Электрохимия, 2022, T. 58, № 6, стр. 282-294
Влияние плотного слоя с ион-электронной проводимостью на характеристики катода ТОТЭ
А. В. Никонов a, *, И. В. Семенова a, Н. Б. Павздерин a, В. Р. Хрустов a, Л. В. Ермакова b
a Институт электрофизики УрО РАН
620016 Екатеринбург, ул. Амундсена, 106, Россия
b Институт химии твердого тела УрО РАН
620990 Екатеринбург, ул. Первомайская, 91, Россия
* E-mail: nikonov@iep.uran.ru
Поступила в редакцию 24.09.2021
После доработки 09.12.2021
Принята к публикации 24.12.2021
- EDN: RHYMBA
- DOI: 10.31857/S0424857022060093
Аннотация
Исследовано влияние плотных слоев катодных материалов La1 –xSrxCo1 –yFey O3 – δ (x = 0.1, 0.2, 0.3, 0.4; y = 0, 0.2, 0.8), расположенных на поверхности электролита, на поляризационные характеристики пористых катодов. Электродные характеристики были измерены методом импедансной спектроскопии на симметричных образцах с тремя типами электродов: пористый электрод, плотный электрод и двухслойный электрод, состоящий из плотного и пористого слоев. Показано, что введение плотного слоя в структуру катода может оказывать как положительное, так и отрицательное влияние на поляризационное сопротивление. Обнаружено, что влияние плотного слоя на высокочастотный вклад в поляризационное сопротивление коррелирует с удельным поверхностным сопротивлением плотного слоя. Слои из высокопроводящих материалов La1– xSrxCoO3 (x = 0.1, 0.3) приводят к падению поляризационного сопротивления, тогда как слои из материалов La1 ‒ xSrxCo1 –yFeyO3 – δ (x = 0.2, 0.4; y = 0.2, 0.8) – к увеличению поляризационного сопротивления.
ВВЕДЕНИЕ
Твердооксидные топливные элементы (ТОТЭ) – многообещающая экологически чистая технология прямого получения электричества из топлива. Высокие рабочие температуры ТОТЭ (до 1000°С) определяют их высокую энергетическую эффективность (электрический КПД 40–60% [1]), а также позволяют использовать широкий спектр углеводородов в качестве топлива, что выделяет ТОТЭ среди других типов топливных элементов. Кроме того, использование тепловой энергии, генерируемой при работе ТОТЭ, может повысить общее значение КПД установки до 90%. Однако именно высокие температуры препятствуют коммерциализации ТОТЭ, вызывая ряд проблем, связанных с герметизацией, морфологической стабильностью электродов и химической стабильностью компонентов топливного элемента, что приводит к высокой стоимости элементов и сокращению срока их службы. Поэтому в настоящее время значительные усилия разработчиков направлены на снижение рабочих температур ТОТЭ с сохранением высокой удельной мощности. Для достижения этой цели ведутся как разработки новых функциональных материалов [2, 3], так и совершенствуется микроструктура ТОТЭ [4, 5].
В обзоре [5] было продемонстрировано, что создание различных гетероструктур для функциональных компонентов ТОТЭ (катода, электролита, анода) позволяет существенно повысить производительность топливных элементов за счет интенсификации и расширения области протекания электродных реакций и увеличения ионной проводимости. В частности, введение плотного слоя со смешанной ион-электронной проводимостью на границу электролит/пористый катод приводит к снижению поляризационных потерь [6–10] и улучшению долговременной стабильности элемента [11]. Однако работ, посвященных этой структуре, крайне мало по сравнению с общим объемом литературы по электродам ТОТЭ. В приведенных исследованиях рассматривались системы, отличающиеся как катодными, так и электролитными материалами. И если в работах [7, 8, 10] поляризационное сопротивление двухслойного электрода, состоящего из пористого и плотного слоев, на ~30% ниже, чем поляризационное сопротивление пористого электрода, то в работе [6] поляризационное сопротивление катода упало в 3 раза при введении плотного катодного слоя на поверхность электролита. При этом во всех исследованиях [6–11] толщина плотных подслоев не превышала 1 мкм.
В представленной работе исследовано влияние на электродные характеристики пористых катодов плотных слоев катодных материалов La1 – xSrxCo1 –yFeyO3 – δ (x = 0.1, 0.2, 0.3, 0.4; y = 0, 0.2, 0.8) толщиной несколько мкм.
ЭКСПЕРИМЕНТАЛЬНАЯ ЧАСТЬ
Наноразмерный порошок электролитного материала Ce0.73Gd0.27O2 – δ (GDC) был получен методом лазерного испарения в ИЭФ УрО РАН. В качестве исходных катодных материалов использовали коммерческий порошок La0.6Sr0.4Co0.8Fe0.2O3 – δ (LSCF-4080) (Kceracell Co., Ltd.) и порошки La0.9Sr0.1CoO3 – δ (LSC-10), La0.7Sr0.3CoO3 – δ (LSC‑30), La0.8Sr0.2Co0.2Fe0.8O3 – δ (LSCF-2020), La0.6Sr0.4Co0.2Fe0.8O3 – δ (LSCF-4020), синтезированные в реакциях горения в ИХТТ УрО РАН. В качестве исходных реактивов были использованы La2O3 (ч. д. а.), SrCO3 (ч. д. а.), Fe(NO3)3 (ч. д. а.) и Co(NO3)2 (х. ч.). Соответствующие навески предварительно прокаленного при 900°С La2O3 и SrCO3 растворяли в 0.1 N растворе HNO3, Fe(NO3)3 и Co(NO3)2 – в воде. В качестве горючих органических веществ использовали глицин (AMK Ltd., Россия) и/или лимонную кислоту квалификации “ч.” (Weifang Ensigh Industry Co. Ltd., Китай) в количестве, обеспечивающем проведение реакции горения в области восстановительного горения. Продукты реакции перешихтовывали и постадийно отжигали при 850, 950 и 1100°С для удаления остатков органической фазы и формирования кристаллической структуры. Фазовый состав и удельную поверхность синтезированных порошков определяли с помощью рентгеновского дифрактометра D8 Discover (Bruker AXS, Германия) и анализатора TriStar 3000 (Micromeritics, США), соответственно. Обработка данных РФА выполнена с использованием программы TOPAS 3.
Порошок GDC состоял из частиц, близких к сферической форме, со средним размером 25 нм. По данным BET, размер частиц катодных материалов составлял 0.5–2.5 мкм. Все порошки были однофазны: GDC имел кубическую флюоритную структуру, катодные материалы – структуру перовскита (пр. гр. R-3c). Характеристики исходных порошков представлены в табл. 1.
Таблица 1.
Характеристики исходных порошков
Порошок | SBET, м2/г | dBET, мкм | Параметр решетки, Å | γXRD, г/см3 |
---|---|---|---|---|
GDC | 34.2 | 0.03 | a = 5.424(4)* | 7.25 |
LSC-10 | 0.32 | 2.63 | a = 5.436(3), c = 13.106(6) | 7.14 |
LSC-30 | 0.39 | 2.28 | a = 5.442(2), c = 13.199(6) | 6.76 |
LSСF-2020 | 2.98 | 0.31 | a = 5.501(3), c = 13.407(7) | 6.60 |
LSCF-4020 | 0.46 | 2.05 | a = 5.481(3), c = 13.382(8) | 6.36 |
LSCF-4080 | 11.8 | 0.08 | a = 5.493(4), c = 13.453(9) | 6.50 |
Для определения химического взаимодействия между катодными материалами и GDC был проведен РФА композитов на их основе. Исходные порошки были тщательно смешаны в весовом соотношении 1 : 1, спрессованы и спечены при двух температурах 1200 и 1300°С в течение 10 ч.
Измерение линейного расширения материалов проводили на образцах в виде брусков, спеченных до плотностей, близких к теоретическим, с помощью дилатометра Dil 402C (NETZSCH, Германия).
Проводимость катодных материалов измеряли 4-зондовым методом на постоянном токе. Исходные порошки были спрессованы в образцы в форме прямоугольных параллелепипедов, которые спекали при 1400°С в течение 10 ч. Исследования проводили с помощью прецизионного измерителя импеданса LCR-76100 (GW Instek, Тайвань).
Для исследования электродных характеристик были изготовлены симметричные образцы на электролите GDC с электродами трех типов: пористый электрод (PE); плотный электрод (DE) и двухслойный электрод, состоящий из плотного и пористого слоев (DE + PE). Пасты для нанесения электродов были изготовлены путем смешивания порошков катодных материалов с 5 вес. % поливинилбутираля. В качестве растворителя использовали изопропиловый спирт, количеством которого варьировали вязкость паст. Плотные слои наносили методом центрифугирования. Скорость вращения образца при нанесении составляла 2300 об/мин. Плотные слои припекали при 1200 и 1300°C с выдержкой 5 ч. Пористые слои наносились методом трафаретной печати и припекались при 1100°C с выдержкой 1 ч. Исследование микроструктуры приготовленных образцов было выполнено на сканирующем электронном микроскопе JSM-6390LV (JEOL Ltd., Япония) с приставкой ЭДС INCA Energy350X-Max50 (Oxford Instruments, Великобритания). Обработка микрофотографий была выполнена с помощью программы ImageJ. Поляризационное сопротивление катодов исследовали методом импедансной спектроскопии с помощью потенциостата/гальваностата P-40X, совмещенного с модулем измерения импеданса (ООО “Electrochemical Instruments”, Россия). Спектры импеданса снимали при напряжении 15 мВ в диапазоне частот 0.5 МГц–0.1 Гц.
РЕЗУЛЬТАТЫ И ОБСУЖДЕНИЕ
На рис. 1 представлены дифрактограммы исходных порошков и композитов, спеченных при различных температурах. Рентгенофазовый анализ композитов не обнаружил образование каких-либо вторичных фаз. Однако, следует обратить внимание, что параметры решетки составляющих композита изменяются с ростом температуры спекания. Для примера в табл. 2 приведены данные для композитов на основе LSC-30 и LSCF-4080. Элементарная ячейка GDC увеличивается, тогда как для электродных материалов наблюдается уменьшение объема элементарной ячейки, что связано с диффузией катионов из катодного материала в электролит [12]. Увеличение параметра решетки GDC, скорее всего, объясняется встраиванием катионов лантана и/или стронция в решетку флюорита. Тогда как встраивание кобальта и/или железа должно было привести к уменьшению элементарной ячейки GDC из-за их малых ионных радиусов. Однако диффузия переходных металлов в структуру электролита возможна по границам зерен. В частности, в работе [13], где взаимодействие на границе между плотными образцами Ce0.8Gd0.2O2 – δ и La0.8Sr0.2Co1 –yFeyO3 – δ (y = 0, 0.2, 0.8 и 1) исследовалось методом масс-спектрометрии вторичных ионов, наблюдалась миграция большого количества стронция, кобальта и железа внутри электролита.
Рис. 1.
Дифрактограммы исходных катодных материалов: (а) LSC-10, (б) LSC-30, (в) LSCF-2020, (г) LSCF-4020, (д) LSCF-4080 и композитов на их основе, прокаленных при 1200 и 1300°С в течение 10 ч.
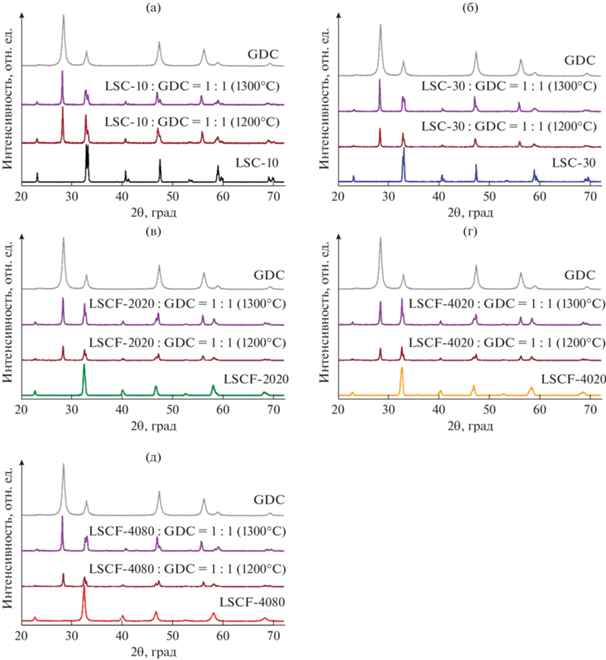
Таблица 2.
Данные РФА для компонентов композитов при различной термической обработке
Температура спекания | Параметр решетки, Å | |||
---|---|---|---|---|
LSC-30 : GDC = 1 : 1 | LSCF-4080 : GDC = 1 : 1 | |||
GDC | LSC-30 | GDC | LSCF-4080 | |
Исходный | a = 5.424 | a = 5.442, c = 13.199 | a = 5.424 | a = 5.493, c = 13.453 |
1200 | a = 5.448 | a = 5.413, c = 13.352 | a = 5.432 | a = 5.503, c = 13.400 |
1300 | a = 5.459 | a = 5.436, c = 13.185 | a = 5.435 | a = 5.503, c = 13.405 |
На рис. 2 представлены результаты измерения линейного расширения исследуемых материалов. Видно, что кривые расширения всех исследованных электродных материалов имеют перегиб при определенной температуре, зависящей от их химического состава, что связано с изменением стехиометрии кислорода при нагревании, приводящим к понижению степени окисления катиона переходного металла и, следовательно, ослаблению связи металл–кислород [14]. Оба фактора определяют химическое расширение и существенно влияют на коэффициент термического расширения (КТР). Усредненные по соответствующим температурным областям значения КТР суммированы в табл. 3. Видно, что, наиболее близкими значениями КТР к электролиту GDC обладают составы с высоким содержанием железа LSCF-2020 и LSCF-4020.
Таблица 3.
КТР исследуемых материалов
Состав | ΔT, °С | КТР, 10–6 К–1 |
---|---|---|
LSC-10 | 100–1050 | 19.9 ± 0.1 |
1050–1200 | 30.0 ± 0.3 | |
LSC-30 | 100–825 | 17.6 ± 0.1 |
825–1200 | 30.8 ± 0.2 | |
LSCF-2020 | 100–815 | 14.5 ± 0.1 |
815–1200 | 20.6 ± 0.2 | |
LSCF-4020 | 100–725 | 14.0 ± 0.1 |
725–1200 | 22.8 ± 0.1 | |
LSCF-4080 | 100–750 | 15.1 ± 0.1 |
750–1200 | 24.5 ± 0.1 | |
GDC | 100–1200 | 12.7 ± 0.02 |
Температурные зависимости проводимости электродных материалов представлены на рис. 3. Видно, что наибольшей проводимостью обладают кобальтиты LSC-30 и LSC-10. При этом проводимость ферро-кобальтитов падает при увеличении в их составе Fe и уменьшении Sr. На кривых проводимости LSC-10, LSCF-4020 и LSCF‑4080 наблюдается максимум в области температур 500–600°С. Проводимость LSC-30 монотонно уменьшается с ростом температуры, однако при температурах выше 800°С падение ускоряется. Разные температурные зависимости проводимости LSC-10 и LSC-30 связаны с тем, что увеличение Sr в составе La1 – xSrxCoO3 – δ приводит к уменьшению расстояния Co–O и росту угла Co–O–Co, и, как следствие, происходит переход от полупроводникового типа проводимости к металлическому [15]. Температурные зависимости проводимости многих перовскитных материалов имеют максимум [16–18]. Уменьшение проводимости при высоких температурах объясняется потерей кислорода, что приводит к снижению концентрации и подвижности носителей электрического заряда [18].
На рис. 4 и 5 представлены микрофотографии сколов образцов с двухслойными электродами, плотный слой которых был припечен при 1200 и 1300°С соответственно. Видно, что методом центрифугирования были получены плотные слои толщиной 3–7 мкм. Несмотря на значительное различие КТР катодных материалов и GDC не было обнаружено слоений и других дефектов на границе электролит/плотный электродный слой. Пористость плотных слоев, припеченных при температуре 1200°С, составляла 3–8%. Повышение температуры спекания до 1300°С привело к снижению пористости до 1–5%. Пористость электродных слоев, нанесенных методом трафаретной печати и припеченных при 1100°С, составляла 15–20%.
Рис. 4.
Микрофотографии сколов образцов с двухслойным электродом: (а) LSC-10, (б) LSC-30, (в) LSCF-2020, (г) LSCF-4080. Плотный слой припекался при 1200°С в течение 5 ч. I – слой электролита, II – плотный электродный слой, III – пористый электродный слой.
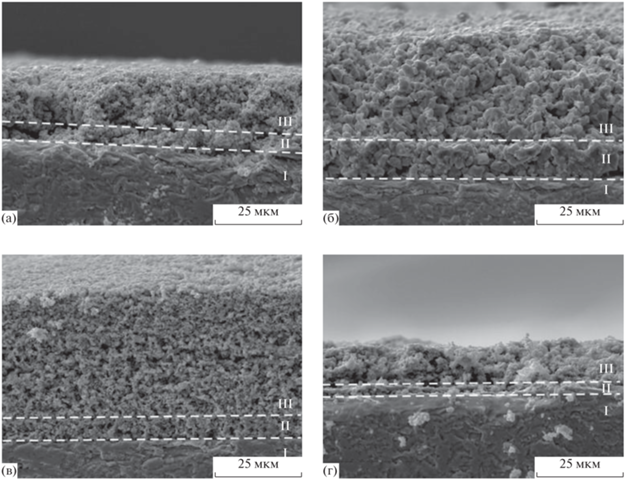
Рис. 5.
Микрофотографии сколов образцов с двухслойным электродом: (а) LSC-10, (б) LSC-30, (в) LSCF-2020, (г) LSCF-4080. Плотный слой припекался при 1300°С в течение 5 ч. I – слой электролита, II – плотный электродный слой, III – пористый электродный слой.
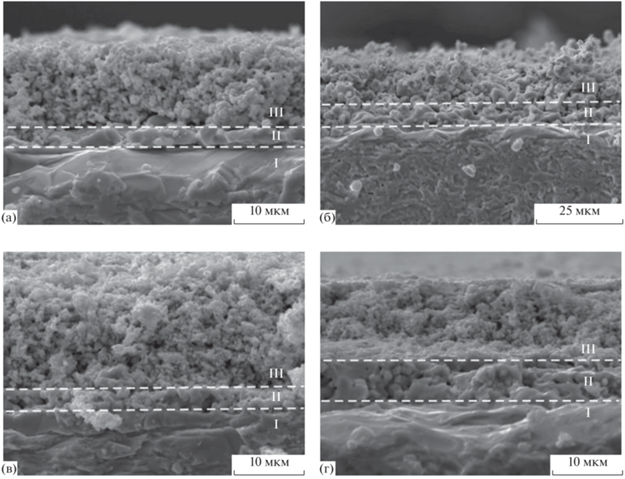
На рис. 6 для примера представлены спектры импеданса катодов LSC-10 и LSCF-4020 с различной структурой, снятые при 750°С. В каждом спектре можно выделить два участка: высокочастотный (HF), который, согласно литературным данным [19], соответствует процессу переноса заряда через границу электролит/электрод, и низкочастотный (LF), который соответствует процессам, происходящим на границе смешанный ион-электронный проводник/газ (адсорбция–десорбция кислорода, диссоциация кислорода, диффузия по поверхности и связь этих процессов) [19]. Анализ спектров импеданса проводили по эквивалентной схеме, состоящей из последовательно соединенных сопротивления Rs и двух элементов (RQ). Сопротивление Rs соответствует омическим потерям и в основном определяется сопротивлением электролита. Элементы (RQ), состоящие из параллельно соединенных сопротивления R и элемента постоянной фазы Q, соответствуют высоко- или низкочастотному процессу.
Рис. 6.
Спектры импеданса катодов: (а) LSC-10 и (б) LSCF-4020 с различной структурой, снятые при 750°С.
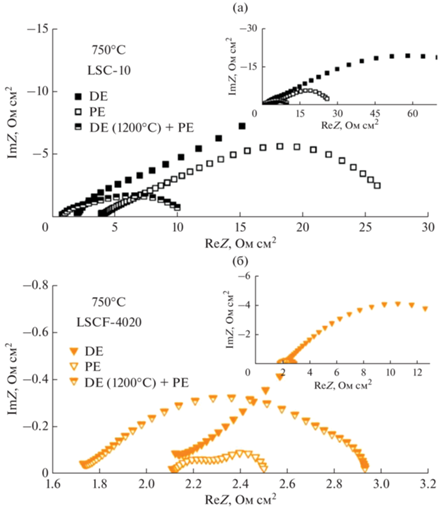
На рис. 7 представлены температурные зависимости полного поляризационного сопротивления исследованных образцов с различной структурой катодов: плотный слой катодного материала, припеченный при 1200°С – DE, пористый электрод, припеченный при 1100°С – PE, и двухслойные электроды, состоящие из плотного и пористых слоев – DE(1200°C) + PE и DE(1300°C) + PE (в скобках указана температура припекания плотных слоев). Поляризационное сопротивление плотных электродов для всех исследованных материалов было в разы больше поляризационного сопротивления пористых электродов. Этот результат ожидаем, так как площадь трехфазной границы для плотных электродов значительно меньше, чем для пористых. Поляризационное сопротивление двухслойных электродов зависело от катодного материала. Видно, что для LSC-10 наблюдается положительный эффект от введения плотного электродного слоя. При 800°С поляризационное сопротивление двухслойного электрода DE(1200°C) + PE в 2 раза меньше поляризационного сопротивления пористого электрода. Формирование плотного слоя при 1200°С не оказало видимого влияния на характеристики катода LSC-30, тогда как припекание плотного слоя при 1300°С привело к росту поляризационного сопротивления в ~4 раза. Как было показано выше, РФА не обнаружил формирования вторичных фаз в смеси LSC-30:GDC, прокаленной при 1300°С, однако косвенно обнаружены диффузионные процессы, которые могли отрицательно повлиять на перенос ионов кислорода через границу электролит/катод. Введение плотного слоя в структуру LSCF катодов повлияло отрицательно на их электродные характеристики: поляризационное сопротивление катодов LSCF-2020, LSCF‑4020 и LSCF-4080 при 800°С выросло в 4.8, 2.4 и 2.6 раза соответственно. Температура припекания плотного слоя практически не сказалась на электродных характеристиках LSCF.
Рис. 7.
Температурные зависимости полного поляризационного сопротивления исследуемых катодов: (а) LSC-10, (б) LSC-30, (в) LSCF-2020, (г) LSCF-4020, (д) LSCF-4080.
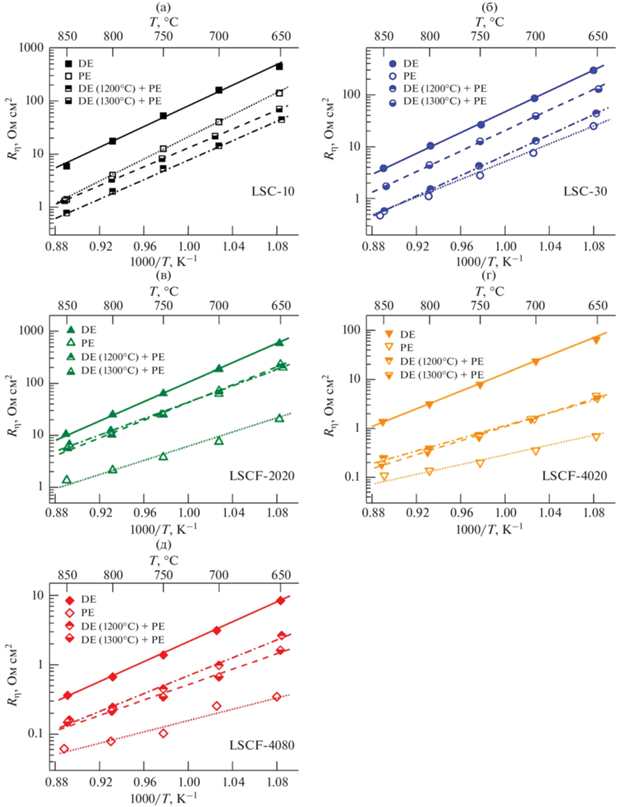
В литературе [6–9] показано, что плотные электродные слои снижают поляризационное сопротивление за счет облегчения переноса ионов кислорода через границу катод/электролит. Результаты разделения полученных спектров импеданса на высоко- (Rη-HF) и низкочастотную (Rη-LF) части представлены на рис. 8, 9. Видно, что для электродов LSCF-2020, LSCF-4020 и LSCF-4080 формирование двухслойной структуры привело как к ухудшению переноса заряда через границу катод/электролит (увеличение Rη-HF), так и к замедлению процессов на границе катод/газ (увеличение Rη-LF). Для катода LSC-30 также наблюдается замедление процессов на границе катод/газ (увеличение Rη-LF) при введении плотного слоя, однако при этом падает Rη-HF, что говорит об улучшении процесса переноса заряда через границу катод/электролит. Для катода LSC-10 обнаружено как значительное падение Rη-HF (при 800°С в 8 раз), так и снижение Rη-LF в 1.27 раза при 800°С. Это свидетельствует об ускорении процессов как на границе катод/электролит, так и на границе катод/газ.
Рис. 8.
Температурные зависимости высокочастотной части (HF) поляризационного сопротивления исследуемых катодов: (а) LSC-10, (б) LSC-30, (в) LSCF-2020, (г) LSCF-4020, (д) LSCF-4080.
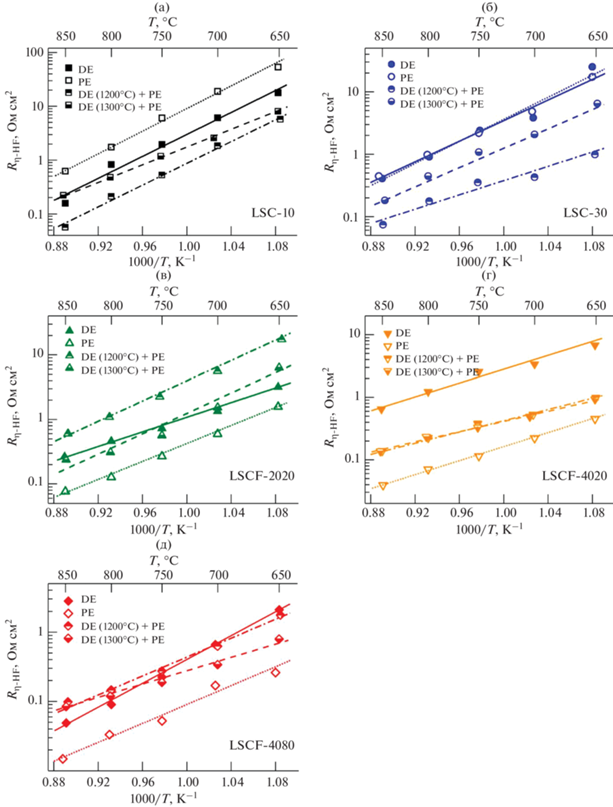
Рис. 9.
Температурные зависимости низкочастотной части (LF) поляризационного сопротивления исследуемых катодов: (а) LSC-10, (б) LSC-30, (в) LSCF-2020, (г) LSCF-4020, (д) LSCF-4080.
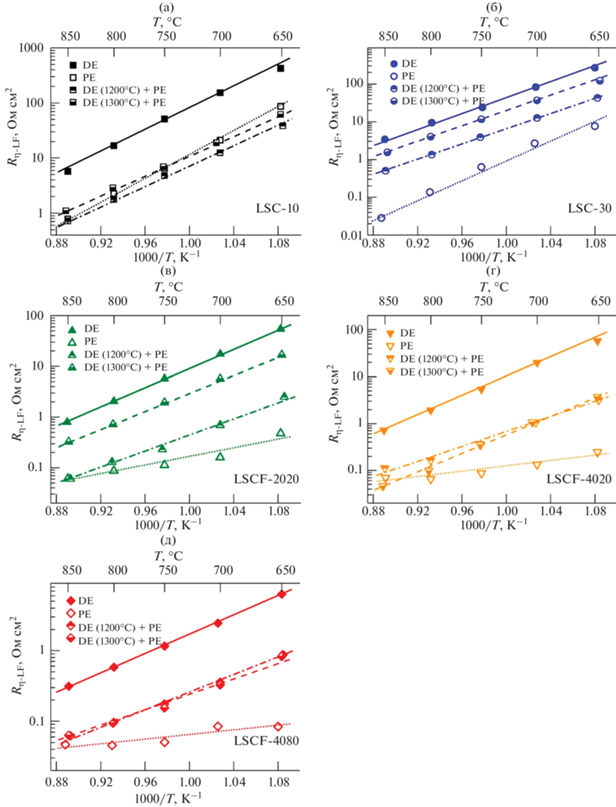
Изменение низкочастотной части поляризационного сопротивления катода при неизменном химическом составе его материала должно быть обусловлено изменением микроструктуры. Таким образом, несмотря то, что пористые слои всех исследуемых электродов были сформированы по одной методике и в одинаковых условиях, добиться идентичности их микроструктуры в однослойных и двухслойных катодах не удалось.
Наблюдаемое изменение Rη-HF при введении плотного слоя коррелирует с данными по проводимости LSC- и LSCF-материалов (рис. 3): высокая проводимость материала плотного слоя приводит к уменьшению высокочастотной части поляризационного сопротивления, тогда как низкая – к увеличению. Так в диапазоне температур 600–900°С полная проводимость LSCF-4080, материала, обладающего наибольшей проводимостью среди исследованных ферро-кобальтитов, приблизительно в 3.5 и 5 раз ниже проводимости с LSC-10 и LSC-30 соответственно. В табл. 4 приведены оценки удельного поверхностного сопротивления (ASR) плотных слоев, припеченных при 1300°С, и отношение значений Rη-HF для пористого и двухслойного электрода. ASR рассчитывали как произведение удельного сопротивления катодного материала при 800°С на толщину плотного слоя (δDE). Значения Rη-HF для PE и DE + PE также были взяты для температуры 800°С. Их отношение характеризует влияние введения плотного слоя в структуру катода: плотный слой приводит к уменьшению поляризационного сопротивления, если отношение больше единицы, и к увеличению сопротивления, если отношение меньше единицы. Из табл. 4 видно, что прослеживается тенденция уменьшения Rη-HF двухслойного электрода с уменьшением ASR плотного слоя. Литературные данные также подтверждают эту оценку. Для плотного слоя La0.6Sr0.4Co0.2Fe0.8O3 толщиной 200 нм при 800°С оценка ARS дает величину 0.09 мкОм см2, что соответствует снижению полного поляризационного сопротивления в 1.7 раза [6], а для плотного слоя из того же материала толщиной 700 нм ASR должна составлять 0.33 мкОм см2, и, по данным работы [7], приводит к снижению полного поляризационного сопротивления в 1.4 раза. Следует заметить, что в приведенных значениях ASR не учитывалась микроструктура плотных слоев, а предполагалось, что они обладают полной плотностью. Однако, скорее всего, изменение скорости переноса ионов кислорода через границу катод/электролит должно быть связано не с полной проводимостью материала плотного слоя, а с ее ионной составляющей. При 800°С ионная проводимость материалов LSC-30, LSCF-2020, LSCF-4020 и LSCF-4080 составляет 0.02 [20], 0.0023 [21], 0.008 [22] и 0.058 [21] См/см соответственно. К сожалению, не удалось найти точных данных о ионной проводимости LSC-10. В работе [22] указано, что при 830°С числа переноса ионов кислорода в составах La1– xSrxCoO3 при 0 ≤ x ≤ 0.4 лежат в диапазоне 0.0001–0.0007, следовательно, минимальная оценка ионной проводимости для состава La0.9Sr0.1CoO3 дает величину 0.12 См/см. Таким образом, в исследованных материалах ионная проводимость коррелирует с полной проводимостью и, следовательно, можно полагать, что найденная тенденция снижения Rη-HF при уменьшении ASR плотного слоя выполняется и для удельного поверхностного сопротивления, обусловленного ионным переносом.
ЗАКЛЮЧЕНИЕ
В ходе работы были исследованы характеристики катодов La1– xSrxCo1 –yFeyO3 – δ (x = 0.1, 0.2, 0.3, 0.4; y = 0, 0.2, 0.8) с тремя различными структурами: пористый электрод, плотный электрод и двухслойный электрод, состоящий из плотного и пористого слоев. Плотные слои формировались методом центрифугирования, и их толщина варьировалась от 3 до 7 мкм. Показано, что введение плотного слоя в структуру катода может оказывать как положительное, так и отрицательное влияние на поляризационное сопротивление. Обнаружена корреляция между изменением высокочастотного вклада в поляризационное сопротивление, которое вызывает введение в структуру катода плотного слоя, и удельным поверхностным сопротивлением вводимого плотного слоя, которое зависит от его толщины и проводимости материала плотного слоя. Таким образом, использование высокопроводящего материала со смешанной ион-электронной проводимостью должно позволить формировать плотные слои, не приводящие к ухудшению катодных характеристик, но при этом обладающих достаточной толщиной, чтобы взять на себя роль несущего элемента в топливном элементе. Это позволит уменьшить толщину слоя электролита и тем самым снизить омические потери в топливном элементе.
Список литературы
High-Temperature Solid Oxide Fuel Cells for the 21st Century, Eds. Kendall, K. and Kendall, M., Amsterdam: Elsevier, 2015. 508 p.
Mahato, N., Banerjee, A., Gupta, A., Omar, S., and Balani, K., Progress in material selection for solid oxide fuel cell technology: A review, Prog. Mater. Sci., 2015, vol. 72, p. 141.
Sreedhar, I., Agarwal, B., Goyal, P., and Singh, S.A., Recent advances in material and performance aspects of solid oxide fuel cells, J. Electroanal. Chem., 2019, vol. 848, p. 113315.
Shin, J.W., Go, D., Kye, S.H., Lee, S., and An, J., Review on process-microstructure-performance relationship in ALD-engineered SOFCs, J. Phys.: Energy, 2019, vol. 1, p. 042002.
Пикалова, Е.Ю., Калинина, Е.Г. Подходы к повышению эффективности твердооксидных топливных элементов на основе керамических мембран со смешанной проводимостью. Успехи химии. 2021. Т. 90. С. 703. [Pikalova, E.Yu. and Kalinina, E.G., Solid oxide fuel cells based on ceramic membranes with mixed conductivity: improving efficiency, Russ. Chem. Rev., 2021, vol. 90, p. 703.]
Hildenbrand, N., Boukamp, B.A., Nammensma, P., and Blank, D.H.A., Improved cathode/electrolyte interface of SOFC, Solid State Ionics, 2011, vol. 192, p. 12.
Dumaisnil, K., Fasquelle, D., Mascot, M., Rolle, A., Roussel, P., Daviero-Minaud, S., Duponchel, B., Vannier, R.-N., and Carru, J.-C., Synthesis and characterization of La0.6Sr0.4Co0.8Fe0.2O3 films for solid oxide fuel cell cathodes, Thin Solid Films, 2014, vol. 553, p. 89.
Chrzan, A., Karczewski, J., Gazda, M., Szymczewska, D., and Jasinski, P., Investigation of thin perovskite layers between cathode and doped ceria used as buffer layer in solid oxide fuel cells, J. Solid State Electrochem., 2015, vol. 19, p. 1807.
Dumaisnil, K., Carru, J.-C., Fasquelle, D., Mascot, M., Rolle, A., and Vannier, R.-N., Promising performances for a La0.6Sr0.4Co0.8Fe0.2O3 – δ cathode with a dense interfacial layer at the electrode-electrolyte interface, Ionics, 2017, vol. 23, p. 2125.
Павздерин, Н.Б., Соловьев, А.А., Никонов, А.В., Шипилова А.В., Работкин, С.В., Семёнов, В.А., Гренадеров, А.С., Оскомов, К.В. Формирование плотного подслоя La(Sr)Fe(Ga)O3 на границе электролит/пористый катод методом магнетронного распыления и его влияние на характеристики электрода. Электрохимия. 2021. Т. 57. С. 301. [Pavzderin, N.B., Solovyev, A.A., Nikonov, A.V., Shipilova, A.V., Rabotkin, S.V., Semenov, V.A., Grenaderov, A.S., and Oskomov, K.V., Formation of a dense La(Sr)Fe(Ga)O3 interlayer at the electrolyte/porous cathode interface by magnetron sputtering and its effect on the cathode characteristics, Russ. J. Electrochem., 2021, vol. 57, p. 519.]
De Vero, J.C., Develos-Bagarinao, K., Kishimoto, H., Ishiyama, T., Yamaji, K., Horita, T., and Yokokawa, H., Enhanced stability of solid oxide fuel cells by employing a modified cathode-interlayer interface with a dense La0.6Sr0.4Co0.2Fe0.8O3 – δ thin film, J. Power Sources, 2018, vol. 377, p. 128.
Khan, M.Z., Song, R.-H., Mehran, M.T., and Lee, S., Controlling cation migration and inter-diffusion across cathode/interlayer/electrolyte interfaces of solid oxide fuel cells: A review, Ceram. Int., 2021, vol. 47, p. 5839.
Sakai, N., Kishimoto, H., Yamaji, K., Horita, T., Brito, M.E., and Yokokawa, H., Degradation behavior at interface of LSCF cathodes and rare earth doped ceria, ECS Trans., 2007, vol. 7, p. 389.
Tu, H.Y., Takeda, Y., Imanishi, N., and Yamamoto, O., Ln0.4Sr0.6Co0.8Fe0.2O3 – δ (Ln = La, Pr, Nd, Sm, Gd) for the electrode in solid oxide fuel cells, Solid State Ionics, 1999, vol. 117, p. 277.
Mineshige, A., Inaba, M., Yao, T., and Ogumi, Z., Crystal structure and metal–insulator transition of La1 –xSrxCoO3, J. Solid State Chem., 1996, vol. 121, p. 423.
Абакумов, А.М., Розова, М.Г., Антипов, Е.В. Сложные оксиды марганца со структурой браунмиллерита: синтез, кристаллохимия и свойства. Успехи химии. 2004. Т. 73. С. 917. [Abakumov, A.M., Rozova, M.G., and Antipov, E.V., Complex manganese oxides with the brownmillerite structure: synthesis, crystal chemistry and properties, Russ. Chem. Rev., 2004, vol. 73, p. 847.]
Taskin, A.A., Lavrov, A.N., and Ando, Y., Achieving fast oxygen diffusion in perovskites by cation ordering, Appl. Phys. Letters, 2005, vol. 86, p. 91910(1–3).
Parfitt, D., Chroneos, A., Kilner, J.A., and Grimes R.W., Molecular dynamics study of oxygen diffusion in Pr2NiO4 + δ, Physical Chemistry Chemical Physics, 2010, vol. 12, p. 6834.
dos Santos-Gomez, L., Porras-Vazquez, J.M., Losilla, E.R., Martinb, F., Ramos-Barrado, J.R., and Marrero-Lopez, D., LSCF–CGO nanocomposite cathodes deposited in a single step by spraypyrolysis, J. Europ. Ceram. Soc., 2018, vol. 38, p. 1647.
Krumpelt, M., Ralph, J., Cruse, T., and Bae, J.-M., Materials for low-temperature solid oxide fuel cells, Proceedings of 5th European SOFC Forum, 2002, p. 215.
Ullmann, H., Trofimenko, N., Tietz, F., Stöver, D., and Ahmad-Khanlou, A., Correlation between thermal expansion and oxide ion transport in mixed conducting perovskite-type oxides for SOFC cathodes, Solid State Ionics, 2000, vol. 138, p. 79.
Kharton, V.V., Naumovich, E.N., Vecher, A.A., and Nikolaev, A.V., Oxide ion conduction in solid solutions Ln1 –xSrxCoO3 – δ (Ln = La, Pr, Nd), J. Solid State Chem., 1995, vol. 120, p. 128.
Дополнительные материалы отсутствуют.