Неорганические материалы, 2023, T. 59, № 3, стр. 251-259
Кинетика высокотемпературной нитридизации твердых растворов Zr–Nb
И. А. Ковалев 1, *, Г. П. Кочанов 1, В. Ю. Зуфман 1, Л. О. Львов 1, С. В. Шевцов 1, К. Ю. Демин 1, А. И. Ситников 1, А. В. Шокодько 1, С. С. Стрельникова 1, А. С. Чернявский 1, К. А. Солнцев 1
1 Институт металлургии и материаловедения им. А.А. Байкова
Российской академии наук
119334 Москва, Ленинский пр., 49, Россия
* E-mail: vankovalskij@mail.ru
Поступила в редакцию 30.11.2022
После доработки 11.01.2023
Принята к публикации 12.01.2023
- EDN: YSIIVM
- DOI: 10.31857/S0002337X23030089
Аннотация
Определены кинетические закономерности образования нитридов сплавов Zr–Nb (содержание Nb 0.1, 2.5 и 5 мас. %) при температуре 1900°C. Процесс азотирования характеризуется двухстадийностью, где обе стадии описываются экспоненциальным законом. Скорость химической реакции на второй стадии значительно меньше, чем на первой. Охарактеризован состав формирующихся гетероструктур Zr1–хNbхN–ZrN1–n/β-твердый раствор циркония в ниобии–Zr1–хNbхN, установлена последовательность нитридизации компонентов исходного сплава. На первой стадии процесса происходят образование α-твердого раствора азота в Zr и его переход в нестехиометрический нитрид. Кинетическая зависимость на второй стадии описывает нитридизацию фазы β-Nb, образовавшейся при распаде твердого раствора Zr〈Nb〉. Показано, что продолжительность второй стадии процесса определяется количеством ниобия в исходном твердом растворе. Экспериментально подтверждена возможность создания однофазной керамики с активными добавками нитридизацией сплавов Zr–М в одностадийном процессе с сохранением исходной формы металлической заготовки.
ВВЕДЕНИЕ
Сплавы на основе твердого раствора ниобия в цирконии и керамика на основе их нитридов находят широкое применение в качестве конструкционных материалов в аэрокосмической индустрии, машиностроении, атомной энергетике и медицине [1–4]. Керамика на основе нитридов металлов подгруппы титана может выполнять функцию матрицы, в состав которой вводят добавки в виде фаз, снижающих или повышающих пористость, замедляющих рост зерен, повышающих трещиностойкость и прочность на изгиб [4–7]. В качестве добавок используют порошки металлов, смеси с непроводящими включениями [8, 9], нитриды урана и трансуранидов [1–4, 9–11]. Введение дополнительных компонентов в исходную шихту осложняет и без того непростой процесс компактирования нитридов [12, 13]. Ранее авторами был реализован подход, позволяющий синтезировать керамику заданной формы в процессе полной нитридизации металлических заготовок [14–16]. Так, прямой нитридизацией металлов подгруппы титана синтезирована однокомпонентная нитридная керамика и композитные гетероструктуры на основе нитридов с разным содержанием азота [17]. В работе [18] описан процесс нитридизации сплавов Zr–Nb с содержанием Nb от 0.1 до 5 мас. %.
В доступной литературе процессы, протекающие при высокотемпературной нитридизации сплавов на основе циркония, практически не описаны, поэтому исследование кинетики процесса и закономерностей формирования субструктуры представляет значительный научный интерес.
Цель работы – исследование кинетики нитридизации и структурных превращений в процессе образования компактных нитридов сплавов Zr〈Nb〉.
ЭКСПЕРИМЕНТАЛЬНАЯ ЧАСТЬ
В качестве объектов исследования были взяты металлические сплавы Zr–Nb (0.1, 2.5, 5.0% Nb)11 в виде лент длиной 60 и сечением 3.0 × 0.3 мм, которые резистивно нагревали в атмосфере азота особой чистоты марки “6.0” (ГОСТ 10157-79) до температуры 1900°C, расположенной вблизи температуры перитектической реакции [19]. Выбор температурно-временных режимов обусловлен особенностями протекания нитридизации сплавов ниобия [20]. Фольгу перечисленных составов изготавливали прокаткой слитков [18]. Температуру реакции контролировали пирометром LumaSense IMPAC ISR 50-LO (Германия) (погрешность 0.1% в рассматриваемом диапазоне температур).
Кинетику насыщения сплавов азотом экспериментально определяли по приросту массы образца за время от 3 до 60 мин. Погрешность измерения массы составляла ±0.0001 г. В процессе нагрева оценивали изменение электросопротивления образца.
Фазовый состав приповерхностного слоя (глубиной ~7 мкм) и порошковых проб образцов определяли на вертикальном рентгеновском θ–2θ-дифрактометре XRD–6000, Shimadzu, а также на θ–θ-дифрактометре ARL X`TRA в геометрии Брэгга–Брентанно. В качестве источника использовали рентгеновскую трубку с медным анодом (CuKα). Приборы откалиброваны по стандартному образцу NIST SRM-1976a, средняя погрешность положения рефлексов на оси 2θ относительно эталона не превышала 0.005°. Кристаллические фазы идентифицировали по банку данных [21]. Параметр кристаллической решетки определяли методом экстраполяции к θ = 90° функцией Нельсона–Райли и аппроксимации их прямой по МНК; относительная погрешность в определении межплоскостных расстояний составляла 5 × 10–5 нм.
Морфологию поверхности поперечных сколов и шлифов исследовали на растровом электронном микроскопе (РЭМ) LEO 1420, Carl Zeiss и на оптическом инвертированном микроскопе Carl Zeiss Axio Observer 3 в поляризационном и дифференциально-интерференционном рельефном контрастах. Для оценки состава фаз, обнаруженных в образцах, был использован электронный микроанализатор JEOL JXA-iSP100, оснащенный детекторами вторичных и обратно-рассеянных электронов для наблюдения внешнего вида образцов, а также энерго-дисперсионным детектором характеристического рентгеновского излучения, возникающего при взаимодействии электронного пучка с образцом. Исследования проводились в режиме “точечный анализ” и “картирование”, т.е. построение карты распределения концентраций элементов по поверхности образца.
РЕЗУЛЬТАТЫ И ОБСУЖДЕНИЕ
На рис. 1 приведены кинетические зависимости доли поглощенного азота W (отношение привеса образца к исходному весу) от времени. Ошибка измерений не превышает 5%.
Рис. 1.
Кинетика насыщения азотом сплавов Zr–Nb, содержащих 0.1, 2.5, 5.0% Nb, при температуре нитридизации 1900°C.
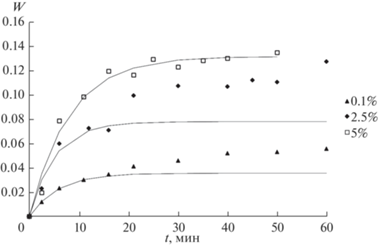
Анализ кинетических закономерностей показал, что процесс насыщения сплава азотом протекает в две стадии: первая и вторая стадии реакции описываются экспоненциальным законом
где W0 – предэкспоненциальный множитель, k – константа скорости (мин–1).При достижении величины предельного привеса W0 начинается вторая стадия, также аппроксимируемая экспоненциальной зависимостью, на которой химическая реакция значительно замедляется. На начальной стадии азотирования в структуре MNxх = 0.23 для 0.1% Nb, при 2.5% х = 0.5, при 5 мас. % х = 0.85. Для сплава, содержащего 5% ниобия, основное количество азота реагирует на первой стадии и второй участок кинетической кривой слабо выражен. Предэкспоненциальный множитель и константа скорости линейно зависят от содержания ниобия в сплаве (рис. 2). Увеличение содержания ниобия в исходном сплаве ускоряет процесс нитридизации.
Рис. 2.
Зависимости предэкспоненциального множителя (а) и константы скорости реакции (б) от содержания ниобия в сплаве.
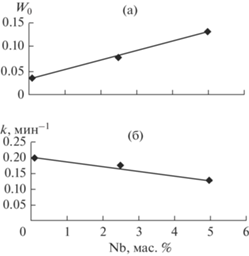
На рис. 3 представлена зависимость электрического сопротивления образцов от времени синтеза. В процессе достижения заданной температуры и при выходе на режим сопротивление образцов с содержанием 2.5 и 5% Nb увеличивается до максимальных значений; с увеличением доли поглощенного азота следует плавное снижение. Для сплава с 0.1% Nb максимум не выражен и сопротивление выходит на плато. Электрическое сопротивление сплавов снижается с увеличением содержания ниобия (рис. 3), что связано с увеличением дефектности и, соответственно, большим вкладом в проводимость ионной составляющей [22].
Ниобий искажает решетку циркония и образует дефекты, облегчая диффузию азота, что приводит к увеличению количества поглощенного азота в единицу времени. После того как металлы, входящие в состав сплава, прореагировали с азотом во всем объеме, начинается вторая стадия процесса, на которой происходит азотирование нестехиометрических нитридов. При образовании нитридов с дефицитом по азоту происходит изменение соотношения коэффициентов диффузии (объемного и зернограничного) [22], что приводит к изменению параметров кинетической кривой и снижению скорости процесса.
Ранее авторами было установлено, что в исследуемом температурном интервале в течение 60 мин поглощение азота чистым цирконием протекает в две стадии: первая стадия аппроксимируется экспоненциальной зависимостью, вторая – линейной [23]. Для установления природы двухстадийности нитридизации сплавов Zr–Nb исследовали фазовый состав образцов с разным временем азотирования. Из анализа рентгеновских дифрактограмм исходных сплавов Zr–Nb с содержанием Nb от 0.1 до 5% следует, что при содержании Nb ≤ 2.5% сплавы однофазные и представляют собой α-твердый раствор Zr〈Nb〉 (ГПУ, пр. гр. P/63mmc (194), а при содержании Nb ≥ 5.0% сплавы двухфазные, являются смесью α- и β-твердых растворов (ОЦК, пр. гр. $Im\bar {3}m$ (229)) [3, 24], причем c увеличением содержания ниобия доля β-фазы увеличивается [18].
Таблица 1.
Результаты локального элементного анализа поверхности поперечного шлифа образца, содержащего 5% Nb, после нитридизации при 1900°C в течение 6 и 21 мин (см. рис. 9)
Время нитридизации, мин | Элемент | С, ат. % | |||
---|---|---|---|---|---|
спектр 1 | спектр 2 | спектр 3 | спектр 4 | ||
6 | N | 3.02 | 43.98 | 50.98 | 52.28 |
Zr | 72.45 | 54.06 | 47.89 | 46.90 | |
Nb | 24.53 | 1.06 | 1.13 | 0.82 | |
21 | N | 0.51 | 49.70 | 52.30 | 52.37 |
Zr | 11.14 | 49.06 | 46.25 | 46.51 | |
Nb | 88.35 | 1.24 | 1.45 | 1.13 |
На рис. 4 представлены дифрактограммы приповерхностного слоя и объема образца. Из анализа дифрактограмм следует, что при τ = 3.5 мин при 1900°C приповерхностный слой состоит из фазы стехиометрического нитрида (рис. 4, дифрактограмма 1), а образующаяся композитная гетероструктура в объеме образца – из нитрида циркония разной стехиометрии и металлического остатка, содержащего две фазы (рис. 4, дифрактограмма 2): основной фазы α-твердого раствора азота в цирконии [24, 25] и следов не вступившего в реакцию с азотом β-твердого раствора ниобия в цирконии.
Рис. 4.
Дифрактограммы сплава Zr–Nb с содержанием 5% Nb в начале процесса нитридизации: 1 – приповерхностный слой образца, 2 – металлический остаток образца при τ = 3.5 мин, 3 – порошковая проба образца при τ = 6 мин.
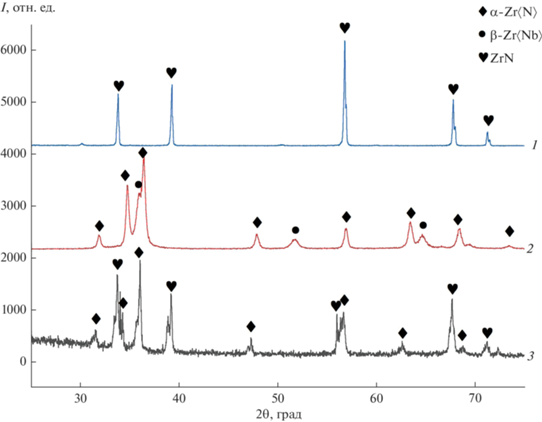
По прошествии 6 мин в объеме образца фиксируются только фазы нитридов циркония и твердого раствора азота в цирконии (рис. 4, дифрактограмма 3).
Сопоставление дифрактограмм нитридов сплавов Zr〈Nb〉 с содержанием 2.5% Nb (рис. 5) с кинетической кривой (рис. 1) подтверждает, что изменение кинетического закона происходит в момент полной конверсии твердого раствора α-Zr〈Nb〉 в нестехиометрический нитрид.
Рис. 5.
Рентгеновские дифрактограммы образцов, полученных в результате нитридизации сплава Zr–Nb c содержанием 2.5% Nb при 1900°C в течение 11 (1), 21 (2), 45 (3), 180 мин (4) [26 ] .
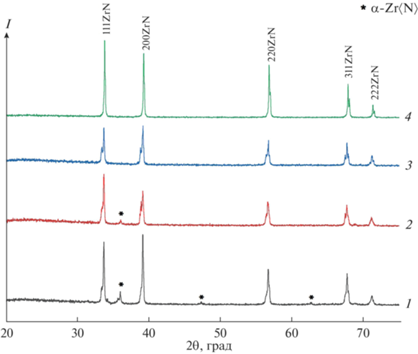
На рис. 6 представлено изменение параметра кристаллической решетки ZrN в процессе синтеза.
Рис. 6.
Изменение параметра а кристаллической решетки ZrN в нитридах сплавов Zr–Nb (2.5 и 5.0 мас. % Nb) в процессе синтеза при 1900°С в течение 60 мин.
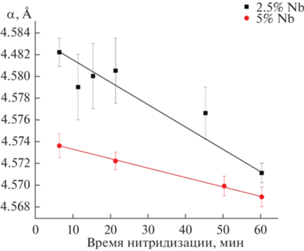
На рис. 7 приведены микрофотографии поверхности поперечных сколов нитридов сплавов Zr–Nb (2.5% Nb) с разным временем азотирования.
Рис. 7.
Морфология поверхности поперечных шлифов образца, полученного в результате нитридизации сплава Zr–Nb, содержащего 2.5 мас. % Nb, при 1900°C в течение 3.5 (а), 6 (б), 16 (в) и 21 мин (г).
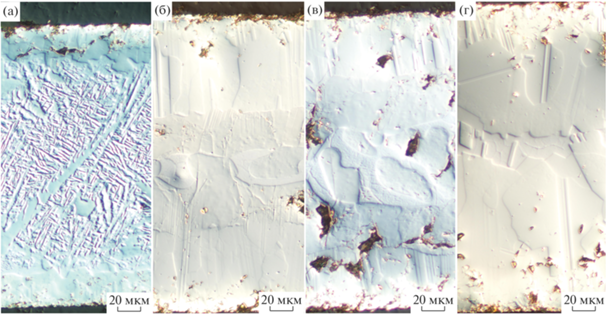
Толщина образца незначительно увеличивается от 300 до 322 мкм для 2.5% Nb и от 300 до 331 мкм для 5% Nb. На первом участке кинетической кривой образуются градиентные слоистые структуры с уменьшением концентрации азота к центру образца. При τ = 3.5 мин в образце (Zr–2.5% Nb)Nх морфологически четко определяются два нитридных слоя разной толщины, соответствующих стехиометрическому и нестехиометрическому нитридам, и слой твердого раствора азота в сплаве. При τ = 6 мин толщина слоя стехиометрического нитрида увеличивается до 65 мкм, а нестехиометрического – до 53 мкм. При τ = 21 мин толщина внешнего слоя достигает 134 мкм, а внутренний слой (до 24 мкм) представляет собой α-твердый раствор азота в сплаве и сохраняется в объеме нестехиометрического нитрида в виде включений до окончания нитридизации (рис. 7г).
Для образца (Zr–0.1% Nb)Nх поверхность представлена поликристаллическим нитридным слоем толщиной до 10 мкм с размерами кристаллитов 5–10 мкм (рис. 8а). В приповерхностной зоне размер пор – до 100 нм, на внутренней границе – 1–3 мкм. Основной слой стехиометрического нитрида имеет размер зерен в десятки микрон и не содержит пор. Центральная часть образца однородна и представлена поликристаллической фазой твердого раствора азота в сплаве.
Рис. 8.
Морфология поверхности поперечных сколов (а, в, д) и шлифов (б, г, е) образцов нитридов Zr–Nb с содержанием 0.1 (а, б), 2.5 (в, г), 5% Nb (д, е) (1900°C, 6 мин).
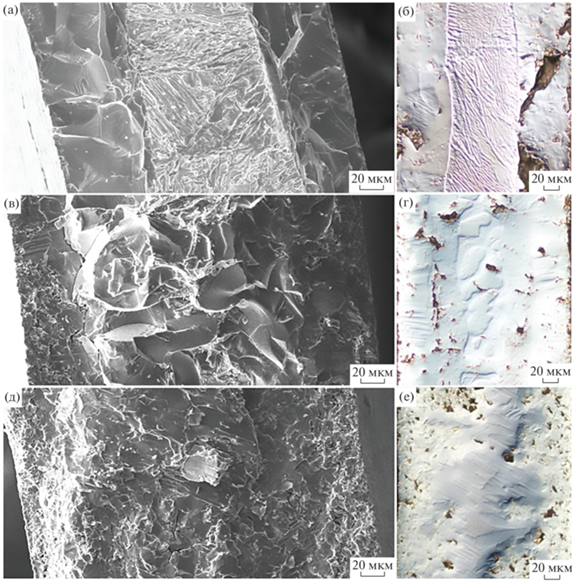
Повышение концентрации ниобия до 2.5% приводит к формированию на поверхности слоя нитрида толщиной до 60 мкм с множеством пор и размером зерен 1–5 мкм. Зерна на внутренней границе слоя имеют размер в десятки микрон с редкими межзеренными порами. Размер зерен в центральной части образца составляет ~100 мкм, наблюдаются включения металлической фазы между кристаллитами (рис. 8в, 8г).
Морфология поверхности скола приповерхностного слоя нитрида твердого раствора Zr–5% Nb близка к морфологии Zr–2.5% Nb, мелкокристаллическая керамическая фаза занимает больший объем образца. Металлическая фаза не фиксируется (рис. 8д, 8е).
Сопоставление РЭМ-изображений поверхности поперечных сколов нитридов сплавов Zr–Nb разного состава подтверждает вывод о зависимости скорости нитридизации от содержания ниобия. При 1900°C для образца Zr–2.5% Nb лимитирующей стадией является нитридизация имеющего высокую температуру плавления α-твердого раствора азота в цирконии, процесс азотирования которого протекает по диффузионному механизму. Для образца Zr–5% Nb, в соответствии с диаграммой состояния Zr–Nb [24], процесс нитридизации идет через образование жидкой фазы с множественным зарождением нитридной фазы (рис. 8), что приводит к ускорению образования нитрида сплава Zr–Nb и сокращению второй стадии процесса.
На рис. 9 представлено элементное картирование поверхности поперечного шлифа образца после нитридизации сплава Zr–Nb, содержащего 5% Nb, при 1900°C в течение 6 и 21 мин. На границе с нитридом циркония видно увеличение концентрации металлического ниобия. Сепарация фазы металлического ниобия происходит вследствие его низкой растворимости в нитриде циркония (~1 ат. %). Это приводит к появлению в формирующемся нитриде включений с содержанием Nb до 88 ат. %. Нитридизация выделившегося β-ниобия происходит на второй стадии процесса.
ЗАКЛЮЧЕНИЕ
Установлены кинетические закономерности взаимодействия твердых растворов Zr–Nb с азотом. Процесс характеризуется двухстадийностью. В отличие от нитридизации чистых металлов обе стадии реакции описываются экспоненциальным законом. На первой стадии происходит образование нитридов циркония на поверхности и α-твердого раствора азота в цирконии в объеме образца. Вторая стадия процесса начинается после конверсии α-твердого раствора азота в Zr и включения в химическую реакцию фазы β-Nb, образовавшейся при распаде твердого раствора Zr〈Nb〉, причем скорость химической реакции азотирования на второй стадии процесса значительно меньше, чем на первой.
Обнаружено, что продолжительность второй стадии процесса уменьшается с увеличением содержания ниобия в исходном сплаве. Для сплавов с высоким содержанием ниобия нитридизация проходит на первой стадии, второй участок кинетической кривой практически не выражен. Это объясняется образованием на первой стадии нестехиометрического нитрида ZrNx с повышенным содержанием азота. Например, для сплава Zr–5% Nb содержание азота х = 0.85, что близко к стехиометрии. Быстрое формирование стехиометрического нитрида приводит к увеличению скорости нитридизации α-твердого раствора азота в Zr и частичной нитридизации распределенного в объеме нитрида циркония β-ниобия уже на первой стадии. Вторая часть кинетической кривой описывает нитридизацию образовавшихся после распада внутреннего слоя твердого раствора включений β-ниобия с низким содержанием циркония. При большем содержании ниобия в исходном сплаве вторая стадия не выражена и процесс нитридизации аппроксимируется одностадийным кинетическим законом.
Образующийся нитрид ниобия полностью растворяется в нитриде циркония, при этом уменьшается параметр кристаллической решетки. Нитридизацию сплавов Zr–М заданного состава можно использовать для одностадийного создания керамики, содержащей необходимые активные добавки.
Список литературы
Кононов А.Г., Кукареко В.А., Белый А.В., Шаркеев Ю.П. Ионно-модифицированные субмикрокристаллические титановые и циркониевые сплавы для медицины и техники // Механика машин, механизмов и материалов. 2013. Т. 1. № 22. С. 47–53.
Zhaoa Y., Lib H., Huanga Yu. The Structure, Mechanical, Electronic and Thermodynamic Properties of bcc Zr–Nb Alloy: A First Principles Study // J. Alloys Compd. 2021. V. 862. P. 158029. https://doi.org/10.1016/j.jallcom.2020.158029
Daniel C.S., Honniball P.D., Bradley L., Preuss M., Fonseca J.Q. Texture Development during Rolling of α + β Dual-Phase ZrNb Alloys // Zirconium in the Nuclear Industry: 18th Int. Symp. STP 1597. 2018. https://doi.org/10.1520/STP159720160070
Соколенко В.И., Мац А.В., Мац В.А. Механические характеристики наноструктурированных циркония и цирконий-ниобиевых сплавов // Физика и техника высоких давлений. 2013. Т. 23. № 2. С. 96–102.
Liua Ya., Yanga Yu., Donga D., Wanga J., Zhoua L. Improving Wear Resistance of Zr-2.5Nb Alloy by Formation of Microtextured Nitride Layer Produced Via Laser Surface Texturing/Plasma Nitriding Technology // Surf. Interfaces. 2020. V. 20. P. 100638. https://doi.org/10.1016/j.surfin.2020.100638
Chernyavskii A.S. Synthesis of Ceramics Based on Titanium, Zirconium, and Hafnium Nitrides // Inorg. Mater. 2019. V. 55. № 13. P. 1303–1327. https://doi.org/10.1134/S0020168519130016
Graziani T., Bellosi A. Densification and Char Acteristics of TiN Ceramics // J. Mater. Sci. Lett. 1995. V. 14. № 15. P. 1078–1081. https://doi.org/10.1007/BF00258170
Bashlykov S.S., Demenyuk V.D., Grigor’ev E.G., Olevskii E.A., Yurlova M.S. Electropulse Consolidation of UN Powder // Inorg. Mater.: Appl. Res. 2014. V. 5. № 3. P. 278–283. https://doi.org/10.1134/S2075113314030034
Деменюк В.Д., Юрлова М.С., Лебедева Л.Ю., Григорьев Е.Г., Олевский Е.А. Методы электроимпульсной консолидации: альтернатива спарк-плазменному спеканию (обзор литературы) // Ядерная физика и инжиниринг. 2013. Т. 4. № 3. С. 195–239. https://doi.org/10.1134/S2079562913030019
Смирнова Д.Е., Стариков С.В., Гордеев И.С. Исследование фазовых переходов и механизмов деформации в цирконии и сплавах цирконий-ниобий: Атомистическое моделирование. Сб. материалов VII Междунар. конф. “Деформация и разрушение материалов и наноматериалов” (7–10 ноября 2017 г.) М.: ИМЕТ РАН, 2017. 951 с.
Белый А.В., Кононов А.Г., Кукареко В.А. Влияние ионно-лучевого азотирования на структурнофазовое состояние и триботехнические характеристики поверхностных слоев сплава Zr–2.5% Nb // Тр. БГТУ. 2016. № 2. С. 87–99.
Pshenichnaya O.V., Kuzenkova M.A., Kislyi P.S. Effect of Powder Particle Size on the Sintering of Zirconium Nitride // Powder Metall. Met. Ceram. 1979. V. 18. P. 882–887.
Petrykina Y.R., Shvedova K.L. Hot Pressing of Transition Metal Nitrdes and Their Properties // Poroshk. Metall. 1972. V. 11. № 4. P. 276–279.
Solntsev K.A., Shustorovich E.M., Buslaev Y.A. Oxidative Constructing of Thin-Walled Ceramics (OCTWC) // Dokl. Chem. 2001. V. 378. № 4–6. P. 143–149.
Солнцев К.А., Шусторович Е.М., Чернявский А.С., Дуденков И.В. Окислительное конструирование тонкостенной керамики (ОКТК) выше температуры плавления металла: получение оксидных волокон из волокон Ai и его сплава // Докл. Академии наук. 2002. T. 385. № 3. C. 372–377.
Кузнецов К.Б., Шашкеев К.А., Шевцов С.В., Огарков А.И., Третьяков Н.Н., Саприна М.П., Костюченко А.В., Чернявский А.С., Иевлев В.М., Солнцев К.А. Структура и твердость керамики, полученной в процессе высокотемпературной нитридизации циркониевой фольги // Неорган. материалы. 2015. Т. 51. № 8. С. 893–900. https://doi.org/10.7868/S0002337X15080126
Шевцов С.В., Огарков А.И., Ковалев И.А., Кузнецов К.Б., Просвирнин Д.В., Ашмарин А.А., Чернявский А.С., Солнцев К.А. Структурно-фазовые превращения и твердость керамики, получаемой в процессе высокотемпературной нитридизации циркония // Журн. неорган. химии. 2016. Т. 61. № 12. С. 1635–1639. https://doi.org/10.7868/S0044457X16120163
Ковалев И.А., Канныкин С.В., Коновалов А.А., Кочанов Г.П., Огарков А.И., Тарасов Б.А., Шорников Д.П., Стрельникова С.С., Чернявский А.С., Солнцев К.А. Фазовые превращения при высокотемпературной нитридизации сплавов Zr–Nb // Неорган. материалы. 2022. Т. 58. № 4. С. 382–388. https://doi.org/10.31857/S0002337X22040078
Ushakov S.V., Navrotsky A., Hong Q-J., Walle A. Carbides and Nitrides of Zirconium and Hafnium // Materials. 2019. V. 12. № 17. P. 2728. https://doi.org/10.3390/ma12172728
Kovalev I.A., Kochanov G.P., L’vov L.O., Shevtsov S.V., Kannikin S.V., Sitnikov A.N., Strel’nikova S.S., Chernyavskii A.S., Solntsev K.A. Compositional Evolution of Zirconium and Niobium in the Process of High-Temperature Nitridation of Zr–Nb Alloys // Mendeleev Commun. 2022. V. 32. № 4. P. 498–500. https://doi.org/10.1016/j.mencom.2022.07.022
Powder Diffraction File. Alphabetical Index Inorganic Compounds. Pensilvania: ICPDS. 1997.
Бутягин П.Ю. Химическая физика твердого тела М.: Изд-во МГУ. С. 185.
Кузнецов К.Б., Ковалев И.А., Зуфман В.Ю., Огарков А.И., Шевцов С.В., Ашмарин А.А., Чернявский А.С., Солнцев К.А. Кинетика насыщения циркония азотом в процессе высокотемпературной нитридизации // Неорган. материалы. 2016. Т. 52. № 6. С. 609–611. https://doi.org/10.7868/S0002337X16060075
Abriata J.P., Bolcich J.C. The Nb−Zr (Niobium−Zirconium) System // J. Phase Equilib. 1982. № 3 (1). P. 34–44.
Самсонов Г.В., Виницкий И.М. Тугоплавкие соединения: Справочник, 2–е изд. М.: Металлургия, 1976. 560 с.
Дополнительные материалы отсутствуют.
Инструменты
Неорганические материалы