Расплавы, 2021, № 6, стр. 553-564
Особенности коррозионного поведения алюминий-графеновых и алюминий-графитовых композиционных материалов в 3% водном растворе хлорида натрия
Л. А. Елшина a, *, Р. В. Мурадымов a, Н. Г. Молчанова a
a Институт высокотемпературной электрохимии УрО РАН
Екатеринбург, Россия
* E-mail: yolshina@ihte.uran.ru
Поступила в редакцию 08.06.2021
После доработки 29.06.2021
Принята к публикации 06.07.2021
Аннотация
Исследована коррозионная стойкость алюминий-графеновых и алюминий-графитовых композитных материалов в 3% растворе хлорида натрия при комнатной температуре. Образование равномерно распределенных в объеме алюминиевой матрицы графеновых пленок и кристаллов графита без формирования карбида алюминия подтверждено методом Рамановской спектроскопии. Скорость коррозии обоих композитов выше скорости коррозии исходного алюминия, закономерно увеличиваясь с повышением содержания углерода в них. Класс коррозионной стойкости алюминия – 3 (стойкий), а алюминиевых композитов – 4 (весьма стойкие) в растворе хлорида натрия. Скорости коррозии алюминий-графитового композита примерно в 3 раза выше, чем у алюминий-графенового композита при равном содержании углерода.
ВВЕДЕНИЕ
Металлическим материалам на основе алюминия и его сплавов можно придавать абсолютно новые функциональные характеристики путем введения в них микро- и наноразмерных порошков оксидов, нитридов, карбидов металлов и неметаллов, а также новых углеродных материалов. Такие композиционные материалы отличаются по своим характеристикам от обычных алюминиевых сплавов большей надежностью при критических нагрузках и длительностью сроков эксплуатации. В композитах с металлической матрицей сочетаются достоинства конструкционных металлических материалов с уникальными свойствами углеродного наполнителя (графена, графита, углеродных нанотрубок).
Первые попытки использовать легкие алюминий-графитовые композитные материалы для создания корпусов подводных лодок были предприняты учеными в 1970–1980 гг. в США [1–3]. Волокнистые алюминий-графитовые металлические композитные материалы с улучшенными механическими свойствами рассматривали также для создания компонентов самолетов и вертолетов, а также в тех применениях, где невероятно важны уменьшенный вес и увеличенная прочность. Оказалось, что алюминий-графитовые композиционные материалы в морской воде подвержены гальванической коррозии [4, 5], что затруднило их коммерческое применение. Ухудшение коррозионных свойств композитов по сравнению с алюминием происходит вследствие синергетического коррозионного эффекта вследствие гальванического электрического контакта на границе волокнистый графит-алюминий в композите.
Металлокомпозитный алюминий-углеродный материал, как правило, производят прессованием, точнее “вдавливанием” алюминия в волокнистые углеродные матрицы [4], или пропиткой углеродных волокон жидким металлом [5], причем, для улучшения смачиваемости углеродных волокон и частиц в расплавленной алюминиевой матрице их покрывают тонкими слоями меди, никеля, серебра толщиной 0.4–1 мкм [6], “смешением в расплаве” частиц, усов или коротких волокон углерода (до 50 мас. %) с расплавом алюминия с последующим формованием деталей по стандартной технологии литья [7].
В качестве альтернативных высокоэнергетических методов создания алюминий-углеродных композитных материалов необходимо назвать имплантацию ионов углерода в алюминиевую мишень [8, 9], при которой на глубину порядка 150 нм внедряется углерод с образованием карбида алюминия, а также тщательное перемешивание (ball-milling) наночастиц углерода, а также углеродных нанотрубок с наночастицами алюминия с образованием алюминий-углеродного композита, содержащего до 50% углерода [10, 11], либо сочетание вышеприведенных приемов синтеза [12].
Известен способ синтеза алюминиевых углеродсодержащих композитов, позволяющий добиться однородности полученного композитного материала, не имеющего анизотропии механических свойств вдоль и поперек волокон, обладающего низкой пористостью и хорошей спекаемостью [13]. В последние несколько лет опубликовано значительное количество работ по синтезу и механическим свойствам алюминий-графенового композита [14–17]. В основном, так же как и в случае использования в качестве упрочняющей добавки углеродных нанотрубок, процессы синтеза сводятся к перемолу и последующему отжигу предварительно синтезированного графена или оксида графена с алюминиевым порошком. Упрочняющее влияние графена на алюминиевый композит практически все исследователи связывают с образованием рентгенографически подтвержденной фазы – карбида алюминия. Однако, даже малые добавки карбида алюминия разрушительно действуют на алюминиево-графеновый композит в агрессивных средах и даже в условиях атмосферной коррозии, вызывая неоднородную питтинговую коррозию, исключая, таким образом, практическое использование полученных таким образом алюминий-графеновых композитов.
Очевидно, что традиционными методами синтеза невозможно получить алюминий-углеродные композитные материалы с высоким содержанием и равномерным распределением углерода в виде графита или графена в алюминиевой матрице, при которых в качестве побочного продукта не образовывался бы карбид алюминия, который даже в примесных количествах крайне негативно сказывается на коррозионных свойствах получаемого металлического материала.
Нами был предложен инновационный метод синтеза алюминий-графеновых и алюминий-графитовых металлических материалов, позволяющий синтезировать алюминиевые композитные материалы, обладающий уникальным сочетанием механических свойств – одновременным повышением пластичности и твердости [18, 19]. Однако, для практического применения этих уникальных материалов необходима оценка их коррозионных свойств в одном из стандартных водных электролитов по ГОСТ 9.913-90.
Целью данного исследования является изучение коррозионно-электрохимического поведения алюминий-графенового и алюминий-графитового композитного материала в 3% водном растворе хлорида натрия.
ЭКСПЕРИМЕНТАЛЬНАЯ ЧАСТЬ
Взаимодействие расплавленного алюминия с углеродсодержащим прекурсором проводили в корундовом тигле, на дно которого помещали смесь хлоридов щелочных металлов с навеской углеродсодержащей добавки. В качестве углеродсодержащей добавки использовали порошок карбида бора. Технический алюминий марки АД0 загружали в тигель в виде диска диаметром 5 см, точно соответствующего внутреннему диаметру тигля. Сверху на алюминий засыпали такую же смесь хлоридов щелочных металлов с карбидом бора. Основные эксперименты были выполнены при температурах от 700 до 800°С в атмосфере воздуха над солевым расплавом. Продолжительность выдержки составляла от 1 до 5 ч. После высокотемпературной выдержки расплавленного алюминия в солевом расплаве, содержащем от 0.1 до 2 мас. % карбида бора, соль вместе с жидким корольком алюминия выливали в холодный корундовый тигель. После застывания солевой смеси ее растворяли, алюминиевый королек отмывали от солей. Затем алюминий распиливали примерно пополам, половину от общего количества заливали в токопроводящую смолу и полировали на полировальном станке фирмы “Struers” (Австрия).
Коррозию алюминий-графеновых и алюминий-графитовых металлических материалов с различным содержанием углерода в 3% растворе NaCl с естественной аэрацией определяли гравиметрическим и химико-аналитическими методами в ходе длительных 14 недельных коррозионных испытаний при комнатной температуре. Концентрацию ионов алюминия после коррозионного теста определяли при помощи оптического эмиссионного спектроскопа с индуктивно связанной плазмой iCAP6300Duo (USA).
Поперечный шлиф исходного алюминий-графенового и алюминий-графитового композитов, а также продукты их коррозии в 3% растворе NaCl исследовали при помощи сканирующей электронной микроскопии на микроскопе JEOL 5900LV и TESCAN MIRA 3, Рамановской спектроскопии на Рамановском спектрометре-микроскопе “Renishaw-1000”, а также анализировали на рентгенофазовой установке “RIGAKU” DNAX 2200PC.
РЕЗУЛЬТАТЫ И ОБСУЖДЕНИЕ
Замешивание нано- и микропорошков углерода в расплавленный алюминий нецелесообразно из-за крайне плохой смачиваемости углерода расплавленным алюминием, вследствие чего образующиеся композиты очень пористы, имеют неоднородный состав. Проблема смачиваемости углеродных частиц расплавленным алюминием легко может быть решена путем использования в качестве реакционных сред для синтеза расплавленных галогенидов (хлоридов и фторидов) щелочных и щелочноземельных металлов. Коэффициенты диффузии ионов углерода в расплавленных галогенидах сопоставимы по величине с коэффициентами диффузии в расплавленном алюминии, что позволяет проводить реакции химического взаимодействия углеродсодержащих добавок с расплавленным алюминием при сравнительно низких температурах (973–1073 К) с высоким выходом алюминиевых сплавов и композитов, содержащих углерод.
Синтез частиц углерода внутри алюминиевой матрицы происходит путем одностадийной реакции компонентов, расплавленной галогенидной смеси с расплавленным алюминием, вследствие чего образованные внутри расплавленной алюминиевой матрицы листы графена, так же как и микрокристаллы графита, прекрасно смачиваются алюминием [18, 19]. Суммарная реакция окисления карбид-иона кислородом воздуха внутри расплавленной алюминиевой матрицы под слоем расплавленных галогенидов может быть описана следующим уравнением (1)
(1)
$4{\text{Al}} + {{{\text{B}}}_{{\text{4}}}}{\text{C}} + 6{{{\text{O}}}_{2}} = 2{\text{A}}{{{\text{l}}}_{{\text{2}}}}{{{\text{O}}}_{3}} + {\text{C}} + 2{{{\text{B}}}_{{\text{2}}}}{{{\text{O}}}_{3}}$При взаимодействии расплавленного алюминия с карбидом бора под слоем расплавленных галогенидов в атмосфере воздуха оксид алюминия образуется в виде нанопорошка в объеме расплавленного электролита, а углерод внедряется в алюминий в больших количествах и образуется в виде нано-тонких слоев графена на поверхности расплавленного электролита. Легколетучий хлорид бора, образующийся при взаимодействии оксида бора с хлоридами, возгоняется в ходе взаимодействия и не обнаруживается в продуктах взаимодействия – ни в металле, ни в солевом электролите.
Были синтезированы алюминий-графеновые и алюминий-графитовые металлические композиты с различным содержанием графена и графита в них. Полученные таким образом алюминий-графеновые металлические материалы беспористы, имеют характерный металлический блеск (рис. 1), высокую электропроводность и прекрасно механически обрабатываются, содержание углерода остается постоянным от поверхности алюминиевой капли к ее центру.
Тонкие прозрачные графеновые пленки обнаружены на поверхности металлического королька, а также по всему объему металла. В том же содержании они остаются на срезе шлифа после резки и полировки алюминий-графенового композита, а также после его прокатки (рис. 2).
Рис. 2.
Изображение в обратно отраженных электронах (а) и вторичных электронах (б) поперечного шлифа алюминий-графенового композита.
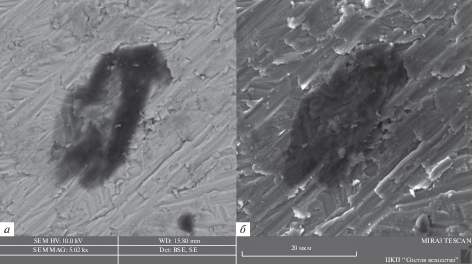
Фазовую чистоту углеродных включений исследовали при помощи спектроскопии комбинационного рассеяния из-за высокой чувствительности метода ко всему ряду структурных состояний углерода – от алмаза до графена, позволяющих идентифицировать углерод в sp2 и sp3 гибридизациях.
Приведенный на рис. 3 Рамановский спектр углеродного включения представляет собой типичный спектр графена. Спектр характеризуется наличием всех основных линий, характерных для графена: линия D – на 1342.64 см–1, G – на 1571.38 см–1, 2D – на 2687.2 см–1. Соотношение интенсивностей пиков I2D/IG равно 0.47, что соответствует трехслойному графену. Низкая интенсивность пика D, обычно приписываемого дефектам графенового слоя, говорит об образовании совершенного, бездефектного графена в алюминиевой матрице [20].
В объеме алюминий-графитового композита содержится большое количество хорошо ограненных кристаллов чистого углерода, которые прекрасно смачиваются жидким алюминием при синтезе и не выкрашиваются при механической обработке. Рамановский спектр этого углеродного включения в точности соответствует графиту пиролитического качества (рис. 4) с единственной экстремально интенсивной линией на 1585 см–1, соответствующей G-связи, и асимметричным узким пиком на 2717 см–1.
Рис. 4.
Электронно-микроскопическое изображение (а) поперечного шлифа алюминий-графитового композита и Рамановский спектр графитового включения в нем (б).
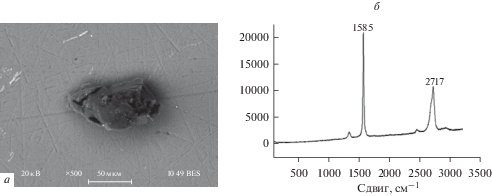
Согласно литературным данным, карбиду алюминия Al4C3 соответствует пик 850 см–1 на спектре комбинационного рассеяния [21]. Этот пик никогда не наблюдался на спектрах как алюминий-графеновых, так и алюминий-графитовых композитных материалов.
Рентгеновский спектр алюминий-графенового композита не содержит пиков углерода, так же, как и пиков карбида алюминия. Кристаллическая решетка алюминий-графенового композита с содержанием графена до 2 мас. % точно соответствует гранецентрированной кубической решетке с симметрией Fm-3m. Причиной отсутствия углеродных пиков на рентгеновском спектре, несмотря на довольно большое содержание углерода, достаточное для его определения, может являться тот факт, что толщины графеновых пленок в композите не более 2 нм, а рентгеновское определение объектов размером менее 20 нм невозможно.
На рентгеновских спектрах алюминий-графитовых композитов фиксируются три углеродных пика, а пики, характерные для карбида алюминия, отсутствуют.
Таким образом, можно заключить, что образованные предложенным методом алюминий-графеновые и алюминий-грфитовые композиты не содержат включений карбида алюминия, что может положительно сказаться на их коррозионных свойствах.
Длительные коррозионные испытания являются простым и надежным методом определения коррозии металлов и сплавов.
Коррозионные испытания проводили в 3% растворе хлорида натрия в течение 16 недель. Известно, что этот раствор является стандартным для определения склонности алюминия и его сплавов к питтингообразованию (локальной коррозии) вследствие образования трихлорида алюминия при взаимодействии алюминия с хлоридным раствором.
Хлорид алюминия (AlCl3) обычно присутствует в растворе внутри питтинга (язвы) и его концентрация увеличивается при развитии коррозии или при снижении влажности окружающего воздуха. Насыщенный раствор хлорида алюминия имеет величину рН около 3.5, поэтому на дне коррозионных язв коррозия продолжается до тех пор, пока туда еще могут мигрировать кислород и корродирующий электролит.
Т.к. питтинги могут достигать значительной глубины и приводить к сквозной коррозии, очевидно, что необходимо знать склонность новых алюминиевых материалов к питтинговой коррозии прежде, чем рекомендовать их промышленное внедрение.
Для проведения коррозионных испытаний из объема металлического композита с разным содержанием графена и графита вырезали по три образца, которые затем полировали на шлифовальных бумагах. Затем поверхности образцов обезжиривали этиловым спиртом и высушивали. Отношение объема электролита к площади образцов было постоянным и составляло 150 мл/cм2.
Образцы алюминий-графенового и алюминий-графитового композитов свободно подвешивали в открытом стакане. Взвешивания проводили 1 раз в неделю: образцы отмывали дистиллированной водой от соли и продуктов коррозии, которые имели плохую адгезию к металлической основе, высушивали, взвешивали, обезжиривали и снова помещали в раствор. В стаканы доливали раствор хлорида натрия, т.к. часть раствора испарялась из открытых стаканов.
Скорость коррозии алюминиевых композитов определяли по формуле:
(2)
$V = \frac{{\Delta m}}{{S \cdot \tau }}\,\,({{\text{г}} \mathord{\left/ {\vphantom {{\text{г}} {{\text{c}}{{{\text{м}}}^{2}} \cdot {\text{ч}}}}} \right. \kern-0em} {{\text{c}}{{{\text{м}}}^{2}} \cdot {\text{ч}}}}),$На рис. 5 представлены кинетические кривые бестокового растворения алюминия, алюминий-графенового и алюминий-графитового композитов с различным содержанием углерода в них. Скорости коррозии алюминия и алюминиевых композитов, определенные гравиметрически по формуле (2), представлены в табл. 1. Скорости коррозии обоих композитов закономерно увеличиваются с повышением концентрации углерода в них. Абсолютные величины скоростей коррозии очень малы, класс коррозионной стойкости алюминия – 3 (стойкий), а алюминиевых композитов – 4 (весьма стойкие).
Рис. 5.
Кинетические кривые изменения масс алюминия, алюминий-графеновых и алюминий-графитовых композитов в 3% растворе NaCl.
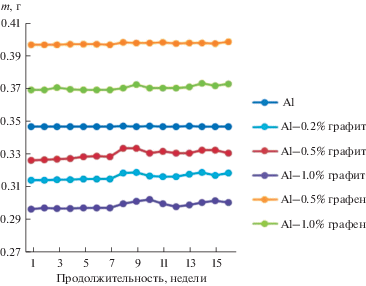
Таблица 1.
Значения скоростей коррозии алюминия, алюминий-графеновых и алюминий-графитовых композитов в 3% растворе NaCl
V ⋅ 107, г/см2 ⋅ ч (гравиметрия) |
V ⋅ 107, г/см2 ⋅ ч (химический анализ) |
|
---|---|---|
Al исходный | 1.71 | 2.31 |
Al–0.05% графен | 4.2 | 5.20 |
Al–0.1% графен | 5.22 | 5.87 |
Al–0.2% графен | 6.24 | 6.75 |
Al–0.01% графит | 10.3 | 5.92 |
Al–0.05% графит | 11.3 | 8.52 |
Al–0.1% графит | 15.6 | 9.30 |
Можно заметить, что скорости коррозии алюминий-графитового композита примерно в 3 раза выше, чем у алюминий-графенового композита при равном содержании углерода в них, причем скорости коррозии алюминий-графеновых композитов, определенные гравиметрическим и химико-аналитическим методом, совпадают, в то время как скорость коррозии алюминий-графитового композита, определенная гравиметрическим методом, всегда выше скорости коррозии, определенной химико-аналитическим методом. Этот факт можно объяснить сравнением микрофотографий алюминия, алюминий-графенового и алюминий графитового композитных материалов после их 4-месячной выдержки в растворе хлорида натрия, сделанные при одинаковом увеличении (рис. 6).
Рис. 6.
Электронные изображения поверхности образцов после 4 мес. выдержки в 3% растворе NaCl: а – алюминий, б – алюминий-графитовый композит, в – алюминий-графеновый композит.
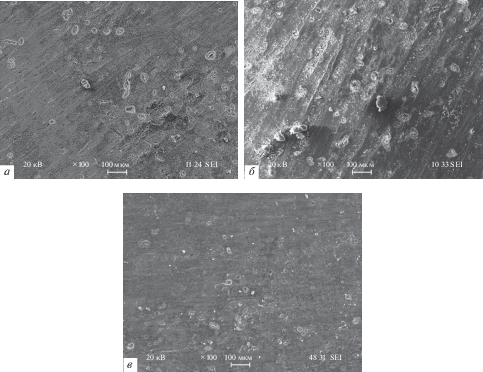
На поверхности алюминия после выдержки в растворе хлорида натрия наблюдаются многочисленные неглубокие питтинги и растравы, поверхность алюминий-графитового композита имеет многочисленные глубокие питтинги и растравы, в то время как поверхность алюминий-графенового композита равномерно корродирует, а пленки графена остаются на поверхности композитного материала даже после длительного коррозионного теста. Наличие графена на поверхности алюминий-графеновых композитных образцов после коррозионного теста было подтверждено Рамановской спектроскопией.
Рис. 7.
Электронные изображения питтингов вокруг кристаллов графита на поверхности алюминий-графитового образца после выдержки 4 мес. (а) и изображение пленки графена на продкутах коррозии алюминий-графенового композита (б).
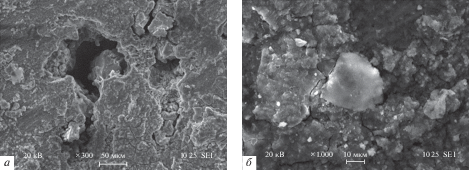
Рис. 8.
Рентгенограмма алюминий-графенового образца после 4 мес. выдержки в 3% растворе хлорида натрия. * Отмечены пики, соответствующие оксиду алюминия AlO.
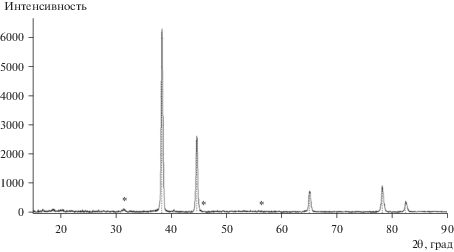
При рассмотрении увеличенного электронного изображения очевидно, что глубокие питтинги образуются вокруг кристаллов графита, что и становится причиной повышения скорости коррозии алюминий-графитового композита по сравнению с исходным алюминием в 10 раз. Коррозия алюминий-графитового композита носит неравномерный характер из-за большой разницы в стандартных потенциалах углерода и алюминия: графит становится катодом, провоцируя растворение алюминия. Глубина питтингов может достигать десятков микрон, площадь корродирующего вещества невозможно правильно оценить, поэтому расчет скорости коррозии такого материала из формулы (2) может быть только оценочным. Определение скорости коррозии по выходу ионов алюминия в раствор представляется более точным.
Вокруг графеновых пленок не наблюдается образование трещин из-за ничтожной толщины графеновых включений, поэтому коррозия алюминий-графенового композита носит равномерный характер.
ВЫВОДЫ
При химическом взаимодействии солевого расплава, содержащего карбид бора, с расплавленным алюминием в атмосфере воздуха синтезированы металлические композитные материалы Al–графен и алюминий–графит с равномерно распределенными по объему металла полностью смачиваемыми алюминием пленками графена размером до 100 мкм или кристаллами графита. Исследована коррозионная стойкость алюминий-графеновых и алюминий-графитовых композитных материалов в 3% растворе хлорида натрия при комнатной температуре. Скорость коррозии композитов выше скорости коррозии исходного алюминия, закономерно увеличиваясь с повышением содержания углерода в них. Отсутствие образования потенциально вредной примеси – карбида алюминия подтверждено как методом Рамановской спектроскопии, так и коррозионными испытаниями. Показано, что коррозия алюминий-графитового композита носит неравномерный характер, вокруг кристаллов графита образуются питтинги из-за большой разницы стандартных потенциалов углерода и алюминия. Коррозия алюминий-графенового композита носит равномерный характер.
Работа выполнена в ИВТЭ УрО РАН по бюджетному плану № темы АААА-А19-119020190042-7 с использованием оборудования Центра коллективного пользования “Состав вещества”.
Список литературы
Amateau M.F. Progress in the Development of Graphite Aluminum Composite Using Liquid Infiltration Technology // J. Composite Materials. 1976. 1. P. 1281–1289.
Meyers M.A., Chawla K.K. Mechanical Metallurgy Principles and Applications // Englewood Cliffs, N.J.: Prentice-Hall, Inc. 1984. P. 438–466.
Mortensen A., Cornie J.A., Flemings M.C. Solidification Processing of Metal–Matrix Composites // J. Metals (F). 1988. P. 12–19.
Yanmei L., Ziyang X., Gaohui W., Longtao J. Microstructure Evolution of Ti–Al–C System Composite // Rare Metal Materials and Engineering. 2010. 39. P. 1152–1156.
Naplocha K., Granat K. Dry sliding wear of Al/Saffil/C hybrid metal matrix composites // Wear. 2008. 265. P. 1734–1740.
Zabolotskiy A.A., Salibekov S.E. The creation of Al–C composite materials // Metallurgy and heat treatment of metals. 1978. 10. P. 49–52.
Корягин С.И., Пименов И.В., Худяков В.К. Способы обработки материалов: Уч. пособие. Калининград: Калининградский ун-т, 2000.
Uglov V.V., Cherenda N.N., Danilyuk A.L. Structural and phase composition changes in aluminium induced by carbon implantation // Surface and Coatings Technology. 2000. 128–129. P. 358–363.
Szcancoski J.C., Richter E., Foerster C.E., Serbena F.C. Mechanical and tribological properties of carbon and nitrogen consecutive ion implantation into aluminium // Surface and Coatings Technology. 2006. 201. P. 1488–1494.
Baba K., Hatada R., Flege S., Kraft G., Ensinger W. Plasma-based carbon ion implantation of aluminium at differ-ent process times in a pulse-ignited methane plasma // Surface and Coatings Technology. 2009. 203. P. 2617–2619.
So K.P., Kim E.S., Biswas Ch., Jeong H.Y. Low-temperature solid-state dissolution of carbon atoms into aluminum nanoparticles // Scripta Materialia. 2012. 66. P. 21–24.
Pérez-Bustamante R., Pérez-Bustamante F., Estrada-Guel I. Characterization of Al2024-CNTs composites produced by mechanical alloying // Powder Technology. 2011. 212. P. 390–396.
Morsi K., Esawi A.M.K., P. Borah. Properties of single and dual matrix aluminum–carbon nano-tube composites processed via spark plasma extrusion (SPE) // Materials Science and Engineering 2010. 527. P. 5686–5690.
Birol Y. In situ synthesis of Al–TiCp composites by reacting K2TiF6 and particulate graphite in molten aluminium // Journal of Alloys and Compounds. 2008. 454. P. 110–117.
Wang J., Li Z., Fan G., Pang H., Chen Z., Zhang D. Reinforcement with graphene nanosheets in aluminum matrix composites // Scripta Materialia. 2012. № 66. P. 594–597.
Bastwros M., Kim G., Zhu Cn. Effect of ball milling on graphene reinforced Al6061 composite fabricated by semi-solid sintering // Composites: Part B. 2014. 60. P. 111–118.
Rashad M., Pan F., Tang A., Asif M. Effect of Graphene Nanoplatelets addition on mechanical properties of pure aluminum using a semi-powder method // Progress in Natural Science: Materials International. 2014. 24. P. 101–108.
Yolshina L.A., Muradymov R.V., Korsun I.V., Yakovlev G.A., Smirnov S.V. Novel aluminum-graphene and aluminum-graphite metallic composite materials: Synthesis and properties // Journal of Alloys and Compounds. 2016. 663. P. 449–459.
Yolshina L.A., Muradymov R.V., Vichuzhanin D.I., Smirnova E.O. // AIP Conf. Proc. 2016. 1785. № 1. 040093. https://doi.org/10.1063/1.4967150
Yolshina L.A., Vovkotrub E.G., Shatunova A.A., Pryakhina V.I. // J. Raman Spectrosc., 2020. 51. № 2. P. 221–231. https://doi.org/10.1002/jrs.5771
Zameshin A., Popov M., Medvedev V., Perfilov S., Lomakin R., Buga S. Electrical conductivity of nanostructured and C60-modified aluminum // Appl. Phys. A. 2012. 107. P. 863–869.
Дополнительные материалы отсутствуют.