Приборы и техника эксперимента, 2023, № 3, стр. 121-124
МЕТОД ПРОВЕДЕНИЯ УСТАЛОСТНЫХ ИСПЫТАНИЙ ТОНКИХ ПРОВОЛОК
О. И. Аксенов a, *, А. А. Фукс a, b, Н. А. Волков a, А. С. Аронин a
a Институт физики твердого тела РАН
142432 Черноголовка, Московской обл., ул. Академика Осипьяна, 2, Россия
b Национальный исследовательский университет “Высшая школа экономикиˮ
109028 Москва, Покровский бульвар, 11, Россия
* E-mail: oleg_aksenov@inbox.ru
Поступила в редакцию 01.09.2022
После доработки 08.09.2022
Принята к публикации 23.10.2022
- EDN: UXDSHZ
- DOI: 10.31857/S0032816223020015
Аннотация
В рамках данной работы разработан новый метод усталостных испытаний на растяжение тонких микропроводов и проволок, соответствующий ГОСТ 25.502-79. Разработанный метод проверен на аморфных микропроводах состава Fe77.5Si7.5B15 в стеклянной изоляции. Установлено, что режим деформирования в интервале напряжений от 0 до 700 МПа соответствует долговечному использованию исследованных микропроводов (миллионы циклов). Кроме того, изученные микропровода способны выдержать сотни тысяч циклов растяжения при напряжениях от 700 до 1100 МПа.
ВВЕДЕНИЕ
Тонкие аморфные микропровода являются перспективным материалом для проектирования на их основе датчиков деформации. Данные материалы проявляют прямую корреляцию магнитных свойств и доменной магнитной структуры с механическими напряжениями (как остаточными, возникающими в результате изготовления, так и внешними). Из литературы известно, что бистабильное перемагничивание, эффект гигантского магнитного импеданса и явление ферромагнитного резонанса в микропроводах строго коррелируют с их напряженно-деформированным состоянием [1–4]. Несмотря на широкие перспективы применения таких материалов в качестве датчиков деформации, практически отсутствует информация о прочности микропроводов при воздействии динамических нагрузок, что является критичным параметром таких устройств. Это может быть обусловлено как высокой прочностью аморфных материалов в целом (единицы гигапаскаль) [5], так и сложностью проведения усталостных испытаний тонких проволок. Большинство существующих методик усталостных испытаний таких объектов предусматривает исследование проволок диаметром порядка единиц и десятых долей миллиметра в соответствии с ГОСТ 25.502-79 [6]. Однако диаметр тонких аморфных микропроводов составляет единицы или десятки микрон. Кроме того, интерес представляет проведение многоцикловых усталостных испытаний на растяжение микропроводов, покрытых стеклянной изоляцией. В таком виде, в частности, изготавливаются микропровода методом Улитовского–Тейлора, имеющие широкое распространение. По этим причинам многие существующие методики усталостных испытаний [7] могут быть применены лишь с модификациями, учитывающими малый диаметр исследуемых объектов.
Целью данной работы являлась разработка простого и эффективного метода усталостных испытаний тонких микропроводов в стеклянной изоляции с учетом ГОСТ 25.502-79.
ЭКСПЕРИМЕНТ И ОБСУЖДЕНИЕ
Циклические испытания на растяжение/сжатие были выполнены в соответствии с ГОСТ 25.502-79 и проводились на пяти уровнях нагрузки, начиная с напряжения, соответствующего 0.95 предела прочности материала. Предел прочности материала определялся путем приложения статической растягивающей нагрузки, при которой исследуемый образец разрушался. Определение предела прочности осуществлялось на пяти одинаковых образцах с дальнейшим усреднением результата. Испытания проводились с частотой 1 Гц на трех образцах на точку для каждого деформированного состояния. База испытаний составляла 107 циклов. В качестве тестовых образцов использовали микропровода состава Fe77.5Si7.5B15 диаметром 16.5 мкм, покрытые стеклянной оболочкой толщиной 3.2 мкм. Длина микропровода составляла 4 см.
Для проведения усталостных испытаний была разработана экспериментальная установка, схема и общий вид которой представлены на рис. 1.
Рис. 1.
Установка для циклической деформации микропроводов: а – схема установки; б – общий вид тестовой сборки установки в процессе работы. 1 – микропровод; 2 – винтовой фиксатор; 3 – нижний винтовой фиксатор; 4 – ограничитель; 5 – нить; 6 – груз; 7 – сервопривод.
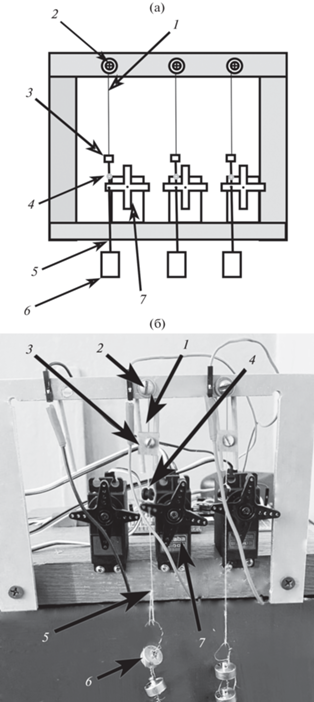
Согласно рис. 1, микропровод крепится между двумя винтовыми фиксаторами в подвешенном состоянии. Каждый фиксатор включает в себя винт, гайку и круглую шайбу. Микропровод зажимается между шайбой и металлической рамой установки. Внутренние части шайбы и рамы покрыты ПВХ пленкой для минимизации повреждения микропровода при зажиме. Масса нижнего фиксатора пренебрежимо мала в сравнении с пределом прочности исследуемых микропроводов и соответствует нагрузке 40 МПа (предел прочности микропроводов находился на уровне 2.1–2.2 ГПа). Согласно рис. 1б, ниже всех верхних фиксаторов размещены направляющие, препятствующие колебанию исследуемого образца в горизонтальном направлении и его кручению. К нижнему фиксатору крепится капроновая нить, пропущенная через отверстие в крестообразной насадке сервопривода. К другому концу капроновой нити крепится груз как добавочная нагрузка к массе фиксатора.
При вращении вала сервопривода по часовой стрелке из положения 180° в положение 135° ограничитель снимает нагрузку с микропровода. Заметим, что в текущей конфигурации установки, даже в момент снятия растягивающей нагрузки, на микропровод действует напряжение 40 МПа, вызванное силой тяжести от нижнего фиксатора. Использование более жесткой нити 5 (см. рис. 1а) может обеспечить полное снятие нагрузки с микропровода за счет подъема нижнего фиксатора и жесткости самой нити. Дальнейшее движение сервопривода против часовой стрелки приводит к повторному приложению нагрузки. В момент, когда нагрузка прикладывается к микропроводу, оси нити и микропровода совпадают.
При снятии нагрузки наблюдалось незначительное отклонение оси нити (на 1°–2°), ось микропровода оставалась неподвижной. Микроконтроллер осуществлял счет каждого акта приложения и снятия нагрузки и выводил количество циклов нагрузки/разгрузки на lcd-дисплей. На рис. 1б также видны пары проводов с разъемом (“femaleˮ) и штекером (“maleˮ), закрепленные слева от винтовых фиксаторов. В случае обрыва микропровода между верхним и нижним фиксаторами нижний фиксатор оказывался в свободном состоянии и размыкал контакт между проводами. Это приводило к прекращению счета числа циклов нагрузки на разрушенном микропроводе и остановке соответствующего сервопривода. Значение числа циклов для разрушенного микропровода сохранялось на lcd-дисплее. Частоту и базу испытаний можно при необходимости варьировать программно. Общее время проведения усталостных испытаний составляло 2.5 месяца.
В силу того что испытанию подвергались микропровода в стеклянной оболочке, величина напряжений, приходящихся на металлическую часть провода, оценивалась в соответствии с [8]:
(1)
${{\sigma }_{{\text{ж}}}} = mg{\text{/}}({{S}_{{\text{ж}}}} + {{S}_{{{\text{ст}}}}}{{E}_{{{\text{ст}}}}}{\text{/}}{{E}_{{\text{ж}}}}),$На рис. 2 приведена зависимость растягивающих напряжений от числа циклов нагрузки/разгрузки до разрушения.
Рис. 2.
Зависимость растягивающих напряжений от числа циклов нагрузки/разгрузки до разрушения. Величина ошибок измерения меньше размера точки на графике по любой из осей.
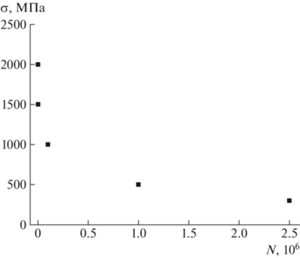
Согласно рис. 2, при приложении нагрузки до 700 МПа наблюдается значительная устойчивость микропроводов к многоцикловому воздействию нагрузки/разгрузки (сотни тысяч и миллионы циклов). При приближении нагрузок к напряжению разрушения (около 2 ГПа) наблюдается порядка 1000 циклов нагрузки/разгрузки до наступления разрушения. Величина ошибки измерения напряжений в металлической части микропровода составляет не более 50 МПа. Величина ошибки измерения числа циклов нагрузки/разгрузки составляет около 720.
Микропровода, подвергнутые разрушению при многоцикловой нагрузке/разгрузке, исследовались методом сканирующей электронной микроскопии (СЭМ) на микроскопе Zeiss Supra 50VP. На рис. 3 представлено характерное СЭМ-изображение микропровода после разрушения.
Рис. 3.
СЭМ-изображение места разрушения микропровода после 2.5 миллиона циклов нагрузки/разгрузки растягивающим напряжением 300 МПа.
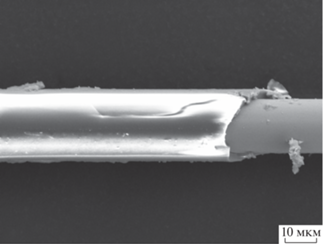
На рис. 3 показано изображение той части микропровода, которая была зажата фиксатором в процессе нагружения. Стеклянная оболочка после разрушения микропровода оставалась целой и была удалена непосредственно перед съемкой изображения для определения диаметра провода и толщины оболочки. Изменение уровня растягивающих напряжений (от 40 до 2000 МПа) не приводило к разрушению стеклянной оболочки на проводе, закрепленном под фиксаторами. Во всех случаях разрушение происходило вблизи центральной части микропровода. На рис. 4 представлено характерное изображение места разрушения микропровода.
Согласно рис. 4, разрушение происходило под углом ≈45° к оси микропровода и приложенной растягивающей нагрузке. При этом стеклянная оболочка претерпевала разрушение лишь в области разрушения металлической части провода.
ВЫВОДЫ
Таким образом, если рассматривать микропровод в стеклянной изоляции в качестве чувствительного элемента датчика деформации, то устойчивым режимом циклического приложения/снятия растягивающей нагрузки можно считать интервал напряжений от 0 до 700 МПа. Важно отметить, что такой режим деформирования микропровода соответствует его долговечному использованию. В диапазоне от 700 до 1100 МПа исследованный в рамках данной работы микропровод может выдержать сотни тысяч циклов нагружения/разгрузки, прежде чем будет разрушен.
Разработанный в рамках данной работы метод циклического деформирования микропроводов может быть использован не только для тонких аморфных проволок, но и кристаллических проволок, а также для проволок большего диаметра. Реализованный метод прост в исполнении и легко масштабируется для одновременного испытания трех и более проволок, что позволяет ускорить получение результатов многоцикловой деформации.
Список литературы
Vazquez M., Gomez-Polo C., Chen D.-X., Hernando A. // IEEE Transactions on Magnetics. 1994. V. 30. P. 907. https://doi.org/10.1109/20.312442
Churyukanova M., Kaloshkin S., Shuvaeva E., Stepashkin A., Zhdanova M., Aronin A., Aksenov O., Arakelov P., Zhukova V., Zhukov A. / Journal of Alloys and Compounds. 2018. V. 748. P. 199. https://doi.org/10.1016/j.jallcom.2018.02.342
Vazquez M., Andenote-Engelvin A.-L. // Journal of Magnetism and Magnetic Materials. 2009. V. 321. P. 2066. https://doi.org/10.1016/j.jmmm.2008.10.040
Aksenov O.I., Abrosimova G.E., Aronin A.S., Orlova N.N., Churyukanova M.N., Zhukova V.A., Zhukov A.P. // Journal of Applied Physics. 2017. V. 122. P. 235103. https://doi.org/10.1063/1.5008957
Luborsky F. Amorphous Metallic Alloys. London: Butterwoths, 1983.
ГОСТ 25.502-79 Расчеты и испытания на прочность в машиностроении. Методы механических испытаний металлов. Методы испытаний на усталость. М. Стандартинформ, 2005.
Костин П.П. Физико-механические испытания металлов, сплавов интерметаллических материалов. М.: Машиностроение, 1990.
Аксенов О.И., Орлова Н.Н., Аронин А.С. // ПТЭ. 2019. № 5. С. 135. https://doi.org/10.1134/S0032816219050136
Bansal N.P., Doremus R.H. Handbook of Glass Properties. Amsterdam: Elsevier LTD, 1986.
Дополнительные материалы отсутствуют.
Инструменты
Приборы и техника эксперимента