Физика и химия стекла, 2019, T. 45, № 2, стр. 189-195
Исследование возможности применения органических веществ как порообразователя при синтезе пеностекла
Е. А. Яценко 1, Б. М. Гольцман 1, *, В. А. Смолий 1, Н. С. Гольцман 1, Л. А. Яценко 1
1 Южно-Российский государственный политехнический университет (НПИ) имени М.И. Платова
346428 Ростовская область, г. Новочеркасск, ул. Просвещения, д. 132, Россия
* E-mail: boriuspost@gmail.com
Поступила в редакцию 31.07.2018
После доработки 27.11.2018
Принята к публикации 05.12.2018
Аннотация
Проведены исследования по применению в качестве порообразователей для пеностекла глицерина и альтернативных вещества: уксусной кислоты, желатина, крахмала, сахарозы, парафина. Рассчитаны составы шихт на основе бесцветного тарного стекла марки БТ-1 и предложенных порообразователей, проведена их термическая обработка. На основе обработки экспериментальных данных по плотности и пористости предложен оригинальный параметр, характеризующий равномерность пористой структуры, и критерии для выбора органического вещества в качестве порообразователя.
ВВЕДЕНИЕ
Стоимость пеностекла в настоящее время регламентируется, в первую очередь, сырьевой базой для его производства. Наиболее затратным является специально сваренное стекло, далее – стеклобой строго фиксированной марки. Утверждается, что только при таких условиях возможно получение высококачественного пеностекла с повышенной прочностью. Однако цена пеностекла, получаемого из такого сырья, превышает цену изделий-аналогов за счет усложнения технологии.
В связи с этим, большинство исследований в области пеностекла в последние годы направлены на расширение сырьевой базы. Главным направлением является использование боя электронно-лучевых трубок (ЭЛТ) [1, 2], а также местных алюмосиликатных сырьевых материалов и отходов промышленности: золошлаковых отходов, отходов добычи и обогащения и т.д. [3–6]. Данной тематике посвящено подавляющее большинство работ, и значительно меньше – другим технологическим параметрам синтеза пеностекла.
Формирование структуры пеностекла – сложный многофакторный процесс, влияние на который оказывает не только состав основного сырья, но и вид, и количество порообразователя, а также режим термической обработки. Известно, что структура пеностекла напрямую зависит как от типа порообразователя (карбонатный или углеродный), так и от конкретно используемого порообразующего вещества [7]. В то же время исследования по подбору порообразователя крайне редки [8, 9], а зачастую его обоснованию вообще не уделяется внимания [10–14].
Ранее нами было установлено, что глицерин является весьма эффективным видом порообразователя, что было показано на некоторых видах тарных стекол (марки БТ-1, ЗТ-1) в интервале температур 800–850°С [15]. Этому способствует ряд факторов. Во-первых, размер и распределение пор напрямую зависит от распределения порообразователя в шихте. В связи с этим, при использовании жидкофазных компонентов, отпадает необходимость в ультратонком измельчении порообразователя без снижения равномерности структуры. Во-вторых, органические вещества обладают низкой температурой горения, вследствие чего по достижении требуемой вязкости стекломассы нет необходимости в дополнительном нагреве для разложения порообразователя.
Глицерин в качестве порообразователя применяется на ряде крупных предприятий, однако его основным недостатком является высокая, в сравнении с традиционными порообразователями, цена. Поэтому в качестве альтернативы глицерину для данного исследования были выбраны более дешевые органические вещества: уксусная кислота, желатин, крахмал, сахароза, парафин.
ЭКСПЕРИМЕНТАЛЬНАЯ ЧАСТЬ
В качестве объекта эксперимента был выбран основной состав, мас. %: бой стекла марки БТ-1 (ГОСТ Р 52022-2003) – 90; стекло натриевое жидкое марки Б (ГОСТ 13078-81) – 4; вода – 3; порообразователь – 3 [16]. В качестве порообразователей использовали в составе № 1 – глицерин марки “ч. д. а.” (ГОСТ 6259-75), № 2 – кислоту уксусную 70%-ную (ГОСТ Р 55982-2014), № 3 – желатин марки Т-9 (ГОСТ 11293-89), № 4 – крахмал картофельный второго сорта (ГОСТ Р 53876-2010), № 5 – сахарозу марки “ч. д. а.” (ГОСТ 5833-75), № 6 – парафин марки П-2 (ГОСТ 23683-89).
Синтез образцов производился порошковым методом. Порошок стекла измельчался до размера 210 мкм и высушивался при 110°C. Порообразующая смесь готовилась в отдельном сосуде путем смешивания компонентов (жидкое стекло, глицерин, вода) в заданном соотношении. Подготовленные сырьевые материалы смешивались в течение 30 минут в барабанной мельнице. Далее из полученной шихты формовались образцы в виде кубов с длиной грани 20 мм. Полученные образцы загружались в разогретую до 600°С электрическую муфельную печь, где подвергались термической обработке согласно рис. 1. Температурно-временной режим синтеза пеностекла включал следующие стадии: нагрев, вспенивание, двухстадийное охлаждение: быстрое (20–25°С/мин) для фиксации структуры и медленное (2–3°С/мин) для устранения термических напряжений. Извлечение образцов производилось по достижении температурой внутри печи 30°С.
Рис. 1.
Температурно-временной режим синтеза пеностекла: 1 – нагрев; 2 – вспенивание; 3 – резкое охлаждение (фиксация структуры); 4 – медленное охлаждение.
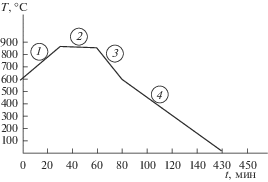
Для расчета средней плотности размеры образцов (обработанных до правильной формы) определялись с помощью штангенциркуля с точностью до 0.01 мм, а масса – на аналитических весах с точностью до 0.01 г. Размеры пор определяли с помощью электронно-микроскопического анализа с применением последующей компьютерной обработки.
Микроструктура образцов была исследована с использованием растрового электронного микроскопа VEGA II LMU (фирмы Tescan). Изображения получены с использованием детекторов BSE (детектор отраженных электронов) и SE (детектор вторичных электронов). Результаты химического анализа образцов получены с применением систем энергодисперсионного микроанализа INCA ENERGY 450/XT (детектор Silicon Drift (ADD)).
ЭКСПЕРИМЕНТАЛЬНЫЕ РЕЗУЛЬТАТЫ И ИХ ОБСУЖДЕНИЕ
На рис. 2 представлен внешний вид образцов пеностекла на основе различных порообразователей при температурах вспенивания 800, 825, 850°С. Для описания пористых материалов обычно используется величина плотности, зная которую можно предсказать другие свойства (прочность, теплопроводность, пористость и пр.). Однако плотность не может охарактеризовать размер и равномерность распределения пор в образце, а также наличие дефектов. В то же время стабильность размера и распределения пор напрямую влияет на все свойства материала и его изотропность. Вследствие этого был введен коэффициент равномерности, показывающий отношение пор максимального размера к порам минимального размера, описываемый уравнением (1). Чем больше данная величина, тем больше разница в размерах пор и тем ниже равномерность структуры.
где Dmax – диаметр наибольшей поры, мм; Dmin – диаметр наименьшей поры, мм.Полученные свойства образцов пеностекла представлены в табл. 1. За диаметр принималось среднее арифметическое двух замеров диаметра поры, сделанных перпендикулярно.
Таблица 1.
Плотность и коэффициент равномерности пеностекла на основе различных порообразователей
Т, °C | Состав | Состав | ||||||||||
---|---|---|---|---|---|---|---|---|---|---|---|---|
1 | 2 | 3 | 4 | 5 | 6 | 1 | 2 | 3 | 4 | 5 | 6 | |
cредняя плотность, кг/м3 | коэффициент равномерности | |||||||||||
800 | 230 | 800 | 970 | 1351 | 593 | 995 | 1.1 | 1.2 | 2.8 | 1.4 | 5.7 | 12.2 |
825 | 175 | 515 | 964 | 675 | 406 | 494 | 1.0 | 1.1 | 3.1 | 1.5 | 5.5 | 21.1 |
850 | 149 | 367 | 773 | 602 | 222 | 265 | 1.0 | 1.1 | 3.9 | 3.6 | 5.4 | 47.4 |
Здесь следует также заметить, что минимальный размер пор для всех образцов составлял порядка 300–400 мкм, тогда как максимальный размер сильно варьировался в зависимости от порообразователя.
Как видно из полученных данных, применение всех органических порообразователей привело к формированию пор в образце. Однако их количество, размер и распределение сильно зависит от конкретного вещества. Можно объединить использованные порообразователи в три группы: высокоуглеродистые (сахароза, парафин), низкоуглеродистые (глицерин, уксусная кислота), естественного происхождения (желатин, крахмал).
Крахмал и желатин демонстрируют низкую эффективность в качестве порообразователя. Образцы с их применением даже при максимальной температуре вспенивания обладают плотностью более 600 кг/м3. Несмотря на сравнительно небольшой коэффициент равномерности (1.4–3.9), в образцах присутствуют большие невспененные области, а поры сосредоточены в центре образца. Подобный комплекс свойств делает данную группу практически непригодной для использования в качестве порообразователей.
Группа высокоуглеродистых материалов продемонстрировала более высокую склонность к порообразованию. Использование парафина при температурах выше 825°C ведет к активному вспениванию со снижением плотности до 265 кг/м3. Однако полученная структура обладает крайней неравномерностью (коэффициент равномерности до 47.4), что позволяет рекомендовать этот материал лишь в качестве микродобавки для интенсификации вспенивания. Образцы с применением сахарозы при более низкой плотности 220 кг/м3 обладают гораздо более равномерной структурой, однако присутствует большая разница размера пор между краями и серединой образца (коэффициент равномерности 5.4–5.7), что нежелательно и требует доработки шихты.
При использовании низкоуглеродистых материалов удалось достичь наиболее равномерной структуры (коэффициентом равномерности 1.0–1.2). Образцы с уксусной кислотой, несмотря на это, обладают сравнительно высокой плотностью более 350 кг/м3. Этот показатель, вероятно, может быть понижен за счет увеличения количества вводимой кислоты, однако целесообразность этого требует дополнительного изучения. Глицерин демонстрирует наилучшие показатели: плотность порядка 150 кг/м3 и коэффициент равномерности, близкий к 1. Таким образом, из всех исследованных материалов наиболее равномерной структурой обладали образцы на основе уксусной кислоты и глицерина.
Очевидно, что различия в структуре образцов заключаются в природе и строении порообразователей. При этом можно выявить корреляцию между растворимостью материала и равномерностью пористой структуры. Жидкофазные материалы – глицерин и уксусная кислота – позволили получить пеностекло с наибольшей равномерностью, далее, в порядке понижения растворимости “сахароза–желатин–крахмал–парафин” равномерность структуры также снижается.
Была исследована микроструктура образцов оптимальных составов. Результаты представлены на рис. 3. Как видно из рисунка, образцы обоих составов обладают весьма схожей структурой – закрытые поры диаметром 300–500 мкм, разделенные тонкими стенками из стекловидного вещества, внутри которых также наблюдаются закрытые микропоры. Более высокая плотность состава 2 обусловленa большей толщиной межпоровых стенок (30–90 мкм) в сравнении с составом 1 (10–40 мкм), а также малым количеством закрытых микропор внутри стенок. Это, в свою очередь, объясняется наличием меньшего количества углерода для вспенивания [7] в уксусной кислоте (2 атома) по сравнению с глицерином (3 атома).
Рис. 3.
Электронно-микроскопический снимок: (a) – состав 1 (глицерин); (б) – состав 2 (уксусная кислота). 1 – микрочастицы углерода; 2 – межпоровые стенки с микропорами.
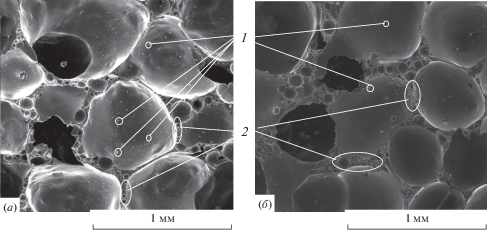
Также на фотографиях видны микрочастицы углерода, адсорбировавшиеся на стенках пор и не вступивших в реакцию окисления. Сравнивая количество частиц углерода на рис. 3, а также цвет образцов на рис. 2 видно, что образцы состава 1 более темные, и частиц углерода в их порах больше. Это дополнительно подтверждает различия в количестве вводимого углерода и необходимость контроля данного параметра при выборе порообразователя.
Результаты элементного анализа образцов (рис. 4) указывают, что основными элементами в стекле являются O, Si, Na, Ca с добавками K, Al, Mg. Эти результаты были ожидаемы, поскольку для вспенивания использовался бой тарного стекла марки БТ-1, состоящий из этих элементов. Помимо этого, важно отметить, что анализ выявил углерод в количестве десятых долей процента, что дополнительно подтверждает адсорбцию частиц углерода на стенках пор.
ЗАКЛЮЧЕНИЕ
Таким образом, была исследована возможность применения различных видов органических веществ в качестве порообразователя при синтезе пеностекла на основе боя тарного стекла. Установлено, что при применении жидкофазных (глицерин, уксусная кислота) или хорошо растворимых в воде (сахароза) веществ удается получить равномерную пористую структуру с плотностью 150–350 кг/м3. Также на интенсивность вспенивания влияет количество атомов углерода в молекуле порообразователя. В ряде случаев необходимы дополнительные исследования по оптимизации состава или режима термообработки. Полученные результаты позволяют корректировать состав пеностекла в зависимости от региона его производства, что повышает его конкурентоспособность.
Работа выполнена при финансовой поддержке Российского научного фонда, Проект № 18-19-00455 “Разработка технологии комплексной защиты трубопроводов для нефти и газа, эксплуатируемых в условиях Дальнего Востока России” в рамках конкурса 2018 года “Проведение фундаментальных научных исследований и поисковых научных исследований отдельными научными группами”.
Список литературы
König J., Petersen R.R., Yue Y. Fabrication of highly insulating foam glass made from CRT panel glass // Ceramics International. 2015. V. 41. № 8. P. 9793–9800.
Guo H.W., Gong Y.X., Gao S.Y. Preparation of high strength foam glass–ceramics from waste cathode ray tube // Materials Letters. 2010. V. 64. № 8. P. 997–999.
Kazmina O.V., Tokareva A.Y., Vereshchagin V.I. Using quartzofeldspathic waste to obtain foamed glass material // Resource-Efficient Technologies. 2016. V. 2. № 1. P. 23–29.
Yin H., Ma M., Bai J., Li Y., Zhang S., Wang F. Fabrication of foam glass from iron tailings // Materials Letters. 2016. V. 185. P. 511–513.
Monich P.R., Romero A.R., Höllen D., Bernardo E. Porous glass-ceramics from alkali activation and sinter-crystallization of mixtures of waste glass and residues from plasma processing of municipal solid waste // J. Cleaner Production. 2018. V. 188. P. 871–878.
Attila Y., Güden M., Taşdemirci A. Foam glass processing using a polishing glass powder residue // Ceramics International. 2013. V. 39. № 5. P. 5869–5877.
Шилл Ф. Пеностекло. М.: Стройиздат, 1965. 327 с.
Østergaard M.B., Petersen R.R., König J., Johra H., Yue Y. Influence of foaming agents on solid thermal conductivity of foam glasses prepared from CRT panel glass // J. Non-Crystalline Solids. 2017. V. 465. P. 59–64.
König J., Petersen R.R., Yue Y., Suvorov D. Gas-releasing reactions in foam-glass formation using carbon and MnxOy as the foaming agents // Ceramics International. 2017. V. 43. № 5. P. 4638–4646.
Rangel E.M., Carvalho C.D.O., Arsand D.R. Synthesis of foam glass with immobilized zinc oxide for photodegradation of alizarin S in aqueous solution // Periodico Tche Quimica. 2018. V. 15. № 29. P. 75–81.
Shi H., Feng K.-Q., Wang H.-B., Chen C.-H., Zhou H.-L. Influence of aluminium nitride as a foaming agent on the preparation of foam glass-ceramics from high-titanium blast furnace slag // International J. Minerals, Metallurgy and Materials. 2016. V. 23. № 5. P. 595–600.
Petersen R.R., König J., Yue Y. The mechanism of foaming and thermal conductivity of glasses foamed with MnO2 // J. Non-Crystalline Solids. 2015. V. 425. P. 74–82.
Petersen R.R., König J., Smedskjaer M.M., Yue Y. Effect of Na2CO3 as foaming agent on dynamics and structure of foam glassmelts // J. Non-Crystalline Solids. 2014. V. 400. P. 1–5.
Wu L., Zhao Y.H., Chen R.F., Yang H., Li Q.Q., Li Z.L., Lu H.F. Effect of manganese dioxide on structure and compressive strength of foam glass // Applied Mechanics and Materials. 2014. V. 488. P. 94–97.
Yatsenko E.A., Goltsman B.M., Smoliy V.A., Kosarev A.S., Bezuglov R.V. Investigation of the influence of foaming agent’s type and ratio on the foaming and reactionary abilities of foamed slag glass // Biosciences Biotechnology Research Asia. 2015. V. 12. P. 625–632.
Yatsenko E.A., Gol’tsman B.M., Kosarev A.S., Karandashova N.S., Smolii V.A., Yatsenko L.A. Synthesis of foamed glass based on slag and a glycerin pore-forming mixture // Glass Physics and Chemistry. 2018. V. 44. № 2. P. 152–155.
Дополнительные материалы отсутствуют.
Инструменты
Физика и химия стекла