Электрохимия, 2019, T. 55, № 4, стр. 414-423
Исследование коррозионного сопротивления нанокомпозитных покрытий Ni–P и Ni–P–C в растворе 3.5 вес. % NaCl
Р. Бадрнежад a, Х. Поурфарзад b, *, А. Р. Мадрам a, М. Р. Ганжали b, c
a Технологический Университет Малек-Аштар
15875-1774 Тегеран, Иран
b Тегеранский Университет
14155-6455 Тегеран, Иран
c Тегеранский Университет медицинских наук
14155-6455 Тегеран, Иран
* E-mail: h.pourfarzad2030@gmail.com
Поступила в редакцию 06.01.2017
После доработки 30.06.2017
Принята к публикации 16.10.2017
Аннотация
Цель работы – сравнить коррозионную устойчивость электроосажденных Ni–P- и Ni–P–C-нанокомпозитных покрытий в растворе 3.5 вес. % NaCl с тем, чтобы оценить влияние наночастиц углерода на коррозионное поведение этих покрытий, с применением методов потенциодинамических поляризационных и тафелевских кривых и спектроскопии электрохимического импеданса. Исследовано также влияние термообработки покрытий на их электрохимическое поведение. Полученные результаты показывают, что после термообработки на воздухе при 673 K коррозионная стойкость покрытия из Ni–P–C-нанокомпозита существенно улучшается по сравнению с Ni–P-покрытием. Такое поведение связано с внедрением наночастиц углерода в Ni–P-матрицу при электрохимическом in situ восстановлении L-лизина, которое сдвигает потенциал коррозии в сторону положительных значений, а значения плотности тока коррозии и емкости двойного слоя уменьшаются; сопротивление переноса заряда и ингибирование эффективностей увеличиваются, указывая на улучшение противокоррозионной стойкости материала в морской воде. Микроструктуру, фазовые переходы и химический состав приготовленных покрытий исследовали методами, соответственно, сканирующей электронной микроскопии, рентгеновской дифракции и элементного микроанализа.
ВВЕДЕНИЕ
Электроосажденные композитные покрытия на основе матрицы из сплава Ni–P, содержащие различные тонкие частицы неметаллов, керамики или полимерных соединений [1–10] привлекают большое внимание во многих отраслях промышленности вследствие их хороших механических, химических и электрокаталитических свойств, таких как износостойкость в сочетании с высокой коррозионной стойкостью и особенно высокой электрокаталитической активностью в реакции выделения водорода в хлор-щелочном производстве и электролизе воды [11–17], тем более в сравнении с никелевыми покрытиями.
Ni–P-покрытия с содержанием фосфора свыше 9 вес. % считаются аморфными и обладают прекрасными механическими свойствами и стойкостью по отношению к коррозии [18, 19]. Эти защитные пленки можно приготовить методом электроосаждения (или бестокового осаждения) на металлические или неметаллические подложки для предотвращения их разрушения со стороны агрессивной среды [20]. Электролитические Ni–P-системы предпочтительнее систем, полученных химическим (бестоковым) осаждением, потому что на путях электролитических процессов достижимы бóльшие скорости осаждения, повышенная устойчивость пленок в электролите, а в случае дисперсных покрытий – более точный контроль за внедрением частиц.
Ni–P-покрытия – это важные материалы в инженерии; они демонстрируют присущую им более высокую электрокаталитическую активность в реакции выделения водорода по сравнению с катализатором из “индивидуального” никеля, и к тому же они существенно дешевле, чем электрокатализаторы на основе благородных металлов, по причине синергического электронного эффекта, присущего сплавам [21–24].
Традиционный электролиз воды в щелочной среде, сопровождающийся выделением водорода, привлекает большое внимание вследствие его важной роли в электрохимической науке и технологии. Это – неразрушающий метод производства водорода, хотя и не самый дешевый. Поэтому производство дешевого водорода – это ключ к коммерциализации этой технологии [25–27]. С другой стороны, вода в природе существует главным образом, как морская вода (около 98%), а морская вода – это природный электролит. В отличие от большинства других водных ресурсов, морская вода в мировом океане имеет соленость около 3.5 вес. %. Таким образом, электролиз морской воды – это один из многообещающих способов производства водорода потому что, во-первых, сырье доступно на Земле в избытке и, во-вторых, морские волны – это источник мощности, использование которого in situ для производства водорода путем электролиза морской воды – это очень выгодный способ [28].
Электродные материалы с высокой каталитической активностью по отношению к реакции выделения водорода должны обладать следующими характеристиками: большая площадь активной поверхности, дешевизна, легкость использования и, в особенности, электрохимическая стабильность и высокая коррозионная устойчивость. В нашей предшествующей работе мы установили, что покрытия из нанокомпозита никель–фосфор–углерод (Ni–P–C), приготовленные путем соосаждения Ni–P с углеродом из l-лизина в качестве источника С, отличаются хорошей каталитической активностью по отношению к реакции выделения водорода, причем наблюдаемая активность вызвана, главным образом, собственной активности углерода, встроенного в Ni–P-матрицу [29].
Электрохимическая стабильность и высокая коррозионная устойчивость электродных материалов в течение долгого времени работы важны для их промышленного применения [14, 30]. По этой причине следует рассматривать их коррозионное поведение на определенном этапе разработки материалов для получения водорода электролизом воды.
В настоящей работе описана первая попытка изучить влияние эффекта внедрения наночастиц углерода методом электрохимического восстановления аминокислоты L-лизина на наноструктуру и антикоррозионные свойства свежеприготовленных электроосажденных Ni–P- и Ni‒P–C-матриц в течение долговременного пребывания в агрессивном хлоридном окружении морской воды (раствор 3.5 вес. % NaCl) с упором на влияние морфологии, химии, фазового состава поверхности и термообработки на коррозионную стойкость методами потенциодинамических поляризационных кривых и спектроскопии электрохимического импеданса.
ЭКСПЕРИМЕНТАЛЬНАЯ ЧАСТЬ
Материалы и покрытия
Композитные Ni–P- and Ni–P–C-покрытия были получены методом электроосаждения в гальваностатических условиях из ванн (A и B) и (A, B и C), соответственно, по двух- и трехстадийной процедуре. Медный электрод площадью 2.5 см2, впаянный в изоляционную трубку с термоусадкой, служил в качестве подложки, а платиновая пластинка (99.99% Pt) площадью больше 25 см2 – противоэлектродом. Перед электроосаждением медную подложку полировали наждачной бумагой (P 600, Siawats), промывали водой, погружали в раствор 1 : 1 HNO3, промывали водой и сразу же помещали в двухкамерную ячейку из стекла Pyrex® для электроосаждения. Состав ванн и условия электроосаждения для каждой стадии приведены в табл. 1. Все реактивы (Merck) имели квалификацию “ч. д. а.” и использовались без дополнительной очистки.
Таблица 1.
Состав ванн и условия электроосаждения
Ингредиенты ванн и условия электроосаждения | Ванна | ||
---|---|---|---|
A | B | C | |
Сульфат никеля, M | 1.14 | 1.14 | 1.14 |
Хлорид никеля, M | 0.19 | 0.19 | 0.19 |
Борная кислота, M | 0.49 | 0.49 | 0.49 |
Цитрат натрия, M | 0.12 | 0.12 | 0.12 |
Гипофосфит натрия, M | – | 0.14 | 0.14 |
L-лизин, M | – | – | 0.06 |
Ток электроосаждения, мA см–2 | 22 | 22 | 13 |
Время, мин | 30 | 45 | 45 |
Температура, K | 298 | 298 | 298 |
Полная толщина покрытия, мкм | 21–22 | 35–37 | 46–47 |
Морфологию и элементный состав поверхности сплавов исследовали методами сканирующей электронной микроскопии (SEM) и энергодисперсионного рентгеновского дифракционного микроанализа (EDX) (Philips-XL-30). Кристаллическую структуру сплавов исследовали методом рентгеновского дифракционного анализа (XRD) (Philips- X’Pert-MPD) с использованием CuKα-излучения с длиной волны 1.5418 Ǻ. для подтверждения фазовых переходов в Ni–P–C-нанокомпозитах применяли метод дифференциальной сканирующей калориметрии (Setaram-SETSYS Evolution DTA/DSC).
Электрохимические измерения проводили в открытой трехэлектродной ячейке с рабочим электродом из композитов Ni–P и Ni–P–C (из L‑лизина), противоэлектродом в виде Pt-пластинки (25 cm2, Pt 99.99%) и Ag/AgCl-электрода сравнения. Все измерения вели в растворе 3.5 вес. % NaCl, освобожденном от кислорода продуванием аргона (99.99%) при температуре 298 K. Перед каждым экспериментом ячейку промывали горячей водой, H2SO4, NaOH, многократно дважды перегнанной водой и, наконец, раствором 3.5 вес. % NaCl, после чего хранили в атмосфере аргона до использования.
Потенциодинамические поляризационные кривые снимали при скорости развертки потенциала 1 мВ/с в интервале потенциалов от (−625 мВ, Ag/AgCl) до (+240 мВ, Ag/AgCl) по отношению к Ecorr. Эти поляризационные кривые записывали через месяц после погружения в раствор.
Спектры электрохимического импеданса снимали в стационарных условиях. На постоянный потенциал накладывали переменнотоковый сигнал с амплитудой 10 мВ; частоту сканировали в широких пределах, от 100 кГц до 0.001 Гц, 30 точек на декаду в логарифмической шкале. При этом записывали импеданс и сдвиг по фазе тока относительно потенциала. Для того, чтобы обеспечить стационарные условия, необходимые для измерений импеданса, рабочие электроды поляризовали током 100 мA в течение 2 ч в растворе 3.5 вес. % NaCl при температуре 25°C.
Измерения проводили с помощью потенциостата/гальваностата EG&G2273A и анализатора частотного отклика 1025 EG&G, управляемых прибором GPIBIEEE-NI-488II. Накопление данных измерений тафелевских кривых и электрохимического импеданса проводили, используя программы, соответственно, Labviews subroutine и EG&GPowerSine; аппроксимацию результатов измерений импеданса – программы ZView и модифицированного нелинейного метода наименьших квадратов.
РЕЗУЛЬТАТЫ И ОБСУЖДЕНИЕ
Морфология и состав поверхности покрытий
SEM-микрофотографии поверхности композитных покрытий из свежеосажденного Ni–P (рис. 1а), свежеосажденного Ni–P–C (рис. 1б) и прогретого Ni–P–C (рис. 1в) демонстрируют глобулярные грибовидные образования, которые деформируются при нагревании покрытий до 673 K в атмосфере воздуха (рис. 1в). На SEM-микрофотографиях просматривается минимальный диаметр этих глобулярных грибовидных образований: 30 нм.
Рис. 1.
SEM-изображения композитных электродов: (а) свежеосажденного Ni83P17, (б) свежеосажденного Ni81P16C3 и (в) отожженного при 673 K на воздухе Ni81P16C3.
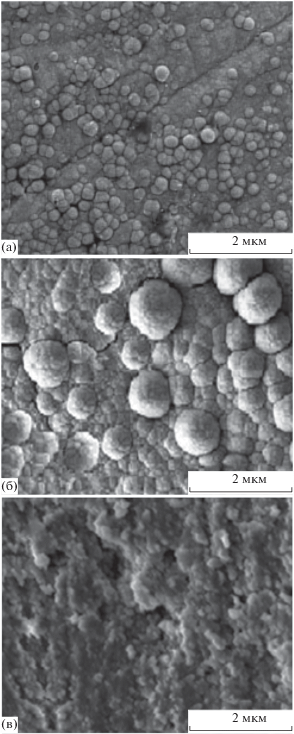
На рис. 2 представлен типичный энергодисперсионный рентгеновский (EDX) спектр, снятый на поверхности свежеосажденного Ni–P–C-покрытия. Аналогичные изображения были получены для прогретых покрытий; это означает, что углеродная составляющая композитов не изменяется в ходе термообработки. Химический состав верхних слоев покрытий, приготовленных в оптимизированных условиях, таков: Ni83P17 (свежеосажденное и прогретое) и Ni81P16C3 (свежеосажденное и прогретое). Эти результаты доказывают внедрение углерода в Ni–P-матрицу и подобны тем, которые описаны в работе [31], а также для электрода из Ni–P–C (графит).
Кристалллическая структура композитных покрытий
На рис. 3 приведены дифрактограммы свежеосажденнных (a) и прогретых (б) композитных покрытий. Видно, что эти свежеосажденные покрытия имеют аморфную структуру Ni–P–C; они демонстрируют единственный широкий пик с центром при 44.5°. После прогрева при 673 K в течение 1 ч они становятся кристаллическими в результате превращения Ni–P-матрицы в систему, содержащую в качестве преобладающей фазы при 673 K никель и фосфид никеля (Ni3P) [31]. Нам представляется, что частицы углерода диспергированы в фазах никеля и фосфида никеля, и образуется нанокомпозитное покрытие Ni81P16C3. Рентгеновские дифрактограммы, полученные в настоящей работе для композитных покрытий Ni–P–C, приготовленных по “L-лизиновому” методу, близко напоминают покрытия, приготовленные по “графитовому” методу путем бестокового осаждения [31], подтверждая этим образование композитных покрытий Ni–P–C в настоящей работе. В качестве приближения для расчета среднего размера зерна использовали уравнение Шеррера. Для Ni83P17 и Ni81P16C3 средний размер зерна составил, соответственно, около 78 и 37 нм. Ясно видно, что добавление углерода в матрицу Ni–P уменьшает этот средний размер зерна. Подобное поведение было описано в работах [32, 33].
Рис. 3.
Рентгеновские дифрактограммы свежеосажденнных (a) и прогретых при 673 K на воздухе (б) Ni81P16C3-электродов, снятые с использованием CuKα-излучения (длина волны 1.5418 Ǻ).
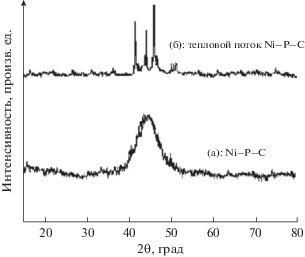
Для окончательного прояснения фазовых изменений в нанокомпозитах Ni–P–C, произошедших в результате термообработки при температуре 673 K мы использовали метод дифференциальной сканирующей калориметрии. Как видно на рис. 4, в исследуемой области температур имеется один хорошо идентифицируемый экзотермический пик при начальной температуре 331°C, который имеет отношение к переходу структуры от аморфной к кристаллической. Подобное же поведение было описано для аморфных сплавов Ni–P [31]. Следует отметить, что при температурах ниже 200°C не происходит никаких специфических изменений, поэтому они и не показаны на рис. 4.
КИНЕТИЧЕСКИЕ ИССЛЕДОВАНИЯ
Потенциодинамические поляризационные исследования
Потенциодинамическое поляризационное поведение свежеосажденных покрытий из сплавов Ni–P и Ni–P–C в освобожденном от кислорода растворе 3.5 вес. % NaCl показано на рис. 5. Видно, что катодная реакция на этих поляризационных кривых – это выделение водорода; анодная же поляризационная кривая – это наиболее важная характеристика, относящаяся к коррозионной стойкости материалов [34].
Рис. 5.
Стационарные тафелевские поляризационные кривые, снятые на исследуемых покрытиях в растворе 3.5 вес. % NaCl при 298 K.
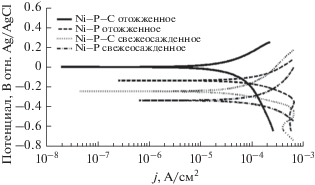
Что касается коррозии, то количественную информацию о коррозионных токах и коррозионных потенциалах можно извлечь из наклона кривых; кроме того, поляризационное сопротивление можно хорошо определить, пользуясь уравнением Штерна–Гири. С другой стороны, вблизи потенциала коррозии при разомкнутой цепи можно ожидать, что уравнение Штерна–Гири вполне применимо [35]. Оно неявно предполагает, что и катодный, и анодный процессы вполне аддитивны, и оба они подчиняются закону Тафеля. Тогда можно выразить полную плотность тока следующим уравнением:
(1)
$\begin{gathered} I = {{I}_{{{\text{corr}}}}} \times \\ \times \,\,\left\{ {\exp \left[ {\beta a\left( {E - {{E}_{{{\text{corr}}}}}} \right)} \right] - \exp \left[ {\beta c\left( {E - {{E}_{{{\text{corr}}}}}} \right)} \right]} \right\}. \\ \end{gathered} $Применив к этому уравнению приближение малого сигнала, мы получили следующее уравнение Штерна–Гири [36]:
(2)
${{I}_{{{\text{corr}}}}} = \frac{1}{{2.303{{R}_{{\text{p}}}}}}\left( {\frac{{{{\beta }_{{\text{a}}}}{{\beta }_{{\text{c}}}}}}{{{{\beta }_{{\text{a}}}} + {{\beta }_{{\text{c}}}}}}} \right).$Потенциал коррозии (Ecorr), плотность тока коррозии (Icorr) и сопротивление коррозии (Rp), определенные из потенциодинамических поляризационных кривых, сведены в табл. 2.
Таблица 2.
Параметры коррозии покрытий, полученные из стационарных тафелевских графиков
Тип покрытия | Ecorr, мВ | Icorr, мA см−2 | Rp, Ом см2 | Электрохимическая скорость коррозии CR (мдюйм/год) ×106 | IE, % |
---|---|---|---|---|---|
Ni–P (свежеосажденное) | –342 | 0.91 | 202.01 | 16.60 | 59.27 |
Ni–P–C (свежеосажденное) | –239 | 0.49 | 307.92 | 9.02 | 77.85 |
Ni–P (термообработанное) | –134 | 0.16 | 632.79 | 3.03 | 92.56 |
Ni–P–C (термообработанное) | +3.32 | 0.04 | 7550.98 | 0.79 | 98.04 |
Скорость коррозии (CR) была вычислена по закону Фарадея [37], как:
(3)
${\text{CR}}\left( {{\text{м д ю й м /г о д }}} \right) = \frac{{0.13{{I}_{{{\text{corr}}}}}({\text{Eq}}{\text{.}}\,\,{\text{wt}}{\text{.}})}}{d},$Плотность тока коррозии (Icorr) была использована для вычисления эффективности ингибирования коррозии (IE, %) покрытий, согласно следующему соотношению:
(4)
${\text{IE}}\left( \% \right) = \left( {\left( {{\text{1}} - \frac{{{{I}_{{{\text{corr}}}}}{\text{(i)}}}}{{{{I}_{{{\text{corr}}}}}{\text{(o)}}}}} \right)\quad\,\, \times {\text{1}}00} \right),$Сравнение электрохимических параметров (табл. 2) свежеосажденных композитных покрытий из Ni–P и Ni–P–C показало, что при внедрении углерода в матрицу Ecorr сдвигается в сторону более положительных значений, значение Icorr уменьшается, а Rp возрастает, что указывает на хорошие защитные (по отношению к коррозии) свойства покрытий. Другими словами, эти Ni–P–C-нанокомпозиты обладают прекрасной противокоррозионной устойчивостью по отношению к морской воде, помогают предотвратить разрастание коррозионного питтинга и дают вклад в ускорение процесса пассивации металлических матриц.
На рис. 5 даны кривые зависимости lg(i)–E для осадков Ni–P и Ni–P–C, подвергнутых термообработке на воздухе при 673 K в течение 1 ч. Потенциал коррозии Ecorr термообработанных осадков Ni–P и Ni–P–C сдвинут в сторону положительных значений, а величина Icorr, отражающая скорость коррозии прогретых покрытий, значительно уменьшилась по сравнению со свежеосажденными покрытиями. Поэтому от термообработанных осадков Ni–P и Ni–P–C следует ожидать высокой коррозионной стойкости, что позволит существенно расширить область их применения.
Вышеприведенные результаты можно объяснить следующими причинами. Во-первых, при температуре 673 K происходит фазовый переход осадка Ni–P от аморфной твердой фазы к кристаллической структуре, т.е. кристаллизация осадка Ni–P, пересыщенного по P, и, следовательно, образование кристаллических фаз никеля и фосфида никеля с заметной термодинамической стабильностью. Во-вторых, обработка отжигом способствует движению поверхностных атомов Ni и P и, как следствие, некоторое количество свободных атомов никеля и фосфора восстанавливается, что приводит к образованию плотных, гладких и гомогенных осадков, что видно и по SEM-изображениям. В-третьих, потенциал коррозии отожженных осадков сдвинут в сторону положительных значений из-за образования оксида Ni на поверхности осадка, поскольку после термообработки поверхность P оказалась заменена кислородными соединениями из воздуха. Действительно, основная цель термообработки на воздухе – это образование однородной пленки, состоящей из Ni–P и NiO на поверхности осадка и усиливающей противокоррозионное действие осадков Ni–P [38].
Исследования методом спектроскопии электрохимического импеданса
Спектроскопия электрохимического импеданса – это мощный не разрушающий метод, позволяющий за короткое время получить информацию относительно вклада всех резистивных, емкостных и индуктивных элементов в рамках подхода, использующего подходящие эквивалентные схемы (рис. 6). Следовательно, этот метод позволяет оценить несколько электрохимических параметров и обнаружить процессы межфазной релаксации, такие как коррозионные явления и адсорбционные эффекты [39, 40].
Рис. 6.
Модельные эквивалентные электрические схемы Рэндлса, использованные при анализе годографов импеданса: a) эквивалентная схема для отожженного композитного Ni–P–C-покрытия, б) эквивалентная схема для отожженных Ni–P- и Ni–P–C-покрытий. R1 – сопротивление раствора, R2 – сопротивление покрытия, R3 – сопротивление коррозии (сопротивление переноса заряда Rct), CPEdl – элемент постоянной фазы.
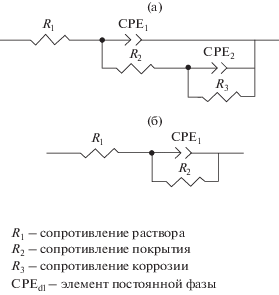
На рис. 7 даны годографы, полученные из измерений импеданса композитных покрытий из Ni–P и Ni–P–C в растворе 3.5 вес. % NaCl при соответствующих им значениях Eсorr. Ясно видно, что полученные во всем исследованном диапазоне частот графики для Ni–P-покрытий и для свежеосажденных Ni–P–C-покрытий содержат лишь одну полуокружность – одну емкостную петлю (что предполагает активационный механизм коррозионного процесса). В то же время термообработанное Ni–P–C-покрытие характеризуется наличием на годографе в исследованном диапазоне частот двух полуокружностей различного диаметра, что указывает на наличие двух временных констант.
Диаметр второй полуокружности дает коррозионное сопротивление покрытий. Высокочастотная полуокружность относится к реакциям в объеме, а следующая, низкочастотная – к границе раздела покрытие/раствор.
Из годографов также следует, что термообработанное композитное покрытие из Ni–P–C демонстрирует полуокружность самого большого радиуса по сравнению с другими покрытиями, показывая этим, что у термообработанного Ni‒P–C-композита более высокое сопротивление коррозии, чем у других покрытий [41, 42], в том числе у исходного Ni–P-покрытия [43]. Причина в том, что отожженный Ni–P–C не содержит ни фазовых границ, ни дефектов кристаллической структуры, таких как дефекты упаковки и сегрегация, а наночастицы углерода способны заполнить некоторые из пор в покрытии и предотвратить дальнейшую диффузию агрессивных веществ вдоль границы раздела.
Наличие на графиках Боде для Ni–P-покрытия и свежеосажденного Ni–P–C-покрытия (рис. 8, 9) единственной точки перегиба и только одного значения угла сдвига фаз указывает на то, что процесс характеризуется только одной временнóй константой. Этот результат согласуется с данными других авторов [44–46]. Кроме того, график Боде, полученный для отожженного композитного Ni–P–C-покрытия содержит две точки перегиба и два пика (на частотной зависимости фазового угла) в исследованной области частот. Это ясно говорит о наличии двух постоянных времени.
На рис. 9 видно, что рост абсолютного значения импеданса при низких частотах на графике Боде подтверждает более высокую степень коррозионной защиты в результате внедрения наночастиц углерода в покрытие.
В результате аппроксимирования экспериментальных данных с помощью предложенных моделей с одним или двумя элементами постоянной фазы (CPE) можно получить следующие параметры: Rp, Rs, T и $\phi ,$ где T – емкостной параметр, а $\phi $ – безразмерный дисперсионный параметр, относящийся к модели СРЕ (значение $\phi $ меняется между нулем и единицей; оно равно единице для совершенно гладкой поверхности электрода, например, при $\phi $ = 1, T = Cdl), ${{Z}_{{{\text{CPE}}}}} = {{{{\text{1}} \mathord{\left/ {\vphantom {{\text{1}} {[\left( {j\omega } \right)}}} \right. \kern-0em} {[\left( {j\omega } \right)}}}^{\phi }}T],$ где ω – круговая частота переменного напряжения. Емкость двойного слоя Cdl вычисляли по формуле [47]:
(5)
$T = C_{{{\text{dl}}}}^{\phi }{{\left( {\frac{1}{{{{R}_{{\text{s}}}}}} + \frac{1}{{{{R}_{{\text{p}}}}}}} \right)}^{{1\, - \,\phi }}}.$Значения Rct и Cdl для композитных покрытий приведены в табл. 3. Значения Rct для композитных покрытий из Ni–P (свежеосажденного), Ni‒P–C (свежеосажденного), Ni–P (термообработанного) и Ni–P–C (термообработанного) равняются, соответственно, 226, 482, 738.8 и 9655 Ом см2, а соответствующие значения Cdl, соответственно, таковы: (0.54), (0.36), (0.15) и (0.01) мФ см−2. Установлено, что большие величины Rct и низкие значения Cdl предполагают более эффективную противокоррозионную защиту, которую обеспечивает покрытие [48, 49].
Таблица 3.
Параметры, полученные из спектроскопии электрохимического импеданса
Тип покрытия | Rs, Ом см2 а | Rct, Ом см2 б | Cdl, мФ/см2в | Rfг |
---|---|---|---|---|
Ni–P (свежеосажденное) | 7.75 | 226 | 0.54 | 26.78 |
Ni–P–C (свежеосажденное) | 8.06 | 482 | 0.36 | 18.24 |
Ni–P (термообработанное) | 9.97 | 739 | 0.15 | 7.33 |
Ni–P–C (термообработанное) | 10.08 | 9655 | 0.01 | 0.54 |
Отношение величины Cdl к емкости идеально гладкой поверхности электролитического никеля (20 мкФ см−2 [47]) дает величину фактора шероховатости поверхности Rf. Значение фактора шероховатости для термообработанного Ni–P–C-покрытия приблизительно в 40 раз ниже, чем для свежеосажденного Ni–P–C-покрытия, указывая на более эффективную блокировку коррозионного процесса. Еще одно свидетельство этому – более высокое значение поляризационного сопротивления Rp для отожженных покрытий, чем для свежеосажденных (см. табл. 2).
Результаты, полученные методом спектроскопии электрохимического импеданса, находятся в хорошем согласии с данными метода потенциодинамических поляризационных кривых, снятых в растворе 3.5 вес. % NaCl; они подтверждают, что композитные Ni–P–C-покрытия, используемые в качестве катализатора реакции выделения водорода, оказывают еще и существенное противокоррозионное действие.
ЗАКЛЮЧЕНИЕ
Суммируя полученные в настоящей работе результаты, можно сделать следующие выводы:
1. Успешно разработано включение частиц углерода в матрицу бинарного Ni–P-сплава путем восстановления L-лизина в ходе электроосаждения покрытия из соответствующей ванны. Частицы углерода хорошо распределены в никель-фосфорном осадке и покрывают его поверхность. Соответствующие коррозионные параметры свидетельствует о том, что внедрение частиц углерода из аминокислоты L-лизина в качестве источника углерода в никель-фосфорное покрытие существенно повышает его коррозионное сопротивление. Кроме того, частицы углерода, равномерно распределенные в никель-фосфорном покрытии, повышают потенциал коррозии образующегося нанокомпозитного покрытия, сдвигая его к более положительным значениям, ограничивают местную коррозию, в результате чего коррозия в основном протекает равномерно по поверхности.
2. Электрохимические измерения показали, что “лизиновые” Ni–P–CL-покрытия после термообработки лучше сопротивляются коррозии в растворе 3.5 вес. % NaCl, чем свежеосажденные покрытия. У покрытий, подвергнутых термообработке при температуре 673 K наблюдаются более положительное значение потенциала коррозии, меньшая величина тока коррозии и фактора шероховатости поверхности, а также более высокое значение поляризационного сопротивления. Причина этого – присутствие кристаллических фаз никеля и фосфида никеля, отличающихся примечательной термодинамической стабильностью. Более того, параметры, определенные методом спектроскопии электрохимического импеданса, дают возможность оценить сопротивление покрытий коррозии и подтверждают результаты, полученные из потенциодинамических измерений.
Список литературы
Berkh, O., Bodnevas, A., and Zahavi, J., Electrodeposited Ni–P–SiC composite coatings, Plat. Surf. Finish, 1995, vol. 82, p. 62.
Sharma, S.B., Agarwala, R.C., Agarwala, V., and Ray, S., Dry sliding wear and friction behavior of Ni–P–ZRO2–Al2O3 composite electroless coatings on aluminum, Mater. Manuf. Processes, 2002, vol. 17, p. 637.
Aghaie, E., Najafi, A., Maleki Ghaleh, H., and Mohebi, H., Effect of SiC concentration in electrolyte on Ni–SiC composite coating properties, Surf. Eng., 2013, vol. 29, p. 177.
Chen, W., Gao, W., and He, Y., A novel electroless plating of Ni–P–TiO2 nano-composite coatings, Surf. Coat. Technol., 2010, vol. 204, p. 2493.
Liu, B., Liu, L.R., and Liu, X.J., Effects of carbon nanotubes on hardness and internal stress in Ni–P coatings, Surf. Eng., 2013, vol. 29, p. 507.
Alirezaei, S., Monirvaghefi, S.M., Salehi, M., and Saatchi, A., Wear behavior of Ni–P and Ni–P–Al2O3 electroless coatings, Wear, 2007, vol. 262, p. 978.
Farzaneh, A., Mohammadi, M., Ehteshamzadeh, M., and Mohammadi, F., Electrochemical and structural properties of electroless Ni–P–SiC nanocomposite coatings, Appl. Surf. Sci., 2013, vol. 276, p. 697.
Sharma, A. and Singh, A.K., Electroless Ni–P–PTFe–Al2O3 dispersion nanocomposite coating for corrosion and wear resistance, J. Mater. Eng. Perform., 2014, vol. 23, p. 142.
Liu, J., Wang, Sh., Li, P., Feng, M., and Yang, X., A modified dip-coating method to prepare BN coating on SiC fiber by introducing the sol–gel process, Surf. Coat. Technol., 2016, vol. 286, p. 57.
Rossi, S., Chini, F., Straffelini, G., Bonora, P.L., Moschini, R., and Stampali, A., Corrosion protection properties of electroless Nickel/PTFE, Phosphate/MoS2 and Bronze/PTFE coatings applied to improve the wear resistance of carbon steel, Surf. Coat. Technol., 2003, vol. 173, p. 235.
Paseka, I., Influence of hydrogen absorption in amorphous Ni–P electrodes on double layer capacitance and charge transfer coefficient of hydrogen evolution reaction, Electrochim. Acta, 1999, vol. 44, p. 4551.
Burchardt, T., The hydrogen evolution reaction on NiPx alloys, Int. J. Hydrogen Energy, 2000, vol. 25, p. 627.
Burchardt, T., Hydrogen evolution on NiPx alloys: the influence of sorbed hydrogen, Int. J. Hydrogen Energy, 2001, vol. 26, p. 1193.
Popczyk, M., Budniok, A., and Lasia, A., Electrochemical properties of Ni–P electrode materials modified with nickel oxide and metallic cobalt powders, Int. J. Hydrogen Energy, 2005, vol. 30, p. 265.
Burchardt, T., Hansen, V., and Valand, T., Microstructure catalytic activity towards the hydrogen evolution reaction of electrodeposited NiPx alloys, Electrochim. Acta, 2001, vol. 46, p. 2761.
Krolikowski, A. and Wiecko, A., Impedance studies of hydrogen evolution on Ni–P alloys, Electrochim. Acta, 2002, vol. 47, p. 2065.
Shibli, S.M.A. and Dilimon, V.S., Effect of phosphorous content and TiO2- reinforcement on Ni–P electroless plates for hydrogen evolution reaction, Int. J. Hydrogen Energy, 2007, vol. 32, p. 1694.
Bredael, E., Blanpain, B., Celis, J.P., and Roos, J.R., On the amorphous and crystallinestate of electrodeposited nickel-phosphorous coatings, J. Electrochem. Soc, 1994, vol. 141, p. 294.
Daly, B.P. and Barry, F.J., Electrochemical nickel-phosphorous alloy formation, Int. Mater. Rev., 2003, vol. 48, p. 326.
Lee, H.B., Wuu, D.S., Lee, C.Y., and Lin, C.S., Study of the corrosion behavior of nanocrystalline Ni–P electrodeposited coating, Metall. Mater. Trans. A, 2010, vol. 41, p. 450.
Cordeiro, G., Mattos, O.R., Barcia, O.E., Beaunier, L., Deslouis, C., and Tribollet, B., Anodic dissolution of nickel in concentrated sulfuric acidic solutions, J. Appl. Electrochem., 1996, vol. 26, p. 1083.
Barbosa, M.R., Bastos, J.A., Garca, J.J., and Vicente, F., Chloride role in the surface of nickel electrode, Electrochim. Acta, 1998, vol. 44, p. 957.
Seyeux, A., Maurice, V., Klein, L.H., and Marcus, P., initiation of localized corrosion at the nanoscale by competitive dissolution and passivation of nickel surfaces, Electrochim. Acta, 2008, vol. 54, p. 540.
Sun, F., Meng, G., Zhang, T., Shao, Y., Wang, F., and Dong, C., Electrochemical corrosion behavior of nickel coating with high density nano-scale twins (NT) in solution with Cl−, Electrochim. Acta, 2009, vol. 54, p. 1578.
Selembo, P.A., Merrill, M.D., and Logan, B.E., The use of stainless steel and nickel alloys as low-cost cathodes in microbial electrolysis cells, J. Power Sources, 2009, vol. 190, p. 271.
Grant, J.C., Nickel.Cadmium Battery Application Engineering Handbook, Third ed., Gainesville: General Electric Company, 1975.
Ahn, K.H., Song. K.G., Cha. H.Y., and Yeom. I.T., Removal of ions in nickel electroplating rinse water using low-pressure nanofiltration, J. Desal., 1999, vol. 122, p. 77.
Mathu, J., Agarwal, N., Swaroop, R., and Shah, N., Economics of producing hydrogen as transportation fuel using offshore wind energy systems, Energy Policy, 2008, vol. 36, p. 1212.
Shervedani, R.K. and Madram, A.R, Electrocatalytic activities of nanocomposite Ni81P16C3 electrode for hydrogen evolution reaction in alkaline solution by electrochemical impedance spectroscopy, Int. J. Hydrogen Energy, 2008, vol. 33, p. 2468.
Madram, A.R.,Pourfarzad, H., and Zare, H.R., Study of the corrosion behavior of electrodeposited Ni–P and Ni–P–C nanocomposite coatings in 1 M NaOH, Electrochim. Acta, 2012, vol. 85, p. 263.
Wu, Y.T., Lei, L., Shen, B., and Hu, W.B., Investigation in electroless Ni–P–Cg(graphite)–SiC composite coating, Surf. Coat. Technol., 2006, vol. 201, p. 441.
Meguro, S., Sasaki, T., Katagiri, H., Habazaki, H., and Kawashima, A., Electrodeposited Ni–Fe–C Cathodes for Hydrogen Evolution Articles, J. Electrochem Soc., 2000, vol. 147, p. 3003.
Hashimoto, K., Sasaki, T., Meguro, S., and Asami, K., Nanocrystalline electrodeposited Ni–Mo–C cathodes for hydrogen production, J. Mater. Sci. Eng., 2004, vol. 375, p. 942.
Dong, H., Sun, Y., and Bell, T., Enhanced corrosion resistance of duplex coatings, Surf. Coat. Technol., 1997, vol. 90, p. 91.
Shervedani, RK. and Lasia, A., Study of the Hydrogen Evolution Reaction on Ni–Mo–P Electrodes in Alkaline Solutions, J. Electrochem. Soc., 1998, vol. 145, p. 2219.
Stern, M. and Geary, A., The Mechanism of Passivating – Type Inhibitors TECHNICAL PAPERS, J. Electrochem. Soc., 1958, vol. 105, p. 638.
Mishra, R. and Balasubramaniam, R., Effect of nanocrystalline grain size on the electrochemical and corrosion behavior of nickel, J. Corros. Sci., 2004, vol. 46, p. 3019.
Magdalena, P., Antoni, B., and Eugeniusz, Ł., Structure and corrosion resistance of nickel coatings containing tungsten and silicon powders, J. Mater. Character., 2007, vol. 58, p. 371.
Priyantha, N., Jayaweera, P., Macdonald, D.D., and Sun, A., An electrochemical impedance study of Alloy 22 in NaCl brine at elevated temperature. I. Corrosion behavior, J. Electroanal Chem., 2004, vol. 572, p. 409.
Macdonald, DD., Sun, A., Priyantha, N., and Jayaweera, P., An electrochemical impedance study of Alloy-22 in NaCl brine at elevated temperature: II. Reaction mechanism analysis, J. Electroanal. Chem., 2004, vol. 572, p. 421.
Li, Q., Yang, Q.X., Zhang, L., Wang, J., and Chen, B., Corrosion resistance and mechanical properties of pulse electrodeposited Ni–TiO2 composite coating for sintered NdFeB magnet, J. Alloys Compd., 2009, vol. 482, p. 339.
Szczygieł, B. and Kołodziej, M., Composite Ni/Al2O3 coatings and their corrosion resistance, Electrochim. Acta, 2005, vol. 50, p. 4188.
Lian, J.S., Li, G.Y., Niu, L.Y., Gu, C.D., Jiang, Z.H., and Jiang, Q., Electroless Ni–P deposition plus zinc phosphate coating on AZ91D magnesium alloy, J. Surf. Coat. Technol., 2006, vol. 200, p. 5956.
Balaraju, J.N., Ezhil Selvi, V., Willium Grips, V.K., and Rajam, K.S., Electrochemical studies on electroless ternary and quaternary Ni–P based alloys, Electrochim. Acta, 2006, vol. 52, p. 1064.
Abdel Aal, A., Hard and corrosion resistant nanocomposite coating for Al alloy, J. Mater. Sci. Eng., 2008, vol. 474, p. 181.
Hu, C.C. and Bai, A., Effects of annealing temperatures on the physicochemical properties of nickel–phosphorus deposits, J. Mater. Chem. Phys., 2003, vol. 79, p. 49.
Shervedani, R.K., Lasia, A., Evaluation of the surface roughness of microporous Ni–Zn–P electrodes by in situ methods, J. Appl. Electrochem., 1999, vol. 29, p. 979.
Contreras, A., Leon, C., Jimenez, O., Sosa, E., and Perez, R., Electrochemical behavior and microstructural characterization of 1026 Ni–B coated steel, J. Appl. Surf. Sci., 2006, vol. 253, p. 592.
Shervedani, R.K., Mehrjardi, A.H., and Zamiri, N., A novel method for glucose determination based on electrochemical impedance spectroscopy using glucose oxidase self-assembled biosensor, J. Bioelectrochem., 2006, vol. 69, p. 201.
Дополнительные материалы отсутствуют.