. Наименьшее содержание кислорода наблюдается для покрытия 2, обладающего максимальной скоростью роста 55 нм/мин. Соотношение титана к углероду для покрытия 1 близко к стехиометрическому Ti : C = 1 : 1 (табл. 2). Концентрации никеля и алюминия были максимальными и составили 7 и 7 ат. % соответственно. В случае покрытия 2 наблюдается отклонение от стехиометрического состава Ti : C = = 1 : 1.8, что может положительно влиять на механические свойства [5, 18]. Концентрация Ni и Al составляет 6 и 5 ат. % соответственно. Для покрытия 3 соотношение Ti : C = 1 : 1.6. Содержание Ni и Al составляет 7 и 4 ат. % соответственно.
Таблица 2.
Элементный состав покрытий до и после отжигов
Элемент, ат. % | Температура отжига, °C | ||||||||||||||
---|---|---|---|---|---|---|---|---|---|---|---|---|---|---|---|
Покрытие 1 | Покрытие 2 | Покрытие 3 | |||||||||||||
Исх. | 500 | 600 | 700 | 800 | Исх. | 500 | 600 | 700 | 800 | Исх. | 500 | 600 | 700 | 800 | |
Ti | 25 | 28 | 24 | 26 | 35 | 24 | 24 | 25 | 24 | – | 25 | 22 | 28 | 16 | – |
C | 25 | 27 | 27 | 26 | 18 | 43 | 44 | 43 | 4 | – | 39 | 38 | 3 | 19 | – |
Ni | 7 | 9 | 8 | 10 | 16 | 6 | 7 | 6 | 10 | – | 7 | 7 | 8 | 6 | – |
Al | 7 | 7 | 7 | 4 | 7 | 5 | 6 | 4 | 6 | – | 4 | 4 | 4 | 4 | – |
O | 30 | 26 | 30 | 30 | 17 | 17 | 16 | 18 | 52 | – | 20 | 22 | 55 | 52 | – |
N | 6 | 3 | 4 | 4 | 7 | 5 | 4 | 4 | 4 | – | 5 | 7 | 2 | 3 | – |
На рентгенограмме покрытия 1 (рис. 3) наблюдается пик низкой интенсивности в положении 36°, соответствующий фазе карбида титана (PDF 89-3828). Уширенный пик в положении 2ϴ = 41°–46°, вероятно, обусловлен наложением фаз TiC (42°) и α-Al2O3 (43.5°) (PDF 75-1865). Пик высокой интенсивности, наблюдаемый в диапазоне = 54°–57°, может быть связан с перекрытием фаз TiO2 (54°, 56.5°) (PDF 86-0147) и NiAl (55°) (PDF 65-0420) [28]. Широкий пик в диапазоне 2ϴ = 60°–64° соответствует фазам TiC (61°) и TiO2 (62.5°). Отметим, что оксидные и интерметаллидные фазы выявляются исключительно на рентгенограмме покрытия 1, что может быть связано с максимальным содержанием кислорода, никеля и алюминия в его составе. На рентгенограмме покрытия 2 наблюдаются пики в положениях 36°, 42° и 61°, соответствующие ГЦК-фазе TiC (PDF 89-3828). Рентгенограмма покрытия 3 аналогична рентгенограмме покрытия 2, и отличается от нее пониженной интенсивностью пиков TiC в положениях 36° и 42°, и отсутствием пика в положении 61°. Такой эффект может быть связан с минимальной толщиной покрытия 3. Размер зерна TiC, определенный при помощи формулы Шеррера при индексе интерференции (111), составляет: 3.5 нм для покрытия 1, 3 нм для покрытия 2 и 3.5 нм для покрытия 3. Параметр решетки а покрытия 1 составляет 0.428 нм, покрытия 2 – 0.432 нм, покрытия 3 – 0.431 нм. Снижение параметра а в случае покрытия 1 может быть связано с частичным растворением кислорода в решетке TiC и отклонением от стехиометрического состава, а также с высоким уровнем остаточных растягивающих напряжений [10]. Параметр а для покрытий 2 и 3 близок к стандартному параметру решетки TiC 0.432 нм.
Твердость (H), модуль упругости (E) и упругое восстановление (W), а также стойкость к упругой деформации разрушения (H/E) и сопротивление пластической деформации (H3/E2), определенные для покрытий, предоставлены в табл. 3. Покрытие 1, осажденное при минимальной пиковой мощности 60 кВт, обладало минимальными твердостью 12 ГПа, упругим восстановлением 66%, модулем упругости 143 ГПа и параметрами H/E = = 0.084 и H3/E2 = 0.085 ГПа. Покрытие 2 характеризовалось максимальными значениями Н = 26 ГПа, W = 90%, E = 194 ГПа, H/E = 0.134 и H3/E2 = 0.467 ГПа, что может быть связано с увеличенным содержанием углерода [5]. Также высокая скорость осаждения и большая толщина покрытия 2 способствует возникновению высоких внутренних напряжений, что в свою очередь положительно влияет на твердость покрытия. Увеличение пиковой мощности с 90 до 120 кВт привело к снижению Н покрытия 3 в 1.6 раз, W и Е в 1.2 раза, H/E в 1.4 раза и H3/E2 в 3.2 раза. Таким образом, наблюдалась экстремальная зависимость механических характеристик от пиковой мощности, при этом максимум достигался при Рпик = 90 кВт. Подобные значения твердости (27 ГПа) наблюдались в покрытиях Ti–Ni–C [15] и Ti–Al–C [29]. Отметим, что покрытие Ti–C–Ni–Al, полученное методом HIPIMS при Рпик = 90 кВт, характеризуется экстремально высокими упругопластическими свойствами W = 90%, H/E = 0.134 и H3/E2 = 0.467 ГПа, по сравнению с значениями W = 74%, H/E = 0.106 и H3/E2 = 0.384 ГПа для покрытия аналогичного состава, полученного в режиме DCMS [11].
Таблица 3.
Механические и трибологические свойства покрытий
Параметр | 1 | 2 | 3 |
---|---|---|---|
Механические свойства | |||
H, ГПа | 12 | 26 | 16 |
W, % | 66 | 90 | 77 |
E, ГПа | 143 | 194 | 167 |
H/E | 0.084 | 0.134 | 0.096 |
H3/E2, ГПа | 0.085 | 0.467 | 0.147 |
Трибологические свойства | |||
Vw, мм3/(Н м) | 4.0 × 10–5 | 1.0 × 10–5 | 4.0 × 10–5 |
μ | 0.4 | 0.24 | 0.28 |
Зависимости коэффициента трения (µ) от дистанции, пройденной контртелом по поверхности покрытий, представлены на рис. 4. Предварительные испытания с применением контртел твердого сплава WC–Co, стали 100Cr6, оксида алюминия и стали 440С показали, что минимальный коэффициент трения (0.2) покрытия 2 наблюдался в контакте с шариком 440С (рис. 4а). Дальнейшие испытания для всех покрытий проводились с использованием контртела из стали 440С. Средние значения коэффициента трения представлены в табл. 3. Покрытие 1, полученное при минимальной Pпик = 60 кВт, обладает максимальным коэффициентом трения 0.4 на дистанции 0–250 м. На участке 250–450 м коэффициент трения плавно возрастает до ~1.0. Минимальным коэффициентом трения 0.24 характеризуется покрытие 2, полученное при пиковой мощной мощности 90 кВт. Образец 3 характеризовался µ = = 0.28. Отметим, что покрытие Ti–C–Ni–Al, полученное при пиковой мощной мощности 90 кВт, обладает более низким коэффициентом трения, по сравнению с значениями 0.3 и 0.25 для покрытий Ti–C–Ni [30] и Ti–C–Al [31] соответственно.
Рис. 4.
Значения коэффициентов трения, полученные в ходе испытаний с разными контртелами (а) и на разных покрытиях с контртелом из 440C (б).
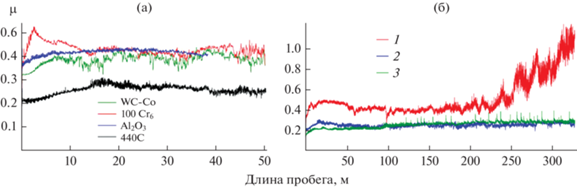
Трехмерные профили канавок износа представлены на рис. 5, зона износа контртела на рис. 6. Дорожки износа покрытий 1 и 2 были равномерными. Глубина дорожки износа покрытия 1 составила ~1.2 мкм при толщине покрытия 1.2 мкм, что говорит о полном износе покрытия в процессе трения. Покрытие 2, напротив, показало высокую износостойкость, канавка износа имела наименьшую глубину (0.3 мкм). Покрытие 3 изнашивалось неравномерно, в ходе испытаний наблюдалось частичное отслоение покрытия. При этом глубина дорожки износа была сравнительно низкой и составила 0.4 мкм. Отслоение покрытия 3 может быть связано с низкой адгезией к поверхности. Приведенный износ Vw покрытий представлен в табл. 3. Лучшую износостойкость продемонстрировало покрытие 2 при значении приведенного износа 1.0 × 10–5 мм3/(Н м) против 4.0 × 10–5 мм3/(Н м) для покрытий 1 и 3.
Трехмерные профили кратеров после ударно-динамических испытаний представлены на рис. 7. Для покрытий 1 и 2 отслоения от подложки и растрескивания не наблюдается, объемы кратеров при этом составляют V = 3.9 × 10–4 и 1.4 × 10–4 мм3 соответственно. В ходе ударно-динамических испытаний покрытия 3 наблюдаются участки отслоения, при этом V = 4.8 × 10–4 мм3.
Таким образом, можно сделать вывод, что низким коэффициентом трения, лучшими износостойкостью и стойкостью к ударно-динамическому нагружению обладает покрытие, полученное при оптимальной пиковой мощности 90 кВт.
Элементные профили покрытий после отжига при температурах 500–800°С представлены на рис. 8, усредненная концентрация элементов в неокисленном слое – в табл. 2. Значения толщины окисленного и неокисленного слоя покрытий после проведения испытаний на жаростойкость приведены на рис. 9. Все покрытия успешно сопротивлялись окислению при температуре 500°С, толщина оксидного слоя всех образцов не превышала 0.3 мкм. После отжига при 600°С толщина оксидного слоя покрытия 1 составила 0.52 мкм. Минимальная толщина оксида 0.3 мкм наблюдалась для покрытия 2, в то время как покрытие 3 окислилось на глубину 0.7 мкм. При повышении температуры отжига до 700°С покрытие 1 характеризуется минимальной толщиной оксидного слоя 0.78 мкм, в то время как покрытия 2 и 3 окислились на глубину 1.9 и 1.6 мкм соответственно. Было установлено, что жаростойкость покрытий при 800°С возрастает в ряду покрытие 3 → покрытие 2 → покрытие 1. Максимальная жаростойкость покрытия 1 может быть связана с высоким содержанием в его составе кислорода, никеля и алюминия, создающих защитный оксидный слой. Также высокая жаростойкость может быть объяснена низким содержанием углерода в составе покрытия 1. Стоит отметить, что все покрытия Ti–C–Ni–Al, полученные методом HIPIMS, обладают хорошей жаростойкость вплоть до 800°С, в то время как покрытие, осажденное методом DCMS, полностью окисляется при температуре 700°С [11].
Исходя из полученных данных, из-за более высоких механических и трибологических характеристик, а также отличной жаростойкости, для проведения натурных испытаний на режущем инструменте было выбрано покрытие 2.
Фотографии режущей кромки испытуемого инструмента на разных этапах натурных испытаний предоставлены на рис. 10. Зависимость усилия подачи пиноли для эффективного сверления от глубины сверления представлена на рис. 11. На непокрытом сверле наблюдалось значительное налипание стружки на режущую кромку и выкрашивание кромки после глубины сверления 100 мм. Покрытый режущий инструмент продемонстрировал значительно меньший износ и меньшее налипание продуктов сверления. Усилие сверления возрастало пропорционально износу режущих кромок для обоих испытываемых сверл, но его значение для сверла с покрытием было меньше на 20–25% для каждой контрольной точки.
ВЫВОДЫ
В работе были исследованы покрытия системы Ti–C–Ni–Al, полученные методом HIPIMS при разной пиковой мощности 60, 90 и 120 кВт. Исследование методом СЭМ продемонстрировало плотную однородную структуру для всех покрытий. Скорость роста покрытий снижалась с ростом пиковой мощности. Данные рентгенофазового анализа позволили обнаружить соединение TiC в составах всех покрытий, а также интерметаллид NiAl и оксиды титана и алюминия в составе покрытия, полученного при пиковой мощности 60 кВт. Покрытие, нанесенное при Pпик = 60 кВт, также отличалось высоким содержанием кислорода (30 ат. %), низким содержанием углерода (25 ат. %). Зависимость механических и трибологических характеристик от пиковой мощности носила экстремальный характер, максимальные значения были зафиксированы для покрытия, полученного при Pпик = 90 кВт: Н = 26 ГПа, W = 90%, E = 194 ГПа, H/E = 0.134 и H 3/E2 = 0.467 ГПа, μ = = 0.24, Vw = 1.0 × 10–5 мм3/(Н м). Лучшей жаростойкостью обладало покрытие, осажденное при минимальной пиковой мощности 60 кВт и содержащее максимальную концентрацию кислорода. Натурные испытания подтвердили эффективность покрытия, полученного по оптимальному режиму (90 кВт) в реальных рабочих условиях и его перспективность. Было зафиксировано снижение износа режущего инструмента, защищенного этим покрытием, на ~25%.
Покрытие, осажденное по оптимальному режиму HIPIMS, характеризуется более высокими упругопластическими характеристиками и жаростойкостью по сравнению с покрытием, полученным в режиме DCMS.
Исследования методом РФА проведены с использованием оборудования Центра коллективного пользования “Материаловедение и металлургия” (соглашение № 075-15-2021-696). Авторы выражают благодарность Н.В. Андрееву за помощь в проведении структурных исследований.
Список литературы
Fukui H. // SEI technical review. 2016. V. 82. P. 39–45.
Mahboobeh A., Aghdam S.R., Ahangarani A. et al. // Advanced Materials Research. 2014. M. 829. № 476.
Chen L., Wang S.Q., Zhou S.Z. et al. // International J. Refractory Metals and Hard Materials. 2008. V. 26. P. 456–460.
Akinribide O.J., Obadele B.A., Akinwamide S.O. et al. // Ceramics International. 2019. V. 45. P. 21077–21090.
Xiao M., Zhang Y., Wu Y. et al. // International J. Refractory Metals and Hard Materials. 2021. V. 101. № 105672.
Shmorgun V.G., Bogdanov A.I., Kulevich V.P. et al. // Materials Today: Proceedings. 2021. V. 38. P. 1627–1630.
Chaliyawala H.A., Gupta G., Kumar P. et al. // Surface and Coatings Technology. 2015. V. 276. P. 431–439.
Ma M., Sun W.-C., Zhang Y.-G. et al. // Materials Research. 2019. V. 22. № e20190530.
Grandin M., Nedfors N., Sundberg J. et al. // Surface and Coatings Technology. 2015. V. 276. P. 210–218.
Kiryukhantsev-Korneev Ph.V., Sheveyko A.N., Shvindina N.V. et al. // Ceramics International. 2018. V. 44. P. 7637–7646.
Kiryukhantsev-Korneev Ph.V., Sheveyko A.N., Vorotilo S.A., Levashov E.A. // Ceramics International. 2020. V. 46. P. 1775–1783.
Bao Y., Huang L., An Q. et al. // J. European Ceramic Society. 2020. V. 40. P. 4381–4395.
Krysina O.V., Ivanov Yu.F., Koval N.N. et al. // Surface and Coatings Technology, 2021. V. 416. № 127153.
Amudha A., Nagaraja H.S., Shashikala H.D. // Physica B: Condensed Matter. 2021. V. 602. № 412409.
Bolelli G., Colella A., Lusvarghi L. et al. // Wear. 2020. V. 450–451. № 203273.
Abegunde O., Akinlabi E., Oladijo P. // Materials Today: Proceedings. 2021. V. 44. P. 1221–1226.
Chen Y., Wu G., He J. // Materials Science and Engineering: C. 2015. V. 48. P. 41–47.
Singh A., Schipmann S., Mathur A. et al. // Applied Surface Science. 2017. V. 414. P. 114–123.
Abegunde O.O., Akinlabi E.T., Oladijo O.P. // Applied Surface Science. 2020. V. 520. № 146323.
Tudose I.V., Suchea M.P. // Functional Nanostructured Interfaces for Environmental and Biomedical Applications. 2019. P. 15–26.
Baghriche O., Zertal A., Ehiasarian A.P. et al. // Thin Solid Films. 2012. V. 520. P. 3567–3573.
Sytchenko A.D., Kiryukhantsev-Korneev Ph.V. // J. Phys.: Conf. Ser. 2021. V. 2064. № 012062.
Souček P., Hnilica J., Klein P. et al. // Surface and Coatings Technology. 2021. V. 423. № 127624.
Helmersson U., Lattemann M., Bohlmark J. et al. // Thin Solid Films. 2006. V. 513. P. 1–24.
Kiryukhantsev-Korneev Ph.V., Sytchenko A.D., Sviridova T.A. et al. // Surface and Coatings Technology. 2022. № 128141.
Musil J., Zeman P. // Solid State Phenomena. 2007. V. 4. P. S6–S10.
Papa F., Gerdes H., Bandorf R. et al. // Thin Solid Films. 2011. V. 520. P. 1559–1563.
Шевцова Л.И. Дис. к-та техн. наук: 05.16.09. НГТУ. 2015. 200 с.
Shtansky D.V., Kiryukhantsev-Korneev Ph.V., Sheveyko A.N. et al. // Surface and Coatings Technology. 2009. V. 203. P. 3595–3609.
André B., Lewin E., Jansson U., Wiklund U. // Wear. 2011. V. 270. P. 555–566.
Pang X., Shi L., Wang P. et al. // Surface and Coatings Technology. 2009. V. 203. P. 1537–1543.
Дополнительные материалы отсутствуют.
Инструменты
Физикохимия поверхности и защита материалов