Электрохимия, 2021, T. 57, № 2, стр. 67-74
Влияние тонких функциональных слоев электродов на характеристики среднетемпературного твердооксидного топливного элемента
А. В. Шипилова a, А. А. Соловьев a, b, *, Е. А. Смолянский b, С. В. Работкин a, И. В. Ионов a
a Институт сильноточной электроники СО РАН
Томск, Россия
b Национальный исследовательский Томский политехнический университет
Томск, Россия
* E-mail: andrewsol@mail.ru
Поступила в редакцию 11.02.2020
После доработки 15.04.2020
Принята к публикации 11.06.2020
Аннотация
Тонкопленочная многослойная структура мембранно-электродного блока твердооксидного топливного элемента, включающая в себя NiO/ZrO2:Y2O3 анодный и La0.6Sr0.4CoO3 катодный функциональные слои, а также двухслойный ZrO2:Y2O3/Ce0.9Gd0.1O1.95 электролит, была сформирована методом магнетронного распыления на несущем NiO/ZrO2:Y2O3 аноде. Было изучено влияние функциональных слоев электродов, вводимых в структуру твердооксидного топливного элемента, на его производительность. Вольт-амперные характеристики многослойных топливных элементов были исследованы в диапазоне температур 800–600°C. Показано, что введение в структуру мембранно-электродного блока тонкого (толщиной 600 нм) катодного функционального слоя позволяет существенно повысить эффективность топливного элемента за счет снижения поляризационных потерь на электродах. Максимальная плотность мощности топливного элемента с катодным функциональным слоем составила 2290 и 500 мВт/см2 при температуре 800 и 600°С соответственно. Формирование и анодного, и катодного функциональных слоев нежелательно, так как приводит к диффузионным ограничениям на аноде.
ВВЕДЕНИЕ
Для повышения долговечности и надежности таких устройств, как твердооксидные топливные элементы (ТОТЭ), необходимо снижать их рабочую температуру при сохранении приемлемого уровня электрических характеристик. Для этой цели широко используется подход, основанный на снижении толщины электролита [1–3]. В этом направлении исследований наиболее популярна конструкция ТОТЭ с несущим анодом, которая позволяет формировать слои электролита в виде тонких пленок толщиной менее 10 мкм. Очевидным преимуществом формирования мембранно-электродного блока (МЭБ) ТОТЭ в виде тонкопленочной структуры является снижение омических потерь и, как результат, повышение эффективности устройства. Снижение рабочей температуры, в свою очередь, позволяет расширить список используемых для изготовления ТОТЭ материалов, снизить скорость их деградации, увеличить срок службы топливного элемента.
Однако снижение рабочей температуры влечет за собой ряд проблем. Одна из них связана с замедлением скорости протекания электрохимических реакций на электродах. Наиболее заметно это отражается на скорости реакции восстановления кислорода на катоде вследствие высокой энергии активации данного процесса. Поэтому очевидно, что необходимо повышать эффективность электродов с целью уменьшения их поляризационного сопротивления и улучшения характеристик ТОТЭ.
Повышение эффективности электродов может быть достигнуто за счет использования материалов, обладающих большей каталитической активностью в реакциях восстановления кислорода и окисления водорода [4–7], а также путем управления микроструктурой электродных слоев. Кроме наноструктурирования электрода [8, 9] эффективным является формирование многослойной (двух- или трехслойной) структуры электрода [10, 11]. Двухслойный электрод состоит из основного крупнопористого слоя, обеспечивающего свободную диффузию газа в рабочую зону, токосъем и удаление продуктов реакции из электрода, и мелкопористого, чаще наноструктурированного, функционального слоя. Последний отвечает за эффективность протекания электрохимических реакций.
Формирование анодного функционального слоя (АФС), примыкающего к электролиту, осуществляют с целью увеличения площади трехфазной границы и уменьшения активационной поляризации на аноде [10]. Такой слой также сглаживает поверхность анода, что облегчает формирование на нем тонкопленочного электролита. K. Chen с соавторами [12] показали, что нанесение АФС толщиной 5 мкм методом центрифугирования из суспензии (slurry spin coating method) позволило уменьшить размеры крупных пор на поверхности исходного анода (первоначальный размер пор до 20 мкм), и привело к формированию более мелкопористой поверхностной структуры анода. Это создало условия для последующего формирования газонепроницаемого слоя электролита меньшей толщины. В работе отмечается, что удалось снизить толщину электролита с 14 (для анода без функционального слоя) до 8 мкм. Вместе с тем авторами [12] показано, что толщина АФС оказывает существенное влияние на характеристики ТОТЭ. При этом существует оптимальная толщина, при которой характеристики ТОТЭ максимальны. Толщина меньше оптимальной не обеспечивает формирование газонепроницаемого электролита, а увеличение толщины АФС приводит к росту диффузионных ограничений на аноде. Очевидно, что оптимальная толщина АФС для каждого конкретного случая будет определяться структурой несущего анода и зависеть от метода формирования АФС.
В нашей предыдущей работе [13] нанопористый анодный NiO/ZrO2:Y2O3 функциональный слой наносился на несущие NiO/ZrO2:Y2O3-аноды методом реактивного магнетронного распыления. Так же как и в [12] было показано, что такой нанопористый анодный слой в структуре МЭБ выступает в роли выравнивающего переходного слоя между крупнопористым анодом и электролитом. Увеличение максимальной плотности мощности ТОТЭ с АФС толщиной 3 мкм, ZrO2:Y2O3 (YSZ) электролитом толщиной 5 мкм и La0.6Sr0.4Co0.2Fe0.8O3/CeO2:Gd2O3 (LSCF/GDC) катодом составило 15–25% в диапазоне рабочих температур 500–800°С. Близкое по величине увеличение мощности (около 15%) было получено в [12] при оптимальной толщине АФС 5 мкм.
Для повышения эффективности катода ТОТЭ осуществляют нанесение тонкого наноразмерного катодного функционального слоя (КФС) на поверхность основного катода ТОТЭ [14], либо формируют тонкий слой из катодного материала на границе между катодом и электролитом [11, 15, 16].
Как показали H.J. Choi и др. [14], модифицирование поверхности LSCF-катода путем осаждения на него La0.6Sr0.4CoO3 (LSC) слоя толщиной всего 1 нм позволяет увеличить плотность мощности ТОТЭ в 1.3 раза. Оптимизация толщины LSC-слоя привела к увеличению плотности мощности в 1.8 раз по сравнению с исходной. Ухудшение характеристик ТОТЭ с увеличением толщины этого слоя больше оптимальной (8 нм) авторы связывают с ростом сопротивления переносу заряда в объеме данного слоя.
Введение в структуру топливной ячейки тонкого (150–200 нм) LSCF функционального слоя между электролитом и катодом также приводит к повышению эффективности катода [11]. При этом электрохимические характеристики катода зависят от микроструктуры КФС. Формирование мезопористой наноразмерной структуры КФС позволяет снизить поляризационное сопротивление на границе раздела электролит/катод на 40%. Увеличение плотности мощности с 390 до 812 мВт/см2 при 700°C было достигнуто в результате нанесения нанокомпозитного LSC слоя толщиной 2 мкм между GDC-электролитом и LSC-катодом [15]. В нашей предыдущей работе [17] формирование функционального слоя LSC толщиной 600 нм на границе раздела электролит/катод привело к росту плотности мощности на 40 и 60% при 750 и 800°C соответственно. Кроме того, результаты, полученные N. Hildenbrand и др. [18], показывают, что введение в структуру МЭБ такого функционального слоя не только повышает эффективность катода, но и улучшает адгезию между электролитом и катодом. Это повышает механическую прочность топливной ячейки в целом.
Для формирования многослойной структуры МЭБ ТОТЭ используются такие методы, как золь–гель [9], импульсное лазерное осаждение [15], метод электрораспыления прекурсоров раствора [16], атомно-слоевое осаждение [14], магнетронное распыление [17] и другие. В [19] авторы использовали магнетронное распыление для формирования наноструктурного NiO/YSZ-анода толщиной 1.5 мкм и двухслойного YSZ/GDC- электролита с соответствующими толщинами слоев 600 и 150 нм, а также импульсное лазерное осаждение катодного слоя LSC. Напряжение разомкнутой цепи ТОТЭ составило 1.1 В, а максимальная плотность мощности при площади катода 16 см2 равнялась 1.2 Вт/см2 при 600°C. Эти результаты демонстрируют эффективность применения методов физического газофазного осаждения для изготовления ТОТЭ. Однако авторы указанной работы формулируют ряд проблем, требующих дополнительной проработки: осаждение покрытий сложного состава, в частности катодных материалов, необходимость увеличения скорости осаждения и улучшения адгезии слоев.
Таким образом, многочисленные исследования показали, что введение в структуру ТОТЭ тонких функциональных слоев анода или катода приводит к улучшению характеристик топливного элемента. Целью данной работы было выяснить, как изменятся характеристики ТОТЭ на несущем NiO/YSZ-аноде с двухслойным YSZ/GDC-электролитом, в структуру которого добавлены как функциональный (NiO/YSZ) анодный, так и функциональный (LSC) катодный слои, сформированные методом магнетронного распыления.
ЭКСПЕРИМЕНТАЛЬНАЯ ЧАСТЬ
В качестве основы для формирования тонкопленочной структуры МЭБ были использованы коммерческие NiO/YSZ-аноды (SOFCMAN, Китай) размером 100 × 100 мм и толщиной 0.4 мм, из которых вырезались образцы диаметром 20 мм. На рис. 1 показана микроструктура поперечного излома данного анода в восстановленном состоянии (снимок сделан вблизи поверхности образца). Данный снимок позволяет визуально оценить пористость и размер пор поверхностного слоя несущего электрода. Осаждение NiO/YSZ функционального слоя осуществлялось путем совместного реактивного магнетронного распыления металлических Ni- и Zr0.86Y0.14-мишеней, располагающихся под углом 45° к плоскости подложкодержателя. Подложки в процессе осаждения АФС нагревались до температуры 400°C. Полученные образцы отжигали на воздухе при 1200°С в течение 1 ч для предотвращения агломерации Ni в пленке при ее последующем использовании в атмосфере водорода. Содержание NiO в осажденных покрытиях составляло около 60 об. %. Подробно параметры осаждения NiO/YSZ-слоя были описаны в [13].
Последующее последовательное осаждение YSZ- и GDC-слоев электролита с соответствующими толщинами 4 и 2 мкм проводилось в реактивном режиме магнетронного распыления Zr0.86Y0.14- и Ce0.9Gd0.1-мишеней на подложки, нагретые до температуры 400°С. Режимы осаждения слоев двухслойного YSZ/GDC-электролита описаны в работе [3].
Формирование LSC функционального слоя осуществлялось в режиме импульсного магнетронного распыления La0.6Sr0.4CoO3-мишени (Nova Fabrica Ltd., Литва) диаметром 72 мм и толщиной 3 мм в атмосфере аргона. Распыляемая мишень располагалась под углом 75°–80° к подложке. Мощность разряда составляла 200 Вт, расстояние между подложкой и магнетроном – 50 мм [17].
Для измерения вольт-амперных характеристик (ВАХ) было изготовлено пять серий образцов единичных ТОТЭ. Образцы серии № 1 (без функциональных слоев электродов) состояли из несущего NiO/YSZ-анода, двухслойного YSZ/GDC-электролита и контактного катодного LSC-слоя, формируемого методом трафаретной печати из LSC-пасты (CERA-FC Co, Корея). Образцы серий № 2–4 в структуре МЭБ имели осажденные методом магнетронного распыления анодный и катодный функциональные слои. При этом толщина КФС во всех образцах была одинаковая и составляла 600 нм. Эта толщина была определена как оптимальная на основе ранее полученных результатов [17]. Толщина АФС варьировалась и составляла для разных серий образцов 0.5, 2 и 4 мкм. Образцы серии № 5 имели в структуре только катодный функциональный слой LSC толщиной 600 нм. Для каждой серии ТОТЭ было изготовлено и испытано как минимум 2 образца.
Исследование электрохимических характеристик топливных элементов осуществлялось на устройстве ProboStatTM (NorECs, Норвегия), схема которого приведена в [20]. Топливный элемент нагревался до температуры 800°С и выдерживался 1 ч при данной температуре. В это время происходило спекание катодного слоя. После этого подавались рабочие газы (водород и воздух), происходил процесс восстановления несущего анода и АФС в течениe 30–40 мин и начиналось измерение ВАХ. Исследование проводилось в диапазоне температур 600–800°С с интервалом 50°С.
Для изучения микроструктуры поперечного излома многослойной тонкопленочной структуры МЭБ и построения карты распределения элементов по сечению образца был использован сканирующий электронный микроскоп Quanta 200 3D (FEI Company, США) с приставкой для энергодисперсионной рентгеновской спектроскопии “EDAX”.
РЕЗУЛЬТАТЫ И ОБСУЖДЕНИЕ
Микроструктура поперечно излома ТОТЭ с несущим NiO/YSZ-анодом, многослойным тонкопленочным МЭБ, включающим в себя NiO/YSZ АФС, YSZ/GDC-электролит и LSC КФС, а также контактным катодным LSC-слоем, представлена на рис. 2.
Рис. 2.
Микроструктура поперечно излома топливного элемента с несущим NiO/YSZ-анодом, многослойным МЭБ, контактным LSC катодным слоем после электрохимических испытаний: (а) полная структура ТЭ, (б) и (в) увеличенные изображения КФС и АФС.
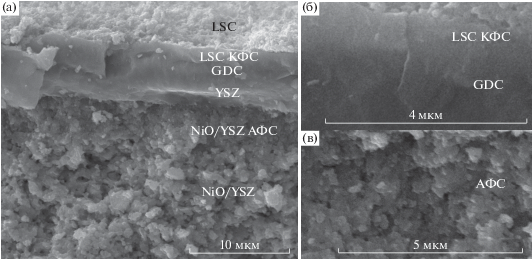
Из рис. 2а видно, что все слои ТЭ имеют хороший контакт друг с другом. Двухслойный электролит представляет собой плотный и однородный слой без расслаиваний. Граница между YSZ- и GDC-слоями слабо выражена. NiO/YSZ функциональный слой после восстановления в водороде приобрел нанопористую структуру с размерами пор около 100 нм. Гранулы АФС имеют хорошее сцепление как с NiO/YSZ несущим анодом, так и с YSZ-слоем. Осаждение наноструктурного NiO/YSZ-слоя на границе раздела анод/электролит должно привести к формированию более развитой трехфазной границы анод/электролит/топливо, поскольку размер пор и гранул у АФС значительно меньше, чем несущего анода (рис. 1в). Хорошая адгезия была получена также между LSC функциональным слоем и GDC-слоем электролита. Как видно из рис. 2б, граница между ними практически неразличима, что должно облегчать диффузию ионов кислорода через эти слои. Растрескивания или отслоения слоев друг от друга также не наблюдалось. LSC функциональный слой является достаточно плотным, что вполне допустимо вследствие его смешанной ионно-электронной проводимости. В работах [21–23] было показано, что даже плотные катоды, обладающие смешанной ионно-электронной проводимостью, могут обладать низким поляризационным сопротивлением.
В качестве дополнительной информации для исследуемых образцов с использованием метода энергодисперсионного анализа были получены карты распределения элементов по сечению многослойной структуры ТЭ. Результаты, представленные на рис. 3, вполне реалистично отображают распределение элементов по слоям МЭБ.
Рис. 3.
Карта распределения элементов по сечению ТЭ с многослойной тонкопленочной структурой (энергодисперсионная рентгеновская спектроскопия).
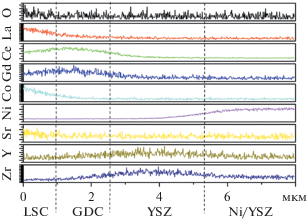
Для того чтобы выяснить влияние функциональных слоев электродов на характеристики ТОТЭ, были измерены ВАХ ТЭ с различной структурой. Результаты измерения плотности мощности ТЭ представлены в табл. 1. Видно, что введение в структуру МЭБ наноструктурных функциональных слоев электродов в некоторых случаях привело к улучшению производительности ТЭ. Наибольшие значения плотности мощности были получены для ТЭ № 2 (с АФС и КФС толщиной 500 и 600 нм, соответственно) и № 5 (с КФС толщиной 600 нм, соответственно). Максимальная плотность мощности ТЭ № 2 при температуре 800 и 600°С составила 1990 и 430 мВт/см2 соответственно. Максимальная плотность мощности ТЭ № 5 равнялась 2290 и 500 мВт/см2 при тех же температурах. У топливного элемента без функциональных электродных слоев плотность мощности при тех же условиях равнялась 1620 и 300 мВт/см2 соответственно. Таким образом, для ТЭ № 2 увеличение плотности мощности при температурах 800 и 600°С составило 23 и 43% относительно ТЭ № 1. Для ТЭ № 5 повышение мощности составило 41 и 67% в зависимости от температуры. Видно, что при меньших рабочих температурах эффект от функциональных слоев более выражен.
Таблица 1.
Результаты испытания ТОТЭ со структурой: несущий анод – NiO/YSZ, АФС – YSZ/GDC-электролит – LSC КФС и контактный слой LSC
№ серии ТЭ | Толщина функциональных слоев NiO/YSZ и LSC, нм |
Максимальная плотность мощности, мВт/см2 | ASR, Ом см2 при 800°С | ||||
---|---|---|---|---|---|---|---|
800°С | 750°С | 700°С | 650°С | 600°С | |||
1 | 0/0 | 1620 | 1320 | 970 | 600 | 300 | 0.15 |
2 | 500/600 | 1990 | 1650 | 1215 | 800 | 430 | 0.12 |
3 | 2000/600 | 1710 | 1560 | 1018 | 590 | 280 | 0.13 |
4 | 4000/600 | 1580 | 1264 | 870 | 550 | 261 | 0.15 |
5 | 0/600 | 2290 | 1920 | 1450 | 850 | 500 | 0.10 |
Из табл. 1 видно, что введение в структуру ТОТЭ двух функциональных слоев (анода и катода) приводит к меньшему увеличению плотности мощности, чем формирование одного катодного функционального слоя. Причем чем больше толщина АФС, тем меньше плотность мощности топливного элемента. С одной стороны, формирование нанопористого АФС за счет увеличения области трехфазной границы должно улучшать характеристики ТЭ. С другой стороны, такая нанопористая структура затрудняет подвод топлива в зону реакции, приводя к появлению диффузионных ограничений. При рабочей температуре 800°С скорости реакций на электродах высокие и через электролит проходит большой ток ионов. Газодиффузионное сопротивление, которое увеличивается на аноде после формирования функционального слоя, препятствует подводу необходимого количества топлива к трехфазной границе и ограничивает ток ТЭ. При снижении рабочей температуры до 600°С уменьшается как скорость реакции восстановления кислорода на катоде, так и проводимость электролита. Поэтому ток, протекающий через ТЭ, значительно снижается и подводимого к аноду топлива становится достаточно для протекания реакции окисления водорода. Это объясняет наибольшее увеличение плотности мощности ТЭ № 2 и № 5 по сравнению с ТЭ № 1 при низких температурах.
О наличии диффузионных потерь в ТОТЭ можно судить по форме вольт-амперных кривых. Как известно, в этом случае наблюдается быстрый спад кривой зависимости напряжения от тока в области больших токов. На рис. 4 приведены вольт-амперные и мощностные характеристики образцов ТОТЭ № 1, 2 и 5, полученные при рабочей температуре 800°С.
Рис. 4.
Вольт-амперные и мощностные характеристики ТЭ № 1 (1), № 2 (2) и № 5 (3), измеренные при температуре 800°С.
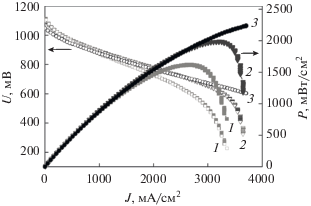
Из приведенных графиков видно, что диффузионные потери для ТЭ № 1 наблюдаются при плотности тока около 2.5 А/см2. У ТЭ № 2 диффузионные потери возникают при большей плотности тока (~3.25 А/см2). У ТЭ № 5 в диапазоне плотностей тока до 3.7 А/см2 диффузионных ограничений не наблюдается.
Все исследуемые ТОТЭ имели напряжение разомкнутой цепи в диапазоне от 1.048 до 1.1 B при температуре 800°С, что говорит о неплохой газонепроницаемости YSZ/GDC-электролита. Из табл. 1 видно, что ТЭ №№ 2 и 5 имеют наименьшие значения эквивалентного удельного сопротивления (ASR, area specific resistance), определяемого по наклону линейной части ВАХ. Самое низкое значение ASR (0.10 Ом см2) имеет ТОТЭ, в структуре которого имеется только катодный функциональный слой (№ 5). ASR включает в себя две составляющие, омическое сопротивление Rs и поляризационное сопротивление электродов Rp [24]. Первая составляющая определяется омическим сопротивлением электролита, электродов и токосъемов. Rs сильно зависит от толщины слоев и контакта между ними. Вторая составляющая, определяется скоростью химических и электрохимических процессов на поверхности электродов, внутри электродов и на границе электрод/электролит, а также скоростью диффузии газа внутри электродов.
Снижение эквивалентного удельного сопротивления ТЭ № 5 в 1.5 раза по сравнению с ТЭ № 1 объясняется, по-видимому, увеличением площади поверхности, через которую ионы кислорода внедряются в электролит. В случае пористого катода эта площадь ограничена местами контакта гранул катода с электролитом. В случае тонкопленочного плотного катода эта площадь составляет всю поверхность электролита, покрытую катодом.
Меньшие значения ASR ТЭ № 5 по сравнению с ТЭ № 2–4 можно объяснить увеличением поляризационного сопротивления анода у последних вследствие диффузионных ограничений, вызываемых наличием в структуре АФС.
Было проведено сравнение значений плотности мощности, полученных в данной работе, со значениями, представленными в литературе для среднетемпературных ТОТЭ с несущим анодом, тонкопленочным (толщиной до 10 мкм) YSZ-электролитом с барьерным слоем GDC и катодом на основе кобальтита лантана стронция (LSC или LSCF) (табл. 2). Показано, что плотность мощности ТЭ №№ 2 и 5 находятся на уровне лучших мировых достижений и большинстве случаев превосходят их.
Таблица 2.
Сравнение значений плотности мощности среднетемпературных ТОТЭ
Структура топливной ячейки: материал несущего анода электролит материал катода |
Плотность мощности, мВт/см2 | Ссылка | ||||
---|---|---|---|---|---|---|
800°С | 750°С | 700°С | 650°С | 600°С | ||
Ni-YSZ YSZ (1 мкм) + GDC (200 нм) LSC |
– | – | – | – | 624 | [25] |
Ni-YSZ YSZ (200 мкм) + GDC (7 мкм) LSC/GDC |
– | – | 540 | 420 | 270 | [26] |
Ni-YSZ YSZ (10 мкм) + GDC (5–7 мкм) LSCF |
1470 | 1120 | 770 | 420 | – | [27] |
Ni-YSZ YSZ (10 мкм) + GDC (1 мкм) LSCF |
1000 | – | 850 | 800 | – | [28] |
Ni-YSZ YSZ (6.5 мкм) + GDC (250 нм) LSC/LSCF |
– | – | – | – | 375 | [14] |
Ni-YSZ YSZ (4 мкм) + GDC (2 мкм) LSC |
1990 | 1650 | 1215 | 800 | 430 | ТЭ № 2 |
ЗАКЛЮЧЕНИЕ
В работе представлены результаты исследования ТОТЭ с многослойной тонкопленочной структурой МЭБ, сформированной на несущем NiO/YSZ-аноде. Все слои МЭБ, включая NiO-YSZ функциональный анодный слой, двухслойный YSZ/GDC-электролит и функциональный LSC катодный слой были сформированы методом магнетронного распыления. Для сравнения были исследованы ТЭ, в структуру которых был введен только функциональный LSC катодный слой. Показано, что последний вариант является наиболее предпочтительным, как с точки зрения генерируемой плотности мощности, так и технологичности (отсутствует этап нанесения АФС). ТЭ с КФС продемонстрировал плотность мощности 2290 и 500 мВт/см2 при температуре 800 и 600°С, соответственно, что на 41 и 67% больше, чем у ТЭ без функциональных слоев электродов. Это объясняется снижением поляризационного сопротивления на катоде.
Показано, что введение в структуру МЭБ ТОТЭ и анодного, и катодного функционального слоев приводит к возникновению диффузионных ограничений на аноде вследствие нанопористой структуры АФС. Это повышает поляризационное сопротивление ТЭ и, тем самым, снижает положительный эффект, вызываемый катодным функциональным слоем.
Полученные результаты демонстрируют возможность формирования МЭБ ТОТЭ на пористой несущей основе методом магнетронного распыления. Это особенно актуально для изготовления низкотемпературных ТОТЭ, которые, как известно, состоят из тонкопленочных слоев как электролита, так и обоих электродов.
Список литературы
Will, J., Mitterdorfer, A., Kleinlogel, C., Perednis, D., and Gauckler, L.J., Fabrication of thin electrolytes for second-generation solid oxide fuel cells, Solid State Ionics, 2000, vol. 131, p. 79.
Huang, H., Nakamura, M., Su, P., Fasching, R., Saito, Y., and Prinz, F.B., High-Performance Ultrathin Solid Oxide Fuel Cells for Low-Temperature Operation, J. Electrochem. Soc., 2007, vol. 154, no. 1, p. B20.
Соловьев, А.А., Шипилова, А.В., Ковальчук, А.Н., Ионов, И.В., Работкин, С.В. Сравнение характеристик твердооксидных топливных элементов с пленочными твердыми электролитами YSZ и CGO, формируемыми методом магнетронного распыления. Электрохимия. 2016. Т. 52. С. 741. [Soloviev, A.A., Shipilova, A.V., Koval’chuk, A.N., Ionov, I.V., and Rabotkin, S.V., Comparison of characteristics of solid oxide fuel cells with YSZ and CGO film solid electrolytes formed using magnetron sputtering technique, Russ. J. Electrochem., 2016, vol. 52, p. 662.]
Qiu, L., Ichikawa, T., Hirano, A., Imanishi, N., and Takeda, Y., Ln1 –xSrxCo1 –yFeyO3 – δ (Ln = Pr, Nd, Gd; x = 0.2, 0.3) for the electrodes of solid oxide fuel cells, Solid State Ionics, 2003, vol. 158, Is. 1–2, p. 55.
Samat, A.A., Somalu, M.R., Muchtar, A., Hassan, O.H., and Osman, N., LSC cathode prepared by polymeric complexation method for proton-conducting SOFC application, J. Sol-Gel Sci. and Technol., 2016, vol. 78, Is. 2, p. 382.
Zhao, F., Peng, R., and Xia, C., LSC-based electrode with high durability for IT-SOFCs, Fuel Cells Bulletin, 2008, vol. 2, p. 12.
Ковальчук, А.Н., Кузьмин, А.В., Осинкин, Д.А., Фарленков, А.С., Соловьев, А.А., Шипилова, А.В., Ионов, И.В., Богданович, Н.М., Береснев, С.М. Единичный ТОТЭ с несущим Ni-YSZ-анодом, двухслойным пленочным YSZ/GDC-электролитом и La2NiO4 + δ-катодом. Электрохимия. 2018. Т. 54. С. 623. [Koval’chuk, A.N., Kuz’min, A.V., Osinkin, D.A., Farlenkov, A.S., Solov’ev, A.A., Shipilova, A.V., Ionov, I.V., Bogdanovich, N.M., and Beresnev, S.M., Single SOFC with Supporting Ni-YSZ Anode, Bilayer YSZ/GDC Film Electrolyte and La2NiO4 + δ Cathode, Russ. J. Electrochem., 2018, vol. 54, p. 541.]
Sato, K., Iwata, C., Kannari, N., and Abe, H., Highly accelerated oxygen reduction reaction kinetics in colloidal-processing-derived nanostructured lanthanum strontium cobalt ferrite/gadolinium-doped ceria composite cathode for intermediate-temperature solid oxide fuel cells, J. Power Sources, 2019, vol. 414, p. 502.
Dieterle, L., Bockstaller, P., Gerthsen, D., Hayd, J., Ivers-Tiffée, E., and Guntow, U., Microstructure of nanoscaled La0.6Sr0.4CoO3 – δ cathodes for intermediate-temperature solid oxide fuel cells, Adv. Energy Mater., 2011, vol. 1, p. 249.
Yamaguchi, T., Sumi, H., Hamamoto, K., Suzuki, T., Fujishiro, Y., Carter, J.D., and Barnett, S.A., Effect of nanostructured anode functional layer thickness on the solid-oxide fuel cell performance in the intermediate temperature, Int. J. Hydrogen Energy, 2014, vol. 39, Is. 34, p. 19731.
Chrzan, A., Karczewski, J., Szymczewska, D., and Jasinski, P., Nanocrystalline cathode functional layer for SOFC, Electrochim. Acta, 2017, vol. 225, p. 168.
Chen, K., Chen, X., Lü, Z., Ai, N., Huang, X., and Su, W., Performance of an anode-supported SOFC with anode functional layers, Electrochim. Acta, 2008, vol. 53, Is. 27, p. 7825.
Solovyev, A.A., Lebedynskiy, A.M., Shipilova, A.V., Ionov, I.V., Smolyanskiy, E.A., Lauk, A.L., and Remnev, G.E., Effect of magnetron sputtered anode functional layer on the anode-supported solid oxide fuel cell performance, Int. J. Hydrogen Energy, 2019, vol. 44, p. 30636.
Choi, H.J., Bae, K., Grieshammer, S., Han, G.D., Park, S.W., Kim, J.W., Jang, D.Y., Koo, J., Son, J.-W., Martin, M., and Shim, J.H., Surface Tuning of Solid Oxide Fuel Cell Cathode by Atomic Layer Deposition, Advanced Energy Materials, 2018, vol. 8, Is. 33, p. 1802506.
Yoon, J., Cho, S., Kim, J.-H., Lee, J.H., Bi, Z., Serquis, A., Zhang, X., Manthiram, A., and Wang, H., Vertically aligned nanocomposite thin films as a cathode/electrolyte interface layer for thin-film solid oxide fuel cells, Advanced Functional Materials, 2009, vol. 19, p. 3868.
Shin, S.S., Kim, J.H., Li, G., Lee, S.Y., Son, J.-W., Kim, H., and Choi, M., A highly activated and integrated nanoscale interlayer of cathodes in low-temperature solid oxide fuel cells via precursor-solution electrospray method, Int. J. Hydrogen Energy, 2019, vol. 44, Is. 9, p. 4476.
Smolyanskiy, E.A., Linnik, S.A., Ionov, I.V., Shipilova, A.V., Semenov, V.A., Lauk, A.L., and Solovyev, A.A., Magnetron sputtered LSC thin films for solid oxide fuel cell application, IOP Conf. Series: J. Physics, 2018, vol. 1115, no. 3, p. 032080. https://doi.org/10.1088/1742-6596/1115/3/032080
Hildenbrand, N., Boukamp, B.A., Nammensma, P., and Blank, D.H.A., Improved cathode/electrolyte interface of SOFC, Solid State Ionics, 2011, vol. 192, p. 12.
Noh, H.S., Hong, J., Kim, H., Yoon, K.J., Kim, B.-K., Lee, H.-W., Lee, J.-H., and Son, J.-W., Scale-up of thin-film deposition-based solid oxide fuel cell by sputtering, a commercially viable thin-film technology, J. Electrochem. Soc., 2016, vol. 163, Is. 7, p. F613.
Sochugov, N.S., Soloviev, A.A., Shipilova, A.V., and Rotshtain, V.P., An ion-plasma technique for formation of anode-supported thin electrolyte films for IT-SOFC applications, Int. J. Hydrogen Energy, 2010, vol. 36, p. 5550.
Chen, D., Bishop, S.R., and Tuller, H.L., Praseodymium-cerium oxide thin film cathodes: study of oxygen reduction reaction kinetics, J. Electroceram., 2012, vol. 28, p. 62.
Okada, S., Miyoshi, S., and Yamaguchi, S., Rate determining step in ORR of PrOx-based film cathodes, ECS Trans., 2015, vol. 68, p. 987.
Nikonov, A.V., Pavzderin, N.B., Shkerin, S.N., Gyrdasova, O.I., and Lipilin, A.S., Fabrication of multilayer ceramic structure for fuel cell based on La(Sr)Ga(Mg)O3–La(Sr)Fe(Ga)O3 cathode, Russ. J. Appl. Chem., 2017, vol. 90, p. 369.
Singhal, S.C. and Kendall, K., High-temperature solid oxide fuel cells: fundamentals, design and applications, Elsevier Science, 2003, p. 230–257.
Noh, H.S., Lee, H., Kim, B.K., Lee, H.W., Lee, J.H., and Son, J.W., Microstructural factors of electrodes affecting the performance of anode-supported thin film yttria-stabilized zirconia electrolyte (∼1 μm) solid oxide fuel cells, J. Power Sources, 2011, vol. 196, p. 7169.
Tao, Y., Shao, J., Wang, W.G., and Wang, J., Optimization and evaluation of La0.6Sr0.4CoO3 – d cathode for intermediate temperature solid oxide fuel cells, Fuel Cells, 2009, vol. 09, no. 5, p. 679.
Mai, A., Haanappel, V.A.C., Uhlenbruck, S., Tietz, F., and Stöver, D., Ferrite-based perovskites as cathode materials for anode-supported solid oxide fuel cells Part II. Influence of the CGO interlayer, Solid State Ionics, 2005, vol. 176, p. 1341.
Fonseca, F.C., Uhlenbruck, S., Nedelec, R., and Buchkremer, H.P., Properties of bias-assisted sputtered gadolinia-doped ceria interlayers for solid oxide fuel cells, J. Power Sources, 2010, vol. 195, p. 1599.
Дополнительные материалы отсутствуют.
Инструменты
Электрохимия