Приборы и техника эксперимента, 2022, № 4, стр. 106-114
ИЗМЕРЕНИЕ РАСПРЕДЕЛЕНИЯ ЧАСТИЦ ПО СЕЧЕНИЮ ТРАКТА УСКОРИТЕЛЯ ДЛЯ МОДЕЛИРОВАНИЯ МИКРОМЕТЕОРИТОВ С ПОМОЩЬЮ ИНДУКЦИОННОГО ДАТЧИКА
А. В. Пияков a, *, А. М. Телегин a
a Самарский национальный исследовательский университет им. академика С.П. Королева
(Самарский университет)
443086 Самара, Московское ш., 34, Россия
* E-mail: piyakov.av@ssau.ru
Поступила в редакцию 26.01.2022
После доработки 15.03.2022
Принята к публикации 19.03.2022
- EDN: WGRJLL
- DOI: 10.31857/S0032816222040243
Аннотация
Рассмотрены методы определения координаты по сечению тракта ускорителя пролета микронных частиц. Приведены расчеты и результаты моделирования работы датчика для измерения распределения частиц по сечению тракта ускорителя и данные проведения эксперимента. Показано, что распределение частиц по сечению тракта на входе в камеру близко к нормальному закону распределения.
ВВЕДЕНИЕ
При проведении экспериментов по соударению высокоскоростных пылевых частиц с материалами конструкций космических аппаратов для повышения качества эксперимента желательно знать плотность распределения частиц по поверхности экспонируемого образца, а еще лучше – точные координаты попадания частиц на мишень, которые бывают необходимы для калибровки датчиков микрометеоритов. На рис. 1 показана задвижка из тракта ускорителя, центральная часть которой была запылена в процессе работы ускорителя микрочастицами (данная задвижка отсекает тракт ускорителя от экспериментальной камеры для обеспечения возможности работы с образцами без выключения ускорителя и развакуумирования его тракта), что говорит о том, что микрочастицы движутся в тракте ускорителя не строго по оси, а распределены по всему сечению тракта.
Рис. 1.
Фотография задвижки, установленной в тракте ускорителя микронных частиц перед камерой для экспериментов. Стрелкой показана область распыления микрочастиц в тракте.
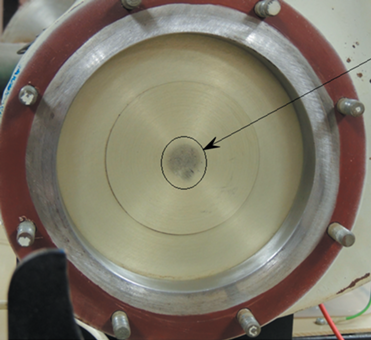
Согласно рис. 1, имеет место распределение частиц по всему тракту ускорителя в пределах внутреннего диаметра дрейфовых трубок, который составляет 20 мм.
Для проведения измерений плотности распределения частиц по сечению тракта в работе [1] предложен датчик, построенный с использованием метода разделения зарядов, в котором координата частицы вычисляется как функция амплитуды напряжения на краях резистивного слоя плоской пластины. В [2] описывается конструкция датчика, работа которого основана на использовании времяпролетного метода для измерения времени пролета частицы от индукционного датчика (цилиндра Фарадея) до места соударения с мишенью. Геометрическая форма мишени выполнена в виде винтовой спирали, что позволяет определить расстояние от начала датчика до поверхности мишени как функцию угловой и радиальной координаты. Однако оба этих способа используют удар частицы о поверхность датчика в качестве источника измеряемого сигнала, что не позволяет одновременно измерять координаты частицы и использовать эту же частицу в дальнейших экспериментах. В [3] описана конструкция и представлены экспериментальные данные работы индукционного датчика, позволяющего измерять координаты частицы в процессе ее движения в вакуумной камере бесконтактным способом. Данный детектор состоит из четырех пар плоских пластин, на которые заряженная частица наводит заряд. Недостатком такого датчика является то, что измерение координат происходит неодновременно, что вносит погрешность в результат измерения координат частиц при движении частицы не параллельно оси ускорителя. Для устранения данного недостатка предлагается использовать индукционный датчик, координаты пролета частицы в котором определяются по принципу триангуляции.
КОНСТРУКЦИЯ ИНДУКЦИОННОГО ДАТЧИКА
Схема датчика для определения координаты пролета заряженной частицы приведена на рис. 2, его фотография – на рис. 3.
Рис. 2.
Схема конструкции индукционного датчика. 1 – экранирующая трубка, 2 – диэлектрическая стойка, 3 – латунная стойка, 4 – медная пластина, 5 – зарядочувствительный усилитель, 6 – заглушки, 7 – корпус.
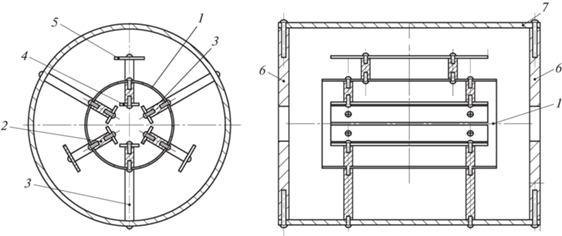
Рис. 3.
Фотография индукционного датчика без передней заглушки (для наглядности снята). Позиции те же, что и на рис. 2.
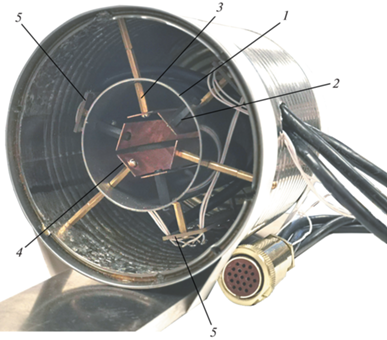
Экранирующая трубка 1 выполнена из нержавеющей стали и имеет размеры: длина 100 мм, внешний диаметр трубки 51 мм, толщина стенки 1 мм. Медные пластины 4 размером 11 × 90 мм имеют толщину 1 мм. Диэлектрические (нейлон) 2 и латунные 3 стойки служат для позиционирования медных пластин внутри датчика и имеют одинаковую высоту 12 мм, в них выполнено резьбовое отверстие М2. Латунные стойки обеспечивают контакт прикрепленных к ним пластин с экранирующей трубкой. Емкость медных пластин, служащих электродами, относительно экранирующей трубки составляет 5.8 пФ, межэлектродная емкость 2.5 пФ.
Ранее при работе с ускорителем микронных частиц для усиления сигналов с индукционных датчиков нами применялись зарядочувствительные усилители (ЗЧУ), схема и конструкция которых, а также результаты экспериментов с которыми приведены в работах [4, 5]. Однако данные усилители имеют большие габариты (размер печатной платы составляет 116 × 56 мм) и их размещение в вакуумной камере в непосредственной близости от медных пластин датчика весьма проблематично. Для уменьшения габаритов новые ЗЧУ были выполнены по схеме, предложенной в [6] и представленной на рис. 4, однако номиналы элементов схемы с целью повышения коэффициента усиления ЗЧУ подверглись небольшой коррекции.
Так, в обратной связи первого операционного усилителя были установлены конденсатор С1 емкостью 1 пФ (в оригинальной схеме применялись конденсаторы 2 или 10 пФ) и резистор R1 сопротивлением 1 ГОм (в оригинальной схеме 500 МОм). Добавлены защитные диоды D1 и D2, а также в обратной связи второго операционного усилителя установлен резистор R3 номиналом 100 кОм (в оригинальной схеме 10 кОм), что позволило увеличить коэффициент усиления зарядочувствительного усилителя. Размеры печатной платы нового ЗЧУ составили 61.5 × 17 мм. Входы усилителей подключены к соответствующим медным пластинам, а выходы соединены с разъемом РС19 посредством коаксиального кабеля РК50. Питание усилителей осуществляется по проводу МГТФ-0,12, выведенному в тот же разъем. Применение разъема РС19 обусловлено наличием гермоперехода РСГСП19 в вакуумной камере, в которой установлен датчик. Питание усилителей двухполярное и осуществлялось от двух батареек типа 3R12 с напряжением 4.5 В.
Для уменьшения возможных помех зарядочувствительные усилители расположены в непосредственной близости от медных пластин. Так как топология печатной платы фактически выполнена в одном слое (за исключением контактных площадок разъемов и выводных элементов, которые возможно сформовать для планарного монтажа), то в дальнейшем предлагается установить зарядочувствительные усилители непосредственно вместо медных пластин. При этом нижний слой печатной платы, представляющий собой цельную медную фольгу, будет служить индукционным датчиком, а на верхнем слое реализована топология зарядочувствительного усилителя. Такая компоновка позволит уменьшить габариты датчика и избавиться от внешнего корпуса, так как его функцию будет выполнять экранирующая трубка.
Сравнение усилителей показало, что предложенный усилитель обладает большей чувствительностью при более простой электрической схеме и меньших габаритах печатной платы. На рис. 5 приведена осциллограмма сигналов, наведенных одной и той же частицей, последовательно пролетающей два соседних индукционных датчика (цилиндра Фарадея) измерительной линейки ускорителя микрочастиц, и усиленных разными зарядочувствительными усилителями. Подробное описание индукционного датчика приведено в [5].
Рис. 5.
Осциллограммы сигналов с одинаковых индукционных датчиков для разных зарядочувствительных усилителей. Масштаб по вертикальной оси: для канала 1 – 500 мВ, для канала 2 – 100 мВ; по горизонтальной оси – 50 мкс.
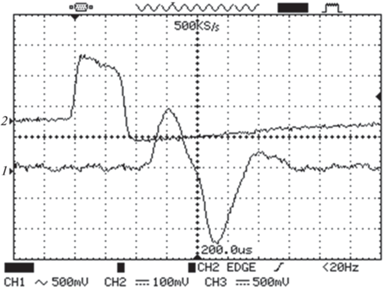
На рис. 5 сигнал канала 1 соответствует сигналу нового ЗЧУ [6], а сигнал канала 2 – сигналу ЗЧУ, описанному в работе [4]. Согласно рис. 5, новый усилитель обладает большей чувствительностью. Коэффициент усиления старого усилителя равен 1000, тогда как нового ЗЧУ – порядка 5000, однако присутствует ярко выраженное дифференцирование сигнала: положительный импульс сигнала соответствует движению частицы в первой половине цилиндра Фарадея, отрицательный импульс – движению частицы во второй его половине. Но так как собственная емкость разрабатываемого индукционного датчика будет гораздо меньше емкости цилиндров Фарадея измерительной линейки ускорителя частиц (порядка 5.8 пФ вместо 45 пФ), то в конечном итоге такого явного дифференцирования сигнала наблюдаться не будет. Таким образом, для функционирования разрабатываемого датчика необходимо лишь равенство коэффициентов усиления всех трех входящих в его состав усилителей, что достигается путем подбора резисторов R3 на этапе сборки.
ПРИНЦИП РАБОТЫ ДАТЧИКА
Принцип работы устройства следующий. В ускорителе заряженные микрочастицы ускоряются под действием электрического поля до скоростей порядка 1–12 км/с. Зарядка частиц происходит в инжекторе и носит случайный характер. Как показали эксперименты [7], заряд используемых в экспериментах частиц алюминиевой пудры марки ПАП-1 с размером от 1 до 10 мкм варьируется от 10–12 до 10–15 Кл. На процесс зарядки частиц влияет множество параметров, однако в первом приближении заряд частицы можно определить по формуле:
где r – средний радиус частицы, R – радиус острия иглы инжектора, U – напряжение на игле инжектора.Максимально возможный заряд частицы ограничивает эффект автоионной эмиссии. Для идеальной сферической частицы заряд соответствует поверхностной плотности электрического поля 1010 В/м. Так как частицы не имеют идеальную сферическую форму, то для частиц одинаковой массы заряд будет зависеть от того, насколько форма частицы близка к сферической. Как показано в [7], в применяемом нами инжекторе частицы пудры ПАП-1 заряжаются до 20%-ного уровня от максимально возможного заряда. Зарядка частиц необходима для дальнейшего их ускорения в электрическом поле ускорителя и также используется для регистрации частиц в датчиках, расположенных в тракте ускорителя.
При пролете заряженной микрочастицы через датчик на измерительные электроды наводится потенциал, зависящий, в соответствии с теоремой Рамо–Шокли [8, 9], от заряда, скорости микрочастицы и расстояния от микрочастицы до измерительного электрода:
где Ek – эффективная (взвешенная) напряженность поля в точке, где находится заряд Q в момент времени t, рассчитанная по схеме: заряд удален, потенциал проводника, с которого снимается ток, равен 1 В, потенциал оставшихся проводников равен 0; VEk – скалярное произведение вектора скорости и эффективной напряженности.Если траектория движения микрочастицы отклонена от оси симметрии датчика, то на каждый из измерительных электродов наводится разный электрический потенциал, зависящий от близости микрочастицы к конкретному измерительному электроду. После обработки полученных данных можно судить об отклонении микрочастицы от оси ускорителя.
Если учитывать параметры внешней измерительной цепи, которая подключена через разделительный конденсатор большой емкости к нечетным электродам для отсекания постоянной составляющей напряжения, то получим формулу, связывающую напряжение на нагрузке Uн(t) с наведенным током iind(t) [8, 9]:
(2)
$\frac{d}{{dt}}{{U}_{{\text{н}}}}(t) + \frac{1}{{{{R}_{{\text{н}}}}C}}{{U}_{{\text{н}}}}(t) = {{i}_{{ind}}}(t)\frac{1}{C},$Считаем, что Rн бесконечно велико, тогда выражение (2) можно упростить:
или переписать в виде: где φ*(t) – эффективный потенциал поля в точке, где находится заряд Q в момент времени t.Таким образом, зная φ*(t) в определенный момент времени t и зная Uн(t), можно рассчитать заряд частицы Q.
Тогда получим
где $\varphi _{{ind}}^{*}(t)$ – потенциал, наведенный на электродах при условии, что емкость C = 1.На рис. 6 представлена конструкция датчика (вид с торца).
Рис. 6.
Геометрия датчика. 1–3 – измерительные электроды; 4 – земляные электроды; М – некоторая точка внутри; φ1, φ2, φ3 – углы между радиус-вектором точки М и осями, перпендикулярно которым расположены измерительные электроды.
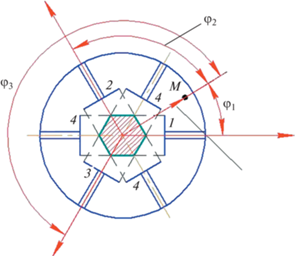
Микрочастица, подлетая к датчику, наводит электрический потенциал на три измерительных электрода, представляющие собой прямоугольные металлические пластины, нормали к которым расположены под углом 120° друг к другу. Максимальное значение потенциала на измерительном электроде будет достигнуто, когда частица находится в середине измерительного электрода относительно оси OZ. Введем следующие допущения: конструкция представляет собой шесть конденсаторных датчиков, расположенных под углом 120° друг относительно друга, и они не оказывают влияния друг на друга в процессе измерений. Это допустимо с погрешностями в пределах заштрихованной области (см. рис. 5).
Тогда напряжение, которое измеряется с каждого измерительного электрода, определяется следующим образом:
– для измерительного электрода 1
(6)
${{U}_{1}} = ({{K}_{1}}{\text{/}}{{C}_{1}})Q\left( {\frac{{d{\text{/}}2 + \rho \cos {{\varphi }_{1}}}}{d}} \right),$– для измерительного электрода 2
(7)
${{U}_{2}} = ({{K}_{2}}{\text{/}}{{C}_{2}})Q\left( {\frac{{d{\text{/}}2 + \rho \cos {{\varphi }_{2}}}}{d}} \right),$– для измерительного электрода 3
(8)
${{U}_{3}} = ({{K}_{3}}{\text{/}}{{C}_{3}})Q\left( {\frac{{d{\text{/}}2 + \rho \cos {{\varphi }_{3}}}}{d}} \right),$Согласно рис. 5 и приведенным выше выражениям получим:
(9)
${{\varphi }_{1}} = {\text{arctg}}\left( {\sqrt 3 \frac{{{{U}_{3}}({{C}_{3}}{\text{/}}{{K}_{3}}){\text{/}}({{U}_{1}}({{C}_{1}}{\text{/}}{{K}_{1}})) - {{U}_{2}}({{C}_{2}}{\text{/}}{{K}_{2}}){\text{/}}({{U}_{1}}({{C}_{1}}{\text{/}}{{K}_{1}}))}}{{{{U}_{3}}({{C}_{3}}{\text{/}}{{K}_{3}}){\text{/}}({{U}_{1}}({{C}_{1}}{\text{/}}{{K}_{1}})) + {{U}_{2}}({{C}_{2}}{\text{/}}{{K}_{2}}){\text{/}}({{U}_{1}}({{C}_{1}}{\text{/}}{{K}_{1}})) - 2}}} \right),$(10)
$\rho = \frac{{({{U}_{2}}({{C}_{2}}{\text{/}}{{K}_{2}}){\text{/}}({{U}_{1}}({{C}_{1}}{\text{/}}{{K}_{1}})) - 1)d}}{{2(\cos (120^\circ - {{\varphi }_{1}}) - ({{U}_{2}}({{C}_{2}}{\text{/}}{{K}_{2}}){\text{/}}({{U}_{1}}({{C}_{1}}{\text{/}}{{K}_{1}})))\cos {{\varphi }_{1}})}}.$В случае использования симметричных каналов для каждого измерительного электрода упростим получившиеся выражения:
(11)
${{\varphi }_{1}} = {\text{arctg}}\left( {\sqrt 3 \frac{{{{U}_{3}}{\text{/}}{{U}_{1}} - {{U}_{2}}{\text{/}}{{U}_{1}}}}{{{{U}_{3}}{\text{/}}{{U}_{1}} + {{U}_{2}}{\text{/}}{{U}_{1}} - 2}}} \right),$(12)
$\rho = \frac{{({{U}_{2}}{\text{/}}{{U}_{1}} - 1)d}}{{2(\cos (120^\circ - {{\varphi }_{1}}) - ({{U}_{2}}{\text{/}}{{U}_{1}})\cos {{\varphi }_{1}})}}.$Так как для определения координат частиц в формулах (11) и (12) напряжения, измеренные с каждого измерительного электрода (U1, U2, U3), входят как соотношения, то для описываемого в статье датчика не имеет значения величина заряда регистрируемой частицы. От заряда будут зависеть лишь сами напряжения U1, U2 и U3, а их соотношения будут зависеть только от координаты пролета частицы через датчик.
НАСТРОЙКА ДАТЧИКА
Для проверки симметричности конструкции устройства и одинаковости коэффициентов усиления зарядочувствительных усилителей вдоль оси устройства был помещен провод, подключенный к генератору импульсов. Осциллограммы с усилителей измерительных электродов представлены на рис. 7. Они подтверждают работоспособность устройства тем, что амплитуда сигналов с измерительных электродов зависит от отклонения провода от оси устройства. На 4-й канал (самый нижний график на рис. 7) осциллографа выведен синхроимпульс генератора.
Рис. 7.
Осциллограммы с зарядочувствительных усилителей при тарировке: а – провод расположен по оси датчика, б – провод смещен от оси датчика. 1, 2, 3 – каналы датчика; 4 – импульс с синхрогенератора.
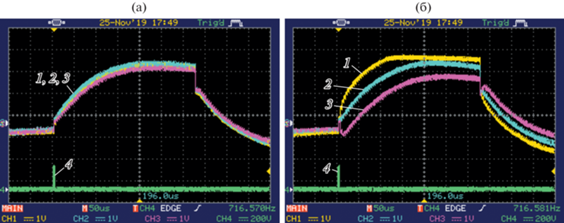
Согласно рис. 7, путем подбора номиналов резисторов удалось обеспечить одинаковые коэффициенты усиления ЗЧУ для всех трех каналов индукционного датчика. Также видна явная зависимость амплитуд сигналов от расположения провода, имитирующего трек пролета частицы внутри датчика.
РЕЗУЛЬТАТЫ ЭКСПЕРИМЕНТОВ
Для измерения распределения плотности частиц по сечению тракта ускорителя индукционный датчик был помещен в вакуумную камеру ускорителя микрочастиц [10]. Схема постановки эксперимента приведена на рис. 8.
Рис. 8.
Схема эксперимента. 1 – вакуумная задвижка (фотография приведена на рис. 1); 2 – вакуумный тройник, обеспечивающий соединение вакуумного тракта с системой насосов; 3 – измерительная линейка (подробное описание дано в [5]); 4 – камера для экспериментов; 5 – описываемый в данной работе индукционный датчик; 6 – гермопереход РСГСП19; 7 – 4-канальный осциллограф RIGOLDS1154Z; 8 – коаксиальный кабель РК50; 9 – штатный ЗЧУ [4]; 10 – батареи питания 3R12.
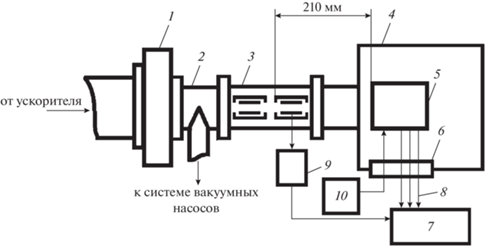
Характерные осциллограммы сигналов, фиксируемые в ходе эксперимента, приведены на рис. 9.
Рис. 9.
Осциллограммы сигналов. 1 – сигнал со штатного ЗЧУ, подключенного к измерительной линейке ускорителя; 2, 3, 4 – сигналы с усилителей описываемого в данной статье датчика.
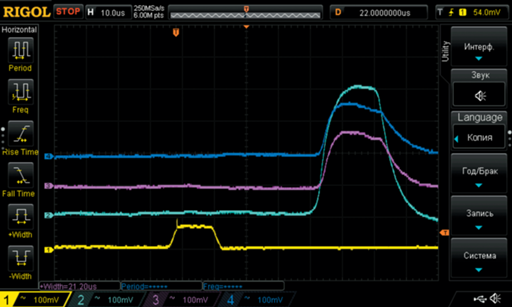
В ходе эксперимента были измерены амплитуды сигналов для 1886 частиц. По измеренным амплитудным значениям по формулам (11) и (12) вычислялись координаты ρ и φ пролета частицы через датчик. Полученные координаты ρ и φ были переведены в декартовую систему координат, преимущество которой в данном случае заключалось в том, что площади всех участков сечения тракта одинаковы и удобны для построения зависимости плотности распределения частиц по сечению тракта.
На рис. 10 приведены координаты пролета фиксируемых датчиком частиц.
На рис. 11 приведена зависимость количества частиц, проходящих через участок сечения с заданными координатами.
Полученные в ходе работы данные могут быть использованы для создания конструкции устройства для определения места пролета высокоскоростной микрочастицы через сечения тракта ускорителя микрочастиц, а также при разработке измерителя вектора скорости микрочастицы, что позволит в дальнейшем улучшить фокусировку ускорителя заряженных микрочастиц и тем самым повысить КПД работы ускорителя. Результаты исследования позволяют расширить функциональные возможности наземной аппаратуры для имитации факторов космического пространства в лабораторных условиях.
Список литературы
Семкин Н.Д., Пияков А.В. // ПТЭ. 2015. № 5. С. 128. https://doi.org/10.7868/S0032816215040126
Пияков А.В. // Вестник Самарского государственного аэрокосмического университета им. академика С.П. Королева (национального исследовательского университета). 2011. № 7. С. 133.
Otto K.A., Srama R., Auer S., Bugiel S., Grün E., Kempf S., Xie J. // Nucl. Instrum. and Methods in Physics Research A. 2013. V. 729. P. 841. https://doi.org/10.1016/j.nima.2013.07.065
Днищенко В.А. // Схемотехника. 2003. № 6. С. 26.
Телегин А.М., Пияков А.В. // ПТЭ. 2017. № 6. С. 101. https://doi.org/10.7868/S0032816217060131
Thomas E., Simolka J., DeLuca M., Horányi M., Janches D., Marshall R.A., Munsat T., Plane J.M.C., Sternovsky Z. // Rev. Sci. Instrum. 2017. V. 88. P. 034501. https://doi.org/10.1063/1.4977832
Семкин Н.Д., Пияков А.В., Воронов К.Е., Шепелев С.М., Богоявленский Н.Л. // ПТЭ. 2006. № 3. С. 154.
Герштейн Г.М. Моделирование полей методом электростатической индукции. М.: Наука, 1970.
Иновенков А.Н., Константинов О.В., Пирогов В.И. // ЖТФ. 1993. Т. 63. Вып. 9. С. 1.
Семкин Н.Д., Пияков А.В. // Сб. материалов конференции “Актуальные проблемы ракетно-космической техники и ее роль в устойчивом социально-экономическом развитии общества”. Самара: ФГУП ГНПРКЦ “ЦСКБ–Прогресс”, 28 сентября–3 октября 2009. С. 151.
Дополнительные материалы отсутствуют.
Инструменты
Приборы и техника эксперимента