Журнал физической химии, 2021, T. 95, № 4, стр. 632-640
Суперконденсаторы на основе активированных углей – продуктов переработки шелухи риса
Р. Ю. Новоторцев a, Е. В. Суслова a, *, Кванки Чен b, А. Н. Акулич c, Ли Лу d, С. В. Савилов a, e
a Московский государственный университет имени М.В. Ломоносова, Химический факультет
119991 Москва, Россия
b Guangxi Key Laboratory of Electrochemical and Magneto-chemical Functional Materials,
College of Chemistry and Bioengineering, Guilin University of Technology
541004 Guilin, China
c ООО НПП “Экологическое природопользование”
353307 Краснодарский край, Станица Холмская, Россия
d Department of Mechanical Engineering, National University of Singapore
117575 9 Engineering Drive 1, Singapore
e Российская академия наук, Институт нефтехимического синтеза им. А.В. Топчиева
119991 Москва, Россия
* E-mail: suslova@kge.msu.ru
Поступила в редакцию 24.04.2020
После доработки 17.08.2020
Принята к публикации 07.09.2020
Аннотация
Зола рисовой шелухи (ЗРШ), промышленно полученная при сжигании шелухи риса, произрастающего в Краснодарском крае Российской Федерации, впервые охарактеризована комплексом современных физико-химических методов исследования. Установлено, что она содержит аморфный кремнезем (более 70 мас. %) и углерод (~8 мас. %). Активированный уголь (АУ) получен при обработке ЗРШ раствором щелочи с последующим отжигом при 700°С. Площадь поверхности АУ составила 1442 м2 г–1 с преобладанием в его структуре мезопор. АУ был использован в качестве материала электродов двойнослойных суперконденсаторов (ДСК) с водным 6М KOH и органическим 1 M Et4NBF4/PC электролитами. Значения энергоемкостей исследованных ДСК составили 299 и 131 Ф г–1 соответственно.
Разработка и внедрение экологически безопасных технологий, включающих утилизацию и переработку отходов сельскохозяйственного производства, является приоритетной задачей развития многих стран. Мировое производство риса в 2019 году составило 512 млн т, при этом отходы в виде рисовой шелухи (РШ) – более 100 млн т [1]. РШ как сырье не имеет спроса, несмотря на большое количество инициатив, связанных с ее использованием, поэтому никаких экономически эффективных технологий ее переработки не существует. До сих пор основной способ утилизации РШ – сжигание, при этом образуется зола рисовой шелухи (ЗРШ), содержащая большое количество кремнезема и углерода. При относительно невысоких температурах пиролиза первый компонент получается аморфным и может быть применен в качестве наполнителей шин, компонента бетонов, сорбентов, источника поликристаллического кремния [2]. Углерод, получаемый из РШ, ЗРШ или любой другой биомассы может применяться в качестве сорбентов, носителей катализаторов, материалов электродов источников хранения и накопления электроэнергии [3].
Особое место среди устройств хранения и накопления энергии занимают двойнослойные суперконденсаторы (ДСК), отличающиеся высокими мощностными характеристиками, быстротой и эффективностью заряда/разряда, продолжительной циклируемостью. Электроды ДСК, изготовленные из углерода, хорошо поляризуются, являются химически инертными, устойчивы в широком диапазоне температур. Аккумулирование энергии в ДСК происходит за счет накопления электростатического заряда на границе раздела электрод/электролит, поэтому эффективность материала увеличивается с ростом значения удельной площади поверхности SБЭТ и доступности пор для проникновения электролита внутрь электродной массы.
Активированные угли (АУ), полученные из РШ, имеют, как правило, высокие значения SБЭТ (1000–3000 м2 г–1). Увеличить долю мезопор в их структуре можно за счет физической или химической активации. Первая заключается в обработке углей или биомассы водяным паром, CO2 или их смесью при 450°С [4, 5]. Под химической активацией подразумевают обработку углерода неорганическими солями, кислотами или щелочами при высоких температурах [6]. При химической активации удается получить более узкое распределение пор и одновременно функционализировать поверхность различными группами, способствующими сродству к водным или органическим электролитам [7].
АУ, полученные из РШ, неоднократно описаны в литературе в качестве материалов электродов ДСК и литиевых батарей [8–15]. Ряд работ посвящен способу активации углерода в составе РШ, подбору эффективного агента, его концентрации, температуры и условий обработки, поиску возможных корреляций между способом получения и характеристиками ДСК [6, 8, 9]. Например, АУ, полученный при карбонизации РШ при 800°С в азоте с последующим удалением SiO2 обработкой при 100°С раствором NaOH, оказался более эффективен в устройствах ДСК по сравнению с АУ без удаления SiO2 [9]. Карбонизацию РШ можно осуществлять и при более низких температурах. Например, авторы [8] описывают уголь, полученный каталитической карбонизацией РШ в кипящем слое при 465 и 550°С, с последующей активацией щелочами и карбонатами щелочных металлов. Характеристики ДСК на его основе зависели от полученных SБЭТ и распределения пор по размерам: их емкость линейно увеличивалась с увеличением SБЭТ при низких скоростях развертки потенциала (0.2 мВ с–1) и уменьшалась при высоких скоростях из-за эффектов пористой структуры.
В настоящей работе впервые в качестве источника углерода для ДСК использована промышленно полученная ЗРШ – продукт переработки сельскохозяйственных отходов риса Краснодарского края. Методом химической активации щелочью получен АУ с высокоразвитой поверхностью и контролируемой пористостью. Он использован в качестве материалов электродов ДСК с водными и органическими электролитами. На основании результатов циклической вольтамперометрии в широком диапазоне плотностей тока показано, что, несмотря на средние значения SБЭТ, емкостные характеристики ДСК превосходят характеристики ДСК описанные ранее с водными электролитами [8–11, 14]. При этом потери при циклировании не превышают 8.5%, что существенно ниже описываемых в литературе [11, 12].
ЭКСПЕРИМЕНТАЛЬНАЯ ЧАСТЬ
Исходные вещества
Исходное сырье (РШ, отход рисового производства) предоставлено одним из лидеров российского рынка – “Южной рисовой компанией”, Краснодарский край, Россия. РШ перед использованием промывали дистиллированной водой для удаления пыли и растворимых примесей. ЗРШ получали пиролизом на оборудовании ООО “Научно-производственное предприятие “Экологическое природопользование” в станице Холмская (Краснодарский край, Россия) при крупнотоннажном сжигании РШ при рабочих температурах 600–750°С (рис. 1) [16]. Отметим, что максимальная температура обработки РШ не должна превышать 750°С, так как в противном случае происходит частичная или полная кристаллизация аморфного SiO2 с формированием структур типа кристобалита или кварца [17].
Рис. 1.
РШ (а) и ЗРШ (б), полученные на базе ООО “Научно-производственное предприятие “Экологическое природопользование”.
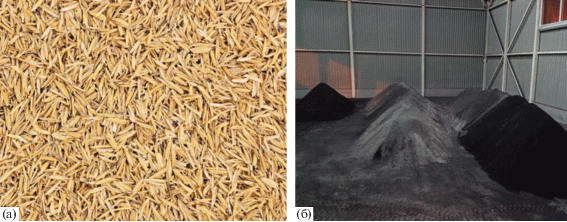
Для получения АУ к навеске ЗРШ добавляли 6М раствор NaOH (мас. соотношение ЗРШ : NaOH = = 1 : 1), суспензию перемешивали 24 ч при комнатной температуре, после чего углеродсодержащий осадок отфильтровывали. К осадку прибавляли сухой NaOH (мас. соотношении углеродный материал: NaOH = 1 : 3), 0.5 об. доли H2O и нагревали до 80°С при перемешивании. Высушенную смесь переносили в трубчатую печь, прокаливали при 700°С в течение 2 ч в проточной атмосфере Ar и охлаждали до комнатной температуры для получения смеси АУ и натриевой соли. Полученную смесь фильтровали, промывая дистиллированной водой 3–4 раза. Затем АУ один раз промывали раствором разбавленной соляной кислоты и три раза дистиллированной водой до нейтрального значения рН промывных вод (рис. 2).
Методы исследования. Приборы и оборудование
Микрофотографии поверхности образцов и концентрации элементов на основе данных локального рентгеноспектрального анализа (EDX) получены на сканирующем электронном микроскопе (СЭМ) “JEOL JSM-6390LA” (Jeol, Япония), снабженном энергодисперсионным микроанализатором, под ускоряющим напряжением 25 кВ. Состав РШ и ЗРШ определяли усреднением по, как минимум, восьми точкам, с учетом данных предварительной калибровки.
Термический анализ проводили на приборе Jupiter STA 449 PC (Netzsch, ФРГ) с подключенным в линию квадрупольным масс-спектрометром Aeolos QMS 403C. Навеску образца (10–20 мг) в алундовом (либо платиновом) тигле нагревали в атмосфере воздуха или инертного газа со скоростью 5 К мин–1.
Удельную площадь поверхности (SБЭТ) и распределение пор по размерам определяли низкотемпературной адсорбцией азота по БЭТ на приборе AUTOSORB-1C/MS/TPR (Quantachrome, США). Для определения SБЭТ 400 мг материала помещали в ампуле в анализатор, вакуумировали штатным насосом и в процессе измерения строили изотерму адсорбции азота при температуре 77 K, по которой согласно модели БЭТ с помощью программного обеспечения прибора рассчитывали удельную поверхность, а по модели BJH – распределение пор в материале по размерам. Пробу предварительно дегазировали 3 ч при 300°С.
Рентгеновские дифрактограммы образцов получали с использованием автоматического порошкового дифрактометра STADI-P (STOE, ФРГ). Для съемки использовали излучение СuKα; регистрацию дифрактограмм проводили в геометрии Брегга–Брентано в диапазоне углов 2θ 5–80°, выдержкой 5 с и шагом 0.05°.
Электрохимические измерения
Для определения энергоемкостных характеристик АУ в среде водного электролита электроды изготавливали следующим образом. Навески АУ и проводящей сажи “Super P” тщательно перетирали в ступке, после чего добавляли раствор (20 мг мл–1) политетрафторэтилена (ПТФЭ). Массовое соотношение АУ : “Super P” : ПТФЭ составило 8 : 1 : 1. К смеси при перемешивании добавляли этанол до комкования образца, который прокатывали между вальцами и комковали еще несколько раз. Наконец полученную толстую пленку разрезали на круглые фрагменты, которые еще раз прокатывали между вальцами. Для изготовления электродов полученные пленки сушили при 80°С в течение 12 ч, после чего запаивали между двумя коллекторами из Ni пены. Перед использованием электроды вымачивали ~12 ч в растворе 6M KOH. Для определения емкостных характеристик монтировали симметричную двухэлектродную ячейку типа coin cell 2032, в качестве электролита используя 6M раствор KOH, а сепаратора – полипропиленовую пленку.
Для определения емкостных характеристик в среде органического электролита монтаж двухэлектродной ячейки проводили схожим образом. АУ смешивали с проводящей сажей “Super P” и поливинилиденфторидом (ПВДФ) при массовом соотношении указанных компонентов 8 : 1 : 1, добавляя N-метил-2-пирролидон. Полученную суспензию перемешивали при комнатной температуре в течение 12 ч и наносили на коллектор из Ni пены, после чего сушили при 120°С 2 ч на воздухе и прокатывали между вальцами. Для удаления остатков растворителя и влаги электроды сушили при 120°С в вакууме в течение 12 ч. В качестве электролита использовали 1M раствор Et4NBF4 в пропиленкарбонате (1M Et4NBF4/PC), сепаратором служил стекловолоконный материал Whatman. Все операции по сборке ячеек и их тестированию осуществляли в сухом боксе производства MBraun (ФРГ) в атмосфере аргона.
Содержание воды в органическом электролите определяли кулонометрическим титрованием по Карлу Фишеру на приборе “Metrohm 756 KF Coulometer”. Масса проб составила 1.2–1.3 г. Содержание воды в 1M Et4NBF4/PC – 24.1 ppm.
Электрохимические характеристики электродов исследовали методом циклической вольтамперометрии (ЦВА) при 0–1.0 и 0.01–2.5 В для водного и органического электролитов соответственно со скоростью развертки от 2 до 500 мВ с‒1 и хронопотенциометрии при токах 0.2–1 А г–1 на приборе IM6-ex (Zahner, ФРГ). Устойчивость в течение 500 циклов определяли с использованием потенциостата Р-2000 (Neware, КНР).
ОБСУЖДЕНИЕ РЕЗУЛЬТАТОВ
Состав и физико-химические характеристики РШ, ЗРШ и АУ
На основании результатов EDX, основными компонентами РШ и ЗРШ являются кремнезем и углерод. Так же в образцах содержатся небольшие количества металлов I, II группы, Al и S (табл. 1), что хорошо согласуется с данными [18, 19].
Таблица 1.
Составы РШ и ЗРШ, полученных при переработке отходов рисового производства Краснодарского края
Образец | Элементный состав (EDX, мас. %) | |||||||||
---|---|---|---|---|---|---|---|---|---|---|
Si | C | O | Na | K | Mg | Ca | Al | S | Cl | |
РШ | 17.50 | 33.90 | 47.12 | 0.06 | 0.20 | 0.12 | 0.05 | 1.01 | 0.03 | – |
ЗРШ | 19.27–35.52 | 23.42–49.13 | 27.62–35.24 | – | 2.84–4.85 | 0.14–0.22 | 0.44–0.73 | – | – | 0.32 |
Содержание углерода в исходной РШ и ЗРШ подтверждено методом термического анализа (рис. 3). Потеря массы РШ при 100°С составила 3.5 мас. %, что соответствует фактической влажности образцов, в диапазоне температур 117–500°С – ~71 мас. %, что связано с удалением органических компонент. Твердый остаток составил 25 мас. % от исходной навески РШ, что превышает типовую зольность РШ, которая, по данным [20], составляет до 18.6 мас. %. ТГ-анализ ЗРШ показал, что доля сгораемой компоненты – углерода – в ней составила 8.1 мас. %.
На рис. 4 приведена рентгеновская дифрактограмма осадка, образующего из ЗРШ после удаления аморфного SiO2 растворением в щелочи. Рефлекс при 2θ ~23 соответствует межплоскостному расстоянию d002, характерному для углеродных структур.
Морфология РШ, остатка после обработки ЗРШ 6 М раствором KOH и АУ исследованы методом СЭМ (рис. 5). Фрагменты угля повторяют морфологию РШ, формируя иерархическую пористую структуру, являющуюся результатом вымывания кремнезема.
Морфология поверхностей РШ, угля из нее и АУ исследованы методом СЭМ. Поверхность угля повторяет морфологию РШ и имеет пористую структуру (рис. 5а). Кремнезем является каркасом структуры и при его удалении структура углерода, хотя и повторяет исходную морфологию (рис. 5б), но уже не обладает достаточной прочностью. При последующей активации и перетирании углерод может утрачивать исходную иерархическую структуру (рис. 5в), сохраняя при этом внутреннюю пористость.
Значение удельной площади поверхности SБЭТ ЗРШ составило 114 м2 г–1, после активации для АУ оно возросло до 1442 м2 г–1. Изотерма адсорбции ЗРШ относится к смешанному I и IV типам: кривая выпуклая относительно оси P/P0, однако не выходит на насыщение при P/P0 = 1. В области P/P0 = 0.6 наблюдается перегиб, характерный для изотерм адсорбции IV типа. Кривая десорбции не совпадает с кривой сорбции, однако повторяет ее характер при P/P0 < 0.5 (рис. 6а). Подобного рода кривые относятся к типу B, характерному для щелевидных пор. Изотерма адсорбции активированного угля ближе всего к типу II (рис. 6б).
Рис. 6.
Изотермы адсорбции азота ЗРШ(а), АУ (б) и распределение пор по размерам ЗРШ(в), АУ(г), согласно модели BJH.
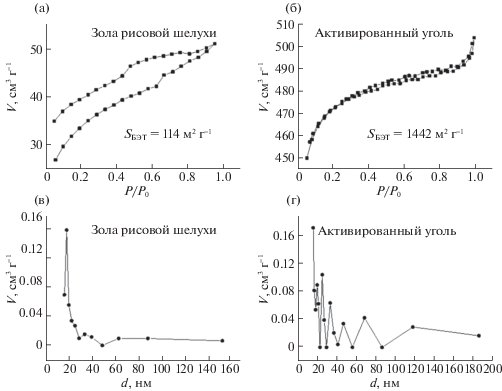
Изотермы I типа характерны для микропористых материалов, а IV типа – для мезопористых. В ЗРШ присутствуют, как микро-, так и мезопоры, причем максимумы приходятся на мезопоры с размером ~18 и 32 нм (рис. 6в). Изотермы II типа характерны для обратимой адсорбции на непористых или макропористых адсорбентах по механизму полимолекулярной адсорбции. Распределение пор по размерам в активированном угле более равномерное, с максимумом при 18–30 нм (рис. 6г). Общий объем пор, согласно модели BJH, составил 0.0208 и 0.0516 см3 г–1 в угле и АГ соответственно.
Электрохимические характеристики ДСК
Кривые ЦВА, как для водного, так и органического электролитов, не демонстрировали пиков, соответствующих протеканию электрохимических реакций, в интервале приложенных потенциалов, что свидетельствует об отсутствии каких-либо побочных окислительно-восстановительных процессов. C увеличением скоростей развертки потенциала ток в системе уменьшался (рис. 7а,б), что можно связать с процессами заряда и разряда двойного электрического слоя (ДЭС). При всех скоростях развертки формы кривых ЦВА отличаются от идеальной прямоугольной, что указывает на частичную потерю эффективности сборок.
Рис. 7.
Кривые ЦВА(а, б) и заряда/разряда ДСК(в, г) в растворах 6M KOH(а, в) и 1M Et4NBF4/PC(б, д). Скорость развертки, плотность тока и рассчитанные значения удельной емкости указаны на рисунках (в, г); I – сила тока, В – потенциал.
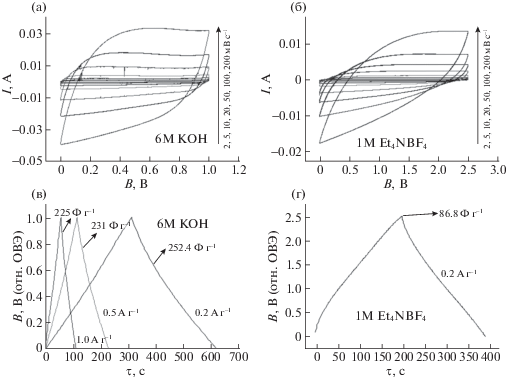
Кривые заряда/разряда регистрировали в интервале потенциалов 0.005–1 В в водном электролите (рис. 7в) и 0.005–2.5 В в органическом (рис. 7г). С увеличением плотности тока от 0.2 до 1 Аг–1 время обоих процессов уменьшалось. Форма кривых была близка к линейным, что согласуется с данными ЦВА: накопление энергии происходит посредством формирования ДЭС.
Исходя из симметричности электродов, удельную емкость Cуд ДСК рассчитывали по формуле:
(1)
${{C}_{{{\text{уд}}}}} = \frac{{{{C}_{{{\text{общ}}}}}}}{{m{\text{/}}2}} = \frac{{2C}}{{m{\text{/}}2}} = \frac{{4C}}{m},$Емкость можно выразить через заряд и напряжение:
где q – заряд, выраженный в Кл, а ΔV – напряжение, выраженное в В. При постоянной силе тока заряд может быть также определен следующим образом: где I – сила тока, выраженная в амперах, а t – время, выраженное в секундах. Подставив выражения (2) и (3) в (1), получается формула:Емкости ДСК в зависимости от скорости развертки потенциала с водным и органическим электролитами представлены в табл. 2.
Таблица 2.
Удельная емкость ДСК с электродами из активированного угля при различных скоростях развертки ($v$) потенциала в 6M растворе KOH и 1М растворе Et4NBF4. Удельный ток 0.2 А г–1 (U – емкость)
Электролит | $v$, мВ с–1 | U, Ф г–1 |
---|---|---|
6M KOH | 2 | 299 |
5 | 277 | |
10 | 263 | |
20 | 251 | |
50 | 228 | |
100 | 201 | |
200 | 162 | |
1M Et4NBF4/PC | 2 | 131 |
5 | 126 | |
10 | 112 | |
20 | 95 | |
50 | 73 | |
100 | 57 | |
200 | 42 | |
500 | 16 |
Емкость 277 Ф г–1 (5 мВ с–1, 0.2 A г–1), полученная для ДСК с водным 6M KOH электролитом, превышает значения, полученные другими авторами для АУ из РШ за исключением тех случаев, когда удавалось увеличить SБЭТ более, чем 3000 м2 г–1 (табл. 3). Однако такие ДСК существенно теряют емкость при увеличении скорости развертки потенциала (315 и 163 Ф г–1 при 0.5 и 20 мВ с–1 соответственно), что связано с присутствием примесей в образцах [11]. Потеря емкости обсуждаемых сборок существенно ниже и составила 83.9% при увеличении скорости развертки потенциала от 0.2 до 20 мВ с–1 (табл. 2).
Таблица 3.
Емкость ДСК с материалами электродов из активированных углей (ρ – плотность тока)
Прекурсор АУ | SБЭТ, м2 г–1 | Электролит | U, Ф г–1 | $v$, мВ с–1 | ρ, A г–1 | Ссылка |
---|---|---|---|---|---|---|
Водные электролиты | ||||||
ЗРШ | 1442 | 6M KOH | 277 | 5 | 0.2 | Настоящая работа |
РШ | 1260 | 1М H2SO4 | 125 | 1 | 0.2 | [8] |
РШ | 2290 | 1М H2SO4 | 230 | 1 | 0.2 | [8] |
РШ | – | 4.9М H2SO4 | 230 | 20 | 0.46 | [21] |
РШ (SiO2 не удален) | 3263 | 6M KOH | 315 | 5 | 0.5 | [11] |
РШ | 2804 | 6M KOH | 278 | 5 | 0.5 | [10, 11] |
Карбонизированная РШ | 527 | 6M KOH | 110 | 5 | 0.1 | [9] |
РШ | 2696 | 6M KOH | 147 | 5 | 1 | [14] |
РШ | 3145 | 6M KOH | 367 | 5 | 2.27 | [12] |
Органические электролиты | ||||||
ЗРШ | 1442 | 1M Et4NBF4/PC | 126 | 5 | 0.2 | Настоящая работа |
РШ | 1260 | BMImBF4 | 100 | 1 | 0.2 | [8] |
РШ | 2290 | BMImBF4 | 232 | 1 | 0.2 | [8] |
РШ | 1892 | 1M Et4NBF4/PC | 147 | 5 | 0.5 | [13] |
РШ | 1442 | TEMA.BF4/PC | 120 | 1 | <10 | [15] |
РШ | 1442 | SPB.BF4/PC | 80 | 1 | <10 | [15] |
РШ | 3145 | 1.5М Et4NBF4/MeCN | 174 | 5 | 2.27 | [12] |
Как правило, наиболее существенно на емкостные характеристики при низких значениях тока в ДСК влияет значение SБЭТ (табл. 3). При увеличении скорости развертки потенциала существенным становится возможность проникать электролиту в поры материала для образования ДЭС [8]. В среде электролита 1M Et4NBF4/PC емкость АУ (126 Ф г–1) ниже по сравнению с данными [13] и выше, чем с электролитами BMImBF4 [8] и TEMA ⋅ BF4/PC или SPB ⋅ BF4/PC [15] (табл. 3).
Текстурные характеристики, в том числе и распределение пор по размерам, играют одну из ключевых ролей при использовании АУ в устройствах ДСК [21]. Щелочная активация РШ или ЗРШ позволяет получить оптимальные значения SБЭТ и пористости структуры АУ, поверхность электродного материала становится доступной для органических электролитов. Это связано с присутствием в исходных РШ и ЗРШ атомов кислорода в составе функциональных групп на поверхности и в составе объемной фазы SiO2 [6]. Удаление последней из ЗРШ в виде растворимого метасиликата натрия обеспечивает пористость материала. При последующей активации происходит элиминирование части атомов углерода в соответствии с реакцией:
Стабильность ДСК с органическим электролитом исследовали в течение 500 циклов разряда/заряда. Емкость существенно уменьшается в течение первых 30 циклов с 131 до ~100 Ф г–1 и практически не изменялась в дальнейшем (рис. 8). Уменьшение емкости после нескольких первых циклов связано, вероятно, с восстановлением кислорода, прочно сорбированного на поверхности АУ, до H2O2 [22].
Рис. 8.
Изменение зарядной и разрядной емкостей ДСК c 1M Et4NBF4/PC электролитом в течение 500 циклов. Ток 0.2 A г–1, диапазон напряжений 0.005–2.5 В, N – номер цикла.
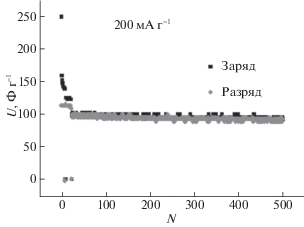
Таким образом, в настоящей работе впервые охарактеризован продукт переработки рисовых отходов Краснодарского края – ЗРШ, а также полученный на ее основе АУ. Показано, что в случае промышленного пиролиза РШ, который позволяет избежать кристаллизации SiO2, содержание углерода в продукте составляет ~8 мас. %. Аморфный SiO2 может быть легко удален из структуры ЗРШ обработкой раствором NaOH при комнатной температуре. Показано, что последующую активацию углей из ЗРШ можно эффективно осуществлять отжигом при 700°С, что упрощает получение АУ и удешевляет конечный продукт. Установлено, что при активации угля из ЗРШ предложенным способом значение SБЭТ увеличивается десятикратно (до 1442 м2 г–1), меняется тип изотермы адсорбции, происходит перераспределение пор в материале по размерам. Это способствует успешному использованию полученных АУ в качестве материала электродов ДСК. Cборки с водным 1M раствором KOH в качестве электролита демонстрируют высокие значения емкостей, которые превосходят большинство описываемых в литературе. ДСК с органическим электролитом 1M Et4NBF4/PC имели сравнимую с литературными данными емкость и высокие показатели циклируемости.
Работа выполнена при финансовой поддержке Российского фонда фундаментальных исследований (код проекта № 19-03-00713a) в рамках государственных заданий МГУ имени М.В. Ломоносова и ИНХС имени А.В. Топчиева РАН. Авторы чрезвычайно признательны к.х.н. С.А. Черняку и к.х.н. А.В. Шумянцеву за регистрацию СЭМ-изображений и термограммы образцов соответственно.
Список литературы
http://www.fao.org/worldfoodsituation/csdb/ru/
Shen Y. // Renew. Sustain. Energ. Rev. 2017. V. 80. P. 453. https://doi.org/10.1016/j.rser.2017.05.115
Chen Y., Zhu Y., Wang Z. et al. // Adv. Colloid Interface Sci. 2011. V. 163. № 1. P. 39. https://doi.org/10.1016/j.cis.2011.01.006
Jiang C., Yakaboylu G.A., Yumak T. et al. // Renew. Energ. 2020. V. 155. P. 38. https://doi.org/10.1016/j.renene.2020.03.111
Xia K., Gao Q., Jiang J., Hu J. // Carbon. 2008. V. 46. P. 1718. https://doi.org/10.1016/j.carbon.2008.07.018
Елецкий П.М., Яковлев В.А., Фенелонов В.Б., Пармон В.Н. // Кинетика и катализ. 2008. Т. 49. Вып. 5. С. 741.; Eletskii P.M., Yakovlev V.A., Fenelonov V.B., Parmon V.N. // Russ. J. Kin. Cat. 2008. V. 49. № 5. С. 708. https://doi.org/10.1134/S0023158408050169
Li X., Wei B. // Nano Energ. 2013. V. 2. № 2. P. 159. https://doi.org/10.1016/j.nanoen.2012.09.008
Лебедева М.В., Елецкий П.М., Аюпов А.Б. и др. // Кат. пром. 2017. Т. 17. Вып. 6. С. 534. Lebedeva M.V., Eletskii P.M., Ayupov A.B. et al. // Catalysis in Industry. 2017. V. 17. № 6. P. 534. https://doi.org/10.18412/1816-0387-2017-6-534-542
Zhang W., Lin N., Liu D. et al.// Energy. 2017. V. 128. P. 618. https://doi.org/10.1016/j.energy.2017.04.065
Liu D., Zhang W., Lin H. et al. // RSC Adv. 2015. V. 5. P. 19294. https://doi.org/10.1039/C4RA15111A
Liu D., Zhang W., Huang W. // Chin. Chem. Lett. 2019. V. 30. P. 1315. https://doi.org/10.1016/j.cclet.2019.02.031
Gao Y., Li L., Jin Y. et al. // Appl. Energ. 2015. V. 153. P. 41. https://doi.org/10.1016/j.apenergy.2014.12.070
Xiao C., Zhang W., Lin H. et al. // New Carbon Mat. 2019. V. 34. № 4. P. 341. https://doi.org/10.1016/S1872-5805(19)60018-1
Teo E.Y.L., Muniandy L., Ng E.-P. et al. // Electrochim. Acta. 2016. V. 192. P. 110. https://doi.org/10.1016/j.electacta.2016.01.140
Kumagai S., Tashima D. // Biomass Bioenerg. 2015. V. 83. P. 216. https://doi.org/10.1016/j.biombioe.2015.09.021
Пaтeнт PФ 2631294 (2016).
Адылов Г.Т., Файзиев Ш.А., Пайзуллаханов М.С. и др. // Письма в ЖТФ. 2003. Т. 29. Вып. 6. С. 7; Adylov G.T., Faiziev S.A., Paizullakhanov M.S. et al. // Tech. Phys. Lett. 2003. V. 29. № 6. P. 221.
Земнухова Л.А., Шкорина Е.Д., Федорищева Г.А. // Журн. прикл. химии. 2005. Т. 78. Вып. 2. С. 329. Zemnukhova L.A., Shkorina E.D., Fedorishcheva G.A. // Russ. J. Appl. Chem. 2005. V. 78. № 2. P. 324.
Земнухова Л.А., Полякова Н.В., Федорищева Г.А., Цой Е.А. // Хим. раст. сырья. 2013. Вып. 1. С. 209.
Ужахова Л.Я., Султыгова З.Х., Арчакова Р.Д. и др. // Вестн. совр. наук. 2017. № 2-1 (26). С. 36.
Вервикишко Д.Е., Школьников Е.И., Янилкин И.В. и др. // Электрохимия. 2017. Т. 53. Вып. 5. С. 567.; Vervikishko D.E., Shkol’nikov E.I., Yanilkin I.V. et al. // Russ. J. Electrochem. 2017. V. 53. № 5. P. 500. https://doi.org/10.7868/S0424857017050164
Рычагов А.Ю., Измайлова М.Ю., Сосенкин В.Е. и др. // Электрохимическая энергетика. 2015. Т. 15. Вып. 1. С. 3.
Дополнительные материалы отсутствуют.
Инструменты
Журнал физической химии