Теоретические основы химической технологии, 2022, T. 56, № 1, стр. 34-47
Исследование динамических режимов работы схем экстрактивной ректификации смеси бензол–циклогексан–толуол
А. С. Бурачук a, *, Е. А. Анохина a, А. В. Тимошенко a
a МИРЭА – Российский технологический университет (Институт тонких химических технологий
им. М.В. Ломоносова)
119571 Москва, пр. Вернадского, 78, Россия
* E-mail: anton@burachuk.com
Поступила в редакцию 12.08.2021
После доработки 23.08.2021
Принята к публикации 29.08.2021
- EDN: TUKQND
- DOI: 10.31857/S0040357122010043
Аннотация
В работе рассмотрено четыре схемы экстрактивной ректификации смеси бензол–циклогексан–толуол различной структуры: одна традиционная, состоящая из трех двухотборных колонн, и три, включающие комплексы со связанными тепловыми и материальными потоками. Для каждой схемы определены оптимальные по критерию суммарных энергетических затрат в кипятильниках колонн статические параметры, разработаны автоматические системы управления и выполнен анализ устойчивости к внешним возмущающим воздействиям в виде изменения расхода и состава потока питания. Показано, что экономия энергозатрат за счет применения комплексов со связанными тепловыми и материальными потоками достигает 31.98%. Для комплекса с боковой исчерпывающей секцией, обеспечивающего сокращение энергопотребления на 28.37%, предложена структура автоматического управления, которая обеспечивает эффективность регулирования и устойчивость к возмущающим воздействиям, сопоставимые с аналогичными показателями традиционной схемы.
ВВЕДЕНИЕ
Бензол является ценным полупродуктом для промышленности основного органического и нефтехимического синтеза. Он используется для получения алкилбензолов, фенола, циклогексана и других органических соединений. В промышленности бензол получают в процессах коксования каменного угля, пиролиза и риформинга нефтяного сырья, гидродеалкилирования ароматических фракций. В результате предварительного разделения смесей компонентов, образующихся в этих процессах, выделяют фракцию сырого бензола, которая содержит большое число как ароматических, так и неароматических соединений. Для извлечения товарного бензола из этой фракции применяют методы экстракции и экстрактивной ректификации (ЭР) [1–6].
Вследствие больших объемов производства бензола снижение энергетических затрат на его выделение является актуальной задачей. Один из возможных способов ее решения – проведение ЭР в комплексах с частично связанными тепловыми и материальными потоками (ЧСТМП) [7], что позволяет приблизить условия протекания реального процесса к гипотетическому режиму термодинамически обратимой ректификации [8], который характеризуется минимальными энергетическими затратами на разделение. Как следует из анализа литературных данных, применение комплексов с ЧСТМП в экстрактивной ректификации в ряде случаев позволяет снизить энергоемкость разделения на 20–30% [9].
Авторы [8] отмечают, что широкому внедрению комплексов с ЧСТМП в промышленность препятствует более сложная система управления по сравнению с обычными ректификационными колоннами. Вызвано это сложной взаимосвязью параметров работы таких комплексов, уменьшением степеней свободы и наличием большего количества каналов обратного распространения возмущающих воздействий (ВВ). В последнее время предложено несколько эффективных схем регулирования комплексов ЭР с ЧСТМП [10–13], и исследования в этом направлении продолжаются.
Цель работы – моделирование и оптимизация схем ЭР смеси бензол (Б) – циклогексан (ЦГ) – толуол (Т) различной структуры, оценка устойчивости динамических режимов их работы, вызванных внешними возмущающими воздействиями.
РАСЧЕТНАЯ ЧАСТЬ
В системе Б–ЦГ–Т имеется азеотроп с минимумом температуры кипения в бинарной составляющей бензол–циклогексан. Основываясь на литературных данных [6], в качестве экстрактивного агента выбран N-метил-2-пирролидон (NMP), который увеличивает летучесть ЦГ по отношению к бензолу.
Схемы ЭР смеси Б–ЦГ–Т, рассматриваемые в данной работе, представлены на рис. 1.
Рис. 1.
Принципиальные схемы экстрактивной ректификации: a – традиционная схема П; б–г – схемы с частично связанными тепловыми и материальными потоками: О.1, О.2 и О.3, соответственно. БКЭР – боковая колонна экстрактивной ректификации; ИБС – исчерпывающая боковая секция; КР – колонна регенерации экстрактивного агента; КЭР – колонна экстрактивной ректификации; ОК – основная колонна; УБС – укрепляющая боковая секция; 3 – колонна разделения бензола и толуола. F – поток питания; Б – бензол; Т – толуол; ЦГ – циклогексан; NMP – N-метил-2-пирролидон (экстрактивный агент).
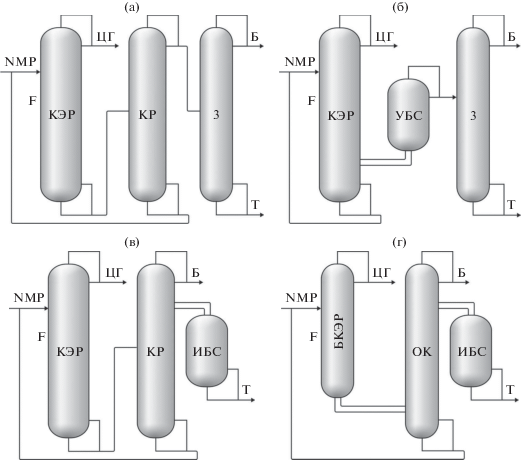
Схема П (рис. 1a) состоит из трех двухотборных колонн. Схемы О.1, О.2 и О.3 (рис. 1б–1г), включающие комплексы с ЧСТМП, получены из схемы П с помощью алгоритма [15]. В основе данного алгоритма лежит структурное представление схем ректификационного разделения посредством графов. Схемы, на основе которых синтезируют новые технологические решения, называют прообразами, а схемы, полученные в результате операций трансформации над графами схем-прообразов, – образами.
В рассматриваемом случае схемой-прообразом выступает схема, представленная на рис. 1a, а схемы, представленные на рис. 1б–1г, являются ее образами.
Схема-образ О.1 (рис. 1б) включает сложную колонну с укрепляющей боковой секцией (УБС), которая получена в результате термического связывания колонны экстрактивной ректификации (КЭР) и колонны регенерации (КР) экстрактивного агента схемы-прообраза П, а также колонну разделения бензола и толуола, которая идентична третьей колонне схемы П.
Трансформация схемы П в схему-образ О.2 (рис. 1в) осуществлена путем термического связывания колонны регенерации экстрактивного агента и колонны 3. В полученном комплексе с ЧСТМП бензол отбирается в виде дистиллята основной колонны, толуол – в качестве кубового продукта исчерпывающей боковой секции (ИБС), а NMP – в виде кубового потока КР. Экстрактивная колонна схемы-прообраза осталась без изменений.
Более глубокие преобразования схем О.1 и О.2 приводят к одному и тому же комплексу с ЧСТМП (схема О.3 , рис. 1г), состоящему из основной колонны (ОК), в дистилляте которой происходит выделение бензола, а в кубе – NMP, и термически связанных с ней боковой колонны экстрактивной ректификации (БКЭР) и исчерпывающей боковой секции. В дистилляте БКЭР выделяется циклогексан, продуктовым потоком ИБС является толуол.
Определение оптимальных рабочих параметров схем. Расчеты проводились на ${{G}_{F}} = 15\,000$ кг/ч исходной смеси, содержащей 78, 12 и 10 мас. % Б, ЦГ и Т, соответственно. Качество продуктовых потоков Б и ЦГ было задано 99.9 мас. % (ГОСТ 9572-93 и ГОСТ 14198-78), Т – 99.75 мас. % (ГОСТ 14710-78). Концентрация NMP в потоке регенерированного ЭА составляла 99.99 мас. %. Расчет колонн проводили с теоретическими тарелками, но с учетом гидравлического сопротивления тарелки, которое задавали равным ∆p = 0.689 кПа.
Для расчета коэффициентов активности использовали уравнение локальных составов NRTL, а для описания зависимости давления насыщенных паров чистых компонентов от температуры – уравнение Антуана (1). Параметры уравнений представлены в табл. 1 и 2 [14].
(1)
${\text{ln}}P = ~{{C}_{1}} + \frac{{{{C}_{2}}}}{{T + {{C}_{3}}}} + {{C}_{4}}T + {{C}_{5}}{\text{ln}}T + {{C}_{6}}{{T}^{{{{C}_{7}}}}}.$Таблица 1.
Параметры бинарного взаимодействия модели NRTL (кПа и К) [14]
Комп. i | Б | Б | Б | ЦГ | ЦГ | Т |
---|---|---|---|---|---|---|
Комп. j | ЦГ | Т | NMP | Т | NMP | NMP |
AIJ | 0.657505 | 0 | 0 | –0.10246 | 0 | –0.4766 |
AJI | –1.2279 | 0 | 0 | –0.77637 | 0 | 1.5075 |
BIJ | –64.7939 | 55.9156 | 663.349 | 142.48 | 523.919 | 270.966 |
BJI | 400.999 | –61.0122 | –502.497 | 271.031 | 323.62 | –615.651 |
CIJ | 0.3375 | 0.3033 | 0.1771 | 0.4299 | 0.2902 | 0.3 |
Таблица 2.
Параметры уравнения Антуана (1), температура в K, давление в кПа для всех компонентов кроме NMP (для NMP давление в Па) [14]
Б | ЦГ | Т | NMP | |
---|---|---|---|---|
С1 | 76.1992 | 44.1792 | 70.0372 | 22.687 |
С2 | –6486.2 | –5226.4 | –6729.8 | –4958.4 |
С3 | 0 | 0 | 0 | –31.139 |
С4 | 0 | 0 | 0 | 0 |
С5 | –9.2194 | –4.2278 | –8.179 | 0 |
С6 | 6.98 × 10–6 | 9.76 × 10–18 | 5.30 × 10–6 | 0 |
С7 | 2 | 6 | 2 | 0 |
С8 | 278.68 | 279.69 | 178.18 | 249.15 |
С9 | 562.05 | 553.8 | 591.75 | 710 |
Были определены оптимальные параметры исследуемых схем в статическом режиме работы по критерию суммарных энергетических затрат в кипятильниках колонн Q∑. Ограничения на оптимизацию – качество продуктов разделения. Параметры оптимизации для схемы П: число теоретических тарелок (т.т.) в колоннах Nобщ, температура подачи ЭА в экстрактивную колонну, расход экстрактивного агента GЭА, положение тарелок питания в колоннах NF (для колонны ЭР дополнительно находили оптимальный уровень ввода ЭА, NЭА). При определении оптимальных параметров схем, включающих комплексы с ЧСТМП, были закреплены положение тарелок подачи питания и ЭА, температура и расход ЭА в соответствии с оптимальными значениями этих величин, определенными для схемы-прообраза П. Суммарное количество тарелок в комплексах с ЧСТМП было равно суммарному числу тарелок в двухотборных колоннах схемы-прообраза. Параметры оптимизации для схем-образов О.1, О.2 и О.3: положение тарелки (тарелок) отбора в боковые секции NБО и количество потока, отбираемого в боковые секции.
Оптимизация схем осуществлялась в соответствии с алгоритмами, описанными в работах [14, 16], в программном комплексе Aspen Plus V9 с помощью встроенных модулей: Sensitivity Analysis и Optimization.
Оптимальные параметры схем ЭР представлены в табл. 3. Согласно алгоритму синтеза комплексов с ЧСТМП [15], в ходе преобразований схемы-прообраза в схемы-образы экстрактивная секция КЭР остается неизменной. Поэтому для всех схем-образов по результатам оптимизации схемы-прообраза П расход ЭА GЭА принят равным 22 600 кг/ч, температура потока ЭА – 70°С, уровень подачи ЭА NЭА = 4 т.т. и уровень подачи питания в КЭР NF = 15 т.т.
Таблица 3.
Оптимальные статические параметры исследуемых схем
Схема | Аппарат | Nобщ, т.т. | NF (NБО) | RR | Qкип, кВт | Qкип.Σ, кВт | Снижение Qкип.Σ, % |
---|---|---|---|---|---|---|---|
П | КЭР | 34 | 15 | 3.21 | 1552 | 7136 | 0 |
КР | 13 | 7 | 0.31 | 2801 | |||
Колонна 3 | 25 | 14 | 1.16 | 2783 | |||
О.1 | КЭР | 40 | 15 (34) | 3.48 | 4268 | 7051 | 1.20 |
УБС | 7 | 7 | 0.31 | ||||
Колонна 3 | 25 | 14 | 1.16 | 2783 | |||
О.2 | КЭР | 34 | 15 | 3.48 | 1552 | 5559 | 28.37 |
КР | 27 | 21 (14) | 1.38 | 2863 | |||
ИБС | 11 | 1 | – | 1144 | |||
О.3 | БКЭР | 34 | 15 | 3.36 | 4293 | 5407 | 31.98 |
ОК | 27 | (17/22) | 1.23 | ||||
ИБС | 11 | 1 | – | 1114 |
Традиционная схема экстрактивной ректификации П, как и ожидалось, обладает наибольшими энергетическими затратами в кипятильниках колонн. Минимальное значение Q∑ среди всех исследуемых схем достигнуто в схеме О.3 с боковой колонной ЭР и боковой исчерпывающей секцией. Данная схема обеспечивает снижение энергозатрат по сравнению со схемой П на 31.98%.
Моделирование динамического режима работы схем ЭР. Моделирование динамического режима работы схем, разработка автоматических систем управления и анализ устойчивости переходных процессов произведены в программном комплексе Aspen Plus Dynamics V9.
Главным каналом поступления возмущающих воздействий (ВВ) в исследуемые схемы ректификации является поток питания, которому свойственны колебания расхода, температуры и состава.
Колебание количества подачи исходной смеси в колонну является одним из наиболее сильных ВВ процесса. В технологической схеме для обеспечения постоянства потока питания колонн предусматривают автоматические системы регулирования (АСР) расхода, наличие которых существенно облегчает работу всех других АСР установки.
Колебания температуры поступающего на разделение потока также регулируется локальной АСР, состоящей из измерителя температуры, установленного после теплообменника (ТО), и регулятора, функцией которого является выработка управляющего воздействия – изменение расхода греющего пара в ТО – по отклонению температуры.
Как и первые два параметра, колебания состава исходной смеси определяются предшествующим технологическим процессом. Однако, возмущающее воздействие не может быть устранено в материальном потоке до попадания его в колонну, тем самым оказывая воздействие непосредственно на параметры работы самой колонны.
Были исследованы следующие ВВ:
1. Ступенчатое изменение массового потока исходной смеси на ±10% от заданного значения ${{G}_{F}} = 15\,000$ кг/ч, которое будет задаваться АСР расхода, таким образом симулируя выход на новый режим по потоку питания.
2. Ступенчатое изменение концентрации циклогексана в исходной смеси $X_{{{\text{ЦГ}}}}^{F}$ на величину ±5 мас. % от 12 мас. % ЦГ в исходной смеси F, т.е. во входном потоке задавались концентрации 7 и 17 мас. %.
АСУ традиционной схемы П. На первом этапе рассмотрим вопросы проектирования одноконтурных систем автоматического регулирования отдельных технологических параметров, совокупность которых отвечает за поддержание материального баланса схемы в целом, поскольку они являются наиболее простыми и надежными как в наладке, так и в работе [17]. К таким АСР относятся регуляторы уровней жидкости в кубовых и флегмовых емкостях, контуры регулирования потока питания и расхода ЭА, локальные АСР температур на выходах из теплообменников и регуляторы давления верха колонн (рис. 2).
Рис. 2.
Автоматическая система управления традиционной схемы П. КР – колонна регенерации экстрактивного агента; КЭР – колонна экстрактивной ректификации; 3 – колонна разделения бензола и толуола. F – поток питания; NMP – N-метил-2-пирролидон (экстрактивный агент).
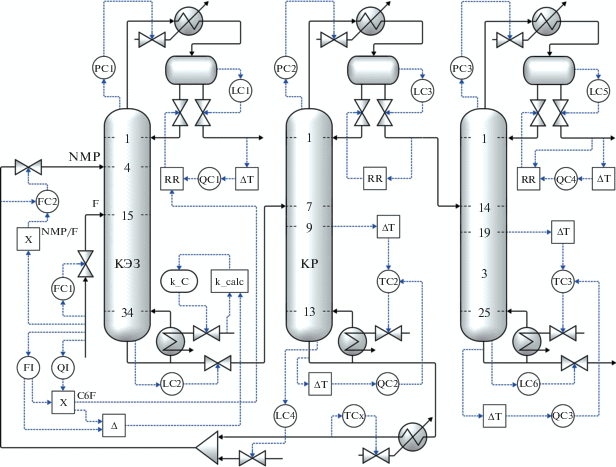
Регуляторы уровней LC подчиняются пропорциональному закону регулирования. Все остальные регуляторы, входящие в базовую АСУ, подчиняются пропорционально-интегральному закону. Настройки АСР, общих для всех исследуемых схем, занесены в табл. 4.
Таблица 4.
Настройки базовых регуляторов
Обозначение | KP | TИ, мин |
---|---|---|
LC | 2 | 9999 |
FC | 0.5 | 0.3 |
PC | 20 | 12 |
TCх | 0.34 | 1.3 |
Принцип действия всех АСР уровня емкостей LC одинаков: прямое действие регулятора при повышении уровня жидкости увеличивает проходное сечение вентиля, тем самым увеличивая расход соответствующего потока, и наоборот. Исключение – регулятор LC4, обратное действие которого направлено на изменение потока подпитки свежим ЭА. При снижении уровня в кубе КР, который заполнен регенерированным NMP, управляющее воздействие должно быть направлено на увеличение расхода NMP в соответствующую емкость, а, т. к. рецикл замкнут, единственным источником NMP в системе является поток свежего экстрактивного агента.
АСР FC обратным действием регулирует поток питания: при изменении расхода управляет положением вентиля.
Регулятор расхода потока ЭА FC2 работает в каскадном режиме. Заданием регулятору служит массовый расход потока питания F, умноженный на константу $~\frac{{{{G}_{{{\text{ЭА}}}}}}}{{~{{G}_{F}}}} = \frac{{22\,600\,\,~{{{\text{кг}}} \mathord{\left/ {\vphantom {{{\text{кг}}} {\text{ч}}}} \right. \kern-0em} {\text{ч}}}}}{{15\,000~\,\,{{{\text{кг}}} \mathord{\left/ {\vphantom {{{\text{кг}}} {\text{ч}}}} \right. \kern-0em} {\text{ч}}}}} = 1.5067.$
Температуры потоков на выходе из теплообменного оборудования регулируются АСР TCх, вырабатывающими управляющие воздействия (УВ) в виде изменения расхода греющего пара вентилем по отклонению температур от заданных значений. Аналогично действуют регуляторы давления верха колонн PC: измеряемая величина – давление, регулируемая величина – теплоотвод в конденсаторе соответствующей колонны.
Управление процессом ректификации в КЭР. Ключевым аппаратом всех исследуемых схем является колонна экстрактивной ректификации. Нарушение режима в ней приведет к отклонению составов всех продуктовых потоков от заданных значений. Регулирование осложняется также и тем, что в КЭР присутствует наибольшее количество компонентов.
Т.к. товарным продуктовым потоком КЭР является дистиллят, то основной регулируемой величиной ректификационной установки будет состав паров в верхней части колонны или состав дистиллята, которые регулируются изменением подачи флегмы в колонну. При этом регулятор может быть установлен как на линии подачи флегмы, так и на линии отвода дистиллята. С точки зрения статики — это равноценно. Однако для повышения качества регулирования АСР состава целесообразно устанавливать на линию подачи флегмы в колонну. При этом для сохранения материального баланса укрепляющей части колонны количество отводимого дистиллята необходимо регулировать с помощью АСР уровня во флегмовой емкости (регулятор LC1). Иначе инерционные свойства емкости будут влиять на качество процесса регулирования, что может привести к нежелательным последствиям [18].
Регулирующие воздействия в исчерпывающей секции колонны могут осуществляться изменением расхода кубового продукта и тепловой нагрузки кипятильника. Одно из них, а именно расход, следует использовать для поддержания материального баланса колонны, т.е. для стабилизации уровня жидкости в кубе (регулятор LC2). Тогда единственным регулирующим воздействием при регулировании температуры (состава) кубового потока является изменение расхода теплоносителя, подаваемого в теплообменник.
Проведен анализ статических моделей колонн исследуемых схем, целями которого являлись:
1. Определение чувствительных к возмущающим воздействиям тарелок колонны в плане изменения температуры (состава) на них. Для этого в настоящей работе использованы методы Slope Criterion и Sensitivity Criterion [19].
2. Определение измеряемых величин для выбранных регулируемых параметров, поиск величин, которые могли бы служить заданными значениями для АСР.
При разделении бинарной смеси температура контрольной тарелки однозначно соответствует составу на этой тарелке, тем самым предоставляя возможность использовать значение температуры как задание регулятору, управляющим воздействием которого является расход флегмы, а цель – поддержание требуемого состава дистиллята. Однако, даже в столь простой системе, такой контур АСР способен выдержать только ВВ в виде изменения количества потока питания. Изменение же состава исходной смеси повлечет за собой изменение температурного профиля колонны, делая задание регулятора неактуальным и приводя к ошибкам регулирования. В таких случаях переходят к регулированию по составу [20].
Выбор регулируемого параметра в исчерпывающей секции колонны, делящей многокомпонентную смесь по первому заданному разделению, задача нетривиальная. Возникает проблема отыскания постоянного параметра для обеспечения регулирования. Часто таким показателем становится соотношение тепловой нагрузки куба и потока, поступающего на разделение $\frac{{{{Q}_{{{\text{кип}}}}}}}{{{{G}_{F}}}} = {\text{const}}{\text{.}}$ Однако, при изменении состава потока питания должного управляющего воздействия АСР с заданным значением $\frac{{{{Q}_{{{\text{кип}}}}}}}{{{{G}_{F}}}}$ не обеспечит.
В ходе поиска заданного значения для регулирования исчерпывающей части КЭР при изменении состава питания были обнаружены определенные закономерности (табл. 5). Если относить энергозатраты кипятильника Qкип КЭР не ко всему потоку питания, а только к той его части, которая направится в куб колонны ($G_{F}^{{{\text{Б}} + {\text{Т}}}}~$ – массовый поток бензола и толуола в исходной смеси), то соотношение $\frac{{{{Q}_{{{\text{кип}}}}} \times 0.0036}}{{G_{F}^{{{\text{Б}} + {\text{Т}}}}}},$ где 0.0036 – коэффициент перевода кВт в ГДж/ч, используемые в среде Aspen Dynamics, линейно зависит от концентрации ЦГ в потоке питания как представлено на рис. 3.
Таблица 5.
Зависимость $\frac{{{{Q}_{{{\text{кип}}}}}}}{{G_{F}^{{{\text{Б}} + {\text{Т}}}}}}$ от состава исходной смеси
$X_{{{\text{ЦГ}}}}^{F}$, мас. д. | $G_{F}^{{{\text{Б}} + {\text{Т}}}}$, кг/ч | $\frac{{{{Q}_{{{\text{кип}}}}} \times 0.0036}}{{G_{F}^{{{\text{Б}} + {\text{Т}}}}}} \times {{10}^{{ - 3}}}$ |
---|---|---|
0.10 | 13 500 | 0.405 |
0.11 | 13 350 | 0.415 |
0.12 | 13 200 | 0.425 |
0.13 | 13 050 | 0.435 |
0.14 | 12900 | 0.447 |
Рис. 3.
Зависимость отношения энергозатрат кипятильника КЭР к массовому потоку бензола и толуола в исходной смеси от концентрации ЦГ в исходной смеси.
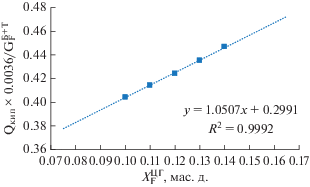
Функция, описывающая линейную зависимость (рис. 3),
(2)
$\frac{{{{Q}_{{{\text{кип}}}}} \times 0.0036}}{{G_{F}^{{{\text{Б}} + {\text{Т}}}}}} = 1.0507X_{{{\text{ЦГ}}}}^{F} + 0.2991$предоставляет возможность применить регулятор с прогнозирующей моделью [17, 21, 22]. Коэффициент $k = 1.0507$ зависимости (2) можно использовать в качестве заданного значения. Поскольку множитель перед аргументом линейной зависимости есть первая производная этой функции, то физический смысл такого регулятора будет в поддержании постоянной скорости изменения $\frac{{{{Q}_{{{\text{кип}}}}}}}{{G_{F}^{{{\text{Б}} + {\text{Т}}}}}}.$
Чтобы организовать такой контур регулирования требуется установка вычислительного устройства (ВУ) на потоке питания, которое по выходным сигналам анализатора содержания циклогексана в исходной смеси QI и измерителя расхода FI будет определять его текущее количество $G_{F}^{{{\text{ЦГ}}}},$ поступающее в колонну. Таким образом значение $G_{F}^{{{\text{Б}} + {\text{Т}}}}$ определится как
Структура регулирования колонны ЭР представлена на рис. 2. Блоки XC6F и ∆ выполняют расчет по уравнению (3) и направляют значение $G_{F}^{{{\text{Б}} + {\text{Т}}}}$ в вычислительное устройство k_calc, рассчитывающее по (2) текущую скорость изменения $\frac{{{{Q}_{{{\text{кип}}}}}}}{{G_{F}^{{{\text{Б}} + {\text{Т}}}}}}.$ Сигнал от ВУ направляется в регулятор K_C и сравнивается с заданным значением k = 1.0507. В случае отклонения текущего значения от заданного, регулятор тепловой нагрузки куба вырабатывает управляющее воздействие в виде изменения расхода греющего пара. Т. к. предложенная АСР – контур с отрицательной обратной связью, применен Closed-loop ATV test по правилу Tyreus–Luyben. Настройки представлены в табл. 6.
Таблица 6.
Настройки АСР схемы П
Обозначение | KP | TИ, мин |
---|---|---|
K_C | 0.2495 | 0.264 |
QC1 | 1590.8 | 71.478 |
TC2 | 0.5573 | 18.414 |
TC3 | 1.886 | 9.702 |
QC2 | 451.4 | 48.84 |
QC3 | 11.11 | 29.96 |
QC4 | 3561.6 | 81.84 |
Применение ВУ открывает еще большие возможности для регулирования состава дистиллята КЭР. Выход блока XC6F, значение которого равно массовому потоку ЦГ в исходной смеси, целесообразно использовать в качестве задания регулятору расхода флегмы. При этом сигнал ВУ необходимо корректировать по составу верхнего продукта колонны с помощью QC1. Данная каскадная система обеспечивает отбор дистиллята заданного качества в соответствии с количеством ЦГ, поступающего в колонну.
Таким образом, АСУ КЭР на рис. 2 состоит из комбинированных АСР с элементами управления по возмущающему воздействию. Достоинством такого принципа является быстродействие, так как возмущающее воздействие может быть скомпенсировано до появления рассогласования между текущим значением регулируемого параметра и его заданным значением.
Далее разработаны контуры регулирования параметров остальных колонн схемы П. За регулирование продуктовых потоков бензола и толуола и потока регенерированного ЭА отвечают каскадные АСР (рис. 2). Регуляторы состава QC вырабатывают управляющее воздействие в виде задания регуляторам температур ТС на контрольных тарелках. Управляющее воздействие – изменение расхода греющего пара в кипятильник колонны. Такие каскадные контуры позволяют сочетать преимущества двух контуров АСР: быстродействие регулирования по температуре и точность управления по составу. Задержки измерения параметров для всех исследуемых схем для температурных контуров составляют 1 минуту, для контуров по составу – 3 минуты. Настройки для вышеуказанных контуров также получены с помощью Closed-loop теста (табл. 6). Колонна регенерации ЭА работает при постоянном флегмовом числе.
В среде моделирования Aspen Dynamics к АСУ схемы П были приложены возмущающие воздействия, получены графики переходных процессов (рис. 4–5), определены их характеристики. По осям ординат графиков отложены концентрации компонентов в соответствующих продуктовых потоках: для бензола и циклогексана ось с заданным значением 99.9 мас. %, для толуола – 99.75 мас. %, для NMP в потоке регенерированного ЭА – 99.99 мас. %.
Рис. 4.
Переходные процессы для составов продуктовых потоков АСУ схемы П. Отклик на изменение расхода потока питания.
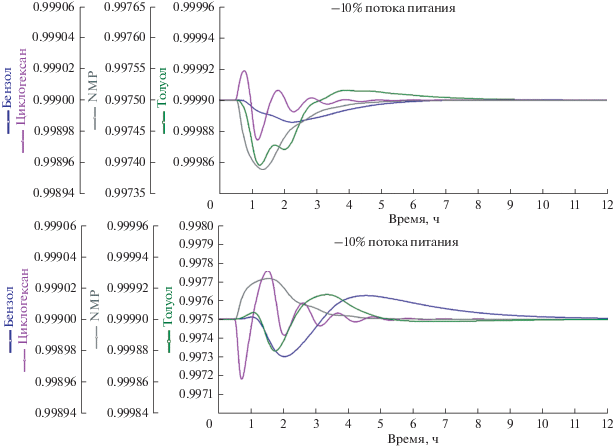
Рис. 5.
Переходные процессы для составов продуктовых потоков АСУ схемы П. Отклик на изменение состава потока питания.
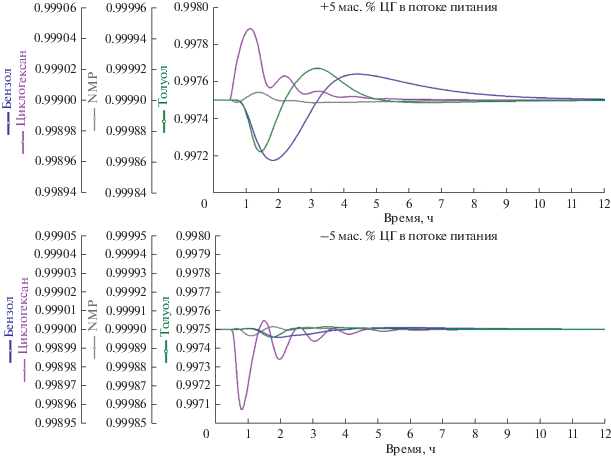
АСУ схемы О.1 . АСУ схемы О.1 представлена на рис. 6. Настройки регуляторов схемы О.1 занесены в табл. 7. АСР на колонне 3, как и сама колонна, полностью идентичны, предложенным для традиционной схемы П.
Рис. 6.
Автоматическая система управления схемы О.1 . КЭР – колонна экстрактивной ректификации; УБС – укрепляющая боковая секция; 3 – колонна разделения бензола и толуола. F – поток питания; NMP – N-метил-2-пирролидон (экстрактивный агент).
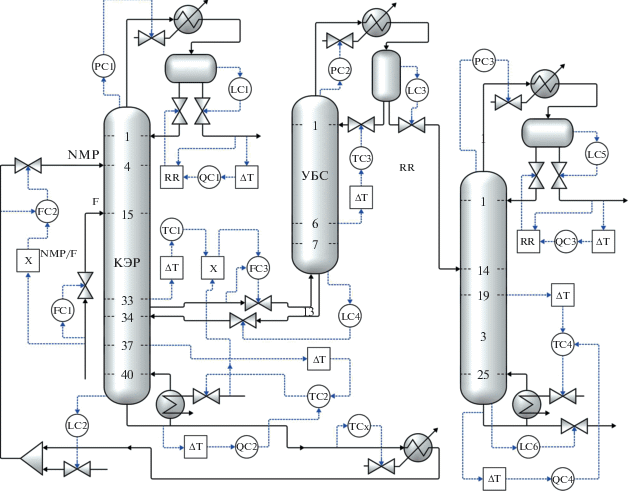
Таблица 7.
Настройки АСР схемы О.1
Обозначение | KP | TИ, мин |
---|---|---|
FC3 | 1.5 | 1.3 |
QC1 | 478.62 | 42.834 |
QC2 | 402.7 | 56.19 |
QC3 | 11.11 | 29.96 |
QC4 | 3561.6 | 81.84 |
TC1 | 792.8 | 45.12 |
TC2 | 2.53 | 22.05 |
TC3 | 1.886 | 9.702 |
Особенностью схемы разделения О.1 является наличие укрепляющей боковой секции (УБС), поток пара в которую генерируется кипятильником КЭР. На этом основана логика регулирования расхода пара в УБС: обеспечить регулирующий вентиль таким управляющим воздействием, которое бы позволило отбирать из основной колонны достаточный для осуществления разделения в УБС поток паровой фазы. При этом тепловой нагрузкой кипятильника решается задача стабилизации состава NMP в потоке регенерированного ЭА с применением каскадного регулирования по температуре и составу (регуляторы TC2 и QC2).
Регулирование расхода пара в УБС реализовано по принципу каскадного комбинированного управления. Управление по отклонению осуществляется блоком FC3, заданием которому служит выход предшествующего блока X, отвечающего за поддержание пропорциональности расхода греющего пара в кипятильник КЭР к расходу пара в УБС. Его значение определяется как расход греющего пара, умноженный на коэффициент пропорциональности. Последний в свою очередь регулируется АСР температуры контрольной тарелки TC1, расположенной выше уровня отбора в УБС.
Среди известных способов стабилизации состава дистиллята боковой укрепляющей секции [19], сделан выбор в пользу регулирования расхода флегмы по температуре контрольной тарелки TC3.
Результаты исследования переходных процессов схемы О.1 занесены в табл. 10.
Выяснено, что схема О.1 не способна выдержать принятые возмущающие воздействия, кроме +10% потока питания. Величина возмущающих воздействий по изменению состава исходной была снижена до ±3 мас. %, по отклонению потока питания в меньшую сторону – до –5%.
АСУ схемы О.2 . Полная схема управления процессом ЭР в схеме с исчерпывающей боковой секцией (ИБС) О.2 приведена на рис. 7, настройки АСР занесены в табл. 8.
Рис. 7.
Автоматическая система управления схемы О.2 . ИБС – исчерпывающая боковая секция; КР – колонна регенерации экстрактивного агента; КЭР – колонна экстрактивной ректификации. F – поток питания; NMP – N-метил-2-пирролидон (экстрактивный агент).
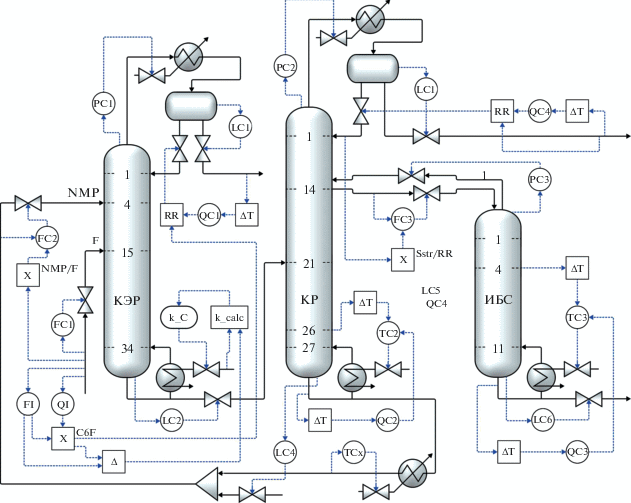
Таблица 8.
Настройки АСР схемы О.2
Обозначение | KP | TИ, мин |
---|---|---|
FC3 | 1.5 | 1.3 |
K_C | 0.2495 | 0.264 |
QC1 | 1590.8 | 71.478 |
QC2 | 2074.7 | 38.28 |
QC3 | 15.8 | 36.89 |
QC4 | 1700.8 | 79.2 |
TC2 | 0.8959 | 15.37 |
TC3 | 1.62 | 10.09 |
В основу регулирования колонны экстрактивной ректификации легла АСУ колонны ЭР схемы-прообраза. Контуры регулирования состава продуктовых потоков бензола и толуола и потока регенерированного ЭА также аналогичны предложенным для схемы-прообраза П.
Особая роль в комплексе с исчерпывающей боковой секцией отведена контролю расхода жидкости в ИБС. Задача регулирования – обеспечить отбор толуола из колонны во избежание его попадания в продуктовый поток бензола.
Блок XSsrt/RR (рис. 7) осуществляет расчет количества бокового отбора на основе его отношения к массовому потоку флегмы колонны. Таким образом, реализуется следующая логика регулирования. Отклонение состава бензола в дистилляте колонны в меньшую сторону возможно только в случае попадания в верх колонны среднекипящего толуола. Тогда АСР QC1 отдаст управляющее воздействие, направленное на увеличение расхода флегмы в колонну, что повлечет за собой увеличение расхода в ИБС и отвод необходимого количества толуола. Значение блока XSsrt/RR служит заданием регулятору расхода FC3.
Давление ИБС регулируется вентилем на потоке пара, направляемого в КР (регулятор PC3).
Данные о качестве переходных процессов представлены в табл. 10.
Было установлено, что схема О.2 при уменьшении концентрации ЦГ в потоке питания на 5 мас. % неспособна обеспечить разделение исходной смеси с заданным качеством продуктовых потоков. С приемлемыми динамическими ошибками и временем регулирования протекают переходные процессы, вызванные изменениями концентрации ЦГ в исходной смеси на –3.5 и +5 мас. %.
АСУ схемы О.3 . Предложенная АСУ процессом ЭР схемы О.3 (рис. 8) состоит из локальных АСР потоков боковых отборов, разработанных для схем О.1 и О.2 . Настройки контуров регулирования занесены в табл. 9, результаты анализа переходных процессов представлены в табл. 10.
Рис. 8.
Автоматическая система управления схемы О.3 . БКЭР – боковая колонна экстрактивной ректификации; ИБС – исчерпывающая боковая секция; ОК – основная колонна. F – поток питания; NMP – N-метил-2-пирролидон (экстрактивный агент).
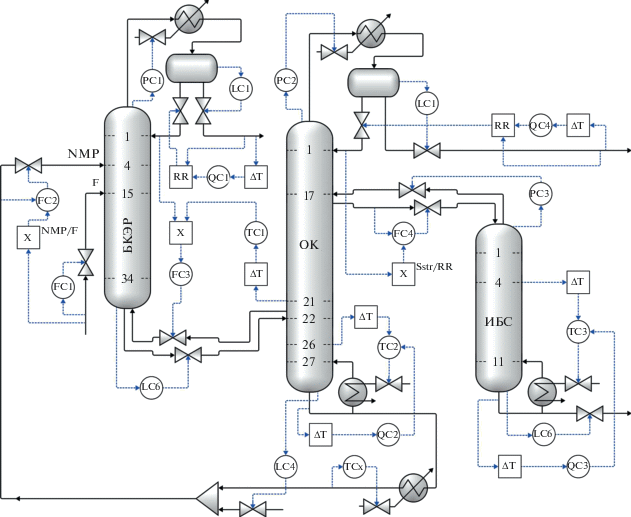
Таблица 9.
Настройки АСР схемы О.3
Обозначение | KP | TИ, мин |
---|---|---|
FC3 | 1.5 | 1.3 |
FC4 | 1.5 | 1.3 |
QC1 | 1737.19 | 88.8 |
QC2 | 2070.7 | 42.72 |
QC3 | 15.8 | 36.89 |
QC4 | 1700.8 | 79.2 |
TC1 | 771.8 | 45.02 |
TC2 | 1.598 | 19.71 |
TC3 | 1.62 | 11.54 |
Таблица 10.
Результаты динамического моделирования исследуемых схем
Схема П | Схема О.1 | Схема О.2 | Схема О.3 | |
---|---|---|---|---|
Qкип.Σ, кВт | 7136 | 7051 | 5559 | 5407 |
Снижение Qкип.Σ относительно схемы П, % | 0 | 1.20 | 28.37 | 31.98 |
Устойчивость к возмущающим воздействиям | ||||
Изменение GF, % | ±10 | +10, –5 | ±10 | ±5 |
Изменение $X_{F}^{{{\text{ЦГ}}}}$, мас. % | ±5 | ±3 | +5, –3.5 | ±2 |
Среднее время регулирования при ВВ по каналу, ч | ||||
Изменение GF | 5.12 | 6.75 | 4.18 | 8.01 |
Изменение $X_{F}^{{{\text{ЦГ}}}}$ | 4.21 | 7.43 | 7.36 | 9.53 |
АСУ схемы О.3 способна обеспечивать адекватное качество переходных процессов при изменении потока питания в пределах ±5% массового расхода от режимного значения и в пределах ±2 мас. % изменения концентрации циклогексана в исходной смеси. Последний переходный процесс отличается стабильностью, маленькими динамическими ошибками и продолжительным временем регулирования.
РЕЗУЛЬТАТЫ И ИХ ОБСУЖДЕНИЕ
Ключевые результаты исследования приведены в табл. 10.
Полученные нами результаты динамического моделирования соотносятся с данными других исследователей [10]. Установлено, что усложнение схемы разделения за счет ее преобразования в комплекс с ЧСТМП приводит к снижению качества регулирования основных технологических величин. Наиболее перспективная в плане энергоэффективности схема разделения О.3 c боковой колонной ЭР и исчерпывающей боковой секцией способна выдерживать наименьшие величины возмущающих воздействий среди всех исследуемых схем.
Интересным результатом является различие в настройках локальных регуляторов для идентичных параметров в различных схемах. Боковые секции в схемах О.2 и О.3 идентичны. Соответственно, идентичны и АСР температуры на контрольной тарелке этих секций TC3. Однако, одинаковыми тестами нами были получены разные значения параметров настройки ПИ-регуляторов. Так для регулятора в схеме О.2 время интегрирования ТИ (время, в течение которого выходная величина регулятора (расход греющего пара) изменяется настолько, насколько изменилась его входная величина – температура 4 тарелки ИБС) составляет 10.09 мин, а для регулятора в схеме О.3 – ТИ = 11.54 мин (табл. 8 и 9, соответственно). Это свидетельствует о более медленном изменении одного и того же параметра при усложнении структуры схемы и, как следствие, о более продолжительном времени регулирования.
Установлено, что схема разделения О.2, включающая комплекс с исчерпывающей боковой секцией, является наиболее устойчивой схемой ЭР с ЧСТМП в плане динамического поведения при наличии внешних возмущающих воздействий. Также следует отметить, что при изменении количества потока питания на ±10% время регулирования для схемы О.2 примерно на 1 ч меньше, чем для схемы П, состоящей из двухотборных колонн.
ЗАКЛЮЧЕНИЕ
В настоящей работе проведены моделирование и оптимизация по критерию суммарных энергетических затрат четырех схем экстрактивной ректификации смеси Б–ЦГ–Т с NMP: традиционной схемы, состоящей из трех двухотборных колонн, и трех схем, включающих комплексы с ЧСТМП. Для каждой схемы разделения разработаны эффективные автоматические системы управления и выполнен анализ устойчивости к внешним возмущающим воздействиям в виде изменения расхода и состава потока питания. Для регулирования качества кубового потока колонны экстрактивной ректификации предложен контур управления с прогнозирующей моделью. Показано, что применение комплексов со связанными тепловыми и материальными потоками позволяет добиться значительного снижения энергозатрат: комплекс, состоящий из основной колонны и термически связанных с ней боковой колонны ЭР и исчерпывающей боковой секции, на 31.98% энергоэффективнее традиционной схемы. Однако схемы, включающие комплексы с ЧСТМП, как объекты регулирования показывают ухудшение динамической устойчивости, и для их промышленного применения необходима разработка сложных систем регулирования. Для комплекса с исчерпывающей боковой секцией, позволяющего снизить энергозатраты на 28.37%, предложена структура автоматического управления, которая обеспечивает сопоставимые с традиционной схемой эффективность регулирования и устойчивость к возмущающим воздействиям.
Работа выполнена при финансовой поддержке Минобрнауки России в рамках государственного задания РТУ МИРЭА, тема № 0706-2020-0020.
ОБОЗНАЧЕНИЯ
∆p | гидравлическое сопротивление тарелки, кПа |
G | массовый расход, кг/ч |
KP | безразмерный коэффициент усиления |
N | общее число тарелок или положение конкретной тарелки |
P | давление, кПа |
Q | тепловая нагрузка, кВт |
T | температура, К |
TИ | интегральное время, мин |
X | концентрация j-го компонента в потоке i, мас. д. или мас. % |
ИНДЕКСЫ
Список литературы
Berg L. Separation of benzene and toluene from close boiling nonaromatics by extractive distillation // AIChE J. 1983. V. 29. № 6. P. 961–966.
Chen B., Lei Z., Li J. Separation on Aromatics and Non-aromatics by Extractive Distillation with NMP. // J. Chem. Eng. JAPAN. 2003. V. 36. № 1. P. 20–24.
Ghaee A., Sotudeh-Gharebagh R., Mostoufi N. Dynamic optimization of the benzene extractive distillation unit // Brazilian J. Chem. Eng. 2008. V. 25. № 4. P. 765–776.
Abushwireb F., Elakrami H., Emtir M. The effect of solvent selection on energy–integrated extractive distillation for aromatics recovery from pyrolysis gasoline: simulation and optimization // Chem. Eng. Trans. 2009. P. 243.
Li W. et al. Separation of benzene and cyclohexane by extractive distillation intensified with ionic liquid // Chem. Eng. Process. – Process Intensif. 2018. V. 126. P. 81–89.
Гайле А.А., Сомов В.Е. Процессы разделения и очистки продуктов переработки нефти и газа: учеб. пособие // СПб.: Химиздат, 2012. 376 с.
Анохина Е.А., Тимошенко А.В., Ребровская А.Е. Энергосберегающие схемы экстрактивной ректификации смеси бензол-циклогексан-толуол с N-метилпирролидоном. Часть 2. Схемы, включающие комплексы с частично связанными тепловыми и материальными потоками // Хим. пром. сегодня. 2015. № 3. P. 47–56.
Петлюк Ф.Б., Серафимов Л.А. Многокомпонентная ректификация. Теория и расчет. М.: Химия, 1983. 303 с.
Gerbaud V. et al. Review of extractive distillation. Process design, operation, optimization and control // Chem. Eng. Res. Des. 2019. V. 141. P. 229–271.
Luyben W.L. Control comparison of conventional and thermally coupled ternary extractive distillation processes // Chem. Eng. Res. Des. 2016. V. 106. P. 253–262.
Ma K. et al. Control of an energy-saving side-stream extractive distillation process with different disturbance conditions // Sep. Purif. Technol. Elsevier B.V. 2019. V. 210, № August 2018. P. 195–208.
Luyben W.L. Control of a distillation column with side stripper and side rectifier // Chem. Eng. Res. Des. Institution of Chemical Engineers. 2020. V. 161. P. 38–44.
Zhang Q. et al. Control comparison of conventional and thermally coupled ternary extractive distillation processes with recycle splitting using a mixed entrainer as separating agent // Sep. Purif. Technol. 2019. V. 224. P. 70–84.
Anokhina E.A., Berdibekova S.A., Timoshenko A.V. Energy saving schemes for separation of benzene-cyclohexane-toluene mixture with different initial compositions by extractive distillation // Chem. Eng. Trans. 2018. V. 69. P. 871–876.
Timoshenko A.V., Morgunov A.V., Anokhina E.A. Flowsheet synthesis for the extractive distillation of azeotropic mixtures in systems consisting of columns with partially coupled heat and material flows // Theor. Found. Chem. Eng. 2007. V. 41. № 6. P. 845–850.
Анохина Е.А., Грачева И.М., Акишин А.Ю., Тимошенко А.В. Разделение смеси ацетон-хлороформ-н-бутанол с применением экстрактивной ректификации в схемах из двухотборных колонн // Тонкие химические технологии. 2017. Т. 12. № 5. С. 34–46.
Беспалов А.В., Харитонов Н.И. Системы управления химико-технологическими процессами. М.: Академкнига, 2007. 696 с.
Полоцкий Л.М., Лапшенков Г.И. Автоматизация химических производств. М.: Химия, 1988. 288 с.
Luyben W.L., Chien I.L. Design and Control of Distillation Systems for Separating Azeotropes // Design and Control of Distillation Systems for Separating Azeotropes. Wiley, 2010.
Голубятников В.А., Шувалов В.В. Автоматизация производственных процессов в химической промышленности. 2nd ed. М.: Химия, 1985. 352 p.
Qian X. et al. Composition/temperature cascade control for a Kaibel dividing-wall distillation column by combining PI controllers and model predictive control integrated with soft sensor // Comput. Chem. Eng. 2019. Vol. 126. P. 292–303.
Mahindrakar V., Hahn J. Model predictive control of reactive distillation for benzene hydrogenation // Control Eng. Pract. 2016. Vol. 52. P. 103–113.
Дополнительные материалы отсутствуют.
Инструменты
Теоретические основы химической технологии