Электрохимия, 2019, T. 55, № 6, стр. 741-749
Получение твердотельных пленочных батарей на основе RbAg4I5 методом аэрозольного осаждения
Н. А. Овсянников a, b, *, Г. В. Нечаев c, Д. В. Новиков c, А. А. Бельмесов a, **, В. Е. Пуха a
a Центр компетенции НТИ при Институте проблем химической физики РАН
142432 Московская обл., Черноголовка, просп. академика Семенова, 1, Россия
b Московский государственный университет им. М.В. Ломоносова,
Факультет фундаментальной физико-химической инженерии
119992 Москва, ГСП-1, Ленинские горы, д. 1, стр. 51, Россия
c АО “ГК ИнЭнерджи”
115201 Москва, 2-й Котляковский пер., д. 18, Россия
* E-mail: nico.ovsyannikov@gmail.com
** E-mail: belmesovaa@mail.ru
Поступила в редакцию 08.10.2018
После доработки 17.12.2018
Принята к публикации 22.01.2019
Аннотация
Разработана технология получения тонкопленочной твердотельной батареи на основе электрохимической системы серебро–иод методом аэрозольного осаждения в вакууме. Функциональные слои батареи исследованы методами оптической и сканирующей электронной микроскопии. Вольт-амперные характеристики полученного химического источника тока показали, что максимальный ток разряда превышает 3 мА/см2, что достаточно для электропитания большинства вживляемых электронных устройств медицинского назначения.
ВВЕДЕНИЕ
В современной медицине используется множество электронных устройств с малым током потребления (кардио- и нейростимуляторы, дефибрилляторы – потребление 10–60 мкВт [1]), для которых необходимы имплантируемые химические источники тока (ХИТ) с большим сроком службы (порядка нескольких десятков лет) и малыми размерами [2]. Таким эксплуатационным условиям удовлетворяют твердофазные системы в тонкопленочном исполнении с твердым электролитом Ag4RbI5 и композитными материалами на его основе. Данный электролит имеет рекордно высокую ионную (0.25 См/см при комнатной температуре) и низкую электронную (порядка 10‒9 См/см) проводимость, и вследствие этого ХИТ на его основе имеют незначительное внутреннее сопротивление и низкий ток саморазряда. Более того, в системах на основе Ag4RbI5 возможна перезарядка ХИТ, что может существенно увеличить срок службы устройства.
К недостаткам Ag4RbI5 следует отнести его низкую термическую стойкость (соединение плавится с разложением при температуре ~503 K, [3]) а также нестабильность в присутствии следов влаги и низкую стойкость к излучению, включая видимый свет. Вследствие перечисленных причин получение однофазного материала является весьма сложной задачей. Кроме того, это соединение неустойчиво в контакте с металлическим серебром [4]. Учитывая все эти особенности, можно заключить, что традиционные методы получения тонких пленок (например, магнетронное напыление) малопригодны для изготовления пленок из этого твердого электролита. Так, авторами работы [4] были получены пленки из Ag4RbI5 с проводимостью примерно на порядок ниже, чем у монолитных образцов. Снижение проводимости пленок авторы связывают с частичным разложением электролита в ходе напыления, что было подтверждено данными рентгенофазового (РФА) и термоанализа.
В настоящей работе для получения тонких слоев электролита и электродных слоев источника тока (катодного и анодного) успешно применен новый метод “холодного” аэрозольного осаждения в вакууме (АОВ) из сверхзвуковой струи аэрозоля твердых частиц. Этот метод разработан в конце 90-х годов прошлого века в Японии [5], и в его основе лежит процесс “ударной консолидации при комнатной температуре” (room temperature impact consolidation – RTIC) [6]. После того, как была показана универсальная применимость АОВ для получения керамических покрытий и получены покрытия из ряда тугоплавких соединений (Аl2O3, BaTiO3, TiO2, ZrO2 [6]), начался экспоненциальный рост количества публикаций по данной тематике. В настоящее время методом АОВ получены электролиты и электроды для топливных элементов и литиевых батарей, биосовместимые покрытия на основе гидроксиапатита для костных имплантатов, а также термобарьерные и трибологические покрытия на основе ZrO2, MAX-фаз и др. [7–12]. Была показана возможность применения метода в сфере аддитивных технологий для получения сложных 2D- и 3D-структур [13]. АОВ позволяет получать композиты при совместном осаждении керамики и металлических частиц [14], керамики и органических соединений [15, 16]. Так, композиты, полученные этим методом из керамики LSM-YSZ и поливинилиденфторида, использованы для производства пористых систем, которые могут служить катодом топливного элемента [8]. Покрытия, получаемые аэрозольным осаждением, обладают высокой адгезией к подложке, единой структурой и сплошностью, газонепроницаемы и не нуждаются в дополнительном отжиге для спекания частиц. Микротвердость керамических покрытий имеет величину, характерную для спеченной под давлением из исходного порошка керамики. Особый низкотемпературный механизм консолидации, реализуемый в этом методе, позволяет также осаждать покрытия из твердых легколетучих или легко разлагаемых соединений. Возможности и особенности АОВ, а также принципы его реализации подробно описаны в недавно вышедших обзорах [7, 17]
Для формирования функциональных слоев ХИТ на основе Ag4RbI5 наиболее интересны возможности АОВ, связанные с формированием композитных слоев из веществ с существенным различием механических, физических и химических свойств. Метод позволяет наносить такие композиты из смеси нескольких порошков [7]. Соотношение керамических, металлических [14] и полимерных компонентов [15, 16] в данных смесях может варьироваться в значительной степени. Подобные композиты являются необходимыми при конструировании пленочных электродов ХИТ, так как для снижения электросопротивления твердофазной границы электрод/электролит и достижения высоких токов разряда электродный материал представляет собой композит на базе металла и электролита с полимерной составляющей.
МЕТОДИКА ЭКСПЕРИМЕНТА
Установка для напыления покрытий методом аэрозольного осаждения, была предоставлена компанией “ИнЭнерджи” (Россия). Установка оснащена высокопроизводительной откачной группой на базе вакуумного двухроторного агрегата АВД 150/25 со скоростью откачки 150 л/с в рабочем диапазоне давлений (50–600 Па).
Схема установки представлена на рис. 1. Покрытия осаждались в вакуумной камере объемом 0.3 м3, в которой с помощью сопла Лаваля аксиальной симметрии формировалась сверхзвуковая струя аэрозоля твердых частиц. Во время осаждения покрытия в камере поддерживалось давление порядка 200 Па. При взаимодействии ускоренных частиц с поверхностью подложки на ней формировалось твердое компактное покрытие. В качестве газа-носителя использовался азот. Генерация газопорошковой смеси производилась в аэрозольной камере с вихревыми потоками газа-носителя при избыточном давлении 0.05 МПа. Аэрозольная камера устанавливалась на виброплатформу с круговыми вибрациями (шейкер Vibramax 100, Heidolfph, Германия). Во всех экспериментах устанавливалась скорость круговой вибрации ~600 об./мин, которая была оптимальной для встряхивания порошка и образования аэрозоля.
Твердый электролит Ag4RbI5 был синтезирован механохимическим методом аналогично методике, описанной в [18]. Исходными веществами служили иодид рубидия RbI квалификации “х. ч.” и иодид серебра AgI, синтезированный из нитрата серебра (“х. ч.”) и иодида калия (“х. ч.”) путем обменной реакции. Синтез проводился в размольном стакане из диоксида циркония. Поскольку Ag4RbI5 в присутствии следов влаги неустойчив, то исходные компоненты перед синтезом сушили в вакууме и сразу переносили в перчаточный бокс с атмосферой сухого аргона, в котором и проводились дальнейшие операции. Приготовление стехиометрической смеси, ее механообработка и извлечение целевого продукта проводилось в инертной атмосфере при защитном освещении (красный свет). На рентгенограмме полученного соединения присутствовали только линии фазы Ag4RbI5 (рис. 2). Кроме того, однофазность материала была подтверждена методом дифференциальной сканирующей калориметрии (ДСК): на кривых ДСК полученного электролита отсутствовали пики при 147 и 201°С, относящиеся к фазовому переходу в AgI и плавлению эвтектики Ag2RbI3 ⋅ Ag4RbI5 соответственно, а температура плавления составила 237°С, что хорошо согласуется с литературными данными [19]. Ионная проводимость полученного материала составила 0.25 См/см, электронная составляющая проводимости – 2 × 10–9 См/см.
Измельчение порошков и приготовление электродных смесей для последующего нанесения методом АОВ также производилось c помощью планетарной мельницы Fritsch Pulverisette 6. Порошок электролита приготавливался при скорости вращения 300–400 об/мин при использовании размольных шаров из диоксида циркония. Композитные порошки необходимого состава для напыления катода и анода изготавливались в тех же условиях, что и электролит – совместным помолом компонентов.
Оптическая микрофотография порошка электролита Ag4RbI5 после помола приведена на рис. 3. Частицы порошка неправильной формы имели средний размер ~5 мкм, т.е. оптимальный для аэрозольного напыления в вакууме [7]. С другой стороны, частицы порошка имеют сильную склонность к образованию агломератов с размерами до 100 мкм и более. Присутствие таких агломератов в сверхзвуковой струе приводит к образованию неплотных, рыхлых и механически непрочных покрытий. Для уменьшения агломерирования порошка внутрь аэрозольной камеры добавлялись стеклянные шарики диаметром 1 мм, движение которых при работе шейкера производило микропомол агломерированного порошка.
Рис. 3.
Оптическая микрофотография порошка электролита Ag4RbI5 перед загрузкой в аэрозольную камеру. Крупные частицы размером в десятки микрон состоят из агломерированных частиц электролита микронного размера.
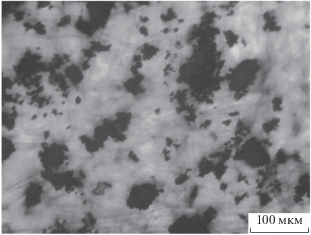
В качестве подложек применялись графитовая бумага (графлекс) толщиной 0.3 мм и стандартный корпус для батареи пуговичного типа “coin cell” (CR-2016, нержавеющая сталь AI-SS304). Подложки при нанесении функциональных слоев имели температуру, близкую к комнатной. Для перемещения подложки в установке и формирования сплошных равномерных функциональных слоев использовалась моторизованная XY-платформа с компьютерным управлением (Jiangxi Liansheng Technology Co., Ltd). Подложка во время осаждения слоев осуществляла параллельное перемещение в виде растра с шагом 0.2 мм. Размеры растра выбирались оптимальным для каждого слоя, чтобы исключить короткое замыкание между катодом и анодом.
Нанесенные слои исследовались на сканирующем автоэмиссионном электронном микроскопе с микроанализом Zeiss LEO SUPRA 25 (“GEMINI” колонна) с разрешением 1.5 нм (ЦКП ИПХФ РАН) и оптическом микроскопе Nikon SMZ 1000.
Для электрохимических измерений и тестирования макетов источников тока был использован потенциостат Р-40Х, Elins (Россия).
РЕЗУЛЬТАТЫ И ИХ ОБСУЖДЕНИЕ
Нанесение слоя композитного анода и электролита непосредственно на дно корпуса ячейки coin cell показало их слабую адгезию к гладкой металлической поверхности и малый коэффициент прилипания частиц (малый коэффициент осаждения покрытия). На рис. 4 представлено оптическое изображение пленки электролита, который является также одной из основных составных частей композитного катода и анода. Стрелками показаны отслоения покрытия, связанные со слабой адгезией Ag4RbI5.
Попытка нанести одну из составных частей анода – серебряный порошок – на полированное дно ячейки также не привела к успеху по причине слабой адгезии. Мы связываем эти неудачи со сложностью формирования “якорного слоя” для случая, когда подложка (нержавеющая сталь) имеет большую твердость, чем налетающие частицы порошка. Улучшить адгезию можно, используя механическое запутывание материала покрытия и подложки [20], т.е., предварительно создавая развитый рельеф на подложке, либо нанося достаточно шероховатый “якорный” подслой. Такой подслой был создан методом АОВ нанесением титанового порошка типа ПТН с основной фракцией менее 40 мкм. На рис. 5 представлены оптические микрофотографии дна корпуса батареи до и после обработки титановым порошком. Возникновение рельефа с характерным размером элементов порядка нескольких микрон оказалось достаточным для закрепления на дне корпуса функциональных слоев ХИТ.
Рис. 5.
Оптические микрофотографии дна корпуса батареи (a) до и (б) после обработки титановым порошком.
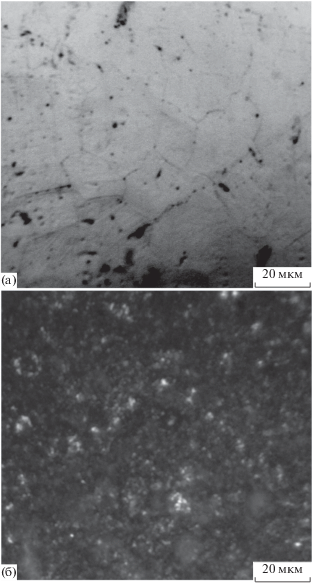
На графлексе, который имеет более мягкую поверхность и развитый рельеф, “якорный слой” возникает сразу и нет необходимости в дополнительной обработке поверхности для обеспечения высокой адгезии композитных покрытий.
Использование разных типов подложек (графлекс и обработанное сверхзвуковой струей аэрозоля титанового порошка дно корпуса батареи) практически не сказалось на рельефе анодного слоя ХИТ (рис. 6a, 6б). В обоих случаях образовалось сплошное покрытие с размером структурных элементов порядка нескольких мкм. Толщина покрытия составляет ~30 мкм, и при такой толщине микрорельеф поверхности подложки нивелируется в процессе осаждения микрочастиц, и формируется характерный для метода АОВ рельеф, связанный с ударами микрочастиц и образованием в результате ударов кратеров [7]. Этот рельеф мезомасштабного уровня и характеризуется элементами (диаметр, глубина и расстояние между этими кратерами) порядка единиц микрон. Было высказано предположение, что кратеры образуются путем воздействия наибольших частиц или агломератов в распределении аэрозоля. Дальнейшее наращивание толщины покрытия за счет слоя электролита до толщины ~60 мкм приводит к огрублению рельефа и появлению элементов порядка 10 мкм (рис. 6), высота которых превышает глубину резкости микроскопа при данном увеличении (элементы показаны стрелками). Такого типа рельеф может быть связан с пластическими течениями при осаждении мягкого и вязкого слоя электролита [21].
Рис. 6.
Оптические микрофотографии: поверхности анодного слоя ХИТ, осажденного на Ti-покрытие (a), на графлекс (б), поверхности электролита осажденного на анодный слой на Ti (в) и на анодный слой на графлексе (г). Стрелками указаны элементы рельефа, высота которых превышает глубину резкости микроскопа при данном увеличении.
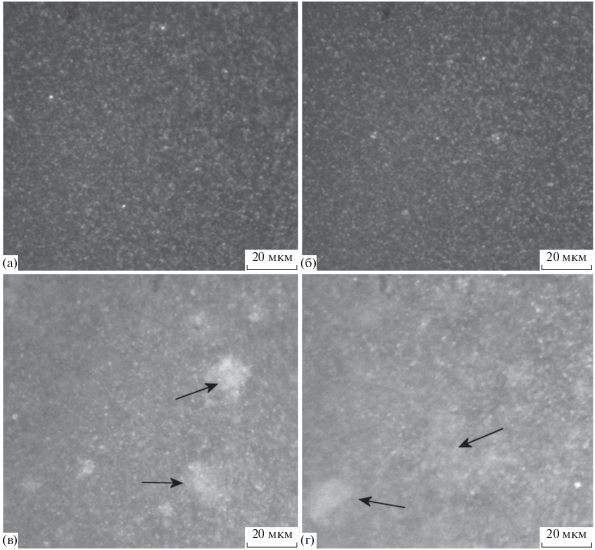
На рис. 7 представлено изображение поверхности слоя электролита, полученное при помощи сканирующего электронного микроскопа (СЭМ). Поверхность имеет кратерообразную структуру с элементами рельефа характерным размером порядка 10 мкм. Последовательное увеличение масштаба изображения (рис. 7a–7в) показывает, что электролит при осаждении образует бездефектное покрытие (трещины и несплошности отсутствуют). Определение структуры покрытия Ag4RbI5 методами СЭМ осложнено тем, что под действием электронного пучка образуются кристаллы Ag, и в результате этого сильно изменяется морфология поверхности слоя (рис. 7г).
Рис. 7.
СЭМ-изображения поверхности слоя электролита с последовательным увеличением масштаба (a, б, в). Изображение (г) является частью участка (в), получившего большую дозу облучения электронами при формировании большего масштаба изображения в микроскопе.
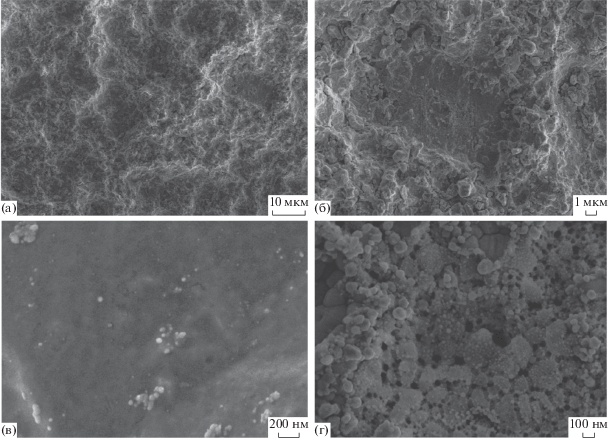
Исходя из предварительных исследований, результаты которых представлены выше, были выбраны две схемы изготовления ХИТ (рис. 8). Возможно формирование батареи как непосредственно в корпусе coin cell, так и на подложке из графлекса. В первом случае для улучшения адгезии анодной пленки на полированный материал корпуса был предварительно нанесен слой титана. Далее был нанесен слой композитного анода на основе Ag, электролит Ag4RbI5 и затем композитный катод. Процесс нанесения функциональных слоев ХИТ проходит без непосредственного извлечения образца из вакуумной камеры нанесения: установка оборудована тремя соплами для каждого из компонентов. Ввиду разложения электролита под действием видимого света, процесс напыления проводили в камере, освещаемой красными светодиодами.
Рис. 8.
Схемы ХИТ: при нанесении на дно корпуса coin cell (слева) и при нанесении на графлекс (справа). Ниже приведен вид подложек перед нанесением: 1 – корпус coin cell; 2 – шайба из графлекса.
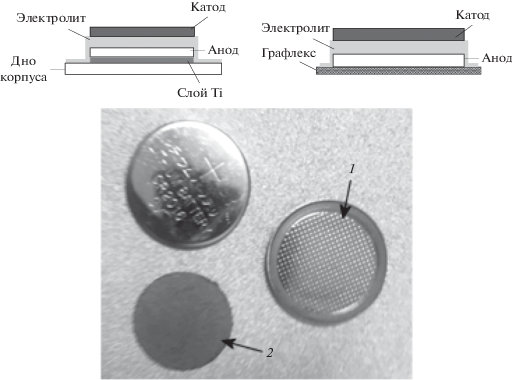
Были получены вольт-амперные характеристики (ВАХ) изготовленных методом АОВ единичных тонкопленочных ячеек. На рис. 9 приведена ВАХ ячейки, полученной на подложке из графлекса. Значение ЭДС ячейки (0.65 В) совпадает с теоретически рассчитанным, что может говорить об отсутствии утечек тока. Максимальный ток разряда составил 3.3 мА/см2. Вблизи потенциала разомкнутой цепи (0.6 В) полученная ячейка обладает мощностью 300 мкВт/см2, что значительно превосходит потребности имплантируемых медицинских устройств (энергопотребление современных кардио- и нейростимуляторов не превышает 60 мкВт).
В результате дальнейшей работы методом АОВ была успешно получена батарея, состоящая из последовательно соединенных трех ячеек, сформированных в одном корпусе coin cell. НРЦ полученной батареи составило 1.8 В, что весьма близко к теоретическому значению ЭДС для системы Ag | RbAg4I5 | Me4NI9 – 0.65 В для единичной ячейки или 1.95 В для сборки из трех ячеек [22]. На рис. 10 (сверху) приведена схема такой батареи. Также на рис. 10 (снизу) изображена схема возможной реализации чисто пленочной батареи из трех ХИТ: вместо использования дополнительных подложек между катодом ниже стоящего ХИТ и анодом выше стоящего ХИТ будет нанесен слой инертного электронного проводника (например, графита), а также дополнительный слой изолятора (например, фторопласта).
Рис. 10.
Схема батареи, собраной из трех ячеек на графлексе (сверху) и схема возможной реализации чисто пленочной батареи из трех ХИТ (снизу).
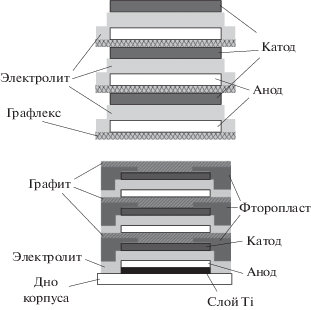
На рис. 11 представлены оптические изображения пленочной ячейки при нанесении функциональных слоев на корпус coin cell, при нанесении на подложку из графлекса, а также изображение готовой батареи из трех ячеек на графлексе, собранных в одном корпусе.
Рис. 11.
Оптические изображения ХИТ, полученных при последовательном нанесении слоев на корпус coin cell (вверху слева) и при нанесении на графлекс (вверху справа); оптическое изображение готовой батареи, собраной из трех ячеек на графлексе (внизу). Обозначения на рисунке: 1 – катод, 2 – электролит, 3 – корпус, 4 – графлекс, 5 – фторопластовая прокладка.
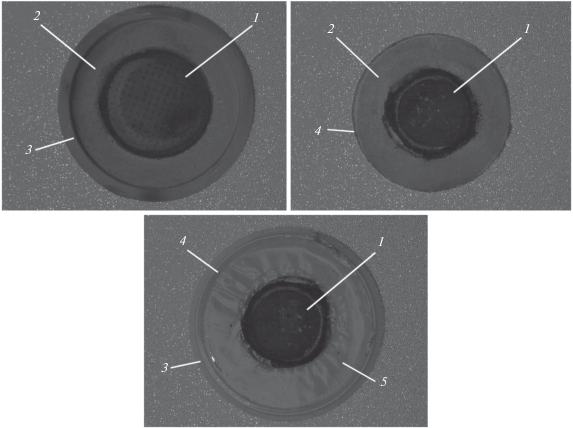
ЗАКЛЮЧЕНИЕ
Экспериментально показана возможность получения тонкопленочнго полностью твердофазного ХИТ на основе системы Ag–(CH3)4NI9, а также батареи из трех ХИТ данной конструкции методом АОВ. Разработана оригинальная методика нанесения бездефектных пленок каждого из функциональных компонентов источника тока (анод, электролит и катод). Вольт-амперные характеристики единичной ячейки, а также батареи из трех ячеек указывают на отсутствие утечек тока, а полученное максимальное значение разрядного тока (3.3 мА/см2) соотвествует техническим требованиям, предьявляемым к ХИТ для электропитания имплантируемых устройств медицинского назначения.
Список литературы
Mond H.G. and Freitag G., The cardiac implantable electronic device power source: evolution and revolution. 2014, Dec; 37, 12, 1728, p. 45. https://doi.org/10.1111/pace.12526
Khanna, V.K., Batteries for Implants, Implantable Medical Electronic, Springer, Cham, 2016, p. 167.
Бабанлы, М.Б., Машадиева, Л.Ф., Велиева, Г.М., Имамалиева, С.З., Шыхыев, Ю.М. Термодинамическое исследование систем Ag–As–Se и AgSI методом ЭДС с твердым электролитом Ag4RbI5. Электрохимия. 2009. Т. 45. С. 424. [Babanly, M.B., Mashadieva, L.F., Velieva, G.M., Imamalieva, S.Z., and Shykhyev, Y.M., Thermodynamic study of the Ag–As–Se and Ag–SI systems using the EMF method with a solid Ag 4 RbI 5 electrolyte, Russ. J. Electrochem., 2009, vol. 45, no. 4, p. 399.]
Деспотули, А.Л., Личкова, Н.В., Миненкова, Н.А., Носенко, С.В. Получение и некоторые свойства тонких пленок твердых электролитов CsAg4Br3 –xI2 +x и RbAg4I5. Электрохимия. 1990. Т. 26. С. 1524. [Despotuli, A.L., Lichkova, N.A., Minenkova, S.V., and Nosenko, S.V., Synthesis and some properties of CsAg4Br3 –xI2 +x and RbAg4I5 solid electrolyte thin films, Elektrohimia (in Russian), 1990, no. 26, p. 1524.]
Akedo, J., Room temperature impact consolidation (RTIC) of fine ceramic powder by aerosol deposition method and applications to microdevices, J. Thermal Spray Technol., 2008, vol. 17, no. 2, p. 181.
Akedo, J. and Lebedev, M., Microstructure and electrical properties of lead zirconate titanate (Pb(Zr52/Ti48)O3) thick films deposited by aerosol deposition method, Jap. J. Appl. Phys., 1999, vol. 38, no. 9S, p. 5397.
Hanft, D., Exner, J., Schubert, M., Stöcker, T., Fuierer, P., and Moos, R., An overview of the aerosol deposition method: Process fundamentals and new trends in materials applications, J. Ceram. Sci. Technol., 2015, vol. 6, no. 3, p. 147.
Baek, S.W., Jeong, J., Schlegl, H., Azad, A.K., Park, D.S., Baek, U.B., and Kim, J.H., Metal-supported SOFC with an aerosol deposited in-situ LSM and 8YSZ composite cathode, Ceramics International., 2016, vol. 42, no. 2, p. 2402.
Hahn, B.D., Park, D.S., Choi, J.J., Ryu, J., Yoon, W.H., Choi, J.H., and Kim, S.G., Preparation and in vitro characterization of aerosol-deposited hydroxyapatite coatings with different surface roughnesses, Appl. Surface Scie., 2011, vol. 257, no. 17, p. 7792.
Piechowiak, M.A., Henon, J., Durand-Panteix, O., Etchegoyen, G., Coudert, V., Marchet, P., and Rossignol, F., Growth of dense Ti3SiC2 MAX phase films elaborated at room temperature by aerosol deposition method, J. Europ. Ceramic Soc., 2014, vol. 34, no. 5, p. 1063.
Seto, N., Hirose, S., Tsuda, H., and Akedo, J., Formation of tough foundation layer for electrical plating on insulator using aerosol deposition method of Cu–Al2O3 Mixed Powder, Advances in multifunctional materials and systems II: John Wiley & Sons, Inc, Hoboken, NJ, USA, 2014, p. 17.
Akedo, J., Aerosol deposition method for fabrication of nano crystal ceramic layer, Materials Sci. Forum. – Trans Tech Publ., 2004, vol. 449, p. 43.
Пуха, В.Е., Овсянников, Н.А. Аддитивные 2D и 3D технологии композитов на основе металлических и керамических систем с использованием аэрозольного осаждения. Станкоинструмент. 2018. Т. 12. № 3. С. 44–54. [Pukha, V. and Ovsyannikov, N., Additive 2D and 3D technologies of composites based on metallic and ceramic systems using aerosol, Stankoinstrument (in Russian), 2018, no. 3(12), p. 44.]
Choi, J.J., Hahn, B.D., Ryu, J., Yoon, W.H., Lee, B.K., and Park, D.S., Preparation and characterization of piezoelectric ceramic–polymer composite thick films by aerosol deposition for sensor application. Sensors and Actuators A: Physical., 2009, vol. 153, no. 1, p. 89.
Kwon, O.Y., Na, H.J., Kim, H.J., Lee, D.W., and Nam, S.M., Effects of mechanical properties of polymer on ceramic-polymer composite thick films fabricated by aerosol deposition, Nanoscale research letters, 2012, vol. 7, no. 1, p. 261.
Kim, H.J., Yoon, Y.J., Kim, J.H., and Nam, S.M., Application of Al2O3-based polyimide composite thick films to integrated substrates using aerosol deposition method. Materials Science and Engineering, B, 2009, vol. 161, nos. 1–3, p. 104.
Akedo, J., Ryu, J., Jeong, D.Y., and Johnson, S.D., Aerosol Deposition (AD) and Its Applications for Piezoelectric Devices. Advanced Piezoelectric Materials (Second Edition), 2017, p. 575.
Machida, N., Peng, H., and Shigematsu, T., Mechano-chemical synthesis of RbAg4I5 and KAg4I5 crystals and their silver-ion conducting properties, J. Japan Soc. Powder and Powder Metallurgy, 2002, vol. 49, p. 69.
Загороднев, В.Н., Личкова, Н.В. Получение твердого электролита RbAg4I5 из расплава при направленной кристаллизации. Изв. АН СССР. Неорган. материалы. 1983. Т. 19. № 6. С. 1031. [Zagorodnev, V.N. and Lichkova, N.V., Synthesis of the solid electrolyte RbAg4I5 by directional crystallization of the melt, Inorganic materials (in Russian), 1983, vol. 19, no. 6, p. 1031.]
Lee, D.W., Kwon, O.Y., Cho, W.J., Song, J.K., and Kim, Y.N., Characteristics and mechanism of Cu films fabricated at room temperature by aerosol deposition, Nanoscale research letters, 2016, vol. 11, no. 1, p. 162.
Bae, H., Choi, J., and Choi, G.M., Electrical conductivity of Gd-doped ceria film fabricated by aerosol deposition method, Solid State Ionics, 2013, vol. 236, p. 16.
Михайлова, А.М., Укше, Е.А. Электрохимические цепи с твердыми электролитами в системе серебро–комплексный йодный электрод. Электрохимия. 1987. Т. 23. С. 685. [Mikhailova, A.M. and Ukshe, E.A., Electrochemical circuits with solid electrolytes in the system silver–complex iodine electrode, Elektrohimia (in Russian), 1987, no. 23, p. 685.]
Дополнительные материалы отсутствуют.