Неорганические материалы, 2023, T. 59, № 3, стр. 243-250
Взаимодействие металлического катализатора с материалом барьерного слоя в процессе высокотемпературного формирования наночастиц никеля
С. В. Булярский 1, *, А. А. Дудин 1, П. Е. Львов 1, 2, Т. С. Гришин 1, Г. А. Рудаков 1, Г. Г. Гусаров 1
1 Институт нанотехнологий микроэлектроники Российской академии наук
119991 Москва,
Ленинский пр., 32А, Россия
2 Ульяновский государственный университет
432017 Ульяновск, ул. Л. Толстого, 42, Россия
* E-mail: bulyar2954@mail.ru
Поступила в редакцию 24.08.2022
После доработки 21.12.2022
Принята к публикации 23.12.2022
- EDN: YQKCYZ
- DOI: 10.31857/S0002337X23030028
Аннотация
Проведено исследование влияния условий отжига на формирование наночастиц никеля на барьерном слое нитрида титана, синтезированного методом атомно-слоевого осаждения. Показано, что размеры наночастиц зависят от температуры и времени отжига. При температурах выше 700°C и длительности отжига более 5 мин наблюдается явление коалесценции, которое приводит к росту частиц и уменьшению их поверхностной плотности. Во время отжига никель диффундирует в нитрид титана и его количество на поверхности падает. Экспериментальные результаты согласуются с моделированием формирования наночастиц в рамках гидродинамической модели. Определены потенциал взаимодействия катализатора с буферным слоем и вязкость расплава, которые показывают, что при плавлении тонкого слоя никеля, порядка единиц нанометров, металл подобен переохлажденной жидкости. Моделирование показало, что при отжиге па́ры тонкая пленка металла–барьерный слой средний размер наночастицы меньше при меньших потенциалах взаимодействия между веществами па́ры.
ВВЕДЕНИЕ
Применение углеродных нанотрубок (УНТ) в качестве функциональных элементов и материалов в наноэлектронике накладывает ограничение на температуру их синтеза, требуя использования в этом случае относительно низких температур. Для выполнения этого условия синтез проводится по технологии химического осаждения из паровой фазы (Chemical Vapor Deposition – CVD) [1]. Результаты такого синтеза во многом определяются наночастицами катализатора, которые являются центрами зарождения и роста УНТ [2, 3]. Чаще всего в качестве катализатора используют железо, никель, кобальт [4], а также их сплавы или оксиды, но применяются и другие материалы [5]. Свойства УНТ, такие как кристаллическая структура, хиральность, диаметр и скорость роста зависят от катализатора [6, 7]. Поэтому выбор материала катализатора и формирование его наночастиц остаются важной задачей кремний-углеродной наноэлектроники.
Элементы наноэлектроники с использованием УНТ создаются на кремниевых подложках. Металлы, используемые в качестве катализатора, взаимодействуют с кремнием с образованием силицидов и их каталитические свойства теряются. Поэтому между тонкой пленкой катализатора и подложкой располагается барьерный слой, который изготавливают, как правило, из нитрида металла [8]. При формировании наночастиц катализатора происходит взаимодействие металла катализатора с барьерным слоем. Материал барьерного слоя, состояние его поверхности, режим отжига пленки катализатора на нем могут оказывать влияние на диаметр синтезированных УНТ и их дефектность.
Важным фактором, который оказывает влияние на распределение наночастиц катализатора по размерам, является эффективный потенциал взаимодействия между веществом катализатора и барьерным слоем [9, 10]. Величина этого потенциала определяется путем сопоставления экспериментальных распределений наночастиц с расчетами, выполненными в рамках гидродинамической модели. Эта модель описывает разрыв пленки катализатора при плавлении и образование нанокапель, которые при остывании превращаются в наночастицы. Заметим, что температуры формирования наночастиц катализаторов существенно ниже температуры плавления никеля. Применение гидродинамической модели возможно в силу того, что наноразмерные объекты плавятся при существенно более низких температурах, чем монолитные [10]. Моделирование опирается на теорию фазовых переходов смачивания [11–13], в рамках которой образование капель на поверхности подложки из жидкой ультратонкой пленки расплава катализатора описывается уравнением [12, 13]:
(1)
${{\eta }}\frac{{\partial h}}{{\partial t}} = \nabla \left( {\frac{{{{h}^{3}}}}{3}\nabla \left[ {\frac{{\partial V}}{{\partial h}} - {{\sigma }}{{\nabla }^{2}}h} \right]} \right),$Минимум эффективного потенциала характеризует способность пленки превращаться в изолированные наночастицы при плавлении [10].
Методика моделирования заключается в оценке эффективного потенциала взаимодействия пленки катализатора с барьерным слоем и расчете с его помощью основных характеристик наночастиц катализатора. Потенциал взаимодействия V(h) оценивается из приближенного равенства $\frac{1}{{{\sigma }}}\frac{{\partial V}}{{\partial h}} \approx {{\nabla }^{2}}h,$ которое соответствует стационарному решению уравнения (1). Результаты расчета сравниваются с такими же характеристиками, полученными экспериментально, например: распределение наночастиц по размерам либо кинетика изменения их геометрии. При этом сам потенциал уточняется в процессе сравнения с экспериментальными данными.
Подобные взаимодействия исследовались другими методами, например рентгеновской фотоэлектронной спектроскопией [8]. Однако при этом не была обнаружена диффузия материала катализатора в барьерный слой, которая приводит к уменьшению количества катализатора на поверхности. Кроме того, не исследована кинетика формирования наночастиц при изменении длительности отжига пленки катализатора и не обсуждалось влияние вещества барьерного слоя на размеры наночастиц.
Целью данной работы является изучение влияния величины потенциала взаимодействия вещества катализатора с барьерным слоем, а также температуры и длительности отжига на формирование наночастиц катализатора.
ЭКСПЕРИМЕНТАЛЬНАЯ ЧАСТЬ
Для проведения исследования были изготовлены экспериментальные образцы с барьерным слоем нитрида металла и слоем катализатора, осажденные на кремниевую подложку. В качестве барьерного слоя использовался слой нитрида титана толщиной 20 нм, полученный методом атомно-слоевого осаждения (АСО) с активацией в индуктивно-связанной плазме. Процесс АСО проводился при температуре 300°C с применением металлорганического прекурсора TDMAT (C8H24N4Ti) и плазмы водорода. Тонкую пленку никеля, являющуюся слоем катализатора, напыляли методом электронно-лучевого испарения при давлении менее 5.0 × 10–5 Па. Толщина слоя катализатора составляла порядка 4 нм. Формирование наночастиц проводили при температурах 600, 700 и 800°C в среде водорода и аргона при давлении 200 Па. Для наблюдения динамики изменения размеров и плотности наночастиц время обработки варьировалось от 0.5 до 30 мин.
Изучение результатов термообработки образцов и формирования наночастиц катализатора на их поверхностях проводилось методами атомно-силовой микроскопии (АСМ) и растровой электронной микроскопии (РЭМ). Химический состав полученных структур определялся методом оже-спектроскопии с использованием эталонных образцов материалов для расчета соотношения химических элементов. С помощью просвечивающей электронной микроскопии (ПЭМ) с применением метода энергодисперсионного анализа (EDX – Energy Dispersive X-ray spectroscopy) проведен элементный анализ в области контакта барьерного слоя и наночастицы.
РЕЗУЛЬТАТЫ И ОБСУЖДЕНИЕ
Оже-спектры, которые были измерены сразу после синтеза нитрида титана методом АСО, показали, что состав пленки близок к стехиометрическому и распределение атомов по толщине пленки равномерное. Оже-спектры, полученные после напыления пленки катализатора на барьерный слой, показывают, что на поверхности барьерного слоя кроме атомов никеля присутствует только небольшое количество атомов углерода и кислорода, что вероятно, связано с загрязнениями, в то время как атомы титана или его соединения не наблюдаются. Глубина выхода оже-электронов с энергией около 400 эВ составляет порядка 3–5 нм, следовательно, электроны выходят только из пленки никеля и она является сплошной. В процессе отжига пленка никеля разрывается и появляется сигнал как от частиц Ni, так и от барьерного слоя TiN.
Результаты исследования методом РЭМ показывают, что на формирование наночастиц катализатора оказывают влияние как температура, так и время отжига. Отжиг при 600°C привел к разрыву пленки, но при этом наночастицы с четкими границами не сформировались даже в течение 30 мин. Для образования четко ограненных частиц при 700°C требуется 5 мин, а при 800°C они образуются уже после 1 мин отжига. РЭМ-снимки пленок, отожженных при температурах 700 и 800°C в течение 1 и 10 мин, приведены на рис. 1. При 800°C наночастицы крупнее, чем при 700°C. После 10 мин отжига при температуре 800°C количество частиц уменьшается, а их диаметры увеличиваются.
Рис. 1.
Наночастицы Ni на поверхности слоя TiN, сформированные термообработкой пленки Ni толщиной 4 нм при температуре 700°C в течение 1 (а), 10 мин (б) и 800°C в течение 1 (в), 10 мин (г).
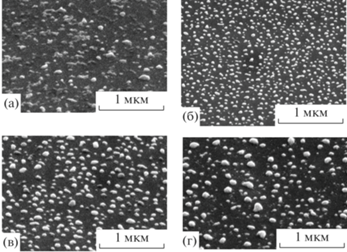
Наглядно эти процессы показывают диаграммы распределения наночастиц катализатора по размерам (рис. 2). С ростом температуры и времени отжига центры распределения смещаются в область больших диаметров, а количество частиц в максимуме распределения падает. Можно предположить, что укрупнение частиц связано с явлением коалесценции, при котором мелкие частицы сливаются с более крупными [14, 15].
Рис. 2.
Распределение наночастиц катализатора по диаметрам после отжига при 700°C, 1 мин (а); 700°C, 10 мин (б); 800°C, 10 мин (в).
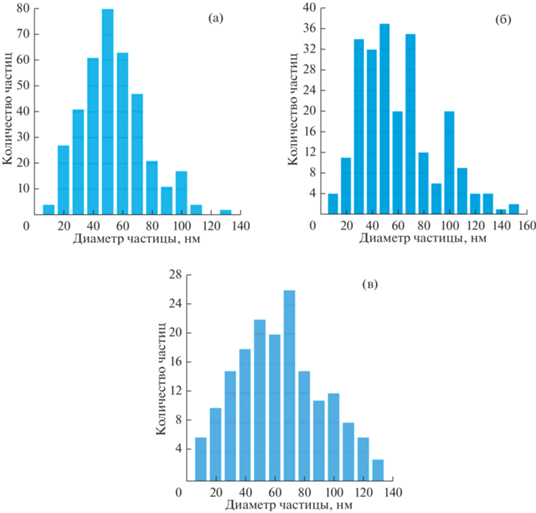
С целью определения формы наночастиц и уточнения распределения никеля на границе раздела Ni/TiN было проведено исследование методом ПЭМ высокого разрешения. На рис. 3а представлено ПЭМ-изображение частицы катализатора на поверхности барьерного слоя, а на рис. 3б показано изображение границы раздела слоев тонкой ламели, вырезанной ионным пучком, с наложенным распределением никеля и титана по глубине структуры Ni/TiN. Экспериментальные результаты приведены после термообработки при температуре 700°C.
Рис. 3.
Изображение наночастицы никеля на барьерном слое нитрида титана (а); распределение титана и никеля в области контакта наночастицы с барьерным слоем после термообработки пленки никеля толщиной 4 нм при температуре 700°C 5 мин: 1 – распределение никеля, 2 – распределение титана (б).
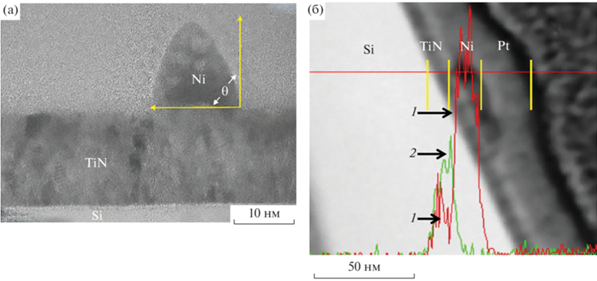
Видно, что после термообработки в объеме TiN фиксируется устойчивый сигнал от Ni с максимумом на границе раздела Si/TiN. Это указывает на диффузию никеля в барьерный слой. Электронограммы слоя нитрида титана показали, что диффузия никеля в этот слой приводит к образованию интерметаллических соединений Ni3Ti и NiTiO3.
Суммарная относительная масса никеля, пропорциональная объему никеля на барьерном слое, определялась с помощью распределений частиц, примеры которых показаны на рис. 2. Приблизительный объем частицы вычислялся по занимаемой площади с учетом ее формы (рис. 3а). Общий объем находили суммированием количеств частиц определенного размера (рис. 2). Эта процедура была выполнена для каждой температуры и каждого времени отжига. На рис. 4 представлены результаты этих вычислений для двух температур. Масса никеля падает с течением времени и с ростом температуры термообработки, что свидетельствует в пользу существования диффузии из наночастиц катализатора в барьерный слой, которая представляет собой случай диффузии из ограниченного источника. При этом первоначальная масса вещества на поверхности изменяется по закону
где m0 – первоначальная масса пленки катализатора, D – коэффициент диффузии никеля в нитрид титана, τ – время термообработки.
Формула (2) позволяет вычислить отношение коэффициентов диффузии при двух температурах термообработки – t1 и t2:
(3)
$\frac{{m_{1}^{2}(\tau )}}{{m_{2}^{2}(\tau )}} = \frac{{{{D}_{2}}}}{{{{D}_{1}}}} = \exp \left( {\frac{{E\left( {{{t}_{2}} - {{t}_{1}}} \right)}}{{k{{t}_{1}}{{t}_{2}}}}} \right),$Отношение квадрата количества вещества в наночастицах катализатора на поверхности (3) позволяет оценить энергию активации диффузии никеля в нитрид титана
(4)
$E = k\frac{{{{t}_{1}}t}}{{{{t}_{2}} - t}}\ln \left( {\frac{{m_{1}^{2}(\tau )}}{{m_{2}^{2}(\tau )}}} \right).$Усредняя отношение квадратов масс, вычисленное по данным рис. 4, и подставляя его в уравнение (4), получаем значение энергии активации 0.68 эВ. В работе [16] для коэффициента диффузии никеля в аморфном нитриде титана получено выражение D = 0.56exp(–67.3/RT) см2/с. В данном выражении энергия активации выражена в ккал/моль, что эквивалентно 0.70 эВ. Эта величина хорошо согласуется с полученным значением энергии диффузии, что подтверждает сделанные выше выводы о наличии диффузии никеля в слой нитрида титана во время формирования наночастиц путем термообработки.
МОДЕЛИРОВАНИЕ РАСПРЕДЕЛЕНИЯ НАНОЧАСТИЦ КАТАЛИЗАТОРА
Моделирование процессов формирования наночастиц катализатора и их распределений по размерам позволяет оптимизировать время и температуру термообработки, а также определить характеристики взаимодействия. С использованием полученных экспериментальных данных по формированию частиц никелевого катализатора была установлена приближенная зависимость для потенциала от толщины пленки V(h):
(5)
$V\left( h \right){\text{/}}\sigma = 24.8{{{\text{e}}}^{{ - 0.7h}}} - 77.1{{{\text{e}}}^{{ - 0.9h}}} + \frac{{27.2}}{{{{h}^{2}}}}{\text{\;}}\left( {\left[ h \right] = {\text{нм}}} \right).$Подбор параметров потенциала взаимодействия (5) осуществляется так, чтобы расчетные величины наилучшим образом описывали кинетику изменения геометрических характеристик наночастиц катализатора (рис. 5).
Рис. 5.
Сопоставление зависимостей среднего радиуса (а), средней высоты (б) и плотности (в) наночастиц катализатора от времени отжига при температуре 700°C с расчетом по формуле (1): точки – эксперимент, линии – расчет.
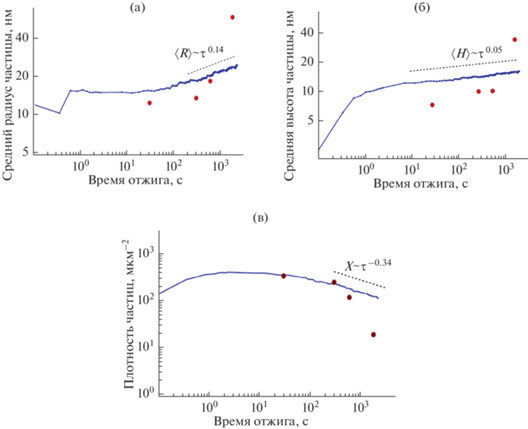
Качественно основные характеристики наночастицы – средний радиус (рис. 5а), высота (рис. 5б), поверхностная плотность (рис. 5в) – согласуются с результатами расчета. Однако гидродинамическая модель не учитывает диффузию никеля в нитрид титана. Поэтому экспериментальные точки, характеризующие размеры частиц, лежат несколько ниже расчетных величин. Причиной этого служит уменьшение массы, а следовательно, размеров частиц в результате диффузии. Когда время отжига превышает 5 мин (300 с), экспериментальные размеры наночастиц значительно превышают расчетные данные, а их плотность становится меньше расчетной. Как уже упоминалось выше, это связано с явлением коалесценции, которое состоит в поглощении большими частицами маленьких [14, 15]. Моделирование позволяет оценить величину динамической вязкости расплава никеля, которая составляет $\eta \sim 2 \times {{10}^{6}}$ Па с. Данное значение существенно выше вязкости никеля при температуре плавления $\eta \sim \left( {5{\kern 1pt} - {\kern 1pt} 10} \right) \times {{10}^{{ - 3}}}$ Па с, но значительно ниже характерного значения $\eta \sim {{10}^{{12}}}$ Па с, обычно связываемого с переходом из жидкого в твердое стеклообразное состояние. В связи с этим можно предположить, что ультратонкая пленка никеля толщиной 4 нм на поверхности нитрида титана при температуре 700°C находится в состоянии переохлажденной вязкой жидкости, так же как и пленка толщиной 9 нм на поверхности нитрида ниобия при температуре 880°C [9].
Для того чтобы показать, как потенциал взаимодействия оказывает влияние на размеры наночастиц катализатора, были проведены расчеты еще при трех модельных потенциалах (рис. 6). Используя значения модельных потенциалов взаимодействия, вычислили распределения наночастиц катализаторов по размерам. Расчетные значения величин распределения, а именно значение среднего радиуса и дисперсия, приведены в табл. 1.
Таблица 1.
Расчетные значения среднего радиуса и дисперсии распределений наночастиц катализатора по размерам для трех модельных потенциалов
Потенциал взаимодействия | А, нм2 | 〈R〉, нм | σ0, нм | 〈R〉, нм | σ0, нм | 〈R〉, нм | σ0, нм |
---|---|---|---|---|---|---|---|
τ = 100 с | τ = 200 с | τ = 300 с | |||||
V1 | 28.9 | 18.6 | 7.7 | 20.0 | 7.8 | 21.2 | 7.6 |
V2 | 27.2 | 12.3 | 3.9 | 13.7 | 3.9 | 14.3 | 3.9 |
V3 | 23.1 | 10.6 | 3.3 | 12.0 | 3.4 | 12.8 | 3.5 |
Примечание. А – числитель последнего слагаемого в формуле (5).
Расчет показывает, что с течением времени центр распределения смещается в сторону больших значений при постоянной дисперсии. С теоретической точки зрения размер частицы растет. Чем выше величина эффективного потенциала взаимодействия, тем больше размер наночастицы. Таким образом, с увеличением потенциала взаимодействия растет смачивание расплавом поверхности.
ЗАКЛЮЧЕНИЕ
Изучен процесс формирования наночастиц из тонкой пленки никеля толщиной 4 нм на барьерном слое нитрида титана, синтезированном методом АСО. Анализ состава пленки методом Оже показал, что он близок к стехиометрическому TiN и постоянен по толщине пленки. Показано, что геометрические размеры наночастиц металла катализатора, которые образуются при плавлении его тонкой пленки на поверхности нитрида титана, определяются рядом факторов, в т.ч. температурой и временем отжига пленки. В процессе отжига никель диффундирует в нитрид титана, в результате чего его количество на поверхности падает. Диффузия происходит с экспериментально определенной энергией активации 0.68 эВ, что согласуется с результатами работы [16]. Проникая в нитрид титана, никель частично остается в свободном состоянии, а частично образует интерметаллические соединения Ni3Ti и NiTiO3. При увеличении времени термообработки свыше 5 мин наблюдается явление коалесценции, которое увеличивает размеры частиц и уменьшает их поверхностную плотность, что нежелательно для синтеза нанотрубок. Поэтому время отжига следует ограничивать.
Эффективный потенциал взаимодействия па́ры никель–нитрид титана и вязкость расплава никеля при температуре отжига находились путем подгонки параметров численного расчета до лучшего согласия расчетных и экспериментальных результатов по кинетике изменения размеров наночастиц при отжиге. Величина вязкости соответствует переохлаженному расплаву никеля. Моделирование также показало, что увеличение потенциала взаимодействия вещества катализатора с барьерным слоем приводит к росту размеров наночастиц и, следовательно, диаметра синтезированных нанотрубок. Поэтому на размеры наночастиц оказывают влияние не только материал и толщина пленки катализатора [6, 7], но и взаимодействие металла с барьерным слоем на подложке.
Средний размер наночастиц зависит от потенциала взаимодействия между металлом и веществом барьерного слоя, температуры и длительности отжига, возможности возникновения явления коалесценции, существования диффузии металла в барьерный слой. Все эти факторы надо учитывать для получения частиц катализатора оптимальных размеров.
Список литературы
Булярский С.В. Углеродные нанотрубки: технология, управление свойствами, применение. Ульяновск: Стрежень, 2011. 480 с.
Dasgupta K., Joshi J.B., Banerjee S. Fluidized Bed Synthesis of Carbon Nanotubes – A Review // Chem. Eng. J. 2011. V. 171. № 3. P. 841–869. https://doi.org/10.1016/j.cej.2011.05.038
Kumar M., Ando Y. Chemical Vapor Deposition of Carbon Nanotubes: A Review on Growth Mechanism and Mass Production // J. Nanosci. Nanotechnol. 2010. V. 10. № 6. P. 3739–3758. https://doi.org/10.1166/jnn.2010.2939
Ago H., Komatsu T., Ohshima S., Kuriki Y., Yumura M. Dispersion of Metal Nanoparticles for Aligned Carbon Nanotube Arrays // Appl. Phys. Lett. 2000. V. 77. № 1. P. 79–81. https://doi.org/10.1063/1.126883
Melechko A.V., Merkulov V.I., McKnight T.E., Guillorn M.A., Klein K.L., Lowndes D.H., Simpson M.L. Vertically Aligned Carbon Nanofibers and Related Structures: Controlled Synthesis and Directed Assembly // J. Appl. Phys. 2005. V. 97. № 4. P. 41301. https://doi.org/10.1063/1.1857591
Lee C.J., Park J., Yu J.A. Catalyst Effect on Carbon Nanotubes Synthesized by Thermal Chemical Vapor Deposition // Chem. Phys. Lett. 2002. V. 360. № 3–4. P. 250–255. https://doi.org/10.1016/S0009-2614(02)00831-X
Andrews R., Jacques D., Qian D., Rantell T. Multiwall Carbon Nanotubes: Synthesis and Application // Acc. Chem. Res. 2002. V. 35. № 12. P. 1008–1017. https://doi.org/10.1021/ar010151m
Bulyarskiy S.V., Zenova E.V., Lakalin A.V., Molodenskii M.S., Pavlov A.A., Tagachenkov A.M., Terent’ev A.V. Influence of a Buffer Layer on the Formation of a Thin-Film Nickel Catalyst for Carbon Nanotube Synthesis // Tech. Phys. 2018. V. 63. № 12. P. 1834–1839. https://doi.org/10.1134/S1063784218120253
L’vov P.E., Bulyarskiy S.V., Gusarov G.G., Molodenskiy M.S., Pavlov A.A., Ryazanov R.M., Dudin A.A., Svetukhin V.V. Kinetics of Nickel Particle Formation on Silicon Substrate with a Buffer Layer of Niobium Nitride // J. Phys.: Condens. Matter. 2020. V. 32. № 24. P. 245001. https://doi.org/10.1088/1361-648X/ab7870
Львов П.Е., Светухин В.В., Булярский С.В., Павлов А.А. Моделирование смачивающих фазовых переходов в тонких пленках // Физика твердого тела. 2019. T. 61. № 10. C. 1916–1925.
Peng Y., Wang Z., Alsayed A.M., Yodh A.G., Han Y. Publisher’s Note: Melting of Colloidal Crystal Films // Phys. Rev. Lett. 2010. V. 104. № 21. P. 205703. https://doi.org/10.1103/PhysRevLett.104.219901
Thiele U. Recent Advances in and Future Challenges for Mesoscopic Hydrodynamic Modelling of Complex Wetting // Colloids Surf., A. 2018. V. 553. P. 487–495. https://doi.org/10.1016/j.colsurfa.2018.05.049
Shchekin A.K., Lebedeva T.S., Suh D. The Overlapping Surface Layers and the Disjoining Pressure in a Small Droplet // Colloids Surf., A. 2019. V. 574. P. 78–85. https://doi.org/10.1016/j.colsurfa.2019.04.071
Kukushkin S.A., Osipov A.V. Kinetics of First-Order Phase Transitions in the Asymptotic Stage // J. Exp. Theor. Phys. 1998. V. 86. № 6. P. 1201–1208. https://doi.org/10.1134/1.558591
Slezov V.V., Schmelzer J. Kinetics of Formation and Growth of a New Phase with a Definite Stoichiometric Composition // J. Phys. Chem. Solids. 1994. V. 55. № 3. P. 243–251. https://doi.org/10.1016/0022-3697(94)90139-2
Nowak W.B., Keukelaar R., Wang W., Nyaiesh A.R. Diffusion of Nickel Through Titanium Nitride Films // J. Vac. Sci. Technol., A. 1985. V. 3. № 6. P. 2242–2245. https://doi.org/10.1116/1.572900
Дополнительные материалы отсутствуют.
Инструменты
Неорганические материалы