Журнал физической химии, 2019, T. 93, № 8, стр. 1252-1258
Математическая модель измельчения и смешивания порошкообразных бинарных твердых веществ в энергонапряженной мельнице
О. В. Лапшин a, *, В. В. Болдырев b, c, **, Е. В. Болдырева c, d, ***
a Российская академия наук, Сибирское отделение, Томский научный центр
Томск, Россия
b Российская академия наук, Сибирское отделение, Институт химии твердого тела и механохимии
Новосибирск, Россия
c Новосибирский государственный университет
Новосибирск, Россия
d Российская академия наук, Сибирское отделение, Институт катализа им. Г.К. Борескова
Новосибирск, Россия
* E-mail: ovlap@mail.ru
** E-mail: boldyrev@solid.nsc.ru
*** E-mail: eboldyreva@catalysis.ru
Поступила в редакцию 19.11.2018
После доработки 19.11.2018
Принята к публикации 14.01.2019
Аннотация
В макроскопическом приближении разработана математическая модель и проведены количественные расчеты динамики смешивания твердых компонентов бинарной порошковой смеси при ее диспергировании в измельчающем устройстве. Определены различные режимы процесса в зависимости от основных параметров механической обработки.
Реакции между твердыми веществами хорошо известны. Для их осуществления компоненты должны быть приведены в контакт, для чего используются операции смешения. Смешение – важная технологическая операция во многих производствах и сама по себе достаточно хорошо исследована. Более сложный случай представляет собой смешение, которое сопровождается одновременным измельчением одного или нескольких смешиваемых компонентов. Именно этот случай реализуется при проведении механохимического синтеза, для реализации которого измельчение и смешивание твердых сыпучих веществ производят одновременно при их механической обработке (МО) в мельницах, гомогенизаторах или иных подобного типа аппаратах. Метод широко распространен в горноперерабатывающей, металлургической, химической, фармацевтической промышленности и лежит в основе так называемых “сухих технологий”, более экологически безопасных и, нередко, также более экономичных и эффективных по сравнению с традиционными методами синтеза [1–8].
Уменьшение степени неоднородного распределения компонентов при гомогенизации смеси создает условия для формирования максимальной межфазной поверхности, определяемой количеством разнородных контактов между ними [9]. Для корректного описания процессов в смесях компонентов и для управления ими необходимо уметь оценивать общее число и суммарную площадь контактов между частицами компонентов как в начальный момент времени, так и в ходе механической обработки, сопровождающейся, к тому же, химическим превращением. Эта задача нетривиальна и на данный момент времени остается не до конца решенной, так как требует учета сразу многих возможных процессов: значительного диспергирования компонентов, увеличения поверхности межчастичных контактов, изменения реологических свойств частиц, их активации путем создания новой высокодефектной структуры, характеризуемой повышенным запасом избыточной энергии [10–12].
В литературе описан ряд математических моделей смешения, которые хотя и не дают точных количественных оценок, но позволяют проводить целенаправленный поиск оптимальных режимов обработки смесей, тем самым сократив число экспериментальных исследований. Так, в работе [13] для теоретического описания процедуры упаковывания среды сферических частиц при ее вертикальной вибрации использовался метод дискретного элемента. Было выявлено, что существуют режимы интенсивности вибрации, способствующие достижению максимальной плотности упаковки. В [14] проведен обзор работ по математическим моделям дробления твердых веществ с применением технологии измельчения под высоким давлением (HPGR). В [15] анализируется обзор научной литературы, посвященной моделированию процессов механической обработки порошковой системы с использованием метода распределенных вычислений на основе модели потока данных об энергии столкновения движущихся объектов, обсуждаются преимущества и недостатки данного метода. В работе [16] делается вывод, что не существует универсального математического соотношения для определения индекса перемешивания (степени гомогенизации) – в каждом конкретном случае, в зависимости от типа системы частиц, необходимо использовать свою формулу, дающую более правильные и стабильные результаты. Предлагается использовать новый индекс перемешивания “Avg. distance mixing index”, позволяющий делать более точные прогностические оценки для степени гомогенизации порошковой смеси.
Основная задача настоящего исследования – рассмотрение динамики измельчения и гомогенизации в объеме мелющего устройства, т.е. в макроскопическом масштабе. Подчеркнем, что в макроскопическом приближении физико-химические величины, характеризующие процесс, являются осредненными, а масштаб их осреднения существенно больше размера отдельных частиц. Ранее макроскопический подход уже был использован нами для построения математических моделей МО и механохимического синтеза [17–20]. Однако в данных моделях предполагалось, что механообрабатываемый порошковый состав изначально полностью гомогенизирован и может быть представлен совокупностью элементарных (минимального размера) сферических ячеек, соотношение компонентов в которых равно их соотношению в смеси в целом. Отличительная особенность настоящей работы – учет в математическом моделировании МО стадии перемешивания компонентов.
МАТЕМАТИЧЕСКАЯ МОДЕЛЬ
Рассмотрим бинарную порошковую смесь компонентов А и В с объемами ${{V}_{{\text{A}}}}$ и ${{V}_{{\text{B}}}}$, плотностями компонентов ${{\rho }_{{\text{A}}}}$ и ${{\rho }_{{\text{B}}}}$, радиусами частиц ${{r}_{{\text{A}}}}$ и ${{r}_{{\text{B}}}}$ соответственно. Смесь занимает объем V. В этом случае ее пористость определится следующим образом:
В специальном аппарате мощностью W происходит смешивание, а также возможное измельчение компонентов порошковой смеси. Дополнительно примем следующие допущения:
– МО порошковой смеси происходит в изотермических условиях,
– в период МО пористость смеси не изменяется.
Принятые допущения позволяют упростить математические выкладки и выделить основные факторы, влияющие на рассматриваемый процесс.
Уравнение измельчения
Динамику изменения размера частиц i-го компонента в результате измельчения можно представить в виде [21]:
(1)
$\begin{gathered} \frac{{d{{\varepsilon }_{i}}}}{{d{{r}_{i}}}} = \frac{{{{A}_{{1i}}}}}{{{{r}_{{{\text{m}}i}}} - {{r}_{i}})}} + \frac{{3{{A}_{{2i}}}}}{{{{r}_{i}}(r_{{{\text{m}}i}}^{{}} - {{r}_{i}})}} + \frac{{9{{A}_{{3i}}}}}{{r_{i}^{2}({{r}_{{{\text{m}}i}}} - {{r}_{i}})}}, \\ i = {\text{A}},{\text{B}}, \\ \end{gathered} $(2)
${{\varepsilon }_{i}} = \int\limits_0^t {\,\frac{{{{a}_{i}}W}}{{{{V}_{{{\text{AB}}}}}}}} {\kern 1pt} dt,$Согласно [21], за исключением случаев грубого помола, наиболее значим второй член в (1), выражающий затраты энергии на неупругое деформирование, работу сил трения и образование новых поверхностей. Это обстоятельство позволяет упростить уравнение (1), оставив в правой части только второе слагаемое. В таком случае математические зависимости, обусловливающие изменение размеров частиц компонентов смеси при измельчении, можно переписать в виде
(3)
$\frac{{d{{r}_{i}}}}{{dt}} \approx {{k}_{i}}{{r}_{i}}({{r}_{{{\text{m}}i}}} - {{r}_{i}}),\quad i = {\text{A}},{\text{B}},$Уравнение смешения
Качество смешения (или степень гомогенизации) можно оценить в предположении непрерывного увеличения поверхности раздела между разнородными частицами. Для этого в смеси выделяют один из компонентов, условно называемый ключевым (основным). По характеру распределения ключевого компонента в смеси можно будет судить о степени ее гомогенизации. Отметим, что для бинарной смеси выделять ключевой компонент необязательно.
Уравнение динамики поверхности раздела (межфазной поверхности), описывающее процесс смешения веществ, можно представить в следующей дифференциальной форме [9]:
(4)
$\frac{{d{{s}_{{{\text{AB}}}}}}}{{dt}} = {{k}_{{\text{G}}}}({{s}_{{{\text{mAB}}}}} - {{s}_{{{\text{AB}}}}}),$В случае сферических частиц уравнение (4) можно преобразовать. Так как поверхность раздела определяется поверхностью контакта разнородных частиц, т.е. пропорциональна их количеству, то, положив ${{s}_{{{\text{AB}}}}} = p{{n}_{{{\text{AB}}}}}$, ${{s}_{{{\text{mAB}}}}} = p{{n}_{{{\text{mAB}}}}}$, (${{n}_{{{\text{AB}}}}}$, ${{n}_{{{\text{mAB}}}}}$ – текущее и максимальное (в случае идеального смешения) количество разнородных контактов, $p$ – коэффициент пропорциональности), уравнение (4) приводим к виду:
(5)
$\frac{{d{{n}_{{{\text{AB}}}}}}}{{dt}} = {{k}_{{\text{G}}}}({{n}_{{{\text{mAB}}}}} - {{n}_{{{\text{AB}}}}}).$Для нахождения степени гомогенизации можно ввести следующий критерий:
Очевидно, что всегда выполняется условие $G < 1$. Если смешение близко к идеальному, то $G \approx 1$.
Вспомогательные соотношения для вычисления параметра nmAB и количества однородных межчастичных контактов
Следуя методологии [22], вычислим входящую в (5) и (6) величину ${{n}_{{{\text{mAB}}}}}$ и количество однородных контактов типа АА (${{n}_{{{\text{AA}}}}}$) и ВВ (${{n}_{{{\text{BB}}}}}$). Для этого все возможные варианты смеси разделим на два типа: частицы одинаковых и частицы разных размеров. В первом случае ${{r}_{{\text{A}}}} \approx {{r}_{{\text{B}}}} = r$, а во втором – ${{r}_{{\text{B}}}} > {{r}_{{\text{A}}}}$ или ${{r}_{{\text{A}}}} > {{r}_{{\text{B}}}}$. Так как ${{n}_{{{\text{mAB}}}}}$ – количество разнородных контактов для идеально гомогенизированного состава ($G = 1$), то в этом случае можно записать следующие условия [22]:
(7)
${{n}_{{{\text{mAB}}}}} = \frac{{7.5}}{{4\pi m{{r}^{3}}}}\frac{{{{V}_{{\text{A}}}}{{V}_{{\text{B}}}}}}{{{{V}_{{{\text{AB}}}}}}},\quad {\text{е с л и }}\quad {{r}_{{\text{A}}}} \approx {{r}_{{\text{B}}}} = r;$(8)
$\begin{gathered} {{n}_{{{\text{mAB}}}}} = \frac{{3[{{{({{r}_{{\text{Y}}}} + 2{{r}_{{\text{X}}}})}}^{3}} - r_{{\text{Y}}}^{3}]}}{{4\pi r_{{\text{A}}}^{3}r_{{\text{B}}}^{3}}}\frac{{{{V}_{{\text{Y}}}}m{{V}_{{{\text{AB}}}}}}}{{m{{V}_{{\text{Y}}}} + {{V}_{{\text{X}}}}}}, \\ {\text{е с л и }}\quad {{r}_{{\text{X}}}} < {{r}_{{\text{Y}}}},\quad ({\text{X}} = {\text{A,B}},\;{\text{Y}} = {\text{A,B}},\;{\text{X}} \ne {\text{Y}}). \\ \end{gathered} $Как видно из (7) и (8), параметр ${{n}_{{{\text{mAB}}}}}$ не является величиной постоянной, а при измельчении частиц за счет уменьшения их размера будет расти.
В свою очередь, количество однородных контактов в бинарной смеси, согласно [22], описывают следующие соотношения:
– для частиц равных размеров
(9)
${{n}_{{{\text{AA}}}}} = (n - {{n}_{{{\text{AB}}}}})\frac{{{{V}_{{\text{A}}}}}}{{{{V}_{{{\text{AB}}}}}}},\quad {{n}_{{{\text{BB}}}}} = (n - {{n}_{{{\text{AB}}}}})\frac{{{{V}_{{\text{B}}}}}}{{{{V}_{{{\text{AB}}}}}}},$– для смеси с разными размерами частиц
(10)
$\begin{gathered} {{n}_{{{\text{XX}}}}}\, = \,({{N}_{{\text{X}}}}\, - \,{{n}_{{{\text{AB}}}}})\frac{{2.5}}{m},\quad {{n}_{{{\text{YY}}}}}\, = \,({{N}_{{\text{Y}}}}\, - \,N_{{\text{Y}}}^{'})\frac{{2.5}}{m}, \\ ({{r}_{{\text{Y}}}} > {{r}_{{\text{X}}}},\;{\text{X}} = {\text{A,B}},\;{\text{Y}} = {\text{A,B}},\;{\text{X}} \ne {\text{Y}}). \\ \end{gathered} $В (10) введены обозначения: ${{N}_{{\text{A}}}} = 3{{V}_{{\text{A}}}}{\text{/}}4\pi r_{{\text{A}}}^{3}$ и ${{N}_{{\text{B}}}} = 3{{V}_{{\text{B}}}}{\text{/}}4\pi r_{{\text{B}}}^{3}$ – количество частиц А и В в порошковой смеси соответственно; $N_{{\text{Y}}}^{'} = {{n}_{{{\text{AB}}}}}{\text{/}}{{N}_{{{\text{AB}}}}}$ – число частиц Y, контактирующих с X; ${{N}_{{{\text{AB}}}}} = \frac{{[{{{({{r}_{{\text{Y}}}} + 2{{r}_{{\text{X}}}})}}^{3}} - r_{{\text{X}}}^{3}]}}{{r_{{\text{Y}}}^{3}}}(1 - {{m}_{*}})$ – число частиц X, контактирующих с одной частицей Y при идеальном смешении; ${{m}_{*}} = \frac{{m{{V}_{{{\text{AB}}}}}}}{{m{{V}_{{\text{Y}}}} + {{V}_{{\text{X}}}}}}.$
Структура механообрабатываемой бинарной смеси
Эволюция структуры бинарной порошковой смеси в зависимости от времени механической обработки схематично представлена на рис. 1. Как видно из рисунка, в исходном состоянии (а) поверхность раздела разнородных компонентов, определяемая количеством контактов типа АВ, незначительна (${{n}_{{{\text{AB}}}}} \approx 0$). Здесь степень гомогенизации пренебрежимо мала ($G\sim 0$). В процессе механической обработки происходит измельчение компонентов А и В, начинается их постепенное перемешивание (рис. 1б). В этот период МО число разнородных контактов возрастает ($0 < {{n}_{{{\text{AB}}}}} \ll {{n}_{{{\text{mAB}}}}}$), и наблюдается частичная гомогенизация смеси ($0 < G \ll 1$). С продлением механообработки порошковая смесь измельчается и окончательно гомогенизируется (рис. 1в). В этом случае количество разнородных контактов и степень ее гомогенизации близки к максимальным своим значениям: ${{n}_{{{\text{AB}}}}} \approx {{n}_{{{\text{mAB}}}}}$, $G \approx 1$. В конечном итоге, при идеальном перемешивании бинарная порошковая смесь будет представлять собой совокупность эквивалентных элементарных ячеек, вид которых, в зависимости от размерных параметров компонентов, изображен на рис. 2.
Рис. 1.
Схема структуры бинарной порошковой смеси в исходном состоянии (a), на начальном (б) и завершающем (в) этапах МО.
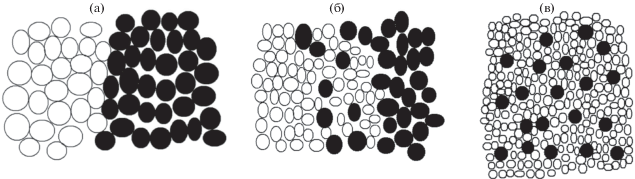
Рис. 2.
Схема элементарной ячейки в зависимости от структуры порошковой смеси при ее идеальном смешении: a – тип I , б –тип II(A), в – тип II(B).

Для частиц равных размеров (${{r}_{{\text{A}}}} \approx {{r}_{{\text{B}}}}$) в элементарной ячейке реализуется структура типа I (рис. 2a). Будем полагать, что тип I имеет место, когда размеры разнородных частиц соизмеримы, а их отношение находится в определенном диапазоне значений: ${{l}_{1}} \leqslant {{r}_{{\text{A}}}}{\text{/}}{{r}_{{\text{B}}}} \leqslant {{l}_{2}}$ (где ${{l}_{1}}$ и ${{l}_{2}}$ – дополнительно задаваемые параметры, причем ${{l}_{1}} \leqslant 1,\;{{l}_{2}} \geqslant 1$). Если ${{r}_{{\text{A}}}} > {{r}_{{\text{B}}}}$ (или ${{r}_{{\text{A}}}}{\text{/}}{{r}_{{\text{B}}}} > {{l}_{2}}$), то в этом случае реализуется структура типа II(A). Здесь в центре ячейки находится крупная частица А, окруженная более мелкими частицами В (рис. 2б). Структура типа II(В) выполняется при ${{r}_{{\text{B}}}} > {{r}_{{\text{A}}}}$ (или ${{r}_{{\text{A}}}}{\text{/}}{{r}_{{\text{B}}}} < {{l}_{1}}$). В этом случае в центре ячейки будет расположена частица В, окруженная частицами А (рис. 2в).
РЕШЕНИЕ ЗАДАЧИ И АНАЛИЗ РЕЗУЛЬТАТОВ
Динамика степени гомогенизации бинарной порошковой смеси и размеров частиц компонентов в процессе МО представлена на рис. 3. Рассматриваются два случая смешения компонентов: без заметного измельчения (кривая 1) и в условиях измельчения порошковой смеси (кривые 2, 2', 2''). Можно констатировать, что с увеличением времени МО структура смеси становится более однородной, вследствие чего растет степень ее гомогенизации G (кривые 1 и 2). В это время может происходить дробление частиц компонентов А и В, сопровождающееся уменьшением их размера (кривые 2' и 2'' соответственно). Радиус частиц стремится к минимальному своему значению, которое соответствует пределу измельчения ${{r}_{m}}$. В приведенном примере частицы В измельчаются лучше, чем А. Как следует из рис. 3, скорость гомогенизации без измельчения частиц выше, чем при их измельчении. Данное обстоятельство можно объяснить тем, что дробление вещества приводит к необходимости затратить дополнительное время и энергию для перераспределения вновь образованных частиц среди компонентов порошкового состава.
Рис. 3.
Динамика степени гомогенизации без измельчения (1) и с учетом измельчения (2), а также размеров частиц компонентов А (2') и В (2'') в условиях МО бинарной порошковой смеси в энергонапряженной мельнице при ${{k}_{G}} = 2$ мин–1, ${{r}_{{{\text{A}},0}}} = {{r}_{{{\text{B}},0}}}$, ${{k}_{{\text{A}}}} = 1$ мин–1, ${{k}_{{\text{B}}}} = 3$ мин–1.
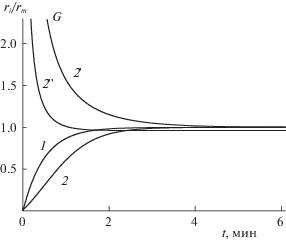
Численное моделирование позволяет рассмотреть ситуацию, когда при определенных параметрах смеси и работы измельчительного устройства зависимость степени гомогенизации $G$ от времени механообработки может быть немонотонной. Подобный режим смешивания твердых порошков, в данном случае имеющий два локальных минимума, демонстрирует рис. 4. Как видно, после прохождения локальных минимумов, характеризующихся заметным снижением величины $G$, степень гомогенизации в процессе МО увеличивается до своего предела, соответствующего идеальному смешению компонентов (рис. 4а). Немонотонную зависимость степени гомогенизации $G(t)$ можно объяснить, анализируя динамику отношения размеров частиц ${{r}_{{\text{A}}}}{\text{/}}{{r}_{{\text{B}}}}$ в процессе МО (рис. 4б). На рисунке горизонтальными пунктирными линиями выделена область, соответствующая режимам МО, при которых структура идеально перемешенной смеси должна соответствовать типу I.
Рис. 4.
Динамика степени гомогенизации (а) и отношения размеров компонентов (б) в условиях МО порошковой смеси при ${{k}_{G}} = 2$ мин–1, ${{l}_{{\text{1}}}} = 0.5$, ${{l}_{2}} = 2$, ${{r}_{{{\text{A}},0}}}{\text{/}}{{r}_{{{\text{B}},0}}} = 10$, ${{r}_{{{\text{Am}}}}}{\text{/}}{{r}_{{{\text{Bm}}}}} = 10$, ${{k}_{{\text{A}}}} = 1$ мин–1, ${{k}_{{\text{B}}}} = 10$ мин–1, ${{r}_{{{\text{A}},0}}} = {{10}^{{ - 4}}}$ м, ${{r}_{{{\text{B}},0}}}{\text{/}}{{r}_{{{\text{A}},0}}} = 10$, ${{k}_{{\text{A}}}} = 1$ мин–1, ${{k}_{{\text{B}}}} = 0.1$ мин–1.
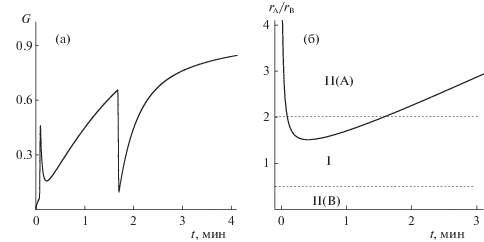
Как видно из рис. 4, в начальный период МО, когда ${{r}_{{\text{A}}}} \gg {{r}_{{\text{B}}}}$, структура обрабатываемой смеси ориентирована на тип II(A). По мере измельчения происходит смена ориентации структуры состава на тип I (${{r}_{{\text{A}}}}\sim {{r}_{{\text{B}}}}$), вследствие чего степень гомогенизации резко падает (первый локальный минимум). При дальнейшей механообработке, сопровождающейся измельчением вещества, ориентация структуры снова меняется на тип II(A), а зависимость $G(t)$ претерпевает второй локальный минимум. Отметим, что в данном примере при МО ориентации структуры смеси на тип II(B) не происходит.
На рис. 5 изображена диаграмма в координатах “отношение коэффициентов измельчения и гомогенизации – время механической обработки”, характеризующая различные режимы МО бинарной порошковой смеси. Для удобства координаты представлены в логарифмическом виде. $\Omega $-образная кривая на диаграмме является геометрическим местом точек, соответствующих условию $G = 0.99$. В областях I, II и III, расположенных выше $\Omega $-кривой, реализуются режимы МО, при которых степень гомогенизации близка к идеальной. Параметры механообработки, фиксирующие точки, расположенные ниже $\Omega $-кривой, соответствуют степени гомогенизации состава меньше заданной (области ${\text{I}}{\kern 1pt} '$, ${\text{II}}{\kern 1pt} '$ и ${\text{III}}{\kern 1pt} '$).
Рис. 5.
Диаграмма в координатах $\ln ({{k}_{i}}{\text{/}}{{k}_{G}}) - \ln {{t}_{{{\text{MO}}}}}$, определяющая различные режимы МО порошковой смеси при ${{r}_{{{\text{A}},0}}} = {{r}_{{{\text{B}},0}}} = {{10}^{{ - 4}}}$ м, ${{k}_{{\text{A}}}} = {{k}_{{\text{B}}}} = 1$ мин–1.
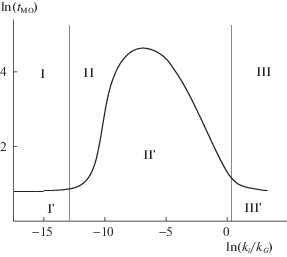
В расположенных слева на диаграмме областях ${\text{I}}$ и ${\text{I}}{\kern 1pt} '$ реализуются режимы МО, при которых измельчение несущественно (${{k}_{i}} \ll {{k}_{G}}$). Здесь происходит только смешение компонентов. В правой части диаграммы в областях ${\text{III}}$ и ${\text{III}}{\kern 1pt} '$ скорость измельчения вещества значительно выше скорости его гомогенизации (${{k}_{i}} \gg {{k}_{G}}$). В этом случае подвергается перемешиванию фактически предельно измельченный материал. И в том, и в другом случаях требуется достаточно небольшое время механообработки для полной гомогенизации смеси. При режимах МО, соответствующих расположенным в средней части диаграммы областям ${\text{II}}$ и ${\text{II}}{\kern 1pt} '$, скорости измельчения и гомогенизации сравнимы (${{k}_{i}}\sim {{k}_{G}}$). Здесь, в силу конкуренции процессов диспергирования разнородных частиц и равномерного их перераспределения в объеме измельчительного аппарата, время смешивания компонентов до полной гомогенизации смеси существенно возрастает.
Таким образом, в макроскопическом приближении разработана математическая модель измельчения и смешивания бинарной порошковой смеси в энергонапряженной мельнице. Модель позволяет вычислять размеры частиц порошковой смеси, степень ее гомогенизации, количество однородных и разнородных контактов в любой момент времени механической обработки. Численным методом исследована динамика процесса. Выявлены основные режимы измельчения и гомогенизации. Дальнейшее развитие предложенной математической модели состоит в учете диссипации тепла на местах межчастичных контактов, запаса избыточной энергии в компонентах в результате их активации, а также химического превращения на контактах типа АВ.
Список литературы
Молчанов В.В., Буянов Р.А. // Успехи химии. 2000. Т. 69. В. 5. С. 476.
Молчанов В.И., Селезнева О.Г., Жирнов Е.Н. Активация минералов при измельчении. М.: Недра, 1988. 208 с.
Каминский Ю.Д. Механохимические реакторы планетарного типа: теория и практика. М.: Наука, 2015. 198 с.
Ломовский О.И., Болдырев В.В. Механохимия в решении экологических задач: аналитический обзор. Сер. Экология. Новосибирск: ГПНТБ СО РАН, 2006. В. 79. 221 с.
Cagnetta G., Intini G., Liberti L. et al. // J. Soils Sediments. 2015. V. 15. № 3. P. 240.
Métro T.X., Colacino E., Martinez et al. // RSC Green Chemistry. 2015. P. 114.
Friščić T., James S.L., Boldyreva E.V. et al. // ChemComm. 2015. V. 51. № 29. P. 6248.
Boldyreva E. // Chem. Soc. Rev. 2013. V. 42. № 18. P. 7719.
Еремин Н.Ф. Процессы и аппараты в технологии строительных материалов. М.: Высш. шк., 1986. 280 с.
Авакумов Е.Г. Механические методы активации химических процессов. Новосибирск: Наука, 1986. 305 с.
Болдырев В.В. // Вестник РФФИ. 2004. № 3(37). С. 38.
Shi H., Mohanty R., Chakravarty S. et al. // KONA. 2018. V. 35. P. 226.
Yue R., Zhang O. // KONA. 2017. V. 34. P. 224.
Rashidi S., Rajamani R.K., Fuerstenau D.W. // Ibid. 2017. V. 34. P. 125.
Tavares L.M. // KONA. 2017. V. 34. P. 106.
Shih-Hao Chou, Yue-Lou Song, Shu-San Hsiau // Ibid. 2017. V. 34. P. 275.
Smolyakov V.K., Lapshin O.V., Boldyrev V.V. // Int. J. SHS. 2007. V. 16. №1. P. 1.
Smolyakov V.K., Lapshin O.V., Boldyrev V.V. // Theor. Found. Chem. En. 2008. V. 42. № 1. P. 54.
Smolyakov V.K., Lapshin O.V., Boldyrev V.V. // Ibid. 2008. V. 42. № 2. P. 187.
Смоляков В.К., Лапшин О.В. Макроскопическая кинетика механохимического синтеза. Томск: Изд-во Института оптики атмосферы, 2011. 191 с.
Ходаков Г.С. Физика измельчения. М.: Наука, 1972. 307 с.
Smolyakov V.K., Lapshin O.V., Boldyrev V.V., Boldyreva E.V. // Russ. J. Phys. Chem. A. 2018. V. 92. № 12. P. 1966.
Дополнительные материалы отсутствуют.
Инструменты
Журнал физической химии