Электрохимия, 2019, T. 55, № 9, стр. 1045-1058
Оценка ухудшения характеристик фотоэлектродов в сенсибилизированных красителем солнечных элементах
Кумар Амит a, Риши Шарма a, *, Гаурав Праншу a, Р. Л. Боксман b
a Отделение физики, Технологический институт Бирла
Ранчи-825215 Мерса, Индия
b Школа электротехники, Университет Тель-Авив
6997801 Тель-Авив, Израиль
* E-mail: rishisharmabit@hotmail.com
Поступила в редакцию 07.07.2018
После доработки 27.11.2018
Принята к публикации 01.02.2019
Аннотация
В настоящей работе представлено взаимодействие фотоэлектродов с электролитами и красителями, поскольку необходимо исследовать ухудшение характеристик прозрачных проводящих электродов в отношении структурных, оптических и электрических свойств, а также характеристик коррозионной устойчивости. В данном исследовании были использованы три электрода, в том числе один на основе оксид индия–олова (ITO) и два на основе легированного алюминием оксида цинка (AZO); два красителя, в том числе эозин желтый и рутений красный, и два электролита, в том числе йодид калия (KI) и йодид лития (LiI). Посредством сочетаний вышеупомянутых электродов, красителей и электролитов получены двенадцать солнечных элементов. Исследован потенциал разомкнутой цепи (Voc) полученных элементов в зависимости от времени (в течение 30 сут). Изменения структуры и элементного состава электродов после взаимодействия с красителем и электролитом проанализированы с использованием рентгеновской дифракции и энергодисперсионной рентгеновской спектроскопии соответственно. Прозрачность и поверхностное сопротивление электродов изучены до и после взаимодействия с электролитами и красителями. Характеристики коррозионной устойчивости трех электродов исследованы с использованием электрохимического анализатора с электролитами KI и LI.
ВВЕДЕНИЕ
Истощение доступных горючих ископаемых и постоянно растущая мировая потребность в энергии мотивируют поиск альтернативных источников энергии, преимущественно солнечной энергии. Поскольку фотоэлектрические устройства обеспечивают чистую энергию, которая способна уменьшать всемирную зависимость от традиционных источников энергии, эти устройства представляют огромный интерес для исследовательского сообщества. После главных прорывных работ в 1991 г., в течение двух десятилетий сенсибилизированные красителем солнечные элементы (СКСЭ) в возрастающей степени привлекают внимание исследователей и проникают в общественное сознание [1–3]. Сенсибилизированные красителем солнечные элементы представляют собой перспективные экономичные солнечные устройства, они были интенсивно исследованы в качестве потенциальной альтернативы традиционным солнечным элементам на основе кремния [4, 5] – с последующим недавним инновационным внедрением в приложения с более жесткими условиями, которые ранее могли выдерживать только традиционные солнечные элементы [6].
Наряду с другими основными компонентами СКСЭ, электроды, содержащие прозрачные проводящие оксиды (ППО), представляют собой неотъемлемую часть тонкопленочных солнечных элементов, которая придает важные параметры, определяющие все эксплуатационные характеристики элементов [7, 8]. Таким образом, эксплуатационные характеристики этих элементов в существенной степени зависят от эксплуатационных характеристик ППО или фотоанодов. Недавние исследования также посвящены дальнейшему улучшению и усовершенствованию устройств с электролитами в целях повышения устойчивости и эффективности [9, 10]. СКСЭ содержит химические вещества, включая красители и электролиты, которые вступают в непосредственный контакт с электродами. Они разрушают проводящий слой и вызывают коррозию электродов. Таким образом, эксплуатационные характеристики СКСЭ в значительной степени зависят от химической устойчивости ППО. Предполагается, что электроды СКСЭ должны быть закрытыми в такой же степени, как химически инертными, и сохранять свою структуру, поверхностное сопротивление и прозрачность в течение продолжительного времени, чтобы обеспечивать продолжительный срок хранения СКСЭ.
Легированный оловом оксид индия (ITO) и легированный фтором оксид олова (FTO) представляют собой обычно используемые прозрачные проводящие электроды в СКСЭ [11]. ITO преобладает в области прозрачных проводящих электров в течение почти четырех десятилетий. Однако применение ITO становится все более проблематичным вследствие: 1) ограниченной доступности и высокой стоимости индия, 2) неустойчивости материала в присутствии кислоты или основания, 3) его чувствительности к диффузии ионов в полимерные слои и 4) его ограниченной прозрачности в ближнем инфракрасном диапазоне. В настоящее время конкурентами ITO становятся новые разрабатываемые проводящие прозрачные оксиды, такие как легированный алюминием оксид цинка (AZO) и графен [12]. AZO является ведущим претендентом в качестве прозрачного проводящего оксида для замены ITO. Существуют несколько сообщений в отношении эксплуатационных характеристик электродов (в частности, ITO), устойчивости СКСЭ, ухудшения каталитических характеристик, использования разупорядоченного углеродного материала в СКСЭ и т.д. [13–16]. Ухудшение эксплуатационных характеристик СКСЭ в различных условиях и его механизмы также были исследованы множеством авторов [17–19]. Долгосрочная устойчивость СКСЭ представляет собой основную проблему вследствие утечки и испарения красителя и электролита, ухудшения эксплуатационных характеристик красителя, ультрафиолетовой фотокаталитической активности TiO2 и ухудшения эксплуатационных характеристик электродов [17, 18, 20–22]. Проведены также исследования в целях улучшения и увеличения продолжиельности устойчивости СКСЭ с мягкими электролитами [23]. Кроме того, для дополнения полученных данных более конкретными результатами и свидетельствами новых и предшествующих исследований требуется более подробное изучение ухудшение эксплуатационных характеристик электродов под действием электролитов и красителей. Отсутствуют всесторонние и подробные исследования ухудшения эксплуатационных характеристик электродов вследствие взаимодействия с красителями и электролитами. Основной анализ сосредоточен на эксплуатационных характеристиках катализатора, TiO2 и противоэлектродов различных типов [16, 18, 20, 24].
В настоящей работе систематически исследовано ухудшение эксплуатационных характеристик прозрачных проводящих электродов в двенадцати СКСЭ. Для получения всех СКСЭ использовали ППО в качестве электродов и угольную сажу в качестве катализатора на противоэлектроде. Использовали три прозрачных проводящих электрода, один электрод ITO (приобретенный товарный электрод) и два электрода AZO (один получен осаждением с помощью анодной дуги в вакууме и другой получен осаждением с помощью системы высокочастотного напыления). Для получения СКСЭ были использованы два популярных красителя, в том числе рутений красный (Ru) и эозин желтый (EY), и два электролита, в том числе йодид лития (LiI) и йодид калия (KI). Эксплуатационные характеристики полученных СКСЭ исследовали в течение месяца (30 сут подряд). Через месяц были оценены изменения потенциала разомкнутой цепи, структуры, прозрачности и поверхностного сопротивления. Кроме того, была проанализирована коррозионная устойчивость электродов по отношению к растворам электролитов.
МАТЕРИАЛЫ И МЕТОДЫ
Синтез электрода AZO
Один электрод AZO, обозначенный AZO-A, получали методом осаждения с помощью фильтрованной анодной дуги в вакууме (ФАДВ), а другой электрод AZO, обозначенный AZO-S, получали методом осаждения с помощью высокочастотного напыления. Для получения электрода AZO-A была использована большая вакуумная система дугового осаждения [25]. В методе ФАДВ струи плазмы испарившегося металла получают из катодных пятен; струи изгибают криволинейным магнитным полем, которое направляет плазму по криволинейному каналу, предотвращая попадания капель металла на подложку. Осаждение AZO-A осуществляли, используя катод на основе Zn, который содержал 9 ат. % Al, на стеклянные подложки в кислородной атмосфере. Подложки перемещали через пучок плазмы на выходе криволинейного канала со скоростью 4 см/с. Пленки AZO-A подвергали закалке на воздухе.
Осаждение AZO-S осуществляли, используя высокочастотное магнетронное напыление при мощности высокочастотного магнетрона 150 Вт на трехдюймовую мишень (содержащую приблизительно 2% алюминия и 98% оксида цинка) при давлении 2 × 10–2 торр (базовое давление до 5.0 × × 10–5 торр) в потоке газообразного аргона со скоростью 30 станд. куб. см/мин в течение одного часа. Дополнительное нагревание камеры не осуществляли.
Исследования
Рентгеновский дифрактометр (Rigaku Smartlab) использовали для анализа структурных изменений в прозрачных проводящих электродах. Прозрачность электродов измеряли, используя спектрометр в ультрафиолетовом и видимом диапазонах (LAMBDA 25). Коррозионную устойчивость исследовали с помощью электрохимического анализатора модели 680B (CH Instruments, США). Поверхностное сопротивление образцов измеряли, используя метод Ван дер Пау и источник-измеритель Keithley (Keithley Sourcemeter 2401 с вольтамперометрической приставкой LabTracer). Энергодисперсионный рентгеновский спектрометр (Oxford Instruments) в сочетании со сканирующим электронным микроскопом (JSM 6390LV, JEOL) использовали для элементного анализа.
Получение и эксплуатация СКСЭ
Всего было получено двенадцать комплектов сенсибилизированных красителем солнечных элементов (по три элемента для каждого сочетания), в которых были использованы в сочетании три электрода (один ITO и два AZO), два красителя (рутений красный и эозин желтый) и два электролита (йодид лития и йодид калия). Полученные элементы подробно описаны в табл. 1. Схематическая диаграмма полученного элемента представлена на рис. 1. В устройствах СКСЭ использовали мезопористый оксидный слой TiO2 для электронной проводимости. Слой красителя с переносом заряда наносили на мезопористый оксидный слой [8]. Электроны, испускаемые посредством фотовозбуждения красителя, поступали в зону проводимости оксида. Краситель возвращался в свое основное состояние посредством получения электронов от электролита. Электролит обычно представляет собой органический растворитель, в котором содержится окислительно-восстановительная система, такая как пара йодид/трийодид. Йодид регенерируется посредством восстановления трийодида на противоэлектроде, причем цепь замыкается посредством миграции электронов через внешнюю нагрузку. Таким образом, устройство производит электроэнергию без какого-либо изменения химического состава [1].
Таблица 1.
Сенсибилизированные красителем солнечные элементы, содержащие TiO2 в качестве полупроводникового слоя и различные сочетания электродов, электролитов и красителей
Номер элемента | Проводящие электроды | Электролиты | Красители |
---|---|---|---|
1 | ITO | LiI | Ru |
2 | ITO | LiI | EY |
3 | ITO | KI | Ru |
4 | ITO | KI | EY |
5 | AZO-A | LiI | Ru |
6 | AZO-A | LiI | EY |
7 | AZO-A | KI | Ru |
8 | AZO-A | KI | EY |
9 | AZO-S | LiI | Ru |
10 | AZO-S | LiI | EY |
11 | AZO-S | KI | Ru |
12 | AZO-S | KI | EY |
В СКСЭ использована суспензия, содержащая измельченный на шаровой мельнице TiO2, и тетраизопропоксид титана и полученная посредством ультразвуковой обработки в этаноле. Растворы двух красителей получали, растворяя рутений красный в деионизованной воде и эозин желтый в этаноле. Два раствора электролитов получали, добавляя йодид лития в ацетонитрил и йодид калия в дистиллированную воду. Йод также добавляли в электролиты, которые затем обрабатывали ультразвуком в течение приблизительно одного часа. Маску площадью 1 см2 получали из клейкой ленты и прикрепляли на проводящую сторону стекла с покрытием ITO или AZO. Пасту TiO2 затем равномерно наносили с помощью стеклянной палочки. После удаления маски из клейкой ленты образец нагревали на горячей плитке в течение приблизительно 10 мин при 100°C. Стекло ITO или AZO с покрытием TiO2 погружали в раствор красителя и выдерживали в течение 10 мин. Образец снова подвергали умеренному нагреванию для ускорения поглощения и окрашивания. Избыток красителя удаляли посредством промывания деионизованной водой или этанолом. Каталитический слой графита наносили на противоэлектрод из того же материала. Оба электрода складывали друг с другом с небольшим сдвигом, используя зажимы для бумаг, причем проводящие стороны были обращены друг к другу. Затем добавляли раствор электролита в элемент и присоединяли провода к открытым краям. Края затем герметизировали силиконовым гелем и лентой. Получение элементов ранее было описано более подробно [26].
ОБСУЖДЕНИЕ РЕЗУЛЬТАТОВ
Эксплуатационные характеристики солнечных элементов
Потенциал разомкнутой цепи Voc полученных элементов измеряли в течение одного месяца при воздействии солнечного излучения с коэффициентом воздушной массы 1.5, которое производил солнечный имитатор (ламповый блок Newport 67005 с мощностью от 50 до 500 Вт источник энергии Newport 69907). Значение Isc здесь не представлено, поскольку оно является очень низким. Изменение Voc с течением времени представлено на рис. 2–4 для солнечных элементов, содержащих электроды ITO, AZO-A и AZO-S соответственно. На рис. 5 представлен потенциал различных элементов в первый день. На рис. 6 представлено процентное уменьшение потенциала в течение 30 сут. На рис. 2–4 можно видеть, что, как правило, Voc уменьшается с течением времени, однако изменения Voc различаются для различных электродов и различных сочетаний электролитом и красителей. Приблизительно через 20 сут Voc становится устойчивым. В настоящем исследовании использованы сочетания электролитов и красителей, которые представляют собой LiI–Ru, LiI–EY, KI–Ru, KI–EY. На рис. 2 представлены графики зависимости Voc от числа суток для элементов, в которых использованы электроды ITO (элементы 1–4). В случае электродов ITO (рис. 5) потенциал первого дня для элемента 1, содержащего сочетание LiI–Ru, принимал наиболее высокое значение (657 мВ). На рис. 5 представлены потенциалы первого дня для электродов ITO и различных сочетаний электролитов и красителей (LiI–EY, KI–Ru, KI–EY). Минимальное значение Voc (30 мВ) первого дня наблюдали для сочетания KI–Ru. Значение Voc элементов, содержащих электроды ITO, уменьшалось с течением времени для всех сочетаний электролитов и красителей, Voc для сочетаний LiI–Ru, LiI–EY, KI–Ru и KI–EY через 30 сут составляло 45, 58, 33 и 45% соответствующего значения первого дня (рис. 6) соответственно.
На рис. 3 представлено изменение Voc с течением времени в течение 30-суточного периода для элементов, содержащих электроды AZO-A (элементы 5–8). Наиболее высокий потенциал первого дня элемента, содержащего электроды AZO-A с сочетанием LiI–EY, составлял 307 мВ (Voc). Второе место занимал потенциал первого дня Voc (287 мВ) для сочетания KI–EY. Электроды AZO-A проявляли минимальный потенциал первого дня Voc для сочетаний Li–Ru (Voc = 152 мВ) и KI–Ru (Voc = 110 мВ). Через 30 сут значение Voc составляло 84, 73, 70% и 66% соответствующего значения первого дня (рис. 6) для сочетаний LiI–Ru, LiI–EY, KI–Ru и KI–EY соответственно. На рис. 4 представлено изменение Voc с течением времени для элементов, содержащих электроды AZO-S (элементы 9–12). Электрод AZO-S проявлял наиболее высокое значение первого дня Voc (321 мВ) с сочетанием LiI–EY и второе по величине значение (268 мВ) с сочетанием KI–Ru. Электрод AZO-S проявлял минимальные значения первого дня Voc для сочетаний Li–Ru (Voc = 149 мВ) и KI–EY (Voc = 95 мВ). Через 30 сут Voc составлял 77, 86, 70 и 91% (рис. 5) от значения первого дня Voc для сочетаний LiI–Ru, LiI–EY, KI–Ru и KI–EY соответственно. Для каждого элемента также измеряли ток короткого замыкания (Isc), который составлял от 0.113 до 0.362 мА.
Эти наблюдения показывают, что электроды ITO сначала проявляли наиболее высокий потенциал с сочетаниями Li-Ru, однако через 30 сут потенциал уменьшается более чем на 50%. Электроды AZO-A и AZO-S проявляли наилучшие характеристики с сочетанием LiI–EY. Однако начальные значения Voc, полученные для электродов, составляли половину соответствующих значений для электродов ITO. Через 30 сут эксплуатационные характеристики электродов AZO становились более высокими и устойчивыми, чем для электродов ITO.
Структурные свойства
Рентгеновские дифрактограммы (РДГ) электродов ITO, AZO-A и AZO-S (до и после использования, наблюдаемые в течение 30 сут при воздействии солнечного излучения с коэффициентом воздушной массы 1.5) представлены на рис. 7–9 соответственно. Рентгеновская дифрактограмма ITO до использования на рис. 7 проявляет широкий пик с центром при 2θ = 24°. Это доказывает образование аморфного ITO [27]. Кроме того, наблюдались несколько узких пиков при 9.48°, 21.28°, 30.15°, 35.17°, 50.46° и 60.08°. Эти узкие пики считаются соответствующими кристаллическому In2O3 [28]. Отсутствовали пики Sn, SnO и SnO2. Сдвиг положений пиков обусловлен внедрением Sn в решетку In2O3 [27, 29]. Рентгеновские дифрактограммы после использования ITO (для элементов, содержащих сочетания электролитов и красителей LiI–Ru, LiI–EY, KI–Ru и KI–EY) также представлены на рис. 7. На дифрактограммах этих электродов наблюдались новые пики при 6.05°, 9.44°, 14.98°, 27.47°, 41.29°, 54.33° и 56.20°. Причины этих новых пиков представляют собой включение, взаимодействие или проникновение молекул электролитов и красителей в электродный материал вследствие химических реакций между ними. Появление этих новых пиков предполагает, что структура ITO изменяется в результате взаимодействия ITO с материалами красителей и/или электролитов. Это может происходить вследствие диффузии элементов электролита и красителя в междоузлия решетки ITO. Система электролитов и красителей, находящихся между двумя электродами, также ведет себя как типичная электролитическая система, в которой существует потеря и наслаивание металлических или проводящих слоев. Это приводит к тому, что используемые элементы вводят новый или дополнительный материал по сравнению с немодифицированными электродами, и изменяются пики, полученные на РДГ.
Рентгеновские дифрактограммы AZO-A представлены на рис. 8. До использования AZO проявляет интенсивные дифракционные пики (002) приблизительно при 34.1° [30]. Это значение 2θ очень близко к соответствующему значению (34.4°) стандартного кристалла ZnO, показывая, что все полученные пленки имели предпочтительную ориентацию вдоль оси c, которая перпендикулярна подложке [31]. Рентгеновские дифрактограммы AZO-S представлены на рис. 9. Наблюдается интенсивный пик с центром при 34.1°, аналогичный пику на РДГ AZO-A. Рентгеновские дифрактограммы образцов AZO-A и AZO-S после использования (рис. 8 и 9 соответственно) проявляют новые пики при 6.05°, 9.44°, 14.98°, 27.47°, 41.29°, 54.33° и 56.20°. Однако интенсивность этих новых пиков очень мала по сравнению с интенсивностью характеристических пиков AZO. Эти наблюдения позволяют предположить, что взаимодействие электролита и красителя изменяет структуру электродов, однако для электродов AZO наблюдалось меньшее изменение, чем для электродов ITO.
Элементный анализ
Энергодисперсионная рентгеновская (ЭДР) спектроскопия была использована для измерения концентраций элементов в пленках. Она показала присутствие Al, Zn, O в пленках AZO до использования и присутствие In, Sn и O в пленках ITO до использования. Другие элементы, такие как Na, Ca, Ru, Br, K, Ti и т.д., также наблюдались в электродах после использования. Атомное процентное содержание элементов Al, Zn, In, Sn и O в электродах до и после использования представлено на рис. 10–12. Атомное процентное содержание O, In и Sn в электродах ITO до использования составляло 87.93, 11.35 и 0.72 соответственно. После взаимодействия с красителями и электролитами процентное содержание O и In в пленке было меньше, чем в электроде до использования. Атомное процентное содержание O составляло 77.00, 82.03, 79.79 и 83.01 для сочетаний электролитов и красителей LiI–Ru, LiI–EY, KI–Ru и KI‒EY соответственно. Атомное процентное содержание In составляло 7.69, 6.4, 6.8 и 5.35 для сочетаний электролитов и красителей LiI–Ru, LiI‒EY, KI–Ru и KI–EY соответственно. Однако концентрация Sn, как правило, увеличивалось, за исключением сочетания LiI–EY. Оно составляло 1.01, 0.56, 0.73 и 0.98 для сочетаний электролитов и красителей LiI–Ru, LiI–EY, KI–Ru и KI–EY соответственно.
Рис. 10.
Изменчивость атомного процентного содержания O, In и Sn в электродах на основе ITO до и после использования.
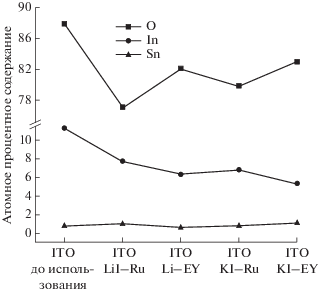
Рис. 11.
Изменчивость атомного процентного содержания O, Al и Zn в электродах на основе AZO-A до и после использования.

Рис. 12.
Изменчивость атомного процентного содержания O, Al и Zn в электродах на основе AZO-S до и после использования.

В электроде AZO-A до использования атомное процентное содержание O, Zn и Al составляло 43, 56.52 и 0.49 соответственно. После взаимодействия с красителями и электролитами концентрация кислорода, как правило, уменьшалась, за исключением LiI–EY. Оно составляло 33.02, 46.49, 35.3 и 35.3 для сочетаний электролитов и красителей LiI–Ru, LiI–EY, KI–Ru и KI–EY соответственно. Атомное процентное содержание Zn и Al составляло 52, 47.11, 59.59, 59.28 и 0.57, 0.57, 0.94, 0.94 для сочетаний электролитов и красителей LiI–Ru, LiI–EY, KI–Ru, KI–EY соответственно. Согласно наблюдениям, атомное процентное содержание Zn было ниже в случае LiI-Ru, чем в электроде AZO-A до использования. Однако концентрация Al была выше во всех электродах после использования, чем в электроде AZO-A до использования.
В электроде AZO-S до использования атомное процентное содержание O, Zn и Al составляло 39.07, 58.71 и 2.22 соответственно. После взаимодействия с красителями и электролитами, концентрации кислорода и Zn, как правило, были выше, чем в электроде AZO-S до использования, за исключением KI–Ru для кислорода и LiI–EY и KI–EY для Zn. Атомное процентное содержание O и Zn составляло 32.02, 33.28, 43.51, 35.34 и 51.04, 61.32, 50.15, 59.28 для сочетаний электролитов и красителей LiI–Ru, LiI–EY, KI–Ru, KI–EY соответственно. Концентрация Al была меньше во всех электродах после использования. Атомное процентное содержание Al составляло 0.57, 0.92, 0.55 и 0.95 для сочетаний электролитов и красителей LiI–Ru, LiI–EY, KI–Ru и KI–EY соответственно.
Поверхностное сопротивление, прозрачность и химическая реакционная способность прозрачных проводящих электродов зависят от состава, включая количество легирующих и других примесей в материалах. Анализ методом энергодисперсионной рентгеновской спектроскопии показал, что состав пленок ITO и AZO изменялся вследствие взаимодействия с электролитом и красителем. Новые элементы внедрялись в пленки. Трудно установить корреляцию изменений, наблюдаемых в составе, со свойствами, однако можно утверждать, что изменение свойств происходит вследствие изменения состава и внедрения новых элементов. Небольшое изменение состава по сравнению с первоначальными значениями является желательным для хорошего качества прозрачных электродов.
Прозрачность
Хорошая прозрачность проводящего электрода представляет собой одно наиболее важное свойство, требуемое для применения в солнечных элементах. Прозрачность (процентное пропускание) как функция длины волны (от 400 до 1000 нм) пленок ITO, AZO-A и AZO-S представлена на рис. 13–15 соответственно. На рис. 13 представлено, что прозрачность ITO до использования составляла более чем 90%. Однако прозрачность электродов после использования уменьшалась. Аналогичные графики прозрачности наблюдались для образцов AZO‑A и AZO-S (на рис. 14 и 15). Таким образом, можно видеть, что прозрачность уменьшается вследствие взаимодействия электродов с электролитами и красителями. Это объясняет ухудшение эксплуатационных характеристик элемента с течением времени, которое представляют рис. 2‑4. Кроме того, исследуемые электроды ITO имели наиболее высокую прозрачность; следует напомнить, что элемент ITO–Lil–Ru имел наиболее высокое начальное значение Voc.
Рис. 13.
График зависимости пропускания от длины волны для электродов на основе ITO до и после использования.

Поверхностное сопротивление
Поверхностное сопротивление электродов представлено на рис. 16. Поверхностное сопротивление измеряли методом Ван дер Пау. Он представляет собой широко используемый метод измерения сопротивления образцов [32]. Он позволяет измерять сопротивление имеющего произвольную форму тонкого пластинчатого образца, содержащего четыре очень малых омических контакта, находящихся на периферии, предпочтительно в углах пластинки. На рис. 16 можно видеть, что до использования электрод ITO имел минимальное поверхностное сопротивление среди всех исследованных электродов. Однако поверхностное сопротивление электродов ITO после использования было выше, чем в случае электродов AZO-A и AZO-S после использования. Наиболее высокое поверхностное сопротивление наблюдалось для электрода ITO в элементе 2 (LiI‒EY). Для устойчивого солнечного элемента оказывается желательным, что поверхностное сопротивление не должно увеличиваться с течением времени, например, вследствие взаимодействия с электролитами и красителями. Минимальное поверхностное сопротивление, полученное в электродах ITO, наблюдалось для элемента 4 (KI–EY). Минимальное поверхностное сопротивление в элементах AZO-A и AZO-S наблюдалось для элемента 7 и элемента 9 соответственно. Эти элементы содержали сочетания KI–Ru и LiI–Ru соответственно.
Характеристики коррозионной устойчивости
Характеристика коррозионной устойчивости прозрачного проводящего электрода представляет собой важное свойство для понимания химической устойчивости электродов в отношении красителей и электролитов. Поскольку СКСЭ представляет собой химическое устройство, химические вещества, такие как электролиты, вступают в непосредственный контакт с электродами, и, таким образом, вызывают коррозию электродов, что ухудшает эксплуатационные характеристики элемента. Промышленное применение СКСЭ станет экономичным только тогда, когда будет гарантирована химическая устойчивость электродов. Коррозия прозрачного электрода происходит вследствие электрохимических реакций на границе раздела между покрытием и раствором электролита. Коррозия обычно происходит со скоростью, которую определяет равновесие между противоположными электрохимическими реакциями. Первая реакция представляет собой анодную реакцию, в которой металл окисляется, высвобождая электроны в металл. Другая реакция представляет собой катодную реакцию, в которой растворенные частицы восстанавливаются, принимая электроны из металла. Когда эти две реакции находятся в равновесии, потоки электронов от обеих реакций выравниваются, и чистый поток электронов отсутствует. Две реакции могут происходить на одном металле или на двух различных металлах, которые находятся в электрическом соединении.
Характеристики коррозионной устойчивости образцов исследовали, используя электрохимический анализатор с четырьмя электродами. Хлорид серебра использовали в качестве электрода сравнения, и платину использовали в качестве противоэлектрода; образец представлял собой рабочий электрод, и один электрод был заземлен. Растворы LiI и KI использовали в качестве растворов электролитов (1 г каждого из KI/LiI в 20 мл ацетонитрила и 2 мл изопропоксида титана). Линейную развертку потенциала рабочего электрода (ППО) осуществляли, используя потенциостат, и измеряли получаемый в результате ток. Развертку потенциал осуществляли в диапазоне от –1.2 до +1.2 В со скоростью 10 мВ/с, причем система находилась при комнатной температуре. Эксперимент проводили таким образом, что электролит находился в контакте с покрытой поверхностью. Площадь контакта во всех случаях составляла 0.5 см2. После завершения исследований коррозии вычисляли скорость коррозии. Поляризационные кривые (т.е., графики зависимости тока от потенциала) электродов ITO, AZO-A и AZO-S с электролитами KI и LiI представлены на рис. 17–19 соответственно. Скорость коррозии, вычисленная из поляризационных кривых, представлена на рис. 20. Наиболее высокие скорости коррозии наблюдались для электродов ITO в случае обоих электролитов KI и LiI. Скорость коррозии была также высокой для электрода AZO-A с раствором LiI. Менее высокие скорости коррозии наблюдались для электродов AZO-S с обоими электролитами KI и LiI и для электрода AZO-A с электролитом LiI.
Результаты наблюдений кратко представлены в табл. 2.
Таблица 2.
Краткий обзор наблюдений электродов ITO, AZO-A и AZO-S
Таблица 2A | |||||
Электрод | Начальное значение Voc | Процентное изменение Voc | Процентное пропускание | Поверхностное сопротивление | Коррозия |
LiI–Ru | LiI–Ru | LiI–Ru | LiI–Ru | LiI | |
ITO | Высокое | Высокое | Высокое | Высокое | Высокая |
AZO-A | Низкое | Низкое | Среднее | Среднее | Средняя |
AZO-S | Низкое | Низкое | Среднее | Низкое | Низкая |
Таблица 2B | |||||
LiI–EY | LiI–EY | LiI–EY | LiI–EY | LiI | |
ITO | Низкое | Высокое | Высокое | Высокое | Высокая |
AZO-A | Среднее | Среднее | Низкое | Низкое | Средняя |
AZO-S | Среднее | Низкое | Низкое | Среднее | Низкая |
Таблица 2C | |||||
KI–Ru | KI–Ru | KI–Ru | KI–Ru | KI | |
ITO | Низкое | Высокое | Высокое | Высокое | Высокая |
AZO-A | Низкое | Среднее | Среднее | Низкое | Низкая |
AZO-S | Среднее | Среднее | Среднее | Среднее | Низкая |
Таблица 2D | |||||
KI–EY | KI–EY | KI–EY | KI–EY | KI | |
ITO | Низкое | Высокое | Высокое | Высокое | Высокая |
AZO-A | Среднее | Среднее | Среднее | Низкое | Низкая |
AZO-S | Низкое | Очень низкое | Среднее | Высокое | Низкая |
В настоящем исследовании наблюдаемые значения определены как высокие, средние и низкие. Высокие, средние и низкие значения определяют характерные свойства исследованных сочетаний электродов, красителей и электролитов. Для графического представления использована схема, содержащая три цвета (черный, серый и белый). Черный цвет показывает наиболее желательный результат, и серый цвет показывает наименее желательный результат для каждого свойства в приложениях солнечных элементов. Например, в столбце “Начальное значение Voc” (представляет собой значение Voc в первый день) значение Voc для сочетания LiI–Ru является наиболее высоким для электрода ITO (Voc = 657 мВ), в то время как для электродов AZO-A (Voc =152 мВ) и AZO-S (Voc =149 мВ) значения Voc являются низкими, таким образом, уровни высокий, низкий и низкий определены для ITO, AZO-A и AZO-S, соответственно. Поскольку высокое значение Voc является желательным для хороших эксплуатационных характеристик солнечного элемента, следовательно, черный цвет соответствует ITO, и серый цвет соответствует AZO-A и AZO-S. В следующем столбце “Процентное изменение Voc” представлено (в процентах) значение Voc через 30 сут. Для сочетания LiI–Ru значение Voc в случае ITO составляет 45% соответствующего значения первого дня, в то время как в случаях AZO-A и AZO-S оно составляет 84 и 77% соответствующего значения первого дня. Следовательно, Voc уменьшается в большей степени для электрода ITO по сравнению с AZO-A и AZO-S, и, таким образом, уровни высокий, низкий и низкий определены для ITO, AZO-A и AZO-S, соответственно (представляют собой значительное изменение и небольшое изменение Voc через 30 сут). Однако для хорошего электрода изменение Voc должно быть низким, и, таким образом, вследствие большого изменения Voc в данном столбце для ITO определен серый цвет, и для AZO-A и AZO-S определен черный цвет.
Черный цвет представляет собой желательное значение данного свойства, и серый цвет показывает неприемлемое значение. Аналогичным образом, белый цвет показывает промежуточное значение, которое может представлять собой приемлемое, но не желательное значение. Оптимальное сочетание среди исследованных вариантов представляет собой полностью черный ряд. Однако здесь отсутствует полностью черный ряд. В таблице 2D AZO-A имеет три белых и два черных блока. Это показывает, что для сочетания электролита KI и красителя EY начальное значение Voc является умеренным, и изменение Voc с течением времени также оказывается не очень большим, прозрачность также является достаточно хорошей, поверхностное сопротивление является низким и скорость коррозии в электролите KI также является низкой. Это означает что электрод AZO-A с электролитом KI и красителем EY должен быть долговечным. Электрод AZO-S также является приемлемым с сочетанием электролита KI и красителя Ru (см. таблицу 2C, четыре белый блока и один черный блок).
ВЫВОДЫ
В настоящей работе представлено систематическое исследование прозрачных проводящих электродов (ITO и AZO). Получены двенадцать элементов из сочетаний красителей, электролитов и электродов. Исследованы потенциал разомкнутой цепи (Voc) полученных элементов и другие свойства, такие как структура, элементный состав, прозрачность, поверхностное сопротивление и коррозионная устойчивость, а также проанализированы изменения свойств. Структура, состав, прозрачность, поверхностное сопротивление и коррозионная устойчивость прозрачных электродов изменяются с течением времени при воздействии солнечного излучения на собранные солнечные элементы. Указанные изменения считают результатом взаимодействия красителя и электролита с прозрачным электродом. Среди исследованных элементов электроды AZO-A с сочетанием электролита KI и красителя EY, а также электроды AZO-S с сочетанием электролита KI и красителя Ru проявляли улучшенные эксплуатационные характеристики по сравнению с электродами ITO.
Список литературы
Grätzel, M., Dye-sensitized solar cells, Inorg. Chem., 2005, vol. 44, p. 6841.
Kavan, L., Electrochemistry and dye-sensitized solar cells, Curr. Opin. Electrochem., 2017, vol. 2, p. 88.
Ooyama, Y. and Nagano, T., Dye-sensitized solar cells based on donor-π-acceptor fluorescent dyes with a pyridine ring as an electron-withdrawing-injecting anchoring group, S. Inoue and I. Imae, Chem.–A Eur. J., 2011, vol. 17, p. 14837.
Freitag, M. and Boschloo, G., The revival of dye-sensitized solar cells, Curr. Opin. Electrochem., 2017, vol. 2, p. 111.
Longo, C. and De Paoli, M.A., Dye-Sensitized Solar Cells: A Successful Combination of Materials, J. Brazilian Chem. Soc., 2003, vol. 14, p. 889.
Bella, F., Lamberti, A., Bianco S., and Tresso, E., Floating, flexible polymeric dye-sensitized solar-cell architecture: the way of near-future photovoltaics, Adv. Mater. Technol., vol. 1.
Joshi, P.H., Korfiatis, D.P., Potamianou, S.F., and Thoma, K.-A.T., Selected parameters leading to an optimized DSSC performance, Russ. J. Electrochem., 2013, vol. 49, p. 628. [Джоши П.Х., Корфиатис Д.П., Потамьяноу С.Ф., Тома-К.А.Т., Избранные параметры, определяющие оптимальную работу электрохимической солнечной батареи с красителем-сенсибилизатором. Электрохимия, 2013. Т. 49. С. 706.]
Joshi, P.H., Korfiatis, D.P., Potamianou, S.F., and Thoma, K.-A.T., Oxide thickness and roughness factor as parameters for TiO2-dye sensitized solar cells performance, Russ. J. Electrochem., 2011, vol. 47, p. 517. [Джоши П.Х., Корфиатис Д.П., Потамиану С.Ф., Тома К.-А.Ф. Толщина оксида и фактор шероховатости как характеристические параметры работы солнечных батарей на основе tio2, сенсибилизированного красителем. Электрохимия. 2011. Т. 47. С. 552.]
Bella, F., Verna, A., and Gerbaldi, C., Patterning dye-sensitized solar cell photoanodes through a polymeric approach: A perspective, Mater. Sci. Semicond. Process., 2018, vol. 73, p. 92.
Galliano, S., Bella, F., Piana, G., and Giacona, G., Finely tuning electrolytes and photoanodes in aqueous solar cells by experimental design, Sol. Energy, 2018, vol. 163, p. 251.
Edwards, P.P., Porch, A., Jones, M.O., and Morgan, D.V., Basic materials physics of transparent conducting oxides, Dalt. Trans., 2004, p. 2995.
Kavan, L., Yum, J.H., and Graetzel, M., Graphene-based cathodes for liquid-junction dye sensitized solar cells, Electrochim. Acta, 2014, vol. 128, p. 349.
Wang, X., Zhi, L., and Müllen, K., Transparent, conductive graphene electrodes for dye-sensitized solar cells, Nano Lett., 2008, vol. 8, p. 323.
Hong, W., Xu, Y., Lu, G., and Li, C., Transparent graphene/PEDOT–PSS composite films as counter electrodes of dye-sensitized solar cells, Electrochem. commun., 2008, vol. 10, p. 1555.
Huang, Z., Liu, X., Li, K., and Li, D., Application of carbon materials as counter electrodes of dye-sensitized solar cells, Electrochem. commun., 2007, vol. 9, p. 596.
Lee, W.J., Ramasamy, E., Lee, D.Y., and Song, J.S., Performance variation of carbon counter electrode based dye-sensitized solar cell, Sol. Energy Mater. Sol. Cells, 2008, vol. 92, p. 814.
Agrell, H.G., Lindgren, J., and Hagfeldt, A., Degradation mechanisms in a dye-sensitized solar cell studied by UV–VIS and IR spectroscopy, Sol. Energy, 2003, vol. 75, p. 169.
Syrrokostas, G., Siokou, A., Leftheriotis, G., and Yianoulis, P., Degradation mechanisms of Pt counter electrodes for dye sensitized solar cells, Sol. Energy Mater. Sol. Cells, 2012, vol. 103, p. 119.
Manor, A., Katz, E.A., Tromholt, T., and Krebs, F.C., Electrical and Photo-Induced Degradation of ZnO Layers in Organic Photovoltaics, Adv. Energy Mater., 2011, vol. 1, p. 836.
Kato, N., Takeda, Y., Higuchi, K., and Takeichi, A., Degradation analysis of dye-sensitized solar cell module after long-term stability test under outdoor working condition, Sol. Energy Mater. Sol. Cells, 2009, vol. 93, p. 893.
Hinsch, A., Kroon, J.M., Kern, R., and Uhlendorf, I., Long-term stability of dye-sensitised solar cells, Prog. Photovoltaics Res. Appl., 2001, vol. 9, p. 425.
Sommeling, P.M., Späth, M., Smit, H.J.P., and Bakker, N.J., Long-term stability testing of dye-sensitized solar cells, J. Photochem. Photobiol. A Chem., 2004, vol. 164, p. 137.
Bella, F., Popovic, J., Lamberti, A., and Tresso, E., Interfacial effects in solid–liquid electrolytes for improved stability and performance of dye-sensitized solar cells, ACS Appl. Mater. Interfaces, 2017, vol. 9, p. 37797.
Lu, S., Yang, H., Li, F., and Wang, Y., Element substitution of kesterite Cu2ZnSnS4 for efficient counter electrode of dye-sensitized solar cells, Sci. Rep., 2018, vol. 8, p. 8714.
Boxman, R.L., Zhitomirsky, V., Alterkop, B., and Gidalevich, E., Recent progress in filtered vacuum arc deposition, Surf. Coatings Technol., 1996, vol. 86, 243.
Sharma, R., Amit, K., Barhai, P.K., and Boxmann, R.L., Evaluating the Performance of Dye-Sensitized Solar Cell with Various Key Components such as Electrodes, Dyes, and Electrolytes, Lecture Notes in Electrical Engineering, 2017, vol. 403, p. 371.
Fallah, H.R., Ghasemi varnamkhasti, M., and Vahid, M.J., Substrate temperature effect on transparent heat reflecting nanocrystalline ITO films prepared by electron beam evaporation, Renew. Energy, 2010, vol. 35, p. 1527.
Raoufi, D., Kiasatpour, A., Fallah, H.R., and Rozatian, A.S.H., Surface characterization and microstructure of ITO thin films at different annealing temperatures, Appl. Surf. Sci., 2007, vol. 253, p. 9085.
Fallah, H.R., Ghasemi, M., and Hassanzadeh, A., Influence of heat treatment on structural, electrical, impedance and optical properties of nanocrystalline ITO films grown on glass at room temperature prepared by electron beam evaporation, Phys. E Low-Dimensional Syst. Nanostructures, 2007, vol. 39, p. 69.
Park, Y.S. and Kim, H.K., Characteristics of sputtered Al-doped ZnO films for transparent electrodes of organic thin-film transistor, Thin Solid Films, 2011, vol. 519, p. 8018.
Tvarozek, V., Novotny, I., Sutta, P., and Flickyngerova, S., Influence of sputtering parameters on crystalline structure of ZnO thin films, Thin Solid Films, 2007, vol. 515, p. 8756.
van der PAUW, L.J., A method of measuring specific resistivity and hall effect of discs of arbitrary shapes, Semiconductor Devices: Pioneering Papers, 1958, vol. 13, p. 1.
Дополнительные материалы отсутствуют.