Электрохимия, 2019, T. 55, № 3, стр. 318-328
Аноды литий-ионных аккумуляторов, полученные спеканием кремниевого нанопорошка
Е. В. Астрова a, *, В. Б. Воронков a, А. М. Румянцев a, А. В. Нащекин a, А. В. Парфеньева a, Д. А. Ложкина a
a Физико-технический институт им. А.Ф. Иоффе РАН
194021 Санкт-Петербург, Политехническая ул., 26, Россия
* E-mail: east@mail.ioffe.ru
Поступила в редакцию 27.08.2018
После доработки 01.10.2018
Принята к публикации 12.10.2018
Аннотация
Исследован изохронный отжиг предварительно спрессованных образцов кремниевого нанопорошка. Определена плотность, структура и электропроводность полученного материала в зависимости от температуры спекания. Исследованы электрохимические характеристики анодов, спеченных в диапазоне температур 1100–1200°С, с помощью гальваностатических испытаний и циклической вольтамперометрии. Установлено, что наилучшие результаты демонстрирует образец, отжигавшийся при Т = 1150°С, имеющий плотность 1.60 г/cм3 и обладающий связным кремниевым каркасом и системой открытых пор.
ВВЕДЕНИЕ
Несмотря на интенсивные исследования в области кремниевых анодов для литий-ионных аккумуляторов (см., например, обзоры [1, 2]), практическое применение их весьма ограничено. Причинами, которые сдерживают внедрение наноструктурированных кремниевых электродов [3–6] в массовое производство, являются сложность технологии, недостаточно хорошая устойчивость к деградации и высокая стоимость. Для повышения удельной емкости производители анодных материалов чаще всего предлагают Si-порошок в виде добавки к углеродным порошкам. Этот вариант привлекателен тем, что он максимально приближен к существующей “намазной” технологии изготовления аккумуляторов, однако такие аноды быстро деградируют из-за нарушения электрического контакта между Si-частицами и токопроводящими составляющими электродной массы. Более перспективными с нашей точки зрения являются электроды, имеющие связную структуру кремниевого каркаса. Для создания таких электродов в настоящей работе предлагается использовать спекание кремниевого нанопорошка. В отличие от аналогичной задачи для солнечных элементов, где стремятся сформировать материал, близкий к монолитному кремнию, анод Li-ионного аккумулятора должен обладать достаточно высокой пористостью. Поэтому, вместо рекристаллизации кремниевого порошка при одновременном воздействии высокого давления и температуры (hot pressed Si) [7, 8], в настоящей работе предлагается использовать отжиг предварительно спрессованного нанопорошка.
Задачей работы явилось изучение процесса спекания порошкового кремния, разработка методики формирования электродов и исследование их электрохимических характеристик.
ЭКСПЕРИМЕНТАЛЬНАЯ ЧАСТЬ
Спекание порошка
Исходным материалом для экспериментов служил коммерческий продукт китайской фирмы Hongwu Nanometer, полученный методом термического разложения силана с помощью лазера. Порошок состоял из сферических частиц размером 30–50 нм (рис. 1) с содержанием Si ≥ 99%, удельная площадь поверхности которого составляла 90–95 м2/г. Наночастицы имели кристаллическую структуру.
Компрессия осуществлялась в пресс-форме, в которую засыпалось 15–20 мг порошка. Прессование проводилось всухую с помощью гидравлического пресса при давлении 140–210 МПа. Полученная таблетка имела диаметр ~6 мм и толщину 400–600 мкм. Спекание таблеток проводилось при Т = 750–1250°С в муфельной печи с горизонтальной кварцевой трубой диаметром 46 мм, продуваемой аргоном высокой чистоты 99.998% (ТУ 6-21-12-94), расход газа составлял 100 л/ч. Содержание примесей в Ar: O2 < 2 × 10–4%, H2O < < 3 × 10–4%. Плотность спрессованного и спеченного материала определялась как ρ = m/lS, где m – масса, l – толщина таблетки, S – ее площадь.
Для определения удельного электрического сопротивления использовалась четырехзондовая установка с головкой фирмы Jandel (Великобритания). Электронно-микроскопические исследования проводились с помощью растрового электронного микроскопа (РЭМ) JSM 7001F (JEOL, Япония) в федеральном ЦКП “Материаловедение и диагностика в передовых технологиях” при ФТИ им. А.Ф. Иоффе. Для изучения зависимости свойств материала от температуры спекания использовался изохронный отжиг в течение 1 ч. Было изготовлено 2 серии образцов. Первая серия после прессовки имела более низкое значение плотности, чем вторая: для нее среднее значение плотности ρс = 0.92 г/cм3, что соответствует пористости р = (1 – ρ/ρSi) × 100% = 60.5%, где плотность кремния ρSi = 2.33 г/см3.
После термообработки при высокой температуре происходила значительная усадка материала, которая выражалась в уменьшении диаметра и толщины таблеток, т.е. в увеличении их плотности. На рис. 2 хорошо видно изменение диаметра и цвета таблеток. При 1250°С спекание приводит к тому, что образец приобретает серый цвет, как у монолитного кремния. На графике рис. 3 приведена зависимость пористости от температуры, из которой видно, что для отжига при Т < 1050°С пористость изменяется незначительно, а при более высокой температуре она резко уменьшается, снижаясь до 11.6%. Эти результаты согласуются с данными работы [9].
Образцы раскалывали и проводили исследования структуры с помощью электронного микроскопа. На рис. 4 видно, что укрупнение Si-частиц и пор становится заметно, начиная с Т = 1150°С.
Следует отметить, что для большинства образцов картина оставалась неизменной как в средней по глубине области, так и вблизи поверхности. Образование корки наблюдалось только при высоких температурах >1200°С. На рис. 5 приводится вид сверху, на котором для температуры 1225°С видно практически полное исчезновение пор и появление тонкой структуры на образовавшихся гранулах размером порядка одного микрона.
Электропроводность образцов возрастает с увеличением температуры отжига, что свидетельствует о появлении связной структуры кремния и превышении порога протекания. На рис. 6 зависимость удельного электрического сопротивления ρel от температуры отжига представлена в полулогарифмическом масштабе. Высокой температуре 1250°С соответствует удельное сопротивление 1.4 Ом см; проводимость, определявшаяся термозондовым методом, оказалась р-типа. Снижение температуры отжига приводит к возрастанию ρel. Для Т < 1150°С сопротивление увеличивается на несколько порядков.
Рис. 6.
Удельное электрическое сопротивление спеченного кремния в зависимости от температуры отжига. Время отжига 1 ч.
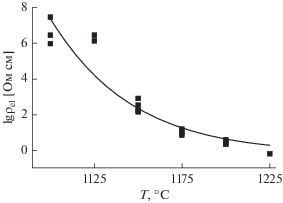
Вторая серия образцов прессовалась при более высоком давлении, и средняя плотность компакта составляла ρс = 1.07 г/cм3, что соответствует пористости р = 54%. Отжиг проводился по 3 образца одновременно при пяти температурах в интервале от 1100 до 1200°С, время отжига составляло также 1 ч. По одному образцу было использовано для проведения электронно-микроскопических исследований и измерения электропроводности, из двух других были изготовлены аноды. На рис. 7 приведена фотография полученных образцов.
Изменение плотности прессования ρс оказывает влияние на плотность образцов после спекания. На рис. 8 построена зависимость плотности от температуры отжига для образцов обеих серий, из которой видно, что более компактное прессование снижает температуру спекания. На рис. 9 представлено среднее значение пористости в зависимости от температуры отжига для образцов серии 2.
Рис. 8.
Зависимость плотности спеченного материала от температуры отжига для образцов с разной исходной плотностью ρс = 0.92 и 1.07 г/см3.
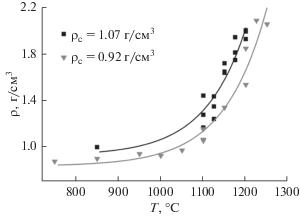
На рис. 10 приведено изображение поперечного сечения образцов серии 2. Здесь увеличение размера гранул можно видеть, начиная с Т = = 1125°С. При Т ≤ 1150°С поры остаются открытыми, а при более высоких температурах большая их часть закрывается и уменьшается в размере. Элементный состав, определявшийся методом энергодисперсионной рентгеновской спектроскопии, показал, что во всех спеченных образцах содержится 93–94% Si, 2.8–3.6% O и 3.4–3.5% C. Если присутствие кислорода можно объяснить окислением, происходящим при высокой температуре за счет следов кислорода и воды, имеющихся в Ar, то появление углерода не вполне понятно (по паспорту, на Si-порошок содержание C < 15 ppm).
Электрохимические характеристики анодов
Для формирования токосъемного контакта на одну из сторон предварительно подшлифованной спеченной таблетки проводилось химическое и гальваническое осаждение меди из электролита на основе медного купороса. Затем толщина кремниевого слоя lSi уменьшалась до 10–30 мкм с помощью шлифовки мелким порошком карбида кремния. Масса кремния в составе анодной структуры mSi определялась из плотности спеченной таблетки ρ и толщины lSi. Полученный анод помещался в двухэлектродную дисковую ячейку CR2032 с литиевым противоэлектродом и электролитом марки TC-E918 (Tinci, КНР), который представлял собой 1 M LiPF6 в смеси EC/PC/DEC/EMC/PA (этиленкарбонат, пропиленкарбонат, диэтилкарбонат, этилметилкарбонат, пропилацетат). Зарядно-разрядные кривые измерялись на стенде CT3008W-5V10mA (Neware, КНР). Циклические вольт-амперные характеристики (ЦВА) фиксировали с помощью потенциостата PGSTST302N (Metrohm, Нидерланды). Из образцов второй серии было изготовлено по 2 анода, спеченных при одной и той же температуре, которые использовались для исследования зарядно-разрядных характеристик и циклических ресурсных испытаний (табл. 1) и для ЦВА (табл. 2).
Таблица 1.
Параметры кремниевых электродов для гальваностатических испытаний
№ образца | Т, °С | lSi, мкм | S, мм2 | mSi, мг |
---|---|---|---|---|
36 | 1200 | 23 | 20.6 | 0.91 |
39 | 1175 | 23 | 18.9 | 0.79 |
45 | 1150 | 10 | 21.1 | 0.35 |
51 | 1125 | 18 | 25.4 | 0.62 |
47 | 1100 | 15 | 27.1 | 0.52 |
Таблица 2.
Параметры кремниевых электродов для ЦВА
№ образца | Т, °С | lSi, мкм | S, мм2 | mSi, мг |
---|---|---|---|---|
38 | 1200 | 26 | 14.3 | 0.74 |
41 | 1175 | 21 | 16.7 | 0.61 |
43 | 1150 | 30 | 22.8 | 1.18 |
50 | 1125 | 28 | 25.4 | 0.89 |
48 | 1100 | 30 | 25.9 | 1.13 |
Заряд (литирование) и разряд (делитирование) ячейки на первых 10 циклах осуществлялись в гальваностатическом режиме при токе 0.1 А/г. При внедрении Li были установлены следующие ограничения: по емкости Q = 1000 мА ч/г и по напряжению кремниевого электрода U = 10 мВ, при экстракции – только по напряжению U = 2 В. Таким образом время заряда и время разряда составляло по 10 ч (режим С/10). Запись кривых ЦВА для пяти первых циклов проводилась при скорости развертки 0.05 мВ/с. На рис. 11 приведены полученные данные для образцов, спекавшихся при трех разных температурах.
Рис. 11.
Зарядно-разрядные кривые 1, 2 и 5 циклов (a, в, д) и циклические вольт-амперные характеристики первых 5 циклов (б, г, е) для образцов, отжигавшихся при разной температуре. Режим заряда–разряда 0.1 С. Скорость развертки напряжения для ЦВА 0.05 мВ/с.
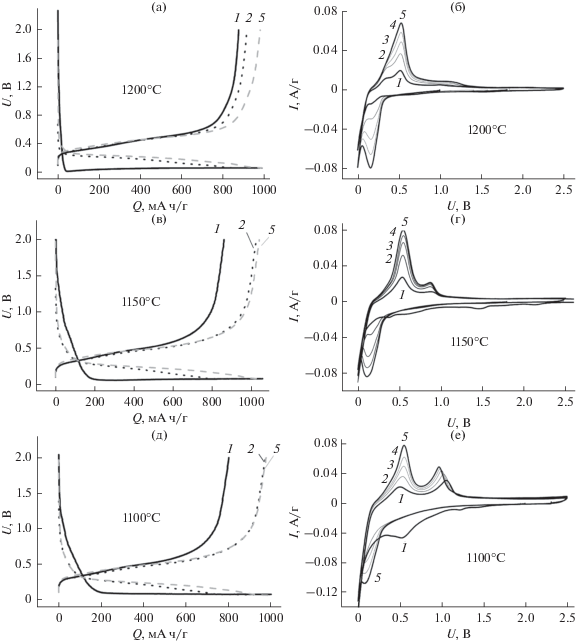
Из рисунка видно, что температура спекания порошка влияет как на форму зарядно-разрядных кривых, так и на пики ЦВА. При первом гальваностатическом литировании напряжение U быстро опускается до значения в несколько десятков мВ, причем наиболее резкое падение U наблюдается для образцов, отожженных при высоких температурах 1200 и 1175°С. Внедрению лития на последующих циклах соответствует скругленная форма кривых заряда, что свидетельствует об аморфизации кремния, которая происходит при первом литировании. Как известно [10], малому размеру Si-частиц соответствуют более округлые формы кривых заряда и разряда, что наблюдается и для наших образцов, для которых повышение температуры отжига приводит к укрупнению зерен. На следующих циклах структура сплавов LixSi и делитированного кремния остается аморфной. Для всех образцов на первом цикле разрядная емкость Qdch оказалась меньше, чем зарядная, за счет потерь, обусловленных образованием на поверхности кремния твердоэлектролитной пленки из продуктов разложения электролита SEI (Solid Electrolyte Interface). Эти потери зависят от площади поверхности открытых пор: чем выше пористость (низкие Т спекания), тем больше потери. На рис. 12 построена зависимость разрядной емкости от номера цикла для всех пяти образцов. Видно, что низкотемпературные образцы уже на втором цикле выходят на высокие значения Qdch, а для высокотемпературных этот процесс растягивается, и выход на постоянное значение емкости происходит только через 6 циклов. Это может быть связано с появлением трещин и образованием на их поверхности нового SEI. Оценка суммарных потерь емкости за первые 6 циклов указывает на то, что образцы, отожженные при более высокой температуре, демонстрируют меньшие необратимые потери заряда (рис. 13).
Рис. 12.
Зависимость разрядной емкости от числа циклов для образцов, спекавшихся при разной температуре.
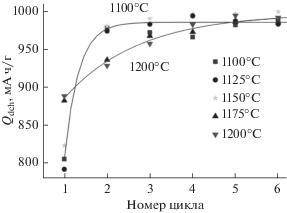
На кривых ЦВА также наблюдается существенное отличие первого заряда от последующих: для образцов, спеченных при Т ≤ 1150°C, при потенциалах выше 0.3 В видны катодные пики, связанные с формированием SEI (рис. 14). Этот процесс происходит, в основном, при потенциалах 1–0.3 В. На рис. 15 построена зависимость кулоновской эффективности для первых пяти циклов ЦВА, которая достаточно хорошо согласуется с результатами рис. 12.
Рис. 14.
Сравнение ЦВА 1 цикла для образцов, отжигавшихся при разной температуре, °С: 1200, 1150 и 1100. Cкорость развертки потенциала 0.05 мВ/с.
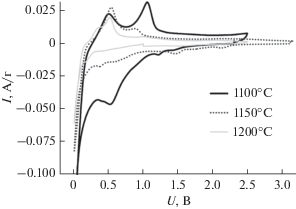
Рис. 15.
Зависимость кулоновской эффективности от номера цикла, полученная из данных ЦВА, для образцов, отжигавшихся при разной температуре.
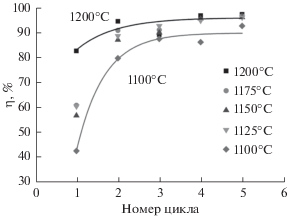
Сами зависимости ЦВА в целом имеют вид, характерный для кремниевых электродов. Токи максимумов увеличиваются с номером цикла, что, по-видимому, связано с разрыхлением структуры, повышением ионной проводимости и облегчением диффузии лития. В большинстве работ на кривых ЦВА регистрируется два анодных максимума при U ≈ 0.3 и 0.5 В [10–14]. В наших образцах анодный пик тока при потенциале 0.3 В различим только в случае высокотемпературного спекания, в остальных случаях преобладает максимум при потенциале 0.5 В. Для низкотемпературных образцов можно также видеть второй хорошо различимый пик тока при U ≈ 1 В. Его появление может быть обусловлено тем, что в образцах, отжигавшихся при Т = 1100°С, при катодной поляризации происходит накопление бóльшего заряда, чем в образцах, отжигавшихся при более высокой температуре (см. табл. 3). При этом становится возможным образование новой фазы LixSi c более высоким содержанием лития. Экстракция лития из этой фазы соответствует пику на ЦВА при потенциале 1 В.
Таблица 3.
Удельная зарядная (Qch), разрядная (Qdch) емкость и кулоновская эффективность (η), полученные из ЦВА
T, °C | Параметр | Цикл 1 | Цикл 2 | Цикл 3 |
---|---|---|---|---|
1200 | Qch, мА ч/г | 74 | 98 | 145 |
Qdch, мА ч/г | 61 | 92 | 140 | |
η, % | 82 | 94 | 97 | |
1175 | Qch, мА ч/г | 190 | 190 | 245 |
Qdch, мА ч/г | 120 | 175 | 235 | |
η, % | 61 | 91 | 96 | |
1150 | Qch, мА ч/г | 220 | 190 | 230 |
Qdch, мА ч/г | 130 | 170 | 220 | |
η, % | 57 | 87 | 96 | |
1125 | Qch, мА ч/г | 240 | 210 | 265 |
Qdch, мА ч/г | 130 | 170 | 250 | |
η, % | 60 | 88 | 96 | |
1100 | Qch, мА ч/г | 330 | 195 | 260 |
Qdch, мА ч/г | 140 | 175 | 240 | |
η, % | 43 | 80 | 92 |
Оценим мощностные характеристики спеченных кремниевых анодов. Для этого аноды после 10–15 циклов испытаний в режиме C/10 разряжались при повышенных плотностях тока, что соответствовало уменьшению времени разряда. На рис. 16a–16в для образцов, отжигавшихся при разной температуре, приведены зарядно-разрядные кривые, полученные при одинаковых плотностях тока заряда j = 0.1 A/г (время внедрения лития 10 ч) и разных плотностях тока разряда j = 0.1, 0.5 и 1 A/г (время экстракции лития, соответственно, 10, 2 и 1 ч). Для высоко- и низкотемпературного спекания повышение плотности тока при делитировании приводит к существенному снижению разрядной емкости, для средних температур это снижение намного меньше. На рис. 16г показана зависимость разрядной емкости от температуры спекания порошка для плотности тока, которая соответствовала времени разряда 1 ч. Она хорошо аппроксимируется гауссовой кривой с максимумом при Т = 1142°С.
Рис. 16.
Разрядные кривые при переменном времени разряда: 10, 2 и 1 ч для образцов, отжигавшихся при разной температуре (a)–(в). Разрядная емкость в зависимости от температуры отжига для времени разряда 1 ч (г). Время заряда всюду 10 ч.
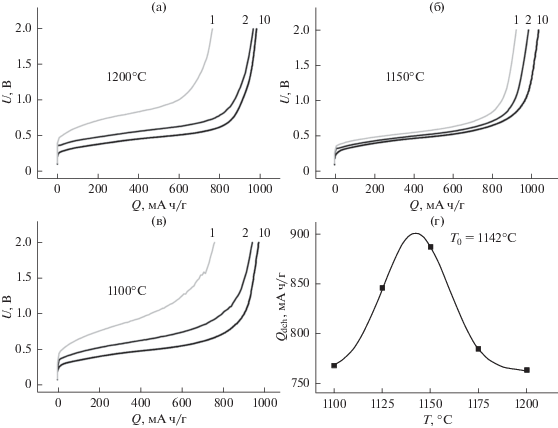
Затем аноды, прошедшие несколько циклов заряда–разряда при высокой скорости делитирования, были поставлены на ресурсные испытания при одинаковом токе заряда и разряда j = 0.2 A/г, что соответствовало 5-часовому режиму С/5. Результаты испытаний представлены на рис. 17. Стабильное циклирование демонстрирует только образец, отжигавшийся при средней температуре использованного диапазона 1150°С (рис. 17в). Низко- и высокотемпературные образцы деградируют либо сразу же (рис. 17д), либо через 30–60 циклов (рис. 17a, 17б, 17г). При этом кулоновская эффективность для всех образцов, также показанная на графиках рис. 17, сохраняется на высоком уровне, близком к 100%. Снижение разрядной емкости при делитировании обусловлено тем, что в процессе заряда (внедрения лития) ограничение по напряжению величиной 10 мВ срабатывает раньше, чем ограничение по накопленному заряду, т.е. происходит уменьшение зарядной емкости до значений меньших, чем 1000 мА ч/г. Причиной быстрого падения напряжения до 10 мВ является возрастающее сопротивление кремниевого электрода, что может быть связано с постепенным его разрушением.
ОБСУЖДЕНИЕ РЕЗУЛЬТАТОВ И ВЫВОДЫ
Проведенные исследования показали, что Si-нанопорошок можно прессовать всухую (без связующих добавок) и получать компакты с пористостью ~50%, которые обладают достаточно высокой механической прочностью для проведения дальнейших операций по изготовлению анодов литий-ионных аккумуляторов. При отжиге спрессованных образцов в инертной атмосфере при высокой температуре 1100–1200°С происходит образование перемычек между наночастицами и увеличение размера зерен. Компромисс, который необходимо соблюсти, состоит в том, чтобы в результате спекания появилась связная структура Si-каркаса, обеспечивающая электронную проводимость, и одновременно сохранилась система открытых пор, доступных для электролита. Эксперименты показали, что наилучшие результаты демонстрирует образец, спекавшийся в течение 1 ч при Т = 1150°С, т.е. компромиссным условиям удовлетворяет материал с плотностью ρ = 1.60 г/см3, имеющий Si-зерна размером 100–500 нм и обладающий пористостью 32%. Изготовленный из него анод с толщиной Si-слоя 10 мкм демонстрирует наиболее стабильную работу, по крайней мере в течение 125 циклов в режиме С/5 при ограничении зарядной емкости величиной Qch = 1000 мА ч/г. Этот же образец показывает наиболее высокую емкость при разряде в режиме 1 С. Как и другие кремниевые аноды [15, 16], образцы, полученные спеканием Si-нанопорошка, не могут быстро заряжаться и разряжаться (циклироваться на высоких плотностях тока) из-за малой скорости твердофазной диффузии лития в кремнии.
Список литературы
Zhang, S., Zhao, K., Zhu, T., and Li, J., Electrochemomechanical degradation of high-capacity battery electrode materials, Prog. Mater. Sci., 2017, vol. 89, p. 479.
Du, F.-H., Wang, K.-X., and Chen, J.-Sh., Strategies to succeed in improving the lithium-ion storage properties of silicon nanomaterials, J. Mater. Chem. A, 2016, vol. 4, p. 32.
Ли, Г.В., Астрова, Е.В., Румянцев, А.M., Воронков, В.Б., Парфеньева, А.В., Толмачев, В.А., Кулова, Т.Л., Скундин, А.М. Кремниевые микроструктурированные аноды для литий-ионных аккумуляторов. Электрохимия. 2015. Т. 51 (10). С. 1020. [Li, G.V., Astrova, E.V., Rumyantsev, A.M., Voronkov, V.B., Parfen`eva, A.V., Tolmachev, V.A., Kulova, T.L., and Skundin, A.M., Microstructured silicon anodes for lithium-ion batteries, Russ. J. Electrochem., 2015, vol. 51 (10), p. 899.]
Астрова, Е.В., Ли, Г.В., Румянцев, А.M., Жданов В.В. Электрохимические характеристики наноструктурированных кремниевых анодов для литий-ионных аккумуляторов. ФТП. 2016. Т. 50 (2). С. 279. [Astrova, E.V., Li, G.V., Rumyantsev, A.M., and Zhdanov, V.V., Semiconductors, 2016, vol. 50 (2), p. 276.]
Li, G.V., Rumyantsev, A.M., Levitskii, V.S., Bere-gulin, E.V., Zhdanov, V.V., Terukov E.I., and Astrova, E.V., Application of silicon zig-zag wall arrays for anodes of Li-ion batteries, Semicond. Sci. Technol., 2016, vol. 31, p. 014008.
Föll, H., Carstensen, J., Ossei-Wusu, E., Cojocaru, A., Quiroga-Gonzalez, E., and Neumann, G., Optimized Cu-Contacted Si Nanowire Anodes for Li Ion Batteries Made in a Production Near Process, J. Electrochem. Soc., 2011, vol. 158 (5), p. A580.
Bellanger, P., Sow, A., Grau, M., Augusto, A., Serra, J.M., Kaminski, A., Dubois, S., and Straboni, A., New method of fabricating silicon wafer for the photovoltaic application based on sintering and recrystallization steps, J. Cryst. Growth, 2012, vol. 359, p. 92.
Buchwald, R., Wurzner, S., Moller, H.J., Siftja, A., Stokkan, G., Ovrelid, E., and Ulyashin, A., Microstructural characterization of Si wafers processed by multi-wire sawing of hot pressed silicon powder based ingots, Phys. Status. Solidi (a), 2015, vol. 212 (1), p. 25.
Moller, H.J. and Welsch, G., Sintering of Ultrafine Silicon Powder, J. Am. Ceramic. Soc., 1985, vol. 68 (6), p. 320.
Zhang, W.-J., Lithium insertion/extraction mechanism in alloy anodes for lithium-ion batteries, J. Power Sources, 2011, vol. 196, p. 877.
Can, C.K., Peng, H., Liu, G., McIlwrath, K., Zhang, X.F., Huggins, R.A., and Cui, Y., High-performance lithium battery anodes using silicon nanowires, Nature Nanotech., 2008, vol. 3, p. 31.
Ge, M., Rong, J., Fang, X., and Zhou, C., Porous Doped Silicon Nanowires for Lithium Ion Battery Anode with Long Cycle Life, Nano Lett., 2012, vol. 12, p. 2318.
Kovalenko, I., Zdurko, B., Magasinski, A., Hertzberg, B., Milicev, Z., Burtovyy, R., Luzinov, I., and Yushin, G., A Major Constituent of Brown Algae for Use in High-Capacity Li-Ion Batteries, Science, 2011, vol. 334, p. 75.
Кулова, Т.Л. Необратимая емкость электродов из тонкопленочного аморфного кремния. Электрохимия. 2008. Т. 44 (5). С. 569. [Kulova, T.L., Irreversible Capacity of the Amorphous Silicon Thin-film Electrodes, Russ. J. Electrochem., 2008, vol. 44 (5), p. 525.]
Астрова, Е.В., Румянцев, А.М., Ли, Г.В., Нащекин, А.В., Казанцев, Д.Ю., Бер, Б.Я., Жданов, В.В. Электрохимическое литирование кремния с разной кристаллографической ориентацией. ФТП. 2016. Т. 50 (7). С. 979. [Astrova, E.V., Rumyantsev, A.M., Li, G.V., Nashchekin, A.V., Kazantsev, D.Y., Ber, B.Y., and Zhdanov, V.V., Electrochemical lithiation of silicon with varied crystallographic orientation, Semiconductors, 2016, vol. 50 (7), p. 963.]
Преображенский, Н.Е., Астрова, Е.В., Павлов, С.И., Воронков, В.Б., Румянцев, А.М., Жданов, В.В. Аноды для литий-ионных аккумуляторов на основе p-Si с самоорганизующимися макропорами. ФТП. 2017. Т. 51 (1). С. 79. [Preobrazhenskiy, N.E., Astrova, E.V., Pavlov, S.I., Voronkov, V.B., Rumyan-tsev, A.M., and Zhdanov, V.V., Anodes for Li-ion batteries based on p-Si with self-organized macropores, Semiconductors, 2017, vol. 51 (1), p. 78.]
Дополнительные материалы отсутствуют.