Доклады Российской академии наук. Химия, науки о материалах , 2020, T. 492-493, № 1, стр. 59-63
Металломатричные нанокомпозиционные материалы Cu–C: синтез
Академик РАН А. И. Рудской *
Санкт-Петербургский политехнический
университет Петра Великого (ФГАОУ ВО СПбПУ)
Санкт-Петербург, Россия
* E-mail: rector@spbstu.ru
Поступила в редакцию 02.06.2020
После доработки 07.07.2020
Принята к публикации 21.07.2020
Аннотация
Представлен анализ результатов оригинальных исследований по синтезу гибридных композиционных материалов медь–углеродные наноструктуры, выполненных за последние пять лет в лабораториях СПбПУ Петра Великого под научным руководством автора. Рассмотрены особенности формирования структуры и свойств композиционных материалов в зависимости от метода синтеза, выбора и количества углеродных нанодобавок. Предложены возможные механизмы, определяющие физико-механические свойства материалов. На примере ряда характеристик (твердость, тепло- и электропроводность) показана возможность варьирования в широком диапазоне всего комплекса физико-механических свойств, что крайне актуально для практического использования гибридных композиционных материалов.
ВВЕДЕНИЕ
Сплавы на основе меди находят все большее применение в качестве материалов для электротехники и сварочного производства. Таким материалам необходимы высокие прочность, жаропрочность, износостойкость, твердость при одновременно больших значениях электро- и теплопроводности [1]. Сохранение прочностных свойств материала при высоких температурах (до 0.8–0.9 Тпл(К), где Тпл – температура плавления) достигается в дисперсно-упрочненных материалах, приготовленных методами порошковой металлургии. Для упрочнения медных сплавов в качестве упрочняющей фазы часто используются оксиды металлов, например, оксид алюминия, церия [2, 3].
Другой широко используемый класс гибридных материалов на основе меди – порошковые материалы системы медь–графит, которые используются, в основном, как антифрикционные материалы и материалы для скользящих электрических контактов. Однако они имеют довольно короткий срок службы, невысокую износостойкость и поверхностную твердость.
В последние годы установлено, что одним из возможных способов улучшения свойств порошковых материалов на основе меди является создание композиционных материалов, содержащих углеродные наноструктуры: фуллерены, графены, углеродные нанотрубки (УНТ) или нановолокна (УНВ) [4–6] и др., сочетающих свойства как дисперсно-упрочненных материалов, так и материалов медь–графит. Несмотря на относительную дороговизну углеродных наноструктур и сложность создания однородного распределения наноуглерода в металлической матрице, количество работ, посвященных таким композиционным материалам, в последнее десятилетие экспоненциально растет, т.к. они обладают уникальным комплексом физико-механических свойств.
Однако в настоящее время отсутствуют систематизированные данные и изученные закономерности влияния метода синтеза при введении углеродных наноструктур различного типа на структуру и физико-механические свойства композиционных материалов. Поэтому в настоящей работе рассмотрены особенности наиболее эффективных способов получения материалов Cu–C с целью направленного регулирования их свойств для разных областей применения.
МАТЕРИАЛЫ И МЕТОДИКА ИССЛЕДОВАНИЙ
Исходным материалом для исследований был выбран медный порошок марки ПМС-1 (ГОСТ 4960-2009, Россия). В качестве упрочняющей фазы использовались углеродные наноструктуры: фуллерены (С60), фуллереновая сажа (ФС), восстановленный оксид графена (ВОГ) и углеродные нанотрубки.
Получение композиционного порошкового материала проводили в планетарной мельнице в защитной атмосфере аргона по методике, описанной в [7]. Синтез УНТ и графена на поверхности частиц медного порошка осуществляли методом химического осаждения из газовой фазы (CVD) при атмосферном давлении [8].
Для приготовления композиционных порошков термохимическим методом (TS) использовали нитрат меди Cu(NO3)2 · 3H2O марки “х. ч.”. Процесс приготовления порошка включал следующие стадии: (1) приготовление суспензии углеродных наноструктур в 50%-м водном растворе нитрата меди; (2) распылительная сушка суспензии горячим воздухом; (3) окислительный отжиг с целью разложения нитрата меди и получения оксидного порошка; (4) восстановление оксидного порошка водородом при температуре 400–500°С.
Исследование физико-механических свойств проводилось методами растровой электронной микроскопии, оптической микроскопии, спектроскопии комбинационного рассеяния, рентгеновской фотоэлектронной спектроскопии (РФЭС) и методами рентгеноструктурного анализа. Испытания на твердость проводились по методу Бринелля. Определение электропроводности образцов проводилось четырехконтактным методом. Измерения теплопроводности полученных компактных образцов выполнялись на установке DXF 200 (TA Instruments, США) в режиме лазерной вспышки (погрешность прибора – не более 5%). Использовались образцы прямоугольной формы с размерами 10 × 10 мм и толщиной 3–5 мм. Источником излучения служил импульсный ксеноновый лазер с энергией импульса до 15 Дж и длительностью импульса от 400 до 600 мкс.
РЕЗУЛЬТАТЫ ЭКСПЕРИМЕНТА И ИХ ОБСУЖДЕНИЕ
Фуллерены представляют собой порошок с содержанием C60 99.9%. Частицы порошка представляют собой агломераты неправильной формы, имеющие широкий диапазон распределения по размерам – от 20 до 250 мкм, где сами агломераты состоят из стержней длиной до 5 мкм. Исследование порошка фуллеренов методом рентгенофазового анализа показало, что фуллерены имеют ярко выраженную кристаллическую структуру фуллерита с небольшим количеством аморфного углерода. В фуллеренах С60 углерод находится преимущественно в состоянии sp2-гибридизации, с небольшим количеством функциональных групп –COOH и –CО на поверхности.
Фуллереновая сажа состоит из аморфного углерода с содержанием 10–15% фуллерена C60. Порошок фуллереновой сажи представляет собой углеродные наночастицы сферической формы размером от 20 до 40 нм. В ФС углерод находится как в sp2-, так и в sp3-состояниях примерно в равных количествах. На поверхности ФС также присутствуют функциональные группы –COOH и –CО. Однако фуллереновая сажа содержит бóльшее количество связанного кислорода, чем С60. Это обусловлено аморфной структурой и большим количеством нескомпенсированных связей на поверхности.
Частицы восстановленного оксида графена представляют собой слоистые агломераты размером до 50 мкм, состоящие из углеродных слоев толщиной порядка 10 нм. В порошках ФС и ВОГ присутствует больше кислорода, который находится в поверхностных функциональных группах, чем в УНТ и С60.
Для устранения проблемы агломерации углеродных наноструктур был разработан метод получения композиционных порошковых материалов путем газофазного синтеза углеродных наноструктур непосредственно на поверхности медных микрочастиц [8–10]. В зависимости от экспериментальных параметров были получены материалы медь–УНВ и медь–графен с равномерным распределением углеродных наноструктур по поверхности матричных частиц.
Исследование графеновых слоев и УНВ методом спектроскопии комбинационного рассеяния показывает наличие D-линии, которая соответствует неупорядоченным углеродным структурам и G-линии (тангенциальные колебания). В случае графеновых слоев также присутствует первый его обертон при 2640 см–1 (D'-линия), форма которого соответствует многослойному графену. Результаты РФЭС графеновых слоев показывают наличие достаточно узкого пика при 284.3 эВ, что свидетельствует о преобладании кристаллической sp2-формы углерода, также наблюдаются компоненты спектра, характерные для углерода в карбоксильных группах.
В процессе обработки в планетарной мельнице композиционные порошки с содержанием углерода до 1 мас. % показывают поведение, характерное для пластичного материала: измельчение приводит к сплющиванию частиц, их скатыванию и холодной сварке, в результате образуются слоистые композитные частицы, в которых наночастицы углерода равномерно распределены внутри медной матрицы [7]. Увеличение содержания углерода до 2% и выше приводит к уменьшению размера композитных частиц, т.к. углерод покрывает поверхность Cu, предотвращая сварку. При содержании углерода 5% тенденция к разрушению преобладает над холодной сваркой, дендриты сплющиваются и разрушаются без укрупнения, а углерод остается на поверхности меди.
Анализ методом РФЭС показал, что после размола количество функциональных групп уменьшается во всех образцах. При этом появляется пик, соответствующий кислороду, связанному с металлом, – Cu–O. Интенсивность пика Cu–O пропорциональна общему содержанию кислорода, т.е. пик интенсивней в образцах с сажей и графеном. Поэтому можно предположить, что медь при помоле окисляется частично кислородом функциональных групп, содержащихся в углеродных наноструктурах.
Морфология композиционных порошков, полученных методом термохимического синтеза, подробно рассмотрена в [11]. Частицы порошка после восстановления в атмосфере водорода при температуре 550°С слегка агломерированы, их размер также зависит от концентрации углерода – размер уменьшается при увеличении содержания углерода. При содержании фуллереновой сажи в количестве 5 мас. % частицы сохраняли форму исходных сферических агломератов, внутренний размер композиционных частиц медь–углерод в агломератах составил 0.5–1 мкм. При содержании более 2 мас. % углерод выделяется в виде отдельной фазы на поверхности частиц порошка. Максимальное содержание углерода, равномерно распределенного внутри медной матрицы, в случае использования 0-мерных частиц, составляет 1.5–2 мас. %. Этот метод обеспечивает высокую чистоту матрицы и равномерное распределение упрочняющих частиц.
На рис. 1 представлено сравнение микроструктуры материалов, содержащих 2% углерода после компактирования порошков, полученных различными методами. Компактирование образцов осуществляли методом горячего прессования, относительная плотность всех образцов была не менее 96%. При получении порошков методом механолегирования размер зерна компактных образцов уменьшается с увеличением содержания углерода, в основном совпадая с размером частиц порошка. Особенностью наблюдаемой микроструктуры является “мраморный рисунок”, образованный светлой “сеткой” рекристаллизованной меди, расположенной по границам зерен. При содержании углерода 5% по границам зерен преобладает чистая медь. Использование УНТ или графена приводит к исчезновению светлой сетки по границам исходных зерен.
Рис. 1.
Микроструктуры композиционного материала Сu–2% С. Углерод в виде ФС, материал получен методом термохимического синтеза (а); углерод в виде ФС, материал получен методом механического легирования (б); углерод в виде углеродных нанотрубок, материал получен методом механического легирования (в).
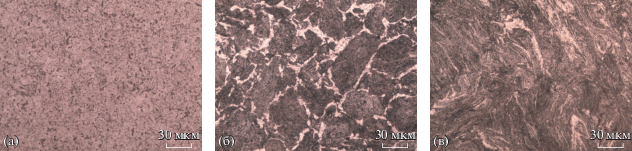
При небольшом (0.5 и 1 мас. %) содержании углерода микроструктура композиционных материалов Cu–С, полученных методом термохимического синтеза, состоит из мелких, рекристаллизованных медных зерен без заметных включений углерода. С увеличением содержания фуллереновой сажи до 2 мас. % микроструктура представляет собой медные зерна, по границам которых равномерно распределены небольшие включения углерода (рис. 1а), а при концентрации 5% ФС происходит их агломерация.
Исследования микроструктуры образцов с УНВ и графитом [8] показали, что в образцах с графитом микроструктура представляет собой зерна меди с грубыми включениями углерода. Замена графита на графен или УНВ, полученных методом CVD, непосредственно на поверхности медного порошка, приводит к образованию более мелкозернистой структуры. При прессовании углеродные наноструктуры заполняют межчастичные поры и располагаются по границам зерен меди, предотвращая их рост при спекании.
Сравнение механических свойств образцов сплавов медь–углеродные наноструктуры представлено на рис. 2а. Как видно из риc. 2а, твердость материалов Сu–С зависит не только от типа и концентрации углеродных наноструктур, но и от метода получения самого композита. Так, наибольшими значениями твердости обладают композиты, полученные методом механического легирования, причем максимум достигается при добавлении углерода в количестве 1–2%. Для этих материалов можно рассмотреть два основных механизма упрочнения: деформационное упрочнение из-за высокой плотности дислокаций, возникающих в процессе синтеза, и упрочнение дисперсными наночастицами углерода, которые являются барьерами для скольжения дислокаций. Последующее снижение твердости связано с увеличением количества обедненных углеродом границ из чистой рекристаллизованной меди и, возможно, с агломерацией углеродных наноструктур.
Рис. 2.
Сравнение твердости (а); тепло- и электропроводности (б) композиционных материалов Cu–С в зависимости от метода получения. MM – материалы, полученные методом механического легирования.
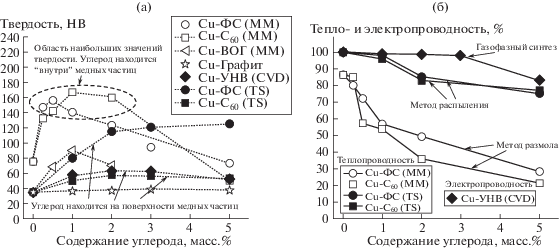
Наименьшее увеличение твердости показывают материалы с распределенными по поверхности медных частиц углеродными наноструктурами. Значения твердости во всех случаях не превышают 63 HB; это ниже значений твердости для чистой меди, полученной из порошков, обработанных в планетарной мельнице. Композиционные образцы медь–УНВ показывают увеличение твердости при содержании 1–3% углеродных наноструктур с последующим снижением до 43 кг/мм2 при увеличении содержания УНВ до 10%. Твердость материалов медь–графит во всем исследованном интервале постоянна в пределах погрешности эксперимента и не превышает 38 кг/мм2 при содержании углерода 5%. При этом относительное удлинение сплавов Cu–УНВ во всех случаях более чем в 2 раза выше, чем для материалов Cu–C, приготовленных по традиционной технологии смешивания.
На рис. 2б показано изменение тепло- и электропроводности композиционных материалов с добавлением углеродных наноструктур в зависимости от метода получения. Электропроводность гибридного материала Cu–УНВ при содержании углерода до 3% меняется незначительно и составляет не менее 98% от электропроводности чистой меди (согласно Международному стандарту по отожженной меди (IACS) ее электропроводность равна 0.01724 мкОм м [12]). При увеличении содержания углерода до 10% электропроводность снижается до 85%, однако этот показатель существенно выше, чем электропроводность материалов медь–графит. Также относительно высокие значения теплопроводности наблюдаются у материалов, полученных методом термохимического синтеза.
ЗАКЛЮЧЕНИЕ
В работе установлена зависимость физико-механических свойств композиционных материалов медь–наноуглерод от метода получения и вида использованных углеродных наноструктур. Показана связь прочностных характеристик с особенностями межфазного взаимодействия в зависимости от метода получения, а также различными механизмами упрочнения, которые реализуются в данных материалах.
При использовании композиционных материалов, полученных механическим легированием, высокая твердость (170 НВ) достигается при содержании углерода 1–2% с последующим снижением при увеличении содержания углерода; размер зерна монотонно уменьшается. При высокой прочности резко снижается пластичность и теплопроводность материала; теплопроводность композитов, полученных размолом, с увеличением содержания углерода снижается до 20% из-за дефектной структуры и большего количества межфазных границ.
В материалах, полученных методом газофазного синтеза, углерод равномерно распределен по поверхности порошка. Упрочнение в этих материалах происходит только за счет уменьшения размеров зерна и хорошо описывается уравнением Холла–Петча.
Твердость материалов, полученных методом термохимического синтеза, монотонно увеличивается при увеличении содержания углерода до 5%; а композиционный материал Cu–5% ФС обладает большей твердостью по сравнению с композитами той же концентрации, полученными другими методами. В этом случае упрочнение происходит как за счет дисперсных частиц, равномерно распределенных в медной матрице, так и за счет уменьшения размера зерна; при применении 1- и 2-мерных углеродных наноструктур твердость композита существенно снижается.
Таким образом, выбор и функционализация углеродных наноструктур, применяемых для создания композиционных материалов, использование современных технологий синтеза, а также методов компактирования позволяет в широком диапазоне регулировать физико-механические свойства композиционных материалов и выбирать метод синтеза для конкретных применений. В настоящее время ведутся работы по использованию различных методов синтеза для получения композиционных материалов с заданными физико-механическими свойствами для авиационно-космической отрасли и специализированных материалов для аддитивных технологий.
Список литературы
Groza J.R., Gibeling J.C. Principles of particle selection for dispersion strengthened copper // Mater. Sci. Eng., A. 1993. V. 171. P. 115–125.
Tian B., Liu P., Song K., Li Y., Liu Y., Ren F., Su J. Microstructure and properties at elevated temperature of a nano-Al2O3 particles dispersion-strengthened copper base composite // Mater. Sci. Eng., A. 2006. V. 435–436. P. 705–710
Groza J. Heat-resistant dispersion-strengthened copper alloys // J. Mater. Eng. Perform. 1992. V. 1. № 1. P. 113–121.
Bor A., Ichinkhorloo B., Uyanga B, Lee J, Choi H. Cu/CNT nanocomposite fabrication with different raw material properties using a planetary ball milling process // Powder Technol. 2018. V. 323. P. 563–573.
Larionova N.S., Nikonova R.M., Ladyanov V.I. Mechanosynthesis of nanostructured composites copper-fullerite, copper-graphite // Adv. Powder Technol. 2018. V. 29. P. 399–406.
Duan B., Zhou Y., Wang D., Zhao Y. Effect of CNTs content on the microstructures and properties of CNTs/Cu composite by microwave sintering // J. Alloys Compd. 2019. V. 771. P. 498–504.
Бобрынина Е.В., Ларионова Т.В., Кольцова Т.С., Чжанг Ю., Лиянг X., Толочко О.В. Получение, структура и свойства композитов на основе меди с добавками фуллеренов и фуллереновой сажи // МиТОМ. 2020. Т. 775. № 1. С. 70–75.
Nasibulina L.I., Koltsova T.S., Joentakanen T., Nasibulin A.G., Tolochko O.V., Malm J.E.M., Karppinen M.J., Kauppinen, E.I. Direct synthesis of carbon nanofibers on the surface of copper powder // Carbon. 2010. V. 48. № 15. P. 4559–4562.
Rudskoy A.I., Nasibulin A.G., Koltsova T.S., Tolochko O.V. Novel metal matrix/carbon composites for airspace applications // 29th Congress of the International Council of the Aeronautical Sciences. ICAS 2014. 7–12 September 2014. St. Petersburg, Russian Federation. 2014. 108502.
Rudskoy A.I., Kol’Tsova T.S., Larionova T.V., Smir-nov A.N., Vasil’eva E.S., Nasibulin A.G. Gas-phase synthesis and control of structure and thickness of graphene layers on copper substrates // Met. Sci. Heat Treat. 2016. V. 58. № 1. P. 40–45.
Ji P., Qi D., Yin F., Wang G., Bobrynina E., Tolochko O. Effect of nanocarbons additions on the microstructures and properties of copper matrix composite by spray drying process // Key Eng. Mater. 2019. V. 822. P. 202–207.
The International Annealed Copper Standard. Дocтyпнo пo: http://www.ndt-ed.org/GeneralResources/IACS/IACS.htm.
Дополнительные материалы отсутствуют.
Инструменты
Доклады Российской академии наук. Химия, науки о материалах