Журнал физической химии, 2020, T. 94, № 2, стр. 254-258
Образование мелкодисперсных структур в сплавах алюминия с кобальтом и цирконием
Е. Ф. Казакова a, Н. Е. Дмитриева a, Н. Л. Зверева a, *
a Московский государственный университет имени М.В. Ломоносова, Химический факультет
Москва, Россия
* E-mail: zvereva.nl@yandex.ru
Поступила в редакцию 22.05.2019
После доработки 22.05.2019
Принята к публикации 11.06.2019
Аннотация
Комплексом методов физико-химического анализа исследованы быстрозакаленные сплавы алюминия с кобальтом и цирконием с целью изучения образования мелкодисперсных структур, способствующих значительному улучшению прочностных характеристик материалов. Исследованы сплавы сверхбыстрой закалки, поскольку именно такой режим обработки сплавов позволяет добиться максимального эффекта при выделении упрочняющих фаз. Установлено, что переход однофазной структуры пересыщенного твердого раствора Alпер(Co, Zr) к равновесной трехфазной структуре (Alр(Co, Zr) + ZrAl3 + Co2Al9) сопровождается увеличением твердости вследствие последовательного выделения интерметаллидных фаз в мелкодисперсном состоянии. Показано, что величина эффекта дисперсионного твердения существенным образом зависит от температурно-временных параметров процесса распада пересыщенных твердых растворов
Сплавы алюминия с переходными металлами являются перспективными для получения сверхжаропрочных и легких сплавов. Однако, предельная растворимость переходных металлов в алюминии в твердом состоянии очень мала [1–5]. Применение высоких скоростей кристаллизации (105–9 град/c) приводит к изменению фазового состава сплавов по сравнению с равновесным. Появление метастабильных фаз в результате сверхбыстрой закалки (пересыщенных твердых растворов на основе алюминия и метастабильных интерметаллических фаз) и их последующий распад по специально подобранному режиму приводят к выделению упрочняющих интерметаллидных фаз в мелкодисперсном состоянии. Кроме того, сверхбыстрая закалка обеспечивает существенное повышение однородности структуры и химического состава сплавов за счет равномерности распределения дефектов, а также основных и примесных компонентов; отсутствия сегрегации примесей по границам зерен; измельчения зерна [6–8]. Таким образом, эффект повышения прочностных и жаропрочных характеристик алюминиевых сплавов при их легировании переходными металлами можно значительно усилить применением сверхбыстрой закалки из жидкого состояния, что приводит к расширению областей гомогенности твердых растворов и диспергированию включений промежуточных фаз в сплавах алюминия с переходными металлами.
В настоящей работе в качестве легирующих добавок выбраны кобальт и цирконий, позволяющие получить при сверхбыстрой закалке пересыщенные твердые растворы в алюминии. Цирконий, являющийся эффективным модификатором, выбран с расчетом на улучшение морфологии упрочняющих фаз. Известно, что добавки кобальта и циркония приводят к образованию химически прочных и тугоплавких интерметаллических соединений Co2Al9 и ZrAl3, которые способствуют повышению прочности сплавов [9]. Применение в качестве легирующего компонента кобальта позволяет избежать нежелательных процессов, связанных с образованием грубых включений интерметаллидных фаз и их быстрой коагуляцией, что вызывает ухудшение прочностных характеристик алюминиевых сплавов [10].
ЭКСПЕРИМЕНТАЛЬНАЯ ЧАСТЬ
Исходные материалы: Al марки А-99.999, кобальт, содержащий 99.98 мас. % Со, цирконий иодистый с содержанием Zr 99.98 мас. %.
Быстрозакаленные сплавы (БЗС) получали методом спиннингования в виде лент шириной 2–5 мм и толщиной 0.01–0.02 мм. Скорость закалки составляла 105–6 град/с.
Исследования проводили комплексом методов физико-химического анализа, опробованным на сплавах систем с участием алюминия [1–5].
Рентгенофазовый анализ (РФА) равновесных сплавов проводили методом порошка на дифрактометре (STOE STADI P, CuKα1 Ge (111)-монохроматоре. Для снятия внутренних напряжений порошки предварительно подвергали отжигу в течение 2 ч. Ленты быстрозакаленных сплавов наклеивали в несколько слоев на стеклянную подложку. Количественный и качественный состав сплавов исследовали методом сканирующей электронной микроскопии на приборе LEO EVO-50 XVP (Сarl Zeiss, Германия) при ускоряющем напряжении 20 кВ, энергодисперсионного микроанализа (ЭДМА) с использованием детектора INCA energy 450 (Oxford Instruments). Для определения температуры фазовых переходов применяли метод дифференциально-сканирующей калориметрии на приборе Jupiter STA 449 F1 (Германия) в атмосфере гелия, скорость нагрева 20 град/мин. Измерение твердости проводили на приборах ТП-7П-1 при нагрузке 50 Н и ПМТ-3, снабженном окулярным микрометром АМ9-2, с нагрузкой 0.2–0.1 Н.
ОБСУЖДЕНИЕ РЕЗУЛЬТАТОВ
Составы исследованных быстрозакаленных сплавов, а также фазовые составы до и после изотермических отжигов приведены в табл. 1. По данным РФА, сплавы состава Al97Co2Zr1 и Al99Co0.67Zr0.33 состоят из двух фаз: пересыщенного твердого раствора циркония в алюминии, и равновесной интерметаллидной фазы Co2Al9. На дифрактограммах образцов указанных сплавов присутствуют две системы отражений от плоскостей кристаллической ГЦК-решетки Al и моноклинной собственного типа, характерной для Co2Al9. РФА и СЭМ сплавов составов Al99.4Co0.40Zr0.2, Al99.91Co0.06Zr0.03 и Al99.98Co0.08Zr0.04 показали, что эти сплавы представляют собой пересыщенные твердые растворы Co и Zr в алюминии, а равновесная интерметаллидная фаза Co2Al9 отсутствует.
Таблица 1.
Фазовый состав (I – Alпер(Zr) + Co2Al9, II – Alр + Co2Al9 + ZrAl3, III – Alпер(Co, Zr)) и термическая устойчивость быстрозакаленных сплавов системы Al–Co–Zr
Состав сплавов, ат. % | Фазовый состав до отжига | Фазовый состав после отжига | ||||
---|---|---|---|---|---|---|
Al | Co | Zr | 200°С | 300°С | 400°С | |
97.00 | 2.00 | 1.00 | I | 1 ч – I | ||
2 ч | ||||||
III | II | |||||
6 ч – II | ||||||
99.00 | 0.67 | 0.33 | I | 1 ч – II | ||
2 ч | ||||||
I | II | |||||
6 ч – II | ||||||
99.40 | 0.40 | 0.20 | III | 0.3 ч | ||
III | I | |||||
0.5 ч – I | ||||||
1 ч | ||||||
I | II | |||||
6 ч – II | ||||||
99.88 | 0.08 | 0.04 | III | 1 ч | ||
III | I | |||||
2 ч – I | ||||||
6 ч – II | ||||||
12 ч – II | ||||||
99.91 | 0.06 | 0.03 | III | 0.5 ч | ||
III | I | |||||
2 ч – I | ||||||
4 ч | ||||||
I | II | |||||
6 ч – II |
Отжиг при температуре 200°С в течение 2 ч быстрозакаленных сплавов из области пересыщенного твердого раствора циркония в алюминии с содержанием легирующих компонентов: Со – 2.00 ат. %, Zr – 1.00 ат. % и Со – 0.67 ат. %, Zr – 0.39 ат. % приводит к увеличению значения твердости, что свидетельствует о начале распада пересыщенного твердого раствора и выделении фазы ZrAl3. Рентгенофазовый анализ этих сплавов, отожженных при температуре 200°С в течение 8 ч, демонстрирует наличие системы отражений от плоскостей тетрагональной кристаллической решетки (ZrAl3). Отжиг в течение 0.5 ч при этой же температуре пересыщенных твердых растворов кобальта и циркония в алюминии с содержанием Со – 0.40 ат. %, Zr – 0.20 ат. % и при концентрациях Со – 0.06 ат. %, Zr – 0.03 ат. % и Со – 0.08 ат. %, Zr – 0.04 ат. % приводит к увеличению значений твердости. После 2 ч отжига этих сплавов начинается новый рост твердости вследствие выделения другой интерметаллидной фазы ZrAl3 .
Для сплава состава Al99.40Co0.40Zr0.20 через 2 ч после начала отжига при 200°С полностью выделяется фаза Co2Al9, а через 6 ч – фаза ZrAl3 (рис. 1). Увеличение времени отжига для сплавов с содержанием Co – 6.00 ат. %, Zr – 3.00 ат. %, и Co – 3.00 ат. %, Zr – 0.04 ат. %, приводит к полному выделению фазы Co2Al9 через 6 ч, а фазы ZrAl3 – через 12 ч. Для последних двух сплавов максимальный эффект дисперсионного твердения обнаружен для сплава алюминия с содержанием Co – 6.00 ат. %, Zr – 3.00 ат. %, прошедшего термообработку при 200°С после 6 ч отжига образца этого сплава от времени отжига при более высоких температурах: 300 и 400°С. Из рис. 2 видно, что чем выше температура отжига, тем раньше начинается процесс распада пересыщенного твердого раствора Co и Zr в алюминии и меньше эффект дисперсионного твердения.
Рис. 1.
Дифрактограмма сплава состава: Al – 99.4 ат. %, Со – 0.4 ат. %, Zr – 0.2 ат. % после 8 ч отжига.
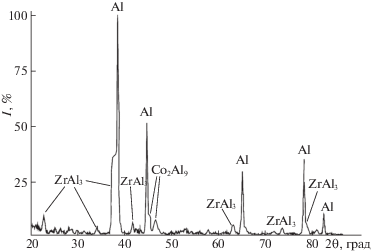
Рис. 2.
Влияние времени отжига на твердость быстрозакаленного сплава состава: Al – 99.91 ат. %, Со – 0.06 ат. %, Zr – 0.03 ат. % при 200 (а), 300 (б) и 400°С (в).
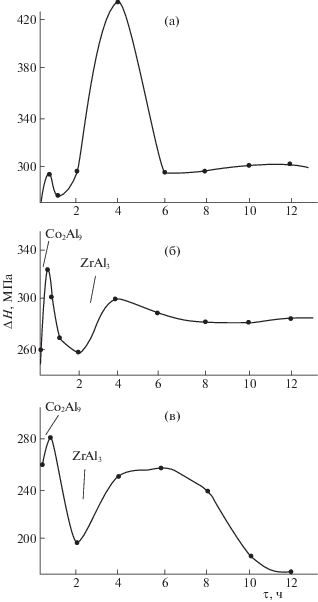
Увеличение концентраций легирующих добавок в быстрозакаленных сплавах алюминия с кобальтом и цирконием приводит к появлению второй фазы уже при сверхбыстрой быстрой кристаллизации. Так, сплавы состава Al97.01Co2.00Zr1.00 и Al99.00Co0.67Zr0.33 двухфазны (табл. 1). В этих сплавах совместно кристаллизуются пересыщенный твердый раствор на основе алюминия и равновесная фаза Co2Al9. Твердый раствор на основе алюминия остается пересыщенным цирконием, так как в процессе термической обработки на кривых дисперсионного твердения наблюдается один эффект – результат выделения в процессе распада пересыщенного твердого раствора упрочняющей фазы ZrAl3. Фаза ZrAl3 начинает выделяться из пересыщенного твердого раствора сплава состава Al99.00Co0.67Zr0.33, содержащего интерметаллидную фазу Co2Al9, при температуре 200°С и времени отжига 2 ч. Однако при повышении температуры отжига время начала выделения равновесной фазы ZrAl3 уменьшается (табл. 1). Распад пересыщенного твердого раствора Zr в алюминии указанного сплава при 300 и 400°С происходит в течение 1 ч.
В табл. 1 приведено время начала выделения равновесных фаз Co2Al9 и ZrAl3 из пересыщенного твердого раствора в быстрозакаленных сплавах состава Al99.40Co0.40Zr0.20, Al99.91Co0.06Zr0.03, Al99.88Co0.08Zr0.04 в зависимости от температуры отжига в соответствии с результатами дюрометрического анализа. Из табл. 1 видно, что с увеличением температуры отжига устойчивость пересыщенного твердого раствора Co и Zr в Al уменьшается. Так, фаза ZrAl3 в сплаве состава Al99.40Co0.40Zr0.20 начинает выделяться из пересыщенного твердого раствора после 1 ч отжига при 300 и 400°С.
Пересыщенные твердые растворы Co и Zr в Al, образующиеся в быстрозакаленных сплавах системы Al–Co–Zr, обладают довольно низкой термической устойчивостью. Первой из пересыщенного твердого раствора выделяется равновесная интерметаллическая фаза Co2Al9, а затем – фаза ZrAl3. Однако, промежуточная метастабильная фаза ZrAl3 при распаде пересыщенного твердого раствора кобальта и циркония в алюминии не обнаружена. Быстрый распад пересыщенных твердых растворов обусловлен легкостью кристаллизации соединения Co2Al9, что, возможно, связано с большой диффузионной подвижностью атомов легирующих элементов.
По результатам РФА и дюрометрического анализа построены Т-Т-Т-диаграммы. На рис. 3 представлена Т-Т-Т-диаграмма сплава состава Al99.91Co0.06Zr0.03, которая характеризует температурно-временные параметры процесса распада пересыщенного твердого раствора Co и Zr в Al. Из рис. 3 видно, что при распаде пересыщенного твердого раствора можно выделить две последовательных стадии, описывающиеся следующей схемой:
РФА сплавов указанных составов (рис. 1) также подтверждает последовательное выделение интерметаллидной фазы Co2Al9, а затем – фазы ZrAl3. Характер структурных изменений, происходящих при распаде пересыщенных твердых растворов, хорошо коррелирует с изменением твердости от времени отжига на кривых дисперсионного твердения. Так, выделение интерметаллидов Co2Al9 и ZrAl3 в мелкодисперсном состоянии сопровождается увеличением твердости. Длительная термообработка приводит к коагуляции этих фаз, в результате значения твердости убывают.
Список литературы
Казакова Е.Ф., Дмитриева Н.Е., Кустов Л.М. // Журн. физ. химии. 2018. Т. 92. № 12. С. 1834.
Казакова Е.Ф., Дмитриева Н.Е., Дунаев С.Ф. // Вестн. Моск. ун-та. Сер. 2. Химия. 2015. Т. 56. № 1. С. 41.
Казакова Е.Ф., Зверева Н.Л., Кустов Л.М. // Журн. физ. химии. 2018. Т. 92. № 12. С. 1840.
Dmitrieva N.E., Kazakova E.F., Dunaev S.F. // 3rd Intern. Symp. “Nanomaterials and Environment”. 2016. June 8–10. Moscow, Russia.
Казакова Е.Ф., Зверева Н.Л., Дмитриева Н.Е., Мешков Л.Л. // Вестн. Моск. ун-та. Серия 2. Химия. 2014. Т. 55. № 5. С. 308.
Захаров В.В., Елагин В.И., Филатов Ю.А. и др. // Технология легких сплавов. 2006. № 4. С. 20.
Sokolovskaya E.M., Kazsakova E.F., Portnoi V.K. et al. // Moscow Univ. Chem. Bull. 1994. V. 49. № 3. P. 43.
Русняк Ю.И., Казакова Е.Ф., Лобода Т.П. // МиТОМ. 2009. № 9. С. 25.
Варич И.И., Кравцов И.А. // Неравновесная кристаллизация металлических сплавов. М.: Химия, 1972.
Добаткин В.И., Елагин В.И. // Гранулируемые алюминиевые сплавы. М.: Металлургия, 1981.
Дополнительные материалы отсутствуют.
Инструменты
Журнал физической химии