Физика и химия стекла, 2021, T. 47, № 1, стр. 86-92
Роль жидкой фазы в формировании фазового состава и свойств строительной облицовочной керамики
Н. Д. Яценко 1, *, Н. А. Вильбицкая 1, А. И. Яценко 1
1 Южно-Российский государственный политехнический университет (НПИ) им. М.И. Платова
346428 Новочеркасск, ул. Просвещения, 132, Россия
* E-mail: natyacen@yandex.ru
Поступила в редакцию 18.03.2020
После доработки 02.09.2020
Принята к публикации 08.10.2020
Аннотация
Установлена роль жидкой фазы в формировании микрострукутры керамической облицовочной плитки с различными физико-техническими свойствами. Выявлено влияние природы сырьевых материалов и соотношения щелочных и щелочноземельных оксидов на образование при низкотемпературном обжиге различных кальцийсодержащих кристаллических фаз.
ВВЕДЕНИЕ
Особенность производства керамической облицовочной плитки заключается в скоростном обжиге, что затрудняет завершение формирования ее фазового состава и микроструктуры и влияет на свойства готовой продукции.
Для ускорения фазообразования в состав масс вводят плавни в виде природного сырья – нефелинового сиенита, пегматита, перлита или синтезированного стеклобоя, что очень часто вызывает снижение интервала спекания, значительную огневую усадку и деформацию плитки.
Для решения этой проблемы российскими и зарубежными учеными разработан целый ряд технологий по производству фаянсовой малоусадочной керамической облицовочной плитки [1–3]. В качестве сырьевого компонента массы использовано кальцийсодержащее природное и техногенное сырье в виде мела, доломита, высококальциевых отходов различных производств, обусловливающее получение известкового фаянса, характеризующегося низкими прочностными свойствами [4, 5].
В связи с этим как с научной, так и с практической точки зрения несомненный интерес представляет управление процессами формирования микроструктуры, фазового состава и свойств керамической плитки на основе глинисто-карбонатного сырья при температурах обжига 1000–1050°С. Интенсификация процессов спекания таких масс происходит путем ввода щелочных природных и синтезированных материалов, а также при определенном соотношении оксидов щелочных (R2O) и щелочноземельных (RO) металлов [6–8].
ЭКСПЕРИМЕНТАЛЬНАЯ ЧАСТЬ
Для исследований были разработаны составы масс на основе местного глинистого тугоплавкого сырья Ростовской области (глина Владимировского месторождения Ростовской области (ВКС) с содержанием оксида железа от 1.8–2.5%, нефелинового сиенита, песка и высококальциевого отхода, образующегося при очистке воды методом известкования на ГРЭС, ТЭС и атомных электростанциях. Химические составы сырьевых материалов и масс приведены в табл. 1, 2.
Таблица 1.
Химический состав сырьевых материалов
Наименование сырья |
Содержание оксидов | Сумма | |||||||
---|---|---|---|---|---|---|---|---|---|
SiO2 | Al2O3+ TiO2 | Fe2O3 | CaO | MgO | К2O | Na2O | ппп | ||
Глина владимировская (ВКС) |
59.48 | 23.86 | 2.29 | 0.83 | 1.39 | 3.48 | – | 9.67 | 100.0 |
Нефелинсиенит | 48.20 | 25.40 | 2.10 | 2.30 | 1.50 | 8.20 | 11.1 | 1.2 | 100.0 |
Песок владимировский | 97.34 | 0.65 | ─ | 0.12 | 0.32 | 0.41 | – | 0.73 | 100.0 |
Отход высококальци-евый (ОВК) | 1.93 | 0.92 | 2.64 | 48.63 | 3.36 | 0.10 | 0.30 | 42.12 | 100.0 |
Таблица 2.
Химический состав разработанных масс
№ композиции | Содержание оксидов | RO/ R2O | ||||||||
---|---|---|---|---|---|---|---|---|---|---|
SiO2 | Al2O3 | TiO2 | Fe2O3 | CaO | MgO | К2O | Na2O | ппп | ||
1 | 55.0 | 24.9 | 0.7 | 1.3 | 2.2 | 2.3 | 3.2 | 2.3 | 8.8 | 0.8 |
2 | 46.7 | 18.7 | 0.6 | 3.3 | 10.5 | 1.3 | 3.2 | 2.2 | 12.3 | 2.1 |
3 | 47.3 | 17.4 | 0.5 | 3.7 | 10.6 | 1.5 | 2.8 | 1.8 | 11.8 | 2.6 |
4 | 51.7 | 15.2 | 0.5 | 4.1 | 10.6 | 1.5 | 2.2 | 1.3 | 10.9 | 3.6 |
5 | 54.3 | 13.2 | 0.4 | 4.4 | 10.7 | 1.4 | 1.7 | 1.1 | 10.4 | 4.3 |
6 | 55.0 | 12.3 | 0.4 | 4.8 | 10.9 | 1.3 | 1.6 | 1.0 | 9.7 | 4.7 |
Исходные сырьевые материалы измельчали мокрым способом в фарфоровом барабане до прохождения через сито № 0063 (9426 отв./см2) в соответствии с ГОСТ 6613-86 с остатком 2–2.5%. Шликер высушивали до влажности пресспорошка 7–8%, просеивали через сито № 1 (51 отв./см2), формовали плитки размером 50 × 50 × 5 и кубики 50 × 50 × 50 мм способом полусухого формования на гидравлическом прессе под давлением 20 МПа. Образцы обжигали в лабораторной муфельной печи с автоматическим регулируемым скоростным режимом обжига при температурах 950–1050°C. Общее время обжига с изотермической выдержкой при максимальной температуре в течение 20 мин составило 100 мин. При этом скорость повышения температуры до максимальной составила 25°C/мин, скорость охлаждения 18–20°C/мин с помощью принудительной вентиляции.
Исследования послеобжиговых свойств (водопоглощения, предела прочности на сжатие) керамических образцов проводили в соответствии с существующими стандартными методиками [9, 10].
Для определения фазового состава керамического черепка на основе керамических масс, отличающихся содержанием щелочных (Na2O, K2O) и щелочноземельных (CaO, MgO) катионов проводили рентгенофазовые исследования с использованием дифрактометра ДРОН-3. Данные исследования позволили установить влияние природы сырьевых материалов и количества щелочных и щелочноземельных оксидов на образование кальцийсодержащих фаз.
РЕЗУЛЬТАТЫ И ОБСУЖДЕНИЕ
С учетом влияния на эти процессы щелочных и щелочноземельных оксидов установлена зависимость основных свойств черепка от их соотношения. В исследуемых массах соотношение RO/R2O изменяется от 0.8 до 4.7. При этом оптимальные результаты по водопоглощению (согласно требованиям ГОСТ 6141-91) достигаются как при соотношении 0.8, так и 4.3–4.7 (рис. 1).
Рис. 1.
Зависимость водопоглощения от соотношения RO/R2O при различных температурах обжига, °С: 1 – 950, 2 – 1000; 3 – 1050.
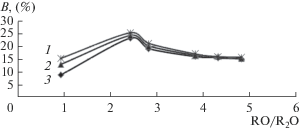
Черепок с водопоглощением не более 16% (по ГОСТ) формируется при температуре обжига 950°С. Соотношение RO/R2O должно находиться в пределах не более 1.0 мас. % с низким содержанием СаО и в пределах 4.3–4.7 мас. % с высоким содержанием СаО. Повышение температуры обжига до температуры 1050°С расширяет интервал оптимальных значений RO/R2O от 3.6 до 4.7 для высококальциевых масс и до 1.8 для масс с низким содержанием СаО.
В формировании исследуемых структур важную роль играют процессы, происходящие при низких температурах, которые, в конечном итоге, обеспечивают свойства черепка. При соотношении RO/R2O менее 1.0, (композиция 1, табл. 2), наличие щелочных компонентов (5.5%) приводит к образованию жидкой фазы. Спекание наблюдается за счет жидкофазовых процессов, со значительной усадкой (табл. 3), а в высококальциевых тонкодисперсных массах (композиции 5, 6) формирование малоусадочной структуры происходит в результате низкотемпературных процессов кристаллизации и повышенной пористости черепка.
Таблица 3.
Послеобжиговые свойства керамических образцов
№ композиции | Свойства черепка | ||||
---|---|---|---|---|---|
водопоглощение, %, при температурах, °С | усадка, % при 950°С | прочность на сжатие (МПа) при 950°С | |||
950 | 1000 | 1050 | |||
1 | 16.8 | 13.7 | 12.3 | 1.5 | 50.0 |
2 | 24.8 | 24.0 | 23.0 | 1.3 | 40.0 |
3 | 21.2 | 20.0 | 19.0 | 1.0 | 42.0 |
4 | 18.0 | 17.7 | 16.5 | 0.8 | 44.0 |
5 | 16.5 | 16.0 | 15.8 | 0.5 | 48.0 |
6 | 16.0 | 16.0 | 15.5 | 0.5 | 48.0 |
Формирование фазового состава и микроструктуры керамической плитки зависит и от природы используемых сырьевых материалов [11–13]. Для образования необходимого количества жидкой фазы в черепке, интенсифицирующей процесс спекания, в составы масс вводили природные и синтезированные щелочесодержащие материалы в виде пегматита (K2O + Na2O = 7.25%) и стеклобоя (K2O + Na2O = 14.6%). Кальцийсодержащие материалы, являющиеся основой для формирования кристаллических фаз, вводили в различном количестве в виде мела или высококальциевого отхода (ОВК) химводоочистки электростанций.
Исходя из заданного химического состава и установленных оптимальных соотношений RO/R2O = 1.2 и 4.3–4.7 разработали шихтовые составы масс (табл. 4), в которых содержание мела меняется от 2.7 до 18.2%, ОВК от 3.1 до 19.8%, пегматита от 30.7 до 62.9%, стеклобоя от 15.2 до 30.6%, что обеспечивает соотношение RO/R2O 1.2 и 4.7.
Таблица 4.
Составы масс шихты
№ п/п | Материалы | Содержание компонентов, % по массе, в композициях | |||||||
---|---|---|---|---|---|---|---|---|---|
1 | 2 | 3 | 4 | 5 | 6 | 7 | 8 | ||
1 | Глина | 38.5 | 55.3 | 60.7 | 26.9 | 54.3 | 37.8 | 26.7 | 60.5 |
2 | Песок | 12.0 | 13.7 | 6.0 | 2.6 | 13.3 | 11.7 | 2.6 | 5.9 |
3 | Пегматит | 31.3 | ─ | ─ | 63.4 | ─ | 30.7 | 62.9 | ─ |
4 | Стеклобой | ─ | 15.2 | 30.6 | ─ | 15.0 | ─ | ─ | 30.5 |
5 | Мел | 18.2 | 15.8 | 2.7 | 7.1 | ─ | ─ | ─ | ─ |
6 | ОВК | ─ | ─ | ─ | ─ | 17.4 | 19.8 | 7.9 | 3.1 |
Сумма | 100.0 | 100.0 | 100.0 | 100.0 | 100.0 | 100.0 | 100.0 | 100.0 | |
RO/R2O | 4.7 | 4.7 | 1.2 | 1.2 | 4.7 | 4.7 | 1.2 | 1.2 |
Подготовку керамического шликера, формование, сушку и обжиг образцов проводили согласно ранее приведенной методике. Свойства исследуемых образцов (табл. 5 ) показывают, что в образцах составов 1, 4, 6, 7 формируется малоусадочная структура. При этом в качестве щелочесодержащего компонента содержится пегматит и не наблюдается зависимости от количества вводимого кальцийсодержащего материала и его вида (мела и ОВК). Водопоглощение этих образцов составляет 16–17% за исключением образца состава 6, водопоглощение которого более 20%. В нем содержание пегматита наименьшее и составляет 30.7%. Все образцы, содержащие стеклобой (составы 2, 3, 5, 8) также независимо от содержания кальцийсодержащего компонента и материала, которым он вводится, имеют высокую усадку – 1.2% (состав 5, содержание стеклобоя 15%) до 2.30% при максимальном содержании стеклобоя 30.6% в составе 3. Водопоглощение этих образцов составляет от 5.3 до 12.8%. Прочность образцов на сжатие на основе пегматита значительно ниже, от 11.78 до 23.85 МПа.
Таблица 5.
Физико-химические свойства образцов
№ композиции | Содержание оксидов, мас. % | RO/R2O | Огневая усадка, % | Водопоглощение, % | Прочность на сжатие, МПа | |
---|---|---|---|---|---|---|
RO | R2O | |||||
1 | 12.33 | 2.60 | 4.7 | 0.35 | 16.43 | 23.95 |
2 | 12.07 | 2.55 | 4.7 | 1.85 | 11.09 | 32.60 |
3 | 5.66 | 4.73 | 1.2 | 2.30 | 5.35 | 49.14 |
4 | 5.10 | 4.22 | 1.2 | –1.00 | 16.24 | 11.78 |
5 | 12.51 | 2.73 | 4.7 | 1.20 | 12.82 | 38.58 |
6 | 12.94 | 2.64 | 4.7 | 0.15 | 20.62 | 19.26 |
7 | 6.37 | 5.12 | 1.2 | –0.50 | 16.94 | 13.86 |
8 | 6.18 | 5.05 | 1.2 | 2.25 | 7.39 | 46.41 |
Полученные результаты свидетельствуют о формировании различных по фазовому составу и свойствам микроструктур, что подтверждается рентгенофазовыми исследованиями (рис. 2).
Рис. 2.
Рентгенограммы керамических образцов составов 1–8, полученных обжигом при температуре 1000°С: ⚫ – кварц; ◻ – анортит; ◼ – волластонит; ◀ – мелилит; ⚪ – микроклин.
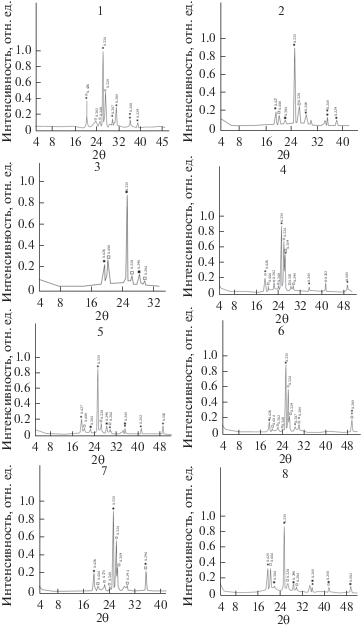
На рентгенограммах всех исследуемых образцов идентифицирована кристаллическая фаза β-кварца с дифракционными максимумами, нм: (0.429, 0.336, 0.245, 0.228). Остальной фазовый состав отличается в зависимости от используемых сырьевых материалов. Все образцы на основе пегматита (композиции 1, 4, 6, 7) содержат преимущественно низкотемпературную форму калиевого полевого шпата (микроклина) с дифракционными максимумами, нм (0.382, 0.348, 0.325), что свидетельствует о том, что его полного перехода в расплав не произошло. В образцах присутствует анортит (0.404, 0.320, 0.313 нм) и высококальциевый твердый раствор мелилитового ряда (0.307, 0.285, 0.245 нм), зависит от содержания СаО.
Образцы, содержащие в качестве щелочесодержащего компонента стеклобой (композиции 2, 3, 5, 8), отличаются наличием, помимо анортита, кристаллической фазы волластонита (0.384, 0.298, 0.248 нм). Это приводит к повышению прочностных свойств керамического черепка (от 32.6 до 49.1 МПа; табл. 5 ), но с повышенной усадкой. Формирование малоусадочной структуры с повышенной пористостью и пониженной прочностью обеспечивается кристаллизацией анортита и мелилита при меньшем содержании стеклофазы (композиции 1, 4, 6, 7).
Относительное количественное соотношение формирующихся кристаллических фаз, согласно интенсивности дифракционных максимумов, приведенных на рис. 3, значительно отличается как в образцах на основе пегматита, так и на основе стеклобоя.
В образцах на основе пегматита присутствует микроклин (калиевый полевой шпат), количество которого зависит от содержания пегматита в массе. Наибольшее количество анортита образуется в образцах составов 4 и 7, в присутствии значительного количества R2O (4.22 и 5.12% соответственно) и отсутствии других кальцийсодержащих фаз. В образцах 1 и 6, содержащих максимальное количество СаО, введенного мелом и ОВК, наблюдается приблизительно одинаковое содержание, но в меньшем количестве, анортита и мелилитового твердого раствора.
В образцах на основе стеклобоя количество волластонита, согласно интенсивности дифракционных пиков, практически одинаково, а количество анортита уменьшается при снижении содержания в массе СаО. Эти результаты свидетельствуют о том, что первоначально образуется волластонит, а оставшийся от его образования СаО идет на формирование анортита.
При избытке жидкой фазы, образующейся за счет стеклобоя, процессы кристаллизации при температурах 950–1050°С происходят по следующей реакции:
2(Al2O3 ∙ 2SiO2) + 4CaO = 2(CaO–SiO2) + CaO–Al2O3 ∙ 2SiO2 + CaO–Al2O3.
В присутствии пегматита при температурах 950–1000°С происходит формирование кальцийсодержащих кристаллических фаз, первоначально твердого раствора мелилитового ряда, непосредственно с участием СаСО3. При более высоких температурах (выше 1000°С) образуется анортит после образования СаО по реакции:
Al2O3 ∙ 2SiO2 + CaO = CaO ∙ Al2O3 ∙ 2SiO2.
Полученные результаты свидетельствуют о том, что природа кальцийсодержащих кристаллических фаз зависит от скорости процесса декарбонизации, на которую существенное влияние оказывает жидкая фаза и ее количество. В образцах на основе стеклобоя происходит образование волластонита при непосредственном взаимодействии метакаолинита с СаО, скорость образования которого, как показывают проведенные исследования, значительно выше в присутствии жидкой фазы, а затем анортита с остатком СаО, обеспечивая высокую прочность структуры, сцементированной значительным количеством стеклофазы с повышенной усадкой.
При наличии пегматита, который при температурах до 1000°С не расплавляется (температура его плавления выше 1200°С), скорость процесса декарбонизации ниже. Формирование структуры зависит от количества карбонатного материала. При содержании СаО более 10% из-за более медленного процесса декарбонизации часть неразложившегося СаСО3 с метакаолинитом образует кальцийсодержащий твердый раствор мелелито-геленитового ряда, а другая часть уже образовавшегося СаО идет на формирование анортита. В этих же образцах с содержанием СаО 5–6 мас. % образуется только анортит. Отсутствие значительного количества жидкой фазы и поризация массы приводит к формированию черепка с повышенной пористостью и низкой усадкой (табл. 5 ).
ЗАКЛЮЧЕНИЕ
Управление фазовым составом и микроструктурой формирующегося черепка керамической облицовочной плитки, для которой важнейшими свойствами наряду с водопоглощением и прочностью является низкая усадка, обеспечивается при использовании глинисто-карбонатных шихт и щелочесодержащего компонента, обусловливающих образование преимущественно кристаллических структур за счет регулирования физико-химических процессов в условиях низкотемпературного обжига.
Список литературы
Yatsenko N.D., Zubekhin A.P., Golovanova S.P., Rat’kova V.P., Vil’bitskaya N.A. An efficient technology for production of faience articles using calcium-containing waste // Glass and Ceramics. 1999. T. 56. № 9–10. C. 271–273.
Кочан И.С., Дятлова Е.М. Малоусадочные плитки с использованием кальций содержащих пород // Стекло и керамика. 1990. № 12. С. 4–6.
Рыщенко М.И., Лисачук Г.В. Повышение эксплуатационных свойств керамики. Харьков:Вища. шк., 1987. 104 с.
Yatsenko N.D., Vil’bitskaysa N.A., Golovanova S.P., Zubekhin A.P., Rat’kova V.P. Intensification of sintering of calcium-bearing ceramic // Glass and Ceramics. 2000. T. 57. № 9–10. C. 318–321.
Мороз В.И. Влияние мела на образование кристаллических фаз из глинистых минералов и полиминеральных глин // Стекло и керамика. 1978. № 4. С. 23
Яценко Н.Д., Вильбицкая Н.А., Голованова С.П., Зубехин А.П., Ратькова В.П. Влияние щелочноземельного модуля на интенсификацию спекания кальцийсодержащих керамических масс // Качество, безопасность энерго- и ресурсосбережения в промышленности строительных материалов и строительстве на пороге ХХ1 в.: Сб. докл, Междунар. науч. практ. конф., 2000. Ч. 2. С. 63–64.
Яценко Н.Д., Вильбицкая Н.А., Голованова С.П., Зубехин А.П., Липкин М.С. Использование комплексного минерализатора в интенсификации спекания высококальциевых масс // Изв. Вузов. Сев.-Кавк. Регион. Техн. науки. 2002. № 2. С.93–96.
Яценко Н.Д., Голованова С.П., Лихота О.В., Вильбицкая Н.А. Влияние природы сырьевых материалов и минерализаторов на спекание керамических масс // Вестник БГТУ. 2003. № 5. Ч. 2. С. 287–289.
ГОСТ 7025-91 “Кирпич и камни керамические и силикатные. Методы определения водопоглощения, плотности и контроля морозостойкости”. М.: Стандартинформ, 2006. 16 с.
ГОСТ 8462-85 “Материалы стеновые. Методы определения пределов прочности при сжатии и изгибе”. М.: ИПК Издательство стандартов, 2001. 7 с.
Зубехин А.П., Голованова С.П., Яценко Е.А., Яценко Н.Д. Научные основы спекания в силикатных технологиях // Техника и технология силикатов. 2014. Т. 21. № 2. С. 16–19.
Зубехин А.П., Яценко Н.Д. Теоретические основы инновационных технологий строительной керамики // Строительные материалы. 2014. № 1–2. С. 88–92.
Vil'bitskaya N.A., Golovanova S.P., Zubekhin A.P., Yatsenko N.D. Intensification of sintering of ceramic tiles using high-calcium waste products and lithium-containing mineralizers // Glass and Ceramics. 2002. T. 4. C. 21.
Yatsenko N.D., Vil’bitskaya N.A., Chernyshev V.M., Zakarlyuka S.G., Yatsenko A.I. Control of structure and phase formation in the development of low-temperature technologies based on clay-containing raw material // Glass and Ceramics. 2017. T. 73. № 11–12. C. 446–449.
Дополнительные материалы отсутствуют.
Инструменты
Физика и химия стекла