Теоретические основы химической технологии, 2022, T. 56, № 6, стр. 696-704
Пористая структуры ацетиленовой сажи после термообработки
А. О. Дудоладов a, *, А. В. Григоренко a, В. Кумар b, c, М. С. Власкин a, b, c
a Объединенный институт высоких температур Российской академии наук
Москва, Россия
b Университет График Эра, Дехрадун
248002 Уттаракханд, Индия
c Российский университет дружбы народов (РУДН)
117198 Москва, Россия
* E-mail: presley1@mail.ru
Поступила в редакцию 13.05.2022
После доработки 30.06.2022
Принята к публикации 03.07.2022
- EDN: KBRLVY
- DOI: 10.31857/S0040357122060033
Аннотация
Проведено исследование пористой структуры образцов углеродной ацетиленовой сажи, полученных при разложении ацетилена при различных давлениях в трубчатом реакторе постоянного объема и последующей термообработки в инертной среде при температурах 200, 400, 600, 800, 1000, 1200 и 1400°С. Методом низкотемпературной адсорбции получены изотермы адсорбции азота при 77 К, по ним рассчитаны текстурные характеристики сажи. Установлено, что с увеличением давления при разложении чистого ацетилена с 2.5 до 5 бар площадь поверхности ацетиленовой сажи практически не меняется и составляет 88 и 83 м2/г (по БЭТ) соответственно. При этом было замечено, что значения удельной поверхности образцов сажи, полученной при 2.5 бар, в результате термообработки в инертной среде снижаются относительно исходной сажи, которая не подвергалась термообработке. Среднее значение радиуса пор, определенное методом Баррета–Джойнера–Халенды (BJH), не менялось при различных температурах и давлении и составило 1.62 нм. Методом сканирующей электронной микроскопии показано, что средний размер частиц уменьшается с 53 до 40 нм при увеличении начального давления ацетилена. По полученным результатам можно судить о том, что последующая термообработка не приводит к видимому изменению формы и размера частиц, а также общей структуры поверхности сажи. Проведен термогравиметрический анализ (ТГА) исходного образца сажи в инертной среде. Методом ТГА показан прирост массы сажи на 4% при нагреве до 400°С, от 400 до 1150°С вес практически не менялся и далее при нагреве от 1150 до 1400°С вес снижался на 1%.
ВВЕДЕНИЕ
Сажа представляет собой наноразмерные сферические частицы, состоящие из атомов углерода. Технический углерод, получаемый в результате частичного сгорания или термического разложения углеводородов, представляет собой материал, состоящий из более чем 98% углерода. Это число может варьироваться в зависимости от производственного процесса и конечного применения, когда технический углерод может быть легирован другими элементами, такими как кислород, азот или сера, для придания материалу растворимости, лучшей дисперсии или связующих свойств [1]. Сажа имеет множество применений в различных коммерческих и потребительских товарах. Чаще всего ее используют в качестве армирующего агента в автомобильных шинах и резиновых автомобильных изделиях, остальными распространенными областями применения, являются чернила, краски, пластмассы и покрытия. [2]. Кроме того, углеродные сажи обладают электропроводностью и поэтому используются в качестве проводящих добавок для высокопроизводительных аккумуляторных батарей и носителей катализаторов для топливных элементов [3].
В настоящее время подавляющее большинство видов сажи получают печными методом, а некоторые другие – термическим разложением и разложением ацетилена. Печной процесс сажи может производить практически все марки углеродного волокна, используемые в резиновой промышленности. В этом процессе используют печь, где происходит частичное сжигание углеводородного сырья при температуре 1200–1900°С при недостатке воздуха для пиролиза сырья в сажу. Печную сажу получают в виде порошка с очень низкой насыпной плотностью (20–60 г/л), уплотняют или гранулируют для облегчения применения [4]. Термическая сажа производится в инертной атмосфере с использованием низкомолекулярных газообразных углеводородов. Печь нагревается до необходимой температуры (1400°С) при сжигании природного газа на воздухе, при этой температуре поток воздуха прекращается, пропуская только газ, который затем пиролизуется до углерода и водорода.
Производство ацетиленовой сажи намного меньше по масштабам, поскольку ацетилен является дорогим исходным материалом и чаще всего используется только в специализированных процессах. Ацетиленовая сажа является особенной благодаря чистоте углерода (>99%) и проводящим свойствам. Поэтому она необходима для некоторых важных областей применения, которые не могут быть реализованы с печным углеродом. В первую очередь к указанным направлениям относятся такие стратегические отрасли, как производство автономных электрохимических систем генерации и хранения энергии, разработка радиоэкранирующих и радиопоглощающих композиционных полимерных материалов, производство экранированных высоковольтных кабелей, производство аккумуляторов или в качестве проводящего слоя в полимерных смесях [5].
Процесс формирования сажи можно разделить на стадию зарождения и стадию роста. Первичные частицы сажи образуются при укладке относительно хорошо выровненных слоев атомов углерода на внешней поверхности ядра, которое является аморфным [3]. Сажа состоит из частиц, агрегатов и агломератов [1]. Агрегаты представляют собой группу хорошо выровненных частиц, обычно диаметром от 10 до 100 нм, с аморфным ядром, окруженным оболочкой из сложенных графеноподобных доменов. Группы агрегатов объединяются, образуя трехмерную массу, называемую агломератом. Размер и количество частиц, присутствующих в агрегате, определяют его пористую структуру.
Удельная поверхность сырой сажи может быть увеличена за счет активации [6–8]. Поэтому необходимо изучить порообразование и изменение внутренней структуры за счет активации технического углерода. Однако не во многих исследованиях подробно изучалось образование пористой углеродной сажи посредством активации. Авторы исследования [3] ранее сообщали о наличии пор размером 2–5 нм внутри сажи, активированной в воздушной атмосфере, на основании ПЭМ-изображений [9]. Эти поры, образовавшиеся внутри сажи, увеличились в размере примерно до 20 нм по мере дальнейшей активации. Численное моделирование процессов термического пиролиза ацетиленовых смесей в диапазоне температур от 800 до 2000 К и давлениях от 1 до 50 бар показало, что при низких температурах наблюдался значительный, достигающий нескольких секунд период индукции саморазложения ацетилена, предшествующий лавинообразному возрастанию температуры и достижению пиковых концентраций промежуточных соединений, таких как пирен C16H10 и другие полиароматические углеводороды (ПАУ) [10]. Сажа может содержать химически связанные водород, кислород, азот и серу в зависимости от используемого сырья и производственного процесса. Гетероатомы удаляются при термической обработке при высокой температуре в инертной атмосфере (карбонизация). Увеличение размеров двумерно-упорядоченных доменов и формирование трехмерной упорядоченности (графитизации) наблюдается выше 2000°С, тогда как аморфное ядро в лучшем случае преобразуется в микропористую структуру, состоящую из искривленных углеродных листов при температуре 3000°С и выше [11]. Таким образом, можно предполагать, что термическая обработка сажи может существенно влиять на ее текстурные характеристики. Поэтому исследования пористой структуры сажи после ее термической обработки представляются вполне целесообразными. В связи с этим в данной работе было предложено исследование возможного изменения пористой структуры ацетиленовой сажи в результате ее термической обработки в трубчатой печи в инертной атмосфере при температурах 200, 400, 600, 800, 1000, 1200 и 1400°С.
Целью данной работы является изучение основных параметров пористой структуры ацетиленовой сажи, получаемой в результате разложения ацетилена в постоянном объеме с искровым поджигом в зависимости от начального давления ацетилена в реакторе и температуры последующей термообработки сажи в инертной атмосфере.
ЭКСПЕРИМЕНТАЛЬНАЯ ЧАСТЬ
Реактивы и материалы. При проведении экспериментов использовались следующие реактивы и материалы:
• Растворенный ацетилен марки “А” (объемная доля ацетилена не менее 99.5%)
• Реактор, изготовленный из нержавеющей стали (12Х18Н10Т) с внутренним диаметром 25 мм и длиной – 520 мм
• Реакция разложения ацетилена инициируется искрой от штатной свечи зажигания двигателя внутреннего сгорания (ДВС)
• Устройство поджига дуги для инициации искры с энергией 0.3 Дж на штатной свече ДВС
• Аргон марки ВЧ (объемная доля аргона не менее 99.998%)
• Трубчатая муфельная печь.
Методика проведения экспериментов по синтезу ацетиленовой сажи. В экспериментах использовался: ацетилен марки А с чистотой 99.5%. Схема установки для получения сажи представлена на рис. 1. Процесс разложения происходит в реакторе, представляющем собой сосуд из нержавеющей стали марки 12X18H10T. В экспериментах использовался реактор с внутренним диаметром 25 мм и длиной – 520 мм. Заправка газом из баллона осуществляется через игольчатые вентиль. Давление газа контролируется при помощи манометра на редукторе. Реакция разложения инициируется искрой от свечи зажигания. Энергия свечи составляет 0.3 Дж. Свеча подсоединена к устройству поджига дуги. Наличие искры контролируется при помощи окна с кварцевым стеклом. Выпуск продуктов реакции осуществляется при помощи шарового крана.
Рис. 1.
Схема экспериментальной установки для термического разложения ацетилена в условиях постоянного объема: 1 – баллон с ацетиленом; 2 – баллон с аргоном; 3, 4 – редуктор; 5, 6, – игольчатый вентиль; 7 – реактор; 8, 9 – свеча зажигания; 10 – устройство поджига дуги; 11 – ключ коммутационный; 12 – окно с кварцевым стеклом; 13 – шаровой кран.
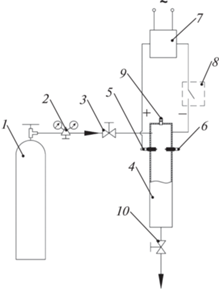
В экспериментах по разложению ацетилена сначала реактор продувается газом из баллона через игольчатый вентиль и открытый шаровой кран для удаления из системы воздуха. Затем шаровой кран закрывается, и реактор наполняется газом из баллона до давления 2.5 и 5 бар. Затем устройство поджига дуги одним проводом соединяется с одной из свечей зажигания, а другим подсоединяется к корпусу стального сосуда, а само устройство поджига дуги запитывается от сети переменного тока 220 В.
Далее подключается устройство поджига дуги, и через окно с кварцевым стеклом наблюдается искра. Если происходит разложение ацетилена, то через окно с кварцевым стеклом наблюдается ярко красная вспышка. После разложения ацетилена открывается шаровой кран, через который осуществляется вывод продуктов реакции (газообразных продуктов и сажи). В конце каждого эксперимента, в котором произошло разложение ацетилена, установка разбирается и очищается от образовавшейся внутри нее сажи.
Далее полученную сажу подвергали термообработке в трубчатой печи в интервале температур 200–1400°С со скоростью нагрева 5°С/мин в атмосфере аргона. Обозначения образцов и температура отжига приведены в табл. 1.
Таблица 1.
Обозначения образцов
Образец | Давление ацетилена при синтезе, бар | Температура термообработки, °С |
---|---|---|
PA01 | 2.5 | – |
PA03 | 2.5 | 200 |
PA04 | 2.5 | 400 |
PA05 | 2.5 | 600 |
PA06 | 2.5 | 800 |
PA07 | 2.5 | 1000 |
PA08 | 2.5 | 1200 |
PA09 | 2.5 | 1400 |
PA02 | 5 | – |
PA10 | 5 | 200 |
PA11 | 5 | 400 |
PA12 | 5 | 600 |
PA13 | 5 | 800 |
PA14 | 5 | 1000 |
PA15 | 5 | 1200 |
PA16 | 5 | 1400 |
Методика проведения экспериментов по термической обработке сажи в трубчатой печи в среде инертного газа. В экспериментах для создания инертной среды использовался: аргон марки ВЧ с чистотой 99.998%. Схема экспериментальной установки по термической обработке сажи в трубчатой печи при различных температурах в среде инертного газа представлена на рис. 2.
Рис. 2.
Схема экспериментальной установки для термической обработки сажи в инертной среде: 1 – баллон с аргоном, 2 – редуктор, 3, 13 – вентиль, 4 – ротаметр, 5 – муфельная печь, 6 – муфель, 7 – нагреватели, 8 – корундовая труба, 9 – корундовый тигель-лодочка, 10 – сажа, 11, 12 – фланец, 14 – барботер.
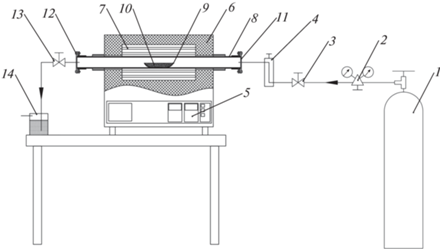
Основным элементом установки для термической обработки сажи является трубчатая муфельная печь (5). Труба печи (8) и тигель-лодочка (9) изготовлены из корунда (Al2O3) с чистотой не менее 99%. Корундовая труба (8) имеет следующие параметры: длина 1.5 м; внешний диаметр 6 см; внутренний диаметр 5 см. Для создания инертной атмосферы в трубе (8) из баллона с аргоном (1), через редуктор (2), вентиль (3) и ротаметр (4) газ поступает во внутреннюю поверхность трубы (8). Концы трубы (8) герметизируются фланцами (11) и (12) имеющие входные и выходные штуцера. Газ, выходя из трубы (8) проходит вентиль (13) и барботер (14) наполненный водой, и далее выбрасывается в атмосферу.
Образец сажи (10) в количестве 2 грамм помещается в корундовый тигель-лодочку (9) и далее помещается в центр корундовой трубы (8) печи (5). Концы корундовой трубы (8) герметизируются фланцами (11) и (12). Далее производится продувка корундовой трубы (8) инертным газом из баллона (1) со скоростью 1 л/мин в течение 10 мин для того, чтобы полностью вытеснить воздух из корундовой трубы. Скорость потока инертного газа задается ротаметром (4). Газ, выходя из корундовой трубы (8), пропускался через барботер (14). После продувки корундовой трубы (8) запускался нагрев печи (5) до заданной температуры встроенным ПИД регулятором со скоростью 5°С/мин. Поток инертного газа через корундовую трубу (8) из баллона (1) продолжается в течение всего эксперимента. После достижения заданной температуры в печи (5), сажа (10) в корундовом тигле-лодочке выдерживалась при этой температуре в течение 60 мин. По прошествии 60 мин нагрев трубчатой печи (5) выключался и печь остывала до комнатной температуры. После остывания печи (5) до комнатной температуры продувка инертным газом из баллона (1) прекращалась путем закрытия вентиля (3). Далее производилась разгерметизация корундовой трубы (8) путем снятия фланца (11) и выемка образца сажи (10) в корундовом тигле-лодочке (9) из корундовой трубы (8) для его дальнейшего исследования.
Методы исследования образцов сажи. Определение структурно-энергетических характеристик образцов сажи проводили по изотермам адсорбции азота при 77 K, снятым на объемной установке Nova 2200е (Quantachrome, США). Перед измерением изотерм проводили дегазацию образцов при 120°С и остаточном давлении 10–3 мм рт. ст. в течение 3 ч. Удельную поверхность (Sуд) образцов рассчитывали по уравнению БЭТ, объем микропор (Wo) по уравнению Дубинина–Астахова. Суммарный сорбционный объем мезо- и микропор (Vобщ) определяли по изотерме адсорбции азота при значении относительного давления, равном 0.995. Распределение пор (Rср) по размеру определяли методом BJH по десорбционной ветви.
Морфология поверхности образцов изучалась на растровом электронном микроскопе Nova NanoSem 650 с использованием кольцевого детектора обратно рассеянных электронов, позволяющего получать на рельефных поверхностях контраст по средним атомным номерам элементов микроструктуры. Образцы крепились к столику микроскопа с помощью электропроводящей ленты. Образцы не были покрыты проводящим покрытием, чтобы избежать возможного экранирования наноразмерных объектов. Сканирование осуществлялось вторичными электронами с ускоряющими напряжениями 2 и 3 кВ. Чтобы уменьшить неизбежную зарядку образцов электронным зондом, изображения SEM были получены путем многократного сканирования с использованием режима “коррекции дрейфа”.
ИК-спектры регистрировались с помощью Фурье-ИК-спектрометра Nicolet 380 (Thermo Fisher Scientific Inc., США) в диапазоне 4000–500 см–1. Перед записью спектров порошок сажи смешивали с KBr и прессовали в таблетки.
Для оценки изменения массы сажи при нагреве в инертной среде был проведен ТГА на термическом анализаторе STA PT1600 (Linseis Messgeraete GmbH). Образец сажи в количестве около 40 мг помещался в корундовый тигель. Нагрев тигля осуществлялся в среде аргона. Скорость нагрева до температуры 1400°С составляла 5°С/мин.
РЕЗУЛЬТАТЫ И ОБСУЖДЕНИЯ
Для обозначения функциональных групп, находящихся на поверхности ацетиленовой сажи, были сняты инфракрасные спектры, как показано на рис. 3. Пик 1536 см–1 соответствует колебанию С–С. Кроме того, широкий резонансный пик, расположенный в области 2900–3000 см–1, свидетельствует о наличии гидроксильных групп. Пик при 1730 см–1 приписываются колебаниям карбонильных групп C=O. Различие между образцами, полученными при разных давлениях ацетилена, заключаются в пиках в области 2350 см–1, которые характерны для CO2 [12–14], эти пики характерны только для образцов, полученных при 2.5 бар.
Рис. 3.
ИК-спектры образцов сажи. PA01 и PA02 – образцы сажи, полученные при разложении ацетилена при начальном давлении 2.5 и 5 бар соответственно, PA09 и PA16 образцы сажи, полученные в результате термообработки в среде аргона при температуре 1400°С из образцов PA01 и PA02 соответственно. (На рисунке PA01 – 4, PA02 – 2, PA09 – 3, PA16 – 1).
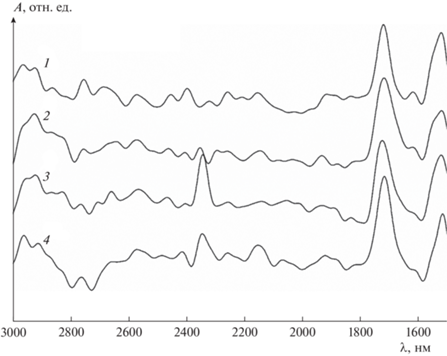
На рис. 4 и 5 показаны изображения, полученные на сканирующем электронном микроскопе для исходных образцов сажи и для образцов сажи, обработанных при 1400°С. Изображения показывают, что структурные единицы ацетиленовой сажи четко различимы. Средний размер частиц исходной сажи, полученной при 2.5 бар составляет около 53 нм, при 5 бар – около 40 нм.
Рис. 4.
СЭМ-снимки образца PA01 и PA02. PA01 и PA02 – образцы сажи, полученные при разложении ацетилена при начальном давлении 2.5 и 5 бар соответственно.
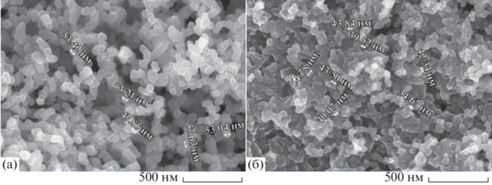
Рис. 5.
СЭМ-снимки образца РА09 и РА16. PA09 и PA16 образцы сажи, полученные в результате термообработки в среде аргона при температуре 1400°С из образцов PA01 и PA02 соответственно.
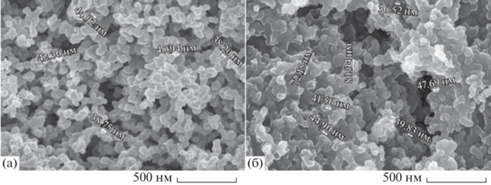
На полученных изображениях видно, что при термообработке средний размер частиц существенно не меняется. При этом можно сказать, что применяемая термообработка не влияет также на форму частиц, а также на общую структуру поверхности.
В ходе работы были получены изотермы адсорбции азота для всех образцов сажи. На рис. 6 представлены изотермы адсорбции–десорбции азота для образцов сажи полученной при давлении ацетилена 2.5 бар (РА01) и 5 бар (РА02) и образцов, полученных их отжигом при температуре 1400°С (РА09 и РА16 соответственно). Видно, что изотермы как для первой, так и второй серии образцов сажи имеют типичную форму изотермы IV типа [15]. По полученным изотермам адсорбции были рассчитаны текстурные характеристики образцов, полученные результаты приведены в табл. 2.
Рис. 6.
Изотерма адсорбции азота при 77 К исходных образцов сажи, полученной при давлении ацетилена 2.5 бар (РА01) и 5 бар (РА02) и образцов, полученных их отжигом при температуре 1400°С (РА09 и РА16 соответственно).
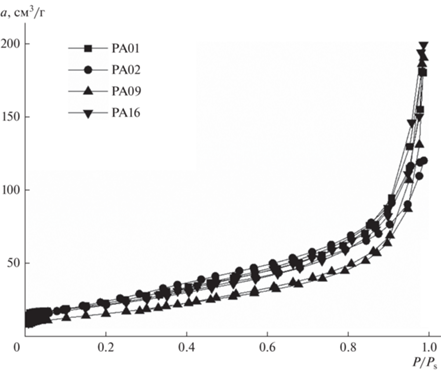
Таблица 2.
Текстурные характеристики образцов сажи. Sуд, Wo, Vобщ, Rср (BJH)
Образец | Sуд (БЭТ), м2/г | Wo, см3/г | Vобщ, см3/г | Rср (BJH), нм |
---|---|---|---|---|
PA01 | 88 | 0.03 | 0.28 | 1.62 |
PA03 | 59 | 0.02 | 0.23 | 1.62 |
PA04 | 45 | 0.01 | 0.22 | 1.62 |
PA05 | 65 | 0.02 | 0.28 | 1.62 |
PA06 | 64 | 0.02 | 0.28 | 1.63 |
PA07 | 61 | 0.02 | 0.30 | 1.62 |
PA08 | 50 | 0.01 | 0.30 | 1.61 |
PA09 | 61 | 0.02 | 0.29 | 1.62 |
PA02 | 83 | 0.03 | 0.29 | 1.62 |
PA10 | 91 | 0.03 | 0.33 | 1.62 |
PA11 | 89 | 0.03 | 0.30 | 1.62 |
PA12 | 84 | 0.03 | 0.33 | 1.62 |
PA13 | 86 | 0.03 | 0.31 | 1.62 |
PA14 | 89 | 0.03 | 0.35 | 1.62 |
PA15 | 84 | 0.03 | 0.34 | 1.62 |
PA16 | 80 | 0.03 | 0.31 | 1.62 |
При том, что значение удельной поверхности исходных образцов сажи близки и составляют 88 и 83 м2/г для 2.5 и 5 бар соответственно, термообработка приводит к различному поведению серий образцов. В первой серии при термообработке величины удельной поверхности снижаются, тогда как при увеличении давления при разложении ацетилена, удельная поверхность образцов сажи, полученных в результате термообработки, остается практически неизменной.
Объемы пор (Vобщ) изменились незначительно. По-видимому, и удельная поверхность, и объем пор меняются исключительно из-за разницы в размерах и форме углеродных агрегатов и агломератов.
Полученные результаты говорят о том, что отжиг и его температура в целом имеют слабое влияние на текстурные характеристики сажи. Для образцов сажи, полученных путем термической обработки исходной сажи, полученной при разложении ацетилена при давлении 2.5 бар, минимальное и максимальное значение удельной поверхности получено для образцов сажи отожженных в инертной среде при температурах 400 и 600°С соответственно. Для образцов сажи, полученных путем термической обработки исходной сажи, полученной при разложении ацетилена при давлении 5 бар, минимальное и максимальное значение удельной поверхности получено для образцов сажи отожженных в инертной среде при температурах 1400 и 200°С соответственно.
Распределение объема пор по размеру приведены на рис. 7. Среднее значение радиуса пор, определенное методом BJH, составило 1.62 нм. Как видно из полученных данных, температура термообработки существенно не влияет на текстурные характеристики полученных образцов сажи. Зарегистрированные изменения находятся в рамках погрешности.
Рис. 7.
Распределение объема пор по размерам методом BJH для образцов сажи, полученных при разложении ацетилена при давлении 2.5 бар (слева) и 5 бар (справа).
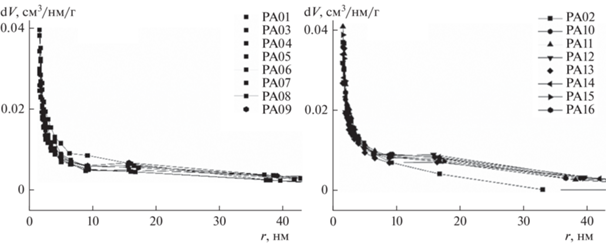
Проведен ТГА анализ исходных образцов сажи РА01 и РА02 в инертной среде. На рис. 8 представлен график ТГА термообработки образца сажи PA01. График ТГА образца сажи РА02 имеет схожий вид.
Результат ТГА эксперимента показал, что в результате нагрева образца ацетиленовой сажи PA01 в инертной среде до 400°С вес сажи увеличивается приблизительно на 4%, что вероятно может быть связано с наличием связанного водорода в ее структуре, который в процессе нагрева высвобождается из структуры сажи. В результате того, что из образца сажи уходит легкий газ, вес образца увеличивает. При нагреве от 400 до 1150°С вес сажи практически не меняется, а при нагреве от 1150 до 1400°С вес падает приблизительно на 1%, что в свою очередь может быт связано с разрушением ПАУ структур. При этом на пористую структуру образцов ацетиленовой сажи, как показали представленные выше результаты, значительного влияния это не оказывает.
ЗАКЛЮЧЕНИЕ
Таким образом, по результатам проведенных исследований можно сделать вывод, что дополнительная термообработка при температуре в интервале 200–1400°C существенно не влияет на текстурные характеристики ацетиленовой сажи, полученной в результате разложения ацетилена в постоянном объеме с искровым поджигом. Наиболее существенным образом изменяется удельная поверхность образцов сажи, полученных при давлении 2.5 бар, относительно сажи, которая не подвергалась термообработке в инертной среде. В остальных случаях изменения носят незначительны характер. Для образцов сажи полученных путем термообработки сажи, полученной при давлении 2.5 бар, получены Sуд по БЭТ от 45 до 65 м2/г. Для образцов сажи полученных путем термообработки сажи, синтезированной при давлении 5 бар, Sуд по БЭТ составила от 80 до 91 м2/г.
Работа выполнена при поддержке Российского научного фонда (соглашение № 21-19-00390, https://rscf.ru/project/21-19-00390/).
ОБОЗНАЧЕНИЯ
T | температура, °C, К |
P | давление, бар |
r | радиус пор, нм |
d | средний размер частиц, нм |
Δm | изменение массы, % |
D | диаметр, мм, см |
L | длина, мм, м |
Е | энергия, Дж |
U | напряжение, В |
ϑ1 | скорость нагрева, °С/мин |
ϑ2 | скорость продувки газа, л/мин |
Sуд | удельная поверхность, м2/г |
Wo | объем микропор, см3/г |
Vs | суммарный сорбционный объем мезо- и микропор, см3/г |
Rср | среднее значение радиуса пор, нм |
m | масса образца, мг |
ИНДЕКСЫ
Список литературы
Singh M., Vander Wal R.L. Nanostructure Quantification of Carbon Blacks // J. Carbon Res. 2019. V. 5(1). P. 2.
Ahmadzadeh Tofighy, Maryam, Mohammadi Toraj. Barrier, Diffusion, and Transport Properties of Rubber Nanocomposites Containing Carbon Nanofillers // Fundamentals and Applications. 2019. P. 253.
Lee SM., Lee SH., Kim SH. et al. Analysis of pore formation and development in carbon blacks activated in a CO2 gas atmosphere through microstructural observation // Carbon Lett. 2021. V 31. P. 1317.
Voll M., Kleinschmit P. Carbon, 6. Carbon Black / In Ullmann’s Encyclopedia of Industrial Chemistry, (Ed.). 2010.
Surovikin Yu.V., Shaitanov, A.G., Lavrenov A.V., Shlyapin D.A. New approaches to the production of acetylene carbon black // AIP Conference Proceedings. 2020. 2301. 040015. [Суровикин Ю.В., Шайтанов А.Г., Лавренов А.В., Шляпин Д.А. Новые подходы к производству ацетиленовой сажи // Материалы конференции AIP. 2020. 2301. 040015.]
Park S.M., Yasuda E., Park Y.D. The influence of graphitic structure on oxidation reaction of carbon materials // J. Korean Ceram Soc. 1996. V. 33. P. 816.
Walker P.L. Jr, Rusinko F. Jr, Austin L.G. Advances in catalysis: gas reactions of carbon // Academic Press. 1959. V. 11. P. 133.
Kinoshita K. Carbon: electrochemical and physicochemical properties / Electrochim Acta. 1989. V. 34. P. 593–594.
Lee S.M., Lee J.H., Nam G., Kim S.H., Kim J., Roh J.S. Surfaces hape and pore size change in carbon blacks isothermally oxidized in air atmosphere according to burn-off ratio // Carbon Lett 2019. V. 29. P. 613.
Cuoci A., Frassoldati A., Faravelli T., Ranzi E. OpenSMOKE++: An object-oriented framework for the numerical modeling of reactive systems with detailed kinetic mechanisms // Comput Phys Commun. 2015. V. 192. P. 237.
Khodabakhshi, Saeid, Fulvio, Pasquale, Andreoli, Enrico. Carbon black reborn: Structure and chemistry for renewable energy harnessing // Carbon. 2020. V. 162. P. 604.
Zu C., Su Y.-S., Fu Y. Improved lithium–sulfur cells with a treated carbon paper interlayer // Phys. Chem. Chem. Phys. 2013. V. 15. P. 2291.
Miao L.-X., Wang W.-K., Wang M.J., Wang A.-B., Yuan K.-G., Yang Y.-S. Carbyne polysulfide as a novel cathode material for lithium/sulfur batteries // J. Mater. Chem. A. 2013. V. 1. P. 11659.
Jin G., Mingang Z., Shijian Y., Xiaoyan Y., Shiwei W. Electrochemical properties of modified acetylene black/sulfur composite cathode material for lithium/sulfur batteries // Ionics. 2018. V. 24. P. 2219.
Kruk M., Jaroniec M. Gas adsorption characterization of ordered organic–inorganic nanocomposite materials // Chem. Mater. 2001. V. 13. P. 3169.
Дополнительные материалы отсутствуют.
Инструменты
Теоретические основы химической технологии