Расплавы, 2023, № 1, стр. 14-21
Увеличение стеклообразующей способности сплава Co41Fe7Cr15Mo14C15B6 при разбавлении редкоземельными металлами
И. В. Евдокимов a, Е. В. Стерхов a, *, В. А. Быков a, К. Ю. Шуняев a, Л. Д. Сон a
a Институт металлургии Уральского отделения РАН
Екатеринбург, Россия
* E-mail: ev.sterhov@mail.ru
Поступила в редакцию 30.07.2022
После доработки 05.09.2022
Принята к публикации 23.09.2022
- EDN: HIDAUH
- DOI: 10.31857/S0235010623010036
Аннотация
Эвтектические сплавы из-за своей низкоплавкости являются перспективными материалами для получения металлических стекол. В отличие от кристаллических сплавов, в стеклах отсутствует дальний порядок, что приводит к повышению твердости, механической прочности, коррозионной стойкости и магнитной проницаемости. Возможности использования данных материалов на практике регламентируются критическим диаметром, при котором еще возможно образование однофазного металлического стекла при закалке. Поэтому актуальной задачей в этой области исследований является повышение критического диаметра имеющихся аморфных сплавов. Одним из методов улучшения стеклообразующей способности сплавов является их разбавление более тугоплавкими металлами. В данной работе представлены рентгеноаморфные металлические стекла сплавов (Co41Fe7Cr15Mo14C15B6)100 –xRx с разбавлением редкоземельными металлами (R = Gd, Ho, La, Nd, Y, Yb; x = 0; 2). Методами рентгеновской дифракции и сканирующей электронной микроскопии установлен критический диаметр, фазовый и элементный состав сплавов в зависимости от скорости закалки. Установлено, что добавление 2 ат. % Gd, Ho и Y значительно увеличивает стеклообразующую способность сплава Co–Fe–Cr–Mo–C–B. Методом спиннингования, при закалке на алюминиевом диске, вращающемся с линейной скоростью 11.5 м/с, получены ленты толщиной от 19 до 73 мкм. На поверхности лент были обнаружены редкие включения с высоким содержанием редкоземельных элементов вплоть до 35 ат. %, которые могут выступать в качестве центров кристаллизации.
ВВЕДЕНИЕ
Практическое применение металлических стекол сильно ограничено их типоразмером. В основном аморфные металлические материалы используют в виде лент, для создания магнитопроводов [1] и сердечников для высокочастотных трансформаторов [2–4], либо их напыляют на конструкционные материалы [5] для повышения коррозионной стойкости и износостойкости. Объемные металлические стекла (ОМС) используют для этих целей реже, из-за недостаточного для технологии (меньше 30 мм) критического диаметра (Dc). На самом деле, ОМС обладают преимуществами перед аморфными лентами и пленками из-за простоты изготовления, высокой воспроизводимости функциональных характеристик изделий и возможности отливать их в произвольную форму.
В последнее время были получены объемно-аморфные сплавы: Fe41Co7Cr15Mo14C15B6Y2 [6], Fe43Co4.5Cr16.5Mo16.5C14B4Y1.5 [7] и (Fe, Co)48Cr15Mo14C15B6Tm2 [8] с критическими диаметрами 10–16 мм. Однако, исследовательский поиск, направленный на выявление оптимального состава, ведется до сих пор. Так, замещение Fe на Co в количестве 4–8 ат. % позволяет увеличить намагниченность насыщения и добиться низкой коэрцитивной силы [9]. Коррозионная стойкость является не менее важным параметром металлических стекол наряду с магнитными характеристиками. Добавление Cr и Mo в количестве 30 ат. % [10] позволяет достичь оптимальной скорости коррозии ~1.3 · 10–4 мм/год в растворах 1н HCl, 1н HNO3 и 1н NaOH [11]. Кроме того, при эквимолярном содержании Cr и Mo достигается наилучшая стеклообразующая способность [12]. Углерод и бор являются важными составляющими для данных металлических стекол, которые повышают стеклообразующую способность и увеличивают прочность [13]. Было обнаружено, что увеличение стеклообразующей способности происходит при содержании С 15 ат. % и B 6 ат. %. Стеклообразующая способность снижается при замещении C на B в ряду С15 –xB6 +x (x = 0, 2, 3, 4). [14]. Сплавы на основе Co без добавления редкоземельного элемента (РЗЭ) имеют низкую стеклообразующую способность, и при одинаковых температурах охлаждения удается получить цилиндры не более 2 мм [15, 16]. В работах [17–19] установлено, что наилучшая стеклообразующая способность проявляется при добавках Y и Er в количестве 2 ат. %. При этом, эффект от добавок Y оказывается более существенным [15, 20]. Данная работа посвящена изучению влияния РЗЭ на стеклообразующую способность сплавов (Co41Fe7Cr15Mo14C15B6)100 –xRx (R = Gd, Ho, La, Nd, Y, Yb; x = 0; 2).
МЕТОДИКА ПРОВЕДЕНИЯ ЭКСПЕРИМЕНТОВ
Для изготовления сплавов использовали стехиометрические навески элементов, углерод и бор после взвешивания прессовали в таблетку. Сплавы были получены путем плавки в дуговой печи в атмосфере аргона с чистотой 99.993%. Сплав переплавляли 8–9 раз на водоохлаждаемой изложнице. Для отливки стержней использовали метод литья в медную цилиндрическую форму с диаметром 3 мм и длиной 100 мм. Ленты получали методом спиннингования [14] на алюминиевом диске с линейной скоростью вращения 11.5 м/с. После каждой отливки для удаления остатков предыдущего сплава и улучшения адгезии диск полировали мелкозернистой наждачной бумагой. Для аттестации сплавов изготавливали шлифы на наждачной бумаге из карбида кремния. Финальную полировку проводили с использованием алмазной пасты АСМ 0-1 до зеркального состояния.
Рентгеновские дифракционные спектры снимали на дифрактометре XRD 7000 фирмы Shimadzu. Рентгеновскую съемку образцов, закаленных в форме стержней и лент, проводили методом порошковой дифракции, для этого их размалывали в агатовой ступке до порошкообразного состояния в среде изопропилового спирта. Фазовый анализ выполнен с помощью международной картотеки ICDD PDF-2 со встроенными модулями автоматического поиска фаз и полуколичественного анализа методом корундовых чисел.
Морфологию, критический диаметр и химический состав поверхности исследовали с помощью сканирующего электронного микроскопа Carl Zeiss EVO 40 с ускоряющим напряжением 20 кВ на V-образном вольфрамовом катоде. Определение элементного состава поверхности проводили с помощью энергодисперсионного рентгеновского анализатора INCA Energy. Спектры набирали в течение минуты для каждой из пяти различных точек для областей, отличающихся по композиционному контрасту.
Для определения температур и теплот структурных фазовых превращений аморфных металлических лент был использован метод дифференциальной сканирующей калориметрии (ДСК). Измерения были выполнены на термоанализаторе NETZSCH STA 409 PC в тиглях из Al2O3 в атмосфере аргона. Температурная программа включала в себя нагрев от комнатной температуры до 1100°С, со скоростью 20 К/мин.
РЕЗУЛЬТАТЫ И ИХ ОБСУЖДЕНИЯ
На дифрактограммах образцов, закаленных на водоохлаждаемой изложнице (рис. 1а) наблюдаются рефлексы, соответствующие кристаллическим фазам Me, Me3C и Me23B6, где Me = Co, Cr, Mo, Fe.
Рис. 1.
Дифрактограммы закаленных сплавов (а) и стержней (б) (Co41Fe7Cr15Mo14C15B6)100 – xRx (R = Gd, Ho, La, Nd, Y, Yb; x = 0; 2).
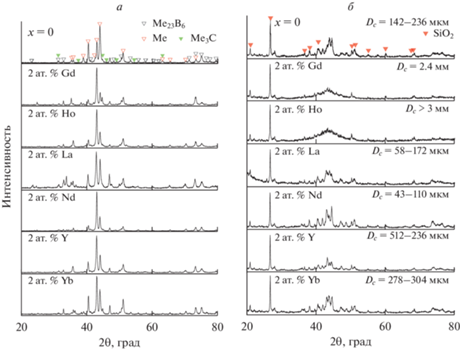
По данным сканирующей электронной микроскопии все образцы содержат минимум 4 фазы (рис. 2). Композиционный контраст фаз обусловлен флуктуацией химического состава Co, Cr, Mo и РЗЭ в пределах 1–3 ат. %, тогда как содержание Fe в пределах погрешности одинаковое для всех фаз (табл. 1). Стержни из сплавов с Ho и Gd являются однофазными металлическими стеклами, о чем свидетельствует одиночный диффузный пик при 2θ 40°–50° (рис. 1б). На дифрактограммах стержней остальных образцов наблюдаются плохо сформировавшиеся кристаллические фазы. Оценку критического диаметра производили по снимкам сканирующей электронной микроскопии в режиме обратно-рассеянных электронов. Стоит отметить, что для всех образцов, перемолотых в агатовой ступке, на рентгеновских паттернах наблюдаются примесные пики, которые относятся к SiO2.
Таблица 1.
Среднее содержание металлов в разных фазах сплава Co41Fe7Cr15Mo14C15B6Ho2
Фаза | Cr, ат. % | Fe, ат. % | Co, ат. % | Mo, ат. % | Ho, ат. % |
---|---|---|---|---|---|
A | 13.22 | 7.52 | 44.22 | 12.22 | 1.81 |
B | 15.15 | 7.24 | 41.69 | 13.88 | 1.03 |
C | 16.65 | 7.21 | 41.42 | 12.83 | 0.89 |
D | 14.80 | 7.45 | 41.39 | 13.41 | 1.94 |
Полученные методом спинингования ленты сплавов (Co41Fe7Cr15Mo14C15B6)100 –xRx (R= Ho, Gd, Nd, Y, La, Yb и x = 0; 2) являются рентгеноаморфными (рис. 3).
Рис. 3.
Дифрактограммы сплавов (Co41Fe7Cr15Mo14C15B6)100– xRx (R = Gd, Ho, La, Nd, Y, Yb; x = 0; 2), закаленных в форме лент.

При помощи сканирующей электронной микроскопии в лентах Co41Fe7Cr15Mo14C15B6R2 (R = Ho, Gd, Nd, Y, La, Yb) были обнаружены включения с высоким содержанием РЗЭ до 35 ат. %. Несмотря на высокую скорость закалки, эти включения успевают образоваться, и могут являться зародышами для кристаллизации фазы.
На рис. 4 приведены ДСК кривые для сплавов (Co41Fe7Cr15Mo14C15B6)100 –xRx (R = = Ho, Nd, x = 0; 2). По кривым ДСК видно, что добавление в сплав Co–Fe–Cr–Mo–C–B Nd и Ho приводит к увеличению температуры стеклования Tg, кристаллизации Tx и первого пика кристаллизации Tp. Для всех образцов характерна многоэтапная кристаллизация. Наименьшая температура начала плавления (Tm) и ликвидуса (Tl) наблюдается у сплава Co41Fe7Cr15Mo14C15B6Ho2 и составляет 1378.2 и 1421.0 К соответственно (табл. 2).
Рис. 4.
ДСК кривые сплавов (Co41Fe7Cr15Mo14C15B6)100 – xRx (R = Ho, Nd; x = 0; 2), снятые при скорости нагрева 20 K/мин.
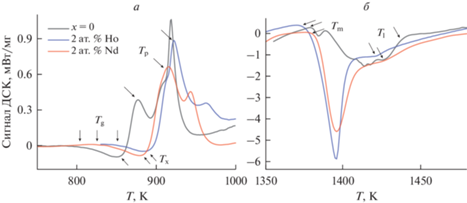
Таблица 2.
Температуры фазовых превращений и приведенная температура стеклования
Сплав | Tg, К | Tx, К | Tp, К | Tm, К | Tl, К | ${{T}_{{rg}}} = \frac{{{{T}_{g}}}}{{{{T}_{l}}}}$ [22] |
---|---|---|---|---|---|---|
x = 0 | 815.2 | 856.8 | 876.9 | 1379.7 | 1440.2 | 0.566 |
2 ат. % Nd | 837.8 | 889.0 | 915.6 | 1383.6 | 1427.1 | 0.587 |
2 ат. % Ho | 856.7 | 898.3 | 922.3 | 1378.2 | 1421.0 | 0.603 |
Для эвтектических систем существует прямая зависимость между Dc и приведенной температурой стеклования (Trg), которая впервые была предложена авторами [23 ] . Добавление Ho приводит к увеличению приведенной температуры стеклования, при этом экспериментально определенный Dc достигает более 3 мм. С другой стороны, сплав с Nd имеет Dc в пределах 43–110 мкм, что меньше чем у базового сплава, у которого приведенная температура ниже. Данное несоответствие объясняется тем, что авторы рассматривали объемные металлические стекла, для которых характерны большие критические диаметры. Для составов с Gd и Ho температура плавления сплава увеличивается c 1585.2 до 1747.2 К, а критический диаметр с 2.4 до 3 мм соответственно. Однако такое поведение не наблюдается для образца с Y. С другой стороны, в ряду Ho–Gd–Y–Yb критический диаметр уменьшается вместе с радиусами редкоземельных элементов. В ряду Y–Yb критический диаметр может зависеть как от температуры плавления, так и от радиуса РЗЭ.
ЗАКЛЮЧЕНИЕ
Впервые получены сплавы состава (Co41Fe7Cr15Mo14C15B6)100 –xRx (R = Gd, Ho, La, Nd, Y, Yb; x = 0; 2) в закаленном и аморфном состояниях. Добавление Ho и Gd в базовый состав позволяет получить объемно-аморфные образцы с критическими диаметрами 3 и 2.4 мм соответственно, в то время как при аналогичных условиях критический диаметр базового состава составляет от 142 до 236 мкм. Стержни сплавов с La, Nd, Y и Yb обладают Dc в диапазоне 43–556 мкм и содержат плохо сформировавшиеся кристаллические фазы (Me, Me3C и Me23B6, где Me = Co, Cr, Mo, Fe), характерные для закаленных образцов. Рентгеноаморфные образцы для этих составов удается получить при закалке на алюминиевый диск с линейной скоростью вращения 11.5 м/с. Средняя толщина лент не превышает критический диаметр сплавов и варьируется от 19 до 73 мкм. При помощи СЭМ на поверхности лент были обнаружены включения с высоким содержанием РЗЭ до 35 ат. %, которые могут выступать в качестве центров кристаллизации.
Работа выполнена при финансовой поддержке РНФ в рамках проекта № 21-13-00202 с использованием оборудования ЦКП “Урал-М”.
Список литературы
Стародубцев Ю.Н. Теория и расчет трансформаторов малой мощности. М.: ИП РадиоСофт, 2005.
Кейлин В.И., Дорощенко Б.Б., Белозеров В.Я., Стародубцев Ю.Н. Жесткий ленточный сердечник. Патент РФ 2 044 796, № 9 300 205/02; заявл. 11.01.1993, опубл. 27.09.1995.
Кейлин В.И., Дорощенко Б.Б., Белозеров В.Я., Стародубцев Ю.Н., Хлопунов С.И. Жесткий ленточный сердечник с высокой магнитной проницаемостью. Патент РФ 2 041 282. № 93 002 058/02; заявл. 11.01.1993; опубл. 09.08.1995.
Кейлин В.И., Белозеров В.Я., Стародубцев Ю.Н. Трансформатор. Патен РФ 2 041 514, № 92 010 326/02; заявл. 07.12.1992; опубл. 09.08.1995.
Jang J., Tsai P., Shiao A., Li T., Chen C., Chu J., Dug J., Chen M., Chang S., Huang W. Enhanced cutting durability of surgical blade by coating with Fe-based metallic glass thin film // Intermetallic. 2015. 65. P. 56–60.
Shen J., Chen Q., Sun J., Fan H., Wang G. Exceptionally high glass-forming ability of an FeCo–CrMoCBY alloy // Applied physics letters. 2005. 86. P. 151907-1–151907-3.
Guo S.F., Chan K.C., Xie S.H., Yu P., Huang Y.J., Zhang H.J. Novel centimeter-size Fe-based bulk metallic glass with high corrosion resistance in simulated acid rain and seawater // J. Non-Crystalline Solids. 2013. 369. P. 29–33.
Amiya K., Inoue A. Fe-(Cr,Mo)-(C,B)-Tm bulk metallic glasses with high strength and high glass-forming ability // Materials Transactions. 2006. 47. P. 1615–1618.
Shen B., Kimira H., Inoue A., Mizushima T. Bulk glassy Fe78 –xCoxGa2P12C4B4 alloys with high saturation magnetization and good soft magnetic properties // Materials Transactions. 2001. 42. P. 1052–1055.
Ponnambalam V., Poon S.J., Shiflet G.J. Fe-based bulk metallic glasses with diameter thickness larger than one centimeter // J. Mater. Res. 2004. 19. P. 1320–1323.
Wang L., Chao Y. Corrosion behavior of Fe41Co7Cr15Mo14C15B6Y2 bulk metallic glass in NaCl solution // Materials Letters. 2012. 69. P. 76–78.
Pang S., Zhang T., Asami K., Inoue A. Formation of bulk glassy Fe75 –x – yCrxMoyC15B10 alloys and their corrosion behavior // J. Mater. Res. 2002. 17. P. 701–704.
Duarte M.J., Klemm J., Klemm S.O., Mayrhofer K.J.J., Stratmann M., Borodin S., Romero A.H., Madinehei M., Serrano J., Gerstl S.S.A., Choi P.P., Raabe D., Renner F.U. Element-resolved corrosion analysis of stainless-type glass-forming steels // Science. 2013. 341. P. 372–376.
Стародубцев Ю. Аморфные металлические материалы // Силовая электроника. 2009. № 2. С. 86–89.
Men H., Pang S.J., Zhang T. Thermal stability and microhardness of new Co-based bulk metallic glasses // Materials Science and Engineering A. 2007. 449–451. P. 538–540.
Lotfollahi Z., Garcia-Arribas A., Amirabadizadeh A., Orue I., Kurlyandskaya G.V. Soft magnetic Co-based Co–Fe–B–Si–P bulk metallic glasses with high saturation magnetic flux density of over 1.2 T // J. alloys and compounds. 2020. 843. P. 3–7.
Maddala D.R., Hebert R.J. Sliding wear behavior of Fe50 –xCr15Mo14C15B6Erx (x = 0, 1, 2 at. %) bulk metallic glass // Wear. 2012. 294–295. P. 246–256.
Chen Q., Zhang D., Shen J., Fan H., Sun J. Effect of yttrium on the glass-forming ability of Fe–Cr–Mo–C–B bulk amorphous alloys // J. Alloys and Compounds. 2007. 427. P. 190–193.
Men H., Pang S.J., Zhang T. Effect of Er doping on glass-forming ability of Co50Cr15Mo14C15B6 alloy // J. Mater. Res. 2006. 21. P. 958–961.
Men H., Pang S.J., Li R., Tao Z. Crystallization kinetics of Co48Cr15Mo14C15B6Er2 bulk metallic glass with high thermal stability // Chinese Phys. Lett. 2006. 23. P. 417–419.
Turnbull D. Under what conditions can a glass be formed // Contemp. Phys. 1969. 10. P. 473–488.
Lu Z.P., Tan H., Li Y., Ng S.C. The correlation between reduced glass transition temperature and glass forming ability of bulk metallic glasses // Scripta mater. 2000. 42. P. 667–673.
Дополнительные материалы отсутствуют.