Расплавы, 2021, № 5, стр. 492-501
Изучение карботермического процесса восстановления элементов системы Cr2O3–FeO–CaO–SiO2–MgO–Al2O3 методом термодинамического моделирования
В. А. Салина a, b, *, В. И. Жучков a
a Институт металлургии Уральского отделения РАН
Екатеринбург, Россия
b Уральский государственный горный университет
Екатеринбург, Россия
* E-mail: valentina_salina@mail.ru
Поступила в редакцию 21.04.2021
После доработки 19.05.2021
Принята к публикации 08.06.2021
Аннотация
Для изучения возможности процесса восстановления элементов многокомпонентной системы Cr2O3–FeO–CaO–SiO2–MgO–Al2O3 проведено термодинамическое моделирование в жидком состоянии. Параметры исходного состояния системы: интервал температур (t) 1500–1800°С с шагом 100°С, общее давление системы 0.1 МПа и количество азота 2.24 м3. Цель работы – изучение влияния количества пыли газоочистки, добавленной к руде, на процесс восстановления элементов при выплавке феррохрома. Состав оксидной системы соответствовал хромовой руде (38% Cr2O3; 11.1% FeO; 0.17% CaO; 15% SiO2; 29.7% MgO; 6% Al2O3) и пыли газоочисток (15.5% Cr2O3; 7.5% FeO; 0.8% CaO; 67.3% SiO2; 7.2% MgO; 1.7% Al2O3) при получении феррохрома среднеуглеродистого. Количество пыли в смеси составило 0; 5; 10; 20%. В качестве восстановителя использовали углерод. Расход восстановителя увеличен на 10% от стехиометрии на восстановление Fe и Cr и на 8% от массы металла для образования карбидов железа, хрома, кремния. Моделирование проведено с применением ПК HSC Chemistry 6.12 (Outokumpu, Финляндия). В базу данных введены термодинамические данные соединения CrO(II), уточнены существующие в базе данных термохимические характеристики соединений: CaCr2O4, SiC, Cr3C2, Cr7C3, Cr23C6, Fe3C. Установлено, что повышение температуры расплава c 1500 до 1700°С увеличивает степень восстановления хрома (ηCr) с 90.2 до 94.8% при различном содержании пыли в системе. Повышение количества пыли в смеси с 0 до 20% снизило ηCr. При этом наибольшее значение ηCr характерно для системы без пыли и равно 94.8% при (СаО + MgO)/(SiO2) = 2.0 и t = 1700°С. Определены химические составы металлического и шлакового расплавов. Содержание [Сr] составило 64–65.6% при температуре расплава 1700°С. Результаты моделирования могут быть использованы при анализе восстановительных процессов хромсодержащих систем и технологии получения сплавов.
ВВЕДЕНИЕ
Металлургическое производство характеризуется образованием больших объемов техногенных отходов как побочных продуктов технологического процесса. Наибольшая часть отходов представлена шлаками, пылью циклонов и газоочистных сооружений, шламами, а также ферросплавным газом. Более 80% всех отходов производства являются конкурентоспособными с используемым сырьем и содержат такие элементы, как железо, марганец, хром, кальций, магний, которые могут быть вовлечены в металлургический передел в качестве шихтовых материалов [1–3].
В шлаковых отвалах России накоплено более 300 млн тонн шлаков металлургического производства, которые должны подлежать переработке по существующим технологиям [4–6]. Примерно 94% всего объема ферросплавов производится в рудовосстановительных электропечах непрерывным углетермическим процессом, в результате которого образуется значительное количество отходов. При объеме выплавки ~2 млн тонн всех видов ферросплавов образуется ~1 млн тонн шлаков и ~130 тыс тонн пылей и шламов [7, 8].
Шлаки производства высокоуглеродистого феррохрома высокопрочные и применяются в виде щебня в дорожном строительстве, а шлаки низко- и среднеуглеродистого феррохрома при остывании рассыпаются в порошок фракции <0.1 мм из-за образования двухкальциевого силиката (2СаО⋅SiO2). После магнитной сепарации они складируются на отвалах либо используются в виде различных добавок [9, 10].
В литературе приведены данные о продуктах карботермического процесса восстановления хрома [11–13], кинетической модели процесса [14], технологиях получения окатышей [15], высокоуглеродистого феррохрома [16] и проволок [17] с применением хромовых отходов (шлак, пыль газоочисток).
Авторами работы [11] изучен процесс восстановления элементов системы Fe–Cr–O углеродом и термодинамически определены возможные продукты. Установлено, что больше раствора Fe–Cr–C и меньше остаточного содержания углерода получается при высоких температурах и низких соотношениях nC : nO (исходное молярное отношение С к O в образце). На начальной стадии процесса восстановления образуются карбиды металлов, а раствор Fe–Cr–C, когда степень восстановления достаточно высокая.
Проведен термодинамический анализ реакций восстановления Cr2O3 (наполнитель порошковой проволоки) углеродом в стандартном состоянии и в условиях, отличных от стандартных, авторами работы [12]. Определено, что при протекании восстановительных реакций образуются карбиды хрома. Термодинамически вероятным является процесс образования хрома как компонента наплавочной ванны при температуре 2227°С. Оксид хрома Cr2O3 имеет наивысшую реакционную способность в жидком состоянии. Наиболее вероятно участие углерода в восстановительном процессе при прямом восстановлении.
Авторами работы [13] проведено исследование термодинамики взаимодействия компонентов пыли газоочистки электросталеплавильной печи с твердым углеродом с применением программного комплекса Terra. Определены металлы, которые восстанавливаться до температуры 1200°С: Fe, Zn, Pb, Na, K, Cu, Cd. Процесс взаимодействия железа с углеродом начинается при температурах выше 650°С с образованием цементита, а в твердой фазе в виде металла остается при более высоких температурах.
В работе [14] разработана и представлена кинетическая модель карботермического процесса восстановления оксида хрома из шлака при получении нержавеющей стали. Химический состав шлака, %: 38.1 СаО; 23.9 SiO2; 13.2 Al2O3; 17.2 MgO; 1.2 FeO; 2 MnO; 4.1 Cr2O3. Определены минимальные значения температур для получения конечной концентрации оксида хрома в шлаке 1.2; 1; 0.8%. Модель позволяет определять наиболее важные параметры процесса, время обработки и температуру, которые имеют большое значение при карботермическом процессе восстановления для снижения концентрации оксида хрома в шлаке.
В работе [15] представлена технология и приведены результаты получения комплексных хромовых окатышей с заданными физико-химическими свойствами для выплавки хромовых ферросплавов в электродуговых печах. Мелкодисперсный хромовый концентрат Донского ГОКа (≥50% Cr2O3), железистую (~10% Fe и 60% SiO2) и/или высокожелезистую (~25% Fe и 25% SiO2) диатомитовую руду Муголжарской группы месторождений, шлаки рафинированного феррохрома и кокс АО “Сары-Арка” с последующим окатыванием и спеканием использовали в составе шихты. Уменьшение температуры обжига окатышей с 1350 до 1200°С для получения неметаллизированных окатышей возможно при содержании 3% кокса в составе шихты без существенного изменения аппаратурно-технологического оформления процесса обжига. Химический состав полученных окатышей, %: 44 Cr2O3; 6.08 Al2O3; 18.65 SiO2; 12.48 FeO; 1.57 CaO; 9.95 MgO; 7.27 остальное. Средняя прочность при температуре обжига окатышей, Н/окатыш: 1050°С – 2893; 1100°С – 3971.7; 1150°С – 4511.1; 1200°С – 5325.
Разработана технология получения высокоуглеродистого феррохрома с использованием до 30–70% антрацита (Р d – 0.016%, Sd – 0.15%) в навеске шихтовых материалов в качестве частичной замены традиционного кокса авторами работы [16]. В качестве шихтовых материалов использовали: хромовую руду, металлоконцентрат, шлак ферросилиция, хромовые отходы, отсевы кварцита, хромовые брикеты. При использовании в качестве восстановителя кокса и антрацита (30–50% на колошу) коэффициент извлечения хрома составил 84.4% и 84.7% при применении кокса и угля.
Изготовление порошковых проволок на основе пыли газоочистки производства феррохрома рассмотрено в работе [17]. Порошки кремния, алюминия и пыли газоочистки алюминиевого производства используются как восстановители в количестве не менее 27%. Определено, что усвоение хрома в наплавленном слое полностью зависит от коэффициента заполнения порошковой проволоки.
В работах [18, 19] приведены результаты термодинамического моделирования процесса восстановления хрома с применением в составе системы шлака феррохрома низкоуглеродистого. Определено изменение степени восстановления хрома от температуры и количества шлака, а также химические составы и содержание продуктов процесса восстановления.
Авторами [20] приведены данные об извлечении хрома из шлака высокоуглеродистого феррохрома методом магнитной сепарации, измерении вязкости шлака системы СаО–SiO2–CrO [21] и применении феррохромного шлака в черной металлургии при получении огнеупорных материалов, керамики и в строительстве [22].
Представленный литературный обзор показал область применения отходов производства при получении металлопродукции (окатыши, феррохром, проволока). Однако физико-химические процессы восстановления в многокомпонентной неорганической оксидной системе Cr2O3–FeO–CaO–SiO2–MgO–Al2O3 методом термодинамического моделирования изучены недостаточно. Не обнаружено данных о применении в составе шихты пыли газоочисток при выплавке феррохрома среднеуглеродистого (ФХСУ). В связи с этим в статье рассмотрен процесс восстановления элементов из оксидов углеродом с применением в качестве исходных материалов хромовой руды и пыли газоочисток ФХСУ. Использование отходов ферросплавного производства, в частности хромсодержащей пыли газоочисток, имеет важное значение для экологии производства.
ТЕРМОДИНАМИЧЕСКОЕ МОДЕЛИРОВАНИЕ
Целью настоящей работы является изучение карботермического процесса восстановления элементов многокомпонентной системы Cr2O3–FeO–CaO–SiO2–MgO–Al2O3 в жидком состоянии (1500–1800°С) методом термодинамического моделирования.
Термодинамическое моделирование процесса восстановления элементов системы Cr2O3–FeO–CaO–SiO2–MgO–Al2O3 с применением в качестве восстановителя углерода проведено по следующим вариантам:
1) изучение влияния температуры процесса (t) в интервале 1500–1800°С на степень восстановления хрома (ηCr) в металлический расплав из состава хромовой руды и 0; 5; 10; 20% пыли газоочисток ФХСУ (рис. 1);
Рис. 1.
Изменение степени восстановления хрома (ηCr) в металлическом расплаве от температуры (t) при содержании 0; 5; 10; 20% пыли газоочисток.
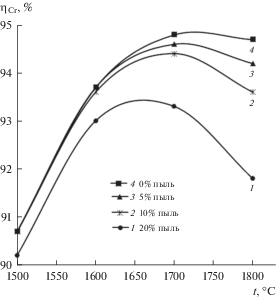
2) определение влияния количества пыли на степень восстановления хрома при температуре 1700°C (рис. 2);
3) изучение влияния количества пыли в смеси на состав металлического (рис. 3а) и оксидного расплавов (рис. 3б) при температуре 1700°С.
Рис. 3.
Изменение содержания элементов в металлическом (а) и оксидном расплавах (б) от количества пыли в смеси при температуре 1700°С.
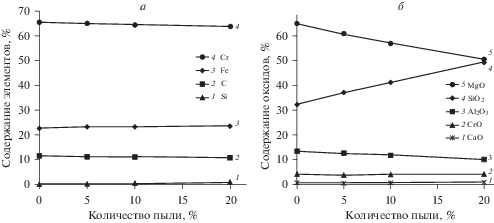
Химический состав пыли ФХСУ, %: 15.5 Cr2O3; 7.5 FeO; 0.8 CaO; 67.3 SiO2; 7.2 MgO; 1.7 Al2O3. В табл. 1 приведены химические составы смесей при различных соотношениях компонентов системы.
Таблица 1.
Химические составы компонентов системы, %
Соотношение руда : пыль |
Cr2O3 | FeO | СаО | SiO2 | MgO | Al2O3 | (СаО + MgO)/ (SiO2) |
MgO/Al2O3 |
---|---|---|---|---|---|---|---|---|
100 : 0 | 38 | 11 | 0.2 | 15 | 29.8 | 6 | 2.0 | 5.0 |
95 : 5 | 36.8 | 10.9 | 0.23 | 17.7 | 28.57 | 5.8 | 1.6 | 4.9 |
90 : 10 | 35.8 | 10.8 | 0.26 | 20.2 | 27.34 | 5.6 | 1.4 | 4.9 |
80 : 20 | 33.5 | 10.3 | 0.32 | 25.48 | 25.3 | 5.1 | 1.0 | 5.0 |
В качестве восстановителя использовали углерод, расход которого увеличен на 10% от стехиометрически необходимого на полное восстановление железа и хрома и на 8% от массы металла для образования карбидов железа, хрома и кремния.
Для проведения термодинамического моделирования использовали программный комплекс HSC Chemistry 6.12, разработанный Outokumpu, и основанный на минимизации энергии Гиббса и вариационных принципах термодинамики [23]. Равновесный состав многокомпонентной системы Cr2O3–FeO–CaO–SiO2–MgO–Al2O3 определен с применением подпрограммы “Equilibrium Compositions”. Исходные параметры для проведения термодинамического моделирования: интервал температур 1500–1800°С с шагом 100°С, общее давление 0.1 МПа, количество азота (N2) в системе 2.24 м3. В базу данных ПК HSC Chemistry 6.12 введены термодинамические характеристики оксида хрома CrO(II), cкорректированы существующие в базе данных термодинамические константы соединений: CaCr2O4, Fe3C, Cr3C2, Cr7C3, Cr23C6, SiC [24].
РЕЗУЛЬТАТЫ МОДЕЛИРОВАНИЯ И ОБСУЖДЕНИЕ
В жидком состоянии системы развиваются реакции взаимодействия оксида хрома с углеродом, реакционная способность которого увеличивается с повышением температуры. Основным восстановителем Cr2O3 является твердый углерод. Хром с углеродом образует прочные карбиды, которые являются носителями углерода: Cr3C2 (∆G°(298.15) = = ‒81.169 ± 6.276 кДж/моль), Cr7C3 (∆G °(298.15) = –163.176 ± 8.368 кДж/моль) и Cr23C6 (∆G °(298.15) = –347.272 ± 8.368 кДж/моль) [24]. Термодинамические характеристики (∆rG °(T)) реакций восстановления оксидов хрома углеродом приведены в табл. 2 [25, 26].
Таблица 2.
Уравнения ∆rG°(T) реакций восстановления оксидов хрома углеродом
Реакция | ∆rG°(Т) = ∆Н°(Т) – – Т · ∆S°(Т), кДж/моль | Температура, при которой ∆rG°(T) = 0, °С |
---|---|---|
Cr2O3 + 13/3C = 2/3Cr3C2 + 3CO | 730 940 – 511.68 · Т | 1157 |
2/3Cr2O3 + 18/7C = 4/21Cr7C3 + 2CO | 511 128 – 364.57 · Т | 1130 |
Cr2O3 + 81/23C = 2/23Cr23C6 + 3CO | 749 452 – 526.47 · Т | 1151 |
2/3Cr2O3 + 2C = 4/3Cr + 2CO | 546 624 – 360.8 · Т | 1240 |
3(FeO·Cr2O3) + 3C = 3Fe + 3Cr2O3 + 3CO | 491 490 – 415.3 · Т | 912 |
MgO·Cr2O3 + 3C = 2Cr + MgO + 3CO | 720 350 – 520.8 · Т | 1273 |
Из приведенных данных в табл. 2 следует, что температуры равновесия реакций образования карбидов (Cr3C2, Cr7C3, Cr23C6) в расплаве не существенно отличаются, что объясняется близким значением термодинамической прочности (энергией Гиббса) всех трех карбидов. Происходит науглероживание жидкофазного металлического расплава вследствие образования карбидов железа, хрома и получение высокоуглеродистого феррохрома [27].
Содержание оксидов железа в расплаве облегчает процесс восстановления хрома из-за снижения температуры плавления сплава [24–26, 28] и уже при 1100°С наблюдается его восстановление из расплава Cr2O3–C–Fe, тогда как без железа хром при указанной температуре не восстанавливается [28]. Присутствие железа в расплаве улучшает условия восстановления кремния [25].
Результаты термодинамического моделирования процесса восстановления элементов многокомпонентной системы Cr2O3–FeO–CaO–SiO2–MgO–Al2O3 с применением в качестве восстановителя углерода представлены в виде графических зависимостей (рис. 1–3). На рис. 1 показана температурная зависимость степени восстановления хрома при содержании в системе 0; 5; 10; 20% пыли.
На рис. 1 показано, что повышение температуры расплава с 1500 до 1700°С увеличивает степень восстановления хрома. Это объяснимо тем, что химические реакции карботермического процесса восстановления хрома (табл. 2) эндотермические, т.е. протекают с поглощением теплоты термодинамической системой при постоянном давлении, смещая ее равновесное состояние в сторону образования продуктов реакций. При этом степень восстановления хрома увеличилась на 4% для шихты без пыли (0%), на 3.9; 3.7 и 3.1% для систем с 5; 10 и 20% пыли соответственно. Уменьшение степени восстановления хрома в интервале температур 1700–1800°С, в основном, для систем с 5; 10 и 20% пыли объясняется снижением основности шлака (СаО + MgO)/ (SiO2) с 1.6 до 1.0 (табл. 1). Повышение содержания кремнезема снизило активности компонентов СаО и Cr2O3 в оксидном расплаве, образуя прочные силикаты кальция (Са2SiO4, CaSiO3).
Увеличение в термодинамической системе содержания пыли с 0 до 20% снижает степень восстановления хрома с 94.8 до 93.3% (рис. 2). Это связано со снижением суммарного содержания Cr2O3 в системе (до 33.5% Cr2O3 при 20% пыли, см. табл. 1). При содержании 5% пыли в системе степень восстановления хрома практически не изменилась. Самая высокая ηCr, равная 94.8%, получена для расплава с 0% оксидной составляющей (пыли) при основности шлака 2.0 и температуре 1700°С. Увеличение содержания кремнезема с 15 до 25.5% в системе, как флюсующего компонента, не оказало влияния на повышение степени восстановления хрома в расплав.
На рис. 3 показано изменение содержания элементов в металлическом и оксидном расплавах при температуре 1700°С. Повышение количества пыли до 20% снижает содержание хрома в расплаве с 65.6 до 64% (рис. 3а), что связано с уменьшением Cr2O3 в суммарной смеси и степени восстановления хрома с 94.8 до 93.3% (рис. 2). Содержание железа в металле увеличивается незначительно с 22.7 до 23.9% при степени восстановления 99.9%. Согласно термодинамической прочности оксидов восстановление хрома протекает после железа и соответствует данным, полученным авторами работ [25, 26, 28]. Количество углерода в металле уменьшается незначительно и составляет 11.5–11.1%. Содержание кремния в металле также мало изменяется (0.26–0.99%).
Химический состава шлака, образованного в процессе восстановления, в основном представлен такими фазовыми составляющими, как MgO, SiO2, Al2O3, CrO и СаО (рис. 3б). С повышением количества пыли в системе увеличивается содержание SiO2 в 1.5 раза (с 28.1 до 43.1%) и незначительно СаО и CrO, а количество MgO и Al2O3 уменьшается. Изменение состава оксидной системы связано с вносимыми пылью компонентами.
Таким образом, проведенные расчеты показали, что при получении углеродистого феррохрома в рудной части шихты можно использовать пыль газоочисток после окускования.
ЗАКЛЮЧЕНИЕ
Результаты термодинамического моделирования процесса восстановления элементов многокомпонентной системы Cr2O3–FeO–CaO–SiO2–MgO–Al2O3 углеродом при изменении ее состава из-за ввода оксидных составляющих (пыли газоочисток феррохрома среднеуглеродистого) в количестве 0; 5; 10 и 20% в состав системы показали, что повышение температуры процесса расплава с 1500 до 1700°С увеличивает степень восстановления хрома. Уменьшение основности шлака (СаО + MgO)/(SiO2) с 2.0 до 1.0 снижает ηCr в металлический расплав. Повышение количества пыли с 0 до 20% снижает степень восстановления хрома и его содержание с 65.6 до 64% в сплаве. Определено, что наибольшее значение степени восстановления хрома, равное 94.8%, получено для системы с 0% пыли при (СаО + MgO)/(SiO2) = 2.0 и температуре 1700°С. Процесс восстановления железа и хрома протекает через образование карбидов Fe3C, Cr3C2, Cr7C3. Расчетным путем определены химический состав металлического и оксидного расплавов жидкофазного процесса восстановления. Пыль газоочисток приведенного состава в количестве до 20% может использоваться в рудной части шихты при выплавке углеродистого феррохрома без заметного изменения показателей процесса плавки. При разработке технологии получения хромовых ферросплавов с вовлечением в металлургический передел отходов производства могут быть использованы полученные результаты термодинамического моделирования для жидкого состояния системы.
Работа выполнена при поддержке гранта РФФИ № 18-29-24 027.
Список литературы
Nikitin L.D., Dyachok N.G., Vashchenko A.V., Shentsov A.I., Kutran’ V.I. // Steel in Translation. 2019. 49. № 7. P. 472–477. https://doi.org/10.3103/S0967091219070064
Темников В.В., Калимулина Е.Г., Тлеугабулов Б.С. Анализ образования и переработки металлургических отходов в АО “ЕВРАЗ НТМК” // Черные металлы. 2018. № 7. С. 32–37.
Буторина И.В., Буторина М.В. Обзор технологий утилизации отходов горно-металлургической отрасли // Черные металлы. 2018. № 12. С. 44–49.
Демин Б.Л., Сорокин Ю.В., Смирнов Л.А., Щерабаков Е.Н. Стабилизация распадающихся ферросплавных и сталеплавильных шлаков // Тр. науч.-практ. конф. “Перспективы развития металлургии и машиностроения с использованием завершенных фундаментальных исследований и НИОКР: Ферросплавы”. Екатеринбург. 2018. С. 342–345.
Демин Б.Л., Сорокин Ю.В., Смирнов Л.А., Щерабаков Е.Н. Существующие способы переработки и направления использования ферросплавных шлаков // Тр. науч.-практ. конф. “Перспективы развития металлургии и машиностроения с использованием завершенных фундаментальных исследований и НИОКР: Ферросплавы”. Екатеринбург. 2018. С. 346–350.
Государственный доклад “О состоянии и об охране окружающей среды Российской Федерации в 2015 году”. Дата обращения 17.03.2020. http://www.mnr.gov.ru/docs/o_sostoyanii_i_ob_okhrane_okruzhayushchey_sredy_rossiyskoy_federatsii/gosudarstvennyy_doklad_o_sostoyanii_i_ob_okhrane_okruzhayushchey_sredy_rossiyskoy_ federatsii_v_2016_/
Zhdanov A.V., Zhuchkov V.I., Dashevskii V.Ya., Leont’ev L.I. // Metallurgist. 2015. 58. № 11–12. P. 1064–1070. https://doi.org/10.1007/s11015-015-0041-5
Zhuchkov V.I., Zayakin O.V., Sychev A.V. // Russian Metallurgy. 2020. № 6. P. 662–666. https://doi.org/10.1134/S003602952006018X
Кушнерев И.В., Оржех М.Б., Либанов Б.Б., Коротеев С.А., Платонов А.А., Плюхин В.В. Стабилизация шлаков внепечной обработки стали от силикатного распада // Новые огнеупоры. 2018. № 4. С. 44.
Kozlov V.V., Shevchik A.P., Suvorov S.A., Arbozova N.V., Kuznetsov D.V. // Refractories and industrial ceramics. 2019. 59. № 5. P. 502–506. https://doi.org/10.1007/s11148-019-00262-9
Zhang Yang-ling, Liu Y., Wei Wen-jie // International journal of minerals, metallurgy and materials. 2013. 20. № 10. P. 931–940. https://doi.org/10.1007/s12613-013-0817-1
Kryukov R.E., Goryushkin V.F., Bendre Yu.V., Bashchenko L.P., Kozyrev N.A. // Steel in Translation. 2019. 49. P. 843–847. https://doi.org/10.3103/S0967091219120052
Doronin I.E., Svyazhin A.G. // Metallurgist. 2013. 57. № 1–2. P. 41–48. https://doi.org/10.1007/s11015-013-9688-y
Leuchtenmüller M., Antrekowitsch J., Steinlechner S. // Metallurgical and Materials Transactions B. 2019. 50B. № 5. P 2221–2228. https://doi.org/10.1007/s11663-019-01649-2
Bondarenko I.V., Tastanov E.A. // Metallurgist. 2019. 62. № 11–12. P. 1213–1218. https://doi.org/10.1007/s11015-019-00776-0
Kaliakparov A.G., Baltabaev S.R., Strakhov V.M., Mukhtar A.A. // Metallurgist. 2017. 61. № 9–10. P. 765–769. https://doi.org/10.1007/s11015-018-0561-x
Козырев Н.А., Усольцев А.А., Прудников А.Н., Крюков Р.Е., Михно А.Р. Изучение свойств порошковой проволоки на основе пыли газоочистки феррохрома // Черная металлургия. 2019. 75. № 3. С. 365–372. https://doi.org/10.32339/0135-5910-2019-3-365-372
Жучков В.И., Салина В.А., Заякин О.В., Сычев А.В. Изучение влияния температуры и состава оксидной системы на восстановление хрома методом термодинамического моделирования // Тр. V-й науч.-практ. конф. “Перспективы развития металлургии и машиностроения с использованием завершенных фундаментальных исследований и НИОКР”. Екатеринбург: УрО РАН. 2020. С. 212–215.
Салина В.А., Жучков В.И., Сычев А.В. Термодинамическое моделирование карботермического процесса восстановления хрома из оксидной системы Cr2O3–FeO–CaO–SiO2–MgO–Al2O3 // Расплавы. 2020. № 6. С. 608–615.
Bai Z.T., Zhang Z.A., Guo M., Hou X.M., Zhang M. // Material Research Innovations. 2015. № 5. P. 113–118. https://doi.org/10.1179/1432891714z.0000000001065
Wu T., Yuan F., Zhang Ya. // ISIJ International. 2018. 58. № 2. P. 367–369. https://doi.org/10.2355/isijinternational.ISIJINT-2017-558
Sahu N., Biswas A., Gajanan U Kapure // Mineral processing and extractive metallurgy review. 2016. 37. № 4. P. 211–219. https://doi.org/10.1080/08827508.2016.1168415
Roine A. Outokumpu HSC Chemistry for Windows. Chemical reactions and Equilibrium software with extensive thermochemical database. Pori: Outokumpu research OY, 2002.
Глушко В.П. Термические константы веществ. М.: Академия наук СССР. М.: Академия наук СССР, 1979. IX.; 1970. IV. Ч. I.; 1974. VII. Ч. I.; 1972. VI. Ч. I.; 1971. V.
Рысс М.А. Производство ферросплавов. М.: Металлургия. 1985.
Гасик М.И, Лякишев Н.П., Емлин Б.И. Теория и технология производства ферросплавов. М.: Металлургия. 1988.
Гасик М.И, Лякишев Н.П. Металлургия хрома. М.: ЭЛИЗ. 1999.
Ryabchikov I.V., Mizin V.G., Yarovoi K.I. // Steel in Translation. 2013. 43. № 6. P. 379–382. https://doi.org/10.3103/S096709121306017X
Дополнительные материалы отсутствуют.