Доклады Российской академии наук. Науки о Земле, 2021, T. 496, № 2, стр. 215-220
Модель выщелачивания “состаренных” натрий-алюмофосфатных стекломатриц радионуклидов
В. И. Мальковский 1, *, член-корреспондент РАН С. В. Юдинцев 1
1 Институт геологии рудных месторождений, петрографии, минералогии и геохимии Российской академии наук
Москва, Россия
* E-mail: malkovsky@inbox.ru
Поступила в редакцию 12.10.2020
После доработки 11.11.2020
Принята к публикации 11.11.2020
Аннотация
Высокорадиоактивные отходы ядерной энергетики включают в стеклообразные матрицы для удаления в глубокие подземные хранилища. Распад радионуклидов вызывает разогрев и кристаллизацию остеклованных отходов с ухудшением способности удерживать опасные компоненты. С учетом экспериментальных данных предложена модель растворения в воде закристаллизованного Na–Al–P-стекла для прогноза поведения такой матрицы в хранилище.
Изоляция высокоактивных отходов (ВАО) от переработки отработанного топлива (ОЯТ) является необходимым условием ресурсосберегающего и экологически безопасного топливного цикла ядерной энергетики. ВАО представляют собой азотнокислые растворы с высокими концентрациями радионуклидов [1]. Основным способом обращения с ними признана стратегия отверждения жидких ВАО и подземного захоронения [2–4]. Перевод жидких ВАО в твердое состояние осуществляется включением растворенных компонентов в матрицу-консервант. В нашей стране для этого используется натрий-алюмофосфатное стекло, в остальных странах – боросиликатное [3–6].
Одним из главных требований к матрицам ВАО является долговременная устойчивость в подземных водах после размещения в хранилище [6, 7]. Имеется большое количество данных по интенсивности растворения стеклообразных матриц отходов в нагретых водных растворах в различных условиях [4–7]. Остеклованные ВАО выделяют тепло за счет радиоактивного распада, из-за чего их температура существенно повышается. Разогрев стекла приводит к изменению его строения (кристаллизации), этот процесс интенсивно протекает в интервале температуры 450–550°С для алюмофосфатных стекол и 600–700°С для боросиликатных матриц [4, 5]. В таких условиях полная или частичная девитрификация стекломатриц происходит за время от нескольких часов до первых суток. В среде паров воды с влажностью около 70% температура кристаллизации Na–Al–P-стекла опускается до 250–300°С [8], а сам процесс занимает не более суток (рис. 1). Изменение остеклованных ВАО в горячем влажном воздухе получило название “паровая гидратация”, а сами измененные матрицы называют состаренными (или aged в англоязычной литературе) [9]. При контакте таких ускоренно-состаренных матриц с водой содержание в ней плутония, нептуния, урана и имитаторов продуктов деления (Cs) возрастает в десятки и даже тысячи раз по сравнению с растворами, полученными в опытах с неизмененным стеклом [9, 10]. Вода в небольшом количестве попадает в контейнер с остеклованными ВАО до его герметизации на радиохимическом заводе. Контакт паров воды с матрицей может также произойти при разрушении контейнера уже на начальной “сухой” стадии эволюции подземного хранилища, которая может длиться до ста лет после его закрытия и характеризуется температурой от 100 до 140°С [11].
Рис. 1.
СЭМ-изображение Na–Al–P-стекла с имитаторами отходов: исходное (а) и после девитрификации в среде пара (б). Цифрами обозначены номера фаз (1–4). Составы фаз 1–4 приведены в табл. 2.
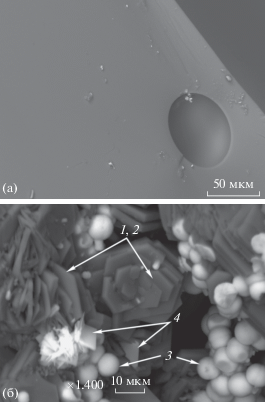
Для прогноза поведения матриц отходов в хранилище необходимо проанализировать их устойчивость в течение всего времени, пока долгоживущие радионуклиды актинидов и продуктов деления представляют экологическую угрозу для биосферы (до десятков тысяч лет и более). С этой целью на основе полученных ранее данных [10] разработана модель временнóй зависимости растворения в воде девитрифицированных Na–Al–P-стекол. Исходное стекло имеет однородное строение (рис. 1а), если не считать газовые поры, и состав. После суточной обработки паром воды при 300 С происходит его раскристаллизация (рис. 1б; табл. 1). Определение интенсивности растворения закристаллизованного Na–Al–P-стекол в воде осуществлялось следующим образом. Монолитные образцы (состава, в мас. %: 17.3 Na2O; 14.0 Al2O3; 51.1 P2O5; 5.5 Fe2O3; 1.1 NiO; 2.1 SrO; 2.5 Cs2O; 2.1 Ce2O3; 2.0 Nd2O3; 2.3 UO3; Σ = 100%) помещались в титановый автоклав с фторопластовым вкладышем. Автоклав заполнялся дистиллированной водой, герметично закрывался и помещался в термостат при температуре 90°С. Через определенное время (1, 3, 10 и 30 сут) автоклав извлекался из термостата и охлаждался проточной водой. Раствор из автоклава сливался, и в нем измерялись концентрации продуктов растворения стекла. Затем автоклав с тем же образцом заполнялся дистиллированной водой, герметизировался и помещался в термостат. Концентрации элементов в растворах измерялись методом ICP–MS в ИГЕМ РАН.
Обозначим $\Delta {{t}_{i}}$ интервал времени между ($i - 1$)-й и $i$-й заменой раствора. Среднюю скорость растворения стекла, нормализованную по элементу $E$, в интервале времени $\Delta {{t}_{i}}$ можно оценить по формуле ${{R}_{{i,E}}}$ = $m{{C}_{{i,E}}}{\text{/}}({{F}_{E}}S\Delta {{t}_{i}})$, где $m$ – масса раствора в автоклаве, ${{C}_{{i,E}}}$ – массовая концентрация элемента $E$ в растворе, $S$ – площадь поверхности образца, ${{F}_{E}}$ – массовая доля элемента $E$ в стекле.
Если растворение образца осуществляется конгруэнтно, т.е. поверхность его контакта с раствором перемещается параллельно самой себе, то ${{R}_{{i,E}}}$ должны быть одинаковыми для всех $E$. Однако в большинстве случаев это не так [10, 12], часть этих элементов относительно легко переходит в раствор, а менее растворимые элементы оседают в поверхностном слое матрицы, уменьшая площадь ее контакта с раствором. Для сравнения скорости поступления в раствор элементов $E$ и $F$, образующих каркас матрицы, удобно использовать количественную характеристику ${{\gamma }_{{E/F}}}({{t}_{n}})$ = ${{R}_{{n,E}}}{\text{/}}{{R}_{{n,F}}}$, где ${{t}_{n}}$ = $\sum\nolimits_{i = 1}^n {\Delta {{t}_{i}}} $. Если ${{\gamma }_{{E/F}}} \ll 1$, то при растворении матрицы элемент $F$ преимущественно поступает в раствор, а элемент $E$ в большей степени оседает в поверхностном слое образца, что замедляет его растворение. Зависимости характеристик ${{\gamma }_{{E/F}}}$ от времени для элементов каркаса стекла (Na, Al и P) после гидратации в паре приведены на рис. 2. Отметим, что Al поступает в раствор гораздо слабее, чем P и Na. За исключением короткого начального интервала времени величины ${{\gamma }_{{{\text{Al/P}}}}}$ и ${{\gamma }_{{{\text{Al/Na}}}}}$ в течение эксперимента меняются незначительно.
Для анализа влияния осаждения продуктов выщелачивания Na–Al–P-стекла на изменение поверхности выщелачивания предложена следующая модель. Обозначим $z$ глубину продвижения фронта растворения, а $S$ – текущее значение поверхности фронта растворения. При продвижении фронта растворения на $\Delta z$ произойдет выщелачивание массы образца ${{\rho }_{m}}S(z)\Delta z$, ${{\rho }_{m}}$ – плотность стекла. Из этой массы часть перейдет в раствор, а часть продуктов выщелачивания массой ${{\delta }_{m}}$ осядет на поверхности образца. Изменение $S$ за счет осаждения этих слаборастворимых продуктов выщелачивания удовлетворяет уравнению
где $A$ – некоторый постоянный коэффициент.Поскольку в течение всего описанного эксперимента по выщелачиванию, за исключением краткого начального периода, величины ${{\gamma }_{{{\text{Al/Na}}}}}$ и ${{\gamma }_{{{\text{Al/P}}}}}$ изменялись незначительно (рис. 2), в линейном приближении можно записать ${{\delta }_{m}}$ = $\theta {{\rho }_{m}}S(z)\Delta z$, где $0 < \theta < 1$. Следовательно,
где ${{S}_{0}}$ – поверхность образца. Отсюда где $B = A\theta {{\rho }_{m}}$.Во всех экспериментах концентрации продуктов выщелачивания матрицы в растворе малы. Это позволяет предположить, что выщелачивание всех кристаллических фаз протекает независимо. Миграция продуктов растворения $i$-й фазы к исходной поверхности образца осуществляется за счет диффузии через канал с переменным сечением ${{s}_{i}}(z)$ и удовлетворяет уравнению:
(2)
$\frac{{\partial {{С}^{{(i)}}}}}{{\partial t}} = \frac{1}{{{{s}_{i}}(z)}}\frac{\partial }{{\partial z}}\left( {{{D}_{i}}{{s}_{i}}(z)\frac{{\partial {{C}^{{(i)}}}}}{{\partial z}}} \right),$Таблица 1.
Состав стекла и фаз после его девитрификации при обработке паром
Элемент | Атомные количества элементов в расчете на 10 катионов | ||||
---|---|---|---|---|---|
№ 1 Na–Al-фосфат-1 | № 2 Na–Al-фосфат-2 | № 3 Sr–Ln–U-фосфат | № 4 Cs–U-фосфат | Исходное стекло | |
Na | 3.84 | 2.69 | – | 1.00 | 3.27 |
Al | 1.96 | 1.66 | 0.44 | 0.50 | 1.61 |
P | 3.89 | 4.15 | 5.06 | 3.73 | 4.22 |
Fe | 0.31 | 0.74 | – | 0.23 | 0.40 |
Ni | – | 0.55 | – | – | 0.09 |
Sr | – | 0.16 | 1.24 | – | 0.12 |
Cs | – | 0.05 | – | 1.57 | 0.10 |
Ce | – | – | 1.41 | – | 0.07 |
Nd | – | – | 1.19 | – | 0.07 |
U | – | – | 0.66 | 2.97 | 0.05 |
О | 15.05 | 16.08 | 19.77 | 20.62 | 15.76 |
Граничные условия для уравнения (2) запишутся в виде
(4)
$z = 0,\quad {{C}^{{(i)}}} = C_{{v}}^{{(i)}};\quad z = {{Z}_{i}}(t),\quad {{C}^{{(i)}}} = C_{{{\text{sat}}}}^{{(i)}},$(5)
$\begin{gathered} \frac{{\partial С_{{v}}^{{(i)}}}}{{\partial t}} = \frac{{{{\rho }_{i}}s\left[ {{{Z}_{i}}(t)} \right]}}{m}\frac{{d{{Z}_{i}}}}{{dt}}, \\ \rho {{D}_{i}}\frac{{\partial {{C}^{{(i)}}}}}{{\partial z}}\left[ {t,{{Z}_{i}}(t)} \right] = {{\rho }_{i}}\frac{{d{{Z}_{i}}}}{{dt}}, \\ \end{gathered} $Уравнение (2) с начальными и граничными условиями (3), (4) и дополнительными соотношениями (5) полностью определяют задачу Стефана, если заданы параметры $\{ C_{{{\text{sat}}}}^{{(i)}}$, ${{D}_{i}}$, ${{\sigma }_{i}}$, ${{b}_{i}}$, i = 1, …, 4}. Их значения получены из условия:
(6)
$\Phi = \sum\limits_{n = 1}^4 {{{{\left[ {\frac{1}{{{{C}_{{n,E}}}}}\sum\limits_{i = 1}^4 {\left( {1 - {{\delta }_{{i,3}}}} \right)C_{{v}}^{{(i)}}({{t}_{n}}){{F}_{{i,E}}}} - 1} \right]}}^{2}}} \to \min ,$(7)
$\begin{gathered} {{Z}_{1}} = 8.09 \times {{10}^{{ - 4}}}{{t}^{{0.38}}},\quad {{Z}_{2}} = 3.36 \times {{10}^{{ - 5}}}{{t}^{{0.58}}}, \\ {{Z}_{4}} = 3.36 \times {{10}^{{ - 5}}}{{t}^{{0.7}}}, \\ \end{gathered} $Таблица 2.
Параметры модели из данных эксперимента по выщелачиванию
Номер фазы | ${{D}_{i}}$, м2/с | $C_{{{\text{sat}}}}^{{(i)}}$, безразм. | ${{\sigma }_{i}}$, безразм. | ${{b}_{i}}$, 1/м |
---|---|---|---|---|
1 | 3.3 × 10–11 | 0.014 | 0.65 | 1.3 × 104 |
2 | 4.9 × 10–13 | 0.011 | 0.17 | 0.73 × 104 |
4 | 6.1 × 10–13 | 0.017 | 0.20 | 2.6 × 104 |
Рис. 3.
Сравнение расчетных (линия) и измеренных (точки) концентраций Na в воде в опытах по растворению закристаллизованного Na‒Al‒P-стекла. Ступенчатое снижение концентрации до нуля соответствует замене раствора в автоклаве через интервалы времени 1, 3, 10 и 30 сут.
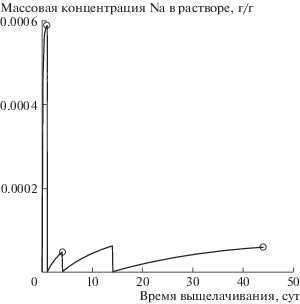
Общая масса $i$-й фазы, выщелачиваемая c единичной поверхности образца, определяется выражением
Тогда масса $i$-й фазы, выщелачиваемая в единицу времени c единичной поверхности раскристаллизованного Na–Al–P-стекла, вычисляется по формуле:
Отсюда масса натрия, переходящая в раствор с единичной поверхности образца в единицу времени, вычисляется по формуле
(8)
$\begin{gathered} \frac{{d{{m}_{{{\text{Na}}}}}}}{{dt}} = \sum\limits_{i = 1}^4 {{{F}_{{i,{\text{Na}}}}}\frac{{d{{m}_{i}}}}{{dt}}} \left( {1 - {{\delta }_{{i,3}}}} \right) = \\ = \sum\limits_{i = 1}^4 {\left( {1 - {{\delta }_{{i,3}}}} \right){{F}_{{i,{\text{Na}}}}}{{\rho }_{i}}{{\sigma }_{i}}\exp ( - {{b}_{i}}Z_{i}^{0}{{t}^{{{{P}_{i}}}}})} \frac{{{{P}_{i}}Z_{i}^{0}}}{{{{t}^{{1 - {{P}_{i}}}}}}}. \\ \end{gathered} $Однако с точки зрения оценки защитных свойств матрицы большее значение имеет определение массы актинидов, поступающей в раствор в единицу времени с единичной поверхности образца. В качестве их имитаторов в образец вводились радиоизотоп 238U и геохимические аналоги актинидов: Ce и Nd. Интенсивность выщелачивания U, Ce и Nd по отношению к интенсивности выщелачивания Na характеризуется параметрами ${{\gamma }_{{{\text{U/Na}}}}}$, ${{\gamma }_{{{\text{Ce/Na}}}}}$, ${{\gamma }_{{{\text{Nd/Na}}}}}$, зависящими от времени (рис. 4). Можно отметить, что за исключением сравнительно короткого начального периода графики всех трех зависимостей практически совпадают. Из табл. 1 следует, что U входит в состав третьей и четвертой фазы, а Ce и Nd – только в состав слаборастворимой третьей фазы. По-видимому, отклонение кривой ${{\gamma }_{{{\text{U/Na}}}}}(t)$ в начальный период времени обусловлено наличием в приповерхностном слое образца более растворимой четвертой фазы (пластинчатые кристаллы на рис. 1б). В дальнейшем переход U, Ce и Nd в раствор осуществляется только за счет частиц третьей фазы, о чем убедительно свидетельствует совпадение всех трех кривых на рис. 4. Для всех трех имитаторов актинидов зависимости ${{\gamma }_{{{\text{Act/Na}}}}}(t)$ (где Act = U, Ce, Nd) вне начального интервала времени с хорошей точностью аппроксимируются функцией
где [t] = сут.Таким образом, массу актинида Act, переходящую в раствор с единичной поверхности в единицу времени, можно оценить по определению ${{\gamma }_{{{\text{Act/Na}}}}}$ как
Данная модель может быть использована для анализа долговременной устойчивости раскристаллизованных алюмофосфатных матриц в отношении основных элементов каркаса стекла (Na, Al, P), а также для оценки интенсивности выноса из нее элементов отходов, в том числе радионуклидов.
Список литературы
Копырин А.А., Карелин А.И., Карелин В.А. Технология производства и радиохимической переработки ядерного топлива: М.: Атомэнергоиздат, 2006. 576 с.
End Points for Spent Nuclear Fuel and High-level Radioactive Waste in Russia and the United States / Committee on End Points for Spent Nuclear Fuel and High-Level Radioactive Waste in Russia and the United States. Washington: National Academies Press. 2003. 137 p.
Laverov N., Yudintsev S., Kochkin B., Malkovsky V. // Elements. 2016. V. 12. P. 253–256.
Вашман А.А., Демин А.В., Крылова Н.В., Кушников В.В., Матюнин Ю.И., Полуэктов П.П., Поляков А.С., Тетерин Э.Г. Фосфатные стекла с радиоактивными отходами / Под ред. А.А. Вашмана, А.С. Полякова. М.: ЦНИИатоминформ, 1997. 172 с.
Donald I.W., Metcalfe B.L., Taylor R.N.J. // Journ. of materials science. 1997. V. 32. P. 5851–5887.
Nuclear Waste Conditioning. A Nuclear Energy Division Monograph. Ed. by Jean-François Parisot. Gif-sur-Yvette: Commissariat à l’énergie atomique, 2009. 151 p.
Abdelouas A., Neeway J., Grambow B. // In: Springer Handbook of Glass. Musgraves J.D., Hu J., and Calvez L. (Eds.). Switzerland AG: Springer Nature. 2019. Chapter 12.
Александрова Е.В., Мальковский В.И., Юдинцев С.В. // ДАН. 2018. Т. 482. № 6. С. 693–696.
Bates J.K., Seitz M.G., Steindler M.J. // Nucl. and Chem. Waste Managem. 1984. V. 5. P. 63–73.
Malkovsky V.I., Yudintsev S.V., Aleksandrova E.V. // Journ. of Nuclear Materials. 2018. V. 508. P. 212–218.
Diomidis N., Johnson L.H. // JOM. 2014. V. 66. Iss. 3. P. 461–470.
Rebiscoul D., Frugier P., Gin S., Ayral A. // Journ. of Nuclear Materials. 2005. V. 342. P. 26–34.
Carslaw H.S., Jaeger J.C. Conduction of Heat in Solids, 2d ed. Oxford: Clarendon Press, 1959. 510 p.
Roache P.J. Computational Fluid Dynamics. Albuquerque: Hermosa Publishers, 1976. 446 p.
Gill P.E., Murray W., Wright M.H. Practical optimization. London: Academic Press: 1981. 401 p.
Дополнительные материалы отсутствуют.
Инструменты
Доклады Российской академии наук. Науки о Земле