Теплоэнергетика, 2023, № 6, стр. 56-66
Результаты исследования регулирующего клапана с обратным подводом пара
В. Г. Грибин a, *, О. М. Митрохова a, А. В. Шерстнева a, П. М. Нестеров a
a Национальный исследовательский университет “Московский энергетический институт”
111250 Москва, Красноказарменная ул., д. 14, Россия
* E-mail: GribinVG@mpei.ru
Поступила в редакцию 19.07.2022
После доработки 13.12.2022
Принята к публикации 23.12.2022
Аннотация
Рассмотрены различные варианты конструкций регулирующих клапанов и способы компоновки органов парораспределения. Выявлено, что традиционная прямоточная схема регулирующего клапана не всегда отвечает требованиям по размещению оборудования паротурбинной установки и приводит к дополнительным потерям энергии. Предлагается использовать регулирующий клапан принципиально новой конструкции – с обратным подводом пара. Спроектирована и создана экспериментальная установка для исследования регулирующего клапана с обратным подводом пара, составлена схема измерений его характеристик. На экспериментальной установке по предлагаемой схеме можно исследовать как базовую конструкцию регулирующего клапана с обратным подводом пара, так и усовершенствованные ее варианты. Используя схему измерений, можно определить массовый расход рабочей среды, гидравлическое сопротивление тракта клапана, силовые и вибродинамические характеристики регулирующего клапана. Приводятся результаты математического моделирования и экспериментального исследования проходного тракта блока регулирующего клапана с обратным подводом пара. Предложены конструктивные изменения нижней половины клапанной коробки, благодаря которым снижаются потери давления и гидравлические потери и уменьшаются статические и динамические усилия, действующие на шток. Показана возможность создания экономичного и надежного клапана с обратным подводом пара, который может быть использован в системах парораспределения паровых турбин. Разработанную конструкцию регулирующего клапана с обратным подводом пара целесообразно применять для упрощения компоновки паротурбинной установки с клапанными коробками, расположенными на корпусе турбины.
Несмотря на многочисленные исследования регулирующих клапанов, проблема их совершенствования по-прежнему остается острой, так как в ряде случаев именно из-за низкой надежности этого вида трубопроводной арматуры бывает невозможно обеспечить бесперебойную работу паровых турбин. Даже если исключить требования по надежности, выбор регулирующего клапана для конкретной турбомашины будет сопровождаться решением многих проблем. Конструкция регулирующего клапана должна обеспечивать не только низкий уровень сопротивления, допустимое значение силы, действующей на шток, и вибронадежность на всех режимах, но и удобство его компоновки на корпусе турбины.
В настоящее время существует множество вариантов конструктивного исполнения регулирующих клапанов [1]. Подавляющее большинство из них имеют традиционную прямоточную схему, при которой пар вначале поступает в клапанную коробку, а затем при подъеме клапана через выпускной диффузор и паропровод – в корпус турбины. Однако такая схема из-за конструкционных и габаритных ограничений не всегда отвечает компоновочным требованиям при размещении органов парораспределения и приводит к дополнительным потерям энергии. Поэтому необходимо было найти принципиально иные решения, которые можно было бы как реализовать в рамках существующих систем парораспределения с сохранением механизма управления каждым клапаном, так и использовать при создании совершенно новых конструкций.
Одним из таких решений может стать регулирующий клапан с обратным подводом пара, в котором пар подводится под чашу, затем проходит клапанную коробку и дальше через выпускной патрубок и соединительный трубопровод поступает в турбомашину. Такая конструкция в ряде случаев позволяет значительно упростить компоновку клапанов и избежать дополнительных гидравлических потерь на участках с поворотами паровпускного тракта.
Однако следует отметить, что конструкции клапанов с обратным подводом пара проигрывают клапанам прямоточного исполнения по экономичности и поэтому не нашли широкого применения в системах паровпуска турбомашин, выпускаемых ведущими производителями. В научно-технической литературе практически отсутствуют данные о профилировании и характеристиках такого типа клапанов. В настоящей статье представлены результаты расчетно-экспериментальных исследований, благодаря которым удалось разработать конкурентоспособный клапан с обратным подводом пара.
В ряде конструкций паротурбинных установок проблемы, связанные с компоновкой системы паровпуска, решаются применением горизонтально расположенных клапанов, при этом возникают трудности, связанные том числе с возможностью заклинивания штоков в процессе эксплуатации.
Принимая во внимание сложность изготовления экспериментальных моделей и их высокую стоимость, исследования целесообразно проводить, совмещая расчетно-теоретические методы с опытной проверкой результатов, обеспечивающей получение достоверных данных, которые могут быть положены в основу создания принципиально новых высокоэкономичных и надежных конструкций клапанов.
Далее рассматриваются результаты расчетных и экспериментальных исследований регулирующего клапана с обратным подводом пара и анализируются его расходные, силовые и вибродинамические характеристики.
ЭКСПЕРИМЕНТАЛЬНАЯ МОДЕЛЬ РЕГУЛИРУЮЩЕГО КЛАПАНА И СХЕМА ИЗМЕРЕНИЙ ЕГО ХАРАКТЕРИСТИК
Для проведения исследований силовых, расходных и вибродинамических характеристик клапана с обратным подводом пара была спроектирована и изготовлена экспериментальная установка, внешний вид которой показан на рис. 1, а продольный разрез модели и схема измерений – на рис. 2.
Рис. 2.
Экспериментальная модель регулирующего клапана и схема измерений его характеристик. 1 – корпус клапана; 2 – сменная чаша клапана; 3 – шток; 4 – сменная клапанная коробка; 5 – подводной конфузор; 6 – отводной трубопровод; 7 – S-образный датчик, воспринимающий статические и динамические составляющие сил на штоке клапана; 8 – датчик вибродинамических измерений; 9 – датчик определения акустического давления. Избыточное давление: Δpi – статическое; Δp0i – полное; i – место измерения: 1 – перед клапаном (в подводном конфузоре); 2 – в клапанной коробке; 3 – за клапаном (перед отводным трубопроводом); 4 – за отводным трубопроводом
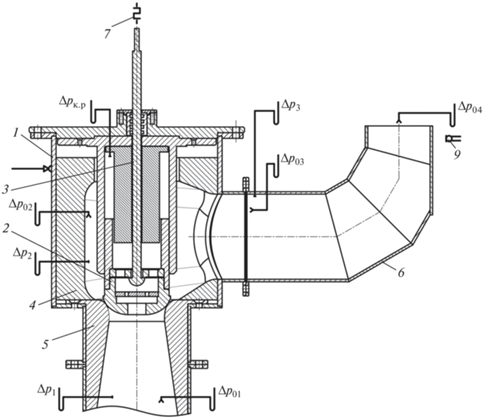
Модель регулирующего клапана состоит из корпуса, сменной чаши, штока, сменной клапанной коробки, подводного конфузора и отводного трубопровода.
Конструкция модели соответствует типовому клапану с обратным подводом пара с разгрузкой по давлению, который используется в частях турбин со средним давлением.
Модель устанавливается на ресивере воздушного стенда, из которого по подводному конфузору в клапан поступает воздух. Открытие клапана осуществляется с помощью координатника на крышке корпуса клапана, в разрыв штока которого помещается S-образный датчик силомера ZF.
Выхлоп воздуха происходит в атмосферу, что не только облегчает монтаж новых рабочих частей, но и позволяет при необходимости проводить траверсирование выходного сечения модели. С использованием модели исследуется блок клапана с обратным подводом пара в широком диапазоне чисел Маха М и Рейнольдса Re.
Схема измерений, приведенная на рис. 2, предназначена для определения силовых, вибродинамических и расходных характеристик клапана.
Для исследования силовых характеристик моделей клапанов применяется многофункциональный измерительный прибор Handy Scope2, разработанный фирмой Tie Pie Engineering (Нидерланды). Его измерительным элементом является S-образный датчик типа ZF с установленными на нем тензодатчиками, воспринимающими как статические, так и динамические составляющие сил на штоке клапана. Датчик работает как на растяжение, так и на сжатие.
В схеме имеются также зонды полных и статических давлений, установленные перед клапаном, за ним и в клапанной коробке.
Кроме обычных пневмозондов при испытаниях использовались малоинерционные датчики типа XTEL-140M-1,7BARA, фиксирующие как абсолютное давление, так и его переменную составляющую.
Измерение расхода воздуха, поступающего в клапан, проводилось на трубопроводе с помощью мерного сопла Вентури.
МЕТОДИКА ОБРАБОТКИ И ПРЕДСТАВЛЕНИЯ ОПЫТНЫХ ДАННЫХ
Определение расходных характеристик регулирующего клапана осуществляется при различных подъемах чаши при постоянном перепаде давления.
Приведенный расход воздуха q через клапан вычисляют по выражению
где ${{G}_{{\max t}}},$ ${{G}_{{\text{д}}}}$ – максимальный теоретический и действительный массовый расход, кг/с.Действительный расход воздуха через проточную часть клапана рассчитывают по следующей формуле, используя данные измерений, проведенных с помощью расходомерного сопла Вентури:
Коэффициент $\alpha $ и поправочный множитель ${{\varepsilon }_{a}}$ находят по справочным таблицам [2] и уточняют по результатам тарировочных испытаний с помощью мерных суживающихся сопл.
Теоретический максимальный расход ${{G}_{{\max t}}}$ рабочей среды через клапан рассчитывают по выражению
Абсолютное давление перед клапаном определяют как сумму барометрического давления $B$ и избыточного давления полного торможения $\Delta {{p}_{0}}$, измеренного в ресивере:
Силовые характеристики исследованных моделей клапанов представляют в виде безразмерных зависимостей:
где $\bar {h} = {h \mathord{\left/ {\vphantom {h {{{D}_{{\min }}}}}} \right. \kern-0em} {{{D}_{{\min }}}}}$ – относительный подъем штока регулирующего клапана; $h$ – его подъем, м; ${{D}_{{\min }}}$ – минимальный диаметр седла, м; $\varepsilon = {B \mathord{\left/ {\vphantom {B {{{p}_{0}}}}} \right. \kern-0em} {{{p}_{0}}}}$ – относительное давление.Безразмерное усилие, действующее на шток клапана, вычисляют по формуле
Потери давления в клапане оцениваются по коэффициенту гидравлического сопротивления
где ${{p}_{1}}$ – давление перед клапаном, Па; ${{p}_{2}}$ – давление за клапаном, Па; ${{\rho }_{1}},$ ${{с}_{1}}$ – плотность, кг/м3, и скорость, м/с, газа на входе в клапан соответственно.Показания всех малоинерционных датчиков, определяющих силу, давление (статическое и полное), вибрацию и акустическое давление, выведены на измерительный комплекс МИК-200М (производства НПО “Мера”, Россия).
ИССЛЕДОВАНИЯ БАЗОВОГО ВАРИАНТА РЕГУЛИРУЮЩЕГО КЛАПАНА
Проходной тракт исследуемого клапана образован типовой клапанной коробкой и сферической чашей (см. рис. 2). Такого рода конструкции вполне обоснованно широко используются в регулирующих и стопорных клапанах прямоточного типа. Однако, как показали проведенные испытания, такое конструкционное решение приводит к недопустимо большим потерям энергии в клапанах с обратным подводом пара.
На рис. 3 показаны зависимости безразмерного расхода $q$ от относительного давления $\varepsilon $ при фиксированных значениях относительного подъема клапана $\bar {h}.$ На рисунке хорошо видно, что при значениях $\varepsilon $ < 0.75 наступает режим критического истечения, и при дальнейшем снижении относительного давления $\varepsilon $ при фиксированном положении открытого клапана безразмерный расход через него уже не меняется. Полученные данные свидетельствуют также о том, что при таком варианте блока клапана возникают очень большие потери давления: так, при $q$ = 0.3 потери давления в клапане равны 4%, а при $q$ = 0.4 соответствуют 8%.
Рис. 3.
Расходная характеристика $q = f\left( \varepsilon \right)$ исходного регулирующего клапана. $\bar {h}{\text{:}}$ 1 – 0.327; 2 – 0.280; 3 – 0.234; 4 – 0.187; 5 – 0.140; 6 – 0.093; 7 – 0.084
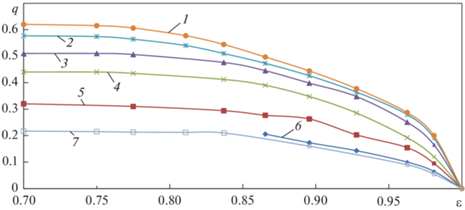
Коэффициент гидравлического сопротивления блока клапана, определенный по формуле (1), при полном открытии клапана ($\bar {h}$ = 0.327) составляет 4.61.
Полученные результаты можно объяснить только наличием участков с недопустимо высокими градиентами давления, приводящими к отрывному режиму течения в проточной части исследуемого клапана.
Особенности конструкции клапана отразились и на его безразмерных силовых характеристиках (рис. 4). На приведенных графиках хорошо видно, что характер изменения безразмерного усилия на штоке существенно отличается от “типичной” картины, свойственной прямоточным клапанам. В прямоточных клапанах безразмерное усилие при фиксированном $\varepsilon $ по мере открытия клапана быстро растет до максимального значения при $\bar {h}$ ≈ 0.10, а затем снижается до минимума при полном подъеме штока клапана [3].
Рис. 4.
Безразмерная силовая характеристика исходного регулирующего клапана ${{\bar {Q}}_{0}} = f\left( {\bar {h},\varepsilon } \right).$ ε: 1 – 0.700; 2 – 0.811; 3 – 0.837; 4 – 0.865; 5 – 0.896; 6 – 0.928; 7 – 0.963
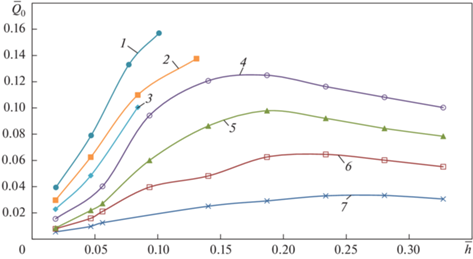
Таким образом, в реальном прямоточном регулирующем клапане по мере его открытия сила на штоке снижается и становится совсем малой при полном открытии клапана.
Кроме того, при наличии выталкивающей силы, действующей на шток, усилие, направленное на него, вообще может поменять знак, и свободно висящая на штоке чаша клапана, находящаяся в нестационарном потоке с высоким уровнем пульсации давления, может потерять осевую устойчивость.
Поэтому во избежание вероятности развития автоколебаний в регулирующих разгруженных клапанах используют разного рода паровые подгрузки, включающиеся в режимах резкого снижения силы на штоке.
Совершенно другая картина наблюдается в клапане с обратным подводом пара. Сила на штоке очень медленно растет от минимального значения (отрывная сила) до момента относительного подъема $\bar {h}$ ≈ 0.05, после чего начинает интенсивно увеличиваться до $\bar {h}$ ≈ 0.08–0.10, затем замедляется, но продолжает повышаться до максимальных значений при $\bar {h}$ ≈ 0.15–0.20, после чего медленно снижается до полного открытия клапана.
Поэтому в клапанах с обратным подводом пара наиболее проблемными для обеспечения устойчивости являются режимы при малых подъемах, а максимальные усилия в реальных клапанах будут фиксироваться при средних и больших подъемах.
Измерения динамической составляющей силы на штоке показали, что исследуемый клапан обладает низкой вибронадежностью практически при всех подъемах клапана, причем при малых подъемах $\bar {h}$ ≈ 0.019 динамические силы не только велики, но и имеют резонансный характер.
Динамические составляющие силы на штоке при всех подъемах $\bar {h}$ росли с увеличением расхода (перепада давлений) и, самое главное, оставались очень большими даже при полном открытии клапана.
На рис. 5 приведены результаты измерения вибродинамических характеристик при полном открытии клапана ($\bar {h}$ = 0.327) и “рабочем” перепаде давлений $\varepsilon $ = 0.865. На представленных графиках показаны интегральные замеры изменения силы $Q$ за определенный период времени $\tau $ (см. рис. 5, а), амплитудно-частотная характеристика, при которой по оси ординат отложены колебания силы ${{A}_{{dB}}}$ (см. рис. 5, б), и амплитудно-частотный спектр, в котором по оси ординат указаны колебания силы ${{A}_{i}}$ (см. рис. 5, в).
Рис. 5.
Результаты измерения сил на штоке исходного клапана при $\bar {h}$ = 0.327 и $\varepsilon $ = 0.865. а – интегральные замеры изменения силы $Q$ за определенный временной период $\tau $; б – амплитудно-частотная характеристика; в – амплитудно-частотный спектр
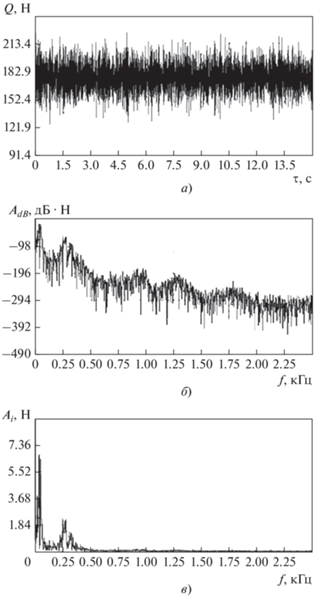
Значение ${{A}_{{dB}}}$ численно равно десятичному логарифму безразмерного отношения измеренной физической величины ${{A}_{i}}$ к одноименной физической величине ${{A}_{0}}$, принимаемой за исходную (базовую), умноженному на десять:
В данном случае ${{A}_{{dB}}}$ на графике (см. рис. 5, б) изменяется по частоте f. Значение ${{A}_{0}}$ равно среднестатистической силе на штоке клапана (базовая величина), ${{A}_{i}}$ – динамическая составляющая ${{A}_{0}}$, которая вычисляется для каждой частоты по формуле
В сложных каналах пульсации давления всегда довольно существенные и растут с увеличением расхода через исследуемый канал, но в рамках настоящего исследования наибольший интерес представляют пульсации давления в клапанной коробке и клапанном канале, образованном нижней поверхностью чаши и входной частью диффузорного седла, так как именно от них зависят значение и изменение динамической силы на штоке. Постоянно меняющееся давление над чашей клапана и под ней приводит к появлению на штоке динамической составляющей силы, которая достигает максимума, когда пульсации над чашей и под ней находятся в противофазе.
Приведенные на рис. 5 графики свидетельствуют о низкой вибронадежности блока клапана на всех его подъемах. Недопустимые пульсации силы появляются уже при относительно небольших перепадах давления $\varepsilon $ < 1.
Таким образом, по результатам проведенных испытаний можно сделать вывод о необходимости серьезной доработки базового варианта регулирующего клапана с обратным подводом пара.
МАТЕМАТИЧЕСКОЕ МОДЕЛИРОВАНИЕ ТЕЧЕНИЯ ПОТОКА В ПРОТОЧНОЙ ЧАСТИ РЕГУЛИРУЮЩЕГО КЛАПАНА
Для моделирования течения в проточной части регулирующего клапана использовалась гибридная расчетная сетка, состоявшая из призматических и тетраэдрических ячеек. Общее число элементов расчетной сетки составило 15 738 833, размер первого пристеночного слоя ячеек – 2 мкм, количество слоев элементов в пограничном слое – 25.
Значение y+ (безразмерное расстояние от стенки, используемое для оценки высоты первой ячейки сетки в пограничном слое) было меньше 1 в пределах всей расчетной области, что свидетельствует об удовлетворительном качестве сетки для выбранного расчетного метода.
Расчет был выполнен в программном коде ANSYS Fluent версии 16.0 со следующими настройками:
стационарный решатель Pressure-based в абсолютной системе координат;
Realizable k–ε-модель турбулентности с функцией Enhanced Wall Treatment (улучшенное моделирование пристеночных течений);
сухой пар с линейно зависящими от температуры свойствами в качестве рабочего тела;
второй порядок дискретизации для всех уравнений.
Сходимость решения достигалась после 8000 итераций. Дополнительные 2000 итераций выполнялись для проверки устойчивости решения. Контролировавшиеся с помощью мониторов значения давлений и скоростей на входе и выходе модели, а также давления в двух точках на неподвижных стенках изменялись менее чем на 2% собственных абсолютных значений в течение последних 2000 итераций, что свидетельствует о полной сходимости решения.
Сравнение результатов расчетов с данными экспериментов, полученных при исследовании базовой модели, показало возможность применения разработанной методики для исследования характеристик течения и профилирования проточной части клапанов различных конструкций.
В процессе исследований был выявлен сложный пространственный характер течения пара в полости клапана. На рис. 6 показано распределение скоростей в полости исследуемого клапана. Хорошо видно, что на входном участке клапанной коробки находится зона развитого отрыва потока, начинающаяся непосредственно от горла подводного конфузора.
Поле скоростей на выходе из горла конфузора крайне неравномерно. Максимальные значения скорости на стенке почти в 3 раза превышают скорость в центральной части горла, где поток, испытывающий тормозящее воздействие чаши клапана, которая имеет очень большое лобовое сопротивление, стремится в зону меньшего сопротивления, т.е. в зону, примыкающую к стенке седла.
Образовавшаяся на периферии входного участка высокоскоростная струя отрывается от стенки на входе в клапанную коробку, обтекает чашу и стенки клапана и далее сворачивается в вихревые шнуры (рис. 7), возникающие из-за поворота потока на 90° и сохраняющиеся до выхода из блока клапана.
Полученная картина течения на входном участке клапанной коробки обусловлена целым рядом причин: большой входной неравномерностью поля скоростей, тормозящим эффектом чаши клапана и кризисным ростом проходной площади этого участка тракта.
Относительная площадь проходного тракта $\bar {F} = {{{{F}_{i}}} \mathord{\left/ {\vphantom {{{{F}_{i}}} {{{F}_{2}}}}} \right. \kern-0em} {{{F}_{2}}}}$ от горла подводного конфузора до центрального сечения клапанной коробки (где ${{F}_{i}}$ – текущее значение площади, ${{F}_{2}}$ – площадь горла подводного конфузора) увеличивается в 3.5 раза. Естественно, что такая большая степень расширения на коротком участке подводного тракта неизбежно приводит к развитому отрыву потока.
Результаты математического моделирования показали, что главной причиной увеличения потерь в регулирующих клапанах с обратным подводом пара является то, что они выполняются по принципу обычных прямоточных клапанов, в которых внутренний объем клапанных коробок, по сути, играет роль ресивера, обеспечивающего равномерный подвод пара под чашу клапана в отводной диффузор. В клапане с обратным подводом пара роль отводного диффузора для частичного восстановления давления должен выполнять канал, образованный специально профилированной чашей, седлом и внутренним обводом клапанной коробки.
В усовершенствованном варианте исследуемого клапана проходной тракт был сформирован новыми осесимметричной клапанной коробкой и профилированной чашей (рис. 8).
Главная особенность предлагаемой конструкции чаши клапана – профилированный входной участок, направленный навстречу потоку. Такой профиль чаши совместно с уменьшенными проходными сечениями клапанной коробки позволили сформировать в выходной части клапанного канала диффузорный участок с приемлемой для безотрывного течения степенью расширения ${{{{F}_{i}}} \mathord{\left/ {\vphantom {{{{F}_{i}}} {{{F}_{2}}}}} \right. \kern-0em} {{{F}_{2}}}}$ = 2.2.
Испытания исследуемого регулирующего клапана полностью подтвердили целесообразность проведенной модернизации.
На рис. 9 представлена расходная характеристика нового клапана. На графике видно, что относительный приведенный расход $q$ заметно вырос по сравнению с расходом базовой конструкции клапана. Так, потери давления при $q$ = 0.3 составили всего 2.5%, а при $q$ = 0.4 не превысили 6%.
Рис. 9.
Расходная характеристика $q = f\left( \varepsilon \right)$ нового регулирующего клапана. $\bar {h}{\text{:}}$ 1 – 0.327; 2 – 0.280; 3 – 0.243; 4 – 0.196; 5 – 0.150; 6 – 0.103; 7 – 0.075; 8 – 0.056
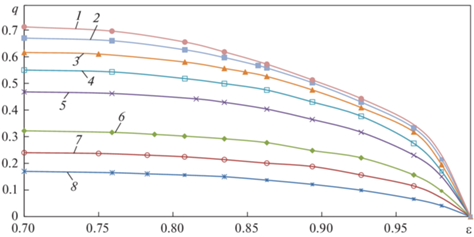
Коэффициент гидравлического сопротивления нового клапана, определенный по формуле (1), равен 3.34.
Достигнутое снижение потерь энергии оказалось возможным благодаря перепрофилированию проходного тракта клапана, которое позволило избежать отрыва потока в выходных сечениях клапана с обратным подводом пара (на входном участке клапанной коробки при прямоточном исполнении клапана). По представленным на рис. 10 безразмерным силовым характеристикам клапана видно, насколько существенно внесенные в конструкцию клапана изменения помогли уменьшить силы, действующие на его шток. На начальном участке кривых по мере подъема клапана $\bar {h}$ силы росли, далее несколько сокращались до $\bar {h}$ ≈ 0.052 и затем снова увеличивались до своих максимальных значений при $\bar {h}$ ≈ ≈ 0.15, после чего плавно снижались до полного открытия клапана.
Рис. 10.
Безразмерная силовая характеристика нового регулирующего клапана ${{\bar {Q}}_{0}} = f\left( {\bar {h},\varepsilon } \right).$ ε: 1 – 0.460; 2 – 0.500; 3 – 0.759; 4 – 0.783; 5 – 0.808; 6 – 0.835; 7 – 0.863; 8 – 0.894; 9 – 0.927; 10 – 0.962
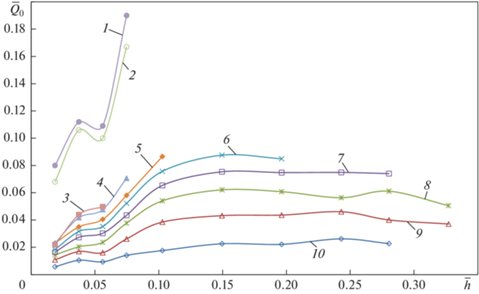
Если на начальном участке силовой характеристики значения сил на штоке были соизмеримы с силами, измеренными в первых двух вариантах, то начиная с подъема $\bar {h}$ = 0.05–0.06 силы в новом клапане стали заметно меньшими по сравнению с предыдущими образцами, причем разница росла по мере подъема клапана. Этот эффект обусловлен падением давления внутри клапана, полость которого соединена системой разгрузки с входным участком, где давление стало заметно ниже.
Улучшенная по сравнению с базовым образцом аэродинамика проходного тракта нового клапана позволила снизить и динамические колебания силы на штоке. Это наглядно иллюстрируют осциллограммы усилий, приведенные на рис. 11. Столь заметное улучшение характеристик по сравнению с базовым вариантом связано с уменьшением пульсаций давления как в клапанной коробке, так и в полости клапана, соединенной системой разгрузки с входным участком клапанной коробки.
Рис. 11.
Результаты измерения сил на штоке нового клапана при $\bar {h}$ = 0.280 и $\varepsilon $ = 0.962. а – интегральные замеры изменения силы Q за определенный временной период τ; б – амплитудно-частотная характеристика; в – амплитудно-частотный спектр
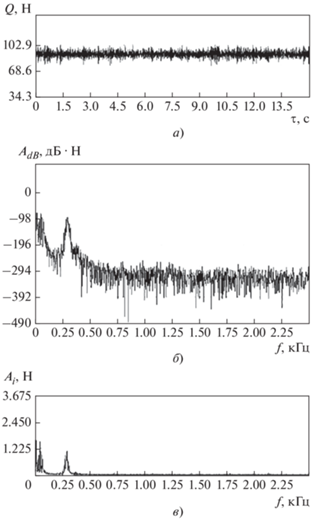
Оценивая характеристики нового регулирующего клапана с обратным подводом пара, следует отметить, что был создан конкурентоспособный, имеющий приемлемый уровень потерь давления и вибронадежности клапан с обратным подводом пара, который может быть использован в частях паровых турбин с высоким и средним давлением.
ВЫВОДЫ
1. Предложенная конструкция клапана с обратным подводом пара основана на базовом прямоточном варианте и не уступает по техническим характеристикам своему прототипу. Применение клапана разработанной конструкции целесообразно для упрощения компоновки паротурбинной установки с клапанными коробками, расположенными на корпусе турбины.
2. В результате перепрофилирования проточной части потери давления снижены на 2%, гидравлические потери – на 27%, уменьшены статические и динамические усилия, действующие на шток.
3. Разработанная и верифицированная математическая модель для изучения физических явлений и расчета характеристик регулирующих клапанов в частях среднего и высокого давления с прямым и обратным подводами пара была применена для проведения расчетов аэродинамической эффективности различных вариантов профилирования. В результате исследования было выявлено, что причиной недопустимого ухудшения характеристик при переходе от прямоточного к обратному течению рабочего тела в клапане являются развитые отрывные зоны, формирующиеся на выходном участке клапанной коробки.
Список литературы
Зарянкин А.Е., Симонов Б.П. Регулирующие и стопорно-регулирующие клапаны паровых турбин. М.: Изд-во МЭИ, 2005.
Преображенский В.П. Теплотехнические измерения и приборы: учеб. для вузов. 3-е изд., перераб. М.: Энергия, 1978.
Коротков В.В. Исследование и разработка стопорно-регулирующих клапанов, обладающих повышенной надежностью и низким аэродинамическим сопротивлением: автореф. дис. … канд. техн. наук. М.: МЭИ, 2003.
Дополнительные материалы отсутствуют.
Инструменты
Теплоэнергетика