Электрохимия, 2023, T. 59, № 2, стр. 101-110
Влияние плотности тока на удельные характеристики отрицательных электродов для литий-ионных аккумуляторов на основе термообработанного нефтяного кокса
Е. В. Кузьмина a, *, Н. В. Чудова a, В. С. Колосницын a
a Уфимский Институт химии Уфимского федерального исследовательского центра РАН
450054 Уфа, Россия
* E-mail: kuzmina@anrb.ru
Поступила в редакцию 16.03.2022
После доработки 20.06.2022
Принята к публикации 05.07.2022
- EDN: NFCFPF
- DOI: 10.31857/S0424857023020068
Аннотация
Приводятся результаты сопоставительных исследований влияния плотности тока на величины среднего разрядного напряжения и удельной разрядной емкости углеродных электродов на основе термически обработанного нефтяного кокса и графита. Установлено, что углерод, полученный термообработкой нефтяного кокса, обладает лучшими кинетическими характеристиками, чем графит. Увеличение плотности тока с 0.2 мА/см2 (36 мА/г) до 2 мА/см2 (364 мА/г) приводит к уменьшению разрядной емкости термообработанного нефтяного кокса на 26%, а графита – на 93%. При восстановлении плотности тока до 0.2 мА/см2 разрядная емкость углеродных электродов восстанавливается до начального значения. Исследования показали, что увеличение плотности тока также приводит к увеличению среднего разрядного напряжения литий-углеродных ячеек. Так при увеличении плотности тока с 0.2 до 2 мА/см2 среднее разрядное напряжение литий-углеродных ячеек с активным компонентом углеродного электрода ТНК увеличивается с 0.39 до 0.62 В, а для графита – с 0.14 до 0.35 В.
ВВЕДЕНИЕ
В первых коммерческих литий-ионных аккумуляторах (ЛИА) использовали твердый углерод в качестве активного материала отрицательного электрода и LiCoO2 – положительного [1, 2]. Позднее твердые углероды были заменены на графит, поскольку он обладает большей удельной емкостью (372 мА ч/г) и более низким потенциалом электрохимической интеркаляции катионов лития (0.15–0.25 В относительно литиевого электрода сравнения) [3–5].
Однако, вследствие невысокой скорости электрохимической интеркаляции катионов лития в графит [6] даже относительно небольшое увеличение плотности тока приводит к существенному возрастанию перенапряжения и достижению потенциала выделения металлического лития. В этом случае на графитовых электродах металлический литий электрохимически осаждается в виде мелкодисперсных осадков, которые могут приводить к увеличению скорости восстановительной деструкции компонентов электролитных систем и внутренним замыканиям. В худших случаях образование мелкодисперсных осадков лития может вызвать возгорание, разгерметизацию и даже взрыв аккумуляторов.
В высокомощных литий-ионных аккумуляторах в качестве активных материалов отрицательных электродов используют титанаты лития, поскольку они способны к обратимой электрохимической интеркаляции катионов лития при высоких токовых нагрузках. Катионы лития интеркалируются в титанаты лития при потенциалах 1.5 В относительно литиевого электрода сравнения [7], поэтому возможность электрохимического выделения металлического лития практически сводится к нулю. Благодаря этому, литий-ионные аккумуляторы с отрицательными электродами на основе титанатов лития обладают высокой безопасностью даже при высоких токовых нагрузках. Однако из-за высокого потенциала электрохимической интеркалляции/деинтеркалляции катионов лития и относительно низкой электрохимической удельной емкости титанатов лития их применение в качестве активных материалов отрицательных электродов приводит к существенному уменьшению удельной энергии ЛИА.
Поэтому актуальна разработка активных материалов для отрицательных электродов, способных обратимо интеркалировать ионы лития при потенциалах более положительных, чем потенциал осаждения металлического лития при высоких токовых нагрузках. Такие материалы могут быть созданы на основе структурно-неупорядоченных углеродов, получаемых термообработкой нефтяного кокса. В отличие от графита и других упорядоченных углеродов, неупорядоченные углеродные материалы не имеют дальнодействующей периодической структуры в плоскости или вдоль направления упаковки. Они образованы случайно ориентированными графитовыми микродоменами с sp2-гибритизацией, частично сшитыми sp3-гибридизированными атомами углерода [6]. При высокотемпературной обработке (1500–3000°С) структурно-неупорядоченные углероды приобретают упорядоченную структуру, т.е. графитизируются. Электрохимическая интеркаляция катионов лития в структурно-неупорядоченные углероды, осуществляется в широком диапазоне электродных потенциалов 1.5–0 В относительно литиевого электрода сравнения [8].
Структурно-неупорядоченные углероды могут быть получены термообработкой нефтяного кокса в различных условиях. Нефтяной кокс (НК) является крупнотоннажным продуктом вторичной переработки нефти. Он доступен, относительно дешев. Нефтяные коксы относятся к мягким углеродам. Ранее было показано, что нефтяные коксы могут быть использованы в качестве материалов отрицательных электродов ЛИА [9‒11].
Ранее нами было показано, что интеркаляция катионов лития в термообработанный нефтяной кокс осуществляется в широком диапазоне потенциалов, что позволяет достичь высокую зарядную емкость (200–250 мА ч/г) при окончании катодного заряда при потенциале 50–100 мВ относительно литиевого электрода для предотвращения возможности электрохимического выделения металлического лития [12].
Помимо удельной емкости, важной характеристикой перспективных электродных материалов для ЛИА является скорость электрохимической интеркаляции ионов лития, т.е. зависимость удельной емкости электродных материалов от плотности тока.
Поэтому с целью разработки дешевых, доступных и безопасных материалов для отрицательных электродов литий-ионных аккумуляторов нами были проведены сопоставительные исследования влияния плотности тока на удельные энергетические характеристики термообработанного нефтяного кокса и графита.
ЭКСПЕРИМЕНТАЛЬНАЯ ЧАСТЬ
Нефтяной кокс электродный (ТУ 0258-098-00151807-98 с изм. 1-4, ТУ 38.1011320-90 с изм. 1-4, Новоуфимский НПЗ г. Уфа, Россия) подвергали термической обработке в собственных парах, выдерживая образцы при 1000°С в течение 10 ч в закрытом керамическом тигле, заполненном углеродом на 2/3 от его объема. Скорость нагрева составляла 10°С/мин. По достижении заданной температуры образец выдерживали в течение 10 ч, затем выключали нагрев и, не открывая тигель, охлаждали до 600°С, переносили в эксикатор и охлаждали до комнатной температуры.
Графит (Dianshi, Китай) использовали без предварительной обработки.
Удельную площадь поверхности углеродных материалов оценивали методом сорбции красителей по метиловому оранжевому [13, 14]. Удельное объемное сопротивление измеряли в кондуктометрических ячейках с блокирующими электродами, изготовленными из нержавеющей стали, при фиксированном давлении 6.4 × 104 кг/см2.
Кислотно-основные свойства углеродов определяли кислотно-основным титрованием с потенциометрической индикацией конечной точки титрования.
Исследование электрохимических свойств углеродных материалов проводили в двухэлектродных дисковых разборных ячейках типа Swagelock cell®. Давление поджима электродного блока составляло 0.3 кг/см2.
Углеродные электроды изготавливали отливкой водной суспензии смеси, состоящей из 94 мас. % активного материала (термообработанный нефтяной кокс (ТНК) или графит), 1 мас. % сажи (Super P, Китай) и 5 мас. % связующего LA‑132 (Китай), на медную фольгу, толщиной 16 мкм. После отливки суспензии на медную фольгу электроды сушили при 40°C в течение 1 ч. Затем каландрировали и вырубали в размер. Готовые электроды сушили в статическом вакууме при 40°C над молекулярными ситами 4 Å не менее 24 ч. Содержание термообработанного нефтяного кокса или графита в электродах составляло 5.5 мг/см2.
Литиевые электроды вырубали из металлической литиевой фольги, толщиной 100 мкм (China Lithium Energy Ltd., Китай), в размер.
В качестве сепаратора использовали комбинацию из 2 слоев нетканого полипропилена и 1 слоя микропористого полипропилена (Celgard®3501).
Электролитом был 1М раствор LiPF6 в смеси диметилкарбоната (DMC), этилметилкарбоната (EMC) и этиленкарбоната (EC) (20 : 45 : 20 мас. %) с добавкой виниленкарбоната (VC, 1%). Количество электролита в ячейках составляло 30 мкл/см2.
Все операции по сборке электрохимических ячеек выполняли в перчаточном боксе в атмосфере сухого воздуха (содержание воды не превышало 2 ppm).
После сборки все электрохимические ячейки помещали в воздушный термостат и выдерживали при 30°С 1 ч до стабилизации их характеристик и затем измеряли их электрохимический импеданс. Электрохимический импеданс регистрировали на гальваностате-потенциостате SP-200 (BioLogic, Франция) в диапазоне частот 0.01 Гц–7 МГц, амплитуда возмущения была 4 мВ.
Гальваностатическое зарядно-разрядное циклирование ячеек осуществляли с помощью батарейного тестера BCS-800 (BioLogic, Франция). Один цикл состоит из катодного заряда (интеркаляция лития в углерод) и анодного разряда (деинтеркаляция катионов лития из углерода) литий-углеродных ячеек.
Ячейки циклировали в диапазоне потенциалов 50–1000 мВ отн. Li/Li+. Плотность тока варьировалась в диапазоне 0.1–2.0 мА/см2 (18–364 мА/г).
Все электрохимические исследования проводили при температуре 30 ± 0.1°С.
Коэффициенты диффузии ионов лития оценивали методом спектроскопии электрохимического импеданса [15–18] для нелитированных и литированных углеродных электродов, изготовленных из графита или термически обработанного нефтяного кокса. Коэффициент диффузии рассчитывали по уравнению 1.
где D – коэффициент диффузии ионов лития, м2 с–1; R – универсальная газовая постоянная, 8.314 Дж К–1 моль–1; T – температура, К; A – габаритная площадь электрода, м2; F – постоянная Фарадея, 96 486 Кл моль–1; σw – коэффициент, Ом/(м2 с0.5); c – концентрация ионов лития, моль м–3.Коэффициент σw определяли, как тангенс угла наклона прямой зависимости мнимой составляющей импеданса ячеек от обратного корня частоты в диапазоне частот 10–150 мГц.
Следует отметить, что уравнение (1) расчета коэффициента диффузии справедливо для идеальных систем. Существуют разные способы учета неидеальности систем, и как следствие коэффициенты диффузии катионов лития в углеродных материалах, определенные различными методами, плохо совпадают между собой [19]. Поскольку целью работы была только сопоставительная оценка коэффициентов диффузии в различных углеродных материалах, нами был выбран простой в исполнении метод, широко описанный в научной литературе.
Для ячеек с нелитированными углеродными электродами концентрацию ионов лития в поверхностном слое углеродных материалов принимали равной концентрации соли в растворе 1 М.
Литирование углеродных электродов осуществляли электрохимически. Для этого собирали ячейки с металлическим литиевым электродом, которые катодно поляризовали плотностью тока 0.1 мА/см2. Интеркалляцию ионов лития проводили до достижения напряжения на ячейках, равного 50 мВ. Затем литий-углеродные ячейки переносили в перчаточный бокс, разбирали, извлекали из них литированные углеродные электроды, с которыми собирали симметричные углерод/углеродные ячейки. Ячейки помещали в термостат при 30 ± 0.1°С до стабилизации их характеристик и затем измеряли электрохимический импеданс в диапазоне частот 10 мГц–7МГц, амплитуда возмущающего сигнала была 4 мВ.
Концентрацию катионов лития в углеродных электродах рассчитывали, исходя из величины электрохимической емкости, по уравнению:
(2)
${{c}_{{{\text{L}}{{{\text{i}}}^{ + }}}}} = \frac{{Q \times 100\% }}{{FAh\left( {100 - P} \right)}},$Все эксперименты проводили не менее 3 раз. Экспериментальная ошибка измерений не превышала 3%.
РЕЗУЛЬТАТЫ И ОБСУЖДЕНИЕ
Некоторые свойства термообработанного нефтяного кокса и графита суммированы в табл. 1. По сравнению с графитом термообработаный нефтяной кокс обладает меньшим удельным объемным сопротивлением, большими удельной площадью поверхности и коэффициентами диффузии ионов лития. В отличие от графита, ТНК обладает кислотными свойствами.
Таблица 1.
Физико-химические свойства термообработанного нефтяного кокса и графита
Показатели | Термообработанный нефтяной кокс | Графит |
---|---|---|
Удельное объемное сопротивление, Ом см | 0.03 | 0.53 |
Удельная площадь поверхности по МО, м2/г | 6.8 | 1.2 |
Коэффициент диффузии Li+ в поверхностном слое нелитированного углеродного материала, м2/с | 12 × 10–12 | 3.4 × 10–12 |
Коэффициент диффузии Li+ в литированном углеродном материале, м2/с | 12 × 10–16 | 8 × 10–16 |
Кислотность (${{c}_{{{{{\text{H}}}^{ + }}}}}$), ммоль/г(С) | 0.013 | $ \ll $0.001 |
Основность (${{c}_{{{\text{O}}{{{\text{H}}}^{ - }}}}}$), ммоль/г(С) | $ \ll $0.001 | $ \ll $0.001 |
Годографы импеданса симметричных ячеек с нелитированными углеродными электродами (рис. 1а) представляют собой вырожденную полуокружность, переходящую в дугу. Размер вырожденной полуокружности существенно меньше дуги. Годограф плохо поддается обработке методом эквивалентных схем. Сопротивление переноса заряда на электродах можно оценить с ошибкой соизмеримой с диаметром полуокружности.
Рис. 1.
Годографы импеданса симметричных ячеек с нелитированными (а) и литированными углеродными электродами (б) и литий-углеродных ячеек c нелитированными (в) и литированными углеродными электродами (г). Активный материал электродов приведен в легенде. Углеродный материал: ⚫ – нефтяной кокс, ◻ – графит. Элементы эквивалентной схемы: Rel – сопротивление электролита, RF – сопротивление переноса заряда, CPE – элемент постоянной фазы, W – элемент Варбурга.

Годографы импеданса симметричных углерод-углеродных ячеек с литированными углеродными материалами состоят из двух вырожденных полуокружностей, переходящих в дугу (рис. 1б). Сопротивление переноса заряда на литированных электродах из ТНК составляет 8.5 ± 0.5 Ом, а на электродах из графита – 15.8 ± 0.6 Ом.
Сопротивление переноса заряда оценивали по эквивалентной схеме, представленной на рис. 1б.
Формы годографов импеданса литий-углеродных ячеек подобны для графита и ТНК и имеют классическую форму (рис. 1в) и представляют собой вырожденную полуокружность, переходящую в дугу. Сопротивление электролита во всех ячейках было 1.6 ± 0.2 Ом, сопротивление переноса заряда на электродах литий-углеродных ячеек составило для ТНК 32 ± 2 Ом, для графита 40 ± ± 5 Ом. Различие в сопротивлении переноса заряда ячеек невелико и близко к разбросу экспериментальных данных. Годографы импеданса литий-углеродных ячеек с литированными углеродными электродами подобны годографам импеданса ячеек с нелитированными углеродными электродами и состоят из вырожденной полуокружности, переходящей в дугу. Сопротивление переноса заряда на электродах литий-углеродных ячеек составляет 18 ± 1 Ом. После литирования ячеек сопротивление электродов уменьшилось вдвое.
Таким образом, можно заключить, что термообработанный нефтяной кокс обладает лучшими транспортными свойствами по сравнению с промышленным графитом: большим коэффициентом диффузии, меньшим сопротивлением переноса заряда и меньшим удельным сопротивлением. Хорошие транспортные свойства термообработанного нефтяного кокса могут быть обусловлены несколькими факторами: особенностью строения кристаллической решетки (что требует дополнительных исследований), а также большей площадью поверхности.
Формы зарядно-разрядных кривых (рис. 2) электродов на основе нефтяного кокса и графита различны. При катодном заряде электродов на основе термообработанного нефтяного кокса потенциал ячеек плавно уменьшается. Примерно при 500 мВ наблюдается слабовыраженный перегиб. Анодные разрядные кривые электродов на основе ТНК подобны зарядным: происходит плавное увеличение потенциала с перегибом около 200 мВ.
Рис. 2.
Зарядные и разрядные кривые углеродных электродов на 1-цикле. Активный материал углеродного электрода: а – термообработанный нефтяной кокс, б – графит. Плотность тока 0.2 мА/см2. Диапазон потенциалов 10–1000 мВ. Температура 30°C.
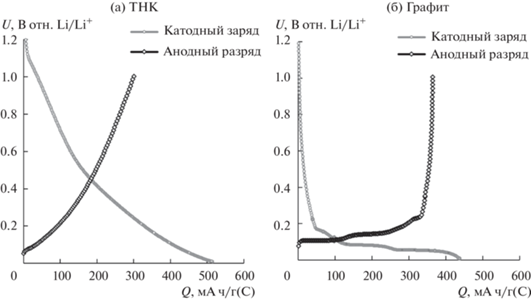
Электрохимическое восстановление мягких неупорядоченных углеродов в литий-ионных системах осуществляется по нескольким механизмам одновременно: интеркаляция, адсорбция, заполнение полостей (дефектов) и пор, взаимодействие с гетероатомами и функциональными группами, содержащимися на поверхности, а также накопление на границе раздела фаз [6]. Пологая форма зарядной и разрядной кривой нефтяного кокса может быть объяснена именно этим.
В идеальном случае внедрение лития в углерод полностью обратимо. Однако на практике при катодном заряде на первом цикле затрачивается большее количество электричества, чем в последующем анодном процессе. Разница между количеством электричества катодного (Qкат) и анодного (Qан) полуциклов составляет необратимую емкость (Qнеобр). Причиной необратимой емкости являются побочные процессы, протекающие при катодной поляризации углеродного электрода: на поверхности углерода до и параллельно интеркаляции лития происходит электрохимическое восстановление компонентов электролитной системы, на что тратится определенное количество электролита [20]. Кроме того, если на поверхности углерода содержатся функциональные группы, то они также могут подвергаться электрохимическому восстановлению [21, 22]. Продукты восстановления формируют на поверхности углеродных частиц барьерный слой твердого электролита, обладающего проводимостью по ионам лития и предотвращающего дальнейшее восстановление компонентов электролитной системы [22].
При заряде на 1-м цикле зарядная катодная емкость составила 515 мА ч/г(С), а разрядная анодная емкость – 294 мА ч/г(С). Необратимая емкость составила 221 мА ч/г, т.е. 43% от зарядной емкости. Необратимая емкость ТНК обусловлена не только восстановлением компонентов электролитной системы, но и электрохимическим восстановлением функциональных групп, содержащихся на поверхности нефтяного кокса.
Для оценки вклада в необратимую емкость кислотных или основных групп, которые могут содержаться на поверхности углеродных материалов, нами были изучены кислотно-основные свойства термообработанного нефтяного кокса и графита (табл. 1). Исследования показали, что на поверхности ТНК содержание кислотных групп составило 0.013 ммоль/г(С). На поверхности графита кислотные и основные группы определить не удалось. При первом катодном заряде содержащиеся кислотные группы могут подвергаться электрохимическому восстановлению, что также вносит свой вклад в необратимую емкость на первом цикле. Однако содержание кислотных групп невелико, и вклад в величину необратимой емкости небольшой. Например, если допустить, что протекает реакция по уравнению (3), то на эту реакцию будет затрачено только 0.35 мА ч/г(С), что существенно ниже необратимой емкости на первом цикле (221 мА ч/г(С)). Таким образом, необратимая емкость обусловлена восстановлением компонентов электролитной системы
(3)
${\text{R--COOH}} + {\text{L}}{{{\text{i}}}^{ + }} + {\text{e}} \to {\text{ R--COОLi}} + {\text{1/2}}{{{\text{H}}}_{2}} \uparrow .$Форма зарядной кривой электродов на основе графита (рис. 2б) описана многократно в научной литературе, и механизм взаимодействия катионов лития с графитом подробно изучен [6]. В начале заряда графитовых электродов происходит восстановление примесей, содержащихся в электролитном растворе и сорбированных в электроде. Этому процессу соответствует резкое снижение напряжения на начальном участке зарядной кривой. Разрядная емкость этого участка составляет примерно 50 мА ч/г(C). По достижению примерно 0.2 В отн. Li/Li+ наблюдается небольшая площадка, соответствующая восстановлению компонентов электролитной системы с формированием защитного слоя твердого электролита на поверхности графита. Длина площадки составляет примерно 30–40 мА ч/г (C). При продолжении заряда графитового электрода на зарядной кривой наблюдаются три площадки: примерно при 80, 50 и 10 мВ отн. Li/Li+, соответствующие электрохимической интеркаляции катионов лития в кристаллическую решетку графита с образованием соединений LiC18, LiC12 и LiC6 соответственно (уравнения (4)–(6)).
(4)
${\text{L}}{{{\text{i}}}^{ + }} + 3{{{\text{С}}}_{6}} + {\text{e}} \to {\text{Li}}{{{\text{C}}}_{{18}}},~~~~~~~~$(5)
${\text{L}}{{{\text{i}}}^{ + }} + {{{\text{С}}}_{6}} + {\text{Li}}{{{\text{C}}}_{{18}}} + {\text{e}} \to 2{\text{Li}}{{{\text{C}}}_{{12}}},$(6)
${\text{L}}{{{\text{i}}}^{ + }} + {\text{Li}}{{{\text{C}}}_{{12}}} + {\text{e}} \to 2{\text{Li}}{{{\text{C}}}_{6}}.$Необратимая емкость графитового электрода составила 73 мА ч/г, т.е. 16%, что хорошо согласуется с литературными данными [6].
Поскольку процессы электрохимического восстановления компонентов электролитной системы гетерогенные, скорость реакции будет зависеть в том числе и от площади поверхности углеродного материала. Удельная площадь поверхности графита 1.2 м2/г по метиловому оранжевому, а ТНК 6.8 м2/г. Необратимая емкость графитового электрода, приведенная к удельной площади поверхности графита по МО, составила 61 мА ч/м2, для электродов на основе термообработанного нефтяного кокса – 31 мА ч/м2. Сопоставление величин приведенной необратимой емкости к площади поверхности позволяет заключить, что на поверхности графита электрохимическое восстановление компонентов электролитной системы осуществляется более интенсивно.
Установлено, что плотность поляризующего тока не оказывает влияние на форму зарядно-разрядных кривых термообработанного нефтяного кокса (рис. 3). Наблюдается только некоторое увеличение перенапряжения.
Рис. 3.
Влияние плотности тока на форму зарядных (а) и разрядных (б) кривых электродов на основе термообработанного нефтяного кокса. Плотности тока: 0.1 мА/см2 (18 мА/г), 0.2 мА/см2 (36 мА/г), 0.5 мА/см2 (91 мА/г), 1 мА/см2 (182 мА/г), 2 мА/см2 (364 мА/г). Диапазон потенциалов 50–1000 мВ отн. Li/Li+.
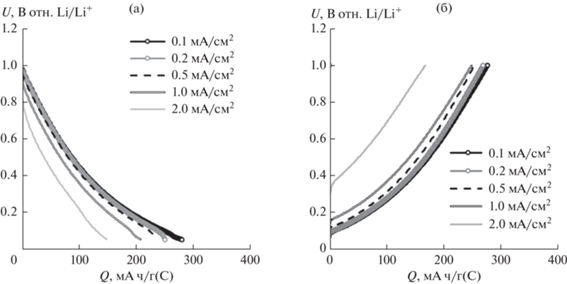
Исследования показали, что увеличение плотности тока с 0.1 до 2 мА/см2 приводит к увеличению среднего напряжения разряда литий-углеродных ячеек с электродами на основе ТНК в 1.6 раз, с 0.39 до 0.62 В. За среднее напряжение разряда литий-углеродных ячеек принимали напряжение на ячейках, соответствующее разряду ячеек на 50% от разрядной емкости.
Более сильное влияние плотность тока оказывает на форму зарядных и разрядных кривых графитовых электродов (рис. 4). При увеличении плотности тока с 0.1 до 0.5 мА/см2 (с 33 до 93 мА/г) происходит увеличение перенапряжения, но форма зарядных и разрядных кривых сохраняется неизменной. При дальнейшем увеличении плотности тока на зарядной и разрядной кривых наблюдается только одна площадка. При этом среднее напряжения разряда литий-углеродных ячеек с электродами на основе графита увеличивается в 2.5 раза, с 0.14 до 0.35 В.
Рис. 4.
Влияние плотности тока на форму зарядных (а) и разрядных (б) кривых электродов на основе графита. Плотности тока: 0.1, 0.2, 0.5, 1, 2 мА/см2. Диапазон потенциалов 50–1000 мВ отн. Li/Li+.
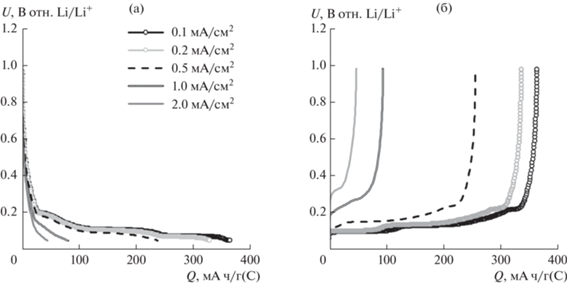
Увеличение плотности тока приводит к уменьшению зарядной и разрядной емкостей углеродных электродов (рис. 5). При увеличении плотности тока с 0.1 (18 мА/г(С)) до 1 мА/см2 (364 мА/г(С)) разрядная емкость электрода на основе термообработанного нефтяного кокса уменьшается на 26%, с 245 до 180 мА ч/г(С), а графитового электрода уменьшается на 93%, с 310 до 22 мА ч/г(С) (рис. 5). При восстановлении плотности тока 0.2 мА/см2 (36 мА/г(С)) разрядная емкость углеродных электродов восстанавливается. Меньшее влияние плотности тока на емкость ТНК по сравнению с графитом может быть объяснено большим коэффициентом диффузии катиона лития в ТНК, меньшим удельным сопротивлением ТНК (табл. 1) и меньшим сопротивлением переноса заряда литированных электродов из ТНК (рис. 1б).
ЗАКЛЮЧЕНИЕ
Таким образом, на основе анализа влияния плотности тока на величину разрядной емкости углеродных электродов, величин коэффициентов диффузии катионов лития в углеродных материалах (термообработанный нефтяной кокс и графит), удельного объемного сопротивления углеродов показано, что углеродный материал, полученный термообработкой нефтяного кокса, обладает лучшими транспортными свойствами по сравнению с графитом и большей разрядной емкостью при высоких значениях плотности поляризующего тока. Это позволяет сделать вывод о перспективности использования нефтяного кокса в качестве активных материалов отрицательных электродов высокомощных литий-ионных аккумуляторов и псевдоконденсаторов. Однако электроды на основе термообработанного нефтяного кокса обладают высокой необратимой емкостью на 1-м зарядно-разрядном цикле. Необходимы дополнительные исследования по ее уменьшению.
Список литературы
Reddy, M.V., Mauger, A., Julien, C.M., Paolella, A., and Zaghib, K., Brief History of Early Lithium-Battery Development, Materials, 2020, vol. 13, p. 1884. https://doi.org/10.3390/ma13081884
Broussely, M., Biensan, P., and Simon, B., Lithium insertion into host materials: the key to success for Li ion batteries, Electrochim. Acta, 1999, vol. 45, p. 3. https://doi.org/10.1016/S0013-4686(99)00189-9
Liu, Y., Li, W., and Zhou, X., An investigation of Li2TiO3–coke composite anode material for Li-ion batteries, RSC Advances, 2019, vol. 9, p. 11710. https://doi.org/10.1039/C9RA02611H
Maurin, G., Bousquet, C., Henn, F., Bernier, P., Almairac, R., and Simon, B., Electrochemical lithium intercalation into multiwall carbon nanotubes: a micro-Raman study, Solid State Ionics, 2000, vol. 136–137, p. 1295. https://doi.org/10.1016/S0167-2738(00)00599-3
Химические источники тока: Справочник / Под ред. Коровина, Н.В., Скундина, А.М. М.: Изд. МЭИ, 2003. 739 с. [Chemical power sources: Handbook (in Russian)/ under review N.V. Korovina, and A.M. Skundina. Moscow: MEI, 2003, 739 p.]
Wang, G., Yu, M., and Feng, X., Carbon materials for ion-intercalation involved rechargeable battery technologies, Chem. Soc. Rev., 2021, vol. 50, 2388. https://doi.org/10.1039/d0cs00187b
Zhao, B., Ran, R., Liu, M., and Shao, Z., A comprehensive review of Li4Ti5O12-based electrodes for lithium-ion batteries: The latest advancements and future perspectives, Mater. Sci. and Engineering: R.: Reports, 2015, vol. 98, p. 1. https://doi.org/10.1016/j.mser.2015.10.001
Moshtev, R.V., Zlatilova, P., Puresheva, B., and Manev, V., Material balance of petroleum coke/LiNiO2 lithium-ion cells, J. Power Sources, 1995, vol. 56, p. 137. https://doi.org/10.1016/j.mser.2015.10.001
Чуриков, А.В., Гридина, Н.А., Чурикова, Н.В., Солопова, Т.А., Форостяный, С.А., Левин, Ф.Ю. Разработка углеродного материала для отрицательного электрода литий-ионного аккумулятора. Электрохим. энергетика. 2001. Т. 1. С. 9. [Churikov, A.V., Gridina, N.A., Churikova, N.V., Solopova, T.A., Forostyanyj, S.A., and Levin, F.Yu., Development of carbon material for negative electrode of lithium-ion battery (in Russian), Elektrohimich. energetika, 2001, vol. 1, p. 9.]
Alca’ntara, R., Lavela, P., Ortiz, G.F., Tirado, J.L., Stoyanova, R., Zhecheva, E., and Jime’nez-Mateos, J.M., Modification of Petroleum Coke for Lithium-Ion Batteries by Heat-Treatment with Iron Oxide, J. Electrochem. Soc., 2004, vol. 151, p. A2113. https://doi.org/10.1149/1.1814031
Concheso, A., Santamaría, R., Menéndez, R., Jiménez-Mateos, J.M., Alca’ntara, R., Ortiz,m G.F., Lavla, P., and Tirado, J.L., Effect of oxidation on the performance of low-temperature petroleum cokes as anodes in lithium ion batteries, J. Appl. Electrochem., 2009, vol. 39, p. 899. https://doi.org/10.1007/s10800-008-9735-8
Чудова, Н.В., Шакирова, Н.В., Кузьмина, Е.В., Колосницын, В.С. Влияние диапазона потенциалов заряда и разряда на электрохимическую емкость нефтяного кокса и графита. Башкир. хим. журн. 2021. Т. 28. С. 85. [Chudova, N.V., Shakirova, N.V., Kuzmina, E.V., and Kolosnitsyn, V.S., Influence of the range of charge and discharge potentials on the electrochemical capacity of petroleum coke and graphite, Bashkirskij himicheskij zhurnal (in Russian), 2021, vol. 28, p. 85.] https://doi.org/10.17122/bcj?2021-4-85-89
Li, W., Li, Z., Zhang, C., Liu, W., Han, C., Yan, B., An, S., and Qiu, X., Hard carbon derived from rice husk as anode material for high performance potassium-ion batteries, Solid State Ionics, 2020, vol. 351, 115319. https://doi.org/10.1016/j.ssi.2020.115319
Кузьмина, Е.В., Дмитриева, Л.Р., Карасева, Е.В., Колосницын, В.С. О возможности применения метода сорбции красителей для определения удельной поверхности углеродных материалов для литий-серных аккумуляторов. Изв. Уфим. науч. центра РАН. 2020. С. 29. [Kuzmina, E.V., Dmitrieva, L.R., Karaseva, E.V., and Kolosnitsyn, V.S., On the possibility of application of the method of sorption of dyes for determining the specific surface area of carbon materials for lithium-sulfur batteries, Izvestiya Ufimskogo nauchnogo centra RAN (in Russian), 2020, p. 29.] https://doi.org/10.31040/2222-8349-2020-0-2-29-34
Lewandowski, A., Biegun, M., Galinski, M., and Swiderska-Mocek, A., Kinetic analysis of Li|Li+ interphase in an ionic liquid electrolyte, J. Appl. Electrochem., 2012, vol. 43, p. 367. https://doi.org/10.1007/s10800-012-0515-0
Rui, X.H., Ding, N., Liu, J., Li, C., and Chen, C.H., Analysis of the chemical diffusion coefficient of lithium ions in Li3V2(PO4)3 cathode material, Electrochim. Acta, 2010, vol. 55, p. 2384. https://doi.org/10.1016/j.electacta.2009.11.096
Kaspar, J., Graczyk-Zajac, M., and Riedel, R., Determination of the chemical diffusion coefficient of Li-ions in carbon-rich silicon oxycarbide anodes by electro-analytical methods, Electrochim. Acta, 2014, vol. 115, p. 665. https://doi.org/10.1016/j.electacta.2013.10.184
Vedalakshmi, R., Saraswathy, V., Song, H.-W., and Palaniswamy, N., Determination of diffusion coefficient of chloride in concrete using Warburg diffusion coefficient, Corr. Sci., 2009, vol. 51, p. 1299. https://doi.org/10.1016/j.corsci.2009.03.017
Иванищев, А.В., Иванищева, И.А. Ионный транспорт в литиевых электрохимических системах: проблемы и решения. Электрохимия. 2020. Т. 56. С. 1002. [Ivanishchev, A.V. and Ivanishcheva, I.A., Ion transport in lithium electrochemical systems: problems and solutions, Russ. J. Electrochem., 2020, vol. 56, p. 907. https://doi.org/10.1134/S1023193520100055]10.1134/S1023193520100055] https://doi.org/10.31857/S0424857020100059
Fong, R., U. von Sacken and Dahn, J.R., Studies of lithium intercalation into carbons using nonaqueous electrochemical cells, J. Electrochem. Soc., 1997, vol. 144, p. 1195. https://doi.org/10.1149/1.2086855
Weibing, X. and Dahn, J.R., Study of Irreversible capacities for Li insertion in hard and graphitic carbons, J. Electrochem. Soc., 1997, vol. 144, p. 1195. https://doi.org/10.1149/1.1837572
Peled, E., Golodnitsky, D., Ulus, A., and Yufit, V., Effect of carbon substrate on SEI composition and morphology, Electrochim. Acta, vol. 50, p. 391. https://doi.org/10.1016/j.electacta.2004.01.130
Дополнительные материалы отсутствуют.