Приборы и техника эксперимента, 2023, № 3, стр. 80-90
ПРЕЦИЗИОННЫЙ ДАТЧИК ПОЛОЖЕНИЯ ДЛЯ ОПЕРАТИВНОГО КОНТРОЛЯ ЛАЗЕРНОГО СИНТЕЗА МИКРОСТРУКТУР НА ТРЕХМЕРНЫХ ПОВЕРХНОСТЯХ ОПТИЧЕСКИХ МАТЕРИАЛОВ
М. А. Завьялова a, *, А. В. Солдатенко a, С. А. Кокарев a
a Конструкторско-технологический институт научного приборостроения СО РАН
630058 Новосибирск, ул. Русская, 41, Россия
* E-mail: zavyalovama@gmail.ru
Поступила в редакцию 22.07.2022
После доработки 13.10.2022
Принята к публикации 19.10.2022
- EDN: UXQXIW
- DOI: 10.31857/S003281622302012X
Аннотация
Представлены результаты компьютерного моделирования прецизионного датчика положения на основе ножа Фуко для автоматической фокусировки излучения в ходе высокоскоростных лазерных технологических процессов, приведены результаты его внедрения и испытания на промышленных предприятиях в составе круговых лазерных записывающих систем. Данный датчик встраивается в лазерные комплексы для микроструктурирования поверхности оптических материалов и позволяет определять их положение с высоким разрешением (погрешность не превышает 0.1 мкм).
ВВЕДЕНИЕ
Прецизионная микро- и нанообработка оптических материалов позволяет создавать принципиально новые и усовершенствовать существующие элементы фотоники и оптоэлектроники [1–3]. Точное позиционирование лазерного луча при использовании фокусирующей оптики с большой апертурой дает возможность контролировать формируемую топологию рельефа (ширину и глубину зон). Для этого в оптические каналы лазерных технологических комплексов внедряют бесконтактные оптические датчики контроля положения поверхности обрабатываемых материалов. В работе [4] проведен обзор таких датчиков и сделан вывод, что при использовании фокусирующих объективов с малым рабочим отрезком (менее 1 мм) требуется встраивание датчика в оптический тракт технологического лазера. Поэтому коммерчески доступные датчики, имеющие свою оптическую систему “закрытогоˮ типа, не могут быть использованы в лазерных установках, в которых излучение фокусируется до размеров, сравнимых с их длиной волны. К бесконтактным датчикам контроля положения поверхностей предъявляются следующие требования: высокое быстродействие (до 1 МГц), разрешение (погрешность не должна превышать 0.1 мкм), возможность контроля положения сферических (выпуклых или вогнутых) поверхностей, приемлемые массогабаритные характеристики, а также совместимость оптических схем датчиков с оптическими схемами лазерных рабочих каналов. Таким образом, задача разработки методов автоматического контроля положения плоских и криволинейных поверхностей с высоким разрешением (менее 1 мкм) в ходе лазерных технологических процессов представляется актуальной.
В настоящее время используется достаточно много различных схем оптических бесконтактных датчиков контроля положения поверхностей [5–7]. Как правило, тот или иной вариант выбирается под конкретную лазерную технологическую установку с учетом материалов, на поверхности которых будет осуществляться лазерная запись, погрешности позиционирования, рабочего диапазона и скорости записи.
В данной работе представлены программное моделирование, оптимизация оптической схемы, результаты исследования и внедрения датчика автоматической фокусировки (ДАФ) на основе ножа Фуко, который используется в круговых лазерных записывающих системах (КЛЗС) для синтеза микроструктур на плоских и криволинейных поверхностях оптических материалов.
РАЗРАБОТКА И ИССЛЕДОВАНИЕ ДАТЧИКА АВТОМАТИЧЕСКОЙ ФОКУСИРОВКИ НА ОСНОВЕ НОЖА ФУКО ДЛЯ КРУГОВЫХ ЛАЗЕРНЫХ ЗАПИСЫВАЮЩИХ СИСТЕМ
В течение многих лет на ведущих отечественных и зарубежных научных и промышленных предприятиях успешно функционируют КЛЗС, разработанные в Конструкторско-технологическом институте научного приборостроения и Институте автоматики и электрометрии СО РАН (г. Новосибирск, Россия) [8]. Важным элементом КЛЗС, определяющим ее характеристики, является ДАФ на основе ножа Фуко. С использованием такого датчика на КЛЗС синтезируются прецизионные оптические элементы на плоских и криволинейных поверхностях.
Рассмотрим структурную схему КЛЗС. Как правило, такие системы имеют в своем составе технологический лазер (один или несколько) и полностью мобильный оптический канал 1 (рис. 1), который целиком размещается на каретке радиального перемещения 2. Гранитное основание 3 с системой виброзащиты 4 предназначено для размещения оптомеханического блока и снижения влияния вибраций на точностные характеристики его составных частей. В состав КЛЗС нового поколения также может входить второй технологический лазер 5 для реализации одновременно нескольких технологий микроструктурирования поверхности оптических прозрачных сред.
Рис. 1.
Модель круговых лазерных записывающих систем нового поколения. 1 – мобильный оптический канал с технологическим лазером № 1 (длина волны 405 нм); 2 – каретка радиального перемещения; 3 – гранитное основание; 4 – система виброзащиты; 5 – технологический лазер № 2 (длина волны 532 нм).
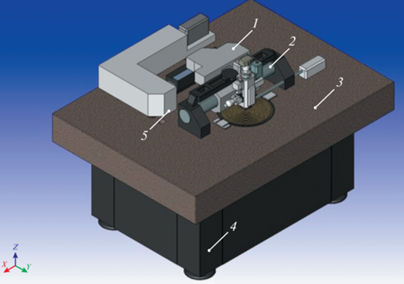
Принцип действия КЛЗС основан на формировании сфокусированным лазерным лучом изображения на вращаемой стеклянной подложке, на которую нанесен либо фоторезист, либо кремний, либо хром, в режиме кругового растрового сканирования. Подложка размещена на высокопрецизионном шпинделе, управляемом шпиндельным приводом. С помощью микроскопа записи, в состав которого входят датчик автоматической фокусировки и видеоузел, с высокой точностью поддерживается фиксированное расстояние между микрообъективом и поверхностью подложки в вертикальном направлении Z. Радиальное смещение R лазерного луча обеспечивается высокоточной кареткой на аэростатическом подшипнике, на которой размещены лазер, акустооптический модулятор и головка микроскопа записи. Смещение R измеряется лазерным интерферометром (модель RLE-10-SX-CX, RENISHAW). Высокая точность синтеза элементов топологии достигается благодаря применению прецизионных систем управления.
В КЛЗС [8] для синтеза микрорельефа дифракционных оптических элементов на криволинейных поверхностях используется ДАФ, который обеспечивает автоматический поиск поверхности записи, ее захват и последующее удержание в зоне наилучшей фокусировки микрообъектива. Основной функцией ДАФ является совмещение без участия оценочных действий оператора плоскости наилучшей фокусировки лазерного пучка с поверхностью обрабатываемой детали. ДАФ используется в оптическом канале лазерной технологической установки с короткофокусным объективом и состоит из чувствительного элемента – датчика расстояния – и привода, смещающего объектив. Также в его состав входит пропорционально-интегрально-дифференцирующий (ПИД) регулятор – устройство с обратной связью, которое формирует управляющий сигнал, являющийся суммой трех слагаемых: первое из них пропорционально разности входного сигнала и сигнала обратной связи (сигнал рассогласования), второе слагаемое является интегралом сигнала рассогласования, третье – производная сигнала рассогласования. ДАФ обеспечивает высокоскоростное зондирование поверхности и за счет обратной связи позволяет обеспечивать постоянный зазор между объективом и поверхностью.
Рабочий микрообъектив для КЛЗС имеет большую числовую апертуру (NA = 0.65). При этом глубина фокуса для длины волны λ = 532 нм составляет ±0.5 мкм. Поэтому во время записи скрытых изображений в пленках светочувствительных материалов их поверхность должна оставаться в пределах глубины фокуса, чтобы формировались линии одинаковой ширины с одинаковым уровнем засветки рабочим излучением. В составе КЛЗС рабочий микрообъектив закреплен на электромагнитном приводе, который путем перемещения микрообъектива вверх/вниз обеспечивает постоянное расстояние до поверхности в пределах приемлемого диапазона. Поскольку шпиндель, на котором закреплена заготовка, вращается со скоростью порядка 10 оборотов/с, привод отрабатывает смещения поверхности в режиме реального времени. Его частотная характеристика составляет несколько килогерц.
На привод поступает управляющий сигнал, пропорциональный коэффициенту отражения от поверхности заготовки зондирующего лазерного излучения. В основу принципиальной схемы ДАФ положена оптическая схема, описанная в работе [9]. Схема содержит полупроводниковый лазер (модель FCM-0640-PM-025-R-M-1-A-5, фирма Fiblaser Technology Co., Китай) с волоконным коллимированным выводом излучения (λ = = 640 нм), светоделительное зеркало, рабочий микрообъектив с числовой апертурой 0.65, нож Фуко (стальная пластина с заостренным краем), линзу (f = 40 мм), фокусирующую отраженное от поверхности заготовки излучение на двухэлементный фотоприемник ФД19-КК. В качестве меры измерения расстояния до объекта используется неравномерность распределения интенсивности отраженного света на элементах фотоприемника. Когда поверхность находится в фокусе, отраженный пучок коллимируется и линза (рис. 2) фокусирует световой пучок в центр сдвоенного фотодиода, который дает разностный сигнал ${{I}_{{{\text{раз}}}}} = \frac{{{{I}_{1}} - {{I}_{2}}}}{{{{I}_{1}} + {{I}_{2}}}}$ (I1 и I2 – сила тока соответственно с элементов фотоприемника K1 и K2), равный нулю. Если поверхность сместилась от микрообъектива, то отраженный пучок будет сходящимся (рис. 2а), освещая только фотодиод К1. В этом случае значение Iраз будет положительным, и привод подвинет микрообъектив к поверхности. В случае, если поверхность сместилась к объективу, отраженный пучок отклоняется таким образом, что будет засвечен фотодиод К2 (рис. 2б). Это приводит к отрицательному значению Iраз. В этом случае привод сместит микрообъектив таким образом, чтобы значение Iраз равнялось нулю.
Рис. 2.
Ход лучей при смещении рабочей заготовки относительно микрообъектива: а – смещение от микрообъектива (сходящийся пучок); б – смещение к микрообъективу (расходящийся пучок). I1 и I2 – сила тока соответственно с элементов фотоприемника K1 и K2.
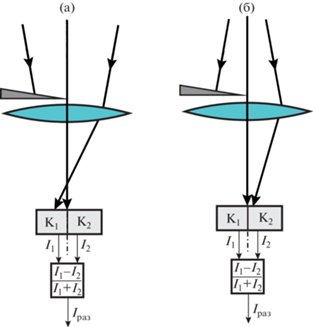
В ходе эксплуатации ранних версий КЛЗС, использующих ДАФ подобного типа, была обнаружена их дестабилизация при записи информации на криволинейных поверхностях, а именно: на разных радиусах сферической поверхности сигнал с ДАФ ошибочно определял смещение поверхности и требовалась его предварительная калибровка. Кроме того, при автоматическом поиске и захвате поверхности заготовки фокальная плоскость определялась ошибочно и происходило столкновение микрообъектива с заготовкой. Поэтому была проведена оптимизация ДАФ с целью обеспечения его бесперебойной работы как в процессе автоматического поиска фокальной плоскости, так и во время записи без предварительной калибровки. Для этого была создана модель данного датчика в программном пакете для расчета оптических систем Zemax, построен график аналитической зависимости сигнала с датчика от смещения поверхности (плоской или сферической).
РЕЗУЛЬТАТЫ МОДЕЛИРОВАНИЯ И РАСЧЕТА ДАТЧИКА АВТОМАТИЧЕСКОЙ ФОКУСИРОВКИ НА ОСНОВЕ НОЖА ФУКО
Модель двухэлементного фотоприемника была реализована путем специальной программной расшифровки изображений пятен с помощью инструмента Diffraction Image Analysis на основе функции Optical Transfer Function (OTF). OTF учитывает дифракционные эффекты, влияющие на формирование изображения.
В результате моделирования смещения поверхности в схеме ДАФ была получена серия дифракционных изображений пятен (рис. 3), программная обработка которых позволила построить зависимость разностного сигнала Iраз от смещения поверхности (плоской или криволинейной) (рис. 4). Для этого полученное изображение экспортировалось в программный пакет Exсel: отдельно вычислялось среднее значение яркости пикселей в верхней части изображений пятен и отдельно – в нижней. Тем самым моделировалась работа двухэлементного фотоприемника, в котором измеряются два сигнала I1 и I2. По полученным значениям I1 и I2 вычислялся результирующий сигнал Iраз. Обозначим параметр Δzaf (см. рис. 4) в качестве рабочего диапазона датчика автофокусировки при смещении контролируемой поверхности в направлении от фокальной плоскости рабочего микрообъектива на величину z, т.е. когда Δzaf = f + z (где f – фокусное расстояние микрообъектива). Этот параметр требует подробного рассмотрения, так как при больших смещениях поверхности, z > Δzaf, возможен сбой в работе датчика автофокусировки. Ошибочное определение смещения поверхности приведет к столкновению микрообъектива с обрабатываемой поверхностью.
Рис. 3.
Дифракционные изображения пятен в плоскости двухэлементного (К1, К2) фотоприемника при совпадении плоскости обрабатываемой детали с фокальной плоскостью микрообъектива (а) и при смещении поверхности на 5 (б), 10 (в), 15 мкм (г).
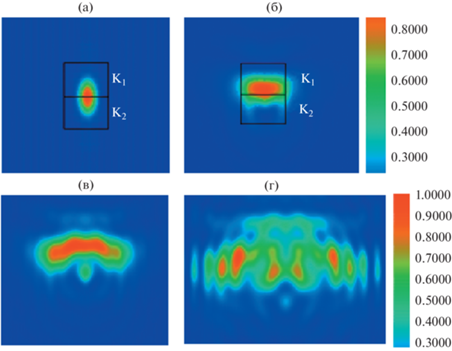
В результате моделирования было выявлено влияние на рабочий диапазон Δzaf положения ножа Фуко, а именно расстояния L между ножом и рабочим микрообъективом (рис. 5а). На рис. 5 показан ход лучей в случае смещения поверхности заготовки к рабочему микрообъективу (рис. 5б) и от него (рис. 5в). Видно, что в зависимости от расходимости пучка излучение фокусируется либо на верхней, либо на нижней части двухэлементного фотоприемника.
Рис. 5.
Оптическая схема датчика автоматической фокусировки на основе ножа Фуко (после микрообъектива показан обратный ход лучей): а – без смещения; б – при смещении плоскости заготовки к микрообъективу; в – при смещении плоскости заготовки от микрообъектива; г – при смещении плоскости заготовки от микрообъектива при значении Δz, превышающем 200 мкм.
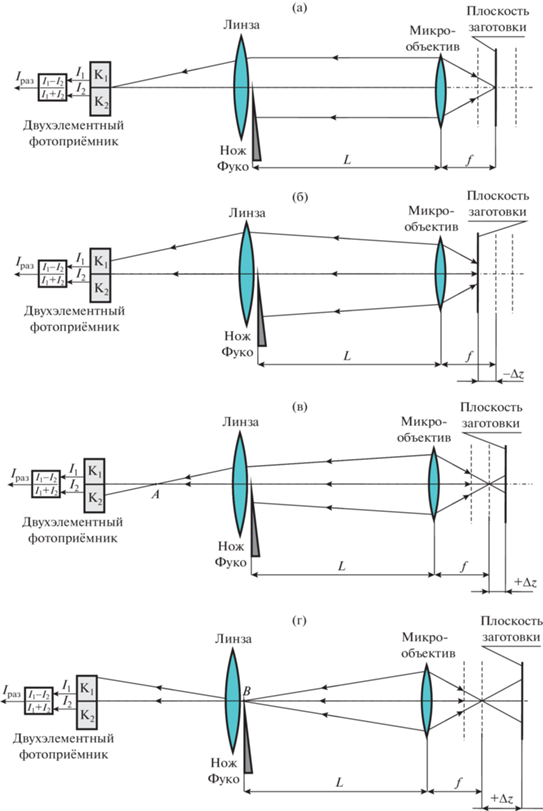
Однако при больших смещениях поверхности в направлении от микрообъектива (+Δz) отраженный пучок может сфокусироваться в плоскости ножа Фуко и, далее, на верхнем квадранте К1 (см. рис. 5г). Это приведет к инверсии сигнала и ошибочному определению направления смещения, поскольку в этом случае ${{I}_{1}}$ > ${{I}_{2}}$. Поэтому для увеличения рабочего диапазона нож Фуко нужно располагать как можно ближе к микрообъективу, т.е. уменьшать либо параметр L (см. рис. 5), либо расстояние между линзой и микрообъективом. Как показали проведенные расчеты (табл. 1), при уменьшении этого расстояния от 180 мм (такое расстояние изначально было заложено при проектировании КЛЗС) до 50 мм рабочий диапазон увеличивается в 10 раз – с 20 до 200 мкм. Рабочий диапазон оценивался по графику, представленному на рис. 4.
Таблица 1.
Результаты расчета рабочего диапазона ДАФ
Расстояние между микрообъективом и ножом Фуко, мм | Расчетный рабочий диапазон ДАФ Δzaf, мкм |
---|---|
180.3 | 20 |
150 | 63 |
100 | 96 |
50 | 200 |
Большое влияние на результат измерения оказывает также наклон поверхности, по которой осуществляется запись. Были проанализированы графики зависимости разностного сигнала Iраз (рис. 6) при смещении поверхностей с разными углами наклона (5°, 7°, 9° и 10°), полученные в результате программного моделирования оптической схемы датчика в программе Zemax.
Рис. 6.
График зависимости сигнала с двухэлементного фотоприемника от смещения поверхности при разных углах ее наклона.
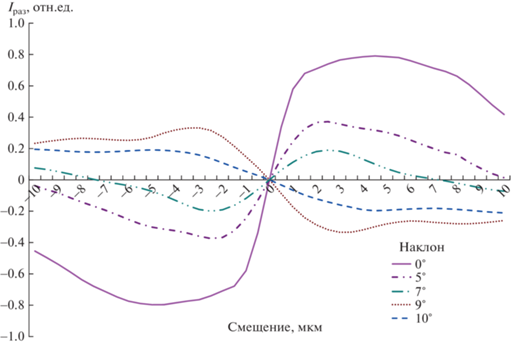
В результате моделирования выявлен критический угол наклона поверхности для микрообъектива с числовой апертурой 0.65, равный 8°, при котором происходит инверсия разностного графика. Это дает ошибочный сигнал смещения поверхности, при котором датчик автофокусировки срабатывает неверно, и возможно столкновение рабочего микрообъектива и поверхности заготовки. Следует отметить, что при наклоне поверхности уменьшается диапазон измеряемых смещений. Так, при угле наклона 8° он сокращается более чем в два раза. Это связано с тем, что в данном случае нож Фуко перекрывает не половину отраженного пучка, а его меньшую часть, и пучок попадает на обе части фотоприемника. Это приводит к уменьшению разностного сигнала и изменению его знака. Зная предельный угол наклона, исходя из диаметра заготовки можно определить ее максимально допустимый радиус кривизны: R = D/(2sinα), где D – диаметр заготовки, α – угол наклона касательной к сферической поверхности.
Как было показано выше, в двухканальной схеме КЛЗС используется лазерное излучение с длинами волн 405 и 532 нм. Зондирующее излучение, используемое в ДАФ, имеет длину волны 640 нм. Для стандартных микрообъективов с числовой апертурой 0.65 величина хроматизма положения в диапазоне указанных длин волн достигает нескольких микрометров. Соответственно, для точной фокусировки в одной плоскости лазерных пучков с тремя разными длинами волн необходимо менять расходимость излучения каждого лазера. При этом расчеты показали, что излучение в ДАФ должно быть строго коллимированным для оптимальной работы на криволинейных поверхностях. Это связано с тем, что в случае зондирования расфокусированным пучком сферической поверхности последняя влияет на расходимость пучка при отсутствии аксиального смещения заготовки (рис. 7).
Рис. 7.
Обратный ход лучей в схеме ДАФ с использованием расфокусированного зондирующего излучения: а – при нахождении в центре криволинейной поверхности; б – при смещении относительно центра криволинейной поверхности.
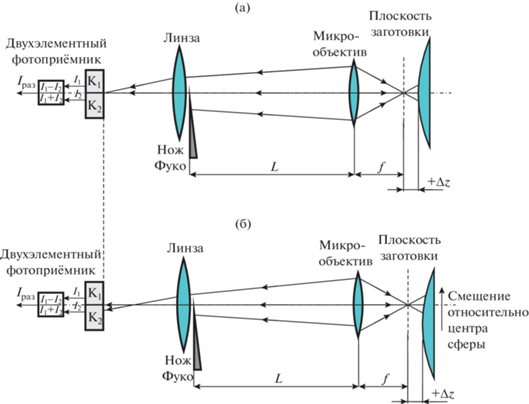
Этот вывод подтверждается приведенным на рис. 8 графиком зависимости ошибки определения смещения заготовки от положения зондирующего пучка относительно центра сферы при разных значениях расфокусировки излучения ДАФ (смещение относительно фокальной плоскости 5, 7 и 10 мкм). Из графиков видно, что с увеличением расфокусировки растет ошибка определения смещения сферы вдоль оси z при смещении зондирующего излучения относительно ее центра в плоскости x, y.
Рис. 8.
Зависимость ошибки определения смещения сферической заготовки (радиус 250 мм) от положения зондирующего пучка относительно центра сферы при значениях расфокусировки: 5, 7 и 10 мкм.
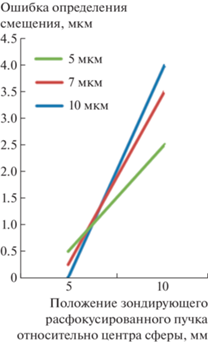
Результаты, полученные при моделировании ДАФ в программе Zemax, использовались при настройке КЛЗС. Зондирующее излучение ДАФ (λr = 658 нм) коллимировалось, а расходимости волновых фронтов излучений технологических лазеров (λb = 405 нм и λg = 532 нм) изменялись для точного совмещения плоскостей наилучшей фокусировки рабочего микрообъектива.
На основании результатов, полученных в ходе программного моделирования оптической схемы ДАФ в программе Zemax, был спроектирован микроскоп записи для КЛЗС (рис. 9). Он входит в состав оптического канала записи КЛЗС и предназначен для автоматической фокусировки выходного записывающего пучка в пятно диаметром порядка 0.5 мкм, а также для обеспечения визуализации и контроля записи при тестировании светочувствительного материала.
Рис. 9.
Конструкция микроскопа записи для круговой лазерной записывающей системы. 1 – поворотное зеркало; 3, 4 – дихроичные зеркала; 5 – микрообъектив; 6 – светоделитель; 7 – двухэлементный фотоприемник ФД19-КК; 2, 8, 9 – линзы.
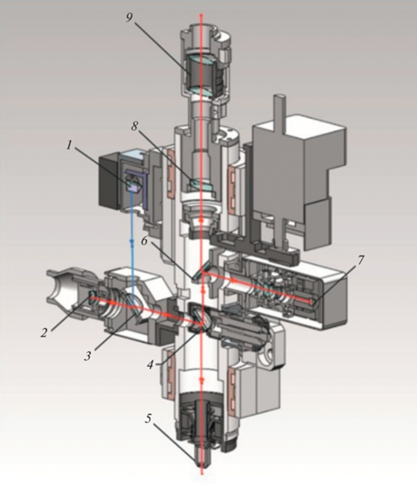
В состав микроскопа записи входят оптические элементы из схемы ДАФ, поворотное 1 и дихроичные 3, 4 зеркала, светоделитель 6, линзы 2, 8, 9, двухэлементный фотоприемник ФД19-КК (7), а также видеокамера для контроля и визуализации записи.
Система контроля и визуализации записи предназначена для автоматического считывания результатов записи в режимах поиска центра вращения заготовки и тестирования светочувствительного материала. В качестве подсвечивающего луча используются три пучка лазеров с длинами волн, равными λ = 405, 532, 648 нм, с уровнем мощности, лежащим ниже порога чувствительности материала записи. В режиме контроля записи отраженный от контролируемой поверхности подсвечивающий пучок света собирается выходным микрообъективом 5, проходит через дихроичное зеркало 4 и светоделитель 6 и направляется линзами 8 и 9 на видеокамеру (3 Mp, Tucsen).
ЭКСПЕРИМЕНТАЛЬНЫЕ ИССЛЕДОВАНИЯ ПОГРЕШНОСТИ ОПРЕДЕЛЕНИЯ ПОЛОЖЕНИЯ ПОВЕРХНОСТИ ОБЪЕКТА ДАТЧИКОМ АВТОМАТИЧЕСКОЙ ФОКУСИРОВКИ
Оценка погрешности позиционирования микрообъектива осуществлялась экспериментально по величине сигнала рассогласования с ДАФ. На рабочем столе шпинделя с помощью вакуумного прижима была закреплена стандартная стеклянная подложка ППХ 102×102А ТУ11-79. С помощью индикаторной головки на радиусе 45 мм измерялся полный размах биения поверхности подложки за один оборот шпинделя. Подложка юстировалась таким образом, чтобы величина этих биений l достигала ±5 мкм. Затем шпиндель раскручивался до скорости 10 оборотов/c. Сначала измерялся размах сигнала рассогласования ΔDif = V1 с выхода ДАФ при отключенном ПИД-регуляторе. Согласно рис. 10а, величина V1 составила 2100 отн.ед.
Рис. 10.
Сигнал рассогласования ΔDif = V1 с выхода ДАФ при: а – отключенном ПИД-регуляторе; б – включенном ПИД-регуляторе.
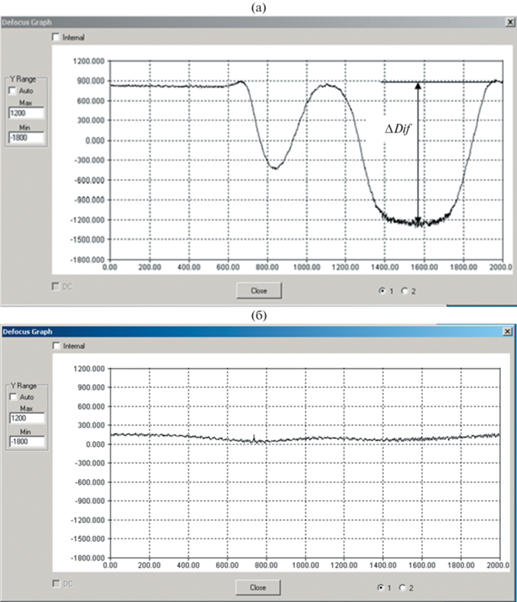
Затем включался ПИД-регулятор системы ДАФ и снова измерялся размах сигнала рассогласования ΔDif = V2. Согласно рис. 10б, его значение не превысило 150 отн.ед.
Погрешность автофокусировки ΔAF вычислялась как ΔAF = lV2/V1 и составила ΔAF = 0.7 мкм. Отсюда можно сделать вывод, что ДАФ подавляет амплитуду биения подложки в 14 раз. На практике используются стандартные подложки для фотолитографии с плоскостностью не более 1–3 мкм. В этом случае погрешность автофокусировки составляет не более 0.1 мкм, что значительно меньше глубины фокусировки записывающего микрообъектива.
Стабильность работы датчика автофокусировки вкупе со всеми устройствами, осуществляющими контроль перемещения сфокусированного луча и положения заготовки (угловой датчик – модель RON886, фирма-производитель Heidenhain; лазерный энкодер – модель RLE10-SX-XD, фирма-производитель Renishaw), проверялась в ходе экспериментальных исследований разработанных КЛЗС. Для этого были синтезированы дифракционные структуры на поверхности стеклянных подложек методом прямой лазерной записи профиля в фоторезисте с последующим переносом профиля в стекло с помощью ионно-плазменного травления [10]. Ошибка волнового фронта при изготовлении бинарных дифракционных линз с помощью КЛЗС на основе полупроводникового лазера не превышает λ/100, что свидетельствует о высоких технических характеристиках КЛЗС.
ЗАКЛЮЧЕНИЕ
Проведен анализ оптической схемы датчика автоматической фокусировки на основе ножа Фуко с использованием программы Zemax для проектирования оптических систем. Установлено, что инверсия разностного сигнала на фотоприемнике и ошибочное определение смещения возникают из-за фокусировки излучения в плоскости ножа Фуко. Показано, что путем изменения расстояния между ножом Фуко и рабочим микрообъективом можно увеличивать или уменьшать рабочий диапазон датчика.
Выявлено, что при угле наклона поверхности более 8° происходят инверсия разностного сигнала датчика автоматической фокусировки и уменьшение рабочего расстояния более чем в два раза. Это накладывает ограничения на радиус кривизны оптической поверхности, на которой происходит запись микро- и наноструктур.
Показано, что в двухканальной схеме лазерного фотопостроителя для компенсации продольной хроматической аберрации микрообъектива необходимо менять расходимость рабочих излучений с длинами волн 405 и 532 нм для фокусировки пятен в плоскости наилучшей фокусировки зондирующего излучения датчика автоматической фокусировки на основе ножа Фуко (λ = 658 нм).
На основании компьютерного моделирования датчика автоматической фокусировки на основе ножа Фуко был спроектирован и изготовлен микроскоп записи для круговых лазерных записывающих систем. Предложенные авторами технические решения были использованы при разработке коммерческих моделей круговых лазерных записывающих систем.
Проведены испытания разработанного датчика в составе круговой лазерной записывающей системы, в результате которых установлена погрешность определения положения поверхности (не более 0.1 мкм). Погрешность данного датчика оценивалась в совокупности с погрешностями датчиков, входящих в состав лазерных круговых записывающих систем. Для этого были синтезированы бинарные дифракционные линзы и измерена ошибка волнового фронта, которая не превысила λ/100.
Список литературы
Skidanov R.V., Ganchevskaya S.V., Vasil’ev V.S., Blank V.A. // J. Opt. Technol. 2022. № 89. P. 132–136. https://doi.org/10.1364/JOT.89.000132
Gerhard C. Optics Manufacturing: Components and Systems. CRC Press. 2017. P. 325. ISBN: 9781351228367. https://doi.org/10.1201/9781351228367
Полещук А.Г., Корольков В.П., Вейко В.П., Заколдаев Р.А., Сергеев М.М. // Автометрия. 2018. № 2. С. 3. https://doi.org/10.15372/AUT20180201
Завьялова М.А. Дис. … канд. техн. наук, Новосибирск: Новосиб. гос. техн. ун-т, 2021.
Radtke D., Zeitner Uwe D. // Optics Express. 2007. V. 15. № 3. P. 1167. https://doi.org/10.1364/OE.15.001167
Taisheng Wang, Weixing Yu, Dengying Zhang, Chunrong Li, Hongxin Zhang, Wenbin Xu, Zhijun Xu, Hua Liu, Qiang Sun, Zhenwu Lu // Optics Express. 2010. V. 18. № 24. P. 25102. https://doi.org/10.1364/OE.18.025102
Luo J., Liang Y., Yang G. // Optical Engineering. 2011. V. 50 (7). P. 073601. https://doi.org/10.1117/1.3597327
Верхогляд А.Г., Завьялова М.А., Качкин А.Е., Кокарев С.А., Корольков В.П. // Датчики и системы. 2015. № 9–10. С. 45.
Handbook of Optics. MacGraw-Hill Companies. Inc. 1995. V. I. P. 31.14.
Chugui Yu.V., Verkhoglyad A.G., Zavyalov P.S., Sysoev E., Kulikov R.V., Vykhristyuk I.A., Zavyalova M.A., Poleshchuk A.G., Korolkov V.P. // Int. J. of Automation Technology. 2015. V. 9. № 5. P. 515.
Дополнительные материалы отсутствуют.
Инструменты
Приборы и техника эксперимента