Неорганические материалы, 2019, T. 55, № 6, стр. 671-677
Керамические композиты на основе Al2O3 с высокой устойчивостью к хрупкому разрушению
Л. И. Подзорова 1, *, А. А. Ильичёва 1, О. И. Пенькова 1, О. С. Антонова 1, А. С. Баикин 1, А. А. Коновалов 1
1 Институт металлургии и материаловедения им. А.А. Байкова Российской академии наук
119334 Москва, Ленинский пр., 49, Россия
* E-mail: ludpodzorova@gmail.com
Поступила в редакцию 02.07.2018
После доработки 28.12.2018
Принята к публикации 10.01.2019
Аннотация
Рассмотрены условия синтеза прекурсоров порошков системы ZrО2–AI2O3–СеО2, модифицированных катионами кальция. Показано влияние последовательности осаждения компонентов и старения реакционных систем прекурсоров синтезируемых составов на морфологию, размерные параметры нанопорошков, закономерности формирования фазового состава, особенности микроструктуры и механические характеристики композитов на их основе. Высокая устойчивость к хрупкому разрушению композитов достигнута за счет суммирования эффектов трансформационного и дисперсионного упрочнения, определяемых присутствием твердых растворов на основе Т-ZrO2 и гексаалюминатов кальция (прочность при изгибе до 1000 МПа, трещиностойкость K1C до 10.5 МПа м1/2).
ВВЕДЕНИЕ
Среди современных керамических материалов, используемых в технике и медицине, композиты системы А12O3–ZrO2 находят широкое применение благодаря высоким параметрам прочности, коррозионной стойкости, устойчивости в агрессивных средах, биоинертности и хорошей биосовместимости [1–4]. Материаловедческие исследования и разработки последних десятилетий направлены на достижение более высоких эксплуатационных свойств данных композитов, в особенности на повышение устойчивости к хрупкому разрушению. К настоящему времени разработан ряд технологических подходов, обеспечивающих подъем данного параметра, например, путем использования наноразмерных исходных порошков, введением в составы модифицирующих добавок, а также фаз, обладающих эффектами трансформационного и/или дисперсного упрочнения [2, 5–8].
Повышение устойчивости к хрупкому разрушению особенно важно для материалов с матрицей из оксида алюминия, поскольку корундовая керамика имеет низкий критический коэффициент интенсивности напряжений (K1C) не выше 3.5 МПа м1/2 [1, 2, 4, 9].
В публикациях [10–12] показано, что при модифицировании системы ZrО2–AI2O3–СеО2 щелочноземельными элементами в процессе спекания нанопорошков формируются материалы, содержащие три кристаллические фазы: корунд, диоксид циркония в тетрагональной форме и соответствующие гексаалюминаты. Последние выполняют роль дисперсионно-упрочняющей фазы, поскольку кристаллизуются в виде зерен длиннопризматического габитуса. Сочетание эффектов трансформационного и дисперсионного упрочнения позволяет повысить трещиностойкость композитов.
Цель настоящей работы – изучение влияния условий синтеза прекурсоров порошков системы ZrО2–AI2O3–СеО2, модифицированных катионами кальция, на морфологию, размерные параметры порошков, формирование фазового состава, микроструктуру и механические характеристики композитов на их основе.
ЭКСПЕРИМЕНТАЛЬНАЯ ЧАСТЬ
В работе рассмотрены условия получения композитов состава (мол. %): 65%Al2O3 + + 35%(88%ZrO2 + 12%СeO2) + 1% CaO. Прекурсоры исходных порошков получали в процессе золь–гель-синтеза соответствующих гидрогелей. Осаждение компонентов проводили из растворов (1 М) солей ZrOCl2, Al(NO3)3, Ce(NO3)3, Ca(NO3)2 раствором аммиака по методике, изложенной в публикации [6]. Изучены следующие схемы осаждения компонентов системы Al2O3–ZrO2–СeO2–СаO: одновременное и последовательное осаждение: вначале алюминий- и кальцийсодержащие компоненты, а затем цирконий- и церийсодержащие компоненты.
Старение реакционной системы прекурсоров обуславливает уменьшение объема осадка, что сокращает длительность его фильтрования, приводит к ослаблению сорбции примесей, т.е. повышаются степень чистоты материала и совершенство кристаллической структуры осадка [13, 14]. Ввиду изложенного в схему получения порошков был введен этап старения реакционных систем в течение 72 ч. Образцы обозначали соответственно схемам осаждения (о – одновременное, п – последовательное) и длительности старения “о72” и “п72”.
Порошки компактировали методом полусухого прессования на гидравлическом прессе (500 кН) при удельном давлении 200 МПа.
Спекание компактов порошков проводили в электрических печах с хромитлантановыми нагревателями в воздушной среде. Относительную плотность и пористость композитов определяли по методу гидростатического взвешивания.
Дифференциальный термический анализ проводили на приборе Netzsch STA 409 PC/PG, совмещенном с масс-спектроскопическим анализатором Aeolos. Удельную поверхность и пористость порошков определяли методом БЭТ (анализатор TriStar-3000), а затем получали интегральные зависимости распределения объема пор от их диаметра в области мезопор.
Средние размеры (D) индивидуальных частиц рассчитывали по оценочной формуле, выведенной для идеальных порошковых систем, состоящих из монодисперсных частиц глобулярной формы:
Гранулометрический состав порошков определяли методом лазерной седиментографии на приборе Аnnalizette-22.
Качественный анализ фазового состава образцов проводили на дифрактометре XRD-6000 (фирма Shimadzu) на излучении CuKα (λ = 1.54 Å). Микроструктуру композитов изучали на растровом электронном микроскопе LEO 1420.
Предел прочности при изгибе определяли методом трехточечного изгиба на универсальной испытательной машине Instron 5581. Трещиностойкость определяли по параметру K1C, используя метод предварительно нанесенных надрезов.
Методом сканирующей импульсной акустической микроскопии (микроскоп SIAM-1) определяли модуль Юнга (E).
РЕЗУЛЬТАТЫ И ОБСУЖДЕНИЕ
Ксерогели всех составов подвергали комплексному термическому анализу. Кривые ДСК для всех образцов характеризуются наличием в низкотемпературной области (до 400°С) двух термических эффектов (эндотермического и экзотермического), связанных с процессами дегидратации и разложением гидроксидов. На рис. 1 приведены ДСК-кривые ксерогелей образцов о, п, о72 и п72. На кривых образцов о и о72 не наблюдается экзоэффектов, характерных для кристаллизации диоксида циркония и стабильной формы оксида алюминия – корунда. Кристаллизация корунда из метастабильных форм происходит в широком интервале температур и не сопровождается выраженным экзоэффектом [15], а процесс кристаллизации диоксида циркония в системах с оксидом алюминия сопровождается слабовыраженным экзоэффектом и сдвигается в высокотемпературную область. Для образцов п и п72 на ДСК-кривых можно выделить слабые экзоэффекты при температурах соответственно 800 и 787°С (рис. 1), которые можно соотнести с кристаллизацией твердого раствора на основе диоксида циркония, содержащего катионы церия и алюминия. При этом этап старения реакционной системы (п72) снижает температуру кристаллизации твердого раствора, что соответствует данным [15, 16].
Основные потери массы всех ксерогелей происходят лавинообразно в интервале температур 240–280°С и связаны, по данным масс-спектроскопии, с удалением водных радикалов. Потеря массы прекращается при температуре выше 900°С, что иллюстрирует рис. 2.
Фазовый состав порошков, полученных после термообработки при 1050°С, представлен твердым раствором на основе тетрагонального диоксида циркония, следами диоксида циркония в моноклинной модификации и переходными метастабильными формами оксида алюминия (рис. 3). В порошках наблюдается различная степень закристаллизованности фазы корунда в зависимости от старения и последовательности осаждения компонентов, которая сохраняется при повышении температуры термообработки до 1250°С, что иллюстрируют фрагменты дифрактограмм порошков в области основных рефлексов, отвечающих α-А12O3 и θ-А12O3, представленные на рис. 4. Замедление процесса кристаллизации стабильной формы А12O3 при последовательном осаждении компонентов согласуется с наблюдаемой в системе Al2O3–ZrO2–СeO2 [17].
Рис. 3.
Фрагменты дифрактограмм образцов, полученных после термообработки при 1050°С: о и о72 (а), п и п72 (б).
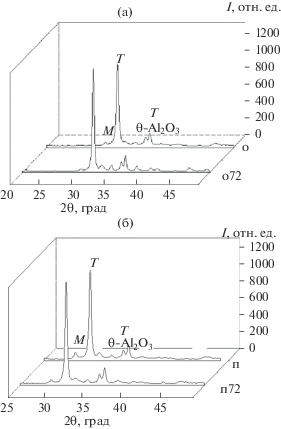
Рис. 4.
Фрагменты дифрактограмм образцов, полученных после термообработки при 1250°С, в области основного рефлекса α-А12O3 (а), θ-А12O3 (б).
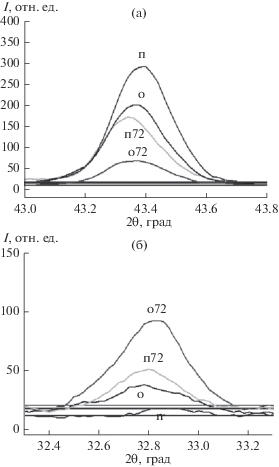
Полученные порошки всех составов имеют высокую дисперсность, относятся к наноразмерным системам. Порошки о и п в сравнении с о72 и п72 обладают более высоким значением удельной поверхности за счет большей внутренней пористости, т.е. являются более рыхлыми или “мягкими”. Данный факт подтверждают результаты, представленные в табл. 1.
Таблица 1.
Размерные характеристики исходных порошков
Образец | о | о72 | п | п72 |
---|---|---|---|---|
Sуд, м2/г ±1 | 34 | 27 | 31 | 29 |
Dср, нм | 38 | 50 | 41 | 40 |
Побщ, см3/г | 0.24 | 0.18 | 0.19 | 0.17 |
Синтезированные порошки представляют иерархию агломератов, размеры которых находятся в широком интервале от 100 до 5000 нм. Следует отметить, что в порошках, полученных при одновременном осаждении компонентов, наблюдаются очень мелкие агломераты (от 100 нм), в порошках последовательного осаждения компонентов самые мелкие агломераты имеют размеры более 200 нм. Этап старения систем, в соответствии с уравнением Оствальда–Фрейндлиха [14], приводит к изменению морфологии порошков, а именно: возрастанию доли агломератов с размерами свыше 500 нм и появлению крупных агломератов с размерами до 5000 нм. Данный факт иллюстрирует рис. 5, на котором представлены дифференциальное и интегральное распределение агломератов.
После спекания заготовок при оптимальной температуре были получены композиты с относительной плотностью не ниже 99% от теоретического значения плотности при отсутствии открытой пористости.
В публикациях [12, 13] показано, что формирование зернового состава микроструктуры модифицированных композитов обусловлено кристаллизацией трех фаз: корунда, диоксида циркония в тетрагональной форме (Т-ZrO2) и гексаалюмината кальция. В микроструктуре полученных композитов наблюдаются три типа зерен различного габитуса: ромбоэдрические, соответствующие фазе корунда, длиннопризматические – гексаалюминату кальция и глобулярной формы – твердому раствору на основе Т-ZrO2. Размеры корундовых зерен в композитах о и п находятся в интервале 500–1500 нм, зерен Т-ZrO2 – в интервале 300–500 нм. Этап старения реакционных систем прекурсоров приводит к увеличению размеров зерен как для корунда, так и для Т-ZrO2. Данный факт иллюстрируют электронные снимки, представленные на рис. 6. Кроме этого, следует отметить изменение форм-фактора длиннопризматических зерен: в микроструктуре образцов о72 и п72 он равен 0.4, а в о и п – 0.25.
Полученные композиты имеют некоторые отличия в достигнутых значениях прочности при статическом изгибе, что подтверждают результаты испытаний, представленные в табл. 2. Поскольку прочностные характеристики являются весьма структурочувствительными параметрами [4], изменения величин прочности рассмотренных композитов можно соотнести с выявленными различиями в зерновом составе их микроструктуры. Более тонкозеренная микроструктура композитов о обеспечивает достижение более высоких значений прочности по сравнению с композитами п, о72 и п72.
Рис. 6.
Микроструктура композитов, полученных из нанопорошков о (а), о72 (б), п (в), п72 (г) (из-за различий энергий поглощения и отражения потока вторичных электронов зерна, содержащие Al2O3, выглядят черными, а зерна Т-ZrO2 – белыми).
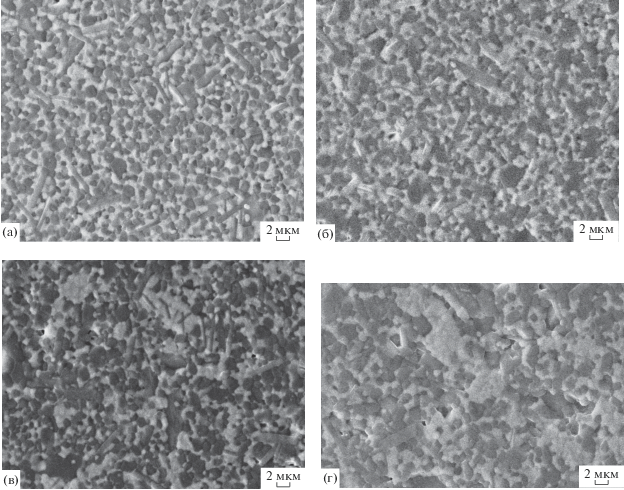
Таблица 2.
Характеристики композитов
Образец | tсп, °С | ρотн, % | σ, МПа | K1С, МПа м1/2 | E, ГПа |
---|---|---|---|---|---|
о | 1630 | 99.4 | 950 | 10.5 | 325 |
о72 | 1650 | 99.1 | 850 | 10.0 | 330 |
п | 1650 | 99.2 | 850 | 10.2 | 326 |
п72 | 1650 | 99.0 | 800 | 10.0 | 327 |
∇ | ±0.1 | ±50 | ±0.5 | ±1 |
Полученные композиты имеют высокие механические параметры, что позволяет представить их как альтернативу известным конструкционным материалам на основе оксида алюминия и диоксида циркония.
ЗАКЛЮЧЕНИЕ
Установлено влияние последовательности осаждения компонентов и старения реакционных систем прекурсоров синтезируемых образцов на морфологию, размерные параметры, закономерности формирования фазового состава порошков Al2O3–ZrO2–СeO2–СаO.
Композиты на основе синтезированных порошков обладают высокой устойчивостью к хрупкому разрушению, что определяется суммированием эффектов трансформационного и дисперсионного упрочнения, обусловленных присутствием твердых растворов на основе диоксида циркония тетрагональной модификации и гексаалюминатов кальция (критический коэффициент интенсивности напряжений K1С достигает 10.5 МПа м1/2).
Список литературы
Гаршин А.П., Гропянов В.М., Зайцев Г.П., Семенов С.С. Керамика для машиностроения. М.: Научтехлиттздат, 2003. 380 с.
Бакунов В.С., Беляков А.В., Лукин Е.С., Шаяхметов У.Ш. Оксидная керамика: спекание и ползучесть. М.: РХТУ им. Д.И. Менделеева, 2007. 584 с.
Piconi C., Maccauro G., Muratori F. Alumina Matrix Composites in Arthroplasty // Key Eng. Mater. 2005. V. 284–286. P. 979–982.
Баринов С.М., Шевченко В.Я. Прочность технической керамики. М.: Наука, 1996. 159 с.
Yang G., Li J., Wang G., Yashima M., Min S. Influences of ZrO2 Nanoparticles on the Microstructure and Mechanical Behavior of Ce-TZP/Al2O3 Nanocomposites // J. Mater. Sci. 2005. V. 40. № 23. P. 6087–6090.
Подзорова Л.И., Ильичёва А.А., Пенькова О.И. Микроструктура керамики системы Al2O3–ZrO2–CeO2 и ее прочностные характеристики // Огнеупоры и техническая керамика. 2005. № 11. С. 2–5.
Burger W., Richter H.G. High Strength and Toughness Alumina Matrix Composites by Transformation Toughening and ‘In Situ’ Platelet Reinforcement (ZPTA) – The New Generation of Bioceramics // Key Eng. Mater. 2001. V. 192–195. P. 545–548.
Савченко Н.Л., Королёв П.В., Мельников А.Г., Саблина Т.Ю., Кульков С.Н. Структура и механические характеристики спеченных композитов на основе ZrO2–Y2O3–Al2O3 // Фундаментальные проблемы современного материаловедения. 2008. Т. 5. № 1. С. 4.
Прохоров И.Ю. Распределение Вейбулла и размерный эффект // Огнеупоры и техническая керамика. 2016. № 10. С. 6–9.
Подзорова Л.И., Шворнева Л.И., Ильичёва А.А., Аладьев Н.А., Пенькова О.И. Микроструктура и фазовый состав композитов ZrO2–CeO2–Al2O3 в присутствии модификаторов MgО и Y2O3 // Неорган. материалы. 2013. Т. 49. № 4. С. 389–394.
Подзорова Л.И., Сиротинкин В.П., Ильичёва А.А., Пенькова О.И., Антонова О.С., Коновалов А.А. Фазообразование в наносистеме Al2O3–ZrO2–СeO2, модифицированной катионами кальция // Неорган. материалы. 2018. Т. 54. № 5. С. 475–481.
Подзорова Л.И., Ильичёва А.А., Пенькова О.И., Аладьев Н.А., Баикин А.С., Коновалов А.А., Мороков Е.С. Дисперсное упрочнение композитов системы Al2O3–Т-ZrO2 // Стекло и керамика. 2017. № 6. С. 16–20.
Вассерман И.М. Химическое осаждение из растворов. Л.: Химия, 1980. С. 208.
Лукин Е.С. Современная высокоплотная оксидная керамика с регулируемой микроструктурой. Ч. 1. Влияние агрегации порошков на спекание и микроструктуру керамики // Огнеупоры и техническая керамика. 1996. № 2. С. 6–9.
Yen F.S., Lo Y.S., Wen H.L., Yang R.J. θ- to α-Phase Transformation Subsystem Induced by α-Al2O3 in Boehmite-Derived Nano-Sized Alumina Powders // J. Cryst. Growth. 2003. № 249. P. 283–293.
Yoshimura M., Oh Sung-Tag, Sando M., Niihara K. Crystallization and Microstructural Characterization of ZrO2 (3 mol. % Y2O3) Nano-Sized Powder with Al2O3 Contents // J. Alloys Compd. 1999. V. 290. P. 284–289.
Подзорова Л.И., Ильичёва А.А., Шворнева Л.И., Куцев С.В., Михайлина Н.А., Пенькова О.И. Фазообразование наноразмерных прекурсоров t-ZrO2–Al2O3 и формирование микроструктуры керамики на их основе // Физика и химия стекла. 2007. Т. 33. № 5. С. 703–709.
Дополнительные материалы отсутствуют.
Инструменты
Неорганические материалы