Физика и химия стекла, 2020, T. 46, № 2, стр. 184-195
Влияние связующего на пористую структуру цеолитных композиций и их каталитическую активность
И. Е. Кононова 1, *, Е. В. Мараева 1, С. А. Скорникова 2, В. А. Мошников 1
1 Санкт-Петербургский государственный электротехнический университет “ЛЭТИ”
197376 Санкт-Петербург, ул. Профессора Попова, 5, Россия
2 Иркутский национальный исследовательский технический университет
664074 Иркутск, ул. Лермонтова, 83, Россия
* E-mail: iegrachova@mail.ru
Поступила в редакцию 13.12.18
После доработки 13.09.19
Принята к публикации 05.12.19
Аннотация
Работа посвящена изучению параметров пористой структуры и каталитической активности материалов, содержащих цеолиты структурных типов ZSM-5 и ВЕА и гидроксиды алюминия от различных производителей. Показано, что возможно целенаправленное регулирование параметров пористой структуры цеолитных композиций, которые служат основой для катализаторов многих процессов, путем варьирования природы цеолита, носителя, пептизатора и их количества. Установлена взаимосвязь текстурных характеристик композиций с их каталитической активностью в реакции изомеризации н-гексана.
ВВЕДЕНИЕ
В настоящее время область применения цеолитов и материалов на их основе все более расширяется [1–3] и не ограничивается их использованием в качестве адсорбентов и катализаторов нефтепереработки.
Цеолиты относятся к микропористым материалам. Однако для каталитических процессов, особенно с тяжелым нефтяным сырьем, требуются материалы, содержащие и мезо- и макропоры [4], а развитая система микропор цеолитов из-за диффузионных ограничений оказывает существенное влияние на скорость реакций, катализируемых цеолитами [5].
Для более эффективного использования активной поверхности цеолитного катализатора в нем создают дополнительную систему более крупных пор заданного размера – микро-мезо-макропор [6]. Цеолиты, характеризующиеся наличием в своей структуре пор различного диаметра, называют иерархическими цеолитными системами.
Согласно [7] способы создания таких цеолитных систем условно могут быть разделены на две группы: “top-down” и “bottom-up”. Первая – “top-down”, заключается в различных типах постсинтетической обработки и модификации цеолита. Среди них наиболее широко применяют способы удаления атомов алюминия (деалюминирование) и кремния (десилилирование) из кристаллической решетки цеолита, которые вызывают изменение отношения Si/Al в цеолитах, и, как следствие, ведут к формированию дополнительной системы пор.
Вторая – “bottom-up”, подразумевает формирование вторичной пористости в процессе гидротермального синтеза цеолитов с использованием соответствующих шаблонов и модифицированием условий синтеза цеолитов
Несмотря на перспективность предлагаемых подходов (“bottom-up”) для получения иерархических цеолитных систем, в настоящее время в промышленности они не реализованы, так как являются продолжительными и достаточно трудоемкими, требуют модернизации существующей технологии, а используемые темплаты достаточно дороги.
В промышленности цеолиты получают в виде порошков, а катализаторы, как правило, в промышленных процессах применяют в виде сформованных гранул. Одним из способов создания цеолитных материалов с развитой системой пор является формирование каталитической композиции цеолит–связующее (матрица). В качестве связующего (матрицы) для цеолитсодержащих материалов, в том числе и катализаторов, используют чаще всего оксид алюминия или его прекурсоры (например, гидроксиды или соли алюминия). Природа связующего, так же как и природа самого цеолита, оказывает существенное влияние на пористую структуру сформованного цеолитсодержащего материала. Использование различных по структуре оксидов алюминия (или их прекурсоров) в композиции “цеолит + связующее”, позволяет получать мономодальное, либо полимодальное распределение пор по размерам. В связи с этим, при приготовлении цеолитсодержащих катализаторов, особое внимание уделяется не только природе цеолита, но и матрице.
Цель данной работы – изучение параметров пористой структуры композиций, содержащих цеолиты структурных типов ZSM-5, ВЕА и гидроксид алюминия от различных производителей, и установление их влияния на каталитическую активность в реакции изомеризации н-гексана.
ЭКСПЕРИМЕНТАЛЬНАЯ ЧАСТЬ
В качестве объектов исследования выбраны цеолиты ZSM-5 и ВЕА. На основе данных цеолитов приготовлены композиции с гидроксидом алюминия (ГА) от разных производителей – Ангарский завод катализаторов и органического синтеза ОАО “АЗК и ОС” (А-64) и Sasol (Pural SB). В табл. 1 представлен состав и условия приготовления композиций.
Таблица 1.
Параметры приготовления исследуемых образцов
Номер образца |
Состав образца цеолит/ГА, % мас. |
Производитель ГА | Пептизатор |
---|---|---|---|
1 | ZSM-5 | – | – |
2 | ВЕА | – | – |
3 | 70 ZSM-5/30 ГА | Sasol | Водный раствор азотной кислоты |
4 | 70 ВЕА/30 ГА | Sasol | Водный раствор азотной кислоты |
5 | 70 ВЕА/30 ГА | ОАО “АЗК и ОС” | Водный раствор азотной кислоты |
6 | 70 ВЕА/30 ГА | ОАО “АЗК и ОС” | Смесь водных растворов азотной кислоты и аммиака (1 : 1) |
7 | 70 ВЕА-1/30 ГА | Sasol | Водный раствор азотной кислоты |
Цеолиты ZSM-5 (образец №1) и ВЕА (образец №2) получены гидротермальной кристаллизацией алюмосиликатных гелей при температуре 140°С в течение 120 и 160 ч соответственно. В качестве сырьевых источников кремния и алюминия использовали силикагель (марка КСКГ) и алюминат натрия (NaAlO2). Цеолит ВЕА синтезирован в присутствии темплата – бромида тетраэтиламмония (С2Н5)4NBr, а в синтезе цеолита ZSM-5 структурообразующий компонент (темплат) не использовали. После синтеза получали цеолит ZSM-5 с силикатным модулем (мольное отношение SiO2/Al2O3), равным 30, а цеолиты ВЕА и ВЕА-1 с SiO2/Al2O3 = 27 и 20 соответственно.
Для получения NH4-формы цеолитов, используемой для приготовления катализаторов, проводили двукратный ионный обмен с раствором нитрата аммония (${{С}_{{{\text{N}}{{{\text{H}}}_{{\text{4}}}}{\text{N}}{{{\text{O}}}_{{\text{3}}}}}}}$ = 30 г/л).
Все композиции цеолит–связующее приготовлены в процессе замеса катализаторной массы с последующим ее формованием. Для приготовления композиции в смеситель загружали необходимые по расчету количества цеолита и гидроксида алюминия (соответствующие 70 и 30 мас. % в пересчете на прокаленное при 650°С вещество). Раствор азотной кислоты (концентрация 46 мас. %) применяли в качестве пептизатора. Азотную кислоту добавляли постепенно, ее количество определяли по достижению смеси определенной пластичности. Для цеолита ZSM-5 это количество составляет 4–9 мл на 100 г композиции (в пересчете на абсолютно сухое вещество), для цеолита ВЕА это количество составляет 5–10 мл на 100 г композиции. Полученную смесь перемешивали в течение 20 мин до получения пластичной массы, затем формовали в гранулы диаметром 1–1.2 мм. Композиции цеолит–связующее в виде сформованных гранул сушили на воздухе при комнатной температуре в течение 24 ч, затем при температуре 120°С в течение 2 ч.
Прокаливали композит (цеолит ZSM-5 + ГА) в муфельной печи при температуре 500°С в течение 3 ч, а композиты (цеолит ВЕА + ГА) при температуре 550°С до полного отжига структурообразующего компонента.
Для установления влияния природы пептизатора на текстурные характеристики композита цеолит–связующее, аналогично образцу № 5 был приготовлен образец № 6, где в качестве пептизатора использовали смесь водных растворов азотной кислоты (концентрация 46 мас. %) и аммиака (концентрация 12 мас. %) в соотношении 1 : 1.
Для приготовления образца № 7 использовали цеолит ВЕА-1 (SiO2/Al2O3 = 20). Композит (ВЕА-1 + ГА) приготовлен по аналогии с другими образцами.
Фазовый состав полученных образцов определяли методом рентгенофазового анализа на дифрактометре Shimadzu Maxima XRD 7000 (напряжение 40 кВ, ток 50 мА, медный анод). Для определения структуры образцов выполняли обзорное сканирование области 2θ = 3°–80° (шаг сканирования 0.02°). Расшифровку рентгенограмм осуществляли в программе Match с использованием базы данных PDF-2 [8].
Анализ морфологии образцов проводили на электронном микроскопе JEOL JIB-24500. Порошки наносили на проводящий скотч и снимали при напряжении 30–40 kV.
Исследование параметров пористой структуры проводили на приборе серии СОРБИ (ЗАО “МЕТА”, Новосибирск) путем сравнения объемов газа-адсорбата (азота), сорбируемого исследуемым образцом и стандартным образцом материала (Al2O3), предоставленных фирмой “МЕТА”, с известной удельной поверхностью 106 м2/г. Удельную поверхность определяли в рамках полимолекулярной модели Брунауэра–Эммета–Теллера, распределение мезопор по размерам – путем моделирования процессов капиллярной конденсации азота. Расчет внешней удельной поверхности проводили по адсорбционной ветви изотермы при четырех относительных парциальных давлениях газа-адсорбата азота 0.15, 0.20, 0.30 и 0.40, расчет объема микропор – по адсорбционной ветви изотермы в диапазоне относительных парциальных давлениях газа-адсорбата азота до 0.40. Построение гистограммы (кривой распределения) пор по размерам осуществляли с помощью специально разработанного программного обеспечения в среде LabView [9].
Тестирование каталитической активности композиций цеолит–связующее проводили в реакции изомеризации н-гексана на лабораторной проточной установке с неподвижным слоем катализатора в токе водорода при температуре 270°С, Р = 20 атм., объемной скорости подачи сырья V0 = 2.0 ч–1, мольном соотношении водород : н-гексан = 2 : 1.
Для каталитических испытаний на все композиции цеолит–связующее был нанесен активный компонент – (Pt) из раствора платинохлористоводородной кислоты, объем которого определяли по влагоемкости носителя. Содержание Pt в составе катализатора составляет 0.3 мас. %. После пропитки образцы катализаторов просушивали на воздухе, затем прокаливали в токе воздуха в течение 3 ч при температуре 500°С, затем образцы восстанавливали в токе водорода в течение 2 ч при температуре 450°С. Углеводородный состав изомеризата определяли методом газовой хроматографии на хроматографе “АГАТ-12” с капиллярной колонкой длиной 6 м с неподвижной фазой – триэтиленгликольдибутират.
РЕЗУЛЬТАТЫ И ИХ ОБСУЖДЕНИЕ
Исследования образцов цеолитов, гидроксидов алюминия и композиций на их основе методом рентгенофазового анализа показали, что у образца №1 присутствуют все характеристические рефлексы, соответствующие структуре цеолита ZSM-5 [10]. Были определены параметры элементарной ячейки образца №1, которые также подтверждают его принадлежность к структурному типу ZSM-5 с параметрами кристаллической решетки a = 20.121, b = 19.919, c = 13.401 Å; α = 90°, β = 90°, γ = 90°. На рис. 1 представлены рентгенограмма (а) и электронно-микроскопический снимок (б) цеолита ZSM-5.
Из анализа скан-снимка следует, что кристаллиты цеолита ZSM-5, в основном, в виде гексагональной формы с преобладающим размером в одном направлении до 2 мкм. Реже встречаются формирования в виде “розы”, достигающие в одном направлении размеров до 3–4 мкм.
По результатам исследования образца № 2 установлено, что наличие характеристических рефлексов (межплоскостное расстояние d/n = 12.3238, 11.4417, 4.0985, 3.9265, 3.7808, 3.5389, 3.4874) свидетельствует о соответствии структуры образца цеолиту ВЕА. На рис. 2 приведены рентгенограмма цеолитов ВЕА и ВЕА-1.
С помощью рентгенофазового анализа был исследован оксид алюминия (ОА) производства Sasol, полученный в результате прокалки образца гидроксида алюминия (Sasol, Pural SB). Согласно результатам анализа, образец ОА (Sasol) представлен фазой (Al2O3)1.333, о чем свидетельствует наличие соответствующих рефлексов (межплоскостное расстояние d/n = 4.5621, 2.2860 и 1.9670) на рентгенограмме. Согласно сертификату качества, представленному производителями (Sasol), исходный гидроксид алюминия Pural SB – псевдобемит. Гидроксид алюминия производства ОАО “АЗК и ОС” содержит, в основном, фазу бемита – AlO(OH), о чем свидетельствует наличие характеристических пиков d/n = 6.1568, 3.1957, 2.3568, 1.9872, 1.8652, 1.7886, 1.6674, 1.5326, 1.4616, 1.4372, 1.3946, 1.3179. В результате обработки образца ГА (ОАО “АЗК и ОС”) при температуре 450°С в течение 3 ч получен оксид алюминия γ-Al2O3 (A-64). На рис. 3 представлены рентгенограммы носителей, используемых для приготовления композиций цеолит–связующее.
Рис. 3.
Рентгенограммы носителей, используемых в композициях: ГА (производство АЗК и ОС) (а) и ГА (Sasol) (б).
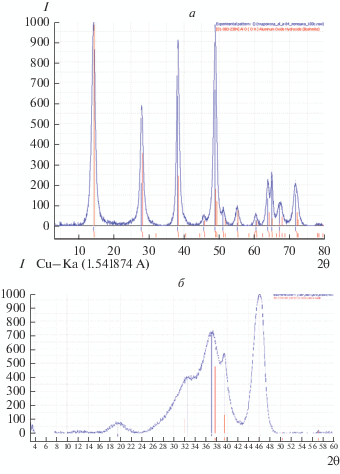
Результаты сорбционных исследований и расчета параметров пористой структуры образцов приведены в табл. 2, где величина ${{\alpha }_{m}}$ удельная емкость монослоя, ${{S}_{{{\text{уд}}}}}$ удельная поверхность исследуемого материала, ${{S}_{{{\text{вн}}{\text{.уд}}}}}$ внешняя (без учета вклада микропор) удельная поверхность материала, ${{V}_{{{\text{сум}}}}}$ суммарный удельный объем пор в образце, ${{N}_{{2.6}}}$ число пор со средним радиусом 2.6 нм.
Таблица 2.
Результаты расчета параметров пористой структуры образцов
Номер образца | ${{\alpha }_{m}},~\,\,{{{\text{моль}}} \mathord{\left/ {\vphantom {{{\text{моль}}} {\text{г}}}} \right. \kern-0em} {\text{г}}}$ | Sуд, м2/г | Sвн.уд, м2/г | Vсум, мл/г | N2.6, % |
---|---|---|---|---|---|
1 | 41.2 | 179 | 25 | 24.4 | 4.5 |
3 | 45.3 | 197 | 82 | 50.1 | 41.0 |
4 | 60.8 | 264 | 184 | 63.8 | 32.1 |
5 | 66.7 | 290 | 146 | 58.1 | 15.6 |
6 | 71.5 | 311 | 156 | 72.1 | 14.9 |
7 | 75.9 | 330 | 181 | 72.9 | 34.2 |
На рис. 4–7 для примера приведены изотерма адсорбции азота и гистограммы распределения пор по размерам, полученные при исследовании композиции “ВЕА–гидроксид алюминия” (образец 4) и аналогичной композиции с использованием в качестве пептизатора смеси водных растворов азотной кислоты и аммиака (образец 6).
Под термином “десорбционная ветвь” на рис. 5, 7 понимается обратный ход гистерезиса, возникающего при понижении относительных парциальных давлений газа-адсорбата.
На завершающей стадии синтеза образцы сформованных гранул сушат на воздухе при комнатной температуре, затем при температуре 120°С и выдерживают в муфельной печи при температуре 500°С. При увеличении температуры обработки величина удельной поверхности образцов уменьшается на 30–80 м2/г.
Было установлено, что при создании композиции цеолита ZSM-5 с гидроксидом алюминия (образец № 3) по сравнению с цеолитом ZSM-5 (образец № 1) величина удельной поверхности ${{S}_{{{\text{уд}}}}}$ возрастает на 18 м2/г (от 179 до 197 м2/г), величина внешней удельной поверхности ${{S}_{{{\text{вн}}{\text{.уд}}}}}$ – в 3.3 раза (от 25 до 82 м2/г), суммарный объем пор – в 2.05 раза (от 24.4 до 50.1 мл/г), количество пор со средним радиусом 2.6 нм ${{N}_{{2.6}}}$ – на 36.5% (с 4.5 до 41.0%).
Замена в композиции цеолита ZSM-5 (образец № 3) на цеолит ВЕА (образец № 4) приводит к возрастанию величины удельной поверхности ${{S}_{{{\text{уд}}}}}$ на 67 м2/г (от 197 до 264 м2/г), величины внешней удельной поверхности ${{S}_{{{\text{вн}}{\text{.уд}}}}}$ в 2.2 раза (от 82 до 184 м2/г) и суммарного объема пор в 1.27 раза (от 50.1 до 63.8 мл/г), то дальнейшие исследования композиций были проведены с образцами на основе цеолита ВЕА.
При выборе в качестве связующего гидроксида алюминия (А-64) производства ОАО “АЗК и ОС” (образец № 5) по сравнению с образцом № 4, для которого в качестве связующего был взят гидроксид алюминия производства Sasol, обнаружено, что параметры удельной поверхности образцов отличаются (величина удельной поверхности ${{S}_{{{\text{уд}}}}}$ отличается на 26 м2/г, а величины внешней удельной поверхности ${{S}_{{{\text{вн}}{\text{.уд}}}}}$ – в 1.3 раза).
Выявлено, что изменение пористой структуры композиции (образцы № 5 и 6) происходит при использовании в качестве пептизатора смеси водных растворов азотной кислоты и аммиака (в соотношении 1 : 1). При этом увеличивается удельная поверхность ${{S}_{{{\text{уд}}}}}$ на 21 м2/г, величины внешней удельной поверхности ${{S}_{{{\text{вн}}{\text{.уд}}}}}$ – в 1.1 раза.
Обнаружено, что при изменении содержания кристаллической фазы и силикатного модуля в композиции (замена цеолита ВЕА на ВЕА-1, образцы № 7 и 4) происходит увеличение величины удельной поверхности ${{S}_{{{\text{уд}}}}}$ на 66 м2/г (от 264 до 330 м2/г), суммарный объем пор – в 1.14 раза (от 63.8 до 72.9 мл/г), количество пор со средним радиусом 2.6 нм ${{N}_{{2.6}}}$ – на 2.1% (с 32.1 до 34.2%); изменение величины внешней удельной поверхности ${{S}_{{{\text{вн}}{\text{.уд}}}}}$ практически не происходит (от 184 до 181 м2/г).
Анализ результатов, представленных в табл. 2 показывает, что использование композиции “гидроксид алюминия ГА(Sasol) + цеолит ZSM-5” приводит к существенному возрастанию величины внешней удельной поверхности ${{S}_{{{\text{вн}}{\text{.уд}}}}},$ суммарному объему пор ${{V}_{{{\text{сум}}}}}$ количеству пор со средним радиусом 2.6 нм ${{N}_{{2.6}}}$ по сравнению с исходным цеолитом ZSM-5. Использование цеолита ВЕА для приготовления композиции “ГА(Sasol) + цеолит ВЕА” приводит к тому, что практически все параметры пористой структуры композиции превышают таковые для композиции “ГА(Sasol) + цеолит ZSM-5”.
Ранее было показано, что природа связующего, так же как и природа самого цеолита, оказывают существенное влияние на характеристики пористой структуры сформованного материала. Это подтверждается и результатами, полученными для образца 5. Для приготовления композиции был использован гидроксид алюминия производства ОАО “АЗК и ОС”. Величины внешней удельной поверхности ${{S}_{{{\text{вн}}{\text{.уд}}}}},$ суммарного объема пор ${{V}_{{{\text{сум}}}}}$ и количества пор со средним радиусом 2.6 нм ${{N}_{{2.6}}}$ по сравнению с образцом № 4 несколько снизились. Возможно, что это связано с тем, что размеры кристаллитов гидроксида алюминия производства ОАО АЗК и ОС (А-64) существенно выше, чем у ГА (Sasol).
Мы предполагали, что использование смеси водных растворов аммиака и азотной кислоты в соотношении 1 : 1 может привести к увеличению общей удельной поверхности ${{S}_{{{\text{уд}}}}}$ и суммарного объема пор ${{V}_{{{\text{сум}}}}}$. Результаты, полученные для образца № 6, подтверждают наше предположение. Следует отметить, что в данном случае снизилось количество пор со средним радиусом 2.6 нм ${{N}_{{2.6}}}$ по сравнению с образцом № 5. Возможно, наблюдаемые изменения параметров пористой структуры связаны с взаимодействием аммиака с моногидратом алюминия (бемитом) – AlOOH, также как и при использовании только азотной кислоты в качестве пептизатора. При взаимодействии моногидрата алюминия с концентрированным аммиаком происходит разрыхление поверхностных слоев бемита, которые затем при прокалке формируют некоторые агрегаты на поверхности, что, возможно, и приводит к уменьшению объема микропор.
Образец № 7 приготовлен с использованием цеолита ВЕА-1 (SiO2/Al2O3 = 20), который в отличие от цеолита ВЕА (SiO2/Al2O3 = 27), имеет более низкое содержание SiO2 в составе цеолита, что приводит к менее гидрофобному характеру поверхности и тем самым обеспечивает более сильное взаимодействие между компонентами системы. По-видимому, при взаимодействии азотной кислоты с поверхностью гидроксида алюминия происходит частичное разрушение кристаллитов на более мелкие, что возможно и приводит к увеличению удельной поверхности и суммарного объема пор. Величина внешней удельной поверхности ${{S}_{{{\text{вн}}{\text{.уд}}}}}$ и количество пор со средним радиусом 2.6 нм ${{N}_{{2.6}}}$ практически не изменяется (в сравнении с образцом 4). Наибольший суммарный объем пор был получен в образце 7, что может быть также связано с высокой дисперсностью частиц ГА (Sasol).
В табл. 3 представлены результаты испытаний катализаторов на основе композиций цеолит–связующее в реакции скелетной изомеризации н-гексана, которая является хорошей тестовой реакцией на текстурные характеристики исследуемых образцов катализаторов. Выбор в качестве модельного сырья н-гексана обусловлен тем, что в промышленности процесс изомеризации пентан-гексановых фракций очень важен для получения высокооктановых компонентов бензинов.
Таблица 3.
Каталитические характеристики цеолитных композиций в реакции изомеризации н‑гексана (Т = 270°С, Vo = 2.0 ч–1, Р = 20 атм., мольное соотношение Н2 : сырье = 2.0)
№ | Катализатор | Углеводородный состав | К, % | S, % | ||||
---|---|---|---|---|---|---|---|---|
ΣС2–С5 | 2,2 ДМБ | 2,3ДМБ + + 2МП | 3МП | н-С6 | ||||
3 | 70ZSM-5/30ГА (Sasol), пепт. HNO3 | 12.0 | 12.3 | 31.6 | 20.6 | 23.5 | 76.5 | 84.3 |
4 | 70BEA/30ГА (Sasol), пепт. HNO3 | 5.6 | 14.6 | 32.3 | 21.5 | 26.0 | 74.0 | 92.4 |
5 | 70BEA/30ГА (АЗК и ОС), пепт. HNO3 | 5.4 | 14.1 | 31.8 | 21.2 | 27.5 | 72.5 | 92.6 |
6 | 70BEA/30ГА (АЗК и ОС), пепт. HNO3 : NH4NO3 (1 : 1) |
5.0 | 15.0 | 32.5 | 21.8 | 25.7 | 74.3 | 93.3 |
7 | 70BEA-1/30ГА (Sasol), пепт. HNO3 |
5.3 | 15.6 | 32.7 | 22.0 | 24.4 | 75.6 | 93.0 |
Из представленных экспериментальных данных видно, что основными продуктами превращения н-гексана в данных условиях являются изомеры гексана: 2-метилпентан (2-МП), 3-метилпентан (3-МП), 2,2-диметилбутан (2,2-ДМБ) и 2,3-диметилбутан (2,3-ДМБ). В табл. 4 представлены значения октанового числа для н-гексана и продуктов его изомеризации. Наибольшее октановое число у 2,3-диметилбутана (2,3-ДМБ). В данном эксперименте разделить продукты превращения 2,3-ДМБ и 2-метилпентан (2-МП) не представилось возможным. Эффективность действия катализаторов рассматривали по выходу 2,2-диметилбутана (2,2-ДМБ).
Таблица 4.
Октановое число углеводородов, образующихся в реакции изомеризации н-гексана [11]
Углеводород | Октановое число |
---|---|
н-гексан | 24.8 |
2-метилпентан | 73.4 |
3-метилпентан | 74.5 |
2,2-диметилбутан | 92.8 |
2,3-диметилбутан | 103.5 |
В продуктах реакции обнаружены продукты гидрогенолиза (углеводороды С2–С5). У катализатора на основе цеолита ZSM-5 их содержание значительно выше, чем у образцов катализаторов на основе цеолита ВЕА. Это может быть обусловлено тем, что цеолит ZSM-5 обладает более высокой кислотностью по сравнению с цеолитом ВЕА [12], или связано с молекулярно-ситовым эффектом. Пористая структура цеолита MFI образована пересекающимися прямыми и синусоидальными каналами с сечением эллиптической формы с размером поперечников около 5.5 Å, в то время как у широкопористого цеолита ВЕА с трехмерной системой пересекающихся каналов с двенадцатичленными кольцами, в местах пересечения каналов образуются полости диаметром 6.68 Å [13].
Анализ табл. 2 и 3 показывает, что наибольший выход 2,2-ДМБ наблюдается для образцов 6 и 7 (15.0 и 15.6%), у которых более высокая площадь удельной поверхности и суммарный объем пор по сравнению с другими исследуемыми образцами композитов.
В работе [14] показано, что отношение Si/Al в цеолитах оказывает влияние на их активность в реакции изомеризации н-парафинов. Увеличение отношения Si/Al в цеолите выше некоторого оптимального значения приводит к снижению активности катализатора из-за уменьшения количества кислотных центров.
Для цеолитов ВЕА и ВЕА-1, несмотря на разные отношения Si/Al, различие в активности катализаторов на их основе незначительно. Из анализа табл. 3 следует, что несмотря на более низкую кислотность цеолита ВЕА по сравнению с кислотностью цеолита ZSM-5, активность катализатора и распределение продуктов реакции являются чувствительными к пористой структуре катализатора, что согласуется с результатами работы [15].
ЗАКЛЮЧЕНИЕ
В работе рассмотрены результаты исследования параметров пористой структуры характеристик цеолитных композиций с иерархической структурой, служащих основой для различных катализаторов, в зависимости от состава композиций. Установлено, что наибольшее влияние на параметры пористой структуры композиций оказывают такие технологические факторы, как выбор пептизатора, значение силикатного модуля, тип связующего материала.
Активность и селективность катализатора в изомеризации н-гексана определяются и его пористой структурой.
По-видимому, в цеолитных композициях возможно целенаправленное регулирование параметров пористой структуры (путем варьирования природы цеолита, носителя, пептизатора и их количеств), которые оказывают существенное влияние на их каталитические характеристики.
Список литературы
Cejka Jiri, Corma Avelino, Zones Stacey. Zeolites and Catalysis: Synthesis, Reactions and Applications // Wiley-VCH, 2010. 918 p.
Bacakova Lucie, Vandrovcova Marta, Kopova Ivana, Jirka Ivan. Applications of zeolites in biotechnology and medicine – a review // Biomater. Sci. 2018. № 6. P. 974–989.
Rhodes C.J. Properties and applications of zeolites // Science Progress. 2010. № 93. P. 223–284.
IUPAC. Manual of symbols and terminology // Pure Appl. Chem. 1972. V. 31. P. 578.
Пархомчук Е.В., Сашкина К.А., Пармон В.Н. Новые гетерогенные катализаторы на основе цеолитов с иерархической системой пор // Нефтехимия. 2016. Т. 56. № 3. С. 214–221.
Грачева И.Е., Мошников В.А. Наноматериалы с иерархической структурой пор: учеб. пособие. СПб.: Изд-во СПбГЭТУ “ЛЭТИ”, 2011. 106 с.
Agnieszka Feliczak-Guzik. Hierarchical zeolites: synthesis and catalytic properties microporous and mesoporous materials. 2018. V. 259. P. 33–45.
PDF-2. The powder diffraction file TM. International Center for Diffraction Data (ICDD), PDF-2 Release 2012, web site: www.icdd.com, 2014.
Мараева Е.В. Программное обеспечение для исследования параметров пористой структуры металлооксидных наноматериалов методами тепловой десорбции азота и аргона // Universum: технические науки. 2016. № 12(33). С. 17–21.
PDF. Powder Diffraction File. Hanawaet search manual. Inorganic phases. 42, 1992.
Химическая энциклопедия / Под ред. Кнунянца И.Л. Т. 1. М.: Советская энциклопедия., 1988. С. 991.
Боруцкий П.Н. Каталитические процессы получения углеводородов разветвленного строения. Санкт-Петербург: НПО “Профессионал”, 2010. 728 с.
Родионова Л.И., Князева Е.Е., Коннов С.В., Иванова И.И. Перспективы применения наноразмерных цеолитов в нефтехимии: синтез и каталитические свойства (обзор) // Нефтехимия. 2019. Т. 59(3). С. 333–349.
Chao K.-J., Wu H.-C., Leu L.-J. Hydroisomerization of light normal paraffins over series of platinum-loaded mordenite and beta catalysts // Applied Catalysis A: General. 1996. V. 143. P. 223–243.
Tromp M., Van Bokhoven J.A., Oostenbrink M.T.G., Bitter J.H., De Jong K.P., Koningsberger D.C. Influence of the generation of mesopores on the hydroisomerization activity and selectivity of n-Hexane over Pt/Mordenite // J. Catalysis. 2000. V. 190. P. 209–214.
Дополнительные материалы отсутствуют.
Инструменты
Физика и химия стекла