Физикохимия поверхности и защита материалов, 2023, T. 59, № 1, стр. 87-98
Нагревание частиц с алюминиевым ядром и гидроксидной оболочкой
Н. С. Шайтура a, *, В. В. Артемов a, b, М. Н. Ларичев a
a Федеральный исследовательский центр химической физики им. Н.Н. Семенова РАН
119991 Москва, ул. Косыгина, 4, Россия
b Институт кристаллографии им. А.В. Шубникова ФНИЦ “Кристаллография и фотоника” РАН
119991 Москва, Ленинский пр., 38, Россия
* E-mail: tesh-s@yandex.ru
Поступила в редакцию 22.08.2022
После доработки 05.09.2022
Принята к публикации 12.09.2022
- EDN: CIVUCX
- DOI: 10.31857/S0044185622700103
Аннотация
Исследованы частицы с алюминиевым ядром и гидроксидной оболочкой, полученные низкотемпературным (до 100°C) окислением водой сферических алюминиевых микронных частиц. Проанализированы процессы, протекающие при нагревании этих частиц до 750°C в контролируемой газовой атмосфере. Исследован состав и количество выделяющихся газофазных продуктов, определена их природа. Рассмотрена трансформация оболочки в результате фазового перехода гидроксида алюминия в оксид. Рассмотрен механизм образования трещин в результате термического расширения ядра и оболочки при нагреве частицы. Отмечены выходы алюминия на поверхность оксидной оболочки после достижения температуры плавления алюминия. Предлагается использовать алюминий, экструдированный на поверхность, для образования связей между частицами при осуществлении 3D-печати.
1. ВВЕДЕНИЕ
Благодаря высокой химической активности поверхность алюминия, контактирующая при комнатных температураех с атмосферой, в состав которой входят кислород и/или пары воды, всегда покрыта инертной газонепроницаемой пленкой из смеси оксидов и гидроксидов алюминия толщиной до нескольких нанометров [1]. Такая пленка предотвращает дальнейшее окисление металлического ядра частицы и необходимо прилагать специальные усилия, чтобы контролируемо увеличить ее толщину. Состав и свойства оксидных пленок, покрывающих поверхность ядра, определяются условиями их формирования. Информация о параметрах, характеризующих пленки, об их эволюции при нагревании в нейтральной и в окислительной средах, и о взаимодействии с Al подложкой представляет интерес для фундаментальной и прикладной науки. Она может быть полезна, в частности, при изучении межфазовых взаимодействий оксидов с металлическим алюминием, а так же для объяснения структурных превращений, наблюдаемых в такой металл-оксидной системе, часто являющейся предметом современных исследований [2–4]. Полученные знания могут оказаться востребованными при разработке новых композиционных материалов с уникальной структурой и свойствами [5], при исследовании процесса окисления алюминиевой поверхности, в частности, низкотемпературного окисления [4], для прогнозирования поведения и определения условий эксплуатации изделий из алюминия и материалов, содержащих алюминий (сплавы, композиты), для прогнозирования поведения диспергированного алюминия при его энергетических применениях [6] и др.
Для увеличения толщины оксидной пленки, покрывающей поверхность Al частиц, может быть рекомендовано низкотемпературное (при температурах, не превышающих температуру кипения воды) окисление алюминиевой поверхности водой с последующим трансформированием образовавшихся поверхностных гидроксидов в оксиды алюминия. Процессы, протекающие при окислении водой микронных частиц алюминия, подробно изучены в [7]. Данный способ позволяет создавать на поверхности Al частиц гидроксидные покрытия контролируемой толщины, т.е. формировать композитные частицы с алюминиевым ядром и гидроксидной оболочкой (АГЧ), которые нагреванием трансформируются в Al частицы, покрытые оболочкой из оксида алюминия (АОЧ).
Полученные данным способом композитные частицы планируется использовать, как прекурсоры для создания керамо-металлических (алюмо-оксидных) композиционных материалов. Предполагается несколько вариантов их возможного применения. В частности, они могут быть использованы:
– в качестве наполнителя в дисперсно-упрочненных композитах с алюминиевой матрицей;
– для 3D печати алюмооксидных изделий методами селективного лазерного плавления (СЛП) и селективного лазерного спекания (СЛС).
В литературе описаны попытки создания алюмо-оксидных материалов с использованием АГЧ и АОЧ. В [8] предложено формировать керамические контакты между АГЧ непосредственно на стадии окисления алюминиевых частиц водой, используя последующее кальцинирование материала. В этом случае на заключительной стадии формирования материала требуется его дополнительная термическая обработка, обеспечивающая “сшивку” частиц керамическими мостиками. Однако, формование из подобного материала изделий, имеющих сложную 3D геометрию, представляется проблематичным. В работе [9] для создания подобных материалов из обсуждаемых АОЧ предлагается использовать метод СЛП. Наиболее равномерное распределение оксида и алюминия в материале удается создать, если при 3D печати плавится не только алюминий, но и оксидная оболочка АОЧ. В этом случае при выполнении ряда достаточно жестких требований к температурному режиму СЛП можно получить плотные изделия заданной сложной формы, в материале которых металл и оксиды будут равномерно перемешаны, однако полностью исключить поры, образующиеся парами испаряющегося алюминия, вряд ли представляется возможным.
На практике часто требуется формировать дисперсно-упрочненные композиты, в которых алюминиевая матрица наполнена тонкодисперсными АОЧ, оксидная оболочка которых позволяет усилить матрицу композита. В таком материале связь между АОЧ наполнителя и металлом матрицы определяется суммой двух факторов. Во-первых, за счет алюминиевых спаек, соединяющих металл матрицы и металлические ядра АОЧ через сквозные поры и трещины, образовавшиеся в оксидной оболочке при формировании как АОЧ, так и собственно композита. Во-вторых, она реализуется благодаря адгезивным силам, возникающим в местах контакта между металлом матрицы и внешней поверхностью оксидной оболочки АОЧ. При этом величиной удельной поверхности и свойствами оксидной оболочки можно управлять во время окисления поверхности алюминиевой частицы [7] в воде. Отметим, что, изменяя технологические условия формирования АГЧ, АОЧ и композита в целом, можно изменять величину каждого из этих факторов. Это дает возможность эффективно управлять свойствами формируемого материала.
Приготовленные описанным выше способом АОЧ могут быть использованы для формирования жестких 3D-каркасов, состоящих из связанных металлическим алюминием, поднявшимся на поверхность через сквозные поры и трещины оксидной оболочки при трансформации АГЧ в АОЧ путем их нагревания. Такие каркасы могут быть использованы, например, как самостоятельные конструкции в качестве катализаторов или носителей катализаторов, обеспечивая оптимальные динамические потоки газа или жидкости через занимаемый катализатором объем реактора.
Объектом исследования в настоящей работе выбраны АГЧ, полученные жидкофазным окислением дистиллированной водой микронных Al частиц порошка АСД-4. Окисление проводилось при атмосферном давлении и температурах ниже 100°С. Такой способ позволяет формировать на поверхности частиц гидроксидные покрытия различной толщины, контролируемого фазового и элементного состава. Подобные АГЧ после их трансформации в АОЧ, предлагается использовать для формирования методами СЛС и СЛП 3D деталей из алюминий-оксидных материалов, а так же применять для создания дисперсно-упрочненных композитов. Целью данной работы являлось исследование механизма процессов, протекающих во время нагревания АГЧ в инертной атмосфере аргона и в атмосфере искусственного воздуха, применяемого для трансформации гидроксидных оболочек частиц в оксидные.
2. ОПИСАНИЕ ОБЪЕКТА ИССЛЕДОВАНИЯ И ПРИМЕНЯВШИЕСЯ МЕТОДЫ ИССЛЕДОВАНИЯ
В качестве исходного реагента для получения АГЧ в работе использовался сферический микронный алюминиевый порошок АСД-4 (ТУ 48-5-226-87) со средним размером частиц около 4 мкм из Al чистоты 99.5%. На рис. 1а приведены СЭМ фотографии частиц порошка в состоянии поставки. Частицы контролировано окислялись в дистиллированной воде при температуре ниже 70°С при атмосферном давлении. Окисление частиц проводилось в специально сконструированной и изготовленной установке, подробно описанной в [10]. Степень превращения Al контролировалась по объему выделяющегося водорода. Важным аргументом в пользу выбора данного процесса окисления алюминия для получения АГЧ с заданной толщиной гидроксидной оболочки является возможность быстрой остановки процесса окисления при достижении заданной степени превращения металла. После остановки окисления и проведения сушки окисленные частицы характеризовались методами РФА и СЭМ.
Рис. 1.
СЭМ микрофотографии: (а) исходных частиц порошка АСД-4; окисленных водой частиц со степенью превращения металла: (а) 10%; (б) 20%, (в, г) 35%.
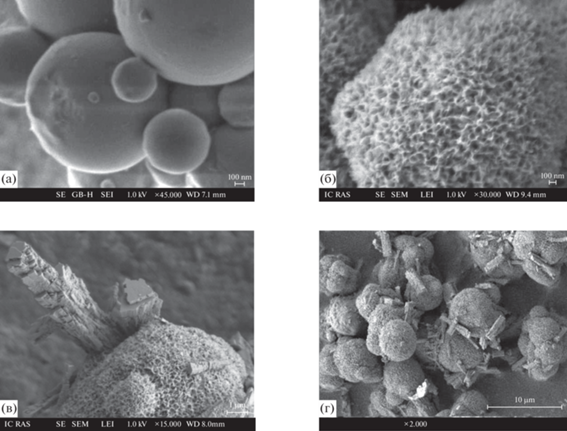
В настоящей работе исследовались два окисленных в стеклянном реакторе образца со степенью превращения алюминия 10 и 20% (рис. 1а, 1б). Это соответствует средним толщинам окисленного алюминиевого слоя 70 и 150 нм. Также был исследован образец, окисленный в стальном реакторе, со степенью превращения 35%, соответствующей толщине окисленного слоя 270 нм (рис. 1в, 1г).
Как показывает сравнительное исследование образцов методом СЭМ при степени превращения алюминия ~10–20% поверхность микронных алюминиевых частиц равномерно покрыта слоем окисленного алюминия (рис. 1б). Образующийся в виде водонасыщенного геля [7] гидроксид алюминия после высушивания принимает разветвленную структуру, называемую в научной литературе “nanowalls”. Исследование пористой структуры таких АГЧ показывает наличие пор с радиусом ~1 нм. Удельная поверхность АГЧ составляет около 60 м2/г в пересчете на общую массу частицы (металл + гидроксид) [11]. Отметим, что удельная поверхность исходных частиц алюминиевого порошка АСД-4 составляет всего (0.35–0.4) м2/г [12], что в (150–170) раз меньше измеренного значения поверхности окисленных частиц. Таким образом, использование окисления поверхности Al частиц водой позволяет многократно контролируемо увеличить их удельную поверхность. Такая возможность представляет собой важный инструмент для управления свойствами формируемых композитов.
При высоких степенях превращения алюминия (выше 30%) среди частиц обнаруживаются отдельные микронные кристаллы гидроксида алюминия (байерит). Об этом свидетельствуют данные СЭМ и РФА (рис. 1в и 1г). Такие АГЧ уже не всегда могут быть рекомендованы для изготовления изделий методами СЛС и СЛП, поскольку хаотично локализованные микронные кристаллы гидроксида алюминия будут создавать неконтролируемые, хаотично распределенные по объему материала зоны дефектов в формируемых изделиях. По этой причине толщина окисленного слоя ~200 нм, по-видимому, является предельной для микронных АГЧ в случае их использовании для 3D печати.
После низкотемпературного окисления в воде и сушки АГЧ подвергались линейному нагреву со скоростью 20°С/мин до температуры 730°С в контролируемой газовой атмосфере: инертной (Ar) и окислительной (смесь 75% Ar и 25% O2, газы марки ВЧ). Для нагрева образцов использовался прибор термического анализа STA 449 F1 Jupiter фирмы NETZSCH, оснащенный масс-спектрометром QMS Aeolos 3. Процесс нагрева АГЧ контролировался методами дифференциального термического анализа и одновременно проводился масс-спектральный контроль состава газофазных соединений, выделяющихся в окружающую среду.
Использование масс-спектрометра позволило не только определять состав выделяющихся летучих соединений и температурный режим их формирования, но и характеризовать эти соединения количественно. Для этого была проведена калибровка чувствительности масс-спектрометра к молекулам Н2, H2O, СО2, СО. В условиях (скорость и состав газовых потоков, протекающих через печь прибора STA449; размеры тигля; программа нагрева образцов), аналогичных условиям нагрева экспериментальных образцов, было изучено термическое разложение гидрида алюминия (АlН3) известной массы, которое протекает по уравнению (1):
и разложение оксалата кальция (CaC2O4·Н2О), протекающее по схеме (2)–(4) :(2)
${\text{Ca}}{{{\text{C}}}_{{\text{2}}}}{{{\text{O}}}_{{\text{4}}}} \cdot {{{\text{Н}}}_{{\text{2}}}}{\text{О}} \to {\text{Ca}}{{{\text{C}}}_{{\text{2}}}}{{{\text{O}}}_{{\text{4}}}} + {{{\text{H}}}_{{\text{2}}}}{\text{O}},$(3)
${\text{Ca}}{{{\text{C}}}_{{\text{2}}}}{{{\text{O}}}_{{\text{4}}}} \to {\text{CaC}}{{{\text{O}}}_{{\text{3}}}} + {\text{CO}},$Интегральное выделение каждого газового компонента в данном температурном диапазоне, регистрируемое масс-спектрометром с учетом поправки на его чувствительность по аргону, контролируемую в каждом опыте, ставилось в соответствие с изменением TG-кривой, регистрируемой прибором термического анализа в этом диапазоне. Отметим, что по полученным результатам чувствительность масс-спектрометра к водороду примерно в 30 раз меньше, чем к молекулам Н2О.
АОЧ, сформированные после программируемого нагрева АГЧ в контролируемой газовой среде, подвергались сравнительному исследованию методами СЭМ на приборе JSM-7401F, а также методами РФА на напорошковом рентгеновском дифрактометре Rigaku Smartlab SE. Элементный анализ поверхности образцов (EDS Elemental Analysis) выполнялся на приборе Quanta 200 3D с энергодисперсионным микроанализом EDAX Genesys. Аналогичными методами были исследованы образцы исходного порошка АСД-4 и АГЧ, полученные его окислением в воде.
3. ПОЛУЧЕННЫЕ РЕЗУЛЬТАТЫ И ИХ ОБСУЖДЕНИЕ
Во время нагревания покрывающие поверхность алюминиевых частиц оксидные оболочки претерпевают ряд превращений, обусловленных протекающими в них химическими и физическими процессами. Основными из них являются десорбция физ- и хемосорбированных поверхностью химических соединений и выделение летучих соединений в окружающую частицы атмосферу; фазовые переходы между структурами оксидов и гидроксидов, формирующих оболочки; плавление металлического ядра частицы; взаимодействие металла ядра частицы с оксидами оболочки, а также с выделяющимися летучими соединениями и компонентами атмосферы.
3.1. Процессы, протекающие при нагревании исходных алюминиевых частиц
На рис. 2 представлены термоаналитические кривые для исходных алюминиевых частиц, нагревавшихся со скоростью 20 гр/мин в окислительной атмосфере. Поведение ТГ кривой (кривая 1) показывает, что масса образца уменьшается в диапазоне температур от 120 до 430°С. При этом наиболее значительное и быстрое уменьшение массы наблюдается в температурном интервале: 250–300°С. Оно коррелирует с выделением в окружающую атмосферу молекул воды. При температурах ниже 200–220°С источником этой воды является сначала десорбция физсорбированных молекул воды, а при более высоких температурах рекомбинация –ОН групп (хемосорбированная вода), сначала парных, потом одиночных и структурных.
Рис. 2.
Нагревание исходного порошка АСД-4 в окислительной атмосфере (75% Ar + 25% O2) со скоростью 20°С/мин (синхронный термический анализ, совмещенный с масс-спектрометрическим анализом состава газовыделения образца): кривая 1 – ТГ; кривая 2 – ДТА; кривая 3 – интенсивность линии м/e = 18 (Н2О); кривая 4 – интенсивность линии м/e = 44 (СО2); кривая 5 – интенсивность линии м/e = 2 (Н2).

В диапазоне 250–300°С на кривой скорости выделения воды наблюдается ярко выраженный максимум (рис. 2, кривая 3), отвечающий фазовому переходу первого рода, во время которого гидроксид алюминия трансформируется в оксигидроксид и оксид алюминия. В этом температурном диапазоне выделение воды сопровождается образованием и выделением водорода (кривая 5). Этот водород, по-видимому, является продуктом реакции, протекающей между молекулами выделяющейся воды и металлическим алюминием ядра частицы. Оценки, сделанные с использованием описанной в разделе 2 калибровки, показывают, что регистрируемое масс-спектрометром количество (массовое) выделяющейся воды в 10–15 раз превышает количество (массовое) регистрируемого водорода.
Отметим, что факт выделения в окружающую среду водорода однозначно свидетельствует о нарушении сплошности оксидной оболочки, покрывающей частицу.
Следующий максимум выделения молекул воды, наблюдается при температуре около 580°С. В области этой температуры также происходит нарушение сплошности оксидного покрытия. Оно, с одной стороны, облегчает доступ кислорода к металлическому алюминию ядра АГЧ и при этом окисление металла приводит к выделению тепла и росту массы образца. С другой стороны, происходит выделение в окружающую частицу атмосферу газов, образующихся в объеме оболочки, растворенных в ядре частицы, а также образующихся при фазовых переходах в оксидной оболочке. Природа воды, выделение которой наблюдается при температуре 580°С в окислительной атмосфере может носить различный характер: она могла быть закапсулирована в оксидном покрытии частицы после фазового перехода при 300°С, могла образовываться в результате реакции растворенного в объеме частицы водорода с кислородом окружающей среды. В принципе, она может образоваться в результате фазового перехода в оксидной оболочке, однако, такой переход не регистрировался в настоящих опытах термоаналитическими методами. Более подробно механизм образования воды будет проанализирован в разделе 3.3 при сравнении газовыделения исходных порошков и АГЧ.
Выделение СО2 (рис. 2, кривая 4, м/е 44) наблюдается в диапазоне 130–600°С. При температурах ниже 250°С интенсивность выделения СО2, в основном, коррелирует с интенсивностью выделения физ- и хемосорбированной частицей воды и не зависит от атмосферы, в которой производится нагрев образца. Это свидетельствует, что сорбция (хемосорбция) молекул СО2 поверхностью оксида алюминия происходит с участием сорбированных молекул воды.
Максимумы газовыделения СО2, регистрируемые при температурах 330 и 440°С (рис. 2, кривая 4) также наблюдаются при нагревании образца в нейтральной атмосфере аргона, что будет обсуждаться ниже. Они не сопровождаются выделением дополнительных газофазных соединений. Это, по-видимому, свидетельствует в пользу существования поверхностных карбонатов алюминия и их разложения при данных температурах.
Максимум выделения СО2 при температуре 580°С (рис. 2, кривая 4) наблюдается не в каждом эксперименте и не наблюдается при нагревании образцов в нейтральной атмосфере. По-видимому, он связан с образованием углекислого газа при окислении кислородом труднолетучих органических загрязнений.
Газовыделение органических молекул (линии м/е 43, м/е 27) имеет малую интенсивность. Линии регистрируются на уровне шума и наблюдаются в масс-спектрах исследуемых образцов не в каждом эксперименте. Это позволяет сделать заключение, что в случае регистрации органических соединений мы имеем дело со случайными загрязнениями образца.
Отметим, что в опытах по нагреванию порошка АСД-4 в нейтральной атмосфере аргона при температурах ниже 500°С наблюдаются зависимости, аналогичные обсуждавшимся выше для атмосферы, содержащей кислород:
– при температурах ниже 250°С интенсивность выделения СО2, в основном, коррелирует с интенсивностью выделения воды для образцов 1 и 2, не содержащих кристаллов гидроксида алюминия;
– наблюдаются максимумы газовыделения м/e 44 при температурах 330 и 440°С, что, по-видимому, подтверждает гипотезу о существовании на поверхности частиц АСД-4 карбонатов алюминия;
– подтверждается вывод, что регистрация органических соединений является результатом случайных загрязнений алюминиевых частиц исследуемого образца.
Однако, в температурном интервале 550–630°С в отсутствие кислорода (окислителя), естественно, не наблюдается окисления металлического алюминия в области нарушения сплошности оксидного покрытия. Также не наблюдается выделения Н2О и Н2, а также выделения СО2 при 580°С.
3.2. Процессы, протекающие при нагревании АГЧ, полученных окислением сферических Al частиц в воде
Результаты масс-спектрометрического анализа газофазных продуктов, выделяющихся при нагревании АГЧ, показывают, что их состав аналогичен составу, наблюдавшемуся для исходных Al частиц. При этом интенсивность удельного газовыделения оказывается существенно более высокой. Это демонстрирует сравнение данных, приведенных на рис. 2 и 3, полученных для частиц АСД-4 и для частиц АГЧ с различной степенью превращения алюминия, нагревавшихся в окислительной атмосфере (75% Ar + 25% O2) до 550°С.
Рис. 3.
Нагревание АГЧ с разной степенью превращения алюминия в окислительной атмосфере (75% Ar + 25% O2) со скоростью 20°С/мин (синхронный термический анализ, совмещенный с масс-спектрометрическим анализом состава газовыделения образца): (а) ДТА кривая; (б) ТГ кривая; (в) интенсивность м/e 18 (Н2О); (г) интенсивность м/e 44 (СО2); (д) интенсивность м/e 2 (Н2). Степень превращения алюминия в образцах: 1 – 10%; 2 – 20%; 3 – 35%.
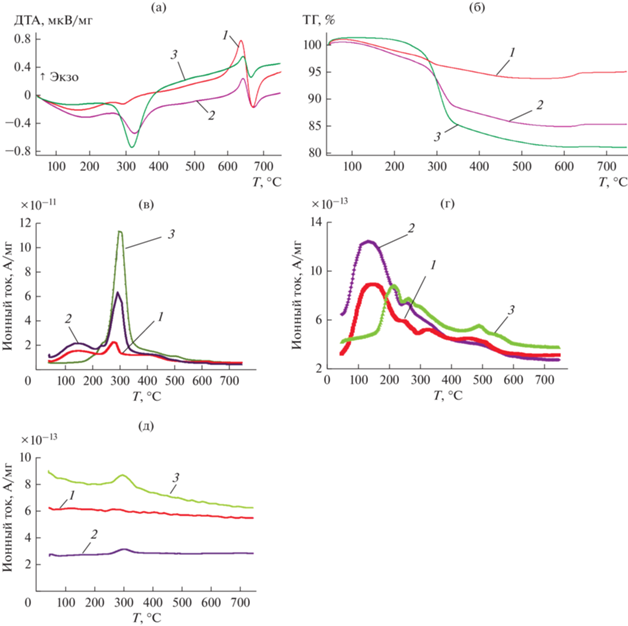
Для образцов АГЧ со степенью превращения алюминия меньше 30%, выделение воды, водорода, углекислого газа наблюдается в тех же температурных диапазонах, что и для исходных частиц (см. предыдущий раздел 3.1). Для АГЧ со степенью превращения алюминия больше 30% наблюдается уменьшение удельного количества выделяющейся физ- и хемосорбированной воды, а также углекислого газа по сравнению с образцами со степенью превращения 10 и 20%.
В табл. 1 приведены значения температур, при которых при линейном нагреве образцов наблюдаются локальные максимумы скорости выделения воды и относительное количество воды, выделяющейся в окрестностях каждого из этих максимумов (по данным масс-спектрометрии, рис. 3в). Жирным шрифтом выделены максимумы, сопровождающиеся выделением тепла и уменьшением массы образца. Данные табл. 1 показывают, что в температурном диапазоне 100–270°C, где происходит десорбция физсорбированной воды и хемосорбированных –ОН групп, в том числе находящихся в составе гидроксидной оболочки, может выделяться свыше 40% всей содержащейся в образце воды. С увеличением степени превращения алюминия в образцах уменьшается относительное количество этой воды и увеличивается температура, при которой наблюдается максимум ее выделения. Это свидетельствует, что увеличение степени превращения металла уменьшает способную сорбировать воду удельную поверхность образующегося гидроксидного покрытия и одновременно увеличивает энергию связи хемосорброванной воды с поверхностью оксидов. Данный факт, по-видимому, объясняется тем, что с ростом степени превращения металла увеличивается доля образующихся кристаллических форм Al(OH)3.
Таблица 1.
Температуры, при которых наблюдаются максимумы скорости выделения воды при линейном нагреве образцов, и относительное количество воды, выделяющейся в областях этих максимумов (по данным масс-спектрометрии, рис. 3в)*
Образец 1 | Образец 2 | Образец 3 | |||
---|---|---|---|---|---|
температура в максимуме пика, °C | количество воды в максимуме, отнесенное к общему количеству выделяющейся воды, % | температура в максимуме пика, °C | количество воды в максимуме, отнесенное к общему количеству выделяющейся воды, % | температура в максимуме пика, °C | количество воды в максимуме, отнесенное к общему количеству выделяющейся воды, % |
150 | 42.2 | 158 | 29 | 206 | 2 |
280 | 24 | 238 | 1.4 | 246 | 9 |
326 | 2.3 | 298 | 46 | 305 | 67 |
397 | 30 | 365 | 16 | 370 | 18 |
620 | 1.5 | 452 | 5 | 514 | 3 |
513 | 0.3 | 631 | 1 | ||
618 | 2.3 |
* Для определения интегрального количества воды в каждой температурной области, экспериментальная зависимость моделировалась суммой Гаусовских функций по алгоритму, реализованному в программе Fityk [9].
Следует отметить, что для АГЧ со степенью превращения алюминия меньше 30% также как и для исходных частиц порошка АСД-4 форма зависимости интенсивности выделения CO2 в обсуждаемом температурном диапазоне коррелирует с формой зависимости выделения воды (рис. 3в, 3г). Это свидетельствует, что сорбция молекул углекислого газа осуществляется с участием сорбированной поверхностью оксида молекул воды.
При температуре около 300°C наблюдается резкое выделение молекул Н2О, сопровождаемое эндотермическим эффектом на ДТА кривой (рис. 3а) и вызывающее потерю массы на ТГ кривой (рис. 3б). Эти результаты свидетельствуют о разложении Al(OH)3 (фазовый переход первого рода).
РФА (рис. 4) показывает, что после окисления в воде АГЧ состоят из металлического ядра (алюминий) и состоящей из гидроксида алюминия оболочки (байерит + гиббсит). Наличие двух модификаций гидроксида алюминия обусловливает расщепление пика ДТА (рис. 3а) на два (295 и 305°C для образца 2 и 301 и 307°C для образца 3). При более низкой температуре происходит разложение менее устойчивой формы – байерита, а затем гиббсита. После нагрева образца до 750°C на рентгенограмме кроме пиков, относящихся к металлическому алюминию, регистрируются только слабые пики, соответствующие Al2O3. Таким образом, поскольку других фазовых переходов в исследуемом диапазоне температур по данным синхронного термического анализа не наблюдается, то принимая во внимание результаты, демонстрируемые ТГ кривой, можно сделать заключение, что в условиях опыта при температуре около 300°C происходит разложение гидроксида с образованием рентгеноаморфного (наноразмерного) оксида алюминия. Количество воды, выделяющейся при фазовом переходе, увеличивается с уменьшением относительного содержания алюминия в образце (увеличением степени превращения образца). При этом значение температуры, при которой достигается максимум скорости процесса разложения гидроксида, также увеличивается (сдвигается с 280 до 305°C).
Рис. 4.
Ренгенограммы образца 2 до его нагрева (а) и после нагрева в окислительной атмосфере (75% Ar + 25% O2) до 750°С (б).
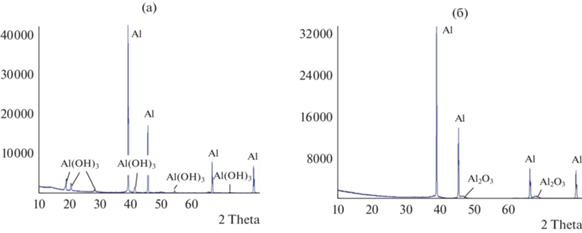
Выделяющаяся в результате разложения Al(OH)3 вода реагирует с алюминием с образованием водорода. Действительно по данным масс-спектрометрии (рис. 3д) выделение Н2 наблюдается при температуре фазового перехода (~300°C). Это связано с тем, что происходящая во время фазового перехода перестройка кристаллической решетки приводит к нарушению сплошности оболочки частицы и, таким образом, облегчает транспорт образующихся молекул воды, как в глубину частицы (к металлическому ядру), так и в окружающую частицу атмосферу. Образующийся водород может выделяться в окружающую среду, проходя через образовавшиеся сквозные поры и трещины оксидного покрытия, а может, оказаться капсулированным под покрытием или растворенным в алюминии ядра частицы. Максимальный объем водорода, которой может образоваться, если вся выделяющаяся при разложении гидроксида алюминия вода прореагирует с алюминием ядра, пропорционально степени превращения образца (толщине Al(OH)3 оболочки при малых степенях превращения металла). Для образца со степенью превращения 10% оно составляет 7 нсм3/г, 20% – 97 нсм3/г, 35% – 235 нсм3/г. Экспериментально наблюдаемое количество выделившегося при 300°C водорода определялось с использованием калибровки абсолютной чувствительности масс-спектрометра по разложению AlH3 описанной в разделе 1. Оно составляет 2.7 нсм3/г для образца 2 и 10 нсм3/г для образца 3, в образце 1 выделение водорода не обнаружено. Таким образом, можно сделать оценку, что с алюминием реагирует до 10% выделяющейся при разложении Al(OH)3 воды для исследуемых типов АГЧ, что коррелирует со значением аналогичного параметра, полученного при нагревании исходного порошка АСД-4 (не окисленный алюминиевый порошок).
Отметим, что в окислительной атмосфере в области нарушения сплошности оболочки при температуре около 300°C термоаналитическими методами не регистрировалось окисление Al ядра АГЧ кислородом. Это связано с низкой скоростью окисления алюминия в этом диапазоне температур и с наложением экзотермического теплового эффекта окисления на эндотермический эффект потери воды при фазовом переходе. Дальнейшее нагревание АГЧ приводит к появлению на кривой ДТА экзотермического эффекта, наблюдаемого при температуре выше 550°C (рис. 3a). Одновременно с тепловыделением наблюдается рост массы образца, фиксируемый ТГ кривой (рис. 3б). Оба эти эффекта свидетельствуют о происходящем с высокой скоростью окислении Al ядра частицы кислородом окружающей среды и о происходящем при этих температурах нарушении сплошности оксидной оболочки частиц. Отметим, что при нагревании образцов в нейтральной атмосфере аргона обсуждаемые эффекты не наблюдаются.
3.3. Процессы нарушения сплошности оксидной оболочки. Образование трещин
Выше сообщалось, что нарушение сплошности оксидной оболочки при нагревании АГЧ наблюдается дважды: в температурных диапазонах около 300 и 570°С. Об этом, в частности, свидетельствует выделение нагреваемыми АГЧ водорода. При 300°С нарушение сплошности является результатом фазового перехода гидроксидов в оксиды алюминия. Этот факт легко детектируется методами термического анализа по изменениям, наблюдаемым на ТГ и ДТА кривых (рис. 3a и 3б) и в окислительной, и в нейтральной атмосфере. Однако из-за недостаточной чувствительности прибора в этом диапазоне температур не удается наблюдать на ТГ и ДТА кривых эффекты, связанные с окислением Al. Для температур выше 570°C факт нарушения сплошности также устанавливается методами термического анализа благодаря наблюдению эффектов, связанным с окислением алюминия, возникающих при нагревании образцов в окислительной атмосфере. Это становится возможным благодаря возрастанию скорости окисления алюминия кислородом с увеличением температуры. Результаты опытов показывают, что величина наблюдаемого на кривой ДТА теплового эффекта и значение температуры, при которой нарушается сплошность оксидного покрытия (начинает наблюдаться окисление Al) зависят от степени превращения образца т.е. толщины оксидной оболочки. Кривые на рис. 5 дают возможность сравнить величины и формы экзотермических эффектов, а также температуры нарушения сплошности оксидного слоя (начало роста DTA-кривой) для образцов с различной степенью превращения, линейно нагреваемых в кислородсодержащей среде. Видно, что максимальный термический эффект и минимальная температура разрушения покрытия наблюдаются для исходных частиц АСД-4. Увеличение степени превращения образца (толщины оксидного слоя) увеличивает температуру разрушения покрытия и уменьшает термический эффект окисления.
Рис. 5.
Зависимость величины термического эффекта и температуры начала процесса окисления алюминия кислородом для АГЧ со степенью превращения алюминия: 1 (черная кривая) – 0% (исходный порошок АСД-4); 2 (красная кривая) – 3%; 3 (зеленая кривая) – 15%; 4 (синяя кривая) – 30%, полученные при нагревании образцов в окислительной атмосфере (70% Ar + 30% O2).
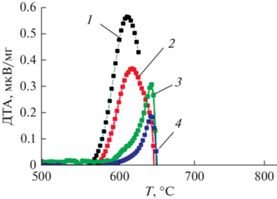
По-видимому, причиной нарушения сплошности оболочек при температурах в области 570°С являются термические напряжения, возникающие в системе ядро–оболочка. Коэффициент термического расширения (КТР) металлического алюминия (αAl = 23.68 × 10–6 1/К) значительно превышает КТР его оксидов (${{\alpha }_{{{\text{A}}{{{\text{l}}}_{{\text{2}}}}{{{\text{O}}}_{{\text{3}}}}}}}$ = 9.6 × 10–6 1/К) и это приводит к разрушению оболочек при нагревании окисленных частиц.
Для получения оценки значения температуры разрушения оксидных оболочек при нагревании частиц АОЧ и АГЧ могут быть рассмотрены два предельных модельных случая, описывающих взаимодействие оболочки и металлического ядра частицы. В первом случае между оболочкой и ядром реализуется прочная связь, не разрушающаяся при нагревании частицы. Такая модель рассмотрена в работе [13] и показывает, что разрушение (образование трещин) наиболее устойчивых к разрушению оксидных оболочек происходит при температурах около 400°С. Во втором случае, каждая АОЧ (АГЧ) может моделироваться алюминиевым шаром, помещенным в слабо связанную с ним тонкую сферическую оксидную оболочку. При нагревании рассматриваются независимые объемное расширение шара и линейное расширение покрывающей его оболочки. Поскольку между значениями КТР существует соотношение αAl > ${{\alpha }_{{{\text{A}}{{{\text{l}}}_{{\text{2}}}}{{{\text{O}}}_{{\text{3}}}}}}}$ (примерно в 2.5 раза), то расширяющуюся с повышением температуры оболочку будет дополнительно растягивать нагревающееся внутри алюминиевое ядро. Удлинение оболочки для этой модели будет:
Предел прочности оксида алюминия (сапфира) на разрыв: F = 1900 МПа [14]; значение модуля Юнга [15] для оксида алюминия: E = 380 ГПа. Учитывая, что разрушение оболочки является хрупким, можно оценить, что ее разрушение произойдет при увеличении температуры на:
Таким образом, обе модели демонстрируют, что при нагревании АОЧ разрушения оксидной оболочки можно ожидать в температурном интервале несколько сот градусов (300–500°С). Результаты оценки подтверждают экспериментально наблюдаемую величину.
Данные масс-спектрального анализа показывают, что при нагревании образцов АГЧ в инертной среде (рис. 6) водород наблюдается как при температуре фазового перехода (около 300°C), так и при температуре нарушения сплошности оболочки около 600°C. В первом случае количество выделяемого водорода составляет 2.7 нм3/г, что примерно в 4 раза меньше, чем во втором (11 нм3/г). По-видимому, во втором случаев результате растрескивания оксидной оболочки выделяется водород, капсулированный в оксидной оболочке (растворимостью водорода в алюминии можно пренебречь [16]).
Рис. 6.
Температурные зависимости интенсивности выделения: (а) водорода (м/e = 2): (б) воды (м/e = 18) в атмосферах: аргона – кривая 1; в окислительной атмосфере (75% Ar + 25% O2) – кривая 2.
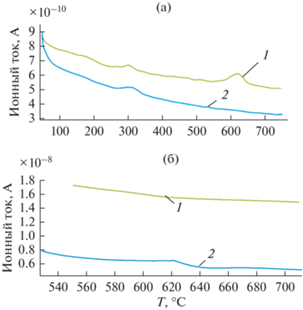
При нагревании образцов АГЧ в окислительной атмосфере Н2 вступает в реакцию с О2, образуя при высоких температурах Н2О. По этой причине при температуре около 600°C в окислительной атмосфере не наблюдается выделения водорода, но наблюдается выделение воды. Напротив, в инертной среде при высокой температуре выделение воды не наблюдается (рис. 6).
В диапазоне температур выше температуры плавления жидкий Al через возникшие в оксидной оболочке трещины и поры начнет выдавливаться на поверхность частицы (рис. 7). Одновременно он будет усиливать эффективность образования трещин благодаря расклинивающему эффекту, оказываемому расплавом на дефекты структуры оболочки и зародыши образующихся трещин. Ширина трещин составляет, как правило, до нескольких десятых микрон. Вышедший на поверхность частиц через сквозные трещины и поры алюминий может локализоваться в виде капель или растекаться по поверхности. Результат определяется условиями, в которых производится нагревание образца. Этот алюминий может быть использован для образования контактов между отдельными АОЧ при формировании из них 3D-структур, в том числе каркасов для композитов.
Рис. 7.
Распределение элементов (алюминий, кислород) по поверхности частиц образца, со степенью превращения 20% после линейного нагрева со скоростью 20°С/мин до температуры 750°С в инертной атмосфере. Красный цвет – O, зеленый цвет – Al. Стрелками отмечены сквозные трещины оксидного покрытия, в овалы обведены сквозные поры. Выполнено на приборе Quanta.
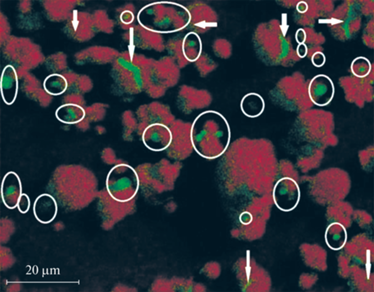
ЗАКЛЮЧЕНИЕ
В работе были проанализированы процессы, протекающие при линейном нагревании алюминиевых частиц в окислительной и нейтральной средах. Были изучены частицы в состоянии поставки и частицы, окисленные водой со степенью превращения металла до 35%. Показано, что в ходе нагревания (до 750°С) гидроксидные оболочки алюминиевых частиц претерпевают ряд превращений, обусловленных протекающими в них химическими и физическими процессами. В результате протекающих процессов выделяются летучие соединения: вода, углекислый газ, водород, иногда следы органики.
Получено, что выделение молекул воды происходит в результате термической десорбции ее физ- и хемосорбированных форм; при трансформации (фазовых переходах) гидроксидов оболочки в оксиды и при окислении образующегося водорода. Водород является результатом химической реакции выделяющейся воды с металлическим ядром АГЧ и при повышенных температурах может реагировать с кислородом окружающей АГЧ атмосферы, снова образуя воду и выделяя тепло.
Наблюдаемое при температурах ниже 200°С выделение СО2 коррелирует с десорбцией физ и хемосорбированных форм воды. Это позволяет говорить о существовании совместных с молекулами воды комплексов на поверхности АГЧ. Выделение СО2, наблюдаемое при более высоких температурах, свидетельствует в пользу существования поверхностных карбонатов.
Нарушение сплошности оксидного покрытия в исследуемом диапазоне температур происходит дважды: при температурах около 300 и 600°С. В первом случае в результате фазового перехода гидроксида Al в оксид происходит перестройка структуры покрытия и о нарушении сплошности свидетельствует выделение воды и водорода. Нарушение сплошности покрытия при температурах около 580°С наблюдается как по данным термического анализа по приросту массы образца и выделению тепла в результате окисления алюминия кислородом в окислительной среде, так и масс-спектрально по выделению капсулированного в покрытии водорода. Образование трещин в оксидной оболочке и выдавливание расплавленного алюминия через трещины, по-видимому, обусловлено различием в термических коэффициентах линейного расширения Al и Al2O3 и усиливается благодаря расклинивающему эффекту, оказываемому расплавом алюминия на дефекты структуры оболочки и зародыши образующихся трещин, при температурах выше температуры плавления алюминия.
Высказано предложение об использовании поднявшегося на поверхность частиц алюминия для фиксации 3D конструкций путем образования спаек между отдельными АГЧ при формировании из них пористой 3D-структуры композитного метало-оксидного материала методом 3D печати.
Полученные результаты, в частности, демонстрируют необходимость предварительного прогрева АГЧ при использовании их для 3D печати с целью их обезгаживания и трансформирования гидроксидов алюминия в оксиды. Такая предварительная дегазация АГЧ позволит избежать образования пор в готовом изделии выделяющимися газами при реализации 3D печати и обеспечит необходимую прочность связи наполнитель-матрица.
Работа выполнена в части РЭМ- и ЭДРА-измерений при поддержке Министерства науки и высшего образования РФ в рамках выполнения работ по
Государственному заданию ФНИЦ “Кристаллография и фотоника” РАН с использованием оборудования ЦКП ФНИЦ “Кристаллография и фотоника” РАН при поддержке Министерства образования и науки России.
Список литературы
Fernandez A., Sanchez-Lopez J.C., Caballero A. et al. // J. Microscopy. 1998. V. 191. P. 212.
Жорин В.А., Киселев М.Р., Ширяев А.А., Котенев В.А. // Физикохимия поверхности и защита материалов. 2022. Т. 58. № 1. С. 45.
Larichev M.N., Shaitura N.S., Artemov V.V. // Письма в журн. технической физики. 2021. Т. 47. № 8. С. 11.
Eisenreich N., Fietzek H., Juer-Lorenzo M. et al. // Propellants, Explosives, Pyrotechnics. 2004. V. 29. № 3. P. 137.
Ambaryan G.N., Vlaskin M.S., Shkolnikov E.I., Zhuk A.Z. // J. Physics: Conference Series. 2020. P. 012030.
Laritchev M.N., Jigach A.N., Leipunsky I.O., Kuskov M.L. // NanoTech 2002: At the Edge of Revolution. 2002.
Шайтура Н.С., Ларичева О.О., Ларичев М.Н. // Химическая физика. 2019. Т. 38. № 3. С. 9.
Тихов С.Ф., Фенелонов В.Б., Садыков В.А. и др. // Кинетика и катализ. 2000. Т. 41. № 6. С. 907.
Nalivaiko A.Yu., Ozherelkov D.Yu., Arnautov A.N. et al. // Applied Physics A. 2020. V. 126. P. 871.
Larichev M.N. Metal Nanopowders: Production, Characterization, and Energetic Applications / Wiley CH Verlag GmbH & Co. KGaA, 2014. P. 163.
Shaytura N.S., Laritchev M.N., Laritcheva O.O., Shkol’nikov E.I. // Current Applied Physics. 2010. V. 10. P. 66.
Popenko E.M., Il’in A.P., Gromov A.M. et al. // Combustion, Explosion, and Shock waves. 2002. V. 38. P. 157.
Томило В.А., Паршуто А.А., Чекан Н.М. // Известия национальной академии наук Белоруссии. Серия физико-технических наук. 2015. № 1. С. 22.
White G.K., Roberts R.B. // High Temperatures-High Pressures. 1983. V. 15. № 3. P. 321.
http://www.virial.ru/materials/95/.
https://fityk.nieto.pl/.
Tiryakioglu M. // Intl. J. Cast. Metals. Res. 2020. V. 32. P. 315.
Дополнительные материалы отсутствуют.
Инструменты
Физикохимия поверхности и защита материалов