Электрохимия, 2022, T. 58, № 2, стр. 54-60
Повышение электрохимической активности катода Pr1.95La0.05CuO4 методом лазерной модификации профиля границы электрод/электролит
Н. В. Лысков a, *, М. З. Галин a, Ф. С. Напольский b, Г. Н. Мазо c
a ФГБУН Институт проблем химической физики РАН
142432 Московская обл., Черноголовка, просп. академика Семенова, 1, Россия
b Государственный университет “Дубна”, Инжиниринговый центр
141982 Московская обл., Дубна, ул. Университетская, 19, Россия
c Московский государственный университет имени М.В. Ломоносова, Химический факультет
119992 Москва, ГСП-1, Ленинские горы, 1, стр. 3, Россия
* E-mail: lyskov@icp.ac.ru
Поступила в редакцию 17.11.2020
После доработки 09.08.2021
Принята к публикации 31.08.2021
- EDN: ATGIXD
- DOI: 10.31857/S0424857022020086
Аннотация
Изучено влияние топологии поверхности твердого электролита Ce0.9Gd0.1O1.95 (GDC), сформированной методом лазерной обработки, на электрохимическую активность катодного материала Pr1.95La0.05CuO4 (PLCO) в реакции восстановления кислорода. Показано, что оптимальной с точки зрения достижения высокой электрохимической активности является упорядоченная столбчатая структура GDC с глубиной профиля рельефа около 11–12 мкм. Установлено, что при переходе от исходной поверхности твердого электролита GDC к ее модифицированному варианту наблюдается двукратное снижение величины поляризационного сопротивления катодного материала PLCO (от 0.87 Ом см2 (исходный образец) до 0.40 Ом см2 (модифицированная поверхность GDC) при температуре 700°С на воздухе). На основании полученных данных применение метода лазерной обработки для формирования заданной топологии границы электрод/электролит можно рассматривать как эффективный технологический способ, позволяющий повысить электрохимическую производительность твердооксидного топливного элемента (ТОТЭ).
ВВЕДЕНИЕ
Твердооксидные топливные элементы (ТОТЭ) представляют собой один из перспективных альтернативных источников энергии, отличительными особенностями которого являются экологичность и высокая эффективность преобразования топлива [1, 2]. Вместе с тем повышенные температуры функционирования таких устройств (800–1000°С) обуславливают их высокую стоимость. В последние десятилетия основные усилия разработчиков ТОТЭ направлены на адаптацию их работы в условиях средних температур (600–800°С), что позволит снизить затраты на их эксплуатацию, повысит ресурс работы и, следовательно, сделает их более экономически привлекательными [2, 3]. Однако при переходе в область средних температур значительно увеличивается электрохимическое сопротивление ключевых компонентов ТОТЭ, в первую очередь это касается материалов твердого электролита и катода. Решение первой проблемы связано с разработкой различных подходов формирования тонкопленочных газоплотных покрытий твердого электролита [4–7]. Что касается второй проблемы, то ее решение во многом определяется повышением эффективности протекания реакции восстановления кислорода (РВК), проходящей с участием кислорода газовой фазы на границе катод/электролит [2, 3, 8, 9]. Традиционными подходами, направленными на повышение электрохимической активности катода в РВК, являются поиск катодных материалов, альтернативных широко используемым манганитам лантана–стронция (LSM) [10–17], и создание композитных электродов на их основе [18–23]. В последнее время актуальным направлением в этой области стало использование инфильтрационных (или импрегнационных) методов создания многокомпонентных катодов [24, 25]. Наряду с развитием упомянутых выше подходов к модификации границы “электрод/электролит”, перспективным представляется также использование ее обработки, связанной с возможностью контроля геометрии на микроуровне. В этом случае появляется возможность контролируемо увеличить протяженность границы электрод/электролит, что будет являться решающим фактором в пользу повышения электрохимической производительности катодного материала в условиях средних температур. В связи с этим представляется перспективным использование метода прецизионной лазерной обработки поверхности твердого электролита для воспроизводимого формирования заданного рельефа границы электрод/электролит, обладающего упорядоченной структурой [26, 27].
Целью настоящей работы явилось изучение влияния условий лазерной обработки поверхности твердого электролита на морфологию формируемого рельефа и электрохимическую активность катода при нанесении слоя электродного материала на модифицированную поверхность твердого электролита. В качестве модифицируемых лазерной обработкой образцов были использованы плотноспеченные мембраны твердого электролита Ce0.9Gd0.1O1.95 (GDC), на поверхность которых был нанесен новый перспективный катодный материал на основе купрата празеодима, допированного оксидом лантана Pr1.95La0.05CuO4 (PLCO) [17, 23]. Отличительными особенностями PLCO, обуславливающими его перспективность при использовании в качестве катодного материала ТОТЭ, являются высокая электропроводность (~120 См/см при 800°С [17]), величина коэффициента термического расширения (КТР) 11.9 × 10–6 K–1 [17], сопоставимая с КТР GDC (12.4 × 10–6 К–1 [28]), и относительно невысокая величина поляризационного сопротивления (0.87 Ом см2 при 700°C на воздухе [23]).
ЭКСПЕРИМЕНТАЛЬНАЯ ЧАСТЬ
Синтез PLCO осуществляли твердофазным методом на воздухе. В качестве исходных реагентов использовали порошки Pr6O11, La2O3 и CuO (Sigma-Aldrich®, 99.9%)), предварительно прокаленные при 400°С на воздухе. Навески исходных веществ смешивали в стехиометрических количествах и гомогенизировали в агатовой ступке под слоем ацетона. Далее полученную смесь отжигали при температуре 1000°C в течение 50 ч на воздухе. Фазовый состав образца контролировали методом рентгенофазового анализа (РФА) с помощью дифрактометра Huber G670 (излучение ${\text{Cu}}{{K}_{{{{\alpha }_{1}}}}}$, интервал 2θ 20°–80°). Обработку рентгенографических данных осуществляли с помощью программы Jana2006, величины параметров элементарной ячейки уточняли по методу Ритвельда.
В качестве модифицируемых твердоэлектролитных мембран были использованы таблетки GDC, полученные из коммерческого реактива (Sigma-Aldrich®) спеканием при 1400°C в течение 4 ч. Относительная плотность образцов GDC составила ~96%. Для увеличения протяженности рельефа границы электрод/электролит их поверхность была подвергнута лазерной обработке с помощью системы прецизионной лазерной маркировки “МИНИМАРКЕР2-20А4” (ООО “Лазерный центр”, Россия). Источником лазерного излучения служил полупроводниковый иттербиевый лазер мощностью 20 Вт с длиной волны 1064 нм. Диаметр пятна лазера в точке фокусировки составлял около 50 мкм. Профиль обработки задавался графически в виде сетки с толщиной линий 50 мкм и шагом 100 мкм. Основные режимы лазерного воздействия, использованные в работе, приведены в табл. 1. Количество проходов в режиме “основной проход” варьировали от 1 до 5. После завершения обработки образец подвергали дополнительному воздействию лазерного излучения в режиме “чистящий проход” для удаления продуктов осаждения, образующихся на поверхности GDC после лазерной обработки, и отжигу при 900°С в течение 4 ч. Применение термической обработки вызвано необходимостью восстановления стехиометрического состава поверхности GDC по кислороду после воздействия лазерного излучения.
Таблица 1.
Основные режимы лазерного воздействия, использованные в работе
Наименование режима | Параметры лазерного импульса (частота, кГц/скорость, мм/с/мощность, %/ длительность импульса, нс) |
Плотность заполнения, линий/мм |
---|---|---|
Основной проход | 40/100/100/8 | 10 |
Чистящий проход | 40/100/20/8 | 10 |
Исследование рельефа обработанной поверхности было осуществлено методом оптической профилометрии (профилометр NANOVEA PS50, США). Для построения 3D-изображения модифицированной поверхности GDC проводили как продольное, так и поперечное сканирование поверхности экспериментальных образцов. Размер области сканирования составлял 500 × 500 мкм2. Анализ полученных данных и построение 3D‑модели проводили с помощью программы Analysis 3D.
Анализ микроструктуры границы электрод/электролит проводили методом растровой электронной микроскопии (РЭМ) (LEO Supra 50VP, Германия). Анализировали поперечное сечение (скол) образцов.
Для исследования электрохимических свойств границы электрод/электролит были приготовлены симметричные ячейки конфигурации электрод/электролит/электрод. В качестве твердого электролита были использованы модифицированные образцы твердоэлектролитных мембран GDC, на поверхность которых наносили электродную пасту на основе PLCO. Электродную пасту готовили путем смешения синтезированного порошка PLCO и органического связующего (Heraeus V006, Германия), взятых в массовом соотношении 1 : 1. Перед использованием порошок PLCO был подвергнут помолу в шаровой мельнице в течение 15 мин в этиловом спирте. Анализ распределения частиц порошка по размерам, проведенный методом динамического светорассеяния на лазерном дифракционном микроанализаторе Analysette 22 “Fritsch” (Германия), показал, что размер частиц порошка варьировался в интервале 1–6 мкм. Нанесение электродной пасты на основе PLCO проводили методом трафаретной печати с использованием тканевой сетки VS‑Monoprint PES HT PW 77/55 (Verseidag-Techfab GmbH, Германия). После нанесения электродного слоя образец сушили при 130°С в течение 30 мин. Процедуру нанесения повторяли 3 раза с каждой стороны электрохимической ячейки. Финальную термообработку проводили при температуре 850°С в течение 10 ч на воздухе.
Измерение поляризационного сопротивления границы электрод/электролит осуществляли методом импедансной спектроскопии по трехэлектродной схеме подключения с использованием импедансметра P-5X (ООО “Electrochemical Instruments”, Россия) в диапазоне частот от 0.1 Гц до 500 кГц с амплитудой сигнала 10 мВ в интервале температур 600–800°C на воздухе. Противоэлектрод и рабочий электрод, нанесенные методом трафаретной печати на поверхность таблетки твердого электролита, были идентичные. В качестве электрода сравнения был использован Pt‑электрод, для создания которого на боковую поверхность таблетки твердого электролита наносили Pt-пасту. Токоподводами служила платиновая проволока, в качестве токосъемных контактов выступали платиновые сетки, плотно прижатые к противоэлектроду и рабочему электроду. Температуру образца измеряли с помощью Pt‒Pt/Rh-термопары, расположенной вблизи образца. Обработку импедансных спектров и расчет параметров импеданса проводили с помощью программы ZView (ver. 3.1, Scribner Associates, Inc.).
РЕЗУЛЬТАТЫ И ОБСУЖДЕНИЕ
На рис. 1 представлены экспериментальная, теоретическая и разностная рентгенограммы купрата Pr1.95La0.05CuO4. Согласно данным РФА, полученный образец PLCO являлся однофазным, все рефлексы на рентгенограмме соответствовали синтезированной фазе. Полученная рентгенограмма была проиндексирована в тетрагональной сингонии с пространственной группой I4/mmm с параметрами элементарной ячейки: a = 3.9605(1) Å, с = 12.2292(1) Å, которые хорошо согласуются с ранее полученными данными [17].
Рис. 1.
Экспериментально полученная, теоретическая и разностная рентгенограммы синтезированного порошка Pr1.95La0.05CuO4 (вертикальными штрихами показаны теоретические положения рефлексов).
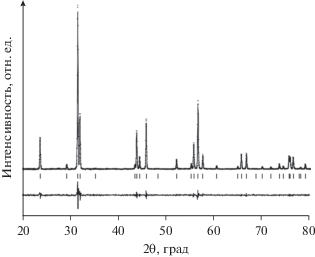
Для изучения воздействия лазерной обработки на топологию поверхности GDC было проведено исследование зависимости глубины профиля, вытравленной лазерным пучком, от количества проходов в режиме “основной проход” (табл. 2). На рис. 2 приведены изображения поперечного профиля поверхности GDC, а также ее 3D-модель при варьировании количества “основных” проходов лазерного пучка. Анализ полученных данных показал, что применение лазерной обработки приводило к формированию столбчатой упорядоченной структуры поверхности, состоящей из островков квадратной формы. Увеличение количества проходов лазерного пучка способствовало повышению глубины профиля, величина которого увеличивалась от 3 мкм (1 проход) до 20 мкм (5 проходов). Следует отметить, что увеличение количества проходов лазерного пучка свыше 3 начинало приводить к разрушению упорядоченной структуры поверхности GDC (рис. 2в). Таким образом, для максимального сохранения упорядоченной структуры рельефа модифицированной поверхности GDC количество проходов лазерного пучка не должно превышать трех.
Таблица 2.
Описание образцов твердоэлектролитных мембран GDC, поверхностность которых была модифицирована с использованием различных режимов лазерной обработки
Маркировка образца | Режим обработки | Глубина профиля, мкм |
---|---|---|
L0 | Без обработки: исходный спеченный образец GDC | – |
L1 | Основной проход – 1 раз, чистящий проход – 1 раз, термическая обработка – при 900°С в течение 4 ч |
3.0–3.5 |
L3 | Основной проход – 3 раза, чистящий проход – 1 раз, термическая обработка – при 900°С в течение 4 ч |
11–12 |
L5 | Основной проход – 5 раз, чистящий проход – 1 раз, термическая обработка – при 900°С в течение 4 ч |
18–20 |
Рис. 2.
Топология поверхности твердого электролита GDC, формируемая в зависимости от количества “основных” проходов лазерного луча: а – 1, б – 3, в – 5 (изображения слева–направо: сканируемая область, профиль поверхности вдоль обозначенной направляющей, 3D-изображение, указатель глубины рельефа).
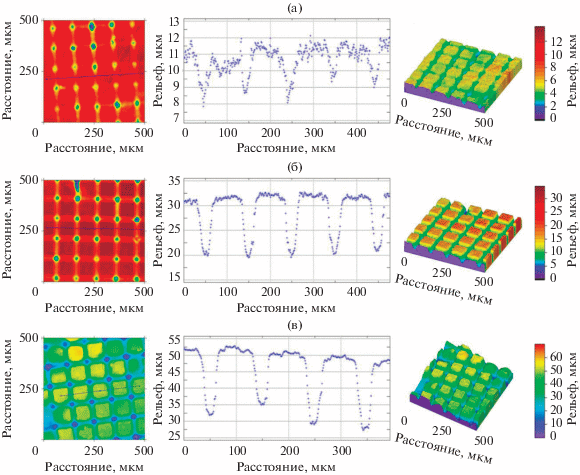
На рис. 3 представлены РЭМ-изображения микроструктуры поверхности твердого электролита GDC, обработанной лазерным излучением, а также электродного слоя PLCO, нанесенного методом трафаретной печати на модифицированную GDC. Из приведенных изображений видно, что поверхность GDC имеет упорядоченную структуру, состоящую из островков квадратной формы и канавок, вытравленных лазерным пучком. Электродный слой PLCO однородно покрывает как канавки, так и сами островки (рис. 3б). Следует отметить, что он имеет пористую структуру, однороден по толщине и обладает хорошей адгезией к поверхности твердого электролита. Толщина электродного слоя PLCO во всех случаях составляла примерно 16 (±1) мкм.
Рис. 3.
(а) Изображение модифицированной лазерным излучением поверхности твердого электролита GDC (вид сверху); (б) изображение микроструктуры электродного слоя PLCO, нанесенного методом трафаретной печати на модифицированную поверхность твердого электролита GDC (вид сбоку).
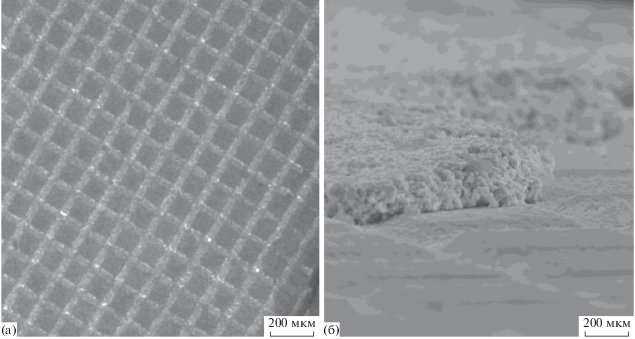
На рис. 4 представлены типичные спектры электродного импеданса границы PLCO/GDC при 713 (±2)°C на воздухе при различной модификации поверхности твердого электролита GDC. Для удобства сравнения приведенных спектров была проведена компенсация сопротивления электролита, определяемого по величине высокочастотной отсечки на действительную ось сопротивлений. Общее поляризационное сопротивление (Rη) электрода рассчитывали, исходя из разницы между низко- и высокочастотной отсечками импедансного спектра на действительную ось сопротивлений, и с учетом нормирования на площадь электрода. Из рисунка видно, что модификация поверхности твердого электролита GDC способствует снижению величины Rη. При этом на начальном этапе повышение глубины профиля формируемого рельефа обеспечивает двукратное снижение поляризационного сопротивления границы электрод/электролит. Дальнейшее увеличение глубины профиля оказывает не такое заметное воздействие на электрохимические характеристики, что, по всей видимости, связано с частичным разрушением упорядоченной структуры поверхности GDC в случае многократного воздействия лазерного пучка.
Рис. 4.
Спектры электродного импеданса границы PLCO/GDC при 713 (±2)°С на воздухе для различной топологии поверхности твердого электролита GDC, формируемой в зависимости от количества “основных” проходов лазерного луча: L0 – без лазерной обработки; L1 – 1; L3 – 3; L5 – 5.
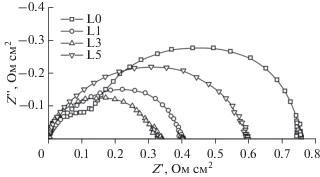
На рис. 5 приведены температурные зависимости общего поляризационного сопротивления электрода PLCO, нанесенного на поверхность твердого электролита GDC, модифицированную лазерным излучением. Полученные зависимости линейны во всем исследованном интервале температур и демонстрируют термоактивационный характер. Следует отметить, что повышение глубины профиля формируемого рельефа поверхности GDC способствует снижению величины кажущейся энергии активации (Ea) от 1.32 эВ (немодифицированный образец – L0) до 1.18 эВ (образец L3). Согласно полученным данным, во всем исследованном интервале температур минимальная величина поляризационного сопротивления достигается при формировании глубины рельефа около 11–12 мкм (образец L3). Вместе с тем переход от исходной поверхности твердого электролита GDC к ее модифицированному варианту путем формирования упорядоченной столбчатой структуры обеспечивает двукратное снижение величины Rη (от 0.87 Ом см2 (L0) [23] до 0.40 Ом см2 (L3) при 700°С на воздухе). Таким образом, применение метода лазерной обработки для формирования заданной топологии поверхности твердого электролита представляет собой перспективный технологический подход, позволяющий повысить электрохимическую активность границы электрод/электролит.
ЗАКЛЮЧЕНИЕ
Проведено комплексное исследование влияния лазерной обработки поверхности твердого электролита GDC на топологию формируемого рельефа. Установлено, что при использовании профиля обработки в виде сетки с толщиной линий 50 мкм и шагом 100 мкм происходит формирование столбчатой упорядоченной структуры, состоящей из островков квадратной формы. Показано, что увеличение количества проходов лазерного пучка способствовало повышению глубины профиля от 3 мкм (1 проход) до 20 мкм (5 проходов). Вместе c тем увеличение количества проходов лазерного пучка свыше 3 приводило к разрушению упорядоченной структуры поверхности GDC. Исследование влияния различной топологии поверхности GDC на электрохимическую активность катодного материала PLCO в реакции восстановления кислорода показало, что оптимальной является упорядоченная столбчатая структура GDC с глубиной профиля рельефа около 11–12 мкм. В случае катодного материала PLCO переход от исходной поверхности твердого электролита GDC к ее модифицированному варианту обеспечивает двукратное снижение величины поляризационного сопротивления (от 0.87 Ом см2 (исходный образец) до 0.40 Ом см2 (модифицированная поверхность GDC) при температуре 700°С на воздухе). Таким образом, формирование заданной топологии границы электрод/электролит с помощью лазерной обработки представляет собой эффективный технологический способ повышения ее электрохимической активности. Кроме того данный метод может быть использован для локального уменьшения толщины твердоэлектролитной мембраны при создании ТОТЭ. В совокупности эти два фактора обеспечивают эффективную возможность снижения рабочих температур ТОТЭ без потери мощностных характеристик.
Список литературы
Cassidy, M., Trends in the processing and manufacture of solid oxide fuel cells, Wiley Interdiscip. Rev.: Energy Environ., 2017, vol. 6, p. e248.
Gao, Z., Mogni, L.V., Miller, E.C., Railsback, J.G., and Barnett, S., A perspective on low-temperature solid oxide fuel cells, Energy Environ. Sci., 2016, vol. 9, p. 1602.
Kilner, J.A. and Burriel, M., Materials for intermediate-temperature solid-oxide fuel cells, Annu. Rev. Mater. Res., 2014, vol. 44, p. 365.
Nédélec, R., Uhlenbruck, S., Sebold, D., Haanappel, V.A.C., Buchkremer, H.P., and Stöver, D., Dense yttria-stabilised zirconia electrolyte layers for SOFC by reactive magnetron sputtering, J. Power Sources, 2012, vol. 205, p. 157.
Solovyev, A.A., Shipilova, A.V., Ionov, I.V., Kovalchuk, A.N., Rabotkin, S.V., and Oskirko, V.O., Magnetron-sputtered YSZ and CGO electrolytes for SOFC, J. Electron. Mater., 2016, vol. 45, p. 3921.
Sønderby, S., Christensen, B.H., Almtoft, K.P., Nielsen, L.P., and Eklund, P., Industrial-scale high power impulse magnetron sputtering of yttria-stabilized zirconia on porous NiO/YSZ fuel cell anodes, Surf. Coat. Technol., 2015, vol. 281, p. 150.
Hidalgo, H., Reguzina, E., Millon, E., Thomann, A.L., Mathias, J., Boulmer-Leborgne, C., Sauvage, T., and Brault, P., Yttria-stabilized zirconia thin films deposited by pulsed-laser deposition and magnetron sputtering, Surf. Coat. Technol., 2011, vol. 205, p. 4495.
Connor, P.A., Yue, X., Savaniu, C.D., Price, R., Triantafyllou, G., Cassidy, M., Kerherve, G., Payne, D.J., Maher, R.C., Cohen, L.F., Tomov, R.I., Glowacki, B.A., Kumar, R.V., and Irvine, J.T.S., Tailoring SOFC electrode microstructures for improved performance, Adv. Energy Mater., 2018, vol. 8, p. 1800120.
Sreedhar, I., Agarwal, B., Goyal, P., and Singh, S.A., Recent advances in material and performance aspects of solid oxide fuel cells, J. Electroanal. Chem., 2019, vol. 848, p. 113315.
Esquirol, A., Brandon, N.P., Kilner, J.A., and Mogensen, M., Electrochemical characterization of La0.6Sr0.4Co0.2Fe0.8O3 cathodes for intermediate-temperature SOFCs, J. Electrochem. Soc., 2004, vol. 151, p. A1847.
Chen, D.J., Ran, R., Zhang, K., Wang, J., and Shao, Z.P., Intermediate-temperature electrochemical performance of a polycrystalline PrBaCo2O5 + δ cathode on samarium-doped ceria electrolyte, J. Power Sources, 2009, vol. 188, p. 96.
Pelosato, R., Cordaro, G., Stucchi, D., Cristiani, C., and Dotelli, G., Cobalt based layered perovskites as cathode material for intermediate temperature Solid Oxide Fuel Cells: A brief review, J. Power Sources, 2015, vol. 298, p. 46.
Philippeau, B., Mauvy, F., Mazataud, C., Fourcade, S., and Grenier, J.C., Comparative study of electrochemical properties of mixed conducting Ln2NiO4 + δ (Ln = La, Pr and Nd) and La0.6Sr0.4Fe0.8Co0.2O3 – δ as SOFC cathodes associated to Ce0.9Gd0.1O2 – δ, La0.8Sr0.2Ga0.8Mg0.2O3 – δ and La9SrSi6O26.5 electrolytes, Solid State Ionics, 2013, vol. 249, p. 17.
Nomura, T., Nishimoto, S., Kameshima, Y., and Miyake, M., Electrode properties of doped Pr2NiO4-based oxide cathode for intermediate-temperature SOFCs, J. Ceram. Soc. Jpn., 2012, vol. 120, p. 534.
Lyskov, N.V., Kaluzhskikh, M.S., Leonova, L.S., Mazo, G.N., Istomin, S.Ya., and Antipov, E.V., Electrochemical characterization of Pr2CuO4 cathode for IT-SOFC, Int. J. Hydrogen Energy, 2012, vol. 37, p. 18357.
Kolchina, L.M., Lyskov, N.V., Kuznetsov, A.N., Kazakov, S.M., Galin, M.Z., Meledin, A., Abakumov, A.M., Bredikhin, S.I., Mazo, G.N., and Antipov, E.V., Evaluation of Ce-doped Pr2CuO4 for potential application as a cathode material for solid oxide fuel cells, RSC Adv., 2016, vol. 6, p. 101029.
Kolchina, L.M., Lyskov, N.V., Kazakov, S.M., Mazo, G.N., and Antipov, E.V., Drastic change of electrical conductivity in Pr2CuO4 by isovalent La doping, RSC Adv., 2015, vol. 5, p. 91993.
Wang, W.G. and Mogensen, M., High-performance lanthanum-ferrite-based cathode for SOFC, Solid State Ionics, 2005, vol. 176, p. 457.
Dusastre, V. and Kilner, J.A., Optimisation of composite cathodes for intermediate temperature SOFC applications, Solid State Ionics, 1999, vol. 126, p. 163.
Murray, E.P., Sever, M.J., and Barnett, S.A., Electrochemical performance of (La,Sr)(Co,Fe)O3–(Ce,Gd)O3 composite cathodes, Solid State Ionics, 2002, vol. 148, p. 27.
Leng, Y., Chan, S. H., and Liu, Q., Development of LSCF–GDC composite cathodes for low-temperature solid oxide fuel cells with thin film GDC electrolyte, Int. J. Hydrogen Energy, 2008, vol. 33, p. 3808.
Kolchina, L.M., Lyskov, N.V., Petukhov, D.I., and Mazo, G.N., Electrochemical characterization of Pr2CuO4–Ce0.9Gd0.1O1.95 composite cathodes for solid oxide fuel cells, J. Alloys Compd., 2014, vol. 605, p. 89.
Lyskov, N.V., Kolchina, L.M., Galin, M.Z., and Mazo, G.N., Development of lanthanum-doped praseodymium cuprates as cathode materials for intermediate-temperature solid oxide fuel cells, Solid State Ionics, 2018, vol. 319, p. 156.
Ding, D., Li, X., Lai, S.Y., Gerdes, K., and Liu, M., Enhancing SOFC cathode performance by surface modification through infiltration, Energy Environ. Sci., 2014, vol. 7, p. 552.
Yoon, K. J., Biswas, M., Kim, H., Park, M., Hong, J., Kim, H., Son, J., Lee, J., Kim, B., and Lee, H., Nano-tailoring of infiltrated catalysts for high-temperature solid oxide regenerative fuel cells, Nano Energy, 2017, vol. 36, p. 9.
Cai, G., Zhang, Y., Dai, H., He, S., Ge, L., Chen, H., and Guo, L., Modification of electrode/electrolyte interface by laser micro-processing for solid oxide fuel cell, Materials Letters, 2017, vol. 195, p. 232.
Cebollero, J.A., Laguna-Bercero, M.A., Lahoz, R., Silva, J., Moreno, R., and Larrea, A., Optimization of laser-patterned YSZ–LSM composite cathode-electrolyte interfaces for solid oxide fuel cells, J. Eur. Ceram. Soc., 2019, vol. 39, p. 3466.
Hayashi, H., Kanoh, M., Quan, C.J., Inaba, H., Wang, S., Dokiya, M., and Tagawa, H., Thermal expansion of Gd-doped ceria and reduced ceria, Solid State Ionics, 2000, vol. 132, p. 227.
Дополнительные материалы отсутствуют.