Журнал физической химии, 2021, T. 95, № 5, стр. 686-691
Термический анализ процессов при твердофазном синтезе литий-титанового феррита
Е. В. Николаев a, *, Е. Н. Лысенко a, А. П. Суржиков a
a Томский политехнический университет
634050 Томск, Россия
* E-mail: nikolaev0712@gmail.com
Поступила в редакцию 01.07.2020
После доработки 21.10.2020
Принята к публикации 21.10.2020
Аннотация
Методами термического и кинетического анализов, исследовалась реакционная активность смеси исходных реагентов Fe2O3–Li2CO3–TiO2 с различной исходной плотностью на фазообразование литий-титанового феррита. В качестве экспериментальных образцов использовали порошок с плотностью 1 г см–3, свободно засыпанный в тигель и прессовку (компакт) c плотностью 2.6 г см–3. Для формирования образцов с высокой плотностью использован метод одностороннего холодного прессования. Было показано, что реакция твердофазного взаимодействия литий-титанового феррита сильно зависит от степени компактирования. Установлено, что для порошковой смеси уменьшение массы образца происходит в интервале температур 500–720°C. Для компактов реакция твердофазного взаимодействия начинается при более низкой температуре (∼420°C). Показано, что в спрессованных образцах, наблюдается образование шпинельной фазы литиевого феррита в процессе нагрева. Методом кинетического анализа определена кинетическая модель реакции синтеза литий-титанового феррита и рассчитаны параметры, характеризующие этот процесс.
Ферриты представляют собой соединения оксида железа Fe2O3 с оксидами других металлов. В настоящее время используют сотни различных марок ферритов, отличающихся по химическому составу, кристаллической структуре, магнитным, электрическим и другим свойствам. Наиболее широкое применение из них нашли ферриты со структурой типа шпинели [1–3].
Литиевые ферриты, в которых ионы Fe3+ [4] замещаются ионами титана, широко применяются в качестве материалов, используемых в микроволновой, электронной и других областях производства. Благодаря хорошим магнитным и электрическим свойствам, данные соединения могут быть применены для замены других ферритов [5–7]. Существует множество способов синтеза литиевых ферритов, наиболее распространенным из которых является метод, который основан на твердофазном взаимодействии уплотненных порошков при высокотемпературном нагреве [8–10]. Однако данный метод имеет ряд существенных ограничений в случае синтеза литиевых ферритов. Данные ограничения связаны с низкой термостабильностью некоторых исходных реагентов и незаконченной реакцией синтеза в результате нагрева. Эти негативные факторы могут привести к снижению химической и структурной однородности конечного продукта. Таким образом, для эффективного производства ферритовых материалов применяют различные способы повышения степени гомогенизации, активации исходных реакционных смесей, что приводит к ускорению процесса твердофазного взаимодействия, за счет понижения температуры синтеза.
Существует ряд химических методов, которые применяют для повышения степени гомогенизации реакционных смесей. К таким методам обычно относят: соосаждение солей или гидроксидов [11], распылительный пиролиз [12], самораспространяющийся высокотемпературный синтез [13, 14] и золь-гель [15]. Стоит отметить, что эти методы имеют ограниченную эффективность, в виду их сложности и низкий потенциал для промышленного производства.
С другой стороны, известно, что химическая реакция между твердыми веществами протекает не по всему объему твердых веществ, которые химически взаимодействуют друг с другом, а в зонах контакта между реагирующими частицами. Таким образом, количество контактов между реагирующими частицами и их площадь контакта сильно влияют на начальную стадию твердофазного синтеза. Одним из эффективных способов увеличения количества контактов в исходных реакционных смесях является метод механической обработки порошковых реагентов в высокоэнергетических планетарных мельницах [16–18]. В наших предыдущих исследованиях было подробно показано, влияние механической активации исходных реагентов на получение ферритов при более низкой температуре синтеза [19, 20]. В то же время вопрос влияния плотности исходной смеси на процесс синтеза без использования операции механической активации был рассмотрен только на примере синтеза литиевого феррита Li0.5Fe2.5O4.
Поэтому, в данной работе для изучения влияния реакционной способности исходных порошков с различными исходными плотностями на твердофазное взаимодействие была проведена реакция синтеза литий-титанового феррита. Для этого были подготовлены образцы с объемными плотностями 1 г/см3 и 2.6 г/см3, которые были изготовлены в результате прессование при 0 и 200 МПа соответственно. Кроме того, кинетическая модель и параметры, описывающие процесс синтеза литий-титанового феррита из порошка и пресс-образцов, были получены с использованием кинетического анализа. Кинетический анализ применяли на основе данных, которые были получены в результате термического анализа реакционных смесей.
ЭКСПЕРИМЕНТАЛЬНАЯ ЧАСТЬ
В качестве исходных реагентов были использованы промышленные порошки Fe2O3, TiO2 (“ан.ч.”), Li2CO3 (“х.ч.”). Порошки исходных реагентов предварительно были высушены в лабораторной печи при температуре 200°С. Соотношение исходных реагентов в порошковых смесях было рассчитано в соответствии с уравнением:
(1)
$\begin{gathered} 0.99{\text{L}}{{{\text{i}}}_{{\text{2}}}}{\text{C}}{{{\text{O}}}_{{\text{3}}}} + 3.63{\text{F}}{{{\text{e}}}_{{\text{2}}}}{{{\text{O}}}_{{\text{3}}}} + 0.66{\text{Ti}}{{{\text{O}}}_{{\text{2}}}} \to \\ \to 3.3{\text{L}}{{{\text{i}}}_{{{\text{0}}{\text{.6}}}}}{\text{F}}{{{\text{e}}}_{{2.2}}}{\text{T}}{{{\text{i}}}_{{{\text{0}}{\text{.2}}}}}{{{\text{O}}}_{4}} + 0.99{\text{C}}{{{\text{O}}}_{2}}{\kern 1pt} \uparrow {\kern 1pt} . \\ \end{gathered} $После этого смесь исходных реагентов Li2CO3–Fe2O3–TiO2 была разделена на две партии. Первая часть исследовалась в виде порошка с насыпной плотностью 1 г/см3 (образец S1). Вторую часть прессовали путем одностороннего холодного прессования в форме таблеток диаметром 9 мм и толщиной 2 мм. Давление прессования составило 200 МПа, время 3 мин. В работе использовали гидравлический пресс марки ПГр-10. Плотность таких образцов составила 2.6 г/см3 (образец S2).
Структурные параметры исходных порошков оценивались с помощью рентгеноструктурного анализа с использованием дифрактометра ARL X’TRA (Швейцария). На рис. 1 приведена дифрактограмма для смеси исходных реагентов для получения литий-титановых ферритов: α-Fe2O3 (PDF № 40-142), Li2CO3 (PDF № 66-941), и TiO2 (PDF № 82-656).
Рис. 1.
Результаты рентгенофазового анализа для исходной смеси Li2CO3 + Fe2O3 + TiO2 : 1 – Fe2O3, 2 – Li2CO3, 3 – TiO2, 4 – шпинель.
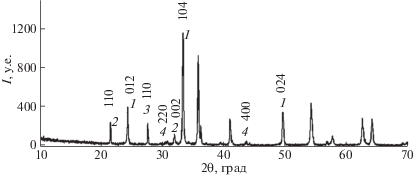
Пики при 2θ ≈ 30.3°, 43° соответствуют шпинельной фазе γ-Fe2O3 (PDF № 79-196), которую обычно добавляют в небольшом количестве ∼1 мас. % в оксид железа для производства литиевых ферритов. С помощью программы “Powder Cell” определены структурные параметры, размер областей когерентного рассеяния (ОКР) и величины внутренних упругих микронапряжений (Δd/d) исследованных порошков. Эти данные сведены в табл. 1.
Таблица 1.
Структурные параметры и фазовый состав для исходных реагентов (R – размер кристаллитов)
Фаза | Параметры решетки, Ǻ | R, нм | (Δd/d) × 103 |
---|---|---|---|
α-Fe2O3 | а = b = 5.033, c = 13.753 | 89 | 0.6 |
Li2CO3 | а = 8.259, b = 4.974, c = 6.198 | 159 | 0.3 |
TiO2 | а = b = 4.594, c = 2.959 | 74 | 0.4 |
γ-Fe2O3 | a = b = c = 8.344 | 42 | 1.5 |
Термический анализ испытуемых образцов проводился с использованием синхронного термического анализатора STA 449C Jupiter (Netzsch, Германия) с чувствительностью весовой части ~0.1 мкг. Исследования проводились в корундовых тиглях (Al2O3) в атмосфере воздуха. Нагрев осуществлялся до 800°С с различной скоростью нагрева в диапазоне 2.5–20 К/мин. Программное обеспечение Proteus Analysis и Thermokinetics были использованы для обработки данных, полученных в результате проведения термического анализа. Кроме того, программу Thermokinetics использовали для проведения кинетического анализа.
ОБСУЖДНИЕ РЕЗУЛЬТАТОВ
На рис. 2 представлены результаты термического анализа для образов с разной исходной плотностью. Поведение термогравиметрической кривой (ТГ-кривая) на стадии нагрева для образцов S1 и S2 соответствует процессу синтеза литий-титанового феррита. Независимо от исходной плотности реакционной смеси, на ТГ-кривых наблюдается потеря массы. В образцах S1 потеря массы начинается при ~500°С. Судя по поведению дифференциальной термогравиметрической кривой (ДТГ-кривая) данный процесс состоит из двух этапов. Первый этап характеризуется взаимодействием исходных оксидов и карбоната в смеси с последующим разложением Li2CO3 в интервале температур 550–680°C, а второй c процессом плавления остатков карбоната лития при ~723°C.
ДТГ-кривая повторяет форму кривой дифференциально-сканирующей калориметрии (ДСК-кривая), судя по которой видно, что наблюдаемое изменение массы можно объяснить эндотермическим эффектом (87 Дж/г), протекающими в температурном интервале 500–720°C. По ТГ-кривой была вычислена потеря массы в процессе нагрева, которая составила 6.2 ± 0.1%. Данное значение хорошо коррелируется с теоретическим значением процесса потери массы по формуле (1). Немного иная картина наблюдается для образца S2 с плотностью 2.6 г/см3 (рис. 2, S2 ). Основная потеря массы в процессе нагрева начинается при температуре ~420°C, что на 80°C меньше, чем в образцах S1. Общее изменение массы так же составило 6.2 ± 0.1%. На ДСК-кривой наблюдается эндотермический пик площадью 111 Дж/г, который соответствует потере массы в интервале 430–720°C. Небольшой эндотермический пик (1.7 Дж/г) наблюдаемый при температуре 753°C характерен для фазового перехода α → β в феррите Li0.5Fe2.5O4. Данная переходная фаза формируется при синтезе литий-замещенных феррошпинелей, включая литий-титановые ферриты.
Сравнивая ТГ/ДСК-кривые для образцов с разной исходной плотностью (рис. 2) можно сделать вывод, что твердофазное взаимодействие в системе Fe2O3–Li2CO3–TiO2 сильно зависит плотности порошковой смеси. Так, в компактированных образцах (S2), при нагреве уже наблюдается образование шпинельной фазы литиевого феррита. Как показано для чистого литиевого феррита ДСК пик при таком фазовом переходе составляет ∼13 Дж/г [21]. Следует полагать, что в данных условиях формируется всего лишь ∼13% фазы литиевого феррита.
По данным термогравиметрического анализа был проведен кинетический анализ реакции синтеза литий-титанового феррита. Измерения ТГ-кривых проводились при различных скоростях нагрева: 2.5, 5, 10 и 20 К/мин в неизотермическом режиме. Как известно [22, 23], основная цель кинетического анализа заключается в описании реакции твердофазного взаимодействия математическими методами и нахождении модели и параметров, которые наилучшим образом могут описать соответствующий процесс. Кинетическая модель и соответствующие параметры применяются в оптимизации технологических режимов термического синтеза [24, 25]. Уравнение кинетического анализа обычно в общем виде представляют следующим уравнением:
где, α – степень превращения, f(α) – функция от степени превращения, зависящая от температуры, и k – параметр, который может быть выражен через уравнение Аррениуса: где A – предэкспоненциальный множитель, Ea – энергия активации, T – температура и R – газовая постоянная (8.314 Дж K–1моль–1).Конечное выражение для определения скорости процесса термического разложения:
(4)
$d\alpha {\text{/}}dt = kf(\alpha ) = Af(\alpha ){\text{exp}}\left( { - \frac{{{{E}_{{\text{a}}}}}}{{RT}}} \right).$Согласно рис. 3, можно заметить, что кинетические параметры сильно зависят от степени превращения во всем диапазоне. Данный факт указывает, что процесс синтеза описывается несколькими стадиями независимо от плотности реакционной смеси. Форма кривых энергии активации для образов S1 и S2 указывает на то, что процесс синтеза литий-титанового феррита протекает по двухступенчатому механизму с различными кинетическими параметрами. Таким образом, можно предположить, что для определения подходящей кинетической модели и кинетических параметров термического синтеза литий-титанового феррита необходимо использовать метод многомерной нелинейной регрессии. Данный метод позволяет получить модель реакции и параметры Аррениуса для каждого из этапов термического синтеза.
С помощью программы Thermokinetics удалось определить, что наилучшие результаты моделирования между ТГ-кривыми и математическими моделями были получены при использовании двухстадийного механизма ${\text{A}} \to \,~\,{\text{B}}~\,\, \to {\text{C}}$ (где A → B это первая стадия синтеза, B → C это вторая стадия). Математическое моделирование проводилось в соответствии с несколькими, широко известными кинетическими моделями, приведенными в табл. 2.
Таблица 2.
Примеры применяемых кинетических реакций
Обозна-чение | $f(\alpha )$ | Название реакции |
---|---|---|
F1 | e | Реакция первого порядка |
F2 | e2 | Реакция второго порядка |
Fn | en | Реакция n-го типа |
D1 | 0.5/(1 – e) | Одномерная диффузия |
D2 | –1/ln(e) | Двухмерная диффузия |
D3 | $1.5{{e}^{{1/3}}}{\text{/}}({{e}^{{ - 1/3}}} - 1)$ | Трехмерная диффузия (Уравнение Яндера) |
D4 | $1.5e{\text{/}}({{e}^{{ - 1/3}}} - 1)$ | Трехмерная диффузия (уравнение Гинстлинга–Бронштейна) |
На рис. 4 представлены результаты кинетического анализа методом нелинейной регрессии для обоих типов образцов, а вычисленные кинетические параметры занесены в табл. 3. Наилучшие результаты для образца S1 (рис. 4) получены при использовании на первом этапе синтеза диффузионной модели Яндера (D3), а на втором этапе – Гинстлинга–Бронштейна (D4).
Рис. 4.
Результаты нелинейной регрессии для образцов S1 и S2 (линии – результаты моделирования, символы экспериментальные данные).
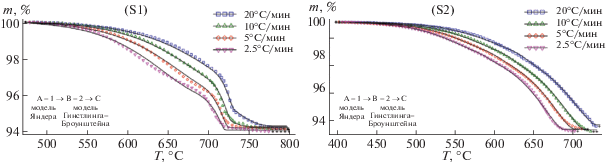
Таблица 3.
Значения кинетических параметров для исследуемых образцов
Образец | $\lg {{A}_{1}}$, [с–1] | Eа1, кДж/моль | $\lg {{A}_{2}}$, [с–1] | Eа2, кДж/моль | α |
---|---|---|---|---|---|
S1 | 14.8 ± 0.2 | 272 ± 3.3 | 35.7 ± 0.6 | 708 ± 4.4 | 0.69 ± 0.01 |
S2 | 12.5 ± 0.1 | 258 ± 1.3 | 17.5 ± 0.2 | 380 ± 1.3 | 0.31 ± 0.01 |
При использовании данных моделей (D3 → → D4) рассчитаны следующие кинетические параметры: энергия активации первой стадии составляет значения Еа = 272 кДж/моль. Данное высокое значение может быть связано с реакцией разложения карбоната лития в результате нагрева. На второй стадии энергия активации значительно увеличивается, достигая значений 708 кДж моль–1. Данное увеличение энергии активации, возможно, связано с процессом плавления непрореагировавших остатков карбоната лития при температуре ~720°C, согласно термическому анализу. Кроме, того данные значения кинетических параметров хорошо коррелируются с параметрами Аррениуса из анализа методом Фридмана (рис. 3, S1 ).
Для образцов с более высокой плотностью (S2) процесс синтеза литий-титановго феррита, так же хорошо описывается двухстадийным процессом, с применением моделей Яндера и Гинстлинга–Бронштейна на обоих стадиях (рис. 4, S2 ). Энергии активации ∼258 кДж моль–1 и 380 кДж моль–1, полученные с помощью многомерной нелинейной регрессии для первой и второй стадий (табл. 3), находятся в очень хорошем соответствии со значениями, полученными методом Фридмана (рис. 3, S2 ).
Энергия активации первой стадии немного ниже, но сопоставима со значением Еа для образца S1 на первой стадии. Далее энергия активации увеличивает, но имеет значение намного ниже, чем для образца S1. Возможно, это связано с тем, что порошки реакционной смеси после прессования имеют большее число контактов между реагентами. В таких образцах взаимодействия между частицами осуществляются на атомном уровне. Следовательно, процесс твердофазного взаимодействия может начаться при более низких температурах и с меньшими затратами энергии. Стоит отметить, что проведенные расчеты кинетических параметров, характеризуются высоким коэффициентом корреляции (~0.9997).
Таким образом, влияние исходной плотности смеси Fe2O3–Li2CO3–TiO2 на твердофазный синтез литий-титановых ферритов было изучено с помощью термического и кинетического анализов. Термический анализ показал, что значительное снижение массы характерно для обоих образцов и связано с разложением карбоната лития и процессов взаимодействия оксидов при нагреве. Кроме того, данное взаимодействие протекает в два этапа для обоих типов образцов. Стоит отметить, что реакция твердофазного взаимодействия для образцов S2 начинает протекать при более низких температурах. Кроме того, основное отличие образцов спресованных при давлении 200 МПа (S2), заключается в образовании небольшого количества феррита лития Li0.5Fe2.4O4, согласно кривым калориметрии.
Так же используя термогравиметрические кривые, полученные при разных скоростях нагрева, и программное обеспечение Netzsch Thermokinetics был проведен кинетический анализ процесса синтеза литий-титанового феррита. Результаты кинетического анализа показали, что реакция твердофазного взаимодействия является диффузионной. Было показано, что синтез обоих образцов лучше всего описывается двухступенчатым механизмом $({\text{A}} \to {}^{1}{\text{B}} \to {}^{2}{\text{C}})$. В независимости от способа изготовления образцов были применены диффузионные модели Яндера и Гинстлинга–Бронштейна на первом и втором этапах соответственно. Показано значительное уменьшение энергии активации и предэкспоненциального множителя процесса синтеза феррита из спресованных образцов.
Исследование выполнено при финансовой поддержке Российского научного фонда (грант № 19-72-10078).
Список литературы
Sharif M., Jacob J., Javed M. et al. // Physica. B. 2019. № 567. P. 45.
Mazen S.A., Abu-Elsaad N.I. // Appl. Nanosci. 2015. № 5. P. 105.
Guo J., Zhang H., He Z., Li S., Li Z. // J. Mater Sci: Mater Electron. 2018. № 29. P. 2491.
Kounsalye J.S., Kharat P.B., Bhoyar D.N., Jadhav K.M. // Ibid. 2018. № 29. P. 8601.
Gao Y., Wang Z., Shi R., Zhang H., Zhou X. // J. Alloy. Compd. 2019. № 805. P. 934
Kavanlooee M., Hashemi B., Maleki-Ghaleh H., Kavanlooee J. // J. Electron. Mater. 2012. № 41. P. 3062.
Yin Q., Liu Y., Liu Q. et al. // J. Mater. Sci.: Mater. Electron. 2019. № 30. P. 5430.
Guo R., Yu Z., Yang Y. et al. // J. Superconductivity and Novel Magnetism. 2017. № 30. P. 1767.
Teixeira S.S., Graça M.F., Costa L.C. // J. Non-Crystalline. Solids. 2012. № 358. P. 1924.
Hrešĉak J., Maliĉ B., Cilenšek J., Benĉan A. // J. Therm. Anal. Calorim. 2017. № 127. P. 129.
Wang Y., Yang L., Zhang Y. et al. // Russ. J. Phys. Chem. A. 2019. № 93. P. 2771.
Kotsikau D., Ivanovskaya M., Pankov V., Fedotova Y. // Solid State Sci. 2015. № 39. P. 69.
Rathod V., Anupama A.V., Jali V.M. et al. // Ceram. Int. 2017. № 43. P. 14431.
Rathod V., Anupama A.V., Vijaya Kumar R. et al. // Vib. Spectrosc. 2017. № 92. P. 267.
Berezhnaya M.V., Mittova I.Y., Pero N.S. et al. // Russ. J. Inorgan. Chem. 2018. № 63. P. 742.
Berbenni V., Bruni G., Milanese C. et al. // J. Therm. Anal. Calorim. 2018. № 133. P. 413.
Parlak T.T., Apaydin F., Yildiz K. // Ibid. 2017. № 127. P. 63.
Kavanlooee M., Hashemi B., Maleki-Ghaleh H., Kavanlooee J. // J. Electron. Mater. 2012. № 41. P. 3082.
Lysenko E.N., Nikolaev E.V., Surzhikov A.P. et al. // J. Therm. Anal. Calorim. 2019. № 138. P. 2005.
Lysenko E.N., Nikolaev E.V., Surzhikov A.P., Nikolaeva S.A. // Mater. Chem. Phys. 2020. № 239. 122055.
Lysenko E.N., Frangulyan T.S., Surzhikov A.P., Ghyngazov S.A. // J. Therm. Anal. Calorim 2012. № 108. P. 1207.
Saikia P., Blaise Allou N., Borah A., Goswamee R.L. // Mater. Chem. Phys. 2017. № 186. P. 52.
Opfermann J. // J. Therm. Anal. Calorim. 2000. № 60. P. 641.
Lysenko E.N., Nikolaev E.V., Surzhikov A.P. // IOP Conf Series: Mater Sci Eng. № 110. 012092.
Sharma P., Uniyal P. // J. Therm. Anal. Calorim. 2017. № 128. P. 875.
Sarsenbekova A.Z., Kudaibergen G.K., Burkeev M.Zh., Burkeeva G.K. // Rus. J. Phys. Chem. A. 2019. № 93. P. 1252.
Erceg M., Krešić I., Jakić M., Andričić B. // J. Therm. Anal. Calorim. 2017. № 127. P. 789.
Дополнительные материалы отсутствуют.
Инструменты
Журнал физической химии