Электрохимия, 2020, T. 56, № 2, стр. 158-166
Электрохимическое поведение анодов твердооксидных топливных элементов на основе (Fe,Ni)Ox в метан-содержащих атмосферах
В. А. Колотыгин a, *, А. И. Иванов a, Д. В. Матвеев a, С. И. Бредихин a, В. В. Хартон a
a ИФТТ РАН
142432 Московской обл., Черноголовка, ул. академика Осипьяна, 2, Россия
* E-mail: kolotygin@issp.ac.ru
Поступила в редакцию 10.10.2018
После доработки 19.01.2019
Принята к публикации 13.06.2019
Аннотация
Работа посвящена исследованию электрохимического поведения композитных анодов на основе (Fe,Ni)Ox в водороде и метан-содержащем топливе. Среди изученных композитов лучшие электрохимические характеристики наблюдались для анодов при соотношении Fe : Ni около 2. В частности, для электродов исходного состава 50 об. % Fe0.67Ni0.33Oх–50 об. % Zr0.85Y0.15O1.93 (8YSZ) при токах 50–80 мА/см2 величина анодного перенапряжения составляет 20–30 мВ в 10% Н2–Ar–H2O при сравнительно низких температурах (873–923 К). Увеличение тока приводит к дальнейшей активации, предположительно связанной с частичным окислением металлических частиц на поверхности. Однако существенной проблемой остается микроструктурная деградация анодных слоев. Испытания электрокаталитической активности на анодах, изготовленных из Ni, Zr0.83Sc0.17O1.92 (ScSZ) и Ce0.9Gd0.1O2 – δ (GDC), продемонстрировали высокую активность к каталитическому парциальному окислению метана с последующим электрохимическим окислением продуктов конверсии, а также образование углеродистого осадка на поверхности никеля. Конверсия метана на никелевом аноде составляет 60–90% и уменьшается со временем или при охлаждении. Допирование оксида никеля железом снижает степень конверсии и повышает уровень зауглераживания, предположительно из-за снижения плотности анодного тока в результате уменьшения электрохимической активности.
ВВЕДЕНИЕ
В связи с необходимостью снижения рабочей температуры твердооксидных топливных элементов (ТОТЭ), переходом на анод-поддерживающие конструкции, а также при возможном наличии монооксида углерода или углеводородов в топливе, в последние годы проводится оптимизация состава и технологии изготовления анодных слоев. Важными направлениями таких разработок являются модификация состава и морфологии композиционных порошков [1–5], изменение условий спекания [6, 7], введение каталитически активных компонентов [8, 9], частичное или полное замещение никеля другой металлической или оксидной фазой, снижающей риск деградации в углеводородном топливе или при окислении [10, 11]. В ряде работ было показано, что композиты на основе никель-содержащих биметаллических сплавов и оксидов характеризуются улучшенными функциональными свойствами по сравнению с аналогами, в которых никель не замещен [12–14]. Например, замещение ~10 мол. % никеля в NiO железом приводило к увеличению удельной мощности модельных ячеек ТОТЭ [15] и снижению анодного перенапряжения при низкотемпературном разложении воды [16]. Кроме того, композиты на основе (Fe,Ni)Ox обладают повышенной каталитической активностью при парциальном окислении углеводородов [17] или метанировании СО [18].
Механизм указанных эффектов на сегодняшний день полностью не изучен. Известно, что в умеренно восстановительных условиях, когда парциальное давление кислорода (р(О2)) составляет около 10–16 атм при 1173 К, происходит образование оксида FeO с достаточно высокой удельной электропроводностью (210 См/см при 1273 К), на несколько порядков превышающей проводимость NiO [19, 20]. По сравнению с никелем, железо способно аккумулировать большее количество поверхностных атомов кислорода, способных выступать в качестве центров селективной адсорбции для водорода и других молекул топлива, что способствует повышенной скорости электрохимических процессов, протекающих по так называемому “oxygen spillover” механизму [21–23]. Известны также каталитические свойства фазы Fe2NiO4 со структурой шпинели [24–26], образование которой наблюдалось при синтезе биметаллических композитов состава FeOx–NiO [27].
Данная работа является продолжением нашего исследования биметаллических анодов на основе (Fe,Ni)Oх. В предыдущей работе [28] было показано, что при умеренном восстановлении шпинели образуется смесь состава (Fe,Ni)3O4–(Fe,Ni)O–металл Fe–Ni. Доля биметаллической фазы составила 10–30%; при этом никель на поверхности оксидов выделяется в форме субмикронных частиц с высокой удельной поверхностью. Поляризационное сопротивление анодов на основе Fe2NiO4–Zr0.85Y0.15O1.93 (8YSZ) при нулевом токе составило ~1.8 Ом см2, что может быть обусловлено низкой температурой (873 К) и низким содержанием водорода в топливной смеси (4%). Настоящая работа посвящена изучению электрохимического поведения анодов при протекании анодной реакции, а также исследованию способности окисления углеводородного топлива.
ЭКСПЕРИМЕНТАЛЬНАЯ ЧАСТЬ
Синтез материалов проводился глицин-нитратным способом из Ni(NO3)2 ∙ 6H2O, FeC2O4 ∙ 2H2O и глицина. Детали синтеза приведены в работе [28]. Изучение фазового состава осуществлялось при помощи рентгенофазового анализа (РФА), с использованием дифрактометра D-500-Braun X02-1787 (Siemens, Германия, CuKα-излучение). Микроструктурный анализ порошков и электродных слоев, а также элементный анализ, проводился с использованием сканирующего электронного микроскопа высокого разрешения Supra 50VP (LEO Carl Zeiss, Германия), снабженный приставкой для рентгеноспектрального микроанализа.
Для измерений электродной поляризации в водород-содержащих атмосферах использовался 3-электродный метод с использованием потенцио-/гальваностата Autolab 302 N PGSTAT (Metrohm Autolab, Нидерланды). Процедуры измерений и схема измерительной ячейки описаны в [29]. В качестве электролита использовалась мембрана 8YSZ (диаметр 20 мм, толщина 1.5 мм). Для изготовления электродных паст порошок (Fe,Ni)Ox был смешан с 8YSZ в объемном соотношении 50% : 50% (в соответствии с [28]) c последующей гомогенизацией в шаровой мельнице. Затем к композиту было добавлено связующее Heraeus V-006A (Германия) до достижения массового соотношения 1 : 1, после чего контейнер со смесью помещался в планетарный миксер ARE-250 (Thinky, Япония). Нанесение полученной пасты осуществлялось с использованием лабораторной установки для трафаретной печати. Паста наносилась на одну сторону мембраны через трафарет в форме полукруга (диаметр 15 мм), после чего следовал отжиг на воздухе при 1523 К. Платина, используемая в качестве противоэлектрода и электрода сравнения, наносилась с использованием пасты Heraeus CL11-5100 (Германия). В качестве токосъема с рабочего электрода и противоэлектрода использовалась платиновая сетка. Измерения проводились в увлажненной смеси 10% Н2–Ar.
Испытания электрокаталитических свойств проводились на модельной ячейке с Zr0.83Sc0.17O1.92 (ScSZ) в качестве электролита (диаметр 20 мм, толщина 0.5 мм), (La,Sr)MnO3 – δ (LSM) в качестве катода и анодом Ni-ScSZ–Ce0.9Gd0.1O2 – δ (GDC) или (Fe,Ni)Ox–YSZ, нанесенным вышеуказанным способом. Пример микроструктуры анодных слоев представлен на рис. 1а–1г). Для обеспечения надежного контакта с токосъемом (Pt-сетка) на катод и анод непосредственно на этапе сборки ячейки были нанесены пасты на основе La0.8Sr0.2MnO3 – δ и никеля, соответственно; методика их изготовления и нанесения описана ранее [30].
Схема стенда для каталитических испытаний представлена на рис. 2. Топливная смесь, полученная путем смешения потоков H2–Ar, CH4–Ar и Ar, предварительно пропускалась через осушитель и подавалась в анодное пространство. Электрическая нагрузка на ячейку осуществлялась при помощи потенцио-/гальваностата Autolab 302 N PGSTAT в гальваностатическом режиме, который обеспечивал постоянный поток ионов кислорода на анод. Из анодного пространства отработанный газ поступал в газовый хроматограф “Хроматэк-Кристалл 5000.2”, оснащенный двумя колонками (Hayesep R и NaX 80/100) и детекторами теплопроводности. В качестве газа-носителя использовались высокочистый аргон и гелий. Данная конфигурация хроматографа позволяет разделять и определять H2 и CO2 при их содержании не менее 0.005%, а также СН4 и СО при содержании не менее 0.1%. Примеры хроматограмм, полученных для каждой из колонок, представлены на рис. 3. Калибровка хроматографа по указанным газам проводилась по 3–5 искусственным поверочным смесям “Линде-Газ”, а также при помощи модифицированного электрохимического метода, предложенного в [31].
Рис. 2.
Схема лабораторного стенда для испытаний анодов ТОТЭ в углеводородном топливе с хроматографическим мониторингом продуктов. Цифрами на схеме обозначены: 1, 2, 3 – регуляторы газового потока; 4 – осушитель; 5 – ячейка для электрохимичеких испытаний; 6 – печь сопротивления; 7 – мембранно-электродный блок; 8 – потенцио-гальваностат; 9 – газовый хроматограф; 10 – камера с термогигрометром; 11 – мыльно-пленочный расходомер.
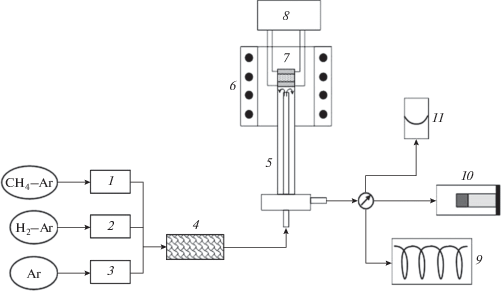
Рис. 3.
Примеры хроматограмм, полученных при электрохимическом окислении метан-содержащего топлива. При анализе в качестве газа-носителя использовался гелий (а) и аргон (б). Вставка на рис. 3б соответствует увеличению выделенной области.
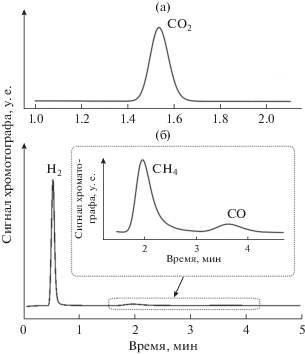
Для контроля содержания воды анализируемая газовая смесь поступала в герметичную камеру, оснащенную термогигрометром “Микрофор ИВА-6”. Для предотвращения пересыщения газовой смеси парами воды и их последующей конденсации на стенках газовой линии, испытания проводились на предварительно осушенной газовой смеси. Скорость потока используемых газов контролировалась при помощи регуляторов “Bronkhorst” (Нидерланды), откалиброванных по соответствующим газовым смесям с использованием лабораторного мыльно-пленочного расходомера, принцип работы которого описан в [32, 33]. Отдельные испытания продемонстрировали, что погрешность определения потоков и уровень их колебаний со временем не превышает 3–5% при параметрах, используемых в данной работе. Также мыльно-пленочный расходомер применялся для определения скорости потока газовой смеси, выходящей из электрохимической ячейки.
РЕЗУЛЬТАТЫ И ОБСУЖДЕНИЕ
Испытания фазовой и структурной стабильности, проведенные в работе [28], показали, что материалы Fe1 – γNiγOх до γ = 0.33 могут быть получены практически без примесей путем контроля содержания кислорода в газовой среде. Исходя из фазовой диаграммы [34], фаза номинального состава Fe0.1Ni0.9Oх со структурой вюстита стабильна лишь при температурах выше 1573 К. Это подтверждается результатами РФА (рис. 4a), на которых можно наблюдать сосуществование оксида на основе NiO и шпинели, в приблизительном соотношении 85 мас. % : 15 мас. %. Содержание последней снижается при восстановлении в аргоне до ~10 мас. %, однако достичь полной однофазности материала с γ = 0.9 не удалось, поэтому дальнейшие испытания проводились для композитной системы (Fe,Ni)3O4–(Fe,Ni)O с суммарным соотношением Fe : Ni = 1 : 9. В то время как для материалов с содержанием никеля до 33% при отжиге в 4% Н2–Ar–H2O при 1023 К доля образованной фазы Fe3Ni не превышает 30–40% [28], для Fe0.1Ni0.9Oх происходит практически полное восстановления до металлической фазы, несмотря на более низкую температуру отжига (рис. 4в).
Рис. 4.
Рентгенограммы Fe0.1Ni0.9Ox после синтеза на воздухе (а), отжига в аргоне (б) и в увлажненной смеси 4% H2–Ar (в). Для сравнения приведены дифрактограммы однофазных порошков Fe0.67Ni0.33Ox (г) и Fe0.87Ni0.13Ox (д), полученные в работе [28].
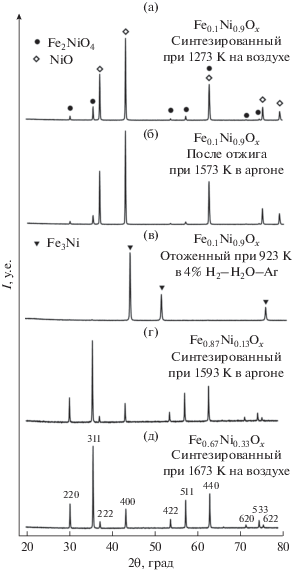
Примеры поляризационных кривых для анодов (Fe,Ni)Ox–8YSZ, полученных в 10% Н2–Н2О–Ar при 873–898 К, представлены на рис. 5. При малых токах наблюдается активационное поведение, характерное для процессов, лимитируемых процессом переноса заряда [35, 36]. Моделирование с помощью уравнения Тафеля (η = = Aln(i/i0), где i0 соответствует так называемому току обмена, А – константа) недостаточно адекватно описывает экспериментальные точки, что предполагает более сложный механизм. В частности, дополнительная активация может быть обусловлена локальным окислением поверхности зерен никеля при анодной поляризации. Тот же эффект может быть причиной резкого снижения перенапряжения при сравнительно высоких токах (рис. 5б). Указанное наблюдение согласуется с механизмом, предложенном в работах [21, 23, 37], при котором в электрохимическом процессе принимают участие атомы кислорода, поступающие на 3-фазную границу из электролита, связанные с атомами металла и представляющими собой центры селективной адсорбции для водорода из газовой фазы.
Рис. 5.
Поляризационные кривые, полученные для анодов (Fe,Ni)Ox–8YSZ (50–50 об. %) в увлажненном топливе 10% H2–Ar при 873 и 898 К. Пунктирные линии соответствуют результатам регрессионного анализа в соответствии с уравнением Тафеля.
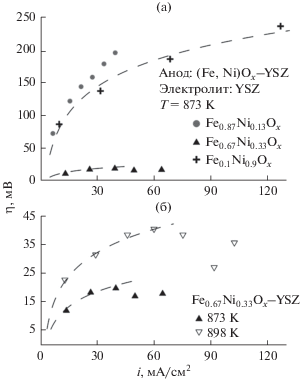
Среди изученных анодов, оптимальные характеристики были достигнуты для композита на основе Fe0.67Ni0.33Oх, что несколько отличается от результатов, полученных в [15]. Для анода Fe0.87Ni0.13Oх–YSZ наблюдалась крайне низкая электрохимическая активность, несмотря на более высокую электронную проводимость [28]. Это показывает, что для изучаемой системы транспортные свойства электрон-проводящей фазы оказывают существенно меньшее влияние на электрохимическое поведение, которые в большей степени определяются другими факторами, такими как микроструктура, фазовая и морфологическая устойчивость по отношению к окислению. Повышенная активность анода с γ = = 0.33 по сравнению с композитом на основе Fe0.1Ni0.9Ox может быть связана с более высоким сродством железа к кислороду, а также каталитическими особенностями фаз на основе (Fe,Ni)O и Fe2NiO4, существование которых в анодных условиях было показано ранее [28]. В частности, при токах 50–80 мА/см2 величина перенапряжения на аноде Fe0.67Ni0.33Oх–YSZ составляет 20–30 мВ, в то время как поляризационное сопротивление не превышает 0.8–1.2 Ом см2 (рис. 6) и существенно уменьшается при повышении тока. Учитывая низкую температуру испытаний и сравнительно малое содержание водорода в топливной смеси, наблюдаемый уровень активности вполне сопоставим со стандартными анодами с более высоким содержанием никеля [38, 39], однако существенной проблемой композитов (Fe,Ni)Ox–YSZ по-прежнему остается микроструктурная деградация при более высоких температурах.
Рис. 6.
Примеры годографов импеданса для анода Fe0.67Ni0.33Ox–YSZ (50–50 об. %) в увлажненном топливе 10% H2–Ar при 873 К. Числами возле точек обозначены соответствующие частоты.
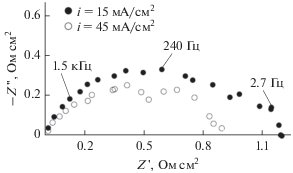
Испытания каталитической активности в метан-содержащей смеси были проведены на композитных анодах Fe0.67Ni0.33Ox–8YSZ и Fe0.1Ni0.9Oх–8YSZ. Для сравнения, аналогичные испытания были проведены на анодах Ni–ScSZ–GDC, для которых хорошо изучены проблемы зауглераживания [12, 38], а также на платиновых электродах. Для проверки герметичности газовых соединений измерительного стенда, включая качество герметизации электрохимической ячейки, а также адекватности калибровки хроматографа, проводилась предварительная проверка материального баланса по кислороду и водороду после электрохимического окисления смеси H2–Ar. Очевидно, что при адекватном функционировании системы, степень превращения водорода и, следовательно, скорость его потока на выходе из ячейки подчиняется закону Фарадея:
(1)
$U\left( {{{{\text{H}}}_{2}}} \right) = {{U{{{\left( {{{{\text{H}}}_{2}}} \right)}}_{0}} - i} \mathord{\left/ {\vphantom {{U{{{\left( {{{{\text{H}}}_{2}}} \right)}}_{0}} - i} {2F}}} \right. \kern-0em} {2F}},$(2)
$U{{\left( {{{{\text{H}}}_{2}}} \right)}_{{{\text{g}}{\text{. c}}}}} = {{{\omega }}_{{{{{\text{H}}}_{2}}}}} \times {{{{U}_{{{\text{tot}}}}}} \mathord{\left/ {\vphantom {{{{U}_{{{\text{tot}}}}}} {100}}} \right. \kern-0em} {100}},$(3)
$U{{\left( {{{{\text{H}}}_{2}}} \right)}_{{{\text{hum}}}}} = U{{\left( {{{{\text{H}}}_{{\text{2}}}}} \right)}_{0}} - {{U}_{{{\text{tot}}}}} \times {{{{{\omega }}_{{{{{\text{H}}}_{{\text{2}}}}{\text{O}}}}}} \mathord{\left/ {\vphantom {{{{{\omega }}_{{{{{\text{H}}}_{{\text{2}}}}{\text{O}}}}}} {100}}} \right. \kern-0em} {100}},$Рис. 7.
Зависимости скорости потока водорода из электрохимической ячейки, полученные с использованием закона Фарадея (уравнение (1)), данных газового хроматографа (уравнение (2)) и показаний термогигрометра (уравнение (3)).
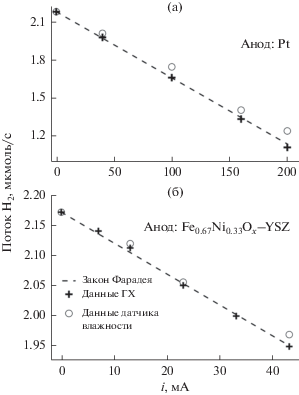
На рис. 8 представлена токовая зависимость распределения продуктов при электрохимическом окислении смеси H2–CH4–Ar (2–2.5 – ост. %) на аноде на основе никелевого композита. Образование СО и увеличение концентрации водорода при прохождении через ячейку, наблюдаемое в том числе и при отсутствии тока, предполагает значительную роль парциального окисления метана в анодной реакции. Конверсия метана составляет 60–90% и слабо зависит от силы тока (рис. 9а), т.е., потока кислорода на анод, однако последний параметр значительно влияет на соотношение продуктов окисления (Н2, СО, СО2, Н2О). Исходя из наблюдаемого поведения, можно предположить, что метан подвергается преимущественно неэлектрохимическому парциальному окислению на поверхности никелевого композита:
где (О) соответствует молекуле кислорода в газовой фазе или кислородному атому на поверхности анода. В свою очередь, ионы кислорода, поступающие к аноду через электролит, участвуют в процессе окисления продуктов:(6)
${{{\text{Н}}}_{{\text{2}}}} + {{{\text{О}}}^{{2 - }}} = {{{\text{Н}}}_{{\text{2}}}}{\text{О}} + 2{\text{е}}.$Рис. 8.
Зависимости концентрации продуктов электрохимического окисления смеси H2–CH4–Ar (2.5–2 – ост. %) на аноде Ni–ScSZ–GDC от силы тока при 1073 К.
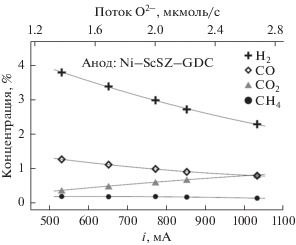
Рис. 9.
Зависимости степени конверсии метана от тока при электрохимическом окислении смеси H2‒CH4–Ar (2.5–2 – ост. %) на анодах Ni–ScSZ–GDC (а) и (Fe,Ni)Ox–8YSZ (б).
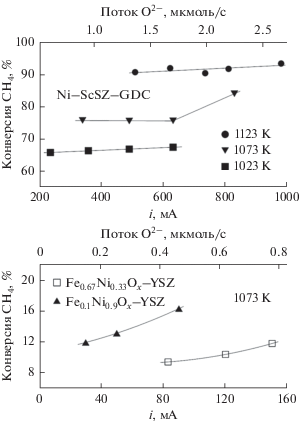
Учитывая незначительное содержание окислителей в топливной смеси и высокую склонность никелевых катализаторов к зауглераживанию, можно также предположить параллельный механизм, включающий пиролиз метана с образованием углеродистых осаждений. На возможное зауглераживание указывает существенное отклонение между содержанием углерода и водорода во входящей и выходящей смеси (рис. 10), существенно превышающее погрешности анализа, а также наличие углерода в анодном слое (табл. 1). Содержание углерода уменьшается от границы анода с газовой фазой к поверхности анод/электролит, вероятно, вследствие медленной диффузии метана в порах электродного слоя и повышенному химическому потенциалу кислорода вблизи электролита, предотвращающем зауглераживание.
Рис. 10.
Зависимость суммарного содержания углерода (а) и водорода (б) во входящей и выходящей из анодного пространства газовой смеси, от концентрации метана в топливе, полученном смешением потоков 4% H2–Ar и 7% CH4–Ar при постоянном токе 290 мА. Испытания проводились на аноде Ni–ScSZ–GDC при 1073 К.
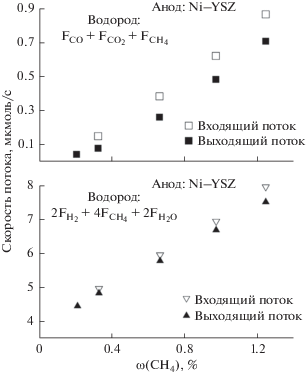
Таблица 1.
Результаты элементного анализа, проведенного в зонах 1–4 на рис. 1б. Результаты приведены в атомных процентах; содержание кислорода опущено
Зона | C | Sc | Ni | Zr | Ce | Gd |
---|---|---|---|---|---|---|
1 | 11.5 | – | 20.9 | – | 10.1 | 1.0 |
2 | 8.1 | – | 26.5 | 0.5 | 13.8 | 1.2 |
3 | 4.4 | 0.9 | 15.4 | 10.2 | 8.5 | 0.7 |
4 | – | 2.6 | – | 23.0 | – | – |
Несмотря на более сильную окисленность поверхности, конверсия метана на анодах (Fe,Ni)Oх–YSZ составила лишь 10–20%. Увеличение содержания железа снижает степень конверсии, предположительно из-за ухудшения каталитических свойств или деградации анодного слоя. В частности, микроскопический анализ обнаружил наличие крупных пор и полостей в анодном слое (рис. 1г), что способствует снижению электрохимической активности и увеличению скорости деградации. Из-за недостаточной активности анода в метан-содержащей атмосфере достичь высоких токов не удалось, что затрудняет расчет материального баланса, поскольку погрешности измерения и скорость деградации превышают изменения концентраций газовых компонентов, вызванные увеличением силы тока. Незначительное содержание СО на выходе предполагает доминирование полного окисления метана: данное наблюдение согласуется с активностью железосодержащих катализаторов при окислении СО [40, 41]. Уровень зауглераживания для Fe0.1Ni0.9Ox оказался даже выше по сравнению с никелевым композитом; в частности, в некоторых зонах анодного слоя, подвергнутого испытаниям в топливе H2–CH4–Ar (2–2.5 – ост. %), содержание углерода составило ~30%, что существенно превышает данные, приведенные в табл. 1. На микрофотографии (рис. 1д) вблизи границы анод/электролит наблюдаются игольчатые осаждения, типичные для углеродистых осадков [11, 42]. Повышенная склонность к зауглераживанию также может быть связана с наличием крупных пор и полостей в анодном слое Fe0.1Ni0.9Ox, облегчающих доступ метана, а также низкими значениями тока, проходящего через ячейку. Последний фактор обуславливает недостаточный уровень кислородного химического потенциала, что способствует зарождению углеродистого осадка. Таким образом, для достижения более высокой эффективности анодов (Fe,Ni)Ox и более адекватного анализа влияния состава анода на его каталитические свойства требуется микроструктурная оптимизация с учетом возможных фазовых превращений материала.
ЗАКЛЮЧЕНИЕ
Композитные аноды на основе Fe0.67Ni0.33Ox–YSZ проявляют высокий уровень электрохимической активности, в то время как величина перенапряжения уменьшается при сравнительно высоких токах. Данный феномен, не наблюдаемый для анодов с повышенным содержанием никеля, может быть связан со стабилизацией поверхностного кислорода вблизи атомов железа, а также наличием фаз (Fe,Ni)O и Fe2NiO4 в анодных условиях, с их возможным участием в электрохимическом процессе. Каталитическая активность при окислении метана уменьшается с повышением содержания железа, при этом возрастает селективность по отношению к глубокому окислению. Анализ продуктов окисления метан-водородной смеси на аноде Ni–ScSZ–GDC предполагает каталитическое окисление или пиролиз метана, с последующим участием компонентов образующегося синтез-газа в электрохимической реакции. Наибольшее содержание углеродистых осаждений наблюдалось для анода Fe0.1Ni0.9Ox–YSZ, что может быть обусловлено неоптимизированной микроструктурой анодного слоя.
Список литературы
Wood, T. and Ivey, D.G., The impact of redox cycling on solid oxide fuel cell lifetime, Solid Oxide Fuel Cell Lifetime and Reliability, Amsterdam, Elsevier Ltd., 2017, 51 p.
Chen-Wiegart, Y.-c.K., Kennouche, D., Cronin, J.S., Barnett, S.A., and Wang, J., Effect of Ni content on the morphological evolution of Ni–YSZ solid oxide fuel cell electrodes, Appl. Phys. Lett., 2016, vol. 108, p. 083903.
Buyukaksoy, A. and Birss, V.I., Highly active nanoscale Ni–Yttria stabilized zirconia anodes for micro-solid oxide fuel cell applications, J. Power Sources, 2016, vol. 307, p. 449.
Osinkin, D.A., Bogdanovich, N.M., Beresnev, S.M., and Zhuravlev, V.D., High-performance anode-supported solid oxide fuel cell with impregnated electrodes, J. Power Sources, 2015, vol. 288, p. 20.
Connor, P.A., Yue, X., Savaniu, C.D., Price, R., Triantafyllou, G., Cassidy, M., Kerherve, G., Payne, D.J., Maher, R.C., Cohen, L.F., Tomov, R.I., Glowacki, B.A., Kumar, R.V., and Irvine, J.T.S., Tailoring SOFC electrode microstructures for improved performance, Adv. Energy Mater, 2018, p. 1800120.
Dai, H., Chen, H., He, S., Cai, G., and Guo, L., Improving solid oxide fuel cell performance by a single-step co-firing process, J. Power Sources, 2015, vol. 286, p. 427.
Hedayat, N., Panthi, D., and Du, Y., Fabrication of anode-supported microtubular solid oxide fuel cells by sequential dip-coating and reduced sintering steps, Electrochim. Acta, 2017, vol. 258, p. 694.
Irvine, J.T.S., Neagu, D., Verbraeken, M.C., Chatzichristodoulou, C., Graves, C., and Mogensen, M.B., Evolution of the electrochemical interface in high-temperature fuel cells and electrolysers, Nature Energy, 2016, vol. 1, p. 1.
Chen, J., Bertei, A., Ruiz-Trejo, E., Atkinson, A., and Brandon, N.P., Characterization of degradation in nickel impregnated scandia-stabilize zirconia electrodes during isothermal annealing, J. Electrochem. Soc., 2017, vol. 169, p. F935.
Konar, R., Mukhopadhyay, J., Sharma, A.D., and Basu, R.N., Synthesis of Cu–YSZ and Ni–Cu–YSZ cermets by a novel electroless technique for use as solid oxide fuel cell anode: Application potentiality towards fuel flexibility in biogas atmosphere, Int. J. Hydrogen Energy, 2016, vol. 41, p. 1151.
McIntosh, S. and Gorte, R.J., Direct hydrocarbon solid oxide fuel cells, Chem. Rev., 2004, vol. 104, p. 4845.
Tsipis, E.V. and Kharton, V.V., Electrode materials and reaction mechanisms in solid oxide fuel cells: a brief review. III. Recent trends and selected methodological aspects, J. Solid State Electrochem., 2011, vol. 15, p. 1007.
Park, H.C. and Virkar, A.V., Bimetallic (Ni–Fe) anode-supported solid oxide fuel cells with gadolinia-doped ceria electrolyte, J. Power Sources, 2009, vol. 186, p. 133.
Gross, M.D., Vohs, J.M., and Gorte, R.J., Recent progress in SOFC anodes for direct utilization of hydrocarbons, J. Mater. Chem., 2007, vol. 17, p. 3071.
Kan, H. and Lee, H., Enhanced stability of Ni–Fe/GDC solid oxide fuel cell anodes for dry methane fuel, Catal. Commun., 2010, vol. 12, p. 36.
Landon, J., Demeter, E., İnoğlu, N., Keturakis, C., Wachs, I.E., Vasić, R., Frenkel, A.I., and Kitchin, J.R., Spectroscopic characterization of mixed Fe–Ni oxide electrocatalysts for the oxygen evolution reaction in alkaline electrolytes, ACS Catal., 2012, vol. 2, p. 1793.
Provendier, H., Petit, C., Estournès, C., Libs, S., and Kiennemann, A., Stabilisation of active nickel catalysts in partial oxidation of methane to synthesis gas by iron addition, Appl. Catal. A, 1999, vol. 180, p. 163.
Tian, D., Liu, Z., Li, D., Shi, H., Pan, W., and Cheng, Y., Bimetallic Ni–Fe total-methanation catalyst for the production of substitute natural gas under high pressure, Fuel, 2013, vol. 104, p. 224.
Кофстад, П. Отклонение от стехиометрии, диффузия и электропроводность в простых окислах металлов. M.: Миp, 1975. 400 c. [Kofstad, P., Nonstoichiometry, diffusion and electrical conductivity in binary metal oxides (in Russian), Moscow: Mir, 400 p.]
Третьяков, Ю.Д. Химия нестехиометрических оксидов. М.: Изд. ГУ, 1974. 364 с. [Tret’yakov, Yu.D., Chemistry of nonstoichiometric oxides (in Russian), M.: Publ. House of Moscow Univer. 364 p.]
Rossmeisl, J. and Bessler, W.G., Trends in catalytic activity for SOFC anode materials, Solid State Ionics, 2008, vol. 178, p. 1694.
An, W., Gatewood, D., Dunlap, B., and Turner, C.H., Catalytic activity of bimetallic nickel alloys for solid-oxide fuel cell anode reactions from density-functional theory, J. Power Sources, 2011, vol. 196, p. 4724.
Bredikhin, S.I., Agarkov, D.A., Aronin, A.S., Burmistrov, I.N., Matveev, D.V., and Kharton, V.V., Ion transfer in Ni-containing composite anodes of solid oxide fuel cells: A microstructural study, Mater. Lett., 2018, vol. 216, p. 193.
Benrabaa, R., Löfberg, A., Caballero, J.G., Bordes-Richard, E., Rubbens, A., Vannier, R.-N., Boukhlouf, H., and Barama, A., Sol–gel synthesis and characterization of silica supported nickel ferrite catalysts for dry reforming of methane, Catal. Commun., 2015, vol. 58, p. 127.
Pouran, S.R., Raman, A.A.A., and Daud, W.M.A., Review on the application of modified iron oxides as heterogeneous catalysts in Fenton reactions, J. Cleaner Production, 2014, vol. 64, p. 24.
Pereira, M.C., Oliveira, L.C.A., and Murad, E., Iron oxide catalysts: Fenton and Fenton-like reactions—a review, Clay Minerals, 2012, vol. 47, p. 285.
Ringuedé, A., Labrincha, J.A., and Frade, J.R., A combustion synthesis method to obtain alternative cermet materials for SOFC anodes, Solid State Ionics, 2001, vol. 141, p. 549.
Колотыгин, В.А., Носкова, В.А., Бредихин, С.И., Хартон, В.В. Окислительно-восстановительное поведение и транспортные свойства композитов на основе (Fe,Ni)3O4 ± δ для анодов твердооксидных топливных элементов. Электрохимия. 2018. Т. 54. С. 584. [Kolotygin, V.A., Noskova, V.A., Bredikhin, S.I., and Kharton, V.V., Redox behavior and transport properties of composites based on (Fe,Ni)3O4 ± δ for anodes of solid oxide fuel cells, Russ. J. Electrochem. (in Russian), 2018, vol. 54, p. 506.]
Kharton, V.V., Tsipis, E.V., Marozau, I.P., Viskup, A.P., Frade, J.R., and Irvine, J.T.S., Mixed conductivity and electrochemical behavior of (La0.75Sr0.25)0.95Cr0.5Mn0.5O3 – δ, Solid State Ionics, 2007, vol. 178, p. 101.
Матвеев, Д.В., Деменева, Н.В., Бредихин, С.И., Иванов, А.И., Хартон, В.В. Способ изготовления контактного электродного материала с контролируемой пористостью для батарей твердооксидных топливных элементов. Пат. 2568815 (Россия). 2014. [Matveev, D.V., Demeneva, N.V., Bredikhin, S.I., Ivanov, A.I., and Kharton, V.V., Method for manufacturing contact electrode material with controlled porosity for stacks of solid oxide fuel cells, Patent 2568815 (Russia), 2014.]
Колотыгин, В.А., Носкова, В.А., Хартон, В.В., Бредихин, С.И. Способ изготовления смесей для калибровки газоаналитического оборудования с использованием твердотельного электролизера. Патент 2661074 (Россия). 2017. [Kolotygin, V.A., Noskova, V.A., Kharton, V.V., and Bredikhin, S.I., Gas analytical equipment calibration mixtures manufacturing method using the solid state electrolysis cell, Patent 2661074 (Russia), 2017.]
Patterson, D. and Levine, N.A., Soap film flowmeter, US Patent 4879907, 1989.
Guo, J. and Heslop, M.J., Diffusion problems of soap-film flowmeter when measuring very low-rate gas flow, Flow Measurement and Instrumentation, 2004, vol. 15, p. 331.
Rhamdhani, M.A., Hayes, P.C., and Jak, E., Subsolidus phase equilibria of the Fe–Ni–O System, Metal. Mater. Trans. B, 2008, vol. 39B, p. 690.
Kawada, T., Sakai, N., Yokokawa, H., Dokiya, M., Mori, M., and Iwata, T., Structure and polarization characteristics of solid oxide fuel cell anodes, Solid State Ionics, 1990, vol. 40–41, p. 402.
Primdahl, S. and Mogensen, M., Gas conversion impedance: a test geometry effect in characterization of solid oxide fuel cell anodes, J. Electrochem. Soc., 1998, vol. 145, p. 2431.
Babaei, A., Jiang, S.P., and Li, J., Electrocatalytic promotion of palladium nanoparticles on hydrogen oxidation on Ni/GDC anodes of SOFCs via spillover, J. Electrochem. Soc., 2009, vol. 156, p. B1022.
Jiang, S.P. and Chan, S.H., A review of anode materials development in solid oxide fuel cells, J. Mater. Sci., 2004, vol. 39, p. 4405.
Tsipis, E.V., Kharton, V.V., Bashmakov, I.A., Naumovich, E.N., and Frade, J.R., Cellulose-precursor synthesis of nanocrystalline Ce0.8Gd0.2O2 – δ for SOFC anodes, J. Solid State Electrochem., 2004, vol. 8, p. 674.
Herzing, A.A., Kiely, C.J., Carley, A.F., Landon, P., and Hutchings, G.J., Identification of active gold nanoclusters on iron oxide supports for CO oxidation, Science, 2008, vol. 321, p. 1331.
Qiao, B., Wang, A., Yang, X., Allard, L.F., Jiang, Z., Cui, Y., Liu, J., Li, J., and Zhang, T., Single-atom catalysis of CO oxidation using Pt/FeOx, Nature Chem., 2011, vol. 3, p. 634.
Cimenti, M. and Hill, J.M., Direct utilization of liquid fuels in SOFC for portable applications: challenges for the selection of alternative anodes, Energies, 2009, vol. 2, p. 377.
Дополнительные материалы отсутствуют.