Доклады Российской академии наук. Химия, науки о материалах , 2023, T. 508, № 1, стр. 70-78
Комплексный подход к утилизации хлорорганических соединений на примере отходов производства винилхлорида
И. В. Мишаков 1, *, Ю. И. Бауман 1, С. Г. Дьячкова 2, А. Р. Потылицына 1, А. А. Ведягин 1
1 Институт катализа им. Г.К. Борескова
Сибирского отделения Российской академии наук
630090 Новосибирск, Россия
2 Иркутский национальный исследовательский технический университет
664074 Иркутск, Россия
* E-mail: mishakov@catalysis.ru
Поступила в редакцию 24.06.2022
После доработки 12.08.2022
Принята к публикации 19.08.2022
- EDN: EVVMLK
- DOI: 10.31857/S2686953522600349
Аннотация
Предложена концепция комплексной каталитической переработки отходов хлорорганических производств с использованием самоорганизующихся катализаторов на основе никеля. На примере 1,2-дихлорэтана изучен процесс углеродной эрозии массивного Ni–Cr-сплава с образованием дисперсных частиц, катализирующих рост углеродных нановолокон. Установлено, что данный подход носит универсальный характер и может быть применим для переработки многокомпонентных смесей хлорорганических соединений, в том числе отходов производства поливинилхлорида. Обсуждены перспективы использования углеродного наноматериала, получаемого в результате переработки отходов, для производства полимерных композитов.
ВВЕДЕНИЕ
Бурное развитие “зеленой химии” и перевод промышленных химических процессов на каталитические “рельсы” позволяют заметно снизить нагрузку на экологию планеты. Использование каталитических методов в энергетике, синтезе материалов, переработке нефтегазового сырья и биомассы способствует резкому снижению удельного количества отходов и побочных продуктов [1]. С другой стороны, катализ можно с успехом применять не только для утилизации различного рода отходов, накопленных за долгие годы работы предприятий химической промышленности, но и для их переработки в ценные продукты [2, 3]. В качестве примера можно привести хлорорганические отходы (ХОО), образующиеся в результате крупнотоннажного промышленного синтеза алифатических хлорзамещенных углеводородов. На стадии пиролиза 1,2-дихлорэтана (1,2-ДХЭ), которая применяется для получения мономера винилхлорида, на 1 т продукта образуется более 30 кг отходов, представляющих собой трудно утилизируемую многокомпонентную смесь полихлорированных углеводородов [4]. Такие методы утилизации, как сжигание и захоронение, влекут за собой вторичное загрязнение объектов окружающей среды, увеличение углеродного следа промышленной зоны. Вместе с тем ХОО являются ценным сырьем для получения углеродных материалов нового поколения. Каталитическая переработка ХОО с получением углеродных наноструктурированных материалов (УНМ) может стать решением данной проблемы.
Идея переработки хлорзамещенных углеводородов в УНМ основана на хорошо известном процессе – каталитическом осаждении углерода из газовой фазы (Catalytic Chemical Vapor Deposition, CCVD) [5, 6]. В качестве катализаторов процесса CCVD часто используют дисперсные металлические системы на основе Ni, Co, Fe. Для разложения хлоруглеводородов лучше всего подходят сплавы никеля как наиболее устойчивые по отношению к дезактивирующему воздействию хлора [7–12]. Никельсодержащие катализаторы испытаны в разложении таких хлорзамещенных углеводородов, как 1,2‑дихлорэтан [8], хлорбензол [10], дихлорметан [13], трихлорэтилен [14], а также в смеси с другими субстратами, например, этанолом и хлороформом [15]. В результате каталитической переработки хлорзамещенных углеводородов образуются углеродные наноструктуры, имеющие в основном нитевидный характер [9, 14, 16]. В частности, в работе [12] описано получение углеродных нанотрубок путем разложения полихлорированных бензолов. В то же время следует отметить, что производительность нанесенных никелевых катализаторов редко достигает уровня в 10 г/г(кат.) вследствие высокой склонности высокодисперсных активных частиц к дезактивации.
Ранее был предложен новый подход, позволяющий значительно увеличить производительность катализаторов, используемых для пиролиза хлоруглеводородов с получением УНМ. В основе подхода лежит явление углеродной эрозии массивных сплавов Ni–M (где М – второй металл), выступающих в роли предшественников активного катализатора [17]. Ранее, на примере разложения 1,2-ДХЭ в присутствии водорода, продемонстрировано, что в результате быстрой углеродной эрозии массивных сплавов Ni–M происходило спонтанное формирование активных частиц, катализирующих дальнейший рост углеродных наноструктур [18]. Изучение модифицирующего воздействия второго элемента М показало, что добавка незначительного количества (~5%) таких металлов, как W, Mo, Cr, способствовала значительному увеличению активности никеля и практически сводила к нулю вероятность спонтанной дезактивации [19]. Наибольший интерес с точки зрения практической реализации вызывают сплавы никеля и хрома (Ni–Cr), производимые в промышленных масштабах. В качестве такого сплава в настоящей работе использовали нихром марки Н80Х20.
Важно отметить, что продуктом каталитической переработки хлорзамещенных углеводородов на катализаторах Ni–M выступает углеродный наноструктурированный материал, имеющий уникальную вторичную структуру (сегментированные углеродные нановолокна, УНВ) и высокую удельную поверхность (до 400 м2 г–1) [20].
При создании полимерных композитов на основе УНВ важным преимуществом являются равномерное распределение и высокая адгезия между волокнами и полимерной матрицей [21]. Такие модифицированные материалы имеют ряд улучшенных механических характеристик (предел прочности при растяжении, модуль упругости при растяжении, прочность на разрыв, усталостные характеристики и т.д.) [22]. Помимо этого, даже малое количество УНВ в составе полимеров может способствовать повышению их электро- и теплопроводности [23].
В настоящей работе предложена концепция комплексной каталитической переработки отходов производства винилхлорида, в основе которой лежит использование самоорганизующихся катализаторов пиролиза хлорзамещенных углеводородов. На примере 1,2-ДХЭ изучен процесс углеродной эрозии массивного Ni–Cr-сплава с формированием дисперсных активных частиц, катализирующих рост УНВ. Новизна исследования заключается в том, что разработанный метод впервые применен для переработки реальных хлорорганических отходов различного состава. Охарактеризованы морфология и структура полученного углеродного наноматериала методами растровой и просвечивающей электронной микроскопии.
ЭКСПЕРИМЕНТАЛЬНАЯ ЧАСТЬ
В роли предшественника катализатора в работе использовали проволоку нихрома (d = 0.01 мм) марки Н80Х20 (ЗАО “Союзнихром”). Фазовый состав массивного сплава представлен однофазным твердым раствором Ni–Cr, с небольшой примесью железа (до 1.7%).
В качестве модельного хлорзамещенного углеводорода применяли 1,2‑дихлорэтан (1,2-ДХЭ, х. ч., ТУ 6-09-06-695-75) – один из многотоннажных хлорорганических продуктов, присутствующий в отходах практически всех производств с участием галогензамещенных углеводородов. Также в работе были испытаны образцы реальных отходов производства винилхлорида в г. Саянске, представляющие собой кубовый остаток ректификации процесса прямого высокотемпературного хлорирования этилена (образец № 1) и ловушечный продукт, объединяющий высококипящие отходы со всех потоков производства винилхлорида (образец № 2). Качественный и количественный состав образцов № 1 и № 2 (табл. 1) был определен с помощью методов газо-жидкостной хроматографии (ГЖХ) и хромато-масс- спектрометрии (ХМС).
Таблица 1.
Состав смесей хлорзамещенных углеводородов, использованных в работе в качестве субстратов
№ п/п | Наименование субстрата | Компоненты | Концентрация, мас. % |
---|---|---|---|
1 | 1,2-ДХЭ | 1,2-Дихлорэтан (х. ч.) модельный субстрат | 99.5 |
2 | Образец № 1 | 1,2-Дихлорэтан | 93.0 |
Смесь полихлорированных алифатических и ароматических углеводородова | 7.0 | ||
3 | Образец № 2 | Алифатические углеводороды | |
1,1,2-Трихлорэтан | 25.6 | ||
1,2-Дихлорэтан | 22.7 | ||
1,3-Дихлорбутен-3 | 13.0 | ||
1-Хлор-2-бромэтан | 6.7 | ||
Трихлорбутан | 3.6 | ||
Трихлоргексан | 1.9 | ||
Ароматические углеводороды | |||
Хлорбензол | 4.6 | ||
1,3-Дихлорхлорметилбензол | 1.6 | ||
1,3,5-Трихлор-2-метилбензол | 1.3 | ||
Смесь полихлорированных алифатических и ароматических углеводородова | 8.8 | ||
Смесь неидентифицированных галогензамещенных углеводородов | 10.2 |
Изучение углеродной эрозии нихрома при разложении 1,2-ДХЭ. Исследование процесса углеродной эрозии массивного сплава Ni–Cr осуществляли в проточной установке, оснащенной весами Мак-Бейна. Навеску сплава (кусочек проволоки массой 5 мг) подвергали контакту с реакционной смесью 1,2‑ДХЭ/Н2/Ar = 7/35/58 об. %, получаемой в результате пропускания потока аргона через сатуратор с жидким 1,2-ДХЭ при 23°С. Температура в реакторе составляла 600°С. Время обработки сплава Ni–Cr реакционной смесью варьировали в диапазоне 1–20 мин.
Полученные образцы обработанной проволоки изучали методом просвечивающей электронной микроскопии (ПЭМ). Для этого образец проволоки фиксировали в стандартном держателе, предназначенном для медных сеток, и помещали в камеру микроскопа JEM 1400 (Jeol, Япония). Исследования проводили при ускоряющем напряжении 80 кВ.
Каталитическое разложение хлорорганических отходов. Разложение сложных смесей хлоруглеводородов осуществляли в укрупненном проточном кварцевом реакторе, оснащенном испарителем и системой подачи жидкого субстрата. В качестве модельного субстрата выбран 1,2-ДХЭ. Подробное описание реактора представлено в работе [24]. При помощи инфузионного насоса жидкие хлорорганические отходы подавались в испаритель и далее в газообразном состоянии поступали в реактор, где смешивались с потоками H2 (6 л ч–1) и Ar (9 л ч–1). Общая скорость газового потока составила 15 л ч–1. Скорость подачи жидкого субстрата составляла 2.5 мл ч–1. Данный вариант подачи позволяет исключить изменение состава субстрата в ходе эксперимента, возникающее вследствие неравномерного испарения компонентов смеси. Масса предшественника катализатора (проволока нихрома), загружаемого в реактор, составляла 50 ± 3 мг. Навеску проволоки помещали на кварцевую пластину, расположенную под испарителем. Температура в реакторе составляла 550 и 600°C, время реакции – 4 ч. По окончании процесса реактор охлаждали в потоке аргона до комнатной температуры, выгружали углеродный продукт, взвешивали и рассчитывали выход УНВ.
Исследование морфологии, структуры и текстуры углеродного продукта. Морфологию и вторичную структуру углеродного продукта изучали методом растровой электронной микроскопии (РЭМ) на приборе JSM-6460 (Япония) при увеличении от 1.000 до 100.000 крат. Первичную структуру углеродных нитей и морфологию каталитических частиц исследовали методом ПЭМ на приборе JEM‑2010CX (ускоряющее напряжение 100 кВ, разрешение – до 0.14 нм). Текстурные характеристики (удельная площадь поверхности и объем пор) углеродного продукта изучены методом низкотемпературной адсорбции азота на приборе ASAP-2400 (США).
ОБСУЖДЕНИЕ РЕЗУЛЬТАТОВ
Процесс каталитического пиролиза смеси хлорзамещенных углеводородов может быть схематически представлен в следующем виде:
* – самоорганизующийся катализатор (СОК) ** – углеродный наноматериалПолучаемый углеродный продукт представляет собой графитоподобные углеродные нановолокна, содержащие в своей структуре частицы катализатора [18]. Остаточное содержание катализатора в составе УНМ определяется выходом углеродного продукта, который может достигать сотен граммов на 1 г катализатора [25]. Отметим, что образующийся углеродный продукт нетоксичен, не горюч и может храниться неограниченное время, не представляя угрозу человеку и окружающей среде [26].
В то же время утилизация большого объема отходов неминуемо приводит к образованию соответствующего количества УНМ, что ставит вопрос о практическом использовании углеродного продукта. Как отмечалось выше, углеродные нановолокна можно успешно применять для модифицирования различных полимерных материалов и придания им особых свойств (высокая прочность, износостойкость, электро- и теплопроводность) [21–23]. В данном случае представляется целесообразным использование УНМ непосредственно на месте производства поливинилхлорида (ПВХ) для создания композитов УНМ/ПВХ, востребованных в индустрии изоляционных материалов [27]. Разработка способа создания подобных полимерных композитов с регулируемыми свойствами представляет собой отдельную научную задачу, решение которой позволит реализовать предложенную концепцию комплексной переработки ХОО.
Далее рассмотрим, в чем заключается принцип работы так называемых самоорганизующихся катализаторов (СОК), используемых на стадии пиролиза ХОО.
Дизайн катализатора для пиролиза ХОО. Ключевой инструмент дизайна катализаторов для пиролиза ХОО заключается в использовании явления ускоренной углеродной эрозии массивных сплавов на основе никеля. Проволока нихрома играет роль исходного сплава, фактически представляющего собой предшественник катализатора. В качестве модельного хлорзамещенного субстрата для изучения углеродной эрозии использовали 1,2‑ДХЭ, составляющий основу промышленных отходов, образующихся на стадии получения винилхлорида (табл. 1).
На рис. 1 представлена эволюция изменений, происходящих на поверхности проволоки нихрома в ходе контакта с агрессивной реакционной средой C2H4Cl2/H2/Ar. Избыток Н2 в реакционной смеси требуется для быстрого формирования СОК и способствует стабильной работе образующегося катализатора с максимальной производительностью.
Рис. 1.
Зарождение активных частиц роста углеродных нановолокон на поверхности проволоки нихрома (а) в результате контакта с реакционной средой C2H4Cl2/H2/Ar, 600°C в течение: 1 мин (б); 2 мин (в); 10 мин (г); 20 мин (д). Данные ПЭМ.
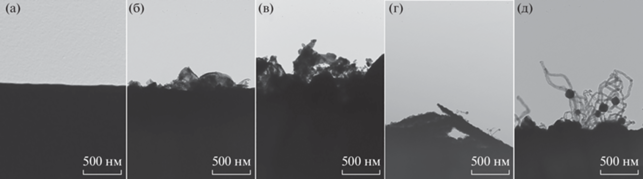
Исходная поверхность массивного сплава, представленная на рис. 1а, является условно гладкой и ровной. Однако уже на раннем этапе взаимодействия с реакционной атмосферой (рис. 1б, в) рельеф поверхности проволоки претерпевает кардинальные изменения. Видно, что приповерхностный металлический слой взламывается, становится рыхлым, что связано с разрушающим воздействием графитоподобного углерода. В результате разложения молекул C2H4Cl2 углерод проникает в объем сплава, где далее диффундирует к межблочным границам, на которых формируется фаза графита [18]. Уже через 1–2 мин контакта на поверхности отчетливо видны следы образовавшейся углеродной фазы (рис. 1б,в). Ее зарождение и последующий рост в зоне межзеренных границ приводят к быстрому разрушению поликристаллической структуры массивного сплава и способствуют быстрому продвижению углеродной эрозии вглубь. Спустя 10–20 мин с момента начала реакции на рыхлой поверхности проволоки формируются металлические частицы субмикронного размера (рис. 1г,д). Отрываясь от поверхности сплава, частицы покидают ее, увлекаемые растущими углеродными нитями (рис. 1д). В данной фазе процесса активные частицы “работают” независимо друг от друга, совмещая функции каталитического разложения 1,2-ДХЭ и роста углеродных нановолокон. Совокупность образовавшихся активных частиц, функционирующих в соответствии с механизмом карбидного цикла [28], представляет собой самоорганизующуюся каталитическую систему [20].
Процесс углеродной эрозии продолжается вплоть до полной дезинтеграции массивного сплава, и в случае проволоки нихрома диаметром 0.1 мм занимает порядка 3 ч. Оценки показывают, что в результате фрагментации 1 г нихрома в среднем в системе появляется ~1 × 1014 дисперсных активных частиц (для удобства расчетов считалось, что образуются одинаковые кубические частицы размером 250 нм). Каждая такая частица вносит свой вклад в переработку 1,2‑ДХЭ с одновременным образованием двух и более углеродных нитей. Количество накопленного углерода может в сотни раз превышать исходную массу катализатора [25], что делает данный подход весьма перспективным для практической реализации.
Таким образом, разрушительный процесс углеродной эрозии, стремительно протекающий в случае контакта сплавов никеля с парами хлорзамещенных углеводородов, может служить эффективным инструментом приготовления катализаторов непосредственно в реакторе. Предшественниками катализаторов могут быть любые сплавы на основе никеля, который отличается наибольшей устойчивостью к хлорированию среди металлов триады железа [7].
Апробация метода для разложения реальных ХОО. Дальнейшая разработка предложенного способа предполагала проведение экспериментов по разложению многокомпонентных смесей хлорзамещенных углеводородов для подтверждения концепта. Напомним, что метод верифицировали на примере двух образцов реальных отходов, различающихся в первую очередь содержанием 1,2‑ДХЭ (табл. 1). В состав смесей входит широкий набор полихлорированных алифатических углеводородов, а также хлорзамещенные углеводороды ароматического ряда. Результаты проведенных экспериментов представлены в табл. 2 и на рис. 2 и 3.
Таблица 2.
Показатели процесса каталитического разложения 1,2-ДХЭ и образцов ХОО № 1 и № 2 в проточном реакторе. Нихром Н80Х20 (проволока, d = 0.1 мм), 600°С, 4 ч
№ п/п | Субстрат | Масса навески предшественника, г | Масса продукта, г | Выход УНВ, г/г(кат.) | Селективность по углероду, % |
---|---|---|---|---|---|
1 | 1,2-ДХЭ | 0.051 | 2.40 | 47 | 67 |
2 | Образец № 1 | 0.051 | 1.54 | 30 | 60 |
3 | Образец № 2 | 0.053 | 1.20 | 23 | 65 |
Рис. 2.
Микрофотографии РЭМ углеродного продукта, полученного каталитическим пиролизом отходов производства винилхлорида. Образец № 1: 550°C, 4 ч (а, б); образец № 1: 600°C, 4 ч (в, г); образец № 2, 600°C, 4 ч (д, е).
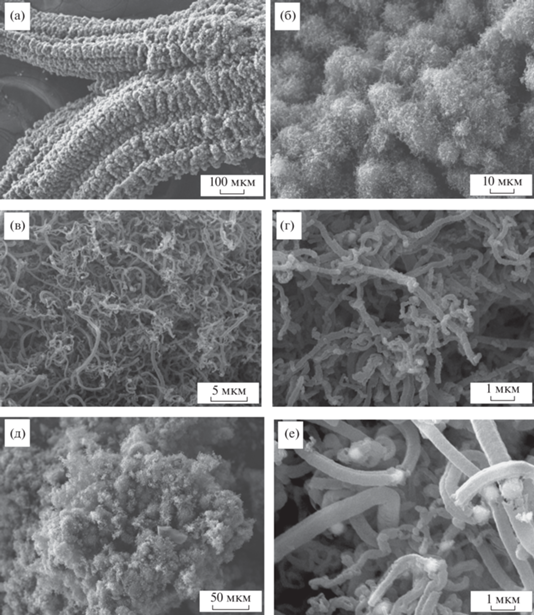
Рис. 3.
Микрофотографии ПЭМ углеродного продукта, полученного каталитическим пиролизом образца № 1: 600°C, 4 ч.
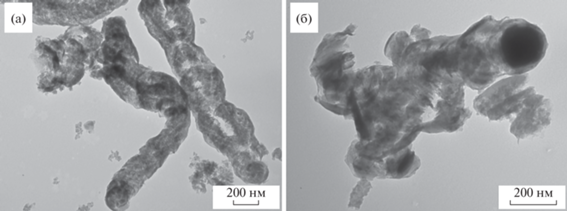
На основании данных, представленных в табл. 2, за 4 ч реакции с модельным субстратом (1,2-ДХЭ) выход углеродного продукта составил 47 г/г(кат.). За это время проволока нихрома, использованная в качестве предшественника катализатора, подверглась 100%-й дезинтеграции. В то же время, в случае использования образцов № 1 и № 2, за указанное время полная дезинтеграция массивного сплава не достигается. Этот факт проиллюстрирован на снимке РЭМ (рис. 2а), где внешний вид углеродного продукта повторяет форму исходной проволоки нихрома, на которой он образовался. Снижение выхода УНВ до 23–30 г/г(кат) в случае многокомпонентных смесей можно объяснить присутствием в их составе хлорароматических соединений (в образце № 2 оно максимально), в присутствии которых скорость дезинтеграции массивных сплавов заметно замедляется [6]. Оценка селективности процесса по углероду показывает сходные значения для всех экспериментов на уровне 60–70%. Полученные значения можно объяснить протеканием параллельной реакции газификации углерода в избытке водорода, в результате которой образуется метан [29]. Образование метана является неизбежным по причине использования избытка водорода в смеси. Количество CH4 может быть снижено за счет уменьшения доли Н2 или использования водородсодержащего газа вместо чистого водорода. С другой стороны, образующийся метан также может быть подвержен каталитическому пиролизу, что позволит извлечь водород и направить его на основную стадию.
Углеродный продукт, образовавшийся в реакторе в результате 4-часового взаимодействия нихрома со смесью хлорзамещенных углеводородов, исследовали методами электронной микроскопии (РЭМ, ПЭМ). На снимках РЭМ, представленных на рис. 2, можно видеть морфологию и вторичную структуру УНМ при различных степенях увеличения. Видно, что полученный материал преимущественно представлен совокупностью тонких углеродных нитей (рис. 2в, г), формирующих вторичные агломераты (“клубки”) размером порядка 10–30 мкм (рис. 2б, д). При этом отмечается отсутствие принципиальных отличий в морфологии углеродного продукта для случаев разложения образца № 1 и образца № 2. Это подтверждает применимость подхода для утилизации многокомпонентных смесей, содержащих хлорзамещенные углеводороды различного класса.
При максимальном увеличении (рис. 2г,е) на снимке РЭМ можно наблюдать отдельные углеродные нити, диаметр которых не превышает 1 мкм. Видно, что в структуре нитей содержатся округлые металлические частицы, проявляющиеся в виде характерных светлых пятен на снимке (рис. 2е). Данные кристаллы, сформировавшиеся в результате дезинтеграции массивного нихрома, выполняют функцию активных частиц, на которых и осуществляется переработка хлорзамещенных углеводородов в углеродный наноматериал.
Более тонкая структура полученных углеродных нитей представлена на рис. 3. На рис. 3б хорошо видна металлическая частица в виде темного контрастного пятна. Размер этих частиц составляет порядка 200 нм. Отметим, что на представленных снимках ПЭМ можно наблюдать лишь фрагменты длинных нановолокон, которые подверглись частичному разрушению в результате подготовки образца перед исследованием на микроскопе (ультразвуковое диспергирование в спирте).
Характер упаковки графеновых слоев в структуре таких нитей является дефектным, с множеством пропусков и пустот, что и делает эти структуры довольно хрупкими. Как было показано в работе [20], формирование подобной дискретной структуры УНВ объясняется наличием хлора в реакционной системе, который периодически блокирует активную поверхность никеля, внося пертурбации в диффузионный поток атомов углерода к месту роста нитей. В то же время низкая степень упорядоченности в структуре таких нитей обусловливает высокие текстурные показатели данного углеродного материала: удельная поверхность достигает 400 м2 г–1, а объем пор – 0.8 см3 г–1.
На основании полученных экспериментальных данных нами разработана принципиальная технологическая схема каталитической трансформации многокомпонентных хлорорганических смесей, которая имеет общий, концептуальный характер и может быть применима для всех видов хлорорганических отходов и побочных продуктов на любом предприятии органического синтеза (рис. 4). В основе метода переработки лежит процесс каталитического пиролиза хлорзамещенных углеводородов CnHmClk с применением самоорганизующихся катализаторов на основе никеля.
Хлорорганические отходы со всех потоков производства объединяются в сборнике. Сформированная таким образом многокомпонентная смесь насосом по трубопроводу направляется в испаритель. В качестве испарителя, в зависимости от фракционного состава и температурных характеристик смеси, может быть использовано стандартное оборудование: ребойлер, ребойлер с вставным огневым нагревателем, кожухотрубчатый теплообменник с плавающей головкой, трубчатая печь. После выхода из испарителя реакционный газ смешивается с водородом и направляется в адиабатический реактор периодического действия, снабженный сменной решеткой из каталитического сплава. Для снижения затрат вместо водорода может быть использован более дешевый водородсодержащий газ. По завершении процесса реактор дросселируется, побочный продукт – газообразный хлороводород – может быть направлен на стадию оксихлорирования этилена, разнообразные процессы гидрохлорирования, либо для получения абгазной соляной кислоты. Целевой продукт – углеродный наноструктурированный материал в виде порошка выгружается снизу реактора и по транспортеру направляется в цех компаундирования с ПВХ либо отгружается на склад. Введение углеродного продукта в ПВХ предполагается делать методом перегрануляции на стадии экструзии.
ЗАКЛЮЧЕНИЕ
В настоящей работе представлено описание научных основ технологии каталитического пиролиза промышленных отходов, образующихся при производстве винилхлорида. В основу подхода заложено явление самодиспергации массивного сплава на основе никеля под воздействием углеродной эрозии, в результате которой быстро формируются активные частицы – центры роста УНВ. Образующаяся таким образом каталитическая система подтвердила свою работоспособность и устойчивость в разложении многокомпонентных смесей полихлорированных углеводородов. В результате переработки отходов на катализаторе происходит рост углеродных нановолокон с дефектной упаковкой, что определяет высокие текстурные показатели получаемого углеродного продукта. Предложенная схема утилизации отходов предполагает использование полученного углеродного наноматериала в качестве модифицирующей добавки в полимерные композиты на основе поливинилхлорида.
БЛАГОДАРНОСТИ
Работа выполнена при финансовой поддержке Министерства науки и высшего образования Российской Федерации в рамках государственного задания Института катализа СО РАН (проект № АААА-А21-121011390054-1).
Список литературы
Rogers L., Jensen K.F. // Green chem. 2019. V. 21. № 13. P. 3481–3498. https://doi.org/10.1039/C9GC00773C
Pan D., Su F., Liu H., Liu C., Umar A., Castañeda L., Algadi H., Wang C., Guo Z. // ES Mater. Manuf. 2021. V. 11. № 6. P. 3–15. https://doi.org/10.30919/esmm5f415
Kosloski-Oh S.C., Wood Z.A., Manjarrez Y., de Los Rios J.P., Fieser M.E. // Mater. Horizons. 2021. V. 8. № 4. P. 1084–1129. https://doi.org/10.1039/D0MH01286F
Демина Т.Я., Шаяхметова Л.Р. // Вестник ОГУ. 2005. № 10–2. С. 10–13.
Hiraoka T., Kawakubo T., Kimura J., Taniguchi R., Okamoto A., Okazaki T., Sugai T., Ozeki Y., Yoshikawac M., Shinohara H. // Chem. Phys. Lett. 2003. V. 382. № 5–6. P. 679–685. https://doi.org/10.1016/j.cplett.2003.10.123
Kenzhin R.M., Bauman Y.I., Volodin A.M., Mishakov I.V., Vedyagin A.A. // Appl. Surf. Sci. 2018. V. 427. P. 505–510. https://doi.org/10.1016/j.apsusc.2017.08.227
Мишаков И.В., Чесноков В.В., Буянов Р.А., Пахо-мов Н.А. // Кинетика и катализ. 2001. Т. 42. № 4. С. 598–603.
Nieto-Márquez A., Valverde J.L., Keane M.A. // Appl. Catal. A Gen. 2007. V. 332. № 2. P. 237–246. https://doi.org/10.1016/j.apcata.2007.08.028
Cherukuri L.D., Yuan G., Keane M.A. // Top. Catal. 2004. V. 29. № 3. P. 119–128. https://doi.org/10.1023/B:TOCA.0000029794.03727.ef
Keane M.A., Jacobs G., Patterson P.M. // J. Colloid. Interface Sci. 2006. V. 302. № 2. P. 576–588. https://doi.org/10.1016/j.jcis.2006.06.057
Shaikjee A., Coville N.J. // Carbon. 2012. V. 50. P. 1099–1108. https://doi.org/10.1016/j.carbon.2011.10.020
Maboya W.K., Coville N.J., Mhlanga S.D. // S. Afr. J. Chem. 2016. V. 69. P. 15–26. https://doi.org/10.17159/0379-4350/2016/v69a3
Brichka S.Ya., Prikhod’ko G.P., Sementsov Yu.I., Brichka A.V., Dovbeshko G.I., Paschuk O.P. // Carbon. 2004. V. 42. P. 2581–2587. https://doi.org/10.1016/j.carbon.2004.05.040
Shaikjee A., Coville N.J. // Mater. Lett. 2012. V. 68. P. 273–276. https://doi.org/10.1016/j.matlet.2011.10.083
Lin W.-H., Li Y.-Y. // Mater. Chem. Phys. 2015. V. 163. P. 123–129. https://doi.org/10.1016/j.matchemphys.2015.07.022
Lv R., Kang F., Wang W., Wei J., Gu J., Wang K., Wu D. // Carbon. 2007. V. 45. P. 1433–1438. https://doi.org/10.1016/j.carbon.2007.03.032
Mishakov I.V., Bauman Y.I., Korneev D.V., Vedyagin A.A. // Top. Catal. 2013. V. 56. № 11. P. 1026–1032. https://doi.org/10.1007/s11244-013-0066-6
Mishakov I.V., Korneev D.V., Bauman Y.I., Vedyagin AA., Nalivaiko A.Y., Shubin Yu.V., Gromov A.A. // Surf. Interfaces. 2022. V. 30. P. 101914. https://doi.org/10.1016/j.surfin.2022.101914
Мишаков И.В., Бауман Ю.И., Потылицына А.Р., Шубин Ю.В., Плюснин П.Е., Стояновский В.О., Ведягин А.А. // Кинетика и катализ. 2022. Т. 63. № 1. С. 86–98.
Bauman Y.I., Mishakov I.V., Rudneva Y.V., Plyusnin P.E., Shubin Yu.V., Korneev D.V., Vedyagin A.A. // Ind. Eng. Chem. Res. 2018. V. 58. № 2. P. 685–694. https://doi.org/10.1021/acs.iecr.8b02186
Al-Saleh M.H., Sundararaj U. // Compos. Part A Appl. Sci Manuf. 2011. V. 42. № 12. P. 2126–2142. https://doi.org/10.1016/j.compositesa.2011.08.005
Rana S., Alagirusamy R., Joshi M. // Compos. Part A. 2011. V. 42. № 5. P. 439–445. https://doi.org/10.1016/j.compositesa.2010.12.018
Poveda R.L., Gupta N. // Mater. Des. 2014. V. 56. P. 416–422. https://doi.org/10.1016/j.matdes.2013.11.074
Wang C., Bauman Y.I., Mishakov I.V., Stoyanovskii V.O., Shelepova E.V., Vedyagin A.A. // Processes. 2022. V. 10. № 3. P. 506. https://doi.org/10.3390/pr10030506
Бауман Ю.И., Мишаков И.В., Ведягин А.А., Дмитриев С.В., Мельгунов М.С., Буянов Р.А. // Катализ в промышленности. 2012. № 2. С. 18–24.
Yokoyama A., Sato Y., Nodasaka Y., Yamamoto S., Kawasaki T., Shindoh M., Kohgo T., Akasaka T., Uo M., Watari F., Tohji K. //Nano Lett. 2005. V. 5. № 1. P. 157–161. https://doi.org/10.1021/nl0484752
Ahmad N., Kausar A., Muhammad B. // Polym. Plast. Technol. Eng. 2016. V. 55. № 10. P. 1076–1098. https://doi.org/10.1080/03602559.2016.1163587
Буянов Р.А., Чесноков В.В. // Химия в интересах устойчивого развития. 2005. Т. 13. № 1. С. 37–40.
Mishakov I.V., Bauman Yu.I., Streltsov I.A., Korneev D.V., Vinokurova O.B., Vedyagin A.A. // Resour. Effic. Technol. 2016. V. 2. № 2. P. 61–67. https://doi.org/10.1016/j.reffit.2016.06.004
Дополнительные материалы отсутствуют.
Инструменты
Доклады Российской академии наук. Химия, науки о материалах