Поверхность. Рентгеновские, синхротронные и нейтронные исследования, 2023, № 2, стр. 23-32
Ядерно-физическое исследование состава поверхностных слоев быстро затвердевших фольг сплава Al–Mg–Li–Sc–Zr после термообработки
И. А. Столяр a, *, В. Г. Шепелевич a, И. И. Ташлыкова-Бушкевич b, **, E. Wendler c
a Белорусский государственный университет
220050 Минск, Беларусь
b Белорусский государственный университет информатики и радиоэлектроники
220013 Минск, Беларусь
c Friedrich-Schiller-Universität Jena
07743 Jena, Germany
* E-mail: uyluana@gmail.com
** E-mail: iya.itb@bsuir.by
Поступила в редакцию 26.06.2022
После доработки 22.07.2022
Принята к публикации 22.07.2022
- EDN: DTKBFU
- DOI: 10.31857/S1028096023020139
Аннотация
Исследовано влияние термообработки на распределение лития по глубине поверхностных слоев быстро затвердевших фольг промышленного сплава Al–Mg–Li–Sc–Zr (1421), полученных сверхбыстрой закалкой из жидкой фазы методом одностороннего охлаждения на внутренней поверхности вращающегося медного цилиндра. Методом дифракции обратно отраженных электронов определено, что свежезакаленные фольги имеют микрозеренную структуру с размером зерна в среднем 12 мкм и текстуру [111]. С помощью атомно-силовой микроскопии получено, что свободная поверхность фольг характеризуется мелкоячеистой структурой, которая также наблюдается в области каверн и впадин на контактной стороне. Шероховатость поверхности фольг составляет от 44 до 56 нм. Закономерности глубинного распределения лития в отожженных образцах установлены методом мгновенных ядерных реакций с использованием ядерной реакции на протонах (p, α). Получено, что при низкотемпературном отжиге поверхностные и глубинные слои образцов обеднены литием, который распределен по глубине фольг равномерно. Обнаруженное в приповерхностной области фольг кратное повышение концентрации лития установлено при высокотемпературном отжиге, приводящем к формированию градиентной по составу структуре фольг. Обсуждается влияние структурно-фазовых изменений, обусловленных распадом пересыщенного твердого раствора с выделением литийсодержащих фаз, на поведение лития в интервале температур отжига 150–380°С.
ВВЕДЕНИЕ
Основными промышленными потребителями алюминий-магниевых сплавов являются порошковая металлургия, машиностроение, приборостроение и предприятия, создающие авиакосмическую технику, для которых важно улучшение динамических характеристик изделий и снижение расхода топлива благодаря увеличению весовой эффективности. Двойные сплавы Al–Mg – это основа термически не упрочняемых сплавов серии 5XXX по международной классификации [1] (по отечественной классификации сплавы типа АМг). Добавка к магнийсодержащим алюминиевым сплавам лития, который является самым легким металлом, несмотря на усложнение технологии выплавки изделий из-за химической неоднородности слитков, приводит к значительному снижению плотности и увеличению модуля Юнга изделий. Повышение уровня механических свойств сплавов, в том числе прочности, достигается за счет выделения в ходе термической обработки упрочняющих метастабильных фаз с литием – δ' (Al3Li) и S1 (Al2LiMg) [2, 3].
Поскольку современный уровень развития авиационной промышленности предъявляет возрастающие требования к эксплуатационным характеристикам промышленных сплавов на основе системы Al–Mg–Li в условиях повышенных температур и влажности, для улучшения комплекса уникальных свойств, которыми они обладают, целесообразно использовать легирование редкоземельными и переходными металлами. Например, среди достоинств многокомпонентных сплавов системы Al–Mg, легированных скандием совместно с цирконием, который замещает часть дорогостоящего скандия, выделяют высокие пластичность и термостабильность дисперсоидов при высокой коррозионной стойкости, умеренной прочности и хорошей свариваемости [4–6]. Однако многие из легирующих компонентов промышленных алюминиевых сплавов в равновесных условиях малорастворимы в алюминии. Поэтому для расширения номенклатуры изделий из магнийсодержащих алюминиевых сплавов активно ведется поиск ресурсосберегающих технологий синтеза сплавов Al–Mg разных систем легирования и оптимальных режимов упрочняющей термообработки [4, 7, 8], решающих проблему отрицательного влияния температурных воздействий на физико-механические и химические свойства материалов. В частности, дополнительное легирование магнийсодержащих алюминиевых сплавов редкоземельными и переходными металлами особенно эффективно при высокоскоростной кристаллизации [1, 9]. В быстро затвердевших материалах модифицирование структуры [10] обеспечивается за счет образования аномально пересыщенных твердых растворов, диспергирования структурных составляющих и формирования метастабильных промежуточных фаз.
Для промышленного использования быстро затвердевших сплавов требуется глубокое понимание структурно-фазовых превращений, происходящих при термообработке, и их влияния на свойства сплавов. Полученные ранее экспериментальные данные [11, 12] указывают на перспективы улучшения свойств сплавов системы Al–Mg–Li в результате высокоскоростной кристаллизации. Особый интерес представляет обнаруженный эффект влияния формирования метастабильной Li-содержащей фазы переменного состава Al(Mg,Sc,Zr,Li)x при температурах около 300°C на механические свойства быстро затвердевших фольг промышленного сплава Al–Mg–Li–Sc–Zr (1421), поскольку эта температура удовлетворяет условиям эксплуатации при повышенных температурах и близка к температуре, оптимальной для получения массивных изделий путем компактирования быстро затвердевших образцов. Поэтому научно-практический интерес представляет детальное изучение зависимости микроструктуры и элементного состава приповерхностных слоев быстро затвердевшего сплава Al–Mg–Li–Sc–Zr от температуры отжига для определения структурно-фазовой стабильности материала. Как известно, значительное влияние на свойства материалов на основе алюминия оказывает защитная оксидная пленка, в формировании которой в случае сплава 1421 участвует также и литий. Его поведение недостаточно изучено в многокомпонентных алюминиевых сплавах, подвергнутых термообработке. В частности, профилирование лития по глубине в алюминиевых сплавах невозможно выполнить с помощью традиционных методов, например, рентгеноспектрального микроанализа. Альтернативно применяемые методы измерения микротвердости или электросопротивления [13–15] также не позволяют получить однозначную количественную информацию о содержании лития в поверхностных слоях и на глубине сплавов до и после отжига.
Целью настоящей работы было ядерно-физическое изучение состава поверхностных слоев быстро затвердевших фольг сплава Al–Mg–Li–Sc–Zr после термообработки. Комплексное исследование структуры поверхности образцов проводили методами атомно-силовой микроскопии (АСМ), дифракции обратно рассеянных электронов и спектрометрии частиц-продуктов ядерных реакций. Использование АСМ для микроструктурных исследований, визуализации и классификации морфологии поверхности свежезакаленных образцов, а также дополнительное применение дифракции обратно рассеянных электронов позволяет без предварительной подготовки фольг изучить их зеренную структуру. Важным преимуществом ядерно-физического метода мгновенных ядерных реакций является то, что с его помощью можно решить проблему обнаружения и количественного измерения профилей распределения по глубине фольг такого легкого элемента, как литий, в зависимости от условий термообработки алюминиевого сплава. Кроме того, данный метод является неразрушающим и характеризуется высоким разрешением и точностью.
МЕТОДИКА ЭКСПЕРИМЕНТА
Фольги алюминиевого промышленного сплава 1421 (Al–5.8 ат. % Mg–8.1 ат. % Li–0.03 ат. % Zr–0.11 ат. % Sc) получали методом высокоскоростной кристаллизации из расплава на внутренней поверхности вращающегося медного цилиндра диаметром 20 см. При скорости вращения цилиндра 1500 об./мин скорость охлаждения расплава составила порядка 106 К/с [16]. Толщина исследуемых фольг была 60–80 мкм. Считали, что сторона А – контактная поверхность фольг, прилегающая к медному цилиндру, сторона Б – свободная поверхность фольг, контактирующая с воздухом. Изотермический отжиг фольг проводили при температурах 150, 220, 300 и 380°С, выдерживая 1 ч при каждой температуре.
Морфологию поверхности свежезакаленных фольг изучали с использованием атомно-силового микроскопа NT-206 в контактном режиме с последующей обработкой изображений размером 20 × 20 мкм с помощью программ SurfaceXplorer и SurfaceView (ОДО “Микротестмашины”, Беларусь [17]). Картины дифракции обратно рассеянных электронов для анализа зеренной структуры фольг были получены в растровом электронном микроскопе марки LEO1455VP с приставкой HKL CHANNEL5 при ускоряющем напряжении 20 кВ с использованием EBSD-детектора. Шаг сканирования составлял 2 мкм. Количественный анализ зеренной структуры был выполнен методом секущих с помощью математического пакета OriginPro.
Для изучения перераспределения лития в фольгах сплава 1421 при термообработке применяли метод мгновенных ядерных реакций с использованием ядерной реакции 7Li(p,α)4He при облучении свежезакаленных и отожженных фольг ускоренными протонами с энергией 1.4 МэВ. Измерения выполняли на ускорителе-тандентроне (3МВ) JULIA (Jena University Laboratory for Ion Acceleration) с разрешением детектора 15 кэВ. Детектор в экспериментах находился под углом θ = = 170°. Диаметр падающего на мишень пучка составлял 1 мм. Полученные спектры частиц были нормализованы на высоту выхода обратно рассеянных протонов в левой границе спектра, т.е. в наименьшем канале низкоэнергетической области спектра. Тестовые опыты [18], проведенные методом мгновенных ядерных реакций с образцом из ниобата лития (LiNbO3), содержащего 20 ат. % лития, позволили с применением компьютерной программы SIMNRA [19] для обработки спектров определить концентрацию лития в фольгах с погрешностью 11%. Методология обработки экспериментальных спектров обратно рассеянных протонов и α-частиц, образующихся в результате ядерной реакции (p, α), описана ранее в [12]. Глубина анализа распределения лития по толщине фольг составила 22 мкм.
РЕЗУЛЬТАТЫ И ИХ ОБСУЖДЕНИЕ
На рис. 1а, 1б показаны типичные двумерные топографические изображения поверхностей свежезакаленных фольг сплава 1421. Геометрические характеристики ансамбля шероховатостей обеих поверхностей подобны. Высота пиков на отдельных участках поверхности А может составлять 200 нм, а глубина впадин – 160 нм (рис. 1в). С противоположной стороны максимальный перепад рельефа на отдельных участках поверхности Б достигает ~270 нм (рис. 1г). Обе поверхности А и Б характеризуются ячеистой структурой: на поверхности А ячейки присутствуют в области впадин и воздушных каверн, а на поверхности Б – на всей изученной площади поверхности. Размер ячеек на стороне А достигает 4 мкм, уменьшаясь до 1 мкм на стороне Б. Искажения изображения в виде белых точек (рис. 1б) учитывали, как артефакты взаимодействия зонда с поверхностью и исключали из анализа с помощью стандартных алгоритмов, исправляющих влияние геометрии зонда на АСМ-изображения. Измеренное значение параметра шероховатости Ra для поверхностей А и Б фольг составляет 56 и 44 нм соответственно.
Рис. 1.
АСМ-изображения поверхностей А (а) и Б (б) свежезакаленных фольг сплава 1421 и соответствующие диаграммы распределения неровностей (в) и (г) вдоль линий сканирования, выделенных на (а) и (б).
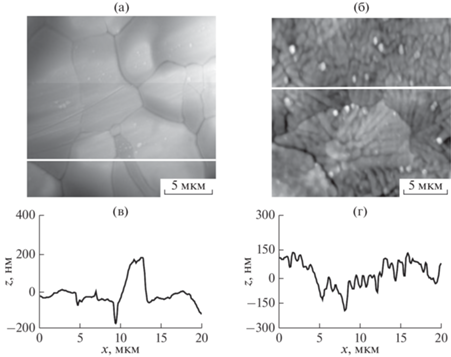
Анализ картин дифракции обратно рассеянных электронов показал, что при использованном методе закалки на охлаждающей поверхности вращающегося цилиндра полученные фольги сплава 1421 микрокристаллические. В них формируется микрозеренная структура. На рис. 2а показан фрагмент высокоразрешающей дифракционной карты типичного участка поверхности быстро затвердевшего сплава 1421. Помимо участков с мелкими зернами среднего размера до 3 мкм наблюдаются также участки с более крупными зернами размером до 20 мкм. На рис. 2а дополнительно приведена цветовая шкала ориентаций в пространстве обратных полюсных фигур для ГЦК-решетки. Согласно полученным ориентационным картам в быстро затвердевших фольгах сплава 1421 формируется текстура [111].
Рис. 2.
Типичная карта поверхности А свежезакаленных фольг сплава 1421, полученная методом дифракции обратно рассеянных электронов (а) (на вставке – цветовая кодировка кристаллографических ориентаций зерен), и соответствующая гистограмма распределения по размерам хорд сечений зерен данного участка поверхности фольги (б).
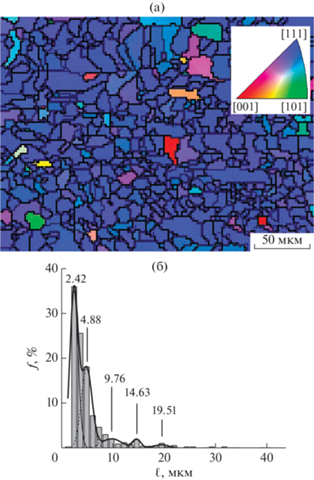
Экспериментальные данные о зеренной структуре, полученные методом дифракции обратно рассеянных электронов для поверхности А фольг сплава 1421 (рис. 2а), были аппроксимированы с помощью распределения Гаусса в математическом пакете OriginPro (рис. 2б) с коэффициентом детерминации COD (R 2), равным 0.88 (табл. 1). Как видно из рисунка, распределение по размерным группам хорд случайных секущих на сечениях зерен может быть описано суперпозицией пяти гауссовых распределений. В качестве параметров моделирования пиков определяли положение (${{\ell }_{{\max }}}$), высоту (${{f}_{{\max }}}$), нормированную площадь (S), а также ширину пика на полувысоте (FWHM) (табл. 1). Средняя длина $\bar {\ell }$ хорд зерен поверхности А равна 7.85 мкм. Если учесть, что форма зерен полигональная (рис. 2а), то согласно расчетам по известной методике [20] средний размер зерен фольг составляет около 12 мкм.
Таблица 1.
Параметры моделирования, аппроксимирующего гистограмму распределения хорд сечений зерен по размерным группам на поверхности А фольг сплава 1421 (рис. 2а)
Метод секущих | OriginPro | ||||
---|---|---|---|---|---|
$\bar {\ell }$, мкм | ${{\ell }_{{\max }}}$, мкм | ${{f}_{{\max }}}$,% | S, % | FWHM | COD (R2) |
7.85 ± 0.79 | 2.42 ± 0.80 | 35.23 | 50.23 | 1.87 | 0.88 |
4.88 ± 1.05 | 17.91 | 36.08 | 2.47 | ||
9.76 ± 2.0 | 2.14 | 8.14 | 4.65 | ||
14.63 ± 0.83 | 1.99 | 3.16 | 1.94 | ||
19.51 ± 1.52 | 0.82 | 2.39 | 3.57 |
Как следует из табл. 1, ширина и положения пиков распределения хорд сечений зерен флуктуируют в случае мелких и более крупных зерен. Амплитуды ${{f}_{{\max }}}$ пиков распределения по размерам хорд сечений мелких зерен размером до 5 мкм в среднем в 17 раз выше по сравнению с хордами сечений крупных зерен. В группах более мелких зерен основная доля хорд попадает в размерные группы в интервале от 1 до 5 мкм, а в случае более крупных зерен – от 7 до 13 мкм.
Экспериментальные спектры частиц (рис. 3, 4) были получены для свежезакаленных и отожженных фольг сплава 1421 при облучении их ускоренными протонами. Они представляют собой спектры обратно рассеянных протонов и α-частиц, образующихся в результате ядерной реакции (p, α). Как видно из рис. 3, в левой области экспериментальных спектров, где регистрируются обратно рассеянные протоны, на шкале каналов отмечены стрелками положения хорошо различимых сигналов алюминия и лития, а также сопутствующих элементов кислорода и углерода, локализованных вблизи поверхностей фольги. Поскольку магний является соседним по массе для алюминия элементом, в спектрах сигналы алюминия и магния визуально не различаются. Сигналы легирующих элементов Sc и Zr в спектрах обратно рассеянных протонов также определить не представляется возможным из-за их малой концентрации в сплаве 1421. В правой области спектров регистрируются α-частицы из реакции 7Li(p, α)4He с литием-7, позволяющие исследовать его содержание в образцах.
Рис. 3.
Типичный спектр рассеянных протонов и продуктов (p, α)-реакции для поверхностей А (1) и Б (2) свежезакаленных фольг сплава 1421.
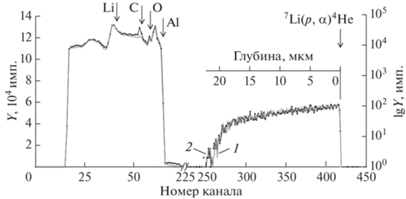
Рис. 4.
Спектры α-частиц из реакции 7Li(p, α)4He для поверхностей А (1) и Б (2) фольг сплава 1421, отожженных при температурах 150 (а), 220 (б), 300 (в) и 380°С (г).
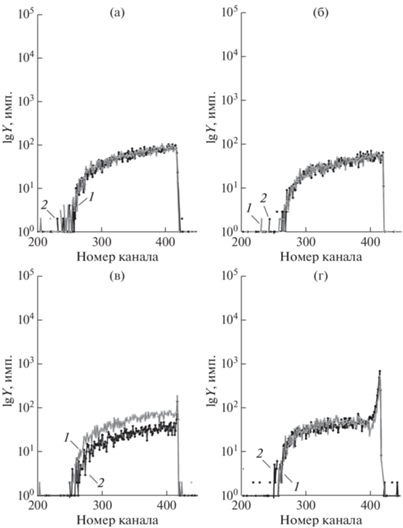
Типичные спектры α-частиц, полученные от поверхностей А и Б свежезакаленных фольг сплава 1421 (рис. 3), хорошо согласуются друг с другом, указывая на то, что существенное различие в концентрации лития в областях обеих сторон фольг отсутствует. В предварительно выполненных экспериментах [12] глубинные профили лития, рассчитанные из спектров ядерной реакции 7Li(p, α)4He с помощью программы SIMNRA, показали, что сигнал лития разрешается до глубины 22 мкм. Литий по глубине фольг в изученных слоях распределен равномерно. Его измеренная концентрация составляет 9.0 ат. % и отличается от расчетного содержания в сплаве в пределах погрешности измерений методом мгновенных ядерных реакций.
Известно, что определение композиционного состава образцов возможно при сравнении интегрированных сигналов компонентов в спектрах рассеянных протонов и продуктов (p, α)-реакции. Это позволило построить (рис. 5а) температурную зависимость нормализованного выхода частиц лития и кислорода в спектрах, полученных при облучении ускоренными протонами отожженных фольг сплава 1421. Сигналы указанных элементов были нормализованы на их высоту в спектре исходного (свежезакаленного) образца. Выполненные измерения позволили оценить содержание лития в приповерхностном слое (~0.5 мкм) и на максимально детектируемой глубине (~20 мкм) фольг, а кислорода – в тонком приповерхностном слое (до 0.1 мкм). Как следует из характера изменения с ростом температуры отжига формы сигналов лития в спектрах мгновенных ядерных реакций (рис. 4), при низкотемпературном отжиге (150 и 220°С) наблюдается снижение концентрации лития в анализируемом слое поверхностей А и Б, включая приповерхностную область фольг, а также на их глубине. Степень оксидации поверхности растет незначительно. С повышением температуры отжига обнаружен рост содержания лития в детектируемых слоях фольг. Наибольший эффект наблюдается в спектрах мгновенных ядерных реакций фольг, отожженных при 380°С, где высота сигнала лития в приповерхностных областях А и Б кратно увеличивается. Также возрастает выход кислорода в спектрах обратно рассеянных протонов.
Рис. 5.
Температурная зависимость (а) нормализованного выхода частиц лития (кружки) и кислорода (треугольники) в спектрах α-частиц и протонов, рассеянных поверхностями А (пустые символы) и Б (закрашенные символы) фольг сплава 1421 (содержание лития на глубине обозначено квадратами (сторона А) и звездочками (сторона Б), Yi и Y0 – выходы i-го элемента в экспериментальных спектрах отожженного и свежезакаленного образца соответственно). Гистограмма (б) изменения концентрации лития в приповерхностной области (1, 3) и на глубине фольг (2, 4) в зависимости от температуры отжига для сторон А (1, 2) и Б (3, 4) (горизонтальные штриховая и пунктирная линии задают профиль распределения лития в свежезакаленной фольге, смоделированный программой SIMNRA [12], и расчетное содержание лития в сплаве 1421 соответственно).
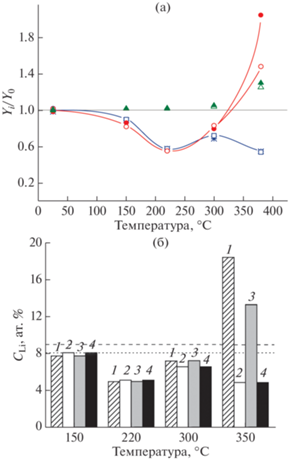
Как видно из рис. 5а, выходы α-частиц из атомов лития в приповерхностной области поверхностей А и Б исходной фольги и фольг, отожженных при температурах 150, 220, 300 и 380°С, относятся, соответственно, как 1 : 0.86 : 0.55 : 0.80 : 2.05 и 1 : 0.86 : 0.55 : 0.80 : 1.48. В то же время установлено, что содержание лития в массиве не зависит от анализируемой поверхности. Для исходной и отожженных при температурах 150, 220, 300 и 380°С фольг в массиве получены следующие соотношения: 1 : 0.90 : 0.57 : 0.73 : 0.54. Выполненное ранее [12] с помощью программы SIMNRA послойное профилирование лития по глубине свежезакаленных и отожженных при 380°С в течение 1 ч фольг позволило построить гистограмму изменения концентрации лития в приповерхностной области и на глубине фольг в зависимости от анализируемой поверхности и температуры отжига (рис. 5б) на основе данных рис. 5а. Таким образом, только для температуры отжига 380°С степень обогащения приповерхностной области поверхности А выше в 1.4 раза, чем поверхности Б (рис. 5б). Во всех остальных случаях в изученном интервале температур отжига содержание лития вблизи противоположных поверхностей фольг в пределах погрешности одинаково.
В современном материаловедении понятие “закалка из расплава” означает операцию термической обработки, связанную с нагревом, выдерживанием и быстрым охлаждением расплавленного сплава с целью получения материалов с уникальным сочетанием свойств. Методы центробежной закалки, спиннингования, облучения поверхности электронными или лазерными пучками, а также левитации, позволяющие получить высокие скорости охлаждения, используются в современных экспериментальных разработках и промышленных технологиях [10, 21]. В настоящее время на практике успешно применяют массивные изделия, прессованные из быстро затвердевших фольг сплавов, а также разрабатывают материалы припоев коррозионностойких покрытий для упрочнения композиционных материалов. Быстро затвердевшие сплавы используют как в исходном (фольги, чешуйки, а также ленты и порошки), так и в консолидированном состоянии, управляя их физическими свойствами за счет термообработки.
Достаточно высокая коррозионная стойкость алюминиевых сплавов, несмотря на высокую химическую активность алюминия, обусловлена самопроизвольным образованием на поверхности материалов защитной оксидно-гидроксидной пленки [22] и объясняется явлениями пассивности в агрессивных средах. На коррозионную стойкость сплавов значительное влияние оказывает структурно-фазовое состояние поверхностного слоя, элементный состав которого определяется также температурой термообработки. Поэтому прикладное значение результатов настоящего исследования заключается в том, что полученные оригинальные данные позволяют определить взаимосвязь между поведением лития при отжиге сплава системы Al–Mg–Li и фазовыми превращениями в быстро затвердевшем сплаве 1421 при отжиге.
На рис. 6 показана схематичная диаграмма, построенная на основе ранее полученных результатов [11, 12, 23], наглядно сопоставляющая температурную зависимость микротвердости фольг сплава 1421 при изохронном отжиге и температурные интервалы выделения литийсодержащих фаз при термообработке. Таким образом, установленные закономерности перераспределения лития в результате низко- и высокотемпературного отжигов микрокристаллических быстро затвердевших фольг сплава 1421 можно объяснить структурно-фазовыми изменениями в образцах в исследованном интервале температур отжига 150–380°С, обусловленными распадом пересыщенного твердого раствора с последовательным выделением следующих интерметаллидных фаз, содержащих литий: метастабильная δ'-фаза (Al3Li), стабильная δ-фаза (AlLi), метастабильная фаза S1 (Al2MgLi) и обнаруженная в [11] метастабильная фаза переменного состава Al(Mg,Sc,Zr,Li)x. Немонотонный характер изменения микротвердости при изохронном отжиге подтверждает известный факт, что выделение стабильных фаз вызывает более слабое упрочнение сплавов, чем выделение метастабильных фаз [24]. Значительное уменьшение микротвердости при нагреве фольг сплава выше 400°C может быть объяснено укрупнением интерметаллидных выделений и затем их растворением, а также процессами рекристаллизации, сопровождающимися ростом зерен. Температурный порог рекристаллизации быстро затвердевшего сплава 1421 повышен за счет выделения частиц фаз Al(Mg,Sc,Zr,Li)x и S1 на границах зерен фольг. Об этом свидетельствуют результаты рентгеноструктурного анализа, поскольку текстура [111], начинающая ослабевать при температурах отжига выше 350°С, частично сохраняется до 450°C [25]. Дополнительно отметим, что с помощью рентгеноструктурного анализа также было обнаружено, что на поверхности фольг литий вступает в реакцию с кислородом, образуя пероксид Li2O2 [12].
Рис. 6.
Схематическая диаграмма температурной зависимости микротвердости и фазовых превращений с выделением литийсодержащих фаз Al3Li (δ') (1), AlLi (δ) (2), Al2LiMg (S1) (3), Al(Mg,Sc,Zr,Li)x (4) в фольгах сплава 1421. Температурные интервалы для метастабильных фаз показаны с помощью штриховки, для стабильной фазы – контуром без штриховки. По авторским данным [11, 12, 23].
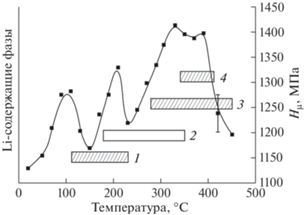
При обсуждении обнаруженных закономерностей изменения переменного состава приповерхностных областей сплава системы Al–Mg–Li при термообработке необходимо обратить внимание на то, что разрозненная и противоречивая информация о поведении лития в алюминиевых сплавах касается, к сожалению, ограниченных температурных и концентрационных интервалов. Исследователи сталкиваются с многочисленными сложностями при интерпретации данных, полученных с помощью косвенных методов, о распределении лития в поверхностных слоях алюминиевых сплавов [13–15, 26–28]. В редких работах сообщается об обеднении литием приповерхностного слоя сплавов в результате отжига при повышенных температурах [14, 29–31]. С одной стороны, например, при изучении процессов пассивации в отожженных, а затем нормализованных бинарных сплавах Al–Li авторы [30] сообщают, что с ростом расчетного содержания лития в сплаве от 1 до 2 мас. % (от 3.4 до 7.4 ат. % Li соответственно) наблюдается повышение степени коррозионной устойчивости. Авторы используют данные фотоэлектронной спектроскопии, полученные после ионного травления поверхности сплавов, и объясняют обнаруженный эффект внедрением Li2O в пассивную пленку на поверхности металла. Стоит отметить, что в эксперименте сплав Al–1 мас. % Li отжигали при 350°С, а сплав Al–2 мас. % Li – при 450°С. К сожалению, повысив температуру отжига, авторы не рассмотрели вопрос, почему измеренная методом фотоэлектронной спектроскопии на поверхности образца сплава Al–2 мас. % Li концентрация лития оказалась на 23% ниже расчетной концентрации, составив 5.7 ат. % вместо 7.4 ат. %. В отожженном сплаве Al–1 мас. % Li измеренное содержание лития совпало с расчетным. В [31] авторы, сообщая о сходстве поведения магния и лития вблизи поверхности образцов при отжиге сплавов системы Al–Mg–Li, связали растворение преципитатов δ'-фазы вблизи поверхности образцов, установленное с помощью просвечивающей электронной микроскопии, с формированием обедненного литием поверхностного слоя. При переходе к отожженному сплаву системы Al–Cu–Mg–Zn авторы [31] обнаружили обогащение поверхностного слоя магнием в отсутствие лития. С этой точки зрения интересны результаты авторов [14], сообщивших о тенденции снижения степени обеднения приповерхностных слоев литием в интервале температур отжига 450–570°С в присутствии таких легирующих элементов, как магний и/или медь по сравнению с бинарными сплавами Al–Li. В то же время после обработки лазерным облучением ультрамелкозернистых сплавов 1420 и 1421, полученных с помощью интенсивной пластической деформации, авторы [26, 27] сообщают об обогащении оксидной пленки литием со ссылкой на то, что литий является активным легко окисляемым металлом. Однако, во-первых, следует констатировать, что без указания измеренных численных значений концентрации лития, а также метода его профилирования по глубине данные результаты могут иметь только качественный характер [26, 27]. Во-вторых, из-за различий в методах получения образцов при высокоскоростной кристаллизации и интенсивной пластической деформации не следует ожидать прямого соответствия характеристик структуры и физико-механических свойств быстро затвердевших и ультрамелкозернистых материалов.
В настоящей работе исследования быстро затвердевших фольг сплава 1421 проведены в сравнительно широком интервале температур отжига. Установленное равномерное распределение лития в образцах, отожженных при температурах ниже 380°С, свидетельствует о достижении высокого уровня концентрационной однородности материала благодаря высокоскоростной кристаллизации. Основной причиной обнаруженной зависимости содержания лития в поверхностных слоях от термообработки образцов, по-видимому, является выделение литийсодержащих фаз в результате структурно-фазовых превращений при отжиге быстро затвердевшего сплава. Например, перераспределение лития в объеме фольг в интервале температур отжига 150–220°С, приводящее к обеднению литием приповерхностных и глубинных слоев (до 5 ат. % после 220°С отжига), очевидно, связано с выделением, а затем с растворением преципитатов δ'-фазы в быстро затвердевшем сплаве 1421 (рис. 5б, 6), что согласуется с данными авторов [31], описанными выше. Последующие преципитация δ-фазы и распад пересыщенного твердого раствора с выделением фазы S1 сопровождаются ростом в приповерхностных слоях содержания лития (в среднем до 7 ат. %) при температуре отжига 300°С. Анализируя установленное кратное повышение содержания лития на поверхности быстро затвердевших фольг сплава 1421 после высокотемпературного отжига при 380°С, сопровождающееся понижением его концентрации на глубине (4.9 ат. %), можно сделать вывод о том, что значительное обогащение поверхности литием из-за диффузии из объема на поверхность фольг, возможно, связано с растворением выделений фазы Al(Mg,Sc,Zr,Li)x, а также структурной модификацией оксидной пленки при отжиге. Следовательно, для улучшения физико-механических свойств сплавов системы Al–Mg–Li, в том числе повышения их коррозионной стойкости, необходимо продолжение структурно-фазовых исследований с целью определения механизмов формирования и эволюции градиентной структуры поверхностных слоев фольг сплава 1421 при отжиге.
ЗАКЛЮЧЕНИЕ
Полученные свежезакаленные фольги быстро затвердевшего сплава 1421 имеют микрокристаллическую структуру и текстуру [111]. Распределение хорд случайных секущих на сечениях зерен по размерным группам может быть описано суперпозицией гауссовых распределений. Средний размер зерен на поверхности фольг составляет 12 мкм. Ячеистая структура наблюдается со стороны свободной поверхности и в области каверн и впадин контактной стороны. Шероховатость поверхности фольг изменяется от 44 до 57 нм.
Впервые показано, что перераспределение лития в результате термической обработки фольг коррелирует со структурно-фазовыми изменениями в быстро затвердевших образцах и связано с распадом пересыщенного твердого раствора и выделением литийсодержащих фаз. Установлена зависимость содержания лития в приповерхностном слое и на глубине фольг от температуры отжига. В области низкотемпературного отжига литий в пределах погрешности измерений распределен по глубине образцов равномерно. Содержание лития в детектируемом слое снижается в 1.8 раз в интервале температур отжига 150–220°С. С последующим ростом температуры отжига формируется градиентная структура в приповерхностных слоях фольг. При высокотемпературном отжиге (при 380°С) приповерхностная концентрация лития превышает его содержание на глубине более чем в три раза.
Список литературы
Dorin T., Vahid A., Lamb J. // Fundamentals of Aluminium Metallurgy / Ed. Lumley R.N. Cambridge: Woodhead Publishing Series, 2018. P. 387. https://doi.org/10.1016/B978-0-08-102063-0.00011-4
Wang Y., Zhang Z., Wu R., Sun J., Jiao Y., Hou L., Zhang J., Li X., Zhang M. // Mater. Sci. Eng. A. 2019. V. 745. № 1. P. 411. https://doi.org/10.1016/J.MSEA.2019.01.011
Колобнев Н.И. // Металловедение и термическая обработка металлов. 2002. № 7. С. 30.
Tsaknopoulos K., Walde C., Champagne Jr., Cote D. // JOM. 2019. V. 71. № 1. P. 435. https://doi.org/10.1016/j.msea.2018.09.017
Захаров В.В., Елагин В.И., Ростова Т.Д., Филатов Ю.А. // Технология легких сплавов. 2010. № 1. С. 67.
Нохрин А.В., Шадрина Я.С., Чувильдеев В.Н., Копылов В.И., Бобров А.А., Лихницкий К.В. // Поверхность. Рентген., синхротр., и нейтрон. исслед. 2022. № 1. С. 24. https://doi.org/10.31857/S1028096022010113
Dumitraschkewitz P., Stephan S.A., Stephenson L.T., Uggowitzer P.J., Pogatscher S. // Adv. Eng. Mater. 2018. V. 20. P. 1800255. https://doi.org/10.1002/adem.201800255
Zuiko I., Kaibyshev R. // Mater. Sci. Eng. A. 2018. V. 737. P. 401. https://doi.org/10.1088/1757-899X/1014/1/012063
Березина А.Л., Сегида Е.А., Монастырская Т.А., Котко А.В. // Металлофизика и новейшие технологии. 2008. № 6. С. 849.
Kurz W., Rappaz M., Trivedi R. // Int. Mater. Rev. 2020. V. 66. № 1. P. 30. https://doi.org/10.1080/09506608.2020.1757894
Шепелевич В.Г., Бушкевич И.А., Вендлер Э., Ташлыкова-Бушкевич И.И. // Поверхность. Рентген., синхротр. и нейтрон. исслед. 2019. № 6. С. 101. https://doi.org/10.1134/S020735281906012X
Столяр И.А., Шепелевич В.Г., Вендлер Э., Ташлыкова-Бушкевич И.И. // Поверхность. Рентген., синхротр. и нейтрон. исслед. 2021. № 7. С. 96. https://doi.org/10.31857/S1028096021070190
Schoeberl T., Kumar S. // J. Alloy Compd. 1997. V. 255. P. 135. https://doi.org/10.1016/S0925-8388(96)02818-6
Soni K.K., Williams D.B., Newbury D.E., Gillen G., Chi P., Bright D.S. // Metall. Mater. Trans. A. 1993. V. 24. P. 2279. https://doi.org/10.1007/BF02648601
Harvey J.-P., Singh S., Oishi K., Acheson B., Turcotte R., Pilon D., Lavoie J., Gange B. // Mater. Des. 2021. V. 198. P. 109293. https://doi.org/10.1016/j.matdes.2020.109293
Мирошниченко И.С. Закалка из жидкого состояния. М.: Металлургия, 1982. 168 с.
Суслов А.А., Чикунов В.В., Шашолко Д.И., Чижик С.А. Атомно-силовой микроскоп NT-206: новые возможности // Докл. VI Белорус. семинара по сканирующей зондовой микроскопии БЕЛСЗМ-6. Минск, 2004. С. 123.
Schmidt E., Ritter K., Gartner K., Wendler E. // Nucl. Instrum. Methods Phys. Res. B. 2017. V. 409. P. 126. https://doi.org/10.1016/j.nimb.2017.03.111
Mayer M. SIMNRA, a Simulation Program for the Analysis of NRA, RBS and ERDA. N.Y.: American Institute of Physics, 1999. 541 p.
Салтыков С.А. Стереометрическая металлография. М.: Металлургия, 1976. 272 с.
Pinomaa T., Laukkanen A., Provatas N. // MRS Bull. 2020. V. 45. № 11. P. 910. https://doi.org/10.1557/mrs.2020.274
Семенова И.В., Флорианович Г.М., Хорошилов А.В. Коррозия и защита от коррозии. М.: Физматлит, 2002. 336 с.
Бушкевич И.А., Шепелевич В.Г., Ташлыкова-Бушкевич И.И., Адинцов Н.В., Кочерга М.В., Лобач Р.Д. Рентгеноструктурный анализ фазовых превращений в быстрозатвердевшем сплаве Al–Mg–Li–Sc–Zr при отжиге // Матер. 5-й Междунар. науч.-практ. конф. “Прикладные проблемы оптики, информатики, радиофизики и физики конденсированного состояния”. Минск, 2019. С. 214.
Новиков И.И. Теория термической обработки металлов. М.: Металлургия, 1986. 480 с.
Бушкевич И.А., Бородын А.В., Фишкина Ю.Э., Ташлыкова-Бушкевич И.И. // Сб. докл. VIII Междунар. науч. конф. Актуальные проблемы физики твердого тела. Минск: Ковчег, 2018. Т. 1. С. 134.
Кикин П.Ю., Перевезенцев В.Н., Русин Е.Е., Землякова Н.В. // Металловедение и термическая обработка металлов. 2012. № 8. С. 23.
Кикин П.Ю., Перевезенцев В.Н., Русин Е.Е. // Физика металлов и металловедение. 2015. Т. 116. № 8.
Minamino Y., Yamane T., Araki H. // Metall. Mater. Trans. A. 1987. V. 18. P. 1536. https://doi.org/10.1007/BF02646667
Фридляндер И.Н., Сандлер В.С., Никольская Т.И. // Металловедение и термическая обработка металлов. 1983. № 7. С. 20.
Wang H.N., Liu C.Z., Lu L.P., Li R.S., Lin D. // Mater. Corros. 2017. V. 68. № 1. P. 58. https://doi.org/10.1002/maco.201609083
Fox S., Flower H.M., McDarmaid D.S. // Scr. Metall. 1986. V. 20. № 1. P. 71. https://doi.org/10.1016/0036-9748(86)90215-2
Дополнительные материалы отсутствуют.
Инструменты
Поверхность. Рентгеновские, синхротронные и нейтронные исследования