Электрохимия, 2019, T. 55, № 1, стр. 78-84
Прогнозирование микрораспределения скорости электроосаждения металла из электролитов с положительной и отрицательной выравнивающей способностьюС. С. Кругликов, Н. В. Титова, Н. Е. Некрасова, Е. С. Кругликова, А. В. Тележкина, В. А. Бродский, В. А. Колесников, А. Ф. Губин
С. С. Кругликов a, *, Н. В. Титова b, Н. Е. Некрасова a, Е. С. Кругликова c, А. В. Тележкина a, В. А. Бродский a, В. А. Колесников a, А. Ф. Губин a
a Российский химико-технологический университет им. Д.И. Менделеева
125047 Москва, Миусская пл., 9, Россия
b Первый Московский государственный медицинский университет им. И.М. Сеченова
Министерства здравоохранения Российской Федерации (Сеченовский университет)
119991 Москва, ул. Трубецкая, 8, стр. 2, Россия
c Московский политехнический университет
107023 Москва, ул. Большая Семёновская, 38, корп. А, Россия
* E-mail: skruglikov@mail.ru
Поступила в редакцию 15.12.2017
После доработки 20.02.2018
Принята к публикации 08.05.2018
Аннотация
Рассмотрена взаимосвязь между выравнивающей способностью электролитов, первичным распределением тока и микрораспределением скорости осаждения металла. На примерах электролитов с положительной, нулевой и отрицательной выравнивающей способностью выполнены расчеты микрораспределения скорости осаждения металла с использованием данных о первичном распределении тока, полученных экспериментально на макромодели исследуемого микропрофиля. Показано хорошее согласие между микрораспределением, рассчитанным с помощью описанного метода, и результатами прямых измерений распределения металла на поверхности с регулярным двухмерным микропрофилем.
ВВЕДЕНИЕ
По мере миниатюризации электронных и других аналогичных устройств, в производстве которых используются процессы электроосаждения металлов и сплавов [1–11], возрастает роль факторов микрораспределения осаждаемого металла [12–26], а для электроосаждения сплавов при этом возрастает роль факторов микрораспределения сплава в целом и микрораспределения его компонентов. В то же время, в соответствии с ростом числа Вагнера, уменьшается вклад факторов макрораспределения в процесс формирования электроосажденных слоев (при рассмотрении макрораспределения тока в пределах произвольно выбранного участка катодной поверхности, например, глухого цилиндрического отверстия, число Вагнера будет увеличиваться пропорционально отношению диаметра и квадрата глубины отверстия; т.е. обратно пропорционально величине масштабного фактора [8]; поэтому для неровностей поверхности размером менее 100 мкм число Вагнера всегда будет много больше единицы, что означает равномерное вторичное макрораспределение тока).
При анализе микрораспределения скорости осаждения металла или сплава целесообразно в качестве объекта выбрать поверхность с развитым начальным микрорельефом. Это позволит расширить диапазон изменения локальной скорости электроосаждения и изучить влияние начальной микрогеометрии поверхности на последующее формирование электроосажденных слоев при различной величине выравнивающей способности электролита [27–46].
Для формирования на катодной поверхности электроосажденных слоев с требуемыми микрогеометрическими параметрами необходимо определить микрораспределение скорости электроосаждения и на этой основе прогнозировать постепенную эволюцию поверхности каждого катодного участка.
Микрораспределение скорости электроосаждения непосредственно связано с выравнивающей способностью электролита [46]:
(1)
$P = {\text{ }}--{{\left( {{{{\text{dln}}i} \mathord{\left/ {\vphantom {{{\text{dln}}i} {{\text{dln}}i{\text{*}}}}} \right. \kern-0em} {{\text{dln}}i{\text{*}}}}} \right)}_{E}}$(2)
${{\Delta i} \mathord{\left/ {\vphantom {{\Delta i} {{{i}_{{{\text{av}}}}}}}} \right. \kern-0em} {{{i}_{{{\text{av}}}}}}}{\text{ = }}--\left( {P{{\Delta i{\text{*}}} \mathord{\left/ {\vphantom {{\Delta i{\text{*}}} {i_{{{\text{av}}}}^{*}}}} \right. \kern-0em} {i_{{{\text{av}}}}^{*}}}} \right).$Первичное распределение тока одинаково для геометрически подобных систем. Поэтому с помощью формулы (2) можно рассчитать микрораспределение скорости осаждения металла, используя данные о первичном распределении тока, полученные на макромодели конкретного микропрофиля.
Наряду с прямыми методами для быстрой полуколичественной оценки выравнивающей способности предлагалось также [43, 46] сравнивать результаты поляризационных измерений при двух режимах перемешивания электролита – двух скоростях вращения дискового электрода или двух значениях частоты колебаний катода в вертикальной плоскости. Поскольку эффективное заполнение осаждаемым металлом углублений микро- и наномасштаба зависит от величины выравнивающей способности электролита, то спустя полвека этот метод получил “второе рождение”, правда, без какого-либо упоминания о его происхождении [34–36, 41].
В данной статье проведено непосредственное сопоставление результатов прогнозирования микрораспределения скорости осаждения металла на катодах с регулярным двумерным микропрофилем и результатов экспериментальных измерений микрораспределения для электролитов с различными значениями выравнивающей способности.
МЕТОДИКА ЭКСПЕРИМЕНТОВ
Первичное распределение тока на макромоделях, используемых в работе микропрофилей, определяли с помощью метода электролитической ванны [13]. В этих измерениях использовали 0.001 N раствор карбоната натрия. На рабочий и вспомогательный электроды подавали переменный ток с напряжением 48 В и частотой 10 кГц. Индикаторным электродом служила платиновая проволока диаметром 0.5 мм и длиной 1 мм. Для расчета относительной первичной плотности тока на электроде ${{i{\text{*}}} \mathord{\left/ {\vphantom {{i{\text{*}}} {i_{{{\text{av}}}}^{*}}}} \right. \kern-0em} {i_{{{\text{av}}}}^{*}}}$ находили соответствующие значения локального градиента потенциала (dE/dl)l→ 0 и его среднего значения на профиле (dE/dl)av непосредственно у поверхности электрода, т.е. при l → 0:
(3)
${{i{\text{*}}} \mathord{\left/ {\vphantom {{i{\text{*}}} {i_{{{\text{av}}}}^{*}}}} \right. \kern-0em} {i_{{{\text{av}}}}^{*}}} = {{\left( {{{dE} \mathord{\left/ {\vphantom {{dE} {dl}}} \right. \kern-0em} {dl}}} \right)}_{{l \to 0}}}{{\left( {{{dE} \mathord{\left/ {\vphantom {{dE} {dl}}} \right. \kern-0em} {dl}}} \right)}_{{{\text{av}}}}}.$Расчетные значения относительной локальной скорости электроосаждения i/iav рассчитывали по формуле
(4)
${i \mathord{\left/ {\vphantom {i {{{i}_{{{\text{av}}}}}}}} \right. \kern-0em} {{{i}_{{{\text{av}}}}}}} = --P{{\left( {i{\text{*}}--i_{{{\text{av}}}}^{*}} \right)} \mathord{\left/ {\vphantom {{\left( {i{\text{*}}--i_{{{\text{av}}}}^{*}} \right)} {i_{{{\text{av}}}}^{*}}}} \right. \kern-0em} {i_{{{\text{av}}}}^{*}}} + {\text{ }}1.$Выравнивающую способность электролитов определяли из результатов профилографических измерений амплитуды пологого синусоидального микропрофиля до и после осаждения слоя металла из исследуемого электролита [13, 45, 46]:
(5)
$P = --\left[ {{a \mathord{\left/ {\vphantom {a {\left( {2\pi {{h}_{{{\text{av}}}}}} \right)}}} \right. \kern-0em} {\left( {2\pi {{h}_{{{\text{av}}}}}} \right)}}} \right]\ln \left( {{H \mathord{\left/ {\vphantom {H {{{H}_{0}}}}} \right. \kern-0em} {{{H}_{0}}}}} \right).$Для прогнозирования микрораспределения скорости осаждения металла использовали образцы, на поверхности которых имелась серия параллельных канавок глубиной 27–28 мкм треугольного поперечного сечения и углом между боковыми сторонами 90°. При этом на краю каждой канавки в процессе изготовления образовывался небольшой выступ – заусенец с размерами на порядок меньше, чем размеры других элементов микропрофиля.
На образцы осаждали медное покрытие из трех сернокислых электролитов меднения со значениями выравнивающей способности –0.6, 0, +0.6 (см. табл. 1).
Таблица 1.
Состав электролитов и режим процесса. Средняя толщина осажденного слоя меди – 10 мкм
Номер электролита | Компоненты и их концентрации | Плотность тока, А/дм2 | Выравнивающая способность, Р |
---|---|---|---|
1 | CuSO4 ⋅ 5H2O 50 г/л H2SO4 175 г/л |
Потенциостатический режим. Катодное перенапряжение –0.3 В |
–0.6 |
2 | CuSO4 ⋅ 5H2O 250 г/л H2SO4 50 г/л |
1 | 0.0 |
3 | CuSO4 ⋅ 5H2O 250 г/л H2SO4 50 г/л UBAC–HS* 5 мл/л UBAC MNT* 1 мл/л Cl– 90 мг/л |
3 | +0.6 |
Для этих же значений выравнивающей способности было рассчитано микрораспределение скорости осаждения металла с помощью формулы (4).
РЕЗУЛЬТАТЫ И ИХ ОБСУЖДЕНИЕ
На рис. 1 приведена микрофотография поперечного шлифа образцов с медным покрытием, нанесенным из электролита № 1, т.е. в условиях отрицательной выравнивающей способности.
Рис. 1.
Микрофотография медного покрытия, осажденного из сернокислого электролита (электролит № 1) без добавок в условиях преимущественного диффузионного контроля скорости процесса – при постоянном значении катодного перенапряжения ‒0.3 В. Начальная глубина канавки 28 мкм. Р = –0.6.
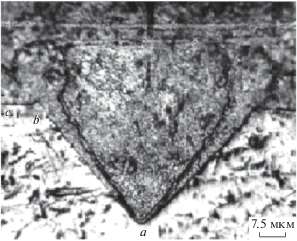
Аналогичная микрофотография, но для образца с покрытием, осажденным при положительном значении выравнивающей способности, показана на рис. 2.
Рис. 2.
Поперечный шлиф медного покрытия, осажденного из электролита с выравнивающей добавкой (электролит № 3, P = +0.6). Начальная глубина канавки 27 мкм.
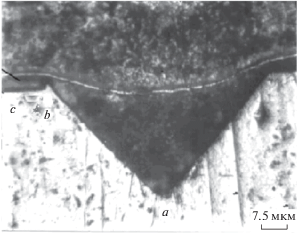
Измеренные локальные значения толщины слоя меди, а также кривые первичного распределения тока на исходном микропрофиле и рассчитанные на их основе кривые распределения скорости осаждения меди при различных значениях выравнивающей способности показаны на рис. 3. Там же приведены результаты измерений толщины осажденного слоя меди.
Рис. 3.
Первичное распределение тока и распределение толщины слоя осажденной меди, а также рассчитанные теоретически кривые распределения скорости осаждения металла на поверхности образца с канавками, показанными на рис. 1 и 2. Точки микропрофиля A, B, C на рис. 3 соответствуют точкам на рис. 1 и 2. 1 – Распределение толщины слоя меди, осажденной из электролита № 1 при Р = –0.3; 2 – распределение толщины слоя меди, осажденной из электролита № 2 при Р = 0; 3 – распределение слоя меди, осажденной из электролита № 3 при Р = +0.6; 4 – первичное распределение тока; 5 – теоретически рассчитанное распределение скорости осаждения меди при Р = –0.6 (электролит № 1); 6 – теоретически рассчитанное распределение скорости осаждения меди из электролита № 3 (Р = +0.6).
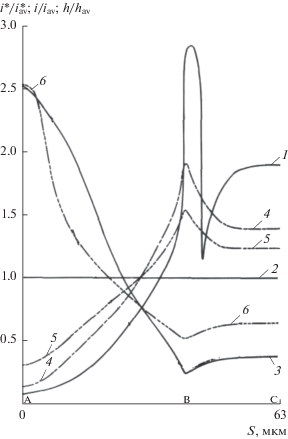
Сама величина выравнивающей способности может характеризовать микрораспределение скорости осаждения металла с высокой точностью лишь в условиях, когда фактические отклонения локальных значений парциальной плотности тока осаждения металла от ее средней величины на микропрофиле составляют небольшую долю последней, т.е. при
При невыполнении условия (6) расхождения между рассчитанными и экспериментальными значениями будут возрастать по мере увеличения абсолютных значений выравнивающей способности. Соответственно, при P → 0 рассчитанное микрораспределение будет приближаться к определенному экспериментально.
С учетом этого, наблюдаемые отклонения фактической толщины слоя осажденной меди от рассчитанной теоретически при P ≥ 0 можно рассматривать как ожидаемые и приемлемые. Исключением является граница плоской поверхности образца и края канавки, на которой имеется небольшой заусенец, образовавшийся при нарезании канавок и затем воспроизводившийся при гальванопластическом тиражировании образцов. При положительном значении P (см. рис. 2) заусенец исчезает, т.е. полностью сглаживается в самом начале процесса осаждения покрытия, что вполне согласуется с теорией. В то же время при отрицательных значениях выравнивающей способности (Р = –0.6) на заусенце реализуется очень высокая скорость осаждения металла, быстро приводящая к значительному изменению микропрофиля на этом участке катодной поверхности. Поэтому при P < 0 (рис. 1) заусенец быстро трансформируется в нарост в форме полуцилиндра, диаметр которого в десятки раз превосходит высоту заусенца. Природа этого явления связана с диффузионным контролем скорости процесса электроосаждения меди при катодном перенапряжении 300 мВ. Когда радиус кривизны рассматриваемого участка катодной поверхности (радиус кривизны вершины заусенца) стремится к нулю, градиент концентрации диффундирующих ионов в этой зоне раствора стремится к бесконечности [13]. Такой рост градиента концентрации эквивалентен пропорциональному росту скорости осаждения меди, что и выражается в ускоренном формировании полуцилиндра. При этом участок поверхности этого полуцилиндра, соседний по отношению к плоскому участку катодной поверхности, расположенному между точками B и C на рис. 1 и 2, представляет собой “отвлекающий катод” по отношению к этой зоне, что ведет к образованию узкой щели между растущим полуцилиндром и слоем меди, осажденной на участке BC.
Таким образом, распределение медного осадка на рис. 1–3 в определенной степени отражает распределение металла не на начальном микропрофиле, а на уже эволюционирующем. Последнее особенно заметно, когда в процессе электроосаждения существенно изменяется микрогеометрия катодной поверхности. Проявление эффекта эволюции особенно заметно при сопоставлении на рис. 3 кривой 5, характеризующей теоретически рассчитанное микрораспределение тока для начальной формы микропрофиля, и кривой 1, на которой уже в значительной степени проявляется эффект эволюции и, в частности, обнаруживается резкий спад плотности тока на экранируемом участке поверхности.
Особенно резко роль масштабного фактора в перераспределении тока с относительно ровных (в микромасштабе) участков поверхности на микро- и субмикровыступы проявляется, когда парциальная плотность тока осаждения металла достигает предельного значения. В таком режиме величина катодного перенапряжения оказывается достаточной для образования на катодной поверхности трехмерных зародышей кристаллов. Эффективная толщина диффузионного слоя у таких зародышей приблизительно равна их радиусу [13]. Это означает увеличение локальной плотности тока на поверхности зародышей обратно пропорционально их радиусу, что и приводит, в конце концов, к формированию порошкообразных осадков металла, имеющих дендритное строение.
К сожалению, прогнозирование распределения скорости осаждения на микропрофиле в условиях предельной плотности тока может иметь только качественный характер. Однако этого оказалось вполне достаточно при решении задачи формирования на катодной поверхности так называемых “адгезионных покрытий”, сочетающих дендритную структуру осажденного слоя с его высокой механической прочностью [10].
При электроосаждении металлов в условиях, когда выравнивающая способность равна нулю, эффект эволюции сводится к так называемому “геометрическому выравниванию” и конкурирующему с ним процессу роста “кристаллической шероховатости” [44, 45].
Если осаждение металла ведут из электролита с положительной выравнивающей способностью, то для определения окончательных микрогеометрических характеристик катодной поверхности можно поэтапно задавать небольшие приращения средней толщины осаждаемого слоя и после каждого этапа проводить теоретической расчет распределения скорости осаждения на уже изменившейся поверхности.
В последнее десятилетие в связи с изменениями в технологии производства компонентов электронных устройств возник интерес к процессу заполнения медным осадком глухих цилиндрических отверстий микро- и наномасштаба. Используя принцип подобия для первичного электрического поля и концентрационного поля для выравнивающей добавки, можно ожидать, что для таких элементов катодной поверхности ингибирующее действие выравнивающей добавки, которое она оказывает на разряд ионов металла на боковых сторонах углублений и на дне, будет усиливаться в соответствии с ростом отношения l2/d [8]. Здесь l – глубина глухого отверстия, а d – его диаметр. Это, в свою очередь, означает, что для эффективного заполнения медью глухих отверстий малого размера целесообразно использовать электролиты с высокой выравнивающей способностью.
ВЫВОДЫ
1. При электроосаждении металлов количественные данные о выравнивающей способности электролитов и первичном распределении тока позволяют прогнозировать микрораспределение скорости осаждения металла из электролитов с выравнивающими добавками.
2. При электроосаждении металлов в условиях отрицательной выравнивающей способности теоретический прогноз позволяет правильно определить микроучастки поверхности катода, на которых локальная скорость осаждения значительно превосходит среднюю величину.
Список литературы
Datta, M. and Landolt, D., Fundamental aspects and applications of electrochemical microfabrication, Electrochim. Acta, 2000, vol. 45, p. 2535.
Schultze, J.W. and Bressel, A., Principles of electrochemical micro- and nano-system technologies, Electrochim. Acta, 2001, vol. 47, p. 3.
Razali, A.R. and Qin, Y.I., A Review on Micro-manufacturing, Micro-forming and their Key Issues, Procedia Engineering, 2013, vol. 53, p. 665.
Fe, M. W. and Chan, W.L., A review on the state of the art microforming technologies, Intern. J. Adv. Manufacturing Technol., 2013, vol. 67, p. 2411.
Гамбург, Ю.Д. Развитие теории электрокристаллизации. Электрохимия. 2016. Т. 52. С. 934. [Gamburg, Y.D., Development of the electrocrystallization theory, Russ. J. Eleсtrochem., 2016, vol. 52, p. 832.]
Волгин, В.М., Давыдов, А.М. Проблемы массопереноса в электрохимических системах. Электрохимия. 2012. Т. 48. С. 627. [Volgin, V.M. and Davydov, A.D., Mass-transfer problems in the electrochemical systems, Russ. J. Eleсtrochem., 2012, vol. 48, p. 565.]
Коротков, В.В., Кудрявцев, В.Н., Загорский, Д.Л., Кругликов, С.С., Сульянов, С.Л., Бедин, С.А. Электроосаждение металлов группы железа в поры трековых матриц для получения нанопроволок. Гальванотехника и обработка поверхности. 2015. Т. 23. № 1. С. 24. [Korotkov, V.V., Kudryavtsev, V.N., Kruglikov, S.S., Zagorskii, D.L., Sul’yanov, S.N., and Bedin, S.A., Electrodeposition of metals of iron groop into the pores of track membranes for the preparation of nanowires, Galvanotekhnika i obrabotka poverkhnosti (in Russian), 2015, vol. 23, no. 1, p. 24.]
Кругликов, С.С. О некоторых особенностях использования потенциостатического режима при электроосаждении металлов и сплавов. Гальванотехника и обработка поверхности. 2016. Т. 24. № 1. С. 40. [Kruglikov, S.S., Certain features of the electrodeposition of metals and alloys under potentiostatic conditions, Galvanotekhnika i obrabotka poverkhnosti (in Russian), 2016, vol. 24, no. 1, p. 40.]
Кругликов, С.С., Некрасова, Н.Е., Кругликова, Е.С. О микрорассеивающей способности электролитов хромирования. Гальванотехника и обработка поверхности. 2016. Т. 24. № 3. С. 4. [Kruglikova, E.S., Kruglikov, S.S., and Nekrasova, N.E., On the microthrowing power of chromium plating baths, Galvanotekhnika i obrabotka poverkhnosti (in Russian), 2016, vol. 24, no. 3, p. 4.]
Кругликов, С.С., Некрасова, Н.Е., Касаткин, В.Э., Корнилова, С.И. Применение импульсного тока для получения механически прочных гальванических покрытий с развитой поверхностью. Гальванотехника и обработка поверхности. 2016. Т. 24. № 4. С. 30. [Kruglikov, S.S., Nekrasova, N.E., Kasatkin, V.E., and Kornilova, S.I., Electrodeposition of Metal Layers with High Mechanical Strength and Large True Surface Area Using Pulsing Current, Galvanotekhnika i obrabotka poverkhnosti (in Russian), 2016, vol. 24, no. 4, p. 30.]
Загорский, Д.Л., Артемов, В.В., Коротков, В.В., Кругликов, С.С., Бедин, С.А. Особенности роста и стабильность нанопроволок из различных металлов. Поверхность. Рентгеновские, синхротронные и нейтронные исследования. 2016. Т. 11. № 1. С. 87. [Zagorsky, D.L., Artemev, V.V., Korotkov, V.V., Kruglikov, S.S., and Bedin S.A., Specific Features, Surface Investigation.X-Ray, Synchrotron and Neutron Techniques, 2017, vol. 11, no. 1, p. 99.]
Kardos, O. and Foulke, D.G., in: Adv. in Electrochemistry and Electrochemical Engineering, ed. Delahay, P. and Tobias, C., N.Y.: Wiley-Intersci., 1962, vol. 2, p. 145.
Кругликов, С.С. Особенности распределения скорости электроосаждения металлов и сплавов в процессах формирования электроосажденных слоев при нанесении покрытий на компоненты электронных устройств. Гальванотехника и обработка поверхности. 2017. Т. 25. № 1. С. 41. [Kruglikov, S.S., Macro- and microdistribution of the deposition rate in the plating of the components of electronic devices, Galvanotekhnika i obrabotka poverkhnosti (in Russian), 2017, vol. 25, no. 1, р. 41.]
De Fogelaere, M., Somme, V., Springborn, H., and Michelsen-Mohammadein, U., High-speed plating for electronic applications, Electrochim. Acta, 2001, vol. 47, p. 109.
Tajiri, K., Nakamura, T., Kabeya, Z., Yamanaka, Y., Naito, F., Kato, T., and Takasaki, T., Development of an electroformed copper lining for accelerator components, Electrochim. Acta, 2001, vol. 47, p. 143.
Peeters, P., Von der Hoorn, G. Daenen, T., Kurowski, A., and Staikov, G., Properties of electroless and electroplated Ni–P and its application in microgalvanics, Electrochim. Acta, 2001, vol. 47, p. 161.
Cachet-Vivier, C., Vivier, V., Cha, C.S., and Nedelev, Yu.L.T., Electrochemistry of powder material studied by means of the cavity microelectrode, Electrochim. Acta, 2001, vol. 47, p. 181.
Andricacos, P.C., Ducovic, J.Y., Horkans, J., and Deligianni H., Damascene copper electroplating for chip interconnections, IBM J. Res. Div., 1998, vol. 42, p. 567.
Healy, J.P., Pletcher, D., and Goodenough, M., The chemistry of the additives in the acid copper electroplating bath. 1. Polyethylene-glycol and chloride-ion, J. Electroanal. Chem., 1992, vol. 338, p. 155.
Kelly, J.J. and West, I.C., Copper deposition in the presence of polyethylene glycol. 1. Quartz crystal microbalabce study, J. Electrochem. Soc., 1998, vol. 145, p. 3472.
Kelly, J.J. and West, L.C., Copper deposition in the presence of polyethylene glycol. II. Electrochemical impedance spectroscopy, J. Electrochem. Soc., 1998, vol. 145, p. 3477.
Feng, Z.V. and Gewirth, A.A., Inhibition due to the interaction of polyethylene glycol, chloride, and acid copper in plating baths: a surface-enhanced Raman study, J. Phys. Chem., 2003, vol. 107, p. 9415.
Doblhofer, K., Wasle, S., Soares, D.M., Weil, K.G., and Ertl, G., An EQSM study of the electrochemical copper-(II)/copper(I)/copper system in the presence of PEG and chloride ions, J. Electrochem. Soc., 2003, vol. 150, p. 657.
Kondo, K., Matsumoto, T. and Watanabe, K., Role of additives for copper damascene electrodeposition. Experimental study on inhibition and acceleration effects, J. Electrochem. Soc., 2004, vol. 151, p. 250.
Hebert, K.R., Role of chloride ions in the suppression of copper electrodeposition by polyethylene glycol, J. Electrochem. Soc., 2005, vol. 152, p. 283.
Cao, Y., Taephaisitphongse, P., Chalupa, R., and West, A.C., Three-additive model of superfilling of copper, J. Electrochem. Soc., 2001, vol. 148, p. 466.
Georgiadou, M., Veyret, D., Sani, R.L., and Alkire, R.C., Simulation of shape evolution during electrodepiosition of copper in the presence of additive, J. Electrochem. Soc., 2001, vol. 148, p. 54.
West, A.C., Mayer, S., and Reid J., A superfilling model that predicts bump formation, Electrochem. Solid-Statye Lett., 2001, vol. 4, p. 50.
Moffat, N.P., Wheeler, T., Huber, W.H., and Josell, D., Superconformal electrodeposition of copper, Electrochem. Solid-State Lett., 2001, vol. 4, p. 26.
Josell, D., Wheeler, D., Huber, W.H., Bonevich, J.E., and Mofatt, T.P., A simple equation for predicting superconformal electrodeposition in submicrometer trenches, J. Electrochem. Soc., 2001, vol. 148, p. 767.
Akolkarm, R. and Landau, U., A time-dependent transport-kinetics model for additive interactions in copper interconnect metallization, J. Electrochem. Soc., 2004, vol. 151, p. 702.
Moffat, N.P., Wheeler, D., Edelstein, M.D., and Josell, D., Superconformal film growth: mechanism and quantification, IBM J. Res. Div., 2005, vol. 49, p. 19.
Dow, W.P., Yen, M.Y., Lin, W.B., and Ho, S.W., Influence of molecular weight of polyethylene glycol on microvia filling by copper electroplating, J. Electrochem. Soc., 2005, vol. 152, p. 769.
Akolkar, R. and Landau, U., Mechanistic analysis of the “bottom-up” fill in copper interconnect metallization, J. Electrochem. Soc., 2009, vol. 156, P. 351.
Mendez, J., Akolkar, R, and Landau, U., Polyether supressors enabling copper metallization of high aspect ratio interconnects, J. Electrochem. Soc., 2009. vol. 156, p. 474.
Adolf, J. and Landau, U., Predictive analytical fill model interconnect metallization providing optimal additives concentrations, J. Electrochem. Soc., 2001, vol. 158, p. 469.
Huang, Q., Bakern-O’Neal, B.C., Kelly, J.J., Broekmann, P., Wirth, K., Emmet, C., Martin, M., Hahn, M., Wagner, A., and Mayer, D., Supressor effects during copper superfilling of sub-100 nm lines. Electrochem. Solid-State Letter, 2009, vol. 12, p. 27.
Huang, Q., Liu, J., and Baker-O’Neal, B., An electrochemical method of suppressor screening for Cu plating in sub-100 nm lines, J. Electrochem. Soc., 2014, vol. 161, p. 207.
Rayan, K., Dunn, K., and van Euisden, J., Development of electrochemical copper deposition screening methodologis for next generation additive selection, Microelectron Eng., 2012, vol. 92, p. 91.
Bard, A.J. and Faulkner, L.R., Electrochemical Methods: Fundamentals and Applications, 2nd ed. N.Y.: Wiley-VCH, 2001, p. 339.
Boehme, L. and Landau, U., Rapid screening techniques of plating additives for bottom-up metallization of nano-scale features, J. Appl. Electrochem., 2016, vol. 46, p. 39.
Gamburg, Y.D. and Zangari, G., Theory and Practice of Metal Electrodeposition, N.Y.: Springer, 2011, 438 p. [Гамбург, Ю.Д., Зангари, Дж. Теория и практика электроосаждения металлов, пер. с англ. М.: БИНОМ. Лаборатория знаний, 2015. 438 с.]
Kruglikov, S.S., Kudryavtsev, N.T., and Semina E.V., On the relationship between the molecular structure of organic inhibitors and their leveling effects in nickel electrodeposition, Proc. 7th international metal finishing conf. (“Interfinish 68”), Hannover, May 1968. P. 66.
Kruglikov, S.S., Surface leveling in the electrodeposition of metals, Itogi nauki. Electrochemistry, 1965. VINITI. Published for the US Dept. of Commerce by the Israel Program of Scientific Translations. [Кругликов, С.С. Выравнивание поверхности при электроосаждении металлов, в сб. Итоги науки, Сер. Химия, Электрохимия. 1965. М.: ВИНИТИ, 1967. С. 117.]
Кругликов, С.С., Коварский, Н.Я. Выравнивание микронеровностей при электроосаждении металлов, в сб. Итоги науки и техники. Электрохимия. Т. 10, М.: ВИНИТИ, 1975, С. 106. [Kruglikov, S.S. and Kovarskii, N.Ya., Microroughnesses leveling in the electrodeposition of metals, Itogi nauki. Electrochemistry, M.: VINITI, 1975, vol. 10, p. 106.
Kruglikov, S.S. and Smirnova, T.A., Leveling power: definition and methods of evaluation, Proc. of 8th Congress of the International Union for Electrodeposition and Surface Finishing (“Interfinish-72”), Zuerich, Forster Verl., p. 105.
Дополнительные материалы отсутствуют.