Электрохимия, 2021, T. 57, № 6, стр. 323-330
Изучение механизма формирования пассивирующего слоя при электрохимическом окислении сульфида меди(I)
О. В. Нечвоглод a, *, С. М. Пикалов a, **
a Институт металлургии УрО РАН
Екатеринбург, Россия
* E-mail: nechvoglodov@mail.ru
** E-mail: s.pikalov@mail.ru
Поступила в редакцию 18.08.2020
После доработки 11.12.2020
Принята к публикации 28.12.2020
Аннотация
Изучена структура и определены фазовые составляющие синтезированного сульфида меди(I). Показано, что при кристаллизации сульфида меди возможно образование как фазы халькозина (Cu2S), так и фазы джарлеита (Cu31S16), характеризующегося дефицитом меди в кристаллической решетке и отклонением от стехиометрического состава. Формирование джарлеита обусловлено кристаллизацией фазы металлической меди. Рассчитаны параметры кристаллических решеток синтезированных фаз и показано их соответствие с международной рентгеновской базой данных. Проведено электрохимическое окисление образца в растворе серной кислоты. Установлено, что при плотности тока 1000 А/м2 и концентрации 100 г/дм3 H2SO4 электрохимическое растворение сульфида меди протекает с образованием пассивирующей пленки труднорастворимых продуктов за счет окисления сульфида меди(I) до сульфида меди(II). Так же в ходе окисления образуются промежуточные нестехиометрические сульфиды (Cu1.74S, Cu1.8S, Cu1.6S, CuS) в следующей последовательности: Сu2S (Cu31S16) → Cu1.8S → Cu1.74S → Cu1.6S → CuS → S + Cu2+. Процесс сопровождается переходом катионов меди в раствор. По мере накопления элементной серы и сульфидов меди на реакционной поверхности образца скорость электрохимического окисления снижается вследствие затрудненного отвода продуктов и подвода реагента в зону реакции.
ВВЕДЕНИЕ
Основным сырьем для производства металлической меди являются сульфидные руды, в которых медь находится в сульфидных соединениях. Для извлечения меди и сопутствующих ценных компонентов применяются различные пиро- и гидрометаллургические технологии [1–3], в частности электрохимическое выщелачивание. Электролиз сульфидных материалов, по мнению авторов, является альтернативной технологией, обладающей рядом преимуществ [4]. В связи с чем, авторами [5] разработан способ электролиза гранулированных сульфидно-металлических медно-никелевых анодов с получением катодной меди и образованием серосульфидного шлама, концентрирующего драгоценные металлы. В рамках этой работы изучены закономерности электрохимического окисления сульфида меди(I) [6]. Определено влияние скорости кристаллизации Cu2S на его структуру и закономерности электрохимического окисления [7]. Показано, что гранулированный сульфид меди имеет более высокую скорость электрохимического окисления, чем медленно охлажденный. Проведены работы по анодному окислению гранулированных медно-никелевых файнштейнов, представляющих собой сульфидно-металлический сплав Cu2S–Ni3S2–Cu–Ni. Возможность ведения такого процесса подтверждена экспериментально, однако, его протекание затруднено пассивацией гранул серосульфидным шламом и элементной серой (до 80% элементной серы в шламе) [4]. Под действием электрического тока в растворе серной кислоты происходит окисление Cu2S с переходом сульфидной серы (S2–) в элементное состояние (S0) [8], и одновалентной меди (Cu+) в двухвалентное (Cu2+). Процесс имеет ступенчатый механизм и сопровождается образованием промежуточных труднорастворимых сульфидов меди [8–10]. Катионы меди переходят в раствор, а на реакционной поверхности образца накапливаются труднорастворимые продукты – сульфиды и элементная сера, образуя серосульфидный слой. Этот слой препятствует отводу продуктов и подводу реагента в зону реакции, вызывая диффузионные ограничения. Снижение скорости отвода катионов меди в объем электролита из зоны анодного окисления ведет к снижению скорости окисления исходного образца. Скорость электрохимического окисления сульфида меди(I) определяется растворением пассивирующего слоя и диффузией через него реагентов и продуктов реакции. Формирование пассивирующего слоя обусловлено фазовыми превращениями Cu2S под действием электрического тока. В результате электрохимического окисления сульфидной серы образуется CuS через ряд превращений сульфидов нестехиометрического состава, о чем свидетельствуют ранее выполненные исследования. В некоторых работах упоминается о более сложном механизме окисления через ряд последовательных превращений с образованием Cu1.8S и Cu1.74S, но не найдено сведений о структуре слоя труднорастворимых продуктов и обоснования механизма его образования. Таким образом, для оценки возможности снижения влияния эффекта пассивации и интенсификации процесса электролиза сульфидных медных материалов, необходимы более детальные сведения о механизме формирования и структуре слоя труднорастворимых продуктов электрохимического окисления сульфида меди(I) в растворе серной кислоты.
Цель настоящего исследования – изучение структуры и процесса формирования пассивирующего слоя труднорастворимых продуктов окисления Cu2S, образующихся на его поверхности в результате электрохимического окисления.
МЕТОДИКА ЭКСПЕРИМЕНТА
Для проведения исследований синтезирован образец сульфида меди(I) цилиндрической формы и помещен в изоляционную обойму. Торец цилиндра, имеющий форму круга площадью 0.0001 м2, служил рабочей поверхностью, на которой проведено формирование пассивирующего слоя. Электролит объемом 30 мл – раствор серной кислоты концентрации 100 кг/м3 H2SO4, обеспечивает высокую электропроводность. Полученный анод из сульфида меди подвергали электрохимическому окислению в течение 15 мин при плотности тока 1000 А/м2 в режиме стабилизации по току. После 15 мин эксперимента наблюдался скачок напряжения, что свидетельствовало о пассивации поверхности. Плотность тока подобрана экспериментально: 1000 А/м2 соответствует достаточно высокой скорости окисления поверхности анода. Увеличение плотности тока ведет к увеличению потенциала анода и интенсификации процесса газообразования (O2), а снижение – к снижению скорости формирования слоя. Также при высокой скорости электрохимического окисления можно ожидать в продуктах большего количества промежуточных нестехиометрических сульфидов меди (состав которых и необходимо определить), в то время как при понижении плотности тока будет увеличиваться содержание элементной серы. Продукты электрохимического окисления и исходный образец анализировали различными методами. Методом рентгенографии на дифрактометре XRD-7000C определены фазовые составы исходного образца сульфида меди(I) и слоя продуктов его электрохимического окисления. Методом оптической микроскопии на оптическом микроскопе Olympus GX-51 получены данные о микроструктуре. Количественный состав фаз определен методом микрорентгеноспектрального анализа (МРСА) на микроскопе JSM-5900LV. Составы образцов определены аналитическими методами.
При потенциале 1000 мВ получена зависимость плотности тока от времени протекания электрохимического окисления [7]. Оценки количества вещества окисленного сульфида меди в установившихся условиях получены путем обработки графических данных. Выбор значения потенциала обусловлен полным протеканием реакции электрохимического окисления Cu2S → CuS. Исходя из этого, массу окисленного вещества можно найти интегрированием площади под кривой i(τ) от времени начала (τ1), до окончания (τ2) реакции. Массу прореагировавшего вещества определили согласно закону Фарадея:
(1)
$m = \frac{M}{{nF}}\int\limits_{{{\tau }_{1}}}^{{{\tau }_{2}}} {i\left( \tau \right)d\tau } \frac{S}{{3600}},$Диффузионный поток (J) рассчитан по формуле [11]:
(2)
${{J}^{{{\text{Cu}}}}} = \frac{{{{D}_{{{\text{Cu}}}}}\left( {{{c}_{{{\text{Cu}}}}} - c_{{{\text{Cu}}}}^{'}} \right)p}}{{\gamma d}},$Расчет величины DСu выполнен по уравнению Стокса–Эйнштейна: DCu = $\frac{{kT}}{{4\pi {{r}_{{{\text{Cu}}}}}\eta }},$ где k – постоянная Больцмана (1.38 × 10–23 кг м2/(c2 К)), T – температура (298 K), rCu – радиус катиона меди, равный 7.3 × 10–11 м, η – вязкость раствора серной кислоты (100 кг/м3), принятая 1.6 × 10–3 Па с [12]. Подставляя в формулу (2) указанные значения k, T, rCu и η, величина коэффициента диффузии катионов меди в растворе серной кислоты концентрации 100 кг/м3 составит 2.8 × 10–9 м2/с.
Пористость пленки определена из выражения:
где $\rho {\kern 1pt} '$, ρ (кг/м3) – насыпная и истинная плотности гранулированного материала.РЕЗУЛЬТАТЫ И ОБСУЖДЕНИЕ
Согласно химическому анализу, исходный образец сульфида меди(I) содержит (%): 77.4 Cu и 22.6 S. По данным РФА (рис. 1), представляет собой нестехиометрический твердый раствор меди и серы с преимущественной моноклинной структурой Р21/n (14) пространственной группы, близкой по своему составу к сульфиду меди Cu31S16 (джарлеит) [13]. В образце присутствует фаза металлической меди, что подтверждено металлографическим анализом. Кристаллизация металлической фазы ведет к образованию сульфидной фазы с дефицитом меди – Cu31S16, что объясняет отклонение от стехиометрического состава. Также в образце присутствует фаза стехиометрического Cu2S.
Рис. 1.
Рентгенограмма исходного образца сульфида меди (а); рентгенограмма после электрохимического окисления (б).
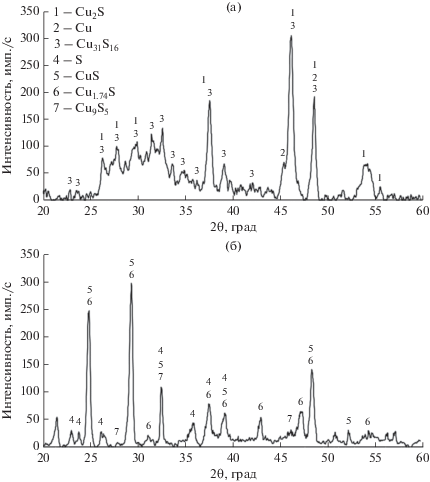
Рассчитаны параметры кристаллических решеток основных фазовых составляющих исходного образца Cu2S и Cu31S16 (табл. 1). Расчетные значения имеют хорошее соответствие с международной базой данных.
Таблица 1.
Параметры решетки фаз исходного образца и пассивирующего слоя
Фаза | Cu31S16 | Cu2S | CuS | Cu1.74S |
---|---|---|---|---|
структура | моноклинная Р21/n (14) | гексагональная P63/mmc (194) | гексагональная P63/mmc (194) | триклинная P – 1(2) |
a, Å | 26.872 | 3.949 | 3.754 | 13.414 |
a0, Å | 26.897 | 3.961(4) | 3.767(1) | 13.387(4) |
b, Å | 15.711 | – | – | 13.328 |
b0, Å | 15.745 | – | – | 13.395(6) |
c, Å | 13.586 | 6.736 | 16.146 | 15.478 |
c0, Å | 13.565 | 6.722(7) | 16.19(2) | 15.481(9) |
c/a | – | 1.706 | 4.301 | |
c0/a0 | – | 1.697 | 4.309 | 1.156 |
α, deg | – | – | – | 89.46 |
α0, deg | – | – | – | 89.80 |
β, deg | 90.000 | – | – | 89.90 |
β0, deg | 93.000 | – | – | 89.98 |
γ, deg | – | – | – | 89.84 |
γ0, deg | – | – | – | 90.03 |
V, Å3 | 5735.88 | 90.953 | 197.03 | 2767.05 |
V0, Å3 | 5744.67 | 91.34 | 197.91 | 2777.02 |
delta 2θ | 0.050 | 0.026 | 0.011 | 0.019 |
В результате электрохимического окисления сульфида меди(I) сформирован слой труднорастворимых продуктов. В условиях анодной поляризации [14–16] окисление сульфида меди протекает через ряд промежуточных сульфидных соединений по суммарным реакциям:
(4)
${\text{C}}{{{\text{u}}}_{{\text{2}}}}{\text{S}}--2{\text{e}} = {\text{CuS}} + {\text{C}}{{{\text{u}}}^{{2 + }}},$По мнению авторов [12–14], под действием электрического тока сульфид меди(I) может распадаться на медь и сульфид меди(II):
Согласно данным РФА [13] и расчета параметров элементарных ячеек фаз, основными фазовыми составляющими слоя продуктов электрохимического окисления являются CuS (ковеллин), Cu1.74S (роксбиит), в меньшем количестве – Cu9S5 (что соответствует Cu1.8 – дигенит), а также выявлены слабые пики, характерные для элементной серы. Рассчитаны параметры кристаллических решеток CuS и Cu1.74S. Расчетные значения имеют хорошее соответствие с международной базой данных. По МРСА (табл. 2, рис. 2), на поверхности образца сформирована фаза Cu1.6S (джирит). Элементная сера является рентгеноаморфной, поэтому может быть не выявлена на рентгенограмме.
Таблица 2.
Химический состав в точках зондирования (по рис. 2в)
№ | Содержание, ат. % | Фаза | ||
---|---|---|---|---|
S | Cu | О | ||
1 | 37.6 | 61.5 | – | Cu1.6S |
2 | 36.8 | 61.9 | – | Cu1.6S |
3 | 11.7 | 88.1 | – | Cu–CuS |
4 | 30.0 | 69.9 | – | Cu–CuS |
5 | 38.9 | 60.4 | – | Cu1.6S |
6 | 17.0 | 33.5 | 49.1 | mCuO·nCuSO4 |
7 | 21.3 | 44.2 | 34.6 | mCuO·nCuSO4 |
Рис. 2.
Слой сульфидов меди, образовавшийся на поверхности образца Cu2S после электрохимического окисления при различном увеличении: а) ×20; б) ×50; в) ×200; г) ×800; д) ×2000; е) ×5000.
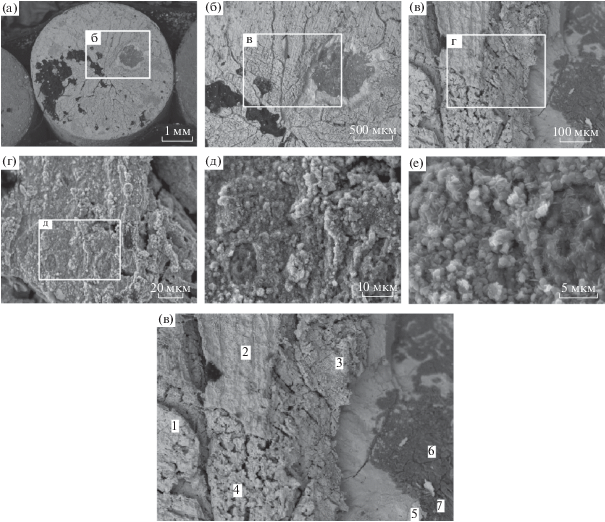
Слой продуктов реакции имеет плотную однородную структуру, образованную мелкодисперсными частицами сульфидов CuxSy размером 4–6 мкм. По данным РФА, отклики, характерные для элементной серы, идентифицированы, но имеют малую интенсивность, что можно объяснить аморфностью серы, незначительным количеством и дисперсностью частиц. Пленка образована внутренним подслоем, имеющим плотную однородную структуру, и внешним слоем, имеющим плотные однородные и рыхлые неоднородные участки. Электрохимическое окисление сульфида меди(I) (Сu2S, Cu31S16) в сернокислом электролите протекает на первой стадии с образованием нестехиометрических Cu1.8S, Cu1.74S, Cu1.6S до CuS. На второй стадии CuS окисляется до S элементной. Процесс сопровождается переводом катионов меди в раствор. При взаимодействии катионов меди с сернокислым электролитом в присутствии кислорода, выделяющегося на аноде, возможно образование оксидно-сульфатных включений типа mCuO·nCuSO4. Последовательность фазовых превращений исследуемого образца сульфида меди(I) может быть представлена в общем виде:
(7)
$\begin{gathered} {\text{С}}{{{\text{u}}}_{{\text{2}}}}{\text{S}}\left( {{\text{C}}{{{\text{u}}}_{{{\text{31}}}}}{{{\text{S}}}_{{{\text{16}}}}}} \right) \to {\text{C}}{{{\text{u}}}_{{{\text{1}}{\text{.8}}}}}{\text{S}} \to {\text{ C}}{{{\text{u}}}_{{{\text{1}}{\text{.74}}}}}{\text{S}} \to \\ \to {\text{C}}{{{\text{u}}}_{{{\text{1}}{\text{.6}}}}}{\text{S}} \to {\text{CuS}} \to {\text{S}} + {\text{C}}{{{\text{u}}}^{{2 + }}}. \\ \end{gathered} $Механизм разложения сульфида меди(I) по реакции (6) объясняет образование участков металлической меди на поверхности электродов.
Для оценки кинетических особенностей процесса была получена зависимость плотности тока от времени в потенциостатическом режиме (рис. 3). По форме кривой видно, что процесс в ходе накопления продуктов реакции из кинетического (в начальный период времени) переходит в диффузионный режим. Интегрированием уравнения (1) определена масса окисленного сульфида меди (при потенциале электрода 1000 мВ). Масса Cu2S, вступившего в электрохимическое взаимодействие, составила 10.3 × 10–6 кг.
Для оценки массопереноса рассчитаны диффузионные потоки катионов меди через пассивирующую пленку. Окисление анода Cu2S с образованием серосульфидной пленки на поверхности (рис. 4) происходит от поверхности внутрь электрода.
Таким образом, состав пассивирующей пленки непрерывно изменяется в соответствии с цепочкой фазовых превращений (7). И, по мере растворения, образуются 2 участка: внутренний слой, представленный промежуточными сульфидами (промежуточные фазы), и внешний – частичками элементной серы. В установившемся стационарном режиме скорости окисления поверхности анода и растворения пленки выравниваются. После того, как катионы меди перешли в раствор, структура пленки становится пористой. И так как поры между частицами серы заполнены электролитом, последующее растворение сульфидных фаз и массоперенос катионов меди в объем электролита происходит в межчастичном пространстве пленки.
Образовавшаяся пассивирующая пленка при этом условно имеет форму полого цилиндра с толщиной стенки δ (толщина пленки) и радиусом 5.6 × 10–3 м. Для расчетов сделано допущение, что плотность пленки равна плотности CuS (4600 кг/м3). Тогда расчетное значение толщины пассивирующей пленки составило 2.3 × 10–6 м. Кажущаяся плотность пассивирующей пленки, образованной частицами серы, рассчитана как отношение массы электрохимически окисленной серы к объему пленки, и составила 1600 кг/м3. По формуле (4) пористость гранул (pгр) после окисления составила 45%. Концентрация меди в растворе после электрохимического окисления равна 35.4 × 10–3 кг/м3. Подстановкой соответствующих значений в формулу (3), расчетное значение диффузионного потока катионов меди в межзеренном пространстве составило 2.4 × 10–7$\frac{{{\text{кг}}}}{{\text{с}}} \cdot {{{\text{м}}}^{2}}.$
ЗАКЛЮЧЕНИЕ
Электрохимическое растворение сульфида меди(I) протекает с образованием пленки труднорастворимых продуктов. На основе данных рентгенофазового анализа, расчета параметров элементарных ячеек и данных микроренгеноспектрального анализа показано, что по мере электрохимического окисления сульфида меди(I) образуются такие соединения, как Cu1.8S, Cu1.74S, Cu1.6S, CuS. По мере окисления сульфидной серы до элементной и одновалентной меди до двухвалентной, сульфид меди(I) претерпевает следующие превращения: Сu2S (Cu31S16) → Cu1.8S → Cu1.74S → Cu1.6S → → CuS → S + Cu2+.
Изучена структура пассивирующего слоя. Он имеет пористое строение, что обуславливает протекание электрохимических превращений даже при образовании частиц элементной серы, которая является диэлектриком. Полного блокирования поверхности не происходит, так как диффузия катионов меди и контакт электролита с реакционной поверхностью осуществляется через промежутки между частичками сульфидных фаз и элементной серы. Расчетное значение пористости пленки составило 45%, а диффузионный поток катионов меди в межзеренном пространстве – 2.4 × 10–7$\frac{{{\text{кг}}}}{{\text{с}}} \cdot {{{\text{м}}}^{2}}.$
Список литературы
Moskalyk, R.R. and Alfantazi, A.M., Review of copper pyrometallurgical practice: today and tomorrow, Minerals Engineering, 2003, vol. 16, p. 893.
Letowski, F., Kolodziej, B., Czernecki, M., Jedrczak, A., and Adamski, Z., A new hydrometallurgical method for the processing of copper concentrates using ferric sulphate, Hydrometallurgy, 1979, vol. 4, p. 169.
Hyvarinen, O. and Hamalainen, M., HydroCopper – a new technology producing copper directly from concentrate, Hydrometallorgy, 2005, vol. 77, p. 61.
Селиванов, Е.Н., Нечвоглод, О.В., Удоева, Л.Ю., Чумарев, В.М., Мамяченков, С.В., Лобанов, В.Г. Способ переработки сульфидных медно-никелевых сплавов, Пат. 2434065 (Россия). 2011. [Seliva-nov, E.N., Nechvoglod, O.V., Udoeva, L.Ju., Chumarev, V.M., Mamyachenkov, S.V., and Lobanov, V.G., Sposoby pererabotki sul’fidnyh medno-nikelevyh splavov, Pat. 2434065, Russia.]
Нечвоглод, О.В., Сергеева, С.В., Пикулин, К.В., Селиванов, Е.Н. Разделение меди и никеля при электролизе гранулированного файнштейна, Изв. вузов. Цветная металлургия, 2018, № 5. С. 16. [Nechvoglod, O.V., Sergeeva, S.V., Pikulin, K.V., and Selivanov, E.N., Razdelenie medi i nikelia pri electrolyze granulirovannogo fainshteina, Russ. Metallurgy Nonferrous Metals, 2018, vol. 5, p. 16.]
Селиванов, Е.Н., Нечвоглод, О.В., Удоева, Л.Ю., Лобанов, В.Г., Мамяченков, С.В. Электрохимическое окисление медно-никелевых сульфидно-металлических сплавов. Изв. вузов. Цветная металлургия. 2009. № 6. С. 15. [Selivanov, E.N., Nechvoglod, O.V., Udoeva, L.Yu., Lobanov, V.G., and Mamyachenkov, S.V., Electrochemical Oxidation of Copper–Nickel Metal–Sulfide Alloys, Metallurgy Nonferrous Metals, 2009, № 6, p. 577.]
Nechvoglod, O.V., Selivanov, E.N., and Mamyachenkov, S.V., Effect of structure on the electrochemical oxidation rate of copper and nickel sulfides, Defect and Diffusion Forum, 2012, vol. 326–328, p. 383.
Chanturiya, V.A. and Vigdergau, V.E. Electrochemistry of sulfides. Theory and practice of flotation. M.: Ore and Metals PH, 2009, 280 p.
Deng, T., Lu, Y., Wen, Z., and Liu, D., Oxygenated chloride – assisted leaching of copper residue, Hydromatallurgy, 2001, vol. 62, p. 23.
Сабаури, Г.Н., Брюквин, В.А., Блохина, Л.И., Левин, А.М. Анодная поляризация сплавов Cu–Fe–S, Металлы. 1993. № 6. С. 49. [Sabauri, G.N., Br’ukvin, V.A., Blohina, L.I., and Levin, A.M., Anodnaya polyarizazciya splavov Cu–Fe–S, Metally (in Russia), 1993, no. 6, p. 49.]
Фролов, Ю.Г. Курс коллоидной химии. Поверхностные явления и дисперсные системы, М.: Химия, 1989. 465 с. [Frolov, U.G. Colloidal chemistry course. Surface phenomena and dispersed systems (in Russia), Moscow: Khimiya, 1989. 465 p.]
Амелин, А.Г. Производство серной кислоты, М.: Высшая школа. 1980. 245 с. [Amelin, A.G., Sulfuric acid production (in Russia), Moscow: Vysshaya shkola, 1980, p. 245.]
Международная база данных ICDD.
Nechvoglod, O.V. and Pikaliv, S.M., Study of the Mechanism for Forming a Passivating Layer under Electrochemical Oxidation of Copper(I) Sulfide. IOP Conference Series: Materials Science and Engineering, Institute of Physics and IOP Publishing Limited, vol. 969, 012058, 2020.
Lu, Z., Tang, J., Mendosa, Maria de Lourdes, Chang, Dingminh, Cai, Lankun, Zhang, Lehua, Electrochemical decrease of sulfide in sewage by pulsed power supply, J. Electroanalit. Chem., 2015, vol. 745, p. 37.
Abd El Haleem, S.M. and Din Abd El Aal E.E., Electrochemical reduction of the corrosion products formed on copper surface in alkaline–sulphide solutions, J. Alloys and Compounds, 2007, vol. 432(1), p. 205.
Дополнительные материалы отсутствуют.
Инструменты
Электрохимия