Неорганические материалы, 2019, T. 55, № 6, стр. 597-603
Синтез и абразивные свойства нанодисперсных модифицированных твердых растворов оксидов алюминия и железа
Л. Ф. Королева *
Институт машиноведения УрО Российской академии наук
620049 Екатеринбург, ул. Комсомольская, 34, Россия
* E-mail: lq@imach.uran.ru
Поступила в редакцию 08.05.2018
После доработки 12.12.2018
Принята к публикации 16.01.2019
Аннотация
Методами РФА, ИК-спектроскопии, химического анализа выявлены закономерности формирования нанодисперсных твердых растворов на основе Al2 – хFeхO3 и Fe2 – yAlyO3, модифицированных диоксидом молибдена, диоксидом циркония и оксидом иттрия, полученных в результате термообработки аммонийных гидроксокарбонатных комплексов типа NH4Al2Fe(OH)5(CO3)2. Установлено, что введение модифицирующих оксидов до 0.005 мол. % обеспечивает увеличение полирующей способности в процессе финишного полирования цветных металлов и сплавов (медь, латунь) в 5–7 раз по сравнению с оксидом алюминия-железа без модифицирования, что объясняется повышенной химической активностью абразивного материала. Для полирования титана более эффективным является модифицированный оксид алюминия-железа, содержащий 0.001–0.003 мол. % Y2O3. При этом достигается шероховатость поверхности Ra 0.005–0.006 мкм.
ВВЕДЕНИЕ
В прецизионном машиностроении, приборостроительной и электронной промышленностях требуется качественная обработка поверхности металлов с получением шероховатости до 5 нм, что гарантирует необходимые эксплуатационные характеристики, надежность приборов. В электронике полирование с получением наношероховатой поверхности существенно определяет последующие процессы эпитаксии и нанесения различных слоев: диэлектрических, отражающих, пропускающих, проводящих. В оптоэлектронике обеспечивается переход от субмикронных к нанометрическим размерам топологических элементов новых приборов с применением поверхностных слоев толщиной 5–15 нм и минимальным геометрическим рельефом. Шероховатость поверхности исходной подложки является одним из основных факторов, влияющих на качество интерфейсов многослойных зеркал рентгеновского диапазона длин волн, и, в конечном итоге, на их отражательные характеристики.
Обычно для получения минимально шероховатой поверхности механическим полированием применяют абразивные дисперсные материалы c высокой твердостью, например наноалмазные порошки, как природные, так и синтетические, а также карбиды бора и кремния, кубический нитрид бора с зернистостью от 0.01–0.3 до 6–10 мкм, находят применение и ультрамикропорошки на основе корунда. При использовании этих материалов отмечаются длительность и многостадийность процесса. Обычно доводочное полирование прецизионных изделий осуществляется за 3–5 операций с последовательным уменьшением зернистости абразива в составе паст и суспензий, используемых на операциях предварительной, чистовой и тонкой доводки [1–8].
К производительным абразивным материалам для прецизионных доводочных операций металлов относят абразивы со средней твердостью на основе оксидов. К ним следует отнести оксиды переходных и редкоземельных металлов со средней твердостью (по шкале Мооса, 5–7 баллов), в число которых входят: CeO2, ZrO2, Cr2O3, Al2O3, Fe2O3 [9, 10].
Модифицирование оксида хрома с образованием твердых растворов с РЗЭ и кальцием дает эффект повышения полирующей способности и одновременно обеспечивает шероховатость поверхности Rа 0.07–0.08 мкм. При этом применение оксида хрома, модифицированного оксидами CaO и ZrO2, повышает качество полирования и выход высокоточных изделий из закаленной стали ШХ-15 до 80–82%. Однако они не всегда обеспечивают получение высокого класса чистоты обработки поверхности, например оксид хрома как наиболее применяемый из мягких абразивных материалов.
Возможным способом улучшения абразивных свойств является модифицирование с образованием твердых растворов оксидов [11–13].
Твердые растворы на основе оксидов алюминия обеспечивают высокую производительность и получение высокого класса чистоты обработки поверхности. Экологически чистым является абразивный материал на основе твердых растворов оксидов алюминия и железа [14].
Известно, что качество полирования определяется структурным состоянием и технологией подготовки поверхности обрабатываемого тела, условиями на границе твердых тел: величиной поверхностной энергии, адгезией и адсорбцией абразивного материала, процессами смачивания поверхности металла. Качество поверхности полируемых металлов зависит от свойств абразивного материала и, особенно, от химической активности абразивных частиц. Обладая механохимической (трибохимической) активностью за счет образования твердых растворов, абразивный материал значительно увеличивает производительность процесса (повышается полирующая способность) и обеспечивает наношероховатость поверхности [10, 15].
Известны различные методы получения наночастиц порошкового материала на основе оксида алюминия, например импульсный нагрев, однако использовать для полирования такой материал не рекомендуется, поскольку он не обладает необходимыми абразивными свойствами: частицы имеют несформированную кристаллическую форму [16]. Методы, основанные на получении золя–геля гидроксидов переходных металлов с последующим прокаливанием, не дают трибохимического эффекта при полировании, так как в процессе трибохимического активирования важен не только наноразмер частиц, но и из каких комплексов были получены смешанные оксиды. Получение наночастиц абразивного материала механохимическим методом не обеспечивает всего комплекса свойств, необходимых для достижения высокого класса чистоты обработки поверхности [17].
Одним из перспективных методов получения наночастиц является метод химической модификации слоистых структур, где используется образование гидроксокомплексов. Структура этих соединений состоит из положительно заряженных гидроксидных слоев и анионов. Для получения ультрадисперсных неорганических материалов, в том числе смешанных оксидов, перспективным является метод синтеза из гидроксокарбонатных комплексов [14].
Многие мягкие металлы и сплавы, как медь, латунь, и более стойкие к окислению, как титан, алюминий, полируются менее эффективно. Для увеличения производительности процесса полирования цветных металлов и сплавов, вероятно, необходимо повысить окислительную способность абразива или абразивной пасты введением какого-либо окислителя [18]. Другое решение может быть осуществлено за счет модифицирования абразивного материала оксидом переходного металла с переменной степенью окисления [19].
Целью настоящей работы является изучение влияния модифицирующих оксидов на синтез нанодисперсных твердых растворов оксидов алюминия и железа из гидроксокарбонатных комплексов и их абразивные свойства в отношении цветных металлов (меди, латуни, титана).
ЭКСПЕРИМЕНТАЛЬНАЯ ЧАСТЬ
Твердые растворы оксидов алюминия и железа, а также модифицированные оксидами молибдена, циркония и иттрия получали термообработкой в интервале температур 1000–1150°С осажденных аммиачных гидроксокарбонатов. В процессе осаждения вводили молибдат-ионы в виде 0.1 M раствора (NH4)6Mo7O24, цирконил-ионы в виде 0.1 M раствора ZrOSO4, ионы иттрия – 0.1 М раствора YCl3. Концентрацию оксида железа в готовом продукте варьировали в интервале 0.12–0.2 мол. %, концентрацию оксидов циркония, молибдена, иттрия – в интервале 0.01–0.005 мол. %. Концентрацию алюминия, железа, и модифицирующих оксидов в образцах определяли по стандартным методикам рентгенофлуоресцентного анализа с применением энергодисперсионного спектрометра EDX-900HS с относительной погрешностью ±0.0005 мол. %. Концентрацию ${\text{NH}}_{{\text{4}}}^{ + }$ определяли фотометрическим методом; концентрацию ${\text{С О }}_{{\text{3}}}^{{{\text{2}} - }}$ – волюмометрическим методом с улавливанием углекислого газа раствором щелочи после нагревания при 220–250°С образцов, высушенных при комнатной температуре; концентрацию суммы ОН–- и ${\text{С О }}_{{\text{3}}}^{{{\text{2}} - }}$-групп – оксалатным.
Для исследования образцов применяли следующие методы: ИК-спектроскопический с использованием спектрофотометра JR-475 фирмы Shimadzu (образцы прессовали в таблетки с КВr); рентгенофазовый анализ (РФА) с использованием дифрактометра STADI-P c программой, включающей сопоставление дифракционных максимумов с данными картотеки JCPDS-JCDD PDF2, в ${\text{Cu}}{{K}_{{\alpha }}}$-излучении (никелевый фильтр). Шаг сканирования составлял 0.03° в области спектра 2θ от 5° до 70°, подсчет секунд от 5 до 25 для каждого шага. Гранулометрический состав образцов устанавливали методом седиментации с помощью центрифугального седиментографа фирмы Shimadzu Analyzier SA-CP2 (вязкость дисперсионной среды 0.0093 пуаз; плотность жидкой фазы 1.0 г/см3).
Абразивные свойства образцов в процессах полирования исследовали согласно стандартным методикам по изменению производительности (полирующей способности) и шероховатости поверхности с помощью оптического профилометра Wyko NT-1100 (Rа), оцениваемой как среднее арифметическое значение неровностей профиля на базовой длине 0.08 мм. Образцы были из закаленной стали с аустенитно-мартенситной структурой, а также меди (М-2), латуни (С-64) и титана (ВТ1-0), начальное значение Rа 1.2–0.3 мкм. Производительность процесса (полирующую способность) полирования вычисляли по формуле:
Шероховатость поверхности Ra является средним арифметическим абсолютного значения отклонения в пределах длины профиля: Ra = 1/n∑|yi|.
Для моделирования процесса полирования была смонтирована специализированная установка на базе вибрационного прибора “Метаполан 2”. Образцы были помещены в специальные держатели на платформе, покрытой сукном, куда вносилась полировальная паста. Контактное давление составляло 12–18 кПа, вращение образцов осуществлялось за счет вращения шпинделя от электродвигателя, скорость вращения 89 об./мин (1.4 м/с) регулировалась резистором. Каждые 15 мин наносили полировальную пасту, состоящую из воды и абразивного порошка. Для полирования была подготовлена паста из абразивного порошка (10 г) и дистиллированной воды (90 мл) со значением pH среды 7–8. Агломерация пасты не наблюдалась в течение всего процесса полировки. Контроль над процессом осуществляли по изменению съема металла и качества поверхности по шероховатости.
РЕЗУЛЬТАТЫ И ОБСУЖДЕНИЕ
Полирование с использованием тонкозернистых абразивных порошковых материалов можно представить как совокупность процессов механического, адсорбционного, адгезионного смачивания и окисления поверхностного слоя. Ранее было установлено, что финишное доводочное полирование представляет собой механохимический процесс в подповерхностном слое металлов. Для получения шероховатости поверхности Ra < 0.02 мкм абразивный материал должен обладать химической (трибохимической) активностью в процессе трения [15, 18–20].
Абразивный материал, полученный методом термообработки аммонийных гидроксокарбонатов алюминия и железа NH4Al2 – xFex(OH)5(CO3)2 · · 2H2O имеет более высокие абразивные характеристики: полирующая способность у образцов на основе твердого раствора оксидов алюминия и железа больше, чем у корунда или карбида бора. Суммарную реакцию осаждения гидроксокарбонатов можно представить следующим образом:
(1)
$\begin{gathered} {\text{FeS}}{{{\text{O}}}_{{\text{4}}}} + {\text{A}}{{{\text{l}}}_{{\text{2}}}}{{({\text{S}}{{{\text{O}}}_{{\text{4}}}})}_{{\text{3}}}} + {\text{9N}}{{{\text{H}}}_{{\text{4}}}}{\text{HC}}{{{\text{O}}}_{{\text{3}}}} = \\ = {\text{N}}{{{\text{H}}}_{{\text{4}}}}{\text{A}}{{{\text{l}}}_{{\text{2}}}}{\text{Fe}}{{\left( {{\text{OH}}} \right)}_{{\text{5}}}}{{\left( {{\text{C}}{{{\text{O}}}_{{\text{3}}}}} \right)}_{{\text{2}}}} \downarrow + {\text{ 4}}{{\left( {{\text{N}}{{{\text{H}}}_{{\text{4}}}}} \right)}_{{\text{2}}}}{\text{S}}{{{\text{O}}}_{{\text{4}}}} + \\ + \,\,{\text{2}}{{{\text{H}}}_{{\text{2}}}}{\text{O}} + {\text{7C}}{{{\text{O}}}_{{\text{2}}}} \uparrow . \\ \end{gathered} $В результате термического воздействия на аммонийные гидроксокарбонаты образуются твердые растворы на основе гематита и корунда [14]:
(2)
$\begin{gathered} {\text{N}}{{{\text{H}}}_{{\text{4}}}}{\text{A}}{{{\text{l}}}_{{{\text{2}} - x}}}{\text{F}}{{{\text{e}}}_{x}}{{{\text{(OH)}}}_{{\text{5}}}}{{{\text{(C}}{{{\text{O}}}_{{\text{3}}}}{\text{)}}}_{{\text{2}}}} \cdot n{{{\text{H}}}_{{\text{2}}}}{\text{O}}\xrightarrow{{220 - 250^\circ {\text{C}}}} \\ \to {\text{A}}{{{\text{l}}}_{{2\, - \,x}}}{\text{F}}{{{\text{e}}}_{x}}{{({\text{OH}})}_{2}}{{{\text{O}}}_{2}}\xrightarrow{{425 - 450^\circ {\text{C}}}} \\ \to {\text{A}}{{{\text{l}}}_{{2\, - \,x}}}{\text{F}}{{{\text{e}}}_{x}}{{{\text{O}}}_{3}}\xrightarrow{{950 - 1150^\circ {\text{C}}}} \\ \to \alpha {\text{ - A}}{{{\text{l}}}_{{2\, - \,x}}}{\text{F}}{{{\text{e}}}_{x}}{{{\text{O}}}_{{{\text{3к р }}}}} + \alpha {\text{ - F}}{{{\text{e}}}_{{2\, - \,y}}}{{{\text{O}}}_{{{\text{3к р }}}}}. \\ \end{gathered} $Для получения наименьшей шероховатости поверхности Ra = 0.002 мкм необходимо применение твердого раствора, содержащего 0.125–0.156 мол. % оксида железа. Это объясняется образованием фаз твердого раствора на основе корунда и гематита с нанодисперсным размером частиц. Изменение долей твердых растворов Al2 – xFexO3 и Fe2 – yAlyO3 в зависимости от концентрации оксида железа в системе твердых растворов представлено в [21].
На рис. 1 представлена зависимость получаемой шероховатости поверхности после полирования стали ШХ-15 с твердым раствором оксидов алюминия и железа (кривая 1), модифицированным оксидом хрома (CaO и ZrO2) (кривая 2) и карбидом бора B4C (кривая 3) от продолжительности процесса.
Рис. 1.
Зависимости получаемой шероховатости поверхности после полирования твердым раствором оксидов алюминия и железа (1), модифицированным оксидом хрома (CaO и ZrO2) (2); карбидом бора B4C (3) от продолжительности процесса.
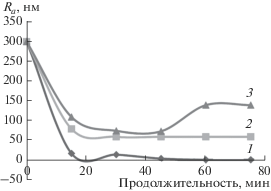
Наименьшей шероховатостью обладают образцы стали, обработанные твердым раствором оксидов алюминия и железа (Ra = 0.002–0.005 мкм). Полирование карбидом бора не обеспечивает наношероховатость поверхности. Данные седиментационного исследования показывают (рис. 2), что образцы на основе твердого раствора оксида алюминия и железа (0.12–0.156 мол. % Fe2O3) содержат наночастицы размером до 10 нм в количестве 4–5%, до 50 нм – 50%.
Рис. 2.
Кривые распределения частиц в дифференциальной форме для оксида алюминия-железа (1), алюминия-железа, модифицированного 0.005 мол. % MoO2 (2), алюминия-железа, модифицированного 0.001 мол. % MoO2 (3).
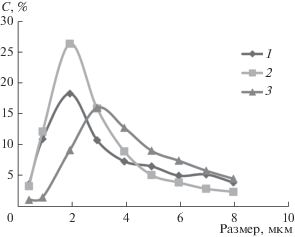
Из данных ИК-спектроскопии и химического анализа следует, что осаждаемые аммонийные гидроксокарбонаты алюминия и железа с добавлением молибдат-ионов содержат гидроксо- и карбоксо-группы. Общая формула осажденных аммонийных гидроксокарбонатов алюминия и железа подобна формуле гидроксокарбонатов, полученных в [14].
По данным РФА синтезируемых образцов и продуктов их термообработки в интервале температур от 25 до 1150°С можно представить общую формулу как (NH4)2Al2Fe(OH)5(CO3) ⋅ nH2O. Следует отметить, что в процессе осаждения наблюдается окисление двухвалентного железа до трехвалентного и восстановление (NH4)6Mo7O24 с образованием молибдата нестехиометрического (NH4)6Mo7O23, т.н. молибденовой сини [22]. В отличие от гидроксокарбонатов алюминия-железа без добавки молибдат-ионов образцы содержат до 1–5 мас. % комплексов, в которых присутствует Fe3+. Химический анализ показал, что в осаждении участвует 1/5 часть от вводимого количества молибдат-ионов, остальные остаются в растворе, что соответствует данным в [22] о неполном осаждении молибдат-ионов в присутствии аммонийных ионов.
На ИК-спектрах образцов гидроксокарбонатных комплексов имеются следующие полосы поглощения: сильные узкие полосы в области валентных колебаний групп ОН– с хорошо выраженными максимумами при 3200 и 3450 см–1, которые отвечают валентным колебаниям ассоциированных гидроксилов Fe–О–Н и Al–O–H; полосы при 860, 985 см–1 представляющие собой деформационные колебания групп ОН–; полоса при 1100 см–1, обусловленная деформационными колебаниями ОН–, характерными для мостиковой водородной связи. Бидентатность карбонатной группы подтверждается расщеплением частот вырожденных колебаний ν1 при симметрии состояний монодентатной и бидентатной группировок С2v и Сs (п. п. 1395, 1445–1449 и 1540 см–1) [23].
Начало образования фазы твердого раствора оксида алюминия и железа на основе корунда и гематита отмечается при температуре 950–1050°С, что подтверждается данными РФА. В процессе термообработки гидроксокарбонатов происходит окисление двухвалентного железа до трехвалентного, что подтверждается данными химического анализа. В результате изотермической выдержки происходит образование двух твердых растворов ромбоэдрической модификации с пр. гр. R$\overline 3 $c: α-Al2 – xFexO3 – дифракционные линии 012, 104, 110, 116 и α-Fe2 –yAlyO3 – линии 104, 110, 116, а также тетрагонального диоксида молибдена MoO2 с пр. гр. P42/mnm – линии 110, 200, 211 – с параметрами решетки, близкими к параметрам диоксида марганца той же модификации [24, 25]. Схему термических превращений аммонийных гидроксокарбонатов с добавкой молибдата аммония можно представить следующим образом:
(3)
$\begin{gathered} {\text{N}}{{{\text{H}}}_{{\text{4}}}}{\text{A}}{{{\text{l}}}_{{\text{2}}}}{\text{Fe}}{{({\text{OH}})}_{{\text{5}}}}{{({\text{C}}{{{\text{O}}}_{{\text{3}}}})}_{{\text{2}}}} + {{({\text{N}}{{{\text{H}}}_{{\text{4}}}})}_{{\text{6}}}}{\text{M}}{{{\text{o}}}_{{\text{7}}}}{{{\text{O}}}_{{{\text{24}}}}} \to \\ \to {\text{N}}{{{\text{H}}}_{{\text{4}}}}{\text{A}}{{{\text{l}}}_{{\text{2}}}}{\text{Fe}}{{({\text{OH}})}_{{\text{6}}}}{{({\text{C}}{{{\text{O}}}_{{\text{3}}}})}_{{\text{2}}}} + \\ + \,\,{\text{N}}{{{\text{H}}}_{{\text{4}}}}{\text{A}}{{{\text{l}}}_{{\text{2}}}}{\text{Fe}}{{({\text{OH}})}_{{\text{5}}}}{{({\text{C}}{{{\text{O}}}_{{\text{3}}}})}_{{\text{2}}}} + \\ + \,\,{{({\text{N}}{{{\text{H}}}_{{\text{4}}}})}_{{\text{6}}}}{\text{M}}{{{\text{o}}}_{{\text{7}}}}{{{\text{O}}}_{{{\text{23}}}}}\xrightarrow{{220 - 250^\circ {\text{C}}}}\quad \\ \to {\text{A}}{{{\text{l}}}_{{\text{2}}}}{\text{Fe}}{{({\text{OH}})}_{{\text{4}}}}{{{\text{O}}}_{{\text{2}}}}\xrightarrow{{425 - 450^\circ {\text{C}}}}{\text{A}}{{{\text{l}}}_{{\text{2}}}}{{{\text{O}}}_{{\text{3}}}} \cdot {\text{F}}{{{\text{e}}}_{{\text{2}}}}{{{\text{O}}}_{{{\text{3}}\,{\text{а м }}}}}\,\,{\text{ + }} \\ {\text{ + }}\,\,{\text{F}}{{{\text{e}}}_{{\text{2}}}}{{{\text{O}}}_{{{\text{3}}\,{\text{к р }}}}}\xrightarrow{{950 - 1150^\circ {\text{C}}}}{\text{A}}{{{\text{l}}}_{{{\text{2}}\, - \,x}}}{\text{F}}{{{\text{e}}}_{x}}{{{\text{O}}}_{{{\text{3}}\,{\text{к р }}}}} + \\ + \,\,{\text{F}}{{{\text{e}}}_{{{\text{2}}\, - \,y}}}{\text{A}}{{{\text{l}}}_{y}}{{{\text{O}}}_{{{\text{3}}\,{\text{к р }}}}} + {\text{Mo}}{{{\text{O}}}_{{{\text{2}}\,{\text{к р }}}}}. \\ \end{gathered} $На второй стадии в процессе твердофазного синтеза при термообработке гидроксокарбонатов, модифицированных диоксидом циркония, в интервале температур от 950 до 1150°С происходит окисление двухвалентного железа до трехвалентного. Одновременно наблюдается образование твердых растворов оксидов алюминия и железа, а также диоксида циркония, что подтверждается данными РФA и химического анализа. Уравнения реакций распада гидроксокарбонатов следующие:
(4)
$\begin{gathered} 4{\text{N}}{{{\text{H}}}_{4}}{\text{FeA}}{{{\text{l}}}_{{\text{2}}}}{{{\text{(OH)}}}_{{\text{5}}}}{{{\text{(C}}{{{\text{O}}}_{3}})}_{2}} + {{{\text{O}}}_{2}} = \\ = \,\,2{\text{F}}{{{\text{e}}}_{{\text{2}}}}{{{\text{O}}}_{{\text{3}}}} + 4{\text{A}}{{{\text{l}}}_{{\text{2}}}}{{{\text{O}}}_{3}} + \\ + \,\,4{\text{N}}{{{\text{H}}}_{3}} + 8{\text{C}}{{{\text{O}}}_{2}} + 12{{{\text{H}}}_{{\text{2}}}}{\text{O}},\quad \\ \end{gathered} $(5)
$\begin{gathered} {{\left( {{\text{N}}{{{\text{H}}}_{4}}} \right)}_{2}}{\text{Z}}{{{\text{r}}}_{{\text{2}}}}{{{\text{O}}}_{2}}{{\left( {{\text{OH}}} \right)}_{2}}{{\left( {{\text{C}}{{{\text{O}}}_{3}}} \right)}_{2}} = \\ = \,\,2{\text{Zr}}{{{\text{O}}}_{2}} + {\text{C}}{{{\text{O}}}_{2}} + 2{{{\text{H}}}_{{\text{2}}}}{\text{O}} + 2{\text{N}}{{{\text{H}}}_{{\text{3}}}}.\quad \\ \end{gathered} $Отмечается образование ромбоэдрического твердого раствора оксидов алюминия и железа с пр. гр. R$\overline 3 $c α-Al2 – xFexO3 (85.9 мас. %) – дифракционные линии 012, 104, 110, 116, α-Fe2O3 (7.7 мас. %) – линии 012, 104, 110, 116, а также тетрагонального диоксида циркония (1.9 мас. %) с пр. гр. P42/nmс – линии 101, 110, 112 и моноклинного диоксида циркония (3.7 мас. %) c пр. гр. R21/c – линии 011 $\overline 1 $11, 111. Химический рентгенофлуоресцетный энергодисперсионный анализ дает следующий состав: Al2O3 – 70.0%, Fe2O3 – 25.0%, ZrO2 – 5.0%, что хорошо совпадает с данными РФА.
На рис. 3 приведены дифрактограммы образцов оксида алюминия-железа, модифицированного диоксидом циркония (а), а также образцов без модифицирующей добавки (б). В последнем случае помимо твердых растворов на основе корунда и гематита ромбоэдрической модификации образуется 3–12 мас. % кубического оксида алюминия-железа Al3Fe5O12 (222, 332, 431) в зависимости от содержания оксида железа (0.125–0.156 мол. %).
Рис. 3.
Характерные дифрактограммы образцов оксида алюминия-железа, модифицированных 0.004–0.008 мол. %, ZrO2 (5 с для каждого шага) (а) и немодифицированных (линии дифракции для α-Al2 – xFexO3, Fe2 – yAlyO3, 25 с для каждого шага) (б).
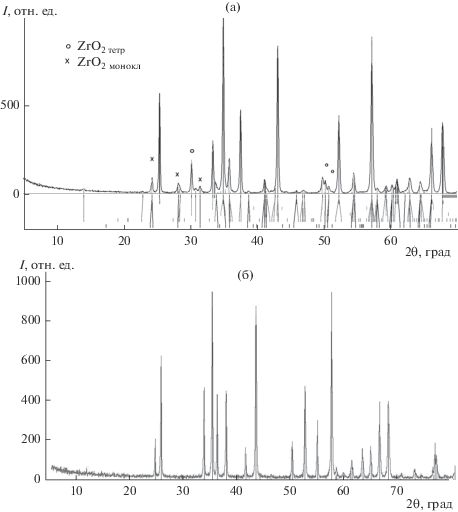
Присутствие кубического оксида алюминия-железа увеличивает полирующую способность в процессе полирования закаленных сталей. Процесс термической обработки гидроксокарбонатов с включением диоксида циркония может быть представлен следующим образом [26]:
(6)
$\begin{gathered} {\text{N}}{{{\text{H}}}_{{\text{4}}}}{\text{A}}{{{\text{l}}}_{{\text{2}}}}{\text{Fe}}{{\left( {{\text{OH}}} \right)}_{{\text{5}}}}{{\left( {{\text{C}}{{{\text{O}}}_{{\text{3}}}}} \right)}_{{\text{2}}}} + \\ + \,\,({\text{N}}{{{\text{H}}}_{{\text{4}}}}{\text{Z}}{{{\text{r}}}_{{\text{2}}}}{{{\text{O}}}_{{\text{2}}}}{{\left( {{\text{OH}}} \right)}_{{\text{2}}}}{{\left( {{\text{C}}{{{\text{O}}}_{{\text{3}}}}} \right)}_{{\text{2}}}} \to {\text{A}}{{{\text{l}}}_{{\text{2}}}}{\text{Fe}}{{\left( {{\text{OH}}} \right)}_{{\text{4}}}}{{{\text{O}}}_{{\text{2}}}} + \\ + \,\,{\text{Z}}{{{\text{r}}}_{{\text{2}}}}{{{\text{O}}}_{{\text{2}}}}{{\left( {{\text{OH}}} \right)}_{{\text{2}}}} \to {\text{A}}{{{\text{l}}}_{{\text{2}}}}{{{\text{O}}}_{{\text{3}}}} \cdot {\text{F}}{{{\text{e}}}_{{\text{2}}}}{{{\text{O}}}_{{{\text{3}}\,{\text{а м }}}}} + \\ + \,\,{\text{Zr}}{{{\text{O}}}_{{{\text{2}}\,{\text{а м }}}}} \to {\text{A}}{{{\text{l}}}_{{{\text{2}}--x}}}{\text{F}}{{{\text{e}}}_{x}}{{{\text{O}}}_{{{\text{3}}\,{\text{к р }}}}} + {\text{Zr}}{{{\text{O}}}_{{{\text{2}}\,{\text{к р }}}}}. \\ \end{gathered} $Процесс образования твердого раствора оксидов алюминия и железа из гидроксокарбонатных комплексов с введением добавки молибдат-ионов влияет на абразивные свойства материала. Присутствие в образцах 0.001–0.005 мол. % MoO2 увеличивает полирующую способность в 5–7 раз при полировании меди и латуни (рис. 4). Получение наименьшей шероховатости поверхности Ra = = 0.002 мкм отмечается в случае образцов, содержащих 0.125–0.156 мол. % оксида железа.
Рис. 4.
Кинетические кривые изменения полирующей способности (Р) при полировании: 1 – меди твердым раствором оксидов алюминия-железа, модифицированным MoO2; 2 – латуни твердым раствором оксидов алюминия-железа; 3 – ШХ-15 карбидом бора; 4, 5 – титана твердым раствором оксидов алюминия-железа, модифицированным 0.08 мол. % ZrO2 и 0.03 мол. % Y2O3 соответственно.
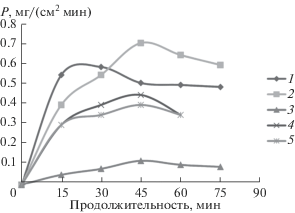
Для полирования титана наилучшими модифицирующими добавками к твердому раствору оксидов алюминия-железа являются диоксид циркония и оксид иттрия: модифицирование ZrO2 увеличивает полирующую способность в 3–4.5 раза; первоначальная шероховатость поверхности Ra титана составляла 1.299 мкм. На рис. 5 представлены кинетические закономерности изменения полирующей способности образцов, модифицированных диоксидом циркония (кривые 2, 3) и оксидом иттрия (кривая 4). Как видно из рис. 5, значения полирующей способности у образцов, модифицированных оксидом иттрия и диоксидом циркония, близки.
Рис. 5.
Кинетические кривые изменения полирующей способности образцов оксидов алюминия-железа при полировании титана: 1 – без модифицирования; 2, 3 – модифицированных 0.08 и 0.04 мол. % ZrO2 соответственно; 4 – модифицированных 0.001–0.03 мол. % Y2O3.
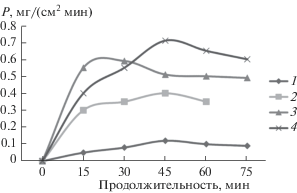
Однако шероховатость поверхности, достигнутая в процессе полирования модифицированным диоксидом циркония, составляет Ra = 0.018–0.019 мкм. Поэтому для понижения шероховатости использовали модифицирование оксидом иттрия. Шероховатость поверхности при этом снизилась до 0.006 мкм. Наименьшая шероховатость поверхности Ra = 0.006 мкм получена для твердого раствора оксидов алюминия и железа, содержащего 0.125–0.156 мол. % оксида железа и 0.01–0.03 мол. % оксида иттрия.
При изучении системы Al2O3–Y2O3–ZrO2–Fe2O3 в процессе твердофазного синтеза при температуре 1150–1200°С выявлено, что образуется ромбоэдрический оксид алюминия α-Al2O3 (012, 104, 110, 113, 116), кубический оксид иттрия (пр. гр. Ia3, а = 10.604(5) Å), тетрагональный диоксид циркония (101, 110, 112), что находится в соответствии с данными [27]. Химический рентгенофлуоресцентный энергодисперсионный анализ показывает следующий состав: 91.5% Al2O3, 2.1% ZrO2, 2.8% Y2O3, 2.0% F2O3, что хорошо согласуется с данными РФА. На рис. 6 представлен микрорельеф поверхности образцов титана.
Рис. 6.
Характерные изображения микрорельефа поверхности образцов титана: исходного (Ra = 1.299 мкм) (а); полированного в течение 15 мин оксидом алюминия-железа (Ra = 0.187 мкм) (б), полированного оксидом алюминия-железа, модифицированным диоксидом циркония (Ra = 0.019 мкм) (в), полированного в течение 30–45 мин оксидом алюминия-железа, модифицированным диоксидом циркония и оксидом иттрия (Ra = 0.006 мкм) (г).
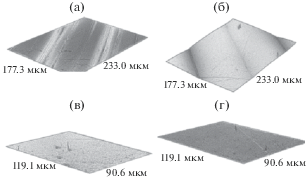
ЗАКЛЮЧЕНИЕ
Выявлены закономерности формирования нанодисперсных твердых растворов на основе Al2 – хFeхO3 и Fe2 – yAlyO3, модифицированных диоксидом молибдена, диоксидом циркония и оксидом иттрия, полученных в результате термообработки аммонийных гидроксокарбонатных комплексов типа NH4Al2Fe(OH)5(CO3)2. Для полирования цветных металлов и сплавов, таких как медь, латунь, более эффективным является модифицированный оксид алюминия–железа, содержащий 0.001–0.005 мол. % MoO2. Для полирования титана более эффективным является модифицированный оксид алюминия-железа, содержащий 0.001–0.003 мол. % Y2O3. Модифицирование оксидов алюминия и железа в процессе полирования обеспечивает наношероховатость поверхности.
Список литературы
Артемов А.С. Наноалмазы для полирования // Физика твердого тела. 2004. Т. 46. № 4. С. 670–678.
Jackson M.J., Mills B., Hitchiner M.P. Controlled Wear of Vitrified Abrasive Materials for Precision Grinding Applications // Sadhana. 2003. V. 28. № 5. P. 897–914.
Bakharev V.P. Dispersion of Ceramics and Composites in Diamond Finishing by Free Abrasive // Russ. Eng. Res. 2009. V. 29. № 2. P. 162–168.
Филатов Ю.Д. Оценка шероховатости и отражательной способности поверхностей изделий из неметаллических материалов при финишной алмазно-абразивной обработке // Сверхтвердые материалы. 2009. № 5. С. 70–81.
Стороженко П.А., Гусейнов Ш.Л., Малашин С.И. Нанодисперсные порошки: методы получения и способы практического применения // Российские нанотехнологии. 2009. Т. 4. С. 27–39.
Pokropivnyi V.V., Silenko P.M. Silicon Carbide Nanotubes and Nanotubular Fibers: Synthesis, Stability, Structure and Classification // Theor. Exp. Chem. 2006. V. 42. № 1. P. 3–15.
Khanra A.K. Production of Boron Carbide Powder by Carbothermal Synthesis of Gel Material // Bull. Mater. Sci. 2007. V. 30. № 2. P. 93–96.
Bogdanov S.P. Influence of Superstoichiometric Boron on the Synthesis of Cubic Boron Nitride // Glass Phys. Chem. 2008. V. 34. № 3. P. 336–339.
Degtyareva E.V., Kabakova I.I., Skorodumova E.B., Armyanovskii V.E. An Abrasive-Resistant Corundum Ceramic for Drawing Microwires // Refract. Ind. Ceram. 1982. V. 23. № 1–2. P. 82–87.
Гаршин А.П., Гропянов В.М., Лагунов Ю.В. Абразивные материалы. Л.: Машиностроение, 1983. 230 с.
Викторов В.В., Фотиев А.А., Бадич В.Д. Абразивные и термические свойства твердых растворов системы Al2O3–Cr2O3 // Неорган. материалы. 1996. Т. 32. № 1. С. 63–65.
Чехомова Л.Ф. Абразивные свойства модифицированного оксида хрома // Неорган. материалы. 2001. Т. 37. № 3. С. 342–348.
Королева Л.Ф. Модифицированные оксиды, оксогидроксид, шпинели хрома для абразивных и пигментных материалов. Екатеринбург: УрО РАН, 2002. 214 с.
Королева Л.Ф. Абразивные свойства нанодисперсного оксида алюминия-железа // Неорган. материалы. 2009. Т. 45. № 10. С. 1235–1242.
Королева Л.Ф. Трибохимическая активность абразивных материалов на основе смешанных оксидов в процессе полирования металлов // Физика и химия обработки материалов. 2006. № 4. С. 84–92.
Котов Ю.А., Саматов О.М. Характеристики порошков оксида алюминия, полученных импульсным нагревом проволоки // Поверхность. 1994. № 10–14. С. 90–94.
Белоусов В.М., Чертов В.М., Рожкова Э.В., Литвин В.И., Зажигалов В.А. Применение золь–гель метода для синтеза и регулирования физико-химических характеристик оксидных железо-алюминиевых пористых веществ // Теоретическая и экспериментальная химия. 1997. Т. 33. № 2. С. 120–123.
Nan-Hoon Kim, Jond-Heun Lim, Sang-Yong Kim, Eui-Goo Chang. Semi-abrasive Free Slurry with Acid Colloidal Silica for Copper Chemical Mechanical Planarization // J. Mater. Sci.: Mater. Electron. 2005. V. 16. P. 629–632.
Марченко Е.А. О природе разрушения поверхности металлов при трении. М.: Наука, 1979. 118 с.
Ребиндер П.А. Значение физико-химических процессов при механическом разрушении и обработке твердых тел в технике // Вестн. АН СССР. 1940. № 8. С. 5–28.
Koroleva L.F. Modified Nanoparticle Oxides for Final Polishing // Diagnostics, Resource Mech. Mater. Struct. 2016. Is. 2. P. 48–73. https://doi.org/10.17804/2410-9908.2016.2.048-073
Бусев А.И. Аналитическая химия молибдена. М.: Изд. АН СССР, 1962. 301 с.
Накамото К. Инфракрасные спектры неорганических и координационных соединений. М.: Мир, 1966. 411 с.
Королева Л.Ф. Синтез и абразивные свойства нанодисперсных твердых растворов Al2 – xFexO3 и Fe2 – yAlyO3, модифицированных MoO2 // Неорган. материалы. 2010. Т. 46. № 12. С. 1465–1471.
Koroleva L.F. Final Polishing of Metals to Obtain Nanoroughened Surface // Nanotechnologies Russia. 2012. V. 7. № 1–2. P. 67–75.
Koroleva L.F. Nanoparticulate Zirconia-Modified Solid Solutions of Aluminum-Iron Oxides for Polishing Titanium Metal // Diagnostics, Resource Mech. Mater. Struct. 2015. Is. 1. P. 90–102. https://doi.org/10.17804/2410-9908
Isasi-Marín J., Pérez-Estébanez M., Díaz-Guerra C., Castillo J.F., Correcher V., Cuervo-Rodríguez M.R. Structural, Magnetic and Luminescent Characteristics of Pr3+-Doped ZrO2 Powders Synthesized by a Sol–Gel Method // J. Phys. D: Appl. Phys. 2009. V. 42. № 7. https://doi.org/10.1088/0022-3727/42/7/075418
Дополнительные материалы отсутствуют.
Инструменты
Неорганические материалы