Физика и химия стекла, 2019, T. 45, № 1, стр. 65-73
Влияние методов подготовки силикат-натриевой смеси на формирование структуры пеностеклокерамики
К. С. Иванов *
Институт криосферы Земли Тюменского научного центра СО РАН
625000 Тюмень, ул. Малыгина, 86, а/я 1230, Россия
* E-mail: sillicium@bk.ru
Поступила в редакцию 28.12.2017
После доработки 08.10.2018
Принята к публикации 14.09.2018
Аннотация
Рассмотрено получение пеностеклокерамики на основе иатомита и гидроксида натрия. Исследованы свойства материала в зависимости от способов воздействия на смесь компонентов перед обжигом. От скорости нагревания образцов до температуры обжига. Применение автоклавной обработки смеси приводит к снижению средней плотности материала в 1.7 раз. Установлена закономерность изменения силикатного модуля смеси в зависимости от вида оказываемого на нее воздействия. Получены образцы пеностеклокерамики со средней плотностью 0.45–0.75 г/см3 и прочностью при сжатии 3.4–15.1 МПа.
ВВЕДЕНИЕ
Высокое содержание в опал-кристобалитовых породах аморфного кремнезема предопределяет возможность его растворения в щелочах с образованием гидратированных щелочных силикатов. Известный, т.н. мокрый способ, получением жидких стекол из опал-кристобалитовых пород, несмотря на всю простоту, имеет недостаток, связанный с окраской продукта в темно-бурый цвет и необходимостью отделения нерастворимого остатка, который образуется ввиду высокого содержания сопутствующих примесей в виде глинистых минералов, кварца, органики и т.п. [1, 2]. Существуют направления прямого применения жидких стекол с нерастворимым остатком (минуя стадию его отделения) в случаях, где нерастворимый остаток может играть структурообразующую роль, например, при получении материалов щелочной активации [3], либо щелочно-силикатных вяжущих композиций [4, 5].
Альтернативным направлением прямого применения силикат-натриевых композиций на основе опал-кристобалитовых пород и щелочей, является синтез пеностеклокерамики – неорганического силикатного материала ячеистого строения [6, 7]. Синтез материала сопровождается термическим вспениванием, который характерен при нагревании жидких стекол и используемый в получении утеплителей горячего вспенивания [8]. Образование ячеистых материалов сопровождается удалением из гидратированных силикатов молекулярной и силанольной воды с последующей поликонденсацией кремнекислородных анионов. Дальнейшее нагревание приводит к образованию структур, близких к стеклам, полученным из расплава [9].
Гранулированную пеностеклокерамику можно использовать в конструкциях автодорог с целью защиты грунтов от промерзания и морозного пучения в зимний период [10].
Пеностеклокерамика является аналогом пеностекла, которое сочетает в себе высокие теплоизоляционные свойства наряду с негорючестью и сравнительно высокой механической прочностью, что делает пеностекло одним из прогрессивных неорганических теплоизоляционных материалов [6, 7]. Существенным недостатком пеностеклокерамики, является необходимость применения дорогостоящего гидроксида натрия. Снижение его содержания, с учетом сохранения функциональных свойств пеностеклокерамики, является актуальной научно-технической проблемой. Решением этой проблемы может быть активизация растворения аморфных форм SiO2 в сырьевой смеси.
Цель работы – исследование влияния способов активизации сырьевой смеси на структуру и свойства пеностеклокерамики. В задачи работы входило исследование следующих способов: механическое воздействие на стадии перемешивания компонентов; гидротермальное выщелачивание смеси до ее вспенивания, активизирующее процесс растворения аморфных фаз кремнезема опал-кристобалитовой породы (что традиционно используется в технологии получения жидкого стекла [1]).
МАТЕРИАЛЫ И МЕТОДЫ ИССЛЕДОВАНИЯ
В исследованиях использовался диатомит Ирбитского месторождения Свердловской области следующего химического состава, в мас. %: 77.6SiO2; 0.4CaO; 0.9MgO; 7.3Al2O3; 4.4Fe2O3; 0.6TiO2; 0.4Na2O; 0.8K2O; 0.7SO3. Потери при прокаливании достигали 6.9%. Диатомит высушивался до постоянной массы при 100°C и измельчался в порошок до полного прохода через сито с размером ячейки 0.16 мм.
Материалы исследовали с применением сканирующего электронного микроскопа Jeol JSM‑6510A (Япония). Фазовый состав определяли с помощью дифрактометра ДРОН-6 (Россия), длина волны 0.179 нм, CuKα-излучение, Fe-фильтр.
Сканирующая электронная микроскопия свидетельствует о том, что диатомит сложен в основном из обломков панцирей диатомей – ископаемых водорослей, состоящих из аморфного кремнезема (рис. 1). Рентгенофазовый анализ показал, что образец содержит опал, β-кварц и глинистые минералы. Определение концентрации SiO2 в жидком стекле, полученном из диатомита по мокрому способу, свидетельствует о содержании в диатомите 44.6% аморфного кремнезема. Оставшиеся 55.4% от массы диатомита приходятся на нерастворимый остаток и органические примеси.
При получении пеностеклокерамики могут применяться два вида совмещения измельченной опал-кристобалитовой породы с раствором NaOH. Первый состоит в приготовлении суспензии в реакторе с мешалкой и ее последующей сушкой в распылительной сушилке. Затем полученный полуфабрикат в виде зерен измельчается и вспенивается при 800–900°С с получением готовых изделий (гранул, плит, блоков и т.п.).
Второй способ состоит в экструзии пресс-порошка, приготовленного из опал-кристобалитовой породы и раствора NaOH с помощью гранулирующего шнекового пресса (экструдера). В результате формируются гранулы заданных размеров, которые в дальнейшем подвергаются обжигу раздельно, с получением гранулированной пеностеклокерамики, либо в специальных формах, с получением блоков, скорлуп и т.п. Этот способ имеет некоторые преимущества: происходит смешивание компонентов и грануляция смеси, не требуется испарение большого количества влаги при сушке смеси для получения полуфабриката, существует возможность оказания дополнительного механического воздействия на смесь шнеком.
В данном исследовании смеси готовили вторым способом. Пресс-порошок готовили вручную в стальной сферической чаше, с использованием раствора NaOH с концентрацией 40 мас. %. При смешивании учитывали массовое соотношение между диатомитом и сухим NaOH, принятое равным 9.1. Теоретически, это дает молярное соотношение между аморфным кремнеземом диатомита и щелочью (в пересчете на Na2O), равное 5. У традиционных жидких стекол последнее соотношение (т.н. силикатный модуль) составляет 3–4.
Используемый в исследованиях лабораторный экструдер имел следующие характеристики: диаметр шнека – 80 мм, шаг витков шнека – 80 мм, число оборотов шнека – 45 мин–1, номинальный крутящий момент привода – 490 Н · м, диаметр отверстий в гранулирующей решетке – 5 мм. Получали гранулы диаметром и длиной 5 мм, средняя плотность гранул была 1.65 г/см3 при их весовой влажности 17% (при температуре сушки 100°С).
Смесь подвергали трем видам воздействия: – механическому, путем возврата гранулированной смеси в экструдер и ее многократной грануляции (M0); гидротермальной обработке гранулированной смеси в среде насыщенного водяного пара при 90°С, в течение часа (MG); автоклавной обработке гранулированной смеси при давлении водяного пара 1.5 МПа, в течение ч (MA).
В дальнейшем гранулы высушивали при 80°С и измельчали с отбором фракции 1–2.5 мм для последующего обжига. Измельченную смесь засыпали в формы из жаростойкой стали и подвергали обжигу в муфельной печи. Охлаждение форм происходило вместе с печью. Из полученного материала выпиливали образцы в виде кубов с длиной ребра 30 мм. Среднюю плотность материала определяли как отношение массы образца к его объему с погрешностью ±0.01 г/см3.
Степень влияния трех указанных способов воздействия на смесь оценивали в основном по изменению средней плотности образцов, т.к. от этого показателя напрямую зависит расход NaOH на единицу объема материала. Плотность теплоизоляционного материала в основном определяет значение его основной характеристики – коэффициента теплопроводности. Определяли прочность при сжатии, ячеистую структуру образцов исследовали с помощью цифрового микроскопа Levenhuk DTX 90.
В зависимости от способа воздействия, у смесей определялся силикатный модуль определяли в завимости от способа воздействия (m). При равном содержании Na2O в смесях, он характеризует количество SiO2 в растворенном состоянии, что может оказывать влияние на вспенивание смесей. Значение m определяли с помощью известного аналитического экспресс-метода [11]. Навеску смеси, высушенную до постоянной массы, измельчали до размеров 0.1 мм. Навеску подвергали кипячению в воде (в пикнометре на водяной бане) при температуре 98°С в течение часа. Полученный раствор анализировали на содержание Na2O и SiO2.
РЕЗУЛЬТАТЫ И ОБСУЖДЕНИЕ
Влияние механического воздействия на смесь анализировали, путем ее многократной грануляции в экструдере. Оптимальной является вторичная грануляция. Большее число грануляций не приводит к увеличению плотности гранул и изменению силикатного модуля смеси. После четвертой–пятой грануляции происходит резкое отверждение смеси в экструдере (вплоть до образования камнеподобной массы) в результате нагревания до 80–90°С.
Дальнейшие эксперименты проводили с применением смеси, подвергнутой вторичной грануляции. На рис. 2 представлено изображение скола просушенной гранулы. Следы обломков панцирей диатомовых водорослей отсутствуют, что говорит об их растворении под воздействием раствора NaOH.
Исследование воздействия обжига позволило установить взаимосвязь между скоростью нагревания смесей и структурой образцов материала. Быстрое нагревание смесей, помещенных в предварительно прогретую до температуры обжига муфельную печь, приводит к формированию крупных пор неправильной формы, размером 2–3 мм. Плавное нагревание со скоростью 30°С/мин, приводит к формированию упорядоченной структуры с порами более правильной формы, размером ~0.5 мм. Средняя плотность образцов в первом случае в 1.4 раза ниже, чем во втором. В первом случае возможно создание пеностеклокерамики с более выраженными теплоизоляционными свойствами, во втором – с прочностными свойствами. Пористая структура образцов после обжига при 850°С, в зависимости от скорости нагревания, представлена на рис. 3, а, б. Поверхность пеностеклокерамики обладает характерным стеклянным блеском.
Рис. 3.
Пористая структура пеностеклокерамики при температуре обжига 850°С: плавный нагрев (а); быстрый нагрев (б).
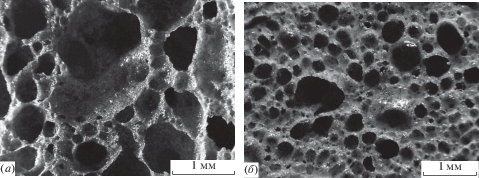
При быстром нагревании происходит оплавление поверхности смеси, что препятствует выходу порообразователя (водяного пара). Избыток порообразователя приводит к коалесценции и укрупнению пор, что заметно на рис. 3, а. В случае плавного нагревания, часть порообразователя выходит из смеси до ее перехода в пиропластическое состояние. В результате образцы имеют более высокую среднюю плотность и меньший размер пор (рис. 3, б).
С целью определения оптимальной температуры обжига образцов, исследовали эволюцию структуры и изменение средней плотности при плавном повышении температуры и выдержке при заданной температуре в течение 20 мин.
Начиная с температуры 350°С (рис. 4, б), в отличие от 250°С (рис. 4, а), наблюдается разрыхление смеси и начало ее поризации.
Рис. 4.
Воздействие температуры на эволюцию пористой структуры, °С: 250 (а), 350 (б), 450 (в), 550 (г), 650 (д), 750 (е).
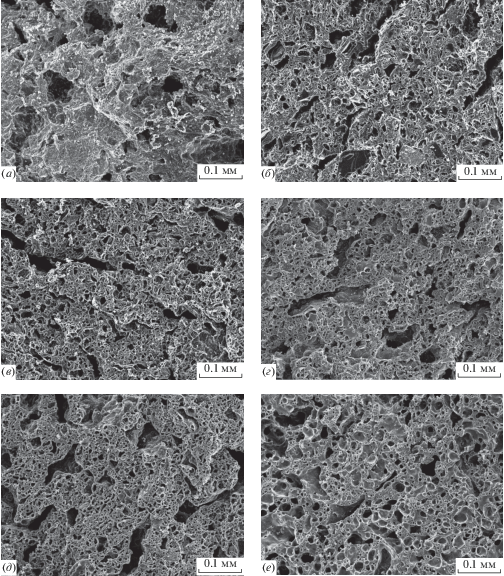
При 650°С (рис. 4, д) можно видеть зарождение новых пор в перегородках уже возникших, что говорит о непрерывном процессе поризации, начиная с 350°С (рис. 4, б). Отдельные замкнутые поры округлой формы можно различить начиная с 750°С (рис. 4, е). Дальнейшее изучение пористой структуры материала при 850°С (рис. 3, б) проводили с помощью оптического микроскопа, в связи с образованием пор порядка 0.5 мм. Хорошо различимы отдельные, преимущественно замкнутые поры сферической формы с остеклованной поверхностью.
Увеличение температуры обжига до 900°С, приводит к возрастанию средней плотности образцов за счет усадки и уплотнения пены. Минимальное значение средней плотности соответствует температуре 850°С, в связи с чем, данную температуру обжига следует считать оптимальной. Сокращение времени выдержки приводит к увеличению средней плотности материала вследствие незавершенности процесса поризации смеси. Время выдержки образцов – 20 мин является оптимальным.
Результаты влияния вида обработки смеси на среднюю плотность образцов представлены на рис. 5 в виде диаграммы. В ряду M0–MG–MA (горизонтальная ось диаграммы) наблюдается увеличение интенсивности воздействия на смесь перед обжигом в виде возрастания температуры и давления водяного пара. Средняя плотность образцов в указанном ряду снижается и составляет: 0.55, 0.47 и 0.45 г/см3 при быстром нагреве (кривая 1, рис. 5) и, соответственно, 0.75, 0.65 и 0.52 г/см3 (кривая 2, рис. 5) при плавном нагреве. В первом случае средняя плотность образцов MG и MA в сравнении с M0, ниже в 1.17 и 1.22 раза соответственно. Во втором случае (плавный нагрев), снижение составляет 1.15 и 1.44 раза соответственно. Разница в средней плотности образцов MA с быстрым нагревом до температуры обжига, в сравнении с M0 при плавном нагреве, достигает почти 1.7 раза (крайняя правая точка на кривой 1 и крайняя левая точка на кривой 2 соответственно, рис. 5). Значения средней плотности образцов в зависимости от вида воздействия на смесь представлены в табл. 1. Было установлено, что величина открытой пористости, о которой можно судить по водопоглощению образцов, несущественно зависит от вида воздействия на исходную смесь, т.к. объемное водопоглощение всех образцов лежало в пределах 5–7%.
Рис. 5.
Изменение средней плотности и силикатного модуля смеси: 1 – быстрый нагрев; 2 – плавный нагрев; 3 – значение m для смеси.
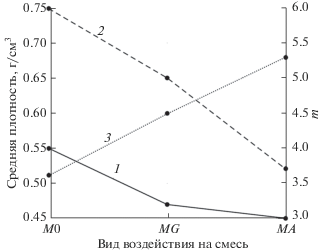
Таблица 1.
Влияние вида воздействия на среднюю плотность образцов
№ пп | Вид воздействия, согласно маркировке исходных смесей | Средняя плотность образцов, г/см3 |
---|---|---|
Быстрое нагревание печи | ||
1 | M0 | 0.55 |
2 | MG | 0.47 |
3 | MA | 0.45 |
Медленное нагревание печи | ||
4 | M0 | 0.75 |
5 | MG | 0.65 |
6 | MA | 0.52 |
На правой вертикальной оси диаграммы (рис. 5) представлена взаимосвязь между видом обработки смеси и значением m смеси. В ряду M0–MG–MA происходит увеличение значения m с 3.6 до 4.5 и 5.3 (кривая 3, рис. 5). В случае MA, значение m превышает расчетное, что говорит о полном растворении аморфного и частичном растворении кристаллического SiO2 (который входит в состав диатомита в виде кварца) при повышенном давлении.
Наиболее вероятной причиной снижения средней плотности в случаях MG и MA, является более высокое содержание растворенного в смеси SiO2. Высокомодульные гидратированные щелочные силикаты содержат в составе большее количество химически связанной воды, что дает дополнительное количество порообразователя при обжиге.
На рис. 6 представлены графики, характеризующие влияние средней плотности образцов на прочность при сжатии в зависимости от скорости нагревание образцов. В ряду MA–MG–M0 наблюдается увеличение прочности при сжатии с ростом средней плотности образцов: с 3.4 до 6.2 МПа для быстрого с 7.4 до 15.1 для плавного нагревания.
Между кривыми 1 и 2 существует разрыв (рис. 6). Прочность при сжатии образцов MA с быстрым нагреванием (крайняя левая точка на кривой 2, рис. 6) выше по сравнению с образцами M0 с быстрым нагреванием (крайняя правая точка на кривой 1, рис. 6): 7.4 и 6.2 Мпа соответственно. Средняя плотность составляет 0.53 и 0.55 г/см3. Это свидетельствует о формировании у образцов с медленным нагревом более высокопрочной и упорядоченной структуры.
Теплопроводность пеностеклокерамики определяли на образцах 100 × 100 × 10 мм с помощью прибора ИТП-МГ-4 (метод стационарного теплового потока). При средней плотности образцов 0.45–0.75 г/см3, значение теплопроводности составляет 0.125–0.147 Вт/(м К).
ЗАКЛЮЧЕНИЕ
1. Показано, что наибольшее влияние на свойства получаемого материала оказывает автоклавная обработка смеси и в меньшей степени гидротермальная обработка при атмосферном давлении. Важным является и увеличение скорости нагревания смеси до температуры обжига, при этом средняя плотность образцов, полученных из смеси без специальной обработки изменяется с 0.75 до 0.55 г/см3. Применение гидротермальной обработки смеси способствует дальнейшему снижению средней плотности при плавном нагревании с 0.75 до 0.65 г/см3, а автоклавной обработки – до 0.52 г/см3, при быстром нагревании происходит соответственное снижение средней плотности с 0.55 до 0.47 и 0.45 г/см3. Изменения средней плотности образцов, по-видимому, можно объяснить изменением силикатного модуля смеси, который возрастает с 3.6 до 5.3 по мере увеличения интенсивности воздействия. Влияние силикатного модуля на рост кратности вспенивания образцов может объясняться как увеличением содержания химически связанной воды в высокомодульных гидратированных силикатах, так и формированием в смеси искусственных цеолитов.
Предложенные способы подготовки смеси позволяют снизить среднюю плотность пеностеклокерамики с 0.75 до 0.45 г/см3, т.е. почти в 1.7 раза. Это дает эффект в виде снижения расхода гидроксида натрия за счет пропорционального увеличения объема материала на выходе. Однако, необходимо учитывать сопутствующие изменения пористого строения материала при быстром нагреве, что приводит к снижению прочности при сжатии.
Список литературы
Григорьев П.Н., Матвеев М.А. Растворимое стекло. Москва.: Стройиздат, 1956. 414 с.
Филиппович Е.Н., Хацринов А.И., Егорова Т.В. Выбор оптимальной обработки диатомита Инзенского месторождения для получения кристаллических силикатов натрия // Вестник КазГУ. 2010. № 8. С. 272–276.
Иванов К.С., Коротков Е.А. Исследование влияния силикат-натриевых суспензий на свойства материалов щелочной активации // Неорганические материалы. 2017. Т. 53. № 9. С. 993–1000. [Ivanov K.S., Korotkov E.A. Effect of Sodium Silicate Slurries on the Properties of Alkali-Activated Materials // Inorganic Materials. 2017. V. 53. № 9. P. 973–979.].
Иванов Н.К, Радаев. С.С., Шорохов С.М. Структурообразование в системах на основе жидкого стекла и опаловых пород // Строительные материалы. 1998. № 8. С. 24–25.
Иващенко Ю.Г., Страхов А.В. Свойства силикатнатриевого связующего, полученного на основе силицитовых пород методом гидротермального синтеза // Вестник Саратовского ГТУ. 2010. Т. 4. № 1(49). С. 193–200.
Kazantseva L.K., Rashchenko S.V. Chemical processes during energy-saving preparation of lightweight ceramics // J. Am. Ceram. Soc. 2014. V. 97 [6]. P. 1743–1749.
Орлов А.Д. Оптимизированная одностадийная технология гранулированного пеностекла на основе низкотемпературного синтеза стеклофазы // Строительные материалы. 2015. № 1. С. 24–27.
Малявский Н.И. Щелочносиликатные утеплители. Свойства и химические основы производства // Российский химический журнал. 2003. Т. XLVIV. № 4. С. 39–45.
Hans R., Dorit B., Jörg T. Structural evolution of sodium silicate solutions dried to amorphous solids // J. Non-Crystalline Solids. 2001. V. 293–295. P. 752–757.
Иванов К.С., Коротков Е.А. Исследование воздействия слоя гранулированной пеностеклокерамики на температурный режим промерзающего грунта // Основания, фундаменты и механика грунтов. 2017. № 5. С. 32–37.
Соколович В.Е. К экспресс-методу определения модуля раствора силиката натрия // Стекло и керамика. 1975. № 10. С. 36. [Sokolovich V.E. Rapid method of determining the modulus of sodium silicate solution // Glass Ceram. 1975. V. 32. P. 707–708.].
Дополнительные материалы отсутствуют.
Инструменты
Физика и химия стекла