Доклады Российской академии наук. Химия, науки о материалах , 2020, T. 494, № 1, стр. 37-41
Низкотемпературное жидкофазное спекание диоксида циркония: исследование фазового состава и микроструктуры
В. В. Смирнов 1, С. В. Смирнов 1, Т. О. Оболкина 1, О. С. Антонова 1, М. А. Гольдберг 1, *, член-корреспондент РАН С. М. Баринов 1
1 Институт металлургии и материаловедения
им. А.А. Байкова Российской академии наук
Москва, Россия
* E-mail: mgoldberg@imet.ac.ru
Поступила в редакцию 24.12.2019
После доработки 21.08.2020
Принята к публикации 03.09.2020
Аннотация
Проведено исследование спекания, микроструктуры и фазового состава керамики на основе диоксида циркония, содержащей добавку 0.2 мас. % оксида алюминия. Впервые показано, что введение дисиликата натрия в качестве легкоплавкой добавки способствует снижению температуры спекания диоксидциркониевой керамики до 1080‒1180°С. Полученные материалы характеризовались высоким содержанием тетрагональной фазы, мелкокристаллической структурой с размером зерен от 40‒50 до 80‒100 нм. Показано, что использование добавок на основе дисиликата натрия способствует жидкофазному спеканию и формированию плотной структуры при 1080°С.
Тетрагональный диоксид циркония, который получают в виде твердого раствора, содержащего 3 мол. % Y2O3, характеризуется наиболее высокими механическими свойствами, по сравнению с другими материалами на основе ZrO2 [1]. Благодаря высокой прочности, трещиностойкости и износостойкости, а также химической инертности и отсутствию токсических реакций, такая керамика нашла применение в качестве материала для изготовления тазобедренных и дентальных имплантатов [2, 3]. В то же время, высокая себестоимость производства ZrO2 материалов лимитирует их широкое распространение в биомедицине, машиностроении и других областях применения. Одним из путей снижения себестоимости производства является переход от дорогостоящего высокотемпературного спекания и горячего прессования к получению спеченной керамики при пониженной температуре, а также технологиям аддитивного производства, обеспечивающим сокращение технологического цикла и объемов отходов при производстве. Введение добавок на основе Al2O3 способно понизить температуру спекания, в том числе для изделий, получаемых методами аддитивного производства – цифровой обработки светом [4].
В работе [5] были получены материалы, содержащие от 1 до 16 мас. % Al2O3. Было выявлено, что спеченные материалы возможно получить при невысоком содержании Al2O3 (до 5 мас. %) при 1500‒1550°С. Интенсифицировать процесс спекания также возможно дополнительным введением добавок, образующих расплав и вызывающих жидкофазное спекание. В качестве добавки использовали силикат натрия Na2SiO3 с температурой плавления около 1072°С в количестве 5 мас. % [6]. В результате при 1250–1330°С были получены плотные материалы (открытая пористость меньше 1%). При этом отмечалось, что наименьшую пористость и наиболее высокую плотность имели материалы, содержавшие 1 мас. % Al2O3, увеличение содержания оксида алюминия до 5 мас. % приводило к увеличению открытой пористости до 8‒10% для материалов, спеченных при 1250°С.
В то же время дальнейшее снижение температуры спекания будет обеспечивать возможность реализации такого метода аддитивного производства, как селективное лазерное спекание, требующего формирования контактов непосредственно в зоне воздействия лазерного луча [7]. В работе [8] было выявлено, что при использовании добавки дисиликата натрия Na2Si2O5 с меньшей температурой плавления 863°С [6] материал на основе ZrO2 имел мелкокристаллическую структуру и характеризовался размером кристаллов 50–400 нм.
В данной работе приведены результаты исследования процесса низкотемпературного жидкофазного спекания, а также формирования фазового состава и микроструктуры диоксидциркониевой керамики, получаемой из нанодисперсного порошка, содержащего добавку оксида алюминия в количестве 0.2 мас. % и легкоплавкую добавку Na2Si2O5 в количестве 5 мас. %. На данный момент сведений о жидкофазном спекании диоксидциркониевой керамики с температурой ниже 1150°С не найдено.
ЭКСПЕРИМЕНТАЛЬНАЯ ЧАСТЬ
Для получения низкотемпературных керамических материалов на основе ZrO2 использовали смесь порошков: 99.8 мас. % оксикарбоната циркония, полученного из растворов оксихлорида циркония путем осаждения в раствор карбоната аммония, содержащего, в пересчете на оксиды, 3 мол. % оксида иттрия по отношению к диоксиду циркония, и 0.2 мас. % Al2O3. В результате прокаливания при 650‒700°С получали порошок диоксида циркония, содержащего Y2O3 и Al2O3, с высокой удельной поверхностью 30‒32 м2/г.
В качестве добавки, образующей расплав, использовали дисиликат натрия в количестве 5 мас. %. Добавку вводили в порошок ZrO2 в планетарной мельнице при интенсивном перемешивании помольными телами из диоксида циркония.
Порошковые материалы на основе ZrO2 (как содержащие дисиликат натрия (СК-13), так и не содержащие (СК-1)) формовали в виде параллелепипедов размером 40 × 4 × 4 мм методом одноосного прессования в стальных пресс-формах при давлении 100 МПа. Спекание проводили в диапазоне температур от 1000 до 1400°С. Порошки исследовали методом просвечивающей электронной микроскопии (ПЭМ) на микроскопе TITAN 80‑300 (США). Фазовый состав порошковых и керамических материалов исследовали методом рентгенофазового анализа (РФА), который проводили на дифрактометре Shumadzu 6000 (Япония) с использованием CuKα излучения. Удельную поверхность измеряли методом БЭТ, (Tristar micromeritics, США). Измерение прочности при изгибе проводили с использованием разрывной машины Instron 3382 (США). Пористость исследовали методом гидростатического взвешивания в соответствии с ГОСТ 2409-2014. Микроструктуру спеченных образцов изучали методом растровой электронной микроскопии (РЭМ, Tescan Vega II, Чехия).
Составы и температуры спекания приведены в табл. 1.
РЕЗУЛЬТАТЫ И ИХ ОБСУЖДЕНИЕ
Согласно результатам ПЭМ, после проведения синтеза порошок состоял из частиц оксикарбоната циркония размером до 80 нм (рис. 1а) преимущественно округлой формы без выраженной огранки.
РФА показал рентгеноаморфное состояние материала, что согласовывалось с исследованиями, проведенными в работах [9, 10]. Дальнейшее прокаливание смеси порошков при 650°С привело к разложению оксикарбоната циркония по реакции (1) и формированию диоксида циркония (рис. 2).
(1)
${\text{ZrOC}}{{{\text{O}}}_{3}} \to {\text{Zr}}{{{\text{O}}}_{2}} + {\text{C}}{{{\text{O}}}_{2}}{\kern 1pt} \uparrow $Рис. 2.
Дифрактограммы порошков после прокаливания при 650°С (а) и после спекания керамических образцов СК-1 (б), СК-13 (в), где t – t-ZrO2, m – m-ZrO2.
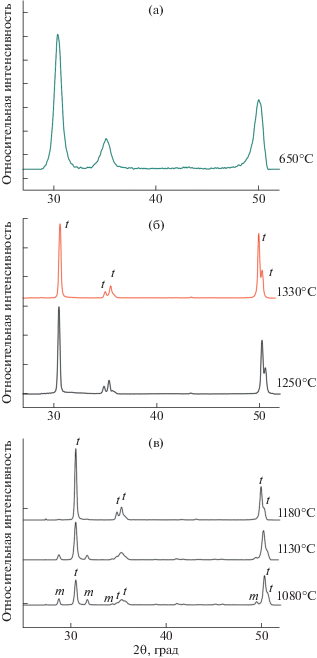
Основные рефлексы на дифрактограмме уширены, имеют низкую интенсивность, проявляются в области формирования кубической и тетрагональной фазы (рис. 2а). Согласно данным ПЭМ, сформированные после термической обработки частицы диоксида циркония имеют округлую морфологию с выраженными гранями, размер частиц около 20 нм. При этом порошок агрегирован, размер агрегатов от 50 до 300 нм (рис. 1б).
Спекание материала состава СК-1 при 1250°С за счет использования высокоактивного к спеканию порошка (табл. 1) позволило получить керамику с открытой пористостью до 2.7%, согласно результатам гидростатического взвешивания.
По данным РЭМ средний размер кристаллов составлял около 80‒100 нм, морфология зерен была без выраженной огранки неправильной или округлой формы (рис. 3). Можно отметить однородность микроструктуры, отсутствие крупных кристаллов и видимой пористости. По фазовому составу материал соответствовал 100%-ной тетрагональной фазе (рис. 2б) диоксида циркония (t-ZrO2). Увеличение температуры до 1330°С позволило снизить открытую пористость до 0.16%, при этом размер кристаллов практически не изменился.
Рис. 3.
Микроструктура керамического материала СК-1, спеченного при 1250°С (а) и материала СК-13, спеченного при 1180°С (б) и 1080°С (в).
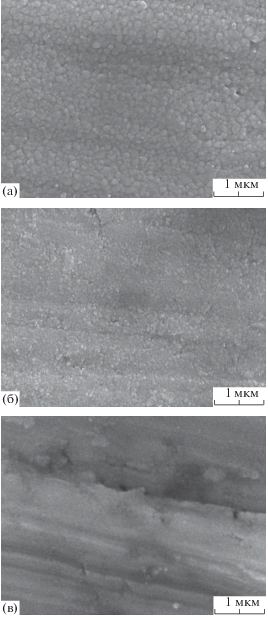
Одной из причин улучшения спекания является увеличение растворимости оксида алюминия (до ∼3%) в диоксиде циркония с ростом температуры до 1330°С [11]. Это приводит к образованию замещения четырехвалентных ионов циркония на трехвалентные ионы алюминия с формированием вакансий по кислороду в кристаллической решетке (реакция 2), что способствует интенсификации процесса диффузии (массопереносу) и, как следствие, спеканию материала [12].
(2)
${\text{А}}{{{\text{l}}}_{{\text{2}}}}{{{\text{O}}}_{3}}\;\xrightarrow{{{\text{Zr}}{{{\text{O}}}_{2}}}}\;2{\text{Al}}_{{{\text{Zr}}}}^{'} + {\text{V}}_{{\text{o}}}^{{\centerdot \centerdot }} + 3{\text{O}}_{{\text{o}}}^{{\text{x}}}\,.$Более плотные образцы при низких температурах спекания были получены на основе материалов состава СК-13, то есть содержащих образующую расплав добавку дисиликата натрия, приводящую к жидкофазному спеканию. Были получены образцы с открытой пористостью ниже 1%: 0.9% при 1080°С, 0.3% при 1130°С и 0% при 1180°С.
Фазовый состав керамики СК-13 изменялся в зависимости от температуры спекания. При наиболее высокой температуре спекания ‒ 1180°C ‒ материал был однофазным – 100% t-ZrO2 (рис. 2в). При более низких температурах спекания наблюдался рост количества моноклинной фазы (m-ZrO2): при 1130°С – 20‒25 мас. %, при 1080°С – 30‒ 40 мас. %. При этом, согласно данным РЭМ, средний размер частиц снижался с 80‒100 нм для 1180°С до 40–50 нм для 1080°С (рис. 3б, 3в). Известно, что для частиц диоксида циркония характерно снижение количества моноклинной фазы по мере уменьшения размера кристаллов, более того, существует критический размер, при котором образование m-ZrO2 невозможно и образуется только t-ZrO2 даже без введения стабилизирующей добавки. В работе [13] было показано, что для порошков этот размер несколько меньше, например, при содержании 1.5 мол. % Y2O3 – около 100 нм, а для керамики несколько больше – около 150 нм (при комнатной температуре). Поэтому можно предположить, что образование m-ZrO2 в материале СК-13, где размер кристаллов меньше критического, вызвано присутствием добавки дисиликата натрия, способствующей дестабилизации t-ZrO2 при низкой температуре спекания. С увеличением температуры m-ZrO2 полностью трансформируется в t-ZrO2, что вызвано достижением температуры фазового перехода для диоксида циркония m → t при 1000‒1200°С [13]. После спекания при охлаждении керамики обратного перехода t → m не происходит.
ЗАКЛЮЧЕНИЕ
Таким образом, разработаны составы и впервые получены наноструктурированные керамические материалы на основе диоксида циркония, полученного из оксикарбоната циркония, при температуре спекания 1250°С. Показано, что использование дисиликата натрия в качестве спекающей добавки способствует жидкофазному низкотемпературному спеканию и формированию плотной структуры с пористостью ниже 1% при 1080°С. Разработанные материалы могут найти применение в реконструктивно-пластической хирургии.
Список литературы
Жигачев А.О., Головин Ю.И., Умрихин, А.В., Коренков В.В., Тюрин А.И., Родаев В.В., Дьячек Т.А. Керамические материалы на основе диоксида циркония. М.: ТЕХНОСФЕРА, 2018. 358 с.
Manicone P.F., Iommetti P.R., Raffaelli L. An overview of zirconia ceramics: Basic properties and clinical applications // Journal of Dentistry. 2007. V. 35. P. 819‒826. https://doi.org/10.1016/j.jdent.2007.07.008
Chevalier J. What future for zirconia as a biomaterial? // Biomaterials. 2006. V. 27. P. 535‒543. https://doi.org/10.1016/j.biomaterials.2005.07.034
Li Y., Wang M., Wu H., He F., Chen Y., Wu S. Cure behavior of colorful ZrO2 suspensions during Digital light processing (DLP) based stereolithography process // J. Eur. Ceram. Soc. 2019. V. 39. № 15. P. 4921–4927. https://doi.org/10.1016/j.jeurceramsoc.2019.07.035
Smirnov V.V., Krylov A.I., Smirnov S.V., Goldberg M.A., Antonova O.S., Shvorneva L.I., Barinov S.M. Study of liquid-phase sintering of materials based on zirconium dioxide containing alumina // Inorg. Mater. Appl. Res. 2017. V. 8. № 1. P. 81‒83. https://doi.org/10.1134/S2075113317010373
Торопов Н.А., Барзаковский В.П., Лапин В.В., Курце-ва Н.Н., Бойкова А.И. Диаграммы состояния силикатных систем. Справочник. Выпуск третий. Тройные силикатные системы. Л.: Наука, 1986. 448 с.
Sing S.L., Yeong W.Y., Wiria F.E., Tay B.Y., Zhao Z., Zhao L., Tian Z., Yang S. Direct selective laser sintering and melting of ceramics: a review // Rapid Prototyping Journal. 2017. V. 23. № 3. P. 611–623. https://doi.org/10.1108/RPJ-11-2015-0178
Смирнов В.В., Смирнов С.В., Оболкина Т.О., Антонова О.С., Гольдберг М.А., Хайрутдинова Д.Р., Баринов С.М. Спекание и свойства композиционных ZrO2‒Al2O3-материалов с добавками, образующими расплавы на основе силиката натрия // Материаловедение. 2019. № 6. С. 32‒36. https://doi.org/10.31044/1684-579X-2019-0-6-32-36
Ismail H.M. Characterization of the decomposition products of zirconium acetylacetonate: nitrogen adsorption and spectrothermal investigation // Powder Technol. 1995. V. 85. № 3. P. 253‒259. https://doi.org/10.1016/0032-5910(95)03025-7
Wu W., Cai J., Wu X., Li Y., Liao S. Nanocrystalline ZrO2 preparation and kinetics research of phase transition // Rare Metals. 2012. V. 31. № 1. P. 51‒57. https://doi.org/10.1007/s12598-012-0462-2
Lakiza S.M., Lopato L.M. Stable and metastable phase-relations in the system alumina-zirconia-yttria // J. Am. Ceram. Soc. 1997. V. 80. № 4. P. 893‒902. https://doi.org/10.1111/j.1151-2916.1997.tb02919.x
Андрианов Н.Т., Балкевич В.Л., Беляков А.В., Власов А.С., Гузман И.Я., Лукин Е.С., Мосин Ю.М., Скидан Б.С. Химическая технология керамики: Учеб. пособие для вузов. М.: ООО РИФ “Стройматериалы”, 2011. 496 с.
Mayo M.J., Suresh A., Porter W.D. Thermodynamics for nanosystems: Grain and particle-size dependent phase diagrams // Rev. Adv. Mater. Sci. 2003. V. 5. № 2. P. 100‒109.
Дополнительные материалы отсутствуют.
Инструменты
Доклады Российской академии наук. Химия, науки о материалах