Журнал физической химии, 2019, T. 93, № 10, стр. 1545-1550
Влияние искрового плазменного спекания на состав, структуру и электропроводность азотзамещенных углеродных нанотрубок, модифицированных наночастицами кобальта
С. А. Черняк a, *, А. С. Иванов a, К. И. Маслаков a, Р. Ю. Новоторцев a, Дж. Ни b, С. В. Савилов a, В. В. Лунин a
a Московский государственный университет имени М.В. Ломоносова, Химический факультет
119991 Москва, Россия
b Университет Сучоу, Факультет физики и технологии
215000 Сучжоу, КНР
* E-mail: chernyak.msu@gmail.com
Поступила в редакцию 15.03.2019
После доработки 15.03.2019
Принята к публикации 09.04.2019
Аннотация
Методом искрового плазменного спекания (ИПС) получены новые материалы на основе азотзамещенных нанотрубок (N-УНТ), на поверхность которых нанесены наночастицы металлического кобальта. Исследована морфология, микроструктура и фазовый состав таких композитов, измерена их электропроводность. Показано, что подбор условий компактизации нанотрубок с кобальтом в условиях ИПС позволяет предотвратить удаление атомов азота из углеродной структуры и существенно увеличить электропроводность исходного материала с 450 См/м у N-УНТ до ∼4000 См/м у спеченных образцов.
Углеродные нанотрубки (УНТ) – первый структурированный углеродный наноматериал, производимый и используемый в промышленных масштабах. Их широкое применение в таких областях науки и техники, как создание полимерных композитов и одежды нового поколения, катализ, микроэлектроника, накопление и хранение энергии, обусловлено высокой механической прочностью, электропроводностью, химической инертностью, термостабильностью и развитой поверхностью [1]. Немаловажное свойство УНТ – возможность структурной и поверхностной модификации для варьирования характеристик материала. Среди множества способов варьирования свойств нанотрубок можно выделить внедрение в структуру графеновых листов атомов азота с получением N-УНТ. Такой подход позволяет изменять электрохимические свойства материала, формирует электронно-избыточную поверхность, обладающую полярностью, и приводит к появлению каталитической и электрокаталитической активности [2–4].
Один из существенных недостатков УНТ – их низкая насыпная плотность, для увеличения которой могут применяться разные методики прессования и спекания. В последнее время для компактизации УНТ внимание исследователей все больше привлекает метод искрового плазменного спекания (ИПС), который заключается в одновременном воздействии на образец высоких давлений и температур [5]. ИПС отличает высокая экспрессность, так как нагрев образца происходит быстро за счет подачи импульсного постоянного тока. Использование в ИПС для нагрева вещества пропускания импульсов электрического тока позволяет существенно снизить температуру и сократить время спекания по сравнению с обычным спеканием и горячим прессованием. Импульс тока высокой энергии мгновенно порождает искровую плазму при высоких локальных температурах (до 10000°С) между частицами, что приводит к высокоскоростной консолидации порошка.
ИПС часто используется в синтезе различных композитных материалов, в том числе и образцах, в составе которых присутствуют УНТ. В основном нанотрубки используют в качестве добавки, улучшающей физические и химические свойства композита (электропроводность, прочность, термическую устойчивость и т.п.) [6, 7]. Композиты на матрице из УНТ встречаются гораздо реже. Влияние температуры спекания на свойства композитов и чистых УНТ исследовалось в работах [8–11]. Установлено, что структура УНТ не повреждается в процессе спекания, а при высоких температурах и давлениях возможно образование консолидированного материала. Вместе с тем, исследования по влиянию ИПС на структуру и свойства N-УНТ ранее проведены не были, тогда как известно, что повышенные температуры могут приводить к частичному удалению азота из материала или трансформации одних азотных групп в другие [2, 12].
Декорирование исходных нанотрубок частицами оксидов переходных металлов может приводить к их восстановлению в процессе ИПС и получению 3D-каркасных структур, состоящих из УНТ, на поверхности которых находятся инкапсулированные в углеродную оболочку наночастицы металла [13]. Получаемый материал – компактный, магнитоактивный, может проявлять каталитическую активность, а наличие кобальта значительно повышает электропроводность УНТ. Вместе с тем, в основе такого материала находятся окисленные УНТ, процесс получения которых связан с обработкой исходных нанотрубок азотной кислотой. Такая методика позволяет создать на поверхности УНТ множество центров стабилизации металла, но при этом может нарушить структуру УНТ и уменьшить их длину, что отрицательно повлияет на проводящие свойства.
В данной работе рассмотрена возможность синтеза таких металлоуглеродных композитов на основе кобальта и N-УНТ с сохранением атомов азота в углеродном каркасе. Использование N‑УНТ вместо окисленных УНТ позволит, во-первых, исключить экологически небезопасную и длительную стадию обработки нанотрубок окислителем, а во-вторых, даст возможность сохранить длину и целостность нанотрубок. При этом наличие азотных фрагментов на поверхности УНТ может способствовать стабилизации частиц металла при спекании.
ЭКСПЕРИМЕНТАЛЬНАЯ ЧАСТЬ
N-УНТ получали методом пиролиза ацетонитрила в присутствии катализатора роста состава Со–Мо/MgO. В трубчатый кварцевый реактор, помещенный в печь, загружали катализатор, а в склянку Дрекселя, подсоединенную к реактору, помещали ацетонитрил. Синтез проводили в течение 5 ч при температуре 750°С, пропуская через ацетонитрил ток азота со скоростью 500 мл/мин. Далее реактор охлаждали в токе азота (300 мл/мин) до 400°С, а затем в атмосфере воздуха до комнатной температуры для удаления аморфных примесей. Очистку от металлических примесей осуществляли кипячением в концентрированном растворе HCl в течение 3 ч при постоянном перемешивании магнитной мешалкой. Конечный продукт промывали дистиллированной водой с использованием колбы Бунзена, на фиксированной в тефлоновом фильтродержателе трековой мембране (ПЭТФ) при пониженном давлении, до нейтрального значения рН. Прекурсор для ИПС-обработки получали методом пропитки. Растворяли Co(NO3)2 · 6H2O в этиловом спирте, раствор при постоянном перемешивании прибавляли к N-УНТ. Количество нитрата кобальта рассчитывали, исходя из конечного содержания Co0 (10 мас. %). Далее смесь упаривали на ультразвуковой бане и сушили при 130°C в муфельной печи в течение 16 ч. После этого образцы отжигали в токе азота 2 ч при 350°С в кварцевом трубчатом реакторе.
ИПС проводили на установке для Labox-625 (Sinterland, Япония) в вакууме 10–2 Торр при давлении 30 МПа при температурах 800, 1000 и 1400°C. Время спекания составляло 5 мин, а скорость нагрева и охлаждения ∼100 K/мин. Для спекания использовали 1–3 г прекурсора, который помещали в графитовую пресс-форму с прокладкой из графлекса. Спеченные таблетки имели цилиндрическую форму, диаметром 1.5 см. Полученные образцы обозначали как CoNУНТ800, CoNУНТ1000 и CoNУНТ1400.
Морфологию образцов изучали методом сканирующей и просвечивающей электронной микроскопии (СЭМ и ПЭМ) с использованием приборов JEOL JSM-6390LA и JEOL 2100F, соответственно. Спектры РФЭС (рентгеновская фотоэлектронная спектроскопия) получали на рентгеновском фотоэлектронном спектрометре Axis Ultra DLD (Kratos, Великобритания) с монохроматическим источником излучения AlKα (hν = = 1486.6 эВ, 150 Вт). Проходная энергия анализатора составляла 160 эВ для обзорных спектров и 40 эВ для спектров высокого разрешения. Рентгеновские дифрактограммы регистрировали в диапазоне 2θ от 20° до 70° с использованием автоматического порошкового дифрактометра “STADI-P” производства “STOE GmbH”, установленного в геометрии Брэгга–Брентано, при использовании CuKα-излучения с длиной волны λ = 1.54060 Å. Электропроводность таблеток измеряли с использованием лабораторной установки, представляющей собой два латунных электрода диаметром 2.1 мм, сдавливающих пружин и мультиметра V7-78/1 АКИП. Значение электропроводности рассчитывали по формуле σ = L/RS, где L – толщина образца, R – измеренное сопротивление, а S – площадь контакта между электродом и образцом.
ОБСУЖДЕНИЕ РЕЗУЛЬТАТОВ
На рис. 1 приведены микрофотографии СЭМ образцов композитов с N-УНТ, спеченных при 800 и 1000°С. Распределение кобальта по образцу исследовали методом EDX, результаты картирования приведены на рис. 1б, 1д. В образце Со/N-УНТ800 размер частиц металла составляет около 100–200 нм, но, по данным EDX, также встречаются и крупные агломераты диаметром до нескольких мкм. Повышение температуры спекания приводит к большему числу таких крупных кобальтовых агрегатов, и разброс в размерах возрастает (рис. 1д, 1е). При этом, по данным EDX, на макроуровне распределение кобальта в объеме образцов имеет однородный характер.
Рис. 1.
Микрофотографии СЭМ образцов Со/N-УНТ800 (а, в) и Со/N-УНТ1000 (г, е), полученных методом ИПС, и карты EDX (б, д) распределения кобальта, соответствующие местам (а) и (г). На микрофотографиях (в) и (г) изображение приведено во вторичных (левая сторона) и в обратно-отраженных (правая сторона) электронах.
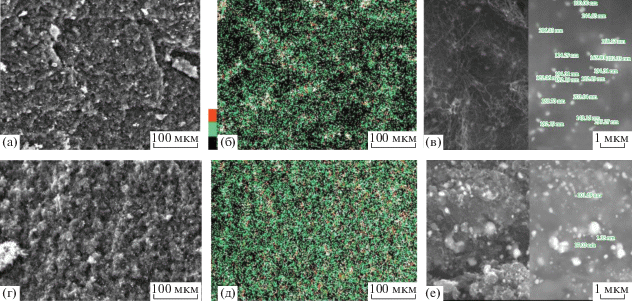
Образец Со/N-УНТ1400 исследовали методами ПЭМ и СЭМ (рис. 2). Распределение частиц кобальта по размеру в этом образце было наименее однородным из всех исследуемых материалов (рис. 2а), что, по-видимому, связано с усилением ударной волны при повышении интенсивности обработки и увеличением подвижности металла на поверхности N-УНТ при приближении к температуре плавления кобальта (1495°С) [13]. Установлено, что N-УНТ в образце сохраняют свою ячеистую или “бамбукообразную” структуру, несмотря на высокую температуру спекания (рис. 2б), а диаметр кристаллитов металла варьируется в широких пределах: от нескольких нанометров до нескольких микрометров (рис. 2а, 2в). При этом частицы кобальта покрыты углеродной оболочкой со структурой графита, толщиной в несколько графеновых слоев (рис. 2г).
Рис. 2.
Микрофотографии СЭМ (а) и ПЭМ (б–г) образца Со/NУНТ1400. На микрофотографии (а) изображение приведено во вторичных (левая сторона) и в обратно-отраженных (правая сторона) электронах.
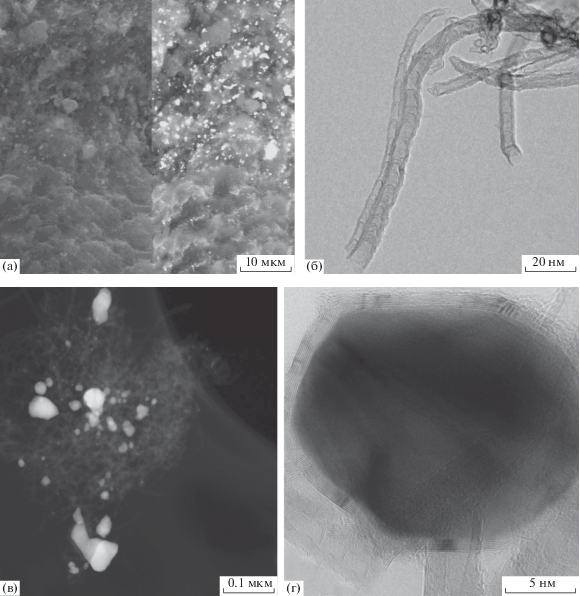
Фазовый состав образца Со/NУНТ800 изучали методом РФА. На дифрактограмме (рис. 3) видны максимумы, относящиеся к фазам металлического кобальта, графита из N-УНТ, оксида кобальта (II), а также карбидов молибдена. Последние образуются при синтезе нанотрубок. Размер ОКР металлического кобальта, определенный по формуле Шеррера, составляет ∼28 нм, что, в комбинации с данными СЭМ, наглядно демонстрирует разброс в диаметрах металлических частиц от нанометров до микрометров, а также может свидетельствовать о том, что крупные частицы кобальта представляют собой агломераты из более мелких. Металлический кобальт в данном образце, по-видимому, стабилизирован как углеродной, так и оксидной оболочкой, что согласуется с данными [13]. Вместе с тем, размер кристаллитов металла сильно выше, чем в случае спекания кобальта на окисленных УНТ. Скорее всего, азотсодержащие группы на поверхности N-УНТ недостаточно сильно связывают ионы металла на стадии пропитки, а также не препятствуют его миграции в процессе дальнейшего нагрева.
Следует отметить, что количество азотных групп в исходных УНТ (2.8 ат. %, табл. 1) значительно меньше, чем кислородных групп в составе окисленных УНТ (5–8 ат. %, [16]). К тому же, азот на стадии синтеза N-УНТ распределяется по объему материала, тогда как кислород при окислении обычных УНТ – по его поверхности. Это также может играть роль в пониженной стабильности частиц металла при спекании азотсодержащих образцов.
Таблица 1.
Содержание разных типов азота в исследуемых образцах по данным РФЭС (Сat – атомная концентрация в образце, %; Crel – концентрация определенного типа азота относительно его общей атомной концентрации в образце, %)
Тип азота | N-УНТ | CoNУНТ800 | CoNУНТ1000 | CoNУНТ1400 | |||
---|---|---|---|---|---|---|---|
Сat | Crel | Сat | Crel | Сat | Crel | Сat | |
Пиридиновый | 0.5 | 18 | 0.3 | 21 | 0.2 | 18 | 0 |
Пиррольный | 0.4 | 14 | 0.1 | 7 | 0.1 | 9 | 0 |
Замещающий/четвертичный | 1.0 | 36 | 0.5 | 36 | 0.4 | 36 | 0 |
Окисленные формы | 0.9 | 32 | 0.5 | 36 | 0.4 | 36 | 0 |
Всего | 2.8 | 1.4 | 1.1 | 0 |
Известно, что содержание азота падает при нагревании N-УНТ [4], поэтому данный параметр для спеченных образцов контролировали методом РФЭС. Исходные N-УНТ содержали ∼2.8 ат. % азота, а в ИПС-обработанных образцах его концентрация снижалась с ростом температуры спекания: 1.4 ат. % для 800°С и 1.1 ат. % для 1000°С (табл. 1). В образце CoNУНТ1400 азота обнаружено не было, что свидетельствует о его полном удалении в диапазоне температур 1000–1400°С. При этом форма спектров РФЭС N1s, как и относительное содержание разных форм азота, практически не менялась, за исключением небольшого падения доли пиррольного азота после спекания. По-видимому, это связано с близкими скоростями разложения пиридинового и замещающего азота, а наличие постоянной доли окисленных форм свидетельствует о поверхностном окислении материала при воздействии воздуха после изъятия из пресс-формы. Пиррольная форма азота – менее термически стабильна, что подтверждается ранее полученными результатами [17].
В табл. 2 приведены данные по измерению электропроводности спеченных образцов и их сравнение с исходными N-УНТ, с литературными данными и с образцами на основе окисленных УНТ, обработанных в ИПС при тех же температурах. Заметно, что электропроводность образцов после ИПС значительно выше, чем у исходных N-УНТ, полученных как в данной работе, так и в ранее опубликованных исследованиях. Значение этого параметра для СоNУНТ800 и СоNУНТ1000 также превышает аналогичную величину для спрессованных ориентированных N-УНТ. Такой эффект достигается за счет структурирования углеродной фазы и образования упорядоченных графитовых оболочек вокруг металлических кобальтовых частиц, а сами частицы создают дополнительные контакты между проводниками тока в образце [13].
Таблица 2.
Литературные и экспериментально полученные данные по электропроводности исследуемых образцов
Электропроводность кобальт-азот-углеродных систем после ИПС оказалась близка и лишь слегка превышала значение для ИПС-обработанных кобальтовых композитов с окисленными УНТ. Несмотря на то, что в случае Со/N-УНТ исходные нанотрубки не подвергались окислению и, таким образом, сохраняли свою целостность (и, следовательно, высокую внутреннюю электропроводность), частицы кобальта в образцах СоNУНТ800 и СоNУНТ1000 крупнее, чем в случае использования окисленных УНТ в работе [13], что, по-видимому, привело к уменьшению числа контактов между проводниками. Наличие заметного количества оксидов кобальта в азотсодержащих образцах могло также повысить контактное сопротивление образца. Тем не менее, наивысшая электропроводность получена именно на азотсодержащем образце, что указывает на эффективность замены окисленных УНТ на N-УНТ.
Таким образом, получен 3D-материал, представляющий собой каркасную структуру из азотсодержащих УНТ, декорированных частицами металлического кобальта, стабилизированных углеродными оболочками. Для синтеза использован метод ИПС. Установлено, что для того, чтобы сохранить в структуре материала азотсодержащие фрагменты, необходимо использовать температуры не выше 1000°С. Получены образцы, обладающие более высокой электропроводностью по сравнению с исходными N-УНТ и подобными композитами, полученными не из азотсодержащих, а обычных окисленных УНТ. Такой эффект, по-видимому, вызван отсутствием стадии окисления N-УНТ, в процессе которого нанотрубки становятся короче, что, в свою очередь, увеличивает количество контактов между отдельными УНТ и повышает сопротивление материала.
Авторы выражают благодарность Р.Ю. Шевченко, Г.С. Селяеву и М.С. Пасловой за помощь в измерении электропроводности и приготовлении исходных материалов, а также А.В. Егорову – за результаты ПЭМ. Исследование выполнено при поддержке Российского научного фонда (проект № 18-13-00217) с использованием оборудования, приобретенного за счет средств Программы развития Московского университета.
Список литературы
De Volder M.F.L., Tawfick S.H., Baughman R.H., Hart J. // Science. 2013. V. 339. P. 535.
Arkhipova E.A., Ivanov A.S., Strokova N.E. et al. // Carbon. 2017. V. 125. P. 20.
Wu J., Yadav R.M., Liu M. et al. // ACS Nano. 2015. V. 9. № 5. P. 5364.
Rocha R.P., G.P. Soares O.S., Gonçalves A.G. et al. // Appl. Catal. A. 2017. V. 548. P. 62.
Zhang Z.-H., Qi L., Shen X.-B et al.// Mater. Sci. Eng., A. 2013. V. 573. P. 12.
Karthiselva N.S., Bakshi S.R. // Mater. Sci. Eng., A. 2016. V. 663. P. 38.
Lis M., Wrona A., Mazur J. et al. // Archives of Metallurgy and Materials. 2015. V. 60. № 2. P. 1351.
Ham H., Park N.-H., Kang I. et al. // Chem. Commun. 2012. V. 48. № 53.
Li J., Wang L., He T., Jiang W. // Carbon. 2009. V. 47. № 4. P. 1135.
Laurent C., Chevallier G., Weibel A. et al. // Carbon. 2008. V. 46. № 13. P. 1812.
Strokova N., Savilov S., Xia H. et al. // Z. Phys. Chem. 2016. V. 230. № 12.
Kundu S., Xia W., Busser W. et al. // Phys. Chem. Chem. Phys. 2010. V. 12. № 17. P. 4351.
Savilov S.V., Chernyak S.A., Paslova M.S. et al. // ACS Appl. Mater. Interfaces. 2018. V. 10. № 24. P. 20983.
Chernyak S.A., Podgornova A.M., Arkhipova E.A. et al. // Appl. Surf. Sci. 2018. V. 439. P. 371.
Boehm H.-P. // Carbon Materials for Catalysis. Ch. (Serp P. and Figueiredo J.L., Editors). 2008. P. 219.
Chernyak S.A., Suslova E.V., Egorov A.V. et al. // Appl. Surf. Sci. 2016. V. 372. P. 100.
Xiao B., Boudou J.P., Thomas K.M. // Langmuir. 2005. V. 21. № 8. P. 3400.
Fujisawa K., Tojo T., Muramatsu H. et al. // Nanoscale. 2011. V. 3. № 10. P. 4359.
Podyacheva O.Y., Cherepanova S.V., Romanenko A.I. et al. // Carbon. 2017. V. 122. P. 475.
Суслова Е.В., Архипова Е.А., Иванов А.С. и др. // Журн. физ. химии. 2019. Т. 93. № 10.
Дополнительные материалы отсутствуют.
Инструменты
Журнал физической химии