Акустический журнал, 2020, T. 66, № 1, стр. 86-94
Лазерный оптико-акустический метод количественной оценки пористости углепластиков на основе измерения их акустического импеданса
Ю. Г. Соколовская a, *, Н. Б. Подымова a, А. А. Карабутов b, c, d
a МГУ имени М.В. Ломоносова, физический факультет
119991 Москва, ГСП-1 Ленинские горы 1, стр. 2, Россия
b МГУ имени М.В. Ломоносова, Международный учебно-научный лазерный центр
119991 Москва, ГСП-1 Ленинские горы 1, стр. 62, Россия
c Национальный исследовательский технологический университет “МИСиС”
119991 Москва, Ленинский пр. 4, Россия
d ИПЛИТ РАН – филиал ФНИЦ “Кристаллография и фотоника” РАН
117342 Москва, ул. Бутлерова 17А, Россия
* E-mail: yu.sokolovskaya@mail.ru
Поступила в редакцию 07.08.2019
После доработки 07.08.2019
Принята к публикации 05.09.2019
Аннотация
Предложен и экспериментально реализован метод измерения акустического импеданса для оценки пористости углепластиков, основанный на лазерном термооптическом возбуждении продольных акустических волн. Акустический импеданс исследуемого образца измеряется по величине первообразной ультразвукового импульса, отраженного от границы раздела иммерсионная жидкость-образец. Приведен метод расчета пористости углепластика по измеренной величине акустического импеданса. Исследованы образцы углепластиков с тремя различными схемами укладки углеродных волокон. Показано, что в исследованных углепластиках распределение локальной пористости является неравномерным вдоль плоскости укладки волокон. Величина пористости, усредненной по результатам оптико-акустических измерений, в пределах погрешности практически совпадает с данными рентгеновской томографии. Представленный метод определения пористости не требует определения объема и массы исследуемого объекта и может быть использован для диагностики композитных конструкций сложной формы.
ВВЕДЕНИЕ
Полимерные композиционные материалы находят все более широкое применение в современной промышленности [1–3]. Одним из примеров таких материалов являются углепластики – композиты, получаемые на основе углеродного волокна и органической матрицы [2]. Благодаря своей высокой прочности и жесткости они могут заменять металлы в тех случаях, когда необходимо снижение массы конструкции. В частности, в авиастроении такие материалы нередко используются в качестве силовых элементов крыльев самолетов [1, 4].
Известно, что из-за особенностей технологии изготовления в углепластиках уже на этапе производства возможно возникновение пористости [5–10]. Причиной образования пор может являться присутствие захваченного воздуха внутри пучков углеродных волокон, а также наличие влаги и летучих продуктов в наполнителе или связующем [10]. Пористость в углепластиках может присутствовать как в виде изолированных сферических пор микронного размера в слоях полимерной матрицы, так и в виде расслоений длиной до нескольких миллиметров, возникающих на границах раздела матрицы и наполнителя. Пористость оказывает негативное влияние на механические свойства материала: его упругие модули, межслойную сдвиговую прочность, прочность на сжатие, растяжение и изгиб, а также на усталостную долговечность [7, 9]. Это приводит к снижению срока службы композитных конструкций. Следовательно, актуальной задачей является разработка новых методов неразрушающего контроля, позволяющих обнаружить и количественно оценить пористость композитов, возникающую как при производстве материала, так и на различных этапах эксплуатации изделий.
В настоящее время для неразрушающей диагностики структуры композитов широко применяются ультразвуковые методы [3, 4, 11, 12]. Такие методы удобны для использования благодаря своей относительной простоте, оперативности, надежности и безопасности. В данной работе для исследования пористости углепластиков предлагается использовать метод, основанный на лазерном термооптическом возбуждении широкополосных импульсов продольных акустических волн (оптико-акустический эффект) [13–17]. Преимуществом оптико-акустического (ОА) метода является возможность создания коротких и мощных зондирующих ультразвуковых импульсов (с амплитудой до сотен мегапаскалей) в широком спектральном диапазоне (от долей до десятков мегагерц), что актуально для исследования сильно поглощающих и рассеивающих ультразвук материалов [15]. Подобный метод ранее успешно применялся для оценки пористости композитных материалов по величине затухания и дисперсии фазовой скорости ультразвуковых волн в режиме прямой пьезоэлектрической регистрации акустических сигналов, проходящих через весь исследуемый образец [13, 15]. Однако использование схемы с прямой регистрацией требует плоскопараллельности входной и выходной поверхностей исследуемых объектов, что не позволяет использовать ее для образцов с вариацией толщины и конструкций сложной формы. В работе [18] для исследования пористых композитов использовался ОА-метод с косвенной схемой регистрации акустических сигналов. При этом пористость определялась по величине скорости продольных акустических волн, измеряемой по времени двойного пробега зондирующего ультразвукового импульса по толщине образца. Это не позволяет в полной мере реализовать преимущества одностороннего доступа к объекту, т.к. требует точного измерения толщины исследуемой области. По этой причине оценка пористости с использованием данного метода в случае образцов и участков конструкций с непараллельностью входной и выходной поверхностей или переменной толщиной также является затруднительной. Кроме того, из-за особенностей технологий производства углепластиков даже для плоских изделий возможна некоторая вариация толщины от точки к точке. Поэтому с практической точки зрения представляется целесообразным разработать ОА метод, позволяющий оценивать пористость материала при одностороннем доступе без измерения толщины исследуемой области.
Целью настоящей работы является разработка лазерного ОА-метода количественной оценки пористости углепластиков, реализующего возможность одностороннего доступа к исследуемому объекту. Зависимость плотности материала и скорости распространения в нем продольных акустических волн от его пористости позволяет рассчитать локальную пористость в исследуемой области образца по экспериментально измеренной величине акустического импеданса этой области. Преимуществом предлагаемого метода является отсутствие необходимости измерения толщины образца, поэтому он может применяться для исследования углепластиковых конструкций и деталей. В работе исследовались образцы углепластика с тремя схемами армирования и различной средней пористостью. Для проверки правильности полученных результатов пористость нескольких выбранных образцов также определялась методом рентгеновской томографии.
МЕТОДИКА ИЗМЕРЕНИЯ АКУСТИЧЕСКОГО ИМПЕДАНСА
В настоящей работе для измерения величины акустического импеданса углепластиков использовался ОА-преобразователь с косвенной схемой регистрации акустических сигналов. Схема такого преобразователя представлена на рис. 1. Преобразователь аналогичен использованному в работе [19], за исключением наличия ОА-источника, позволяющего создавать зондирующий ультразвуковой импульс с заданной амплитудой и временной формой, которые определяются оптическими и теплофизическими свойствами источника, временным профилем интенсивности поглощенного лазерного импульса и граничными условиями возбуждения ультразвука [15]. С помощью оптоволокна в преобразователь доставлялось излучение Nd:YAG лазера с модуляцией добротности. Длительность лазерного импульса 10 нс, энергия в импульсе 100 мкДж, частота следования импульсов 500 Гц. Лазерное излучение через прозрачную призму под углом падает на поверхность ОА-источника (в качестве ОА-источника использовался черный полиэтилен). Призма находится в акустическом контакте с источником и одновременно является звукопроводом широкополосного пьезоэлектрического приемника. При поглощении лазерного импульса происходит неоднородный нестационарный нагрев приповерхностного слоя источника, его последующее тепловое расширение приводит к возникновению двух импульсов продольных акустических волн [18]. Один из них проходит в призму-звукопровод (обозначен на рис. 1 цифрой 1) и является зондирующим в данной системе, а другой через источник проходит в иммерсионную жидкость. Из-за рассогласования акустических импедансов иммерсионной жидкости (дистиллированной воды) и исследуемого образца часть сигнала отразится от границы раздела жидкость-образец (обозначена на рис. 1 цифрой 2), и будет зарегистрирована пьезоприемником с временной задержкой, соответствующей двойному пробегу импульса по слою иммерсионной жидкости и ОА-источнику. Такая схема позволяет проводить исследования при одностороннем доступе к объекту. Электрические сигналы с пьезоприемника передавались на цифровой осциллограф и затем обрабатывались на персональном компьютере. Запуск осциллографа был синхронизирован с лазерным импульсом.
Таблица 1.
Средние значения акустических импедансов и пористости для исследованных образцов углепластиков
№ образца | 〈Z〉OA × 106, кг/(м2 с) | 〈P〉OA, % | 〈P〉X-ray, % | |
---|---|---|---|---|
Группа № 1 | 1-1 | 4.39 ± 0.08 | <0.1 | <0.1 |
1-2 | 4.39 ± 0.08 | <0.1 | – | |
1-3 | 4.27 ± 0.07 | 0.8 ± 0.7 | – | |
Группа № 2 | 2-1 | 4.01 ± 0.07 | 3.4 ± 0.7 | 2.8 |
2-2 | 4.07 ± 0.07 | 2.7 ± 0.7 | 2.5 | |
2-3 | 3.90 ± 0.06 | 4.7 ± 0.7 | – | |
2-4 | 3.97 ± 0.07 | 4.5 ± 0.7 | – | |
2-5 | 4.06 ± 0.07 | 2.9 ± 0.7 | – | |
Группа № 3 | 3-1 | 4.06 ± 0.07 | 2.9 ± 0.7 | 2.6 |
3-2 | 4.08 ± 0.07 | 2.6 ± 0.7 | 2.5 | |
3-3 | 3.93 ± 0.07 | 4.3 ± 0.7 | – |
Амплитуды зондирующего импульса A0 и импульса, отраженного от границы вода–образец A, будут соотноситься как A = RA0, где $R = {{\left( {{{Z}_{{\text{c}}}} - {{Z}_{{{{{\text{H}}}_{{\text{2}}}}{\text{O}}}}}} \right)} \mathord{\left/ {\vphantom {{\left( {{{Z}_{{\text{c}}}} - {{Z}_{{{{{\text{H}}}_{{\text{2}}}}{\text{O}}}}}} \right)} {\left( {{{Z}_{{\text{c}}}} + {{Z}_{{{{{\text{H}}}_{{\text{2}}}}{\text{O}}}}}} \right)}}} \right. \kern-0em} {\left( {{{Z}_{{\text{c}}}} + {{Z}_{{{{{\text{H}}}_{{\text{2}}}}{\text{O}}}}}} \right)}}$ – коэффициент отражения продольной акустической волны от границы раздела сред, Zc=ρcCc, ${{Z}_{{{{{\text{H}}}_{{\text{2}}}}{\text{O}}}}} = {{\rho }_{{{{{\text{H}}}_{{\text{2}}}}{\text{O}}}}}{{C}_{{{{{\text{H}}}_{{\text{2}}}}{\text{O}}}}}$ – акустические импедансы композитного образца и воды [20]. Таким образом, коэффициент отражения и, соответственно, амплитуда отраженного сигнала будут зависеть от величины акустического импеданса образца. Однако это выражение не учитывает наличие затухания ультразвука в иммерсионной жидкости и ОА-источнике, а также рассеяние ультразвука на поверхности образца. Затухание в слое воды и в источнике может приводить к дополнительному изменению амплитуды и длительности отраженного сигнала по сравнению с зондирующим. Для исключения влияния этого затухания вместо зондирующего ультразвукового импульса предлагается использовать импульс, отраженный от опорной плоскопараллельной полированной кварцевой пластины с известными акустическими свойствами. Эта пластина помещается на место исследуемого образца. Коэффициент отражения продольных акустических волн от границы раздела вода-пластина рассчитывается как ${{R}_{{{\text{ref}}}}} = {{\left( {{{Z}_{{{\text{ref}}}}} - {{Z}_{{{{{\text{H}}}_{{\text{2}}}}{\text{O}}}}}} \right)} \mathord{\left/ {\vphantom {{\left( {{{Z}_{{{\text{ref}}}}} - {{Z}_{{{{{\text{H}}}_{{\text{2}}}}{\text{O}}}}}} \right)} {\left( {{{Z}_{{{\text{ref}}}}} + {{Z}_{{{{{\text{H}}}_{{\text{2}}}}{\text{O}}}}}} \right)}}} \right. \kern-0em} {\left( {{{Z}_{{{\text{ref}}}}} + {{Z}_{{{{{\text{H}}}_{{\text{2}}}}{\text{O}}}}}} \right)}},$ где импеданс кварца Zref = 13.1 × 106 кг/(м2 с), импеданс воды ${{Z}_{{{{{\text{H}}}_{{\text{2}}}}{\text{O}}}}}$ = 1.49 × 106 кг/(м2 с) [21]. Тогда амплитуда ультразвукового сигнала, отраженного от границы раздела вода-кварц, Aref = RrefA0, и, следовательно, R = RrefA/Aref. Отсюда можно вычислить акустический импеданс исследуемого композитного образца:
(1)
${{Z}_{{\text{c}}}} = {{Z}_{{{{{\text{H}}}_{{\text{2}}}}{\text{O}}}}}\frac{{1 + R}}{{1 - R}} = {{Z}_{{{{{\text{H}}}_{{\text{2}}}}{\text{O}}}}}\frac{{{{A}_{{{\text{ref}}}}} + {{R}_{{{\text{ref}}}}}A}}{{{{A}_{{{\text{ref}}}}} - {{R}_{{{\text{ref}}}}}A}}.$Таким образом, по измеренным амплитудам ультразвуковых сигналов A и Aref можно определить величину акустического импеданса образца углепластика. Однако амплитуда отраженного от образца сигнала A может также уменьшаться из-за рассеяния ультразвуковых волн на шероховатой поверхности углепластика и ее некоторой кривизны, при этом одновременно будет увеличиваться его длительность. Для учета рассеяния на шероховатой поверхности вместо амплитуд отраженных ультразвуковых сигналов предлагается использовать максимальные значения их первообразных, которые рассчитываются как:
где U(τ) – временной профиль регистрируемого ультразвукового сигнала. Тогда для расчета акустического импеданса исследуемого образца вместо (1) будет использоваться выражение:(3)
${{Z}_{{\text{c}}}} = {{Z}_{{{{{\text{H}}}_{{\text{2}}}}{\text{O}}}}}\frac{{{{I}_{{{\text{max}}\,{\kern 1pt} {\text{ref}}}}} + {{R}_{{{\text{ref}}}}}{{I}_{{\max }}}}}{{{{I}_{{{\text{max}}\,{\kern 1pt} {\text{ref}}}}} - {{R}_{{{\text{ref}}}}}{{I}_{{\max }}}}},$На рис. 2а показаны примеры зарегистрированных временных треков ультразвуковых сигналов для опорной кварцевой пластины и углепластикового образца. Наблюдаемая амплитуда отраженного сигнала для углепластикового образца будет заметно меньше, чем для опорной пластины, так как Zc< Zref. Отрицательные фазы сигналов возникают из-за дифракции акустических волн при распространении через призму-звукопровод. Отличие в отрицательных фазах, по-видимому, обусловлено небольшой кривизной поверхности исследуемого композитного образца, а также наложением последовательности импульсов, возникающих из-за отражения от периодических слоев углепластика. На рис. 2б, 2в показаны временной профиль ультразвукового импульса, отраженного от поверхности исследуемого образца углепластика (в увеличенном масштабе), и его первообразная. Момент времени, соответствующий максимуму первообразной, на временном профиле сигнала совпадает с моментом перехода от положительной фазы сигнала к отрицательной. Таким образом, значение Imax будет соответствовать полной площади положительной фазы отраженного от образца сигнала.
Рис. 2.
Примеры временных треков сигналов от опорной пластины и образца: (а) – зондирующий и отраженный сигналы, (б) – сигнал, отраженный от поверхности образца (в увеличенном масштабе) и (в) – его первообразная.
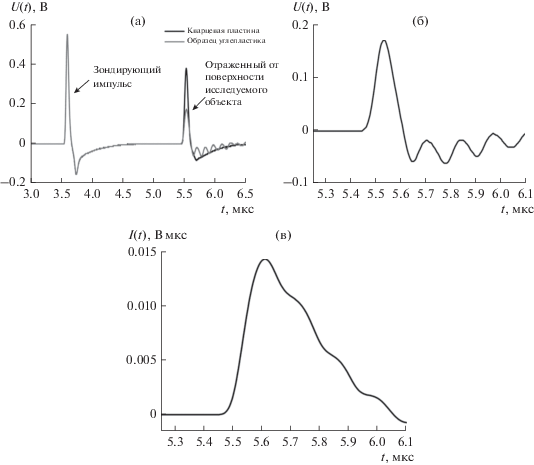
Характерный диаметр лазерного пучка на поверхности ОА-источника, и, соответственно, диаметр зондирующего ультразвукового пучка составляет 2–3 мм. Это позволяет проводить измерения акустических импедансов образцов в локальных участках характерного поперечного размера 2–3 мм.
МЕТОДИКА РАСЧЕТА ПОРИСТОСТИ
Пористость – объемное содержание газовых пор в материале – определяется как отношение суммарного объема пор в образце к его полному объему:
(4)
$P = \frac{{\Delta V}}{V} \times 100\% = \left( {1 - \frac{\rho }{{{{\rho }_{0}}}}} \right) \times 100\% ,$(5)
${{C}_{c}} = {{C}_{0}}\sqrt {1 - {{P}^{{{2 \mathord{\left/ {\vphantom {2 3}} \right. \kern-0em} 3}}}}} ,$(6)
$\begin{gathered} {{Z}_{{\text{c}}}} = \rho C = {{\rho }_{0}}{{C}_{0}}\left( {1 - P} \right)\sqrt {1 - {{P}^{{{2 \mathord{\left/ {\vphantom {2 3}} \right. \kern-0em} 3}}}}} = \\ = {{Z}_{{{\text{c0}}}}}\left( {1 - P} \right)\sqrt {1 - {{P}^{{{2 \mathord{\left/ {\vphantom {2 3}} \right. \kern-0em} 3}}}}} . \\ \end{gathered} $Следовательно, пористость углепластика может быть определена по измеренной величине его акустического импеданса при известном значении импеданса Zс0 для аналогичного по составу беспористого материала.
ИССЛЕДОВАННЫЕ ОБРАЗЦЫ УГЛЕПЛАСТИКОВ
Углепластики представляют собой материал, состоящий из чередующихся слоев полимерной матрицы и так называемой углеродной ткани, образованной из нескольких слоев углеродных волокон, собранных в ленты. Одним из главных преимуществ углепластиков является возможность подбирать определенную укладку волокон для конкретной задачи, т.е. в зависимости от геометрии будущей конструкции и предполагаемых нагрузок могут применяться различные схемы армирования материала [6, 24, 25]. Таким образом, прочностные свойства углепластиков зависят не только от свойств наполнителя и матрицы, но и от направлений укладки слоев.
В настоящей работе исследовались углепластики с тремя различными схемами укладки слоев углеродной ткани, условно разделенные на три группы. Все образцы углепластика представляли собой плоскопараллельные пластины размером 40 × 15 мм. В группу № 1 входит 3 образца со слоями, уложенными под углами 0°, 90°, ±45°, в группу № 2 – 5 образцов со слоями 0°, ±30°, ±45°, в группу № 3 – 3 образца со слоями 0°, 90°, ±45°. В группах № 1 и 3 соотношение числа слоев 0°, 90°, ±45° было различно (группа № 3 имела большее число слоев 0° и меньшее число слоев 90° по сравнению с группой № 1). Объемная концентрация матрицы и наполнителя во всех исследуемых образцах была одинакова. Примеры послойных изображений укладки углеродной ткани, полученных методом рентгеновской компьютерной томографии, показаны на рис. 3. Зондирующий ультразвуковой импульс при исследовании образцов распространяется перпендикулярно плоскости укладки слоев углеродной ткани.
Рис. 3.
Послойные изображения укладки углеродной ткани в углепластиках: (а) – слои 30°, 45°, 0°, (б) – слои 90°, 45°.
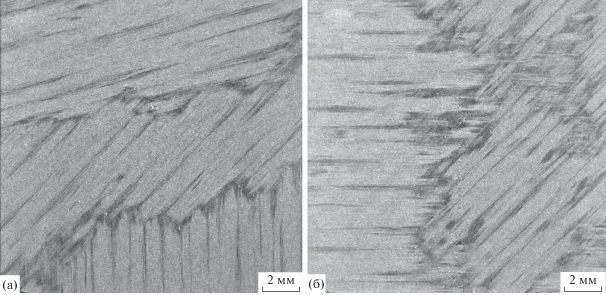
Практически во всех исследованных образцах присутствовала некоторая пористость, образовавшаяся в процессе производства материала. Для последующей проверки результатов, полученных лазерным оптико-акустическим методом, была проведена оценка пористости пяти выбранных образцов (1 образец из группы № 1 и по 2 образца из групп № 2 и 3) с помощью рентгеновской компьютерной томографии (см. ниже). Примеры томографических изображений сечений пористых образцов № 2-1 и № 3-1 приведены на рис. 4. Поры диаметром 20–120 мкм составляют приблизительно половину суммарной объемной пористости этих образцов, оставшаяся половина приходится на поры диаметром свыше 120 мкм.
ЭКСПЕРИМЕНТАЛЬНЫЕ РЕЗУЛЬТАТЫ И ОБСУЖДЕНИЕ
Величины акустических импедансов углепластиковых образцов определялись по первообразным ультразвуковых импульсов, отраженных от границы раздела вода‑образец, с использованием формулы (3). Примеры временных профилей отраженных ультразвуковых сигналов для образцов с Zc1 > Zc2 > Zc3 и их первообразные приведены на рис. 5. Относительная погрешность измерения амплитуды ультразвуковой волны (и, соответственно, максимума первообразной) определяется отношением сигнал/шум для системы регистрации акустических сигналов, а также нестабильностью энергии лазерных импульсов. Для используемой экспериментальной установки относительная погрешность ΔI/I = ΔA/A ≈ 1–1.2%, что приводит к относительной погрешности измерения акустического импеданса композита ΔZc/Zc ≈ 1.6–1.8%.
Рис. 5.
Примеры ультразвуковых сигналов, отраженных от поверхности: (а) – для образцов углепластиков с акустическими импедансами Zc1 > Zc2 > Zc3 и (б) – их первообразные.
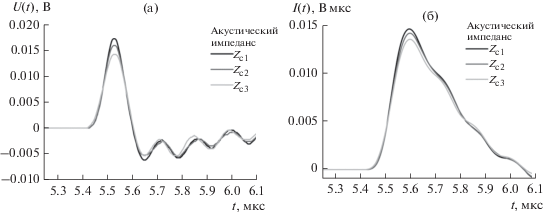
Вообще говоря, распределение пор в углепластиках вдоль плоскости укладки слоев углеродной ткани может быть неравномерным. Поэтому для оценки средней пористости образца и ее сравнения с данными рентгеновской томографии, измерение величины акустического импеданса и последующий расчет пористости проводились для нескольких участков каждого образца. Это позволяет определить так называемую локальную пористость. Как было сказано выше, представленная методика позволяет проводить измерения импеданса образца в локальных участках поперечного размера 2–3 мм. Измерение локальных величин акустического импеданса, и, соответственно, локальных пористостей в нескольких участках позволяет получить приблизительную величину усредненной пористости каждого из образцов.
Пористость углепластиковых образцов рассчитывалась по измеренным значениям импедансов с использованием формулы (6). Образец № 1-1 группы № 1 по данным рентгеновской томографии может считаться практически беспористым (P < 0.1%). Измерения, проведенные с использованием ОА-метода, показали, что изменения локальной величины акустического импеданса этого образца в исследованных участках не превышают 0.7% и не выходят за пределы погрешностей измерения (см. рис. 6а). Поэтому в качестве величины импеданса беспористого образца Zс0 в формуле (6) было взято максимальное значение импеданса для образца № 1-1. Это допустимо, так как концентрация полимерной матрицы и углеродного наполнителя во всех исследованных образцах одинакова.
Рис. 6.
(а) – Локальные значения акустического импеданса для образца № 1-1 и (б) – локальные значения пористости для образцов группы № 1, (в) – группы № 2 и (г) – группы № 3.
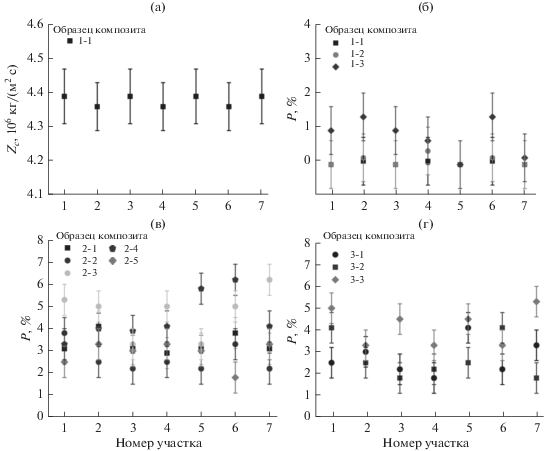
На рис. 6б приведены полученные значения локальных пористостей в семи исследованных точках каждого из образцов группы № 1. Видно, что в образце № 1-2 (как и в № 1-1) пористость также практически отсутствует (P < 0.1%). В образце № 1-3 имеются как беспористые участки, так и участки с некоторой локальной пористостью, не превышающей 1.4%, а в среднем пористость этого образца составляет менее 1%. На рис. 6в и 6г приведены значения локальных пористостей в исследованных участках для образцов группы № 2 и группы № 3. Из рисунков видно, что распределение локальной пористости вдоль плоскости укладки слоев в этих образцах действительно является неоднородным. Неоднородность пористости углепластиковых образцов можно количественно охарактеризовать величиной ΔP = (Pmax– Pmin)/Pmax, где Pmax и Pmin– максимальное и минимальное значения локальной пористости в исследованных участках данного образца. Для образцов группы № 2 значение ΔP в пределах каждого исследуемого образца меняется от 1.2 до 2.9%, в то время как для образцов группы № 3 оно варьируется от 2 до 2.3%. Таким образом, для образцов группы № 2 наблюдаемый разброс величины локальной пористости сильнее, чем для образцов группы № 3. Эта разница, по-видимому, связана с отличием схем укладки слоев углеродной ткани, что может приводить к различному распределению газовых пор в материале в процессе его изготовления.
В табл. 1 приведены средние значения акустического импеданса 〈Zc〉 для каждого из исследованных образцов, полученные ОА-методом, а также рассчитанные величины их средней пористости 〈P〉OA. Усредненная по N точкам пористость определяется как ${{\left\langle P \right\rangle }_{{{\text{OA}}}}} = \frac{1}{N}\sum\nolimits_{i = 1}^N {{{P}_{N}}} ,$ где PN – локальная пористость в N-й точке образца. Для пяти образцов также приведены величины суммарной пористости 〈P〉X-ray, полученные с помощью рентгеновской томографии. Из таблицы видно, что данные, полученные лазерным ОА-методом, в пределах погрешности измерений совпадают с результатами томографии. Таким образом, ОА-метод может быть использован для измерения акустических импедансов, оценки локальной и средней пористости углепластиков и распределения локальной пористости по образцу.
ЗАКЛЮЧЕНИЕ
В настоящей работе предложен и экспериментально реализован лазерный оптико-акустический метод количественной оценки пористости углепластиков на основе измерения их акустических импедансов. Разработана методика измерения акустического импеданса образца композита по первообразной ультразвукового сигнала, отраженного от поверхности композита на границе раздела иммерсионная жидкость–образец. Данный метод позволяет учесть возможное рассеяние ультразвуковых волн на шероховатой поверхности композитных образцов при измерении их импедансов, что особенно актуально для углепластиков, всегда имеющих некоторую шероховатость поверхности, обусловленную структурой углеродной ткани.
Показано, что в исследованных пористых образцах присутствует неоднородное распределение пористости в плоскости укладки слоев – локальная пористость в некоторых участках может значительно отличаться от средней по объему. Это связано с особенностями технологий изготовления материала. Распределение локальной пористости в углепластике также зависит от схемы укладки слоев углеродной ткани. Локальность исследования образцов в поперечном направлении составляла 2–3 мм. Для пяти образцов проведено сравнение величины средней пористости, измеренной лазерным оптико-акустическим методом, с результатами рентгеновской томографии. Полученные результаты практически совпадают в пределах погрешностей измерения.
Достоинством предложенного метода является возможность оперативной диагностики пористости материала при одностороннем доступе к исследуемому объекту без измерения его габаритов и массы, что может применяться для композитных конструкций сложной формы. Измерение локальной пористости и ее распределения позволяет обнаружить потенциально уязвимые участки композитной конструкции с повышенной пористостью. Метод может быть использован как для контроля качества получаемых композитов при модернизации технологий и подборе оптимальных условий производства, так и для диагностики изменений структуры композитов в процессе их эксплуатации или при усталостных испытаниях деталей и изделий.
Список литературы
Soutis C. Fibre reinforced composites in aircraft construction // Progress in Aerospace Sciences. 2005. V. 41. P. 143–151.
Chand S. Carbon fibers for composites // J. Mater. Sci. 2000. V. 35. P. 1303–1313.
Ibrahim M.E. Nondestructive evaluation of thick-section composites and sandwich // Composites Part A. 2014. V. 64. P. 36–48.
Зверев А.Я., Черных В.В. Экспериментальное определение акустических и виброакустических характеристик многослойных композитных панелей // Акуст. журн. 2018. Т. 64. № 6. С. 727–736.
Adams R.D., Cawle P. A review of defect types and nondestructive testing techniques for composites and bonded joints // NDT Int. 1988. V. 21. № 4. P. 208–222.
Перепелкин К.Е. Армирующие волокна и волокнистые полимерные композиты. СПб.: Научные основы и технологии, 2009. 380 с.
Scott A.E., Sinclair I., Spearing S.M., Mavrogordato M.N., Hepples W. Influence of voids on damage mechanisms in carbon/epoxy composites determined via high resolution computed tomography // Compos. Sci. Technol. 2014. V. 90. P. 147–153.
Stamopoulos A.G., Ilio A.D. On the predictive tools for assessing the effect of manufacturing defects on the mechanical properties of composite materials // Procedia CIRP. 2019. V. 79. P. 563–567.
Мурашов В.В., Румянцев А.Ф. Дефекты монолитных деталей и многослойных конструкций из полимерных композиционных материалов и методы их выявления. Часть 1. Дефекты монолитных деталей и многослойных конструкций из полимерных композиционных материалов // Контроль. Диагностика. 2007. № 4. С. 23–32.
Душин М.И., Донецкий К.И., Караваев Р.Ю. Установление причин образования пористости при изготовлении ПКМ // Электронный научный журнал “Труды ВИАМ”. 2016. № 6. С. 68–78.
Chimenti D.E. Review of air-coupled ultrasonic materials characterization // Ultrasonics. 2014. V. 54. P. 1804–1816.
Sachse W., Castagnede B., Grabec I., Kim K.Y., Weaver R.L. Recent developments in quantitative ultrasonic NDE of composites // Ultrasonics. 1990. V. 28. P. 97–104.
Карабутов А.А., Подымова Н.Б. Влияние пористости на дисперсию фазовой скорости продольных акустических волн в изотропных металломатричных композитах // Акуст. журн. 2017. Т. 63. № 3. С. 265–274.
Кожушко В.В., Палтауф Г., Кренн Х. Регистрация наносекундных оптико-акустических импульсов в стали // Акуст. журн. 2013. Т. 59. № 2. С. 279–282.
Карабутов А.А., Подымова Н.Б., Беляев И.О. Исследование влияния пористости на затухание ультразвука в углепластиковых композитах методом лазерно-ультразвуковой спектроскопии // Акуст. журн. 2013. Т. 59. № 6. С. 714–721.
Карабутов А.А., Подымова Н.Б., Соколовская Ю.Г. Локальные соотношения Крамерса-Кронига для коэффициента затухания и фазовой скорости продольных ультразвуковых волн в полимерных композитах // Акуст. журн. 2019. Т. 65. № 2. С. 182–189.
Юсупов В.И., Коновалов А.Н., Ульянов В.А., Баграташвили В.Н. Генерация акустических волн непрерывным лазерным излучением на торце оптического волокна в воде // Акуст. журн. 2016. Т. 62. № 5. С. 531–539.
Соколовская Ю.Г., Карабутов А.А. Лазерно-ультразвуковая дефектоскопия конструкций из мультиаксиальных полимерных композиционных материалов // Конструкции из композиционных материалов. 2018. № 1. С. 56–60.
Karabutov A.A., Podymova N.B. Nondestructive porosity assessment of CFRP composites with spectral analysis of backscattered laser-induced ultrasonic pulses // J. Nondestruct. Eval. 2013. V. 32. № 2. P. 315–324.
Karabutov A.A. (Jr.), Karabutov A.A., Sapohznikov O.A. Determination of the elastic properties of layered materials using laser excitation of ultrasound // Phys. Wave Phenomena. 2010. V. 18. № 4. P. 297–302.
Физические величины. Справочник. Ред. Григорьев И.С., Мейлихов Е.З. М.: Энергоатомиздат, 1991. 1232 с.
Поляков В.В., Головин А.В. Влияние пористости на скорости ультразвуковых волн в металлах // Письма в ЖТФ. 1994. Т. 20. № 11. С. 54–57.
Поляков В.В., Головин А.В. Упругие характеристики пористых материалов // ПМТФ. 1993. Т. 34. № 5. С. 32–35.
Тарнопольский Ю.М., Жигун И.Г., Поляков В.А. Пространственно-армированные композиционные материалы. Справочник. М.: Машиностроение, 1987. 224 с.
Любин Дж. Справочник по композиционным материалам. М.: Машиностроение, 1988. 447 с.
Дополнительные материалы отсутствуют.
Инструменты
Акустический журнал